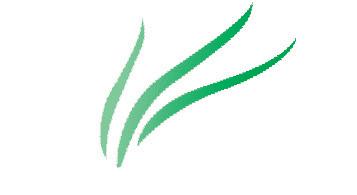
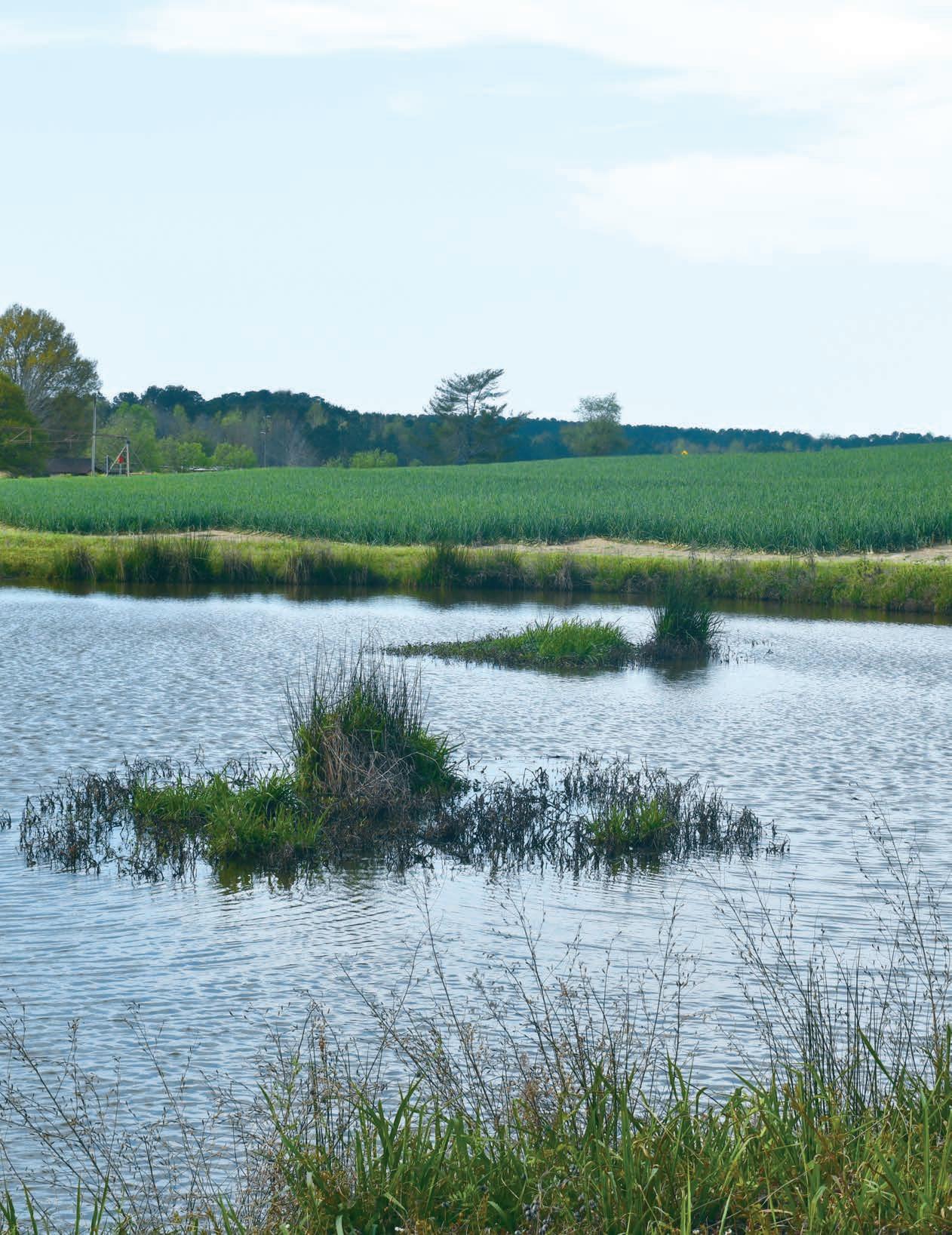


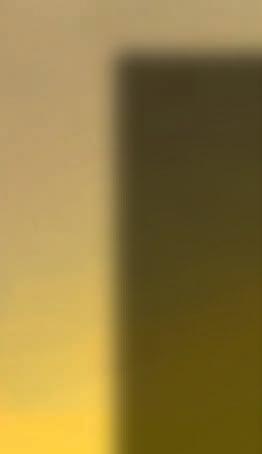

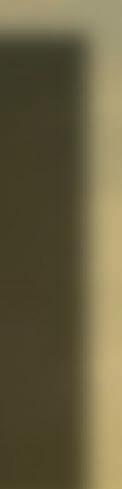

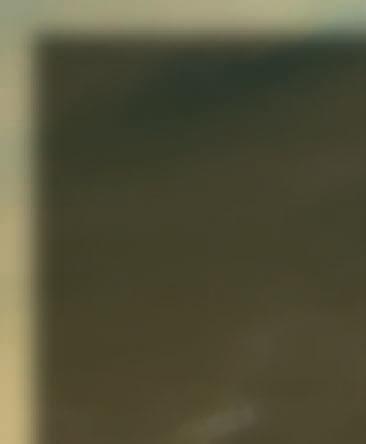
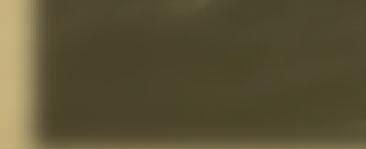


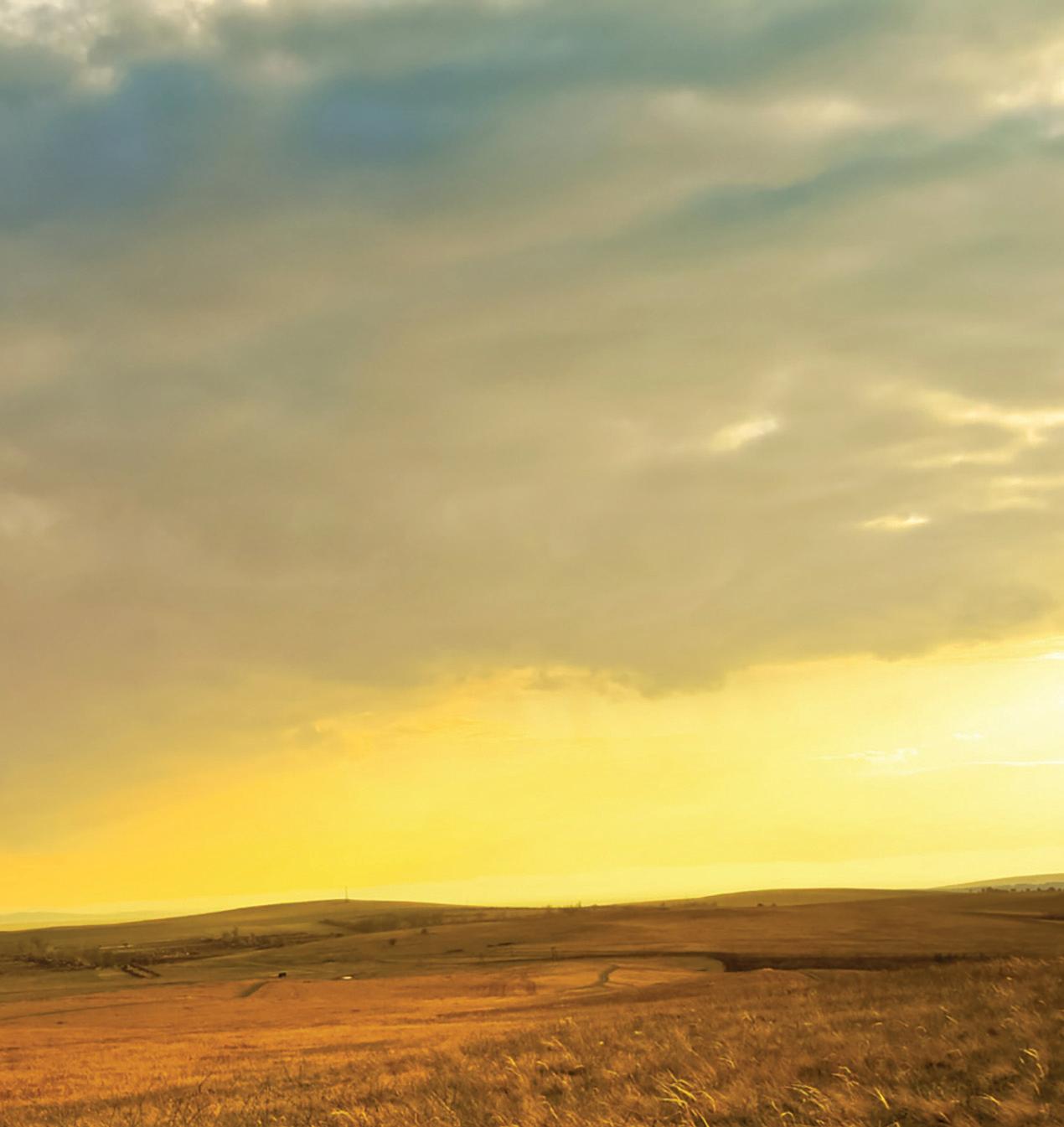

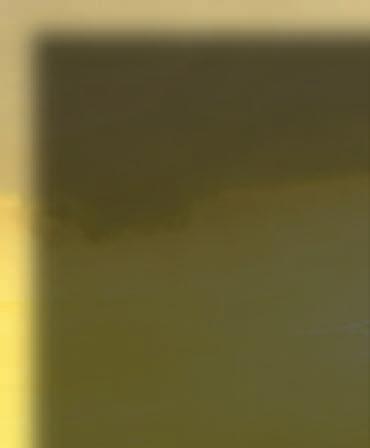

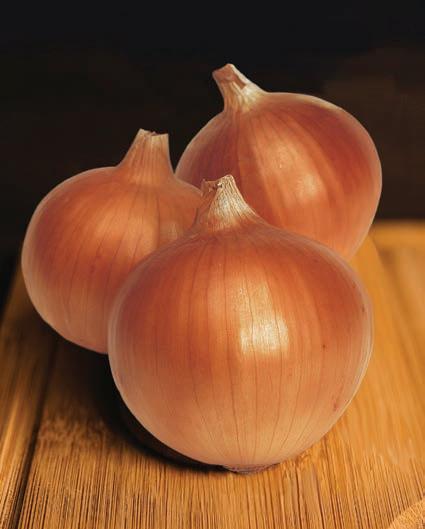
