
6 minute read
CASOS DE ÉXITO
CITEagroindustrial ICA
El CITEagroindustrial emerge desde la experiencia del CITEvid, creado en el 2000, Centro de Innovación Tecnológica que hizo de la cadena vitivinícola y el pisco, uno de los productos bandera peruano, con mayor
Advertisement
crecimiento de la última década. Su misión es apoyar al fortalecimiento de las cadenas agroindustriales del Perú, promoviendo la innovación, a través de la investigación, la transferencia tecnológica, la capacitación, la asistencia técnica, el desarrollo de productos y la optimización de procesos que impulsen la competitividad industrial en el Perú y contribuya a la seguridad alimentaria y nutricional.
El CITEagroindustrial ha trabajo en la mejora de sus procesos aplicando las 5S: subordinar, sistematizar, sanear, simplificar y sostener. Logrando minimizar el desperdicio, asegurando que las zonas de trabajo se encuentren limpias y organizadas, mejorando la productividad y la seguridad. Adicionalmente, cuenta con un sistema integrado de gestión basado en normas internacionales, el resguardo responsable de las operaciones comerciales a lo largo de toda la cadena de suministro y la calidad e inocuidad de los productos y servicios que ofrecen. Las normas/estándares con las que cuenta son: HACCP, NTP - ISO/IEC 17025, Global GAP, ISO 9001 y Buenas Prácticas Logísticas. 11
Con el respaldo de la experiencia adquirida y el alto nivel de sus profesionales, el CITEagroindustrial viene realizando servicios de implementación de sistemas de mejora de la calidad y de mejora continua en empresas del sector, obteniendo buenos resultados.
Agroindustrial Laredo
En Agroindustrial Laredo se apuesta por la mejora continua con el fin de obtener cada vez mejores resultados. Así, sus colaboradores integran diferentes herramientas de gestión orientadas a mejorar el desempeño de los procesos de producción.
Como parte de la mejora continua, la empresa también obtuvo la certificación ISO 9001, que garantiza la correcta implementación de nuestro Sistema de Gestión de Calidad y el ISO 22000, que certifica un estricto respeto por la
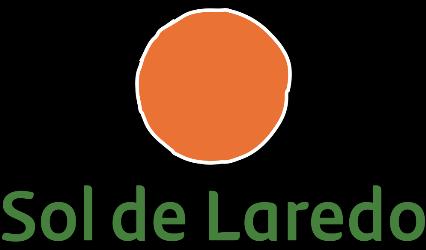
seguridad alimentaria. A estas certificaciones, se suma el ISO 14001, que acredita la implementación de su Sistema de Gestión Ambiental, mediante el cual se establecen controles operativos para minimizar los impactos ambientales que sus procesos podrían generar. 12
11 Extraído de: http://citeagroindustrial.com.pe 12 Extraído de: http://www.agroindustriallaredo.com/index.php/mejora-continua/ UNIDAD DE VIGILANCIA TECNOLÓGICA E INTELIGENCIA COMPETITIVA
Agro Industrial Paramonga
La empresa Agro Industrial Paramonga (AIPSAA) procesa y comercializa caña de azúcar y productos derivados (alcohol y generación de energía eléctrica). La caña de azúcar llega desde los campos de cultivo hacia fábrica, en donde luego de pasar por diversos procesos finalmente se obtiene el azúcar granulado en dos presentaciones: azúcar rubia y azúcar blanca. El azúcar finalmente es embolsado y comercializado atendiendo la demanda de sus principales clientes importantes cadenas de supermercados.
Se estableció el
procedimiento Lean Manufacturing durante el año 2014, alcanzando mejoras en la producción, manteniendo un lugar de trabajo limpio y ordenado que influye en la moral de un trabajador de forma positiva. Adicional

a ello se busca minimizar tiempos para que la
realización de las tareas se efectúan con mayor rapidez cuando se realiza el intercambio de componentes para el embolsado de diferentes presentaciones y/o tipo de azúcar según la necesidad del cliente. 13
Toyota
Toyota y su director, el ingeniero Taiichi Ohno, fueron los artífices del primer lean manufacturing. De esta empresa nipona surgió también uno de los programas de mejora de procesos más famoso del mundo, el llamado 5S: subordinar, sistematizar, sanear, simplificar y sostener el proceso. 14
A través de estas nuevas medidas Lean, Toyota muestra que sigue siendo un modelo a seguir con su estrategia de innovación como ventaja competitiva
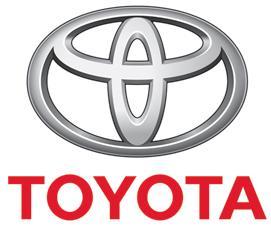
sostenible. El método Lean y las medidas de mejora continua que la compañía incorpora a sus procesos mejoran el rendimiento, reducen los desperdicios y maximizan la flexibilidad permitiendo ofrecer un mayor valor para el cliente y reducir los costes. 15
Dell
La implementación de Six Sigma en Dell es uno de los ejemplos principales y exitosos de una compañía que usa Six Sigma como un habilitador para lograr resultados exitosos. Michael Dell construyó un modelo exitoso utilizando Lean Six Sigma que ha emulado Dell Inc. en gran medida. Alrededor del año 2000, utilizando las metodologías Six Sigma y manteniéndola como base para la mejora, una de las

