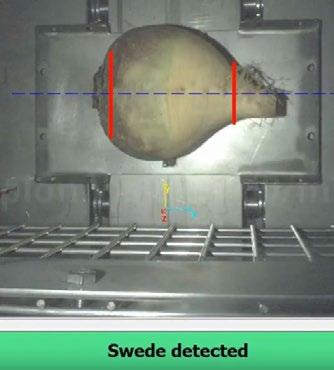
4 minute read
3D IMAGING INTELLIGENT
Paul Wilson, CEO of Scorpion Vision, explains the advantages of intelligent 3D imaging with artificial neural networks in the fresh food packaging industry.
The lack of seasonal workers to pick and pack vegetables and fruit across Europe is acute according to an article in The Food Navigator.
Advertisement
For example, in France it is estimated that up to 800,000 people are needed during the harvest season. Automation systems for harvesting and post-harvest processing can help solve these problems but it is still relatively early days in terms of the existing technological capability available to the horticultural industry.
Automated harvesting of crops in the field is one big challenge that will not be solved overnight. One company that appears to be making good headway in this area is Israeli based FFRobotics, who have developed an apple harvesting solution which they claim works as fast as eight people. However, this system cannot be used to harvest other produce. Nevertheless, it’s a good start and perhaps the technology can be adapted for pears and other tree hanging fruit over time.
Then there is the challenge of preparing the product for packing. This often requires trimming and cutting and is a very labour-intensive task.
The most demanding aspect of automation in food production is the sheer diversity of what the produce might look like and how it is presented. If we consider the automated trimming of root vegetables - top and tailing of leeks for example, then the procedure requires locating the correct cut points without losing too much of the stalk and not undercutting it, so it leaves some of the roots in place. To ensure this is done accurately, it requires an ‘intelligent’ 3D vision system that can analyse the shape of the product to find the optimum cut point.

The cutting coordinates can then be sent to a robot or servos, so that the final trimming can be completed accurately with repeatability - and faster than a human - that only a machine can achieve. The benefits here are not just more optimum trimming but also the ability to scale up production without increasing the reliance on humans. Such is the efficiency of the system it is feasible to realise a return on investment within a few months of the initial capital investment in the system.
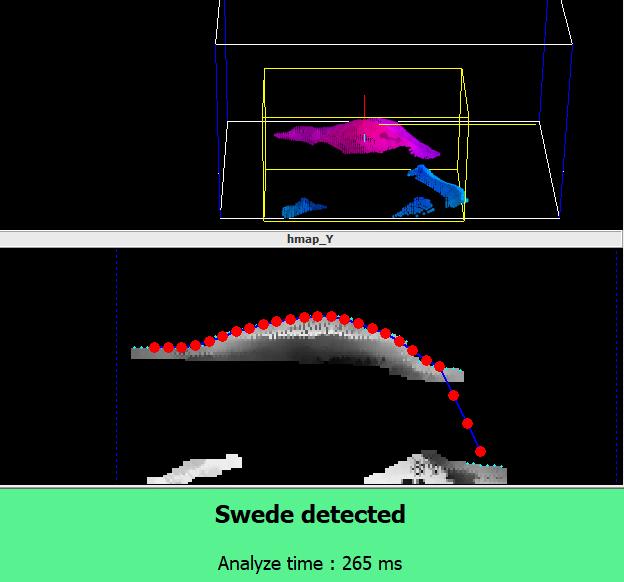
Scorpion Vision has provided the technology to enable mass sorting and processing of freshly harvested fruit and vegetables. Combining 3D imaging with artificial neural networks offers great advantages over classic machine vision. The ability to look at and analyse each individual vegetable, be it leek, carrot, potato, swede or turnip, before making a decision on how to process it. This means humans are no longer a critical part of the process.
Our solution is built around our established 3D camera technology, which is tailored to suit the specific application. It can consist of a stereo vision system using two cameras or optics to create two images, a high-speed 3D scanner or traditional laser triangulation. Typically, though, stereo vision is the technique used for post-harvest processing tasks.
The post-harvest processing system is built around a high performance embedded computer system running Scorpion Vision Software which controls the camera array and integrated light sources - usually random pattern projection in NIR and both white and IR LEDs. Housed in an IP67 rated stainless steel housing, the system is classed as a food safe camera that can be retrofitted to any production line.
The challenges that a machine vision system has to overcome isn’t just in the variability of the product but its condition as well. Taking automated leek trimming as an example, the capital investment will only make sense to the farmer/food processor if the leeks are trimmed with high accuracy. Over-trimming the leek is highly undesirable as, over a period of several hours, that can amount to significant wasted crop. Undercutting it, so that some roots are left attached to the stem is not accepted by some volume customers.

If the vision system simply had to find the point at which the leek stem should end and the roots start, then it would be a straightforward task of shape measurement, but leeks come with mud and debris attached. In many cases, leaves have been stripped from the stem and cover the root completely. So, using standard 2D machine vision will not achieve the desired level of accuracy. A more sophisticated inspection method is required and this is where 3D stereo vision, enhanced with a neural network based algorithm comes into its own.

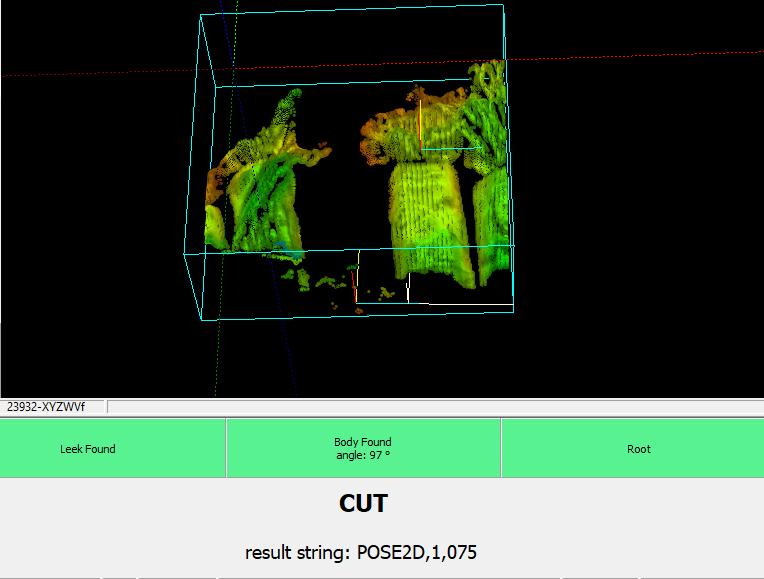

The point from when the camera is installed to the point at which it is performing at 99 per cent cutting accuracy can take several weeks. This consists of several phases of image acquisition where thousands of images are collected and analysed and run through a Scorpion Vision Benchmarking tool that identifies the weaknesses. If a Neural Network is being used, the data is used to train the software with thousands of images.
The same process can be applied to other vegetables and Scorpion Vision - with their robotics partners - have built systems to also trim swedes and sprouts. Accuracy performance is in the millimetre, which, when you are trimming a leek is critical to the machine’s success. MV