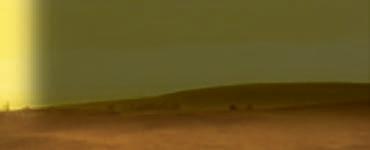
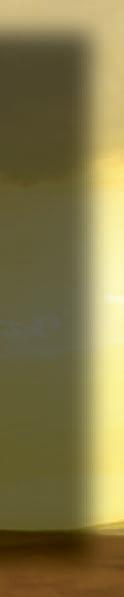
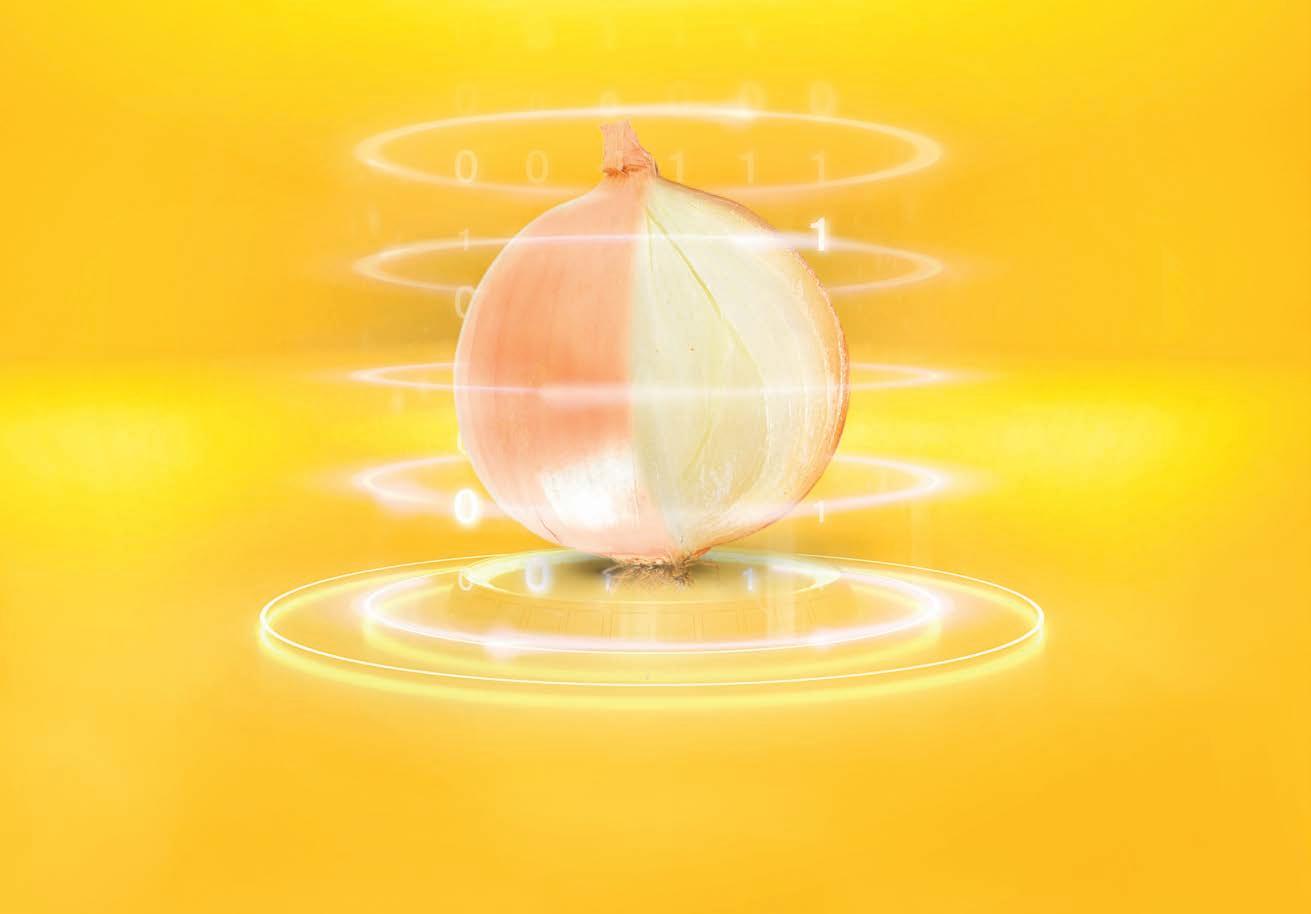
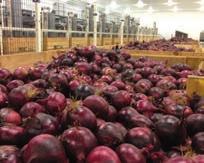
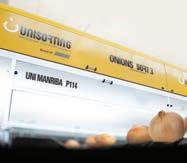

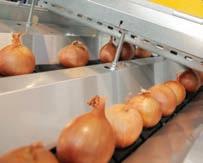

PO Box 333 Roberts, Idaho 83444
Telephone: (208) 520-6461
Circulation: (503) 724-3581
OnionWorld.net
OnIOn WOrld COntaCts
Editor Denise Keller editor@ColumbiaMediaGroup.com
Publisher / advertising Manager
Dave Alexander dave@ColumbiaMediaGroup.com
director of Operations
Brian Feist brian@ColumbiaMediaGroup.com
EdItOrIal InFOrMatIOn
Onion World is interested in newsworthy material related to onion production and marketing. Contributions from all segments of the industry are welcome. Submit news releases, new product submissions, stories and photos via email to: editor@ColumbiaMediaGroup.com, or call (509) 697-9436.
adVErtIsInG salEs
For information on rates, mechanics, deadlines, list rental, direct mail, inserts or other information, call (208) 520-6461 or email: dave@onionworld.net
sUBsCrIPtIOns
U.S. $24 per year
Canada $40 per year
Foreign $80 per year
subscribe online at: www.OnionWorld.net/subscribe or call (503) 724-3581.
