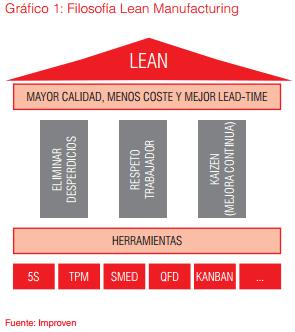
9 minute read
METODOLOGÍAS
Lean manufacturing
El Lean Manufacturing nace en Japón, concretamente de la mano de la empresa automovilística Toyota. A partir de 1950 la empresa vio que el futuro de Japón requeriría construir coches pequeños y de bajo coste. Estableció entonces las bases del nuevo sistema de gestión Just in Time, que formulaba un principio muy simple: “producir solo que se demanda y cuando el cliente lo solicita”. 4
Advertisement
‘Lean’ significa “esbelto”, “sin grasa”, “ágil”…atributos que, al fin y al cabo, son más que apetecibles si nos referimos a plantas productivas. De esta manera, estos desperdicios no hacen otra cosa que añadir coste aumentando las necesidades del cliente sin incrementar el valor que este percibe del producto. Y es que hemos de recordar y tener presente que el coste siempre ha sido un factor fundamental para competir. Lean Manufacturing está compuesto de una serie de herramientas que tienen como único fin la eliminación o reducción de los mentados desperdicios. 5
La filosofía lean manufacturing busca la forma de mejorar y optimizar el sistema de producción, tratando de eliminar o reducir todas las actividades que no añadan valor dentro en el proceso de producción. Se basa en los siguientes sistemas de producción: 6
TQM: Calidad total JIT: Justo a tiempo Kaizen: Mejora continua TOC: Teoría de las restricciones Reingeniería de procesos
Herramientas importantes 7 lean manufacturing más
Muchas veces las herramientas se basan en aplicar el sentido común y un enfoque práctico, como son las siguientes:
5s
Las 5s se utilizan para mejorar las condiciones de cada puesto de trabajo, a través de la organización, orden y limpieza.
Elimina lo que no necesitas en un área de trabajo mal organizada y así, se evitan pérdidas de tiempo buscando herramientas. 8
Seiri –Clasificar Seiton –Organizar Seiso –Limpieza Seiketsu –Estandarizar Shitsuke –Disciplina
4 Extraído de: https://www.iebschool.com/blog/que-es-leanmanufacturing-negocios-internacionales/ 5 Extraído de: https://www.improven.com/blog/productividadlean-manufacturing-como-gestionar-eficazmente-laorganizacion/ 6 Extraído de: https://leanmanufacturing10.com/ 7 Extraído de: https://leanmanufacturing10.com/herramientaslean-manufacturing-mas-importantes-implantarlas 8 Extraído de: http://www.eoi.es/blogs/nayellymercedeslazala/2011/12/18/lean -manufacturing-y-sus-herramientas/
Andon
Andon es un sistema de control visual que permite que todos los empleados sepan el estado y el avance de las acciones de mejora, permitiendo así la involucración de todo el personal.
Ante un problema grave detectado, la producción se para, con el fin de que analizar su causa raíz y resolverlo rápidamente. SMED es una técnica empleada para disminuir los tiempos de cambios de utillaje en máquinas y herramientas. Permite fabricar con lotes pequeños, reduce inventario intermedio y permite adaptarse a cualquier imprevisto del plan de producción. producción, trabajando en lotes más pequeños y mezclando diferentes tipos de productos en el mismo proceso, para adaptar la capacidad de producción a la inventario en curso. Value stream mapping es una herramienta utilizada para visualizar el flujo de producción. Muestra el estado actual del proceso de producción y define el proceso esperado (proceso futuro), obteniendo oportunidades
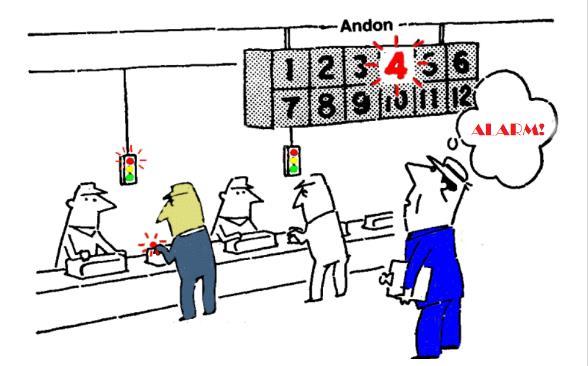
operaciones que no añaden valor y proporciona una hoja de ruta para mejorar hacia el estado futuro.
