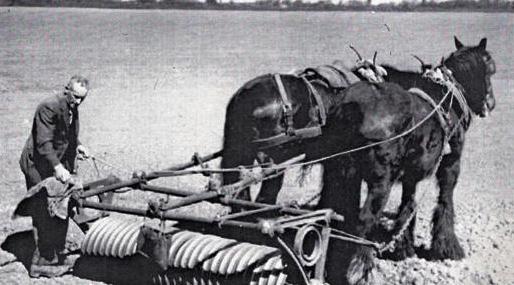
4 minute read
Farming through the years
Farming today is becoming more advanced with the aid of technology. At CLAAS, we are always trying to make our machines perform better and be more eco-friendly.
Today, farming is the most efficient, time-saving and cost-saving as it has ever been but things weren’t always this way...
Advertisement
1940’s
Farming relied heavily on manual work as machines like tractors were too expensive for most farmers. Work was largely done by hand and hand tools with the aid of strong horses, that could pull ploughs. Ploughs turn and break up the soil but also bury old crops and help control weeds.
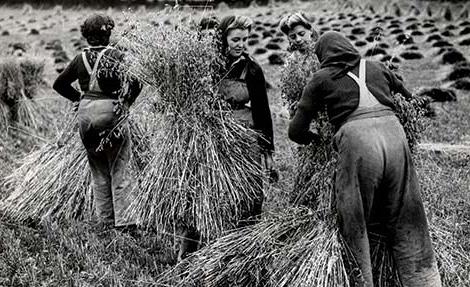
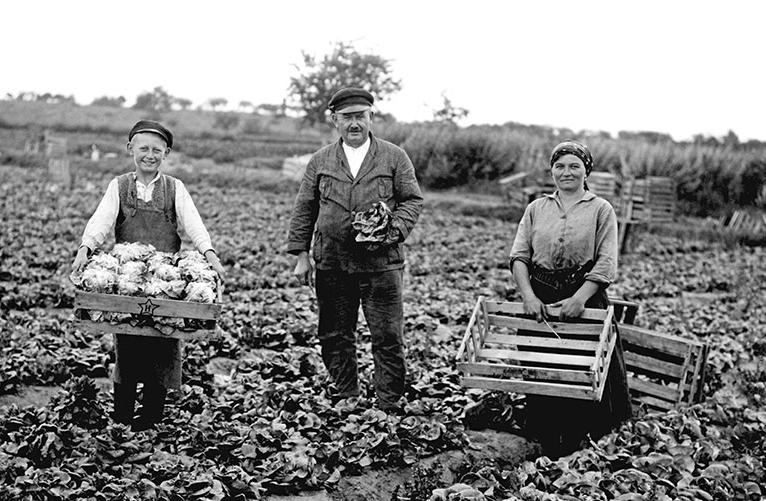
“We are called Land Girls!”
With the rise of the second World War, Britain faced many challenges which included a depletion in the male workforce as men were enlisted for war. This meant that women would help take on men’s jobs (which at the time was unusual!) and carry out the manual work on farms. Tractors with engines were now quite common and were used for most farming jobs.
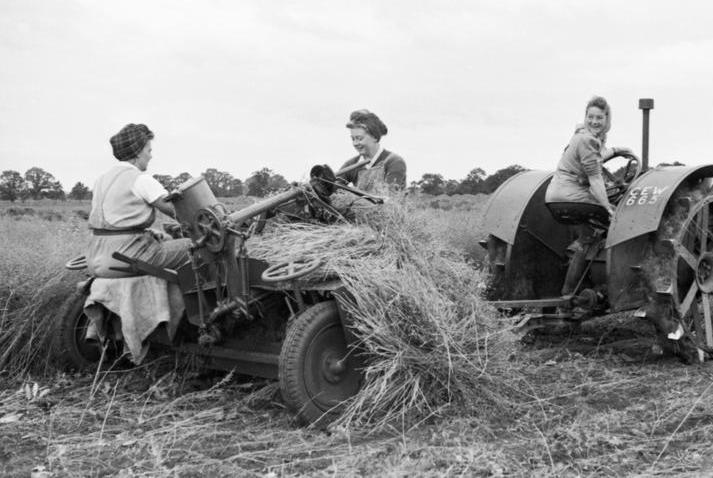
1920’s 1960’s
With a boom in mechanisation, machine manufacturers like CLAAS struggled to cope with demand! Combine harvesters were self-propelled - this meant they had an engine and did not need to be ‘pulled’ by a tractor. This made harvesting much faster, so farmers had more time to spend on other jobs. The business of farming also grew and CLAAS worked on building it’s dealerships and offices for their staff.
