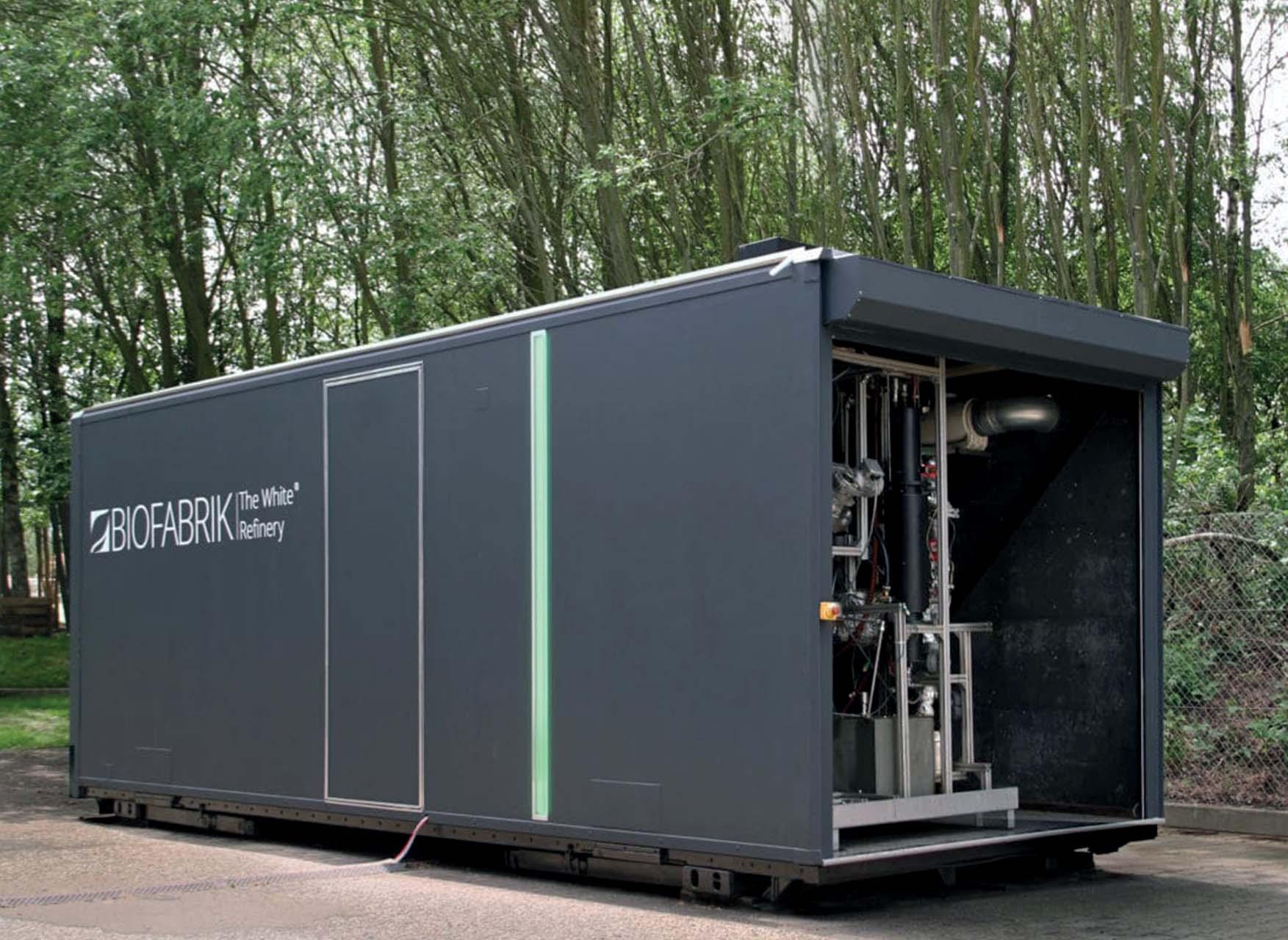
6 minute read
Plastic waste
from CITY:ONE.1.2020.EN
by CityOne
as a source of income for municipalities
OVER 400 MILLION TONS OF PLASTICS ARE PRODUCED ANNUALLY WORLDWIDE, BETWEEN 1950 AND 2015 A TOTAL OF 8.3 BILLION TONS OF PLASTICS WERE PRODUCED, OF WHICH ONLY 9% WERE RECYCLED. NINE MILLION TONS OF PLASTICS OF THIS AMOUNT END UP AT SEA EACH YEAR. BY COMPARISON, THE CHEOPS PYRAMID WEIGHS „ONLY“ 5.97 MILLION TONS. IF NOTHING CHANGES, THERE WILL BE MORE PLASTICS THAN FISH IN THE OCEANS BY 2050.