TPM
TPM es un método de gestión de mantenimiento, que evita las paradas en las máquinas causadas por averías. El objetivo es conseguir cambiar la forma de pensar de los trabajadores, consiguiendo eliminar las averías, los defectos y los accidentes.
Mejora la productividad, ya que reduce tiempos muertos, disminuye el tiempo de ciclo y elimina
SMED
Heijunka
Heijunka es
una forma de planificar y nivelar la demanda del cliente. defectos.
Reduce plazos de entrega e
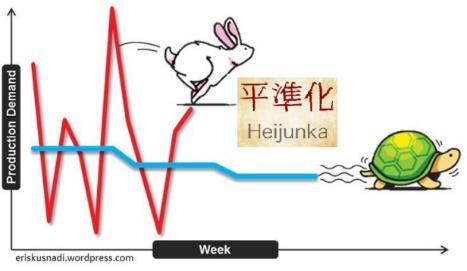
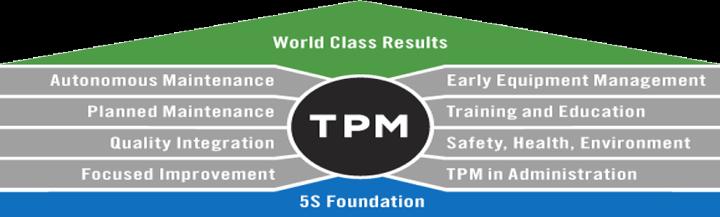
KPIs
Los KPIs son métricas
diseñadas para monitorizar y realizar un seguimiento de los objetivos que se pretenden conseguir.
Indican si nos acercamos o nos alejamos de los objetivos propuestos, que están alineados con otros objetivos estratégicos y muestran si cualquier cambio, ya sea una mejora, un problema o un imprevisto, beneficia o perjudica a la consecución de los objetivos.
Estandarización de trabajos
La estandarización de trabajos consiste en definir una metodología a seguir para realizar los diferentes trabajos con las mejores prácticas y conseguir que todo el personal trabaje siguiendo esta metodología.
Reduce el tiempo de ejecución de las operaciones y
Value Stream Mapping
establece una base para seguir mejorando en el futuro. de mejora.
Exponen todos los desperdicios y
Flujo continuo
El flujo continuo o flujo de una sola pieza (one piece flow) es un sistema de producción en el que el trabajo en curso fluye suavemente entre los diferentes puestos del proceso de producción. Reduce inventario, tiempos de espera y transportes innecesarios.

Kanban
Kanban es un sistema que permite regular el flujo de producción entre procesos y entre proveedores y clientes, basado en un reaprovisionamiento a través de señales que indican cuando se necesita más material. Elimina inventario en curso y sobreproducción, reduce tiempos muertos y mejora el plazo de entrega. El Jidoka es una técnica que consiste en diseñar los equipos para automatizar parcialmente el proceso de producción, con el fin de que se pare cuando se detecta algún tipo de defecto. Es una forma de controlar los realizar el seguimiento de varias estaciones a la vez, reduciendo costes de producción y se pueden detectar muchas incidencias de calidad, por lo que se mejora el nivel de calidad. La gestión visual es una herramienta que utiliza indicadores visuales, pantallas y controles para mejorar la comunicación de la información entre los empleados mundo, operarios y directivos, de controlar el estado del proceso de producción, conforme a los plazos de entrega. Takt time es el ritmo de producción al que se debe de producir de acuerdo con la demanda del cliente.