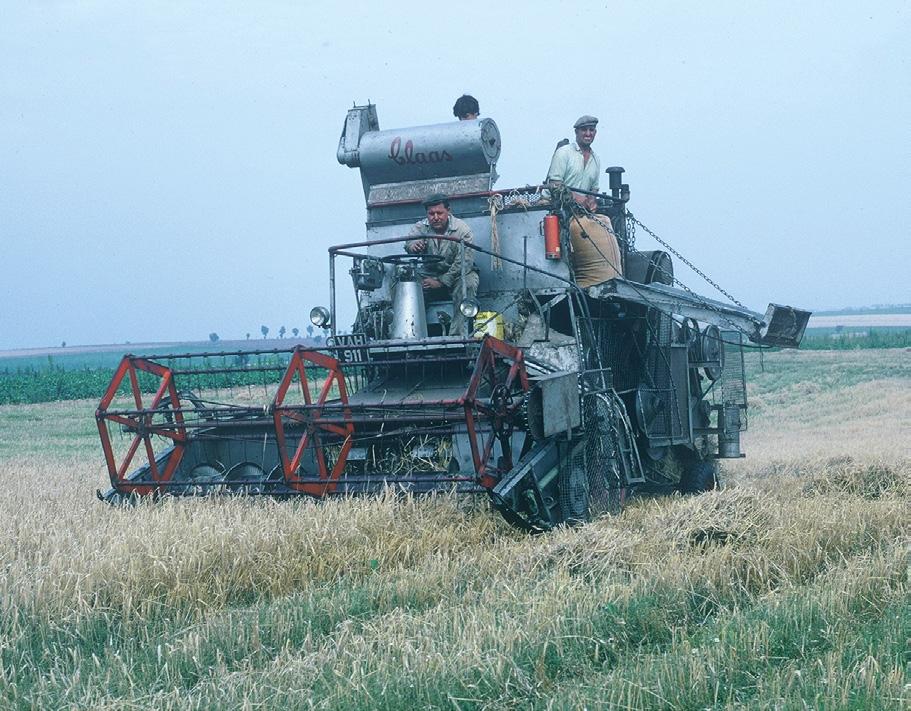
1980’s 2020’s
CLAAS continued to invest in engineering, making farming easier and faster. With more machines being introduced on farms, there was less of a need to have people. Due to the speed at which farmers could harvest crop, it also meant that they could own and work more land - which meant farmers could earn more money. 1984 was a record year for wheat yields - Europe’s wheat levels reached 170 megatonnes which is the same weight as 566 Empire State Buildings!