Email address changes/corrections to brian@ColumbiaMediaGroup.com or mail to:
Onion World PO Box 333 Roberts, ID 83444
Onion World magazine (ISSN 0892-578X), is published eight times a year and mailed under a standard rate mailing permit at Idaho Falls, Idaho and at additional mailing offices.
Produced by Columbia Media Group PO Box 333, roberts, Id, 83444. Copyright 2024. all rights reserved.
No part of this publication may be reproduced or transmitted in any form or by any means, electronic or mechanical, for any purpose without the express written permission of Columbia Media Group.
For information on reprints call (208) 520-6461.
| Nunhems experts are committed to providing you with support and guidance when and where you need it
Individual results may vary. Nunhems USA, Inc. (“Nunhems”) strives to provide accurate and complete information, descriptions, content, illustrations, images, and data (“Information”) on its websites, social media sites/posts, and printed materials (“Publications”) as such Information is reasonably available to Nunhems at time of compilation. When the Information is based on experiences with tests, trials, or practices, such Information is provided by Nunhems as closely as commercially possible to such experiences. Information may also be based on general observations. However, Nunhems cannot guarantee the Information in any form whatsoever; therefore, the Information is provided on an ‘AS IS’ basis and without any guarantee, either express or implied, including, without limitation, that the Information is accurate or complete. Under no circumstances is the Information to be considered as advice or as a recommendation. Buyer is solely responsible for seed selection and purchasing decisions, including whether to rely upon the Information and for determining suitability of the seed for the intended growth and use under buyer’s local conditions.
The Publications are intended to help buyer identify plant diseases that may or could affect his/her crops. The images may give a distorted image of reality and may otherwise not be an accurate portrayal of the disease.
©Nunhems USA, Inc. 2024. All rights reserved.
By Ali Montazar, Irrigation and Water Management Advisor, University of California Cooperative Extension
Given the essential role that sustainability and conservation play in successful farming today, the agriculture industry continues to search for ways to do more with less. A recent three-year research project in California is making a case for drip irrigation in desert processing onion production, with results suggesting benefits including water, nitrogen and energy savings.
Processing onions are produced throughout California with main production areas in Imperial, Kern, Fresno, Siskiyou and Modoc counties. In the Imperial Valley, a significant increase of acreage has occurred over the last decade, increasing from nearly 4,500 acres in 2013 to 14,500 acres in 2022.
Growers use different irrigation practices of furrow, subsurface drip and solid-set sprinkler to produce processing onions in the low desert. It is estimated that nearly 40 percent of desert processing onions are currently under sprinkler and drip irrigation. A University of California study aimed to evaluate the impact of the common irrigation practices on water, nitrogen and energy productivity in desert processing onion cropping systems (Fig. 1).
The experiment was carried out in 15 commercial fields, including six fields under subsurface drip irrigation, six fields under solid-set sprinkler irrigation and three furrow-irrigated fields in the Imperial Valley over three crop seasons (2020-21, 2021-22, 2022-23). All fields consisted of 40-inch beds with six plant rows per bed with a spacing of 2.5 inches between planting lines. The driplines were installed in the center of beds at an average depth of 1.5 inches. The experimental fields were typically planted from early October to mid-November and harvested from late April to early June. The fields had a variable soil type with predominate soil texture from fine sandy to silty clay loam. Water, nitrogen and energy used; bulb weights; soil moisture; soil nitrate and soil salinity were monitored in each trial field.
A wide range of seasonal irrigation water applied was observed across the experimental sites (Fig. 2). Irrigation water applied varied from 3.3 ac-ft/ac in a drip-irrigated field (field D6) to 7.2 ac-ft/ac in a furrow-irrigated field (field F3). The average seasonal water applied was 3.9 ac-ft/ac for the drip fields, 4.6 ac-ft/ac for the sprinkler fields and 6.4 ac-ft/ac for the furrowirrigated fields. In other words, an average water conservation of 0.7 ac-ft/ac (~19 percent) and 2.5 ac-ft/ac (~60 percent) could be expected from converting sprinkler and furrow irrigation to drip irrigation in desert processing onions, respectively.
BAC
Figure 3. Irrigation water productivity in the experimental fields. Fields D1-D6, S1-S6 and F1-F3 were drip, sprinkler and furrow irrigated, respectively. The bars demonstrate standard deviation values.