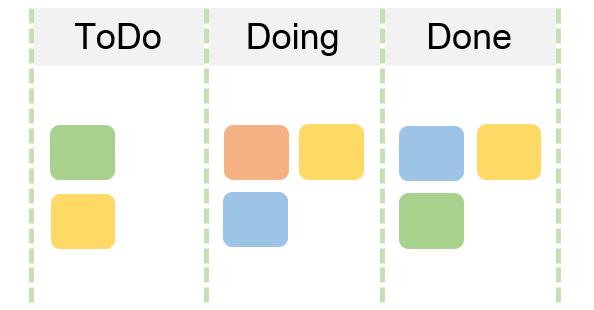
determinar si el ritmo de producción es el adecuado para cumplir con los plazos de entrega.
Just in time
El just in time consiste en producir la cantidad necesaria de productos en el momento necesario. Más que una herramienta es una filosofía de trabajo. Está relacionada con otras herramientas lean manufacturing como flujo continuo, Heijunka, Kanban.
Estandarización de trabajo y takt time.
Se reduce el nivel de inventario, se reducen costes de producción y
Jidoka
defectos automáticamente. Los operarios pueden el espacio requerido en planta.


Análisis de cuellos de botella
Analizar
los cuellos de botella es identificar que procesos de producción limitan la capacidad de producción de una planta y mejora el rendimiento de esos procesos en cuestión. Mejora la productividad gracias a fortalecer el eslabón más débil del proceso de
Gestión visual
de la fábrica. Es una forma accesible para todo el
Takt time
fabricación. Proporciona un método
simple e intuitivo para
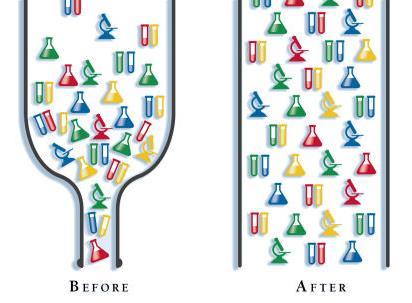
Gemba
Gemba es una filosofía que nos recuerda no estar tanto tiempo en la oficina y pasar más tiempo en el taller, que es donde se producen los problemas reales. Ayuda a entender los problemas que ocurren en el taller y que no dejan que la productividad aumente todo lo que debiera, mediante conversaciones con operarios y la observación de primera mano.
Hoshin Kanri
Hoshin Kanri es una herramienta que permite alinear los objetivos estratégicos de la empresa, con los planes de los mandos intermedios y el trabajo realizado en el taller. Asegura que cada acción llevada a cabo en el taller, conduce a la empresa a cumplir sus objetivos estratégicos, eliminando los desperdicios debidos a una comunicación ineficiente o a no tener una dirección clara.
Kaizen
Kaizen es una estrategia donde los empleados trabajan todos juntos proactivamente para conseguir mejoras continuamente. Utiliza el talento de la unión de todo el mundo para crear una búsqueda constante de eliminación de desperdicios del proceso de producción.

PDCA
PDCA es un método iterativo para implementar mejoras.
Te puede servir como procedimiento definido para implementar una mejora poco a poco.
Poka-Yoke
Poka-Yoke permite detectar errores y prevenirlos en el proceso de producción, con el objetivo de conseguir cero defectos.
Encontrar los defectos con una inspección de calidad y después corregirlos, es mucho más caro que si se detectan antes o directamente si no se producen.
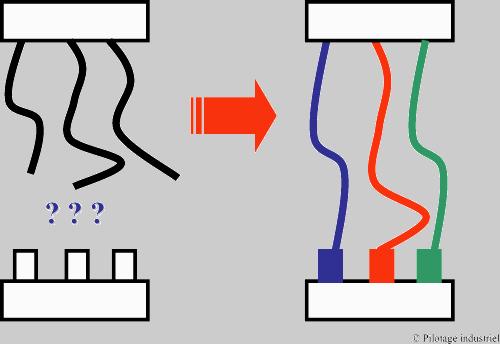
Análisis de la causa raíz
El análisis de la
causa raíz es una metodología de resolución de problemas, que se centra en resolver el problema que causa el defecto, en vez de solamente corregir el problema.
