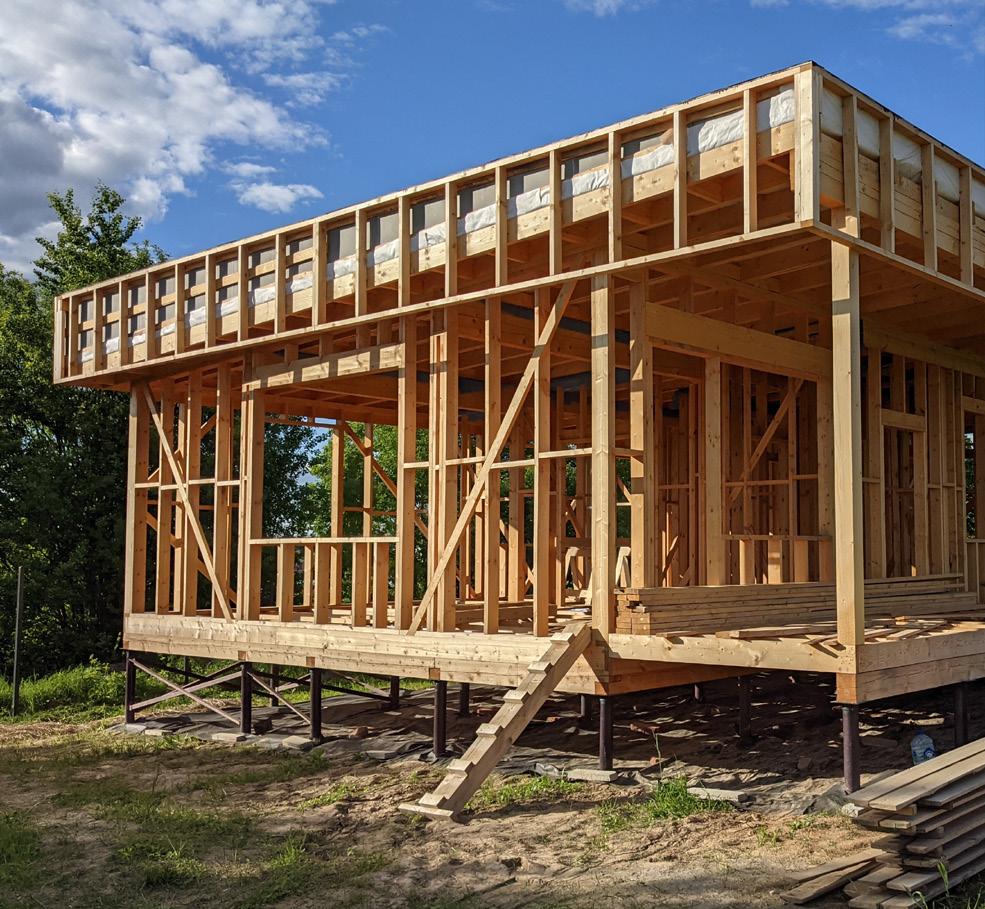
6 minute read
Construction Costs & Supply Shortages
(SUPPLY) CHAIN OF FOOLS & THE NEWS FOR HOMEBUYERS
Construction Costs & Supply Shortages
Many words in our COVID vocabulary have dwindled, however, supply chain is and will continue to be pervasive for the months to come. For those of you who somehow haven’t been affected by this system, the supply chain is the process our society has created to get goods from production to our front doors. Computer parts, refrigerators, furniture, toilet paper, and even soy sauce have all been affected in the past year and a half and magnified by COVID-related disruptions.
In addition to the scarcity of resale home inventory, inventory overall has been negatively impacted by the construction industry’s challenges in building new homes. Sourcing and affording building materials has hit the building industry hard, slowing the construction of much-needed new inventory for homebuyers. Building materials aside, finding qualified labor to build the homes is an ongoing issue as well, one that predates but has been made worse by the pandemic.
And at the very end of the supply chain, you will find REALTORS® and their clients. “With supply chain delays and shortages, builders just cannot build fast enough,” said Aurora REALTOR® Sunny Banka. “Resale homes in the 80019 ZIP code of Aurora boasts at least a 15% increase with the median price of $542,000. Due to the costs of lumber, labor, and materials, new home prices have risen at a much faster rate.
The main delays for new home construction are finding the materials and the labor. The media has touted increases in lumber prices by 300 percent, but there are many other building materials that have seen up to 50% price increases: In June 2021, this included steel mill products, building paper, asphalt, and plastic pipe. Fertilizer; laminated veneer lumber; resin and plastics; metal joists and rebar; wood windows and doors; and copper pipe were up 40%. Overall, buyers are paying about 30% more for new homes, mostly because these materials are hard to source, according to Ted Leighty, CEO for the Colorado Home Builders Association.