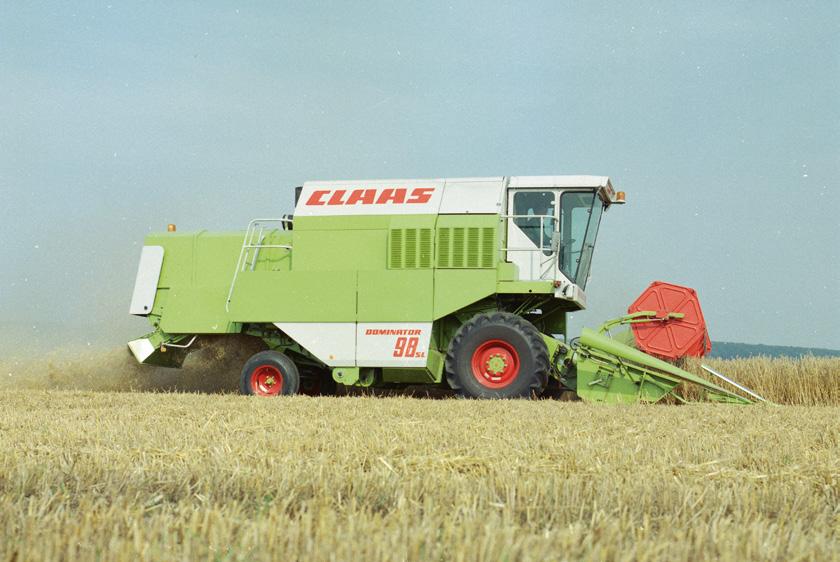
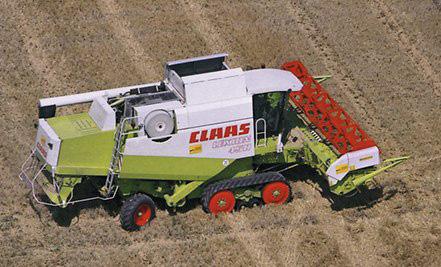
2000’s
Agricultural machines would now typically have an on board computer screen inside the cab to show the driver how the machine was performing. The operator could even control the machine from this screen - for example, they could alter the speed of the cutterbar reel, which affects how fast the crop is entering the machine. Another big evolution was the development of track tyres on agricultural machines, particularly on combine harvesters. Tracks would offer a large surface area, meaning less compaction on the soil, therefore less damage. Tracks can also pull the machine more efficiently in challenging conditions.
Technology has been the driving force of modern engineering efforts. The computer inside a machine is now able to send messages to CLAAS when there is a problem with the machine. The computers also help to drive the machine, so that the driver does not have to do as much work. Using GPS will also guide machines on where to drive to harvest the crop most efficiently. The computer can even help detect soil, moisture and crop quality so the machine can react accordingly!
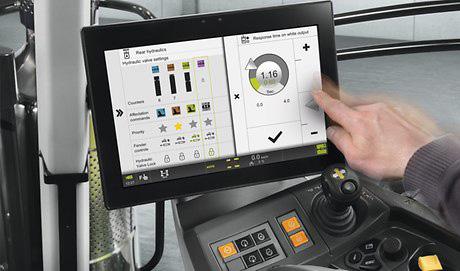

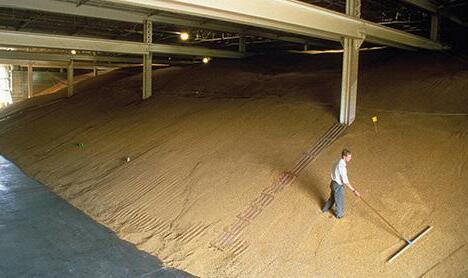

Sheep to Shop
Spring is also a busy time for shearing on the farm. Shearing means to cut, which can be done using a blade shear (which are like big scissors) or using electric clippers (similar to what hairdressers use). By shearing a sheep, the person is cutting off the sheeps coat, which is made of wool. Sheep like having this done as their coats can get very big, hot and heavy - which is quite uncomfortable in the hotter months. Shearing starts in May and can continue right through to July.
Find out below exactly what happens in the wool making process so that the next time you are in a shop, or you are cosying up with your woolly blanket, you will remember how it was made! This is a long process but creates a wonderful and natural material to keep us warm and help us live out our daily lives. Wool can be used for many things such as carpets, curtains and horse rugs (coats)! Wool can also be produced from other animals such as llamas and alpacas.