Nos ayuda
a asegurar que el problema es eliminado, aplicando acciones correctivas en la causa que originó el problema.
Las 8 ds.
Las 8 disciplinas es una metodología que permite solucionar problemas.
Nos ayuda a mejorar la producción ya que evita realizar retrabajos y otra clase de despilfarros, como pérdidas de tiempo.
Gestión de la calidad total (TQM)
La gestión de la calidad total (TQM) es una de las herramientas en las que se basa el lean manufacturing y se enfoca en cumplir todos los requisitos de calidad solicitados por el cliente desde el principio del proceso productivo.
Requiere la implicación de todos los componentes del sistema productivo: cliente, proveedor, operarios, gerencia… y permite aumentar la eficiencia del proceso de producción y reducir los plazos de entrega
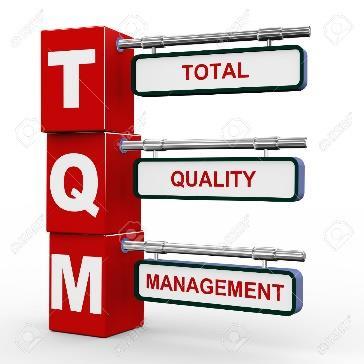
Six Sigma
Six Sigma es un término acuñado por el ingeniero Bill Smith, de Motorola, en la década de los años ochenta. Fue así como la compañía denominó a su propuesta de reducción radical de defectos en los productos. Luego experimentó un nuevo impulso hacia fines del siglo XX, al ser aplicada por General Electric en toda su organización, tanto para la fabricación como para los servicios, logrando espectaculares resultados.
Six Sigma constituye un modelo de gestión de calidad que también se conoce como DMAIC, siglas de las palabras en inglés: define, measure, analyze, improve y control. En español: definir, medir, analizar, mejorar y controlar. Estas son las cinco fases que se han de aplicar en cada proceso. 9
Six sigma utiliza la metodología
DMAIC (Define,
Measure, Analyze, Improve, Control), que consiste en: 10
Definir
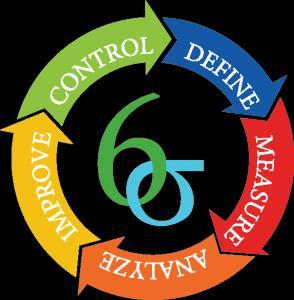
Determinar las principales necesidades de la empresa y los puntos más importantes para la calidad de los procesos involucrados en el negocio.
Medir
Medir y evaluar el desempeño de estos procesos.
Analizar
Estudiar y mapear los datos recogidos, para poder localizar el origen de los problemas en los procesos e identificar oportunidades para mejorarlos.
Mejorar
Optimización de los procesos a través de la implementación de soluciones que sean al mismo tiempo correctivas y preventivas.
Controlar
Acompañar el efecto de las soluciones a corto, medio y largo plazo, por medio del control de rendimiento de los procesos y señalando posibles mejoras adicionales.
Lean manufacturing y Six sigma = Lean Six Sigma
Lean Six Sigma es una combinación de dos métodos potentes de mejora de procesos: Lean y Six Sigma.
Eliminando "Residuos" de un proceso. Residuos es cualquier actividad dentro de un proceso que no se requiere para fabricar un producto o proporcionar un servicio que cumpla con las especificaciones.
Resolviendo problemas causados por un proceso. Los problemas son defectos en un producto o servicio que le cuestan dinero a su organización
Lean es popular por su enfoque metódico para simplificar los procesos de fabricación y servicio al eliminar el desperdicio mientras continúa entregando valor a los clientes.
Six Sigma es simplemente un método para resolver un problema de manera eficiente. El uso de Six Sigma reduce la cantidad de productos defectuosos fabricados o servicios proporcionados, lo que resulta en mayores ingresos y una mayor satisfacción del cliente.

9 Extraído de: https://www.esan.edu.pe/apuntesempresariales/2016/06/la-metodologia-six-sigma/ 10 Extraído de: https://www.heflo.com/es/blog/calidad/metodologia-six-sigma/