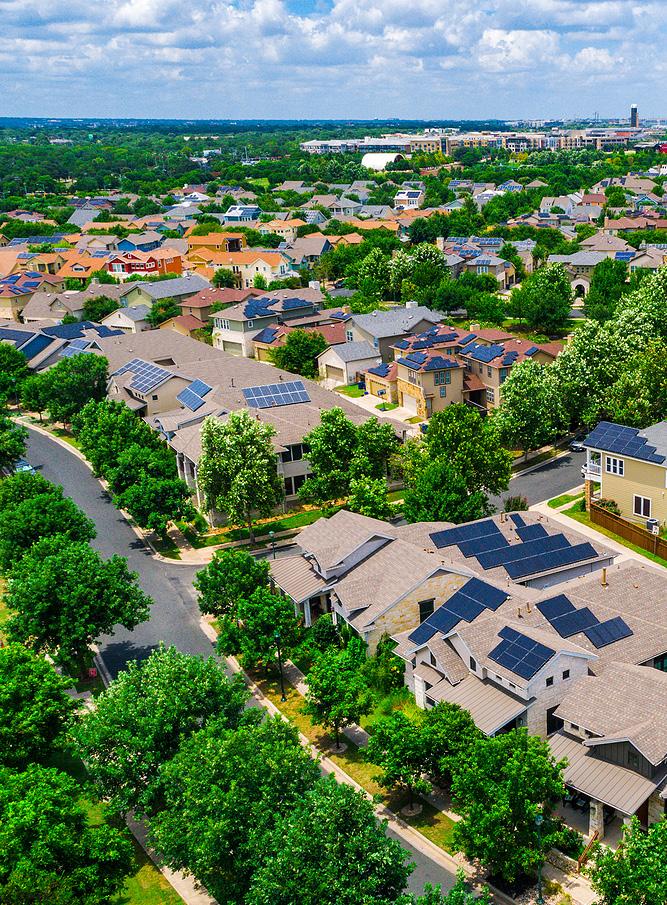
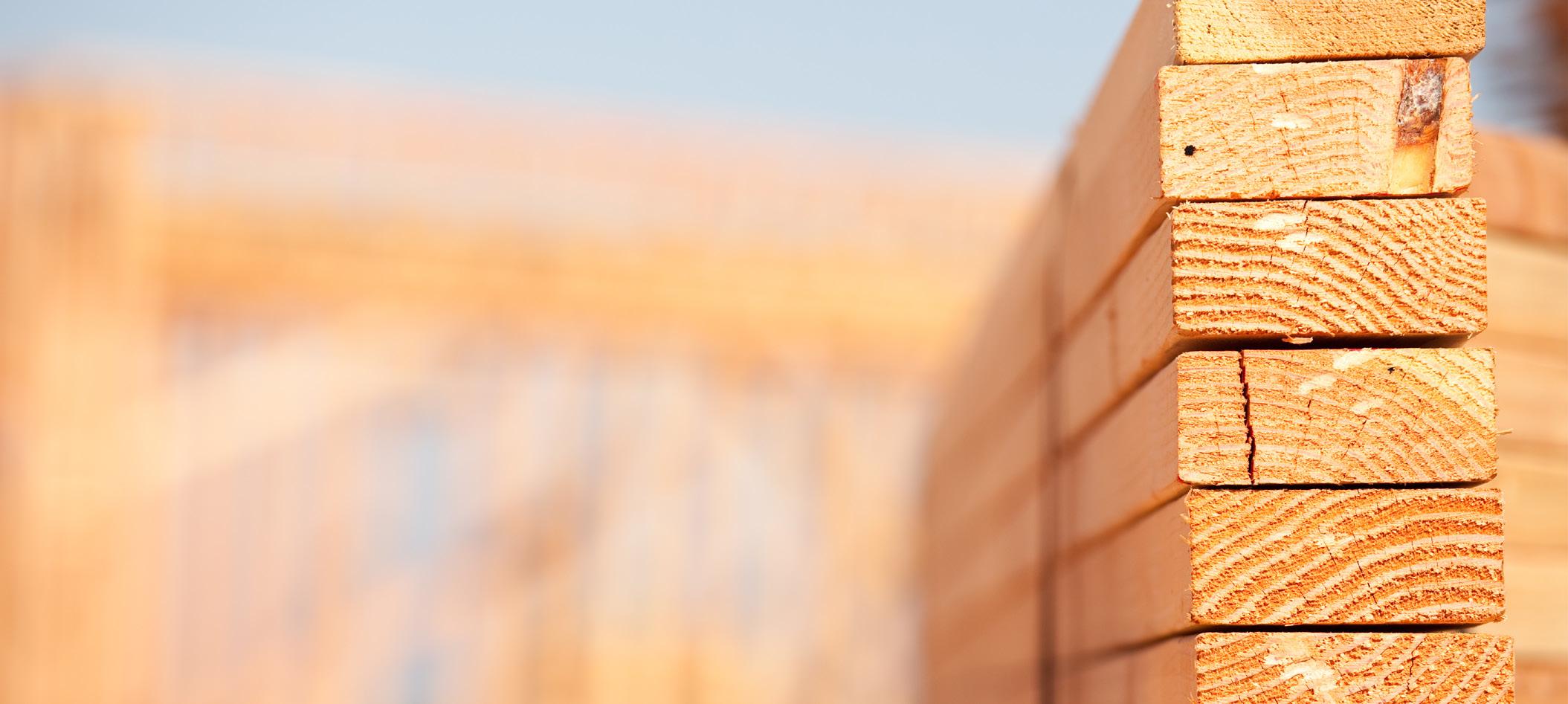
CAUSES AND EFFECTS
But what exactly is causing the shortages and delays? Unfortunately, the answers are stacked precariously on top of each other.