1. Shearing the sheep
From May onwards, the farmer will start shearing his sheep using a blade shear or electric clippers. Many farmers like to use blade shears as this is the traditional method though electric clippers are the modern choice. The farmer has to gently hold the sheep down to make sure they are shearing safely and do not injure themselves or the sheep.
2. Washing the wool
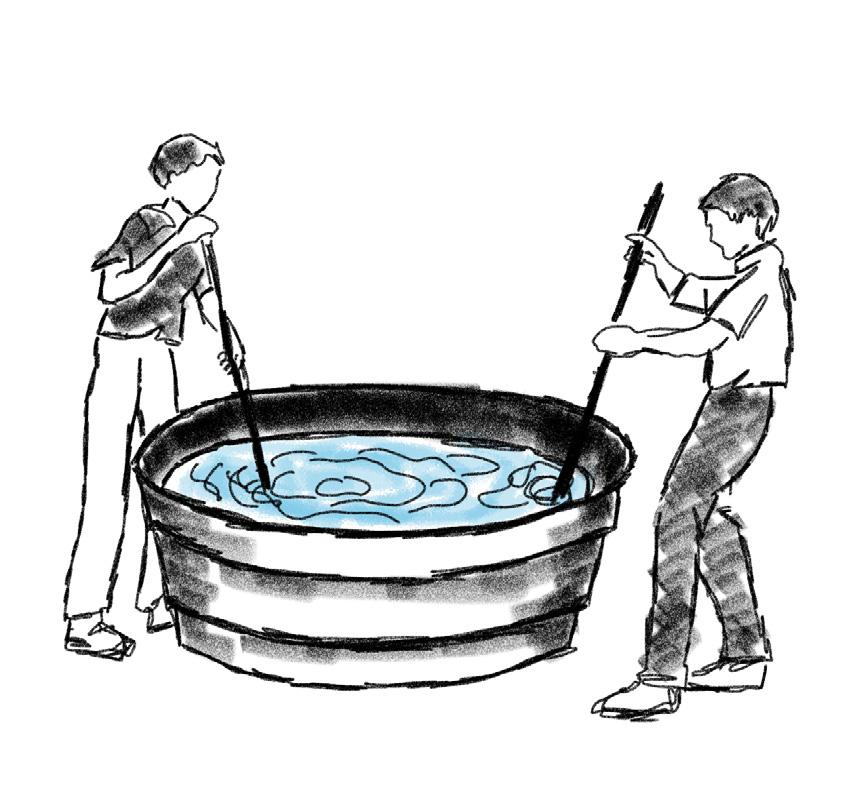
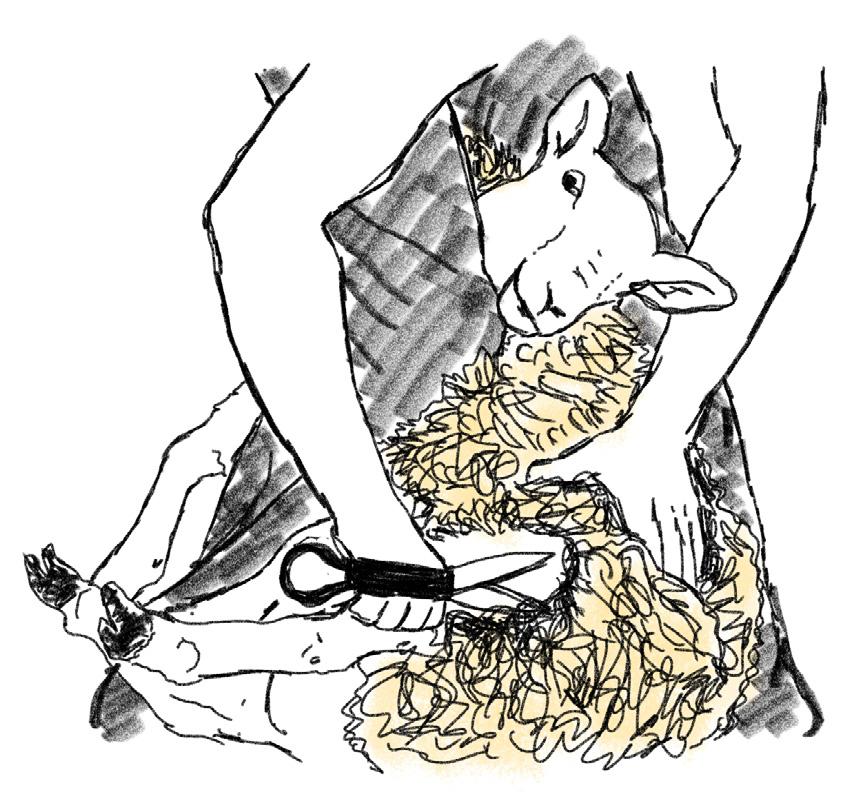
Because sheep are animals that live outside, their woolly coats can be muddy and smelly! So the next stage of the process is to clean the wool using water and soap. This is to clean the wool of dust, dirt and grease that has built up. The wool will now start to become soft and fluffy.