Advertisement
In addition to the ecological impact, the accumulation of plastic waste, especially packaging, is also an economic and logistical problem for municipalities. In 2018, the European Parliament adopted a resolution collectively entitled the Circular Economy Action Package, which sets out, among other things, the obligation to recycle at least 50% of plastic packaging by 2025 and 55% by 2030. In the Czech Republic, according to EKOKOM sources, about 35% of plastic packaging is currently actually recycled, which is about half of the content of yellow containers. The others end up in landfi lls or, at best, in incinerators. The share of usable PET bottles is up to 30% in yellow containers, foils and other plastics account for about 60%, the rest is made up of non-plastic additives. Plastics other than PET bottles are usually not recycled because there is no demand for them. The situation is worse since China ceased to function as the world‘s dump and banned the import of most plastics.
The validity of our landfi ll law is constantly shifting and changing, but if we start from the current proposal, which the Senate returned to the Chamber of Deputies in November, it counts on a total ban on landfi lling from 2030, when the price of waste will gradually increase from 800 CZK / ton to 1850 CZK / tonne if municipalities exceed the permitted limit per capita. EKOKOM states the average cost for municipalities for the collection of sorted waste is at about CZK 5,000 / ton, but plastic costs much more than glass or paper, for example, due to its low bulk density.
: There is a solution
How to get out of the circle, when municipalities are obliged to ensure the recycling of plastic waste, but there is no interest among processors in it? An interesting solution may be the process of pyrolysis known for centuries. After several promising reports on progress in the fi eld of using pyrolysis for the disposal of diffi cult-to-use plastic waste, there has fi nally been a breakthrough in the practical usability of the pyrolysis unit in normal operation. We took the opportunity to see the fi rst pyrolytic unit (due to the coronavirus epidemic only online) in Kent, England, where it is already operating successfully in commercial operation. The owners named the unit Marie and placed it in Longfi eld near Dartford. Tim StClair – Pearce from the pyrolysis company in South Africa shared with us his practical experience with the use of this technology.
Pyrolysis means the decomposition of the input raw material, in our case HDPE and LDPE plastics, into a liquid usable in the chemical industry, gases and a solid carbon fraction. At high temperatures without access to oxygen, long molecular chains are depolymerized into gas, which in the next process condenses into a liquid and pyrolytic oil. While the gas is collected in
pressure vessels for further energy use; the refi ning industry, such as BASF, ÖMV or Shell is interested in liquid oil, and carbon can be used, for example, in the manufacture of tires. „For every kilogram of plastic waste, 1 litre of oil can be produced, plus 1 kilowatt hour of electricity,“ explains StClair-Pearce.
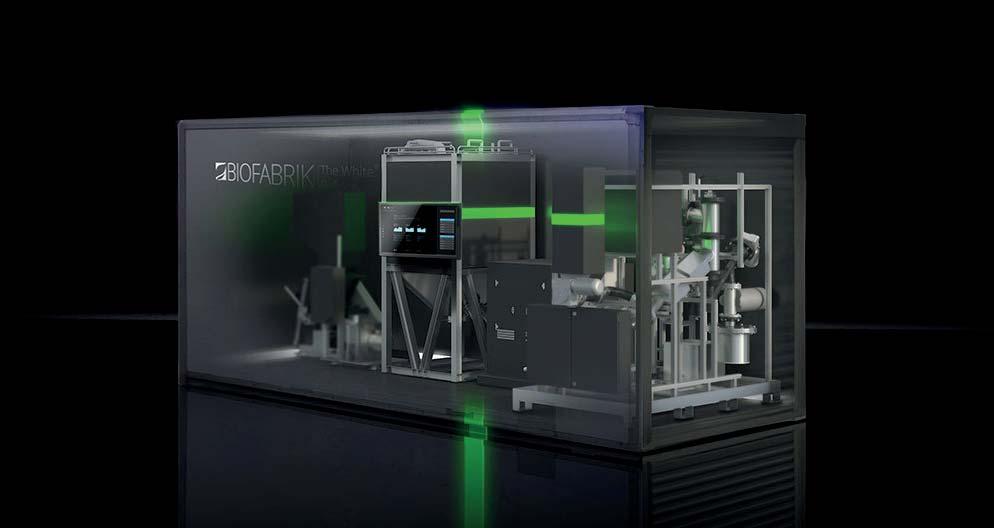
It is a very elegant modular solution, where each unit is installed in its own container, while the number of containers is not theoretically limited. The largest installation is being prepared in Austria, where the customer ordered 16 pyrolytic units with next spring delivery and a capacity of almost half a million litres of oil per month. There are enough input raw materials and the logistics of the oil produced are provided based on a framework contract by the manufacturer.