“As a country, we have relied on Canadian forest lumber whose supply has diminished in recent years,” said Tony Uphoff, president and CEO of Thomas, which provides analysis and tools that reflect the buying process. “Part of the problem is also due to tariffs going up, which resulted in further withering demand in the U.S. due to the increased prices. As a result, Canadian mills began to shut down locations to protect themselves against lost revenue,” he says.
He goes on to mention that when we entered the early stage of the pandemic, people working from home wanted more space and took on DIY projects. Uphoff explains, “this exacerbated the demand on an already fragile lumber supply chain, which drove prices to an all-time high.”
Steel is another building material feeding the impact. The price of steel went up to 215% in June when compared to last year, according to Fortune magazine, and is also subjected to tariffs in China. Even with these 25 percent tariffs, importing steel is still less expensive that producing it in the United States. Prices are now plunging due to a decreasing seasonal demand from the construction and automobile industries.
Asphalt, also up about 50% in price, is impacted mostly due to that old economic principle of supply and demand. In a recent report, UP.com said that during the pandemic, people weren’t driving as much, which resulted in lower gas prices, and thusly, lower taxes generated. The tax on gas is how the US funds road repairs with asphalt. Since people drove less, the price for gas decreased and in turn, created a lower production of asphalt. Now that people are driving more and using more gas, the U.S. is doubling down on efforts to update its infrastructure, since most of our roads and bridges are declining.
One more common problem is finding enough of the materials needed for building. For example, Bloomberg.com reports that aluminum products are hard to find because of shortages of magnesium found naturally in mines, as magnesium is used to help cure the alloys in aluminum. The US mostly imports magnesium from China, which brings us right back to our country’s trade policies and taxes.
Although finding these materials on American soil is rebounding, the labor required for manufacturing is not. Hiring workers in the industry has been difficult for some time, though numbers in that sector are trending up. Jobs in the construction trade are also up, according to the US Bureau of Labor and Statistics report about jobs. Construction employment rose by 44,000 in October, following an increase of 30,000 in September. In October, employment increased in nonresidential specialty trade contractors (+19,000) and in heavy and civil engineering construction (+12,000). However, construction employment is still 150,000 workers below its February 2020 levels.
Immigration restrictions in the US have piled on top of an already dwindling population of Americans who are willing to go into the trades, such as construction, plumbing, HVAC, and electrical trades. The work Visa application process is complicated and residency lengths are too short.
“True Immigration reform with funding and workforce development programming are the keys to finding a sustainable workforce in the construction industry,” said Leighty.
WHAT’S A REALTOR® TO DO?
Time to put on those creative hats and open clients’ minds to new possibilities.
In CAR’s November Market Trends report, Brighton REALTOR® Jody Malone says new home builder sites are making some changes in how they sell. “I have visited multiple new home builder sites and was pleasantly surprised when buyers are offered choices of homes that are in different stages of completion. Many builders try to push to get their homes under contract before the end of the year.”
Some builders suggest advising clients to consider building on to their current smaller home, trying custom building with reduced square footage, using different materials for building, and purchasing spec or prefabricated homes.
Some companies are innovating around new types of “prefab” homes. A new company called Stackhouse is taking refurbishing shipping containers and “stacking” them into high-rises that allow for amenities like parking and gyms. The homes can be moved around the country to other Stackhouse sites. Is it time for some consumers to revisit the historic affordability of townhomes and condos? Unlike the single-family home market, there was a little seasonal slowdown in the condominium and townhome market in Fort Collins, where the October median sales price was a reasonably attainable $350,000. “With so few single-family homes available below the median price, median-income buyers are turning in greater numbers to condos and townhomes where the affordability ratio is at 114%, which relieves a bit of the financial pressure of home ownership,” said Fort Collins-area REALTOR® Chris Hardy.”