iniciativas clave lideradas por Michael Dell se conocía como Business Process Improvement que es un conjunto de herramientas y habilidades que Dell ha empleado para mejorar, comprender e investigar procesos empresariales. Siguiendo a BPI durante bastantes años, Dell ha realizado cambios significativos en su forma de tratar con los clientes, mejorando así la satisfacción del cliente y los proveedores. La esencia de la última estrategia es Lean. En lugar de producir grandes lotes de sistemas como competidores, Dell ha decidido seguir la estrategia Lean, es decir, producir lotes pequeños que pueden personalizarse según las preferencias del usuario. 16
13 Extraído de: http://repositorio.upn.edu.pe/bitstream/handle/11537/10884/T055_40951824_T.pdf?sequence=1 14 Extraído de: https://smarterworkspaces.kyocera.es/blog/lean-manufacturing-casos-exito-internacional/ 15 Extraído de: http://www.progressalean.com/las-nuevas-medidas-lean-para-la-mejora-continua-de-toyota/ 16 Extraído de: https://henryharvin.com/blog/67/six-sigma-implementation-in-dell
Caterpillar
La longeva empresa norteamericana Caterpillar fundada en el siglo XIX fue una de las primeras compañías occidentales que
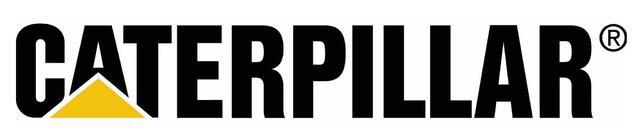
apostó por el modelo de mejora continua de Toyota.
Caterpillar implantó Six Sigma a escala global desde el primer día, a partir de enero de 2001, se utilizó una estrategia de implantación transformacional, en lugar de usar una estrategia funcional o una específica. Estas dos últimas centran su atención en personas o procesos específicos y, aunque requieren una menor inversión inicial, hacen que resulte difícil integrar Six Sigma en otros ámbitos de la empresa, en gran medida porque no existe un lenguaje común y un compromiso generalizado en toda la empresa. En el caso de Caterpillar, la alta dirección de la empresa se comprometió desde el principio y dejó claro que 6 Sigma había llegado para quedarse. 17
Motorola
En 1988, Motorola Corp. se convirtió en una de las primeras compañías en recibir el Premio Nacional de Calidad Malcolm Baldrige. El premio se esfuerza por identificar aquellas firmas excelentes que son dignos modelos para otras empresas. Una de las innovaciones de Motorola que atrajo gran atención fue su programa Six Sigma. Six Sigma es, básicamente, un objetivo de calidad de proceso. Como tal, cae en la categoría de una técnica de capacidad de proceso (Cp).
Una de las contribuciones más importantes de
Motorola fue cambiar la discusión de la calidad de una en la que los niveles de calidad se midieron en porcentajes (partes por cien) a una discusión de partes por millón o incluso partes por mil millones. Motorola señaló correctamente que la tecnología

moderna era tan compleja que las viejas ideas sobre niveles aceptables de calidad ya no eran aceptables. 18
General Electric
Fue en 1995 cuando comenzó la implementación de Six Sigma por parte de General Electric. Su CEO Jack Welch fue la fuerza impulsora detrás de esta implementación, actuando como un testaferro para que el resto de la compañía se recuperara. Bajo su supervisión, se esforzó por garantizar que la empresa
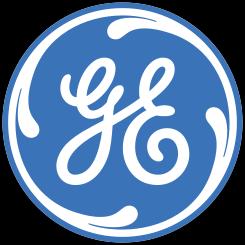
integrara Six Sigma en sus operaciones. Este cambio en las operaciones comenzó cuando Welch se dio cuenta de los muchos reveses de GE, la compañía a menudo no alcanzaba su potencial. Welch reconoció que GE requería una revisión completa de todas sus operaciones fundamentales.
Trabajando con ingenieros y consultores, Welch detectó una gran cantidad de defectos que anteriormente habían pasado desapercibidos. Esta acumulación de residuos estaba reteniendo a la compañía, perdiéndoles dinero y ralentizando su producción. Welch sabía qué hacer. Lo había visto en acción y sabía que podría salvar a General Electric de sí mismo. Sabía que Six Sigma podría ayudar a optimizar la empresa, hacerla más eficiente y productiva, eliminar el desperdicio y cambiarlo para mejor. Lo hizo. 19
17 Extraído de: http://jmrentabiliza.com/casos%20de%20exito%20sigma%20y%20carterpilar.pdf 18 Extraído de: https://www.qualitydigest.com/magazine/1997/dec/article/motorolas-six-sigma-program.html# 19 Extraído de: https://www.6sigma.us/ge/six-sigma-case-study-general-electric/ UNIDAD DE VIGILANCIA TECNOLÓGICA E INTELIGENCIA COMPETITIVA