: How does it work
Each pyrolytic unit in the container has its own shredder, where the sorted plastic waste enters. After shredding, it is fed to an intermediate hopper, from where it is fed directly to the hopper of the pyrolysis unit by pneumatic transport. From there, it is fed into the reactor in the required amount by a screw feeder and melted. In a constant motion, the material is heated in the pyrolysis reactor to a temperature of up to 500 °C, during which depolymerization takes place without the access of oxygen. A gaseous and liquid component is formed together with carbon residues. These are separated in the separator by their own weight, while the gase-
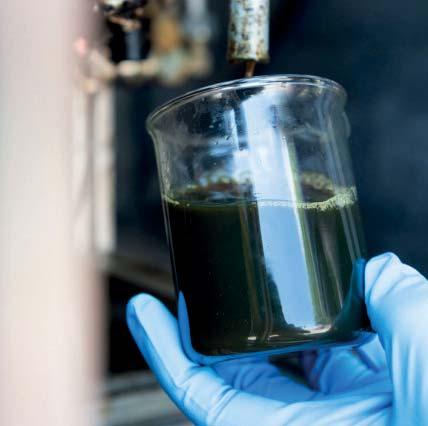
Graph 5: Timeline of treated plastic waste from municipal waste collection system 2008-2016 in %, source: EKO-KOM
PET foil other plastic non plastic mix
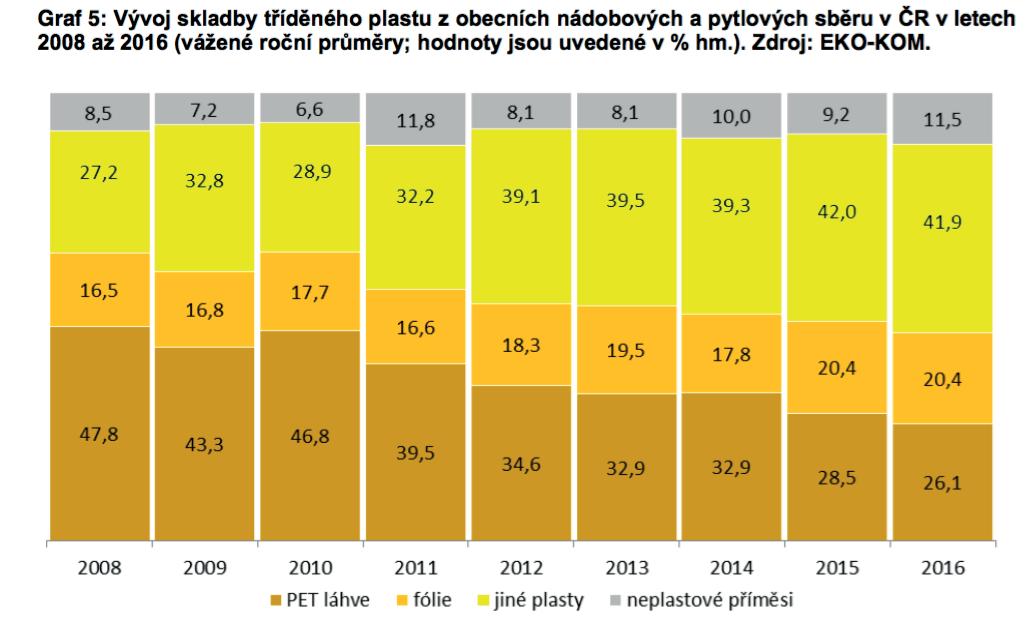
ous and liquid components continue to the condenser. Multi-stage cooling ensures the separation of the liquid component as a fi nal product and the remaining gas is collected in pressure cylinders and ready for further use. Pyrolytic oil is stored in tanks with a capacity of about 28,000 m3 to ensure uninterrupted operation even during loading into tanks. The whole process is fully automated and remotely controlled by a central control room.
: Can we aff ord it?
The vision of Biofabrik founder Oliver Riedel, who manufactures WASTX units, is summed up in one sentence: „We wanted a small, decentralized tablet-controlled device that is profi table and meets European environmental standards.“ After six years of research, he fi nally managed to start mass production, with which he successfully penetrates the markets in Germany, Austria, England, but also in more exotic countries such as Nigeria or Saudi Arabia. The equipment returns the used plastics back to refi neries, in full accordance with the principles of circular economy, where they are used for subsequent chemical production. And what does profi table mean? „The investment in the equipment is not high for its maturity and performance,“ says Jaroslav Hradílek from the company, which provides distribution for the Czech and Slovak markets. One unit with complete accessories and commissioning can be purchased for under three quarters of a million euros with a return, depending on local conditions, within fi ve years. In addition, to reduce the initial investment and spread the risk, the German manufacturer off ers a partner model, where the investment is halved and Biofabrik takes care of all the logistics associated with the sale of the resulting oil. Despite the subsequent license fees for this service, the return on the device has been based for about 4 years. Of course, there is a two-year warranty on the equipment and a contract for service, where trained staff performs both routine maintenance and possible warranty and post-warranty repairs. Thus, the operation of a fully automated device can be handled by short-trained personnel of the operator in the complexity of several hours a week. In the case of a region, city, or association of municipalities, it may be a PPC project, in addition with a guaranteed return for the investor. In this case, it is true that the ECOlogical benefi t can also be ECOnomic. Not to mention solving an almost unsolvable problem – what in the future to do with waste that no one wants?
Pyrolysis is from the Greek pyr (pyros) fi re and lysis release. It is a thermal decomposition of substances without access to oxygen. There is a process of breaking down more complex molecules into simpler hydrocarbons. Historically, it was used to produce charcoal; during World War II, coal fuels were produced in Germany due to a shortage of oil. Recently, we have seen a renewed interest in pyrolysis in the fi eld of biomass processing, municipal waste, and plastics.