For now, the struggles for homebuyers continues. One piece of advice from Leighty for REALTORS®: “Tell new construction homebuyers to have patience. Their house will be delivered but there could be delays in getting it finished. Builders are being very cautious about setting realistic expectations for construction schedules.”
Sources: Bloomberg.com, CAR Market Trends, October 2021, Channel 7 Meghan Lopez, Grand Junction Sentinel, Colorado Association of Home Builders, Reuters, Up.com, and US Bureau of Labor and Statistics.
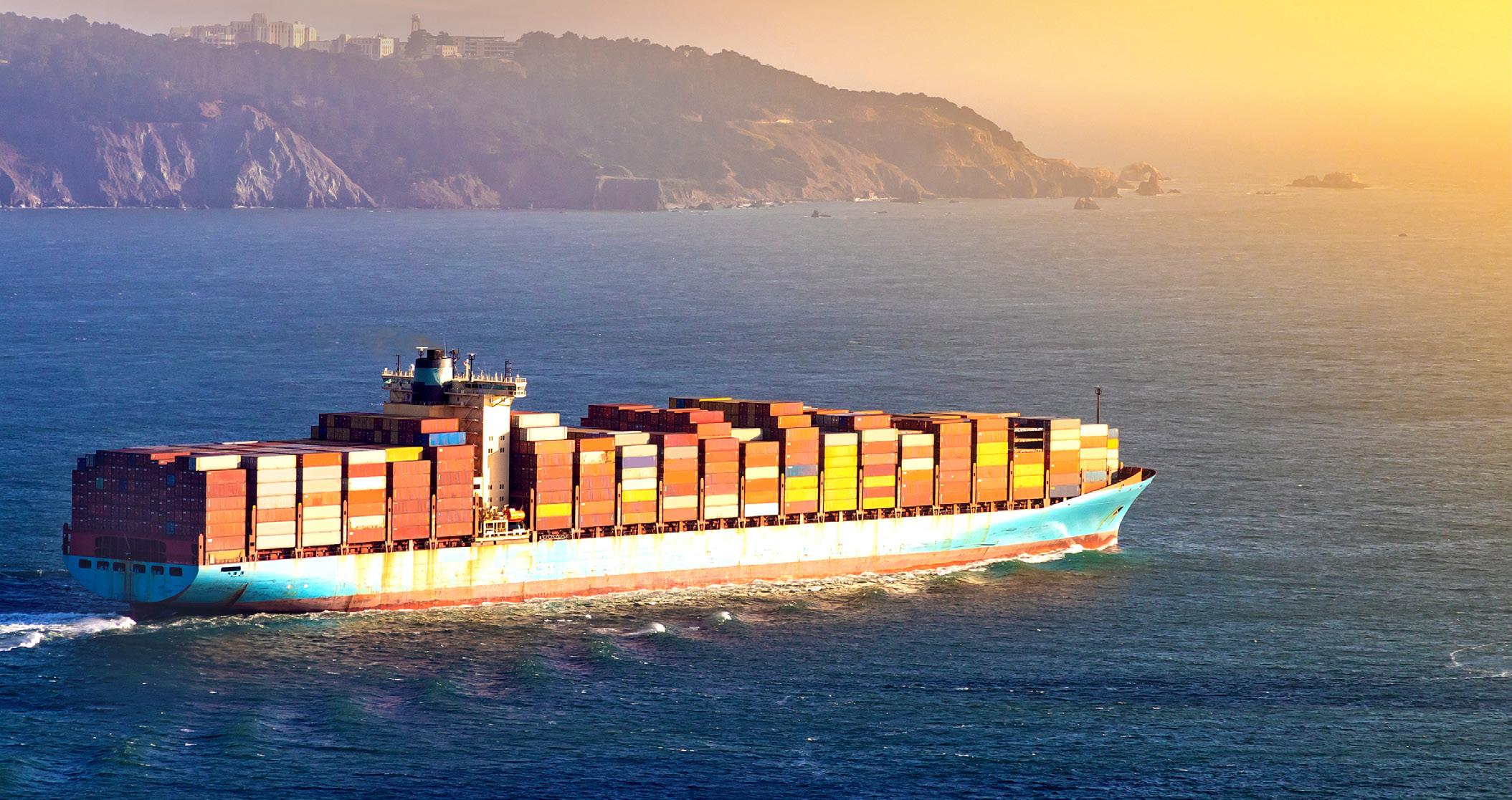