This is also called
3. Combing the wool

This is also called “carding”
The wool is now like big, fluffy clouds which although is nice to touch, is difficult to work with. So, the next stage is to comb the wool so it starts to form a string shape. This can be done with a machine (like the one on the left) or using 2 square combs. Each method uses tiny ‘teeth’ to pull the wool and separate the many strands of wool from each other.
4. Dying the wool
This part of the process is optional, as many people like to use wool in it’s natural colour. However, most wool is dyed which produces beautiful and striking fabrics for clothing, blankets and more! This is a simple task of adding dyes (which can be man-made or natural dyes) to water and soaking the wool.

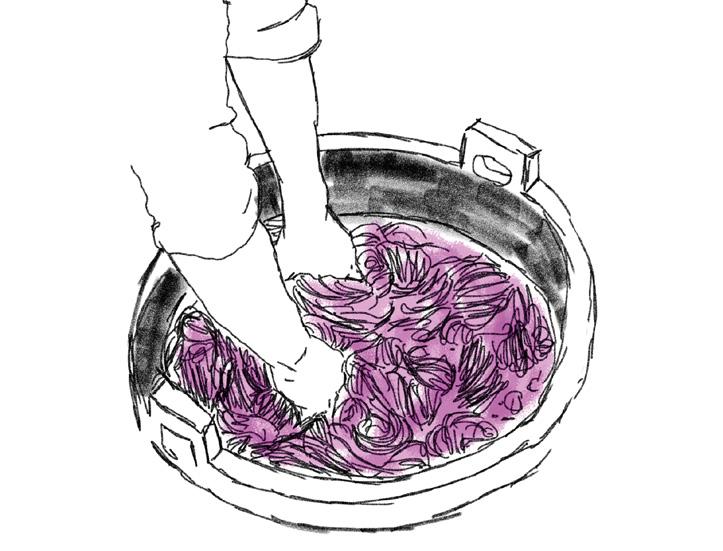
This is also called “spinning”
5. Making the yarn

Like step 2, 3, 4, and 6, this part can be achieved with big machines that don’t need people to work.
Although we have combed (or “carded”) the wool into fluffy strands, it is still too hard to work with. The wool will now be fed into a machine that spins it around. The person using the machine uses their hands to pull back on the wool whilst the machine is pulling in the other directionthis forces the wool to form a tight string. By using less force (pull and speed), the “looser” the yarn will be. Some yarn is loose and some is thin and tight.
6. The final woolly result
The last part is to create something usable with the wool yarn. The yarn on the right is “loose” so it still looks quite fluffy - this would be great for a blanket to keep you warm. Thin yarn would be good to create rugs as it is less likely to be damaged by shoes - this is because it is more compacted. Woolly items can be produced by machines or knitting them by hand!