The irrigation water productivity, as the ratio of onion bulb weights to irrigation water applied, was calculated for each site (Fig. 3). A maximum and minimum water productivity of 6.4 and 2.5 t/ac-ft was found for processing onions across the experimental sites. A 14 percent greater water productivity was obtained for the drip-irrigated fields (4.9 t/ac-ft) than the sprinkler- (4.3 t/ac-ft) and the furrow- (2.7 t/ac-ft) irrigated fields. Negligible difference of bulb weights at harvest was observed between the two field categories of drip and sprinkler. Sites D1 and D6 were partially salt-affected, and their yield production could be impacted by salinity.
A wide range of nitrogen (N) application rates was observed across the trial fields, varying from 183 to 275 lbs./acre. N application rate was averagely 16.1 percent (in fields under sprinkler) and 40.4 percent (in fields under furrow) greater than the drip fields.
The nitrogen productivity was computed for each of the experimental fields as the ratio of onion bulb weights to N applied. The results demonstrated that the mean N productivity was greater at the drip-irrigated fields, averagely 13.1 percent greater than the sprinkler- and 50.5 percent greater than the furrow-irrigated fields (Fig. 4).
Figure 4. Nitogen productivity (ton of onion bulb weights harvested per pound of N units applied). Fields D1-D6, S1-S6 and F1-F3 were drip, sprinkler and furrow irrigated, respectively. The bars demonstrate standard deviation values.
Reducing energy consumption may reduce greenhouse gas emissions from an environmental aspect and energy costs from an economic aspect. While no energy is typically used for gravity furrow-irrigated fields, energy cost is one of the considerable components of production costs in pressurized irrigation systems. In the desert, growers typically use onfarm portable diesel pump stations for both drip and solid-set sprinkler irrigation systems (Fig. 5).
An analysis was conducted to evaluate energy consumption and productivity in the experimental fields of D4-D6 and S3-S6. The average fuel consumption varied from 87.3 to 118.2 gal/ac
(with an average of 99.5 gal/ac) for the sprinkler-irrigated fields and ranged between 65.4 and 92.1 gal/ac (with an average of 78.3 gal/ac) for the drip-irrigated fields.
The energy productivity, as the ratio of onion bulb weights to diesel fuel used, was determined for these sites (Fig. 6). The results illustrated greater energy productivity values in the drip fields compared with the sprinkler fields. Averagely, this measure was 26.3 percent higher for the drip fields (0.24 t/gal and 0.19 t/gal in the drip and sprinkler fields, respectively).
Irrigation practice has a clear impact on resource use efficiency and water, nitrogen and energy productivity in desert processing onions. An average water conservation of 0.7 and 2.5 ac-ft/ac could be expected from converting solid-set sprinkler and furrow irrigation, respectively, to subsurface drip irrigation. Energy productivity of the onion fields under drip was averagely 26.3 percent greater than the fields under sprinkler.
Subsurface drip irrigation could cause salinity impacts on the topsoil. More frequent light irrigation events can be considered as a tool to manage salinity within the season. Summer salt leaching is a common practice in the desert region, which is highly recommend in drip-irrigated onion fields.
Greater water, nitrogen and energy productivity values could be considered as effective tools to increase net benefits of farming, along with enhancing efficiency as the main pathway to reduce the environmental risk in agricultural production.
Author’s note: Funding for this study was made possible by the California Garlic and Onion Research Advisory Board. I gratefully acknowledge the cooperating farms for their sincere collaborations during this study and for allowing the research staff to implement the project in their agricultural operations.
Figure 6. Energy productivity values (ton of onion bulb weights harvested per gallon of diesel fuel used) determined for the experimental fields. Fields D4-D6 were drip irrigated, and S3-S6 were sprinkler irrigated.
By Molly Sears, Assistant Professor, Michigan State University
Drought is a major source of production risk in agriculture across the United States. Dry conditions can decrease planted or harvested acreage, reduce crop yields and livestock productivity, and increase expenses. Even places that usually get enough rain can face regular droughts. According to the USDA’s Economic Research Service, areas at high risk for drought experience one month of severe, extreme or exceptional drought once every two to three growing seasons. In places with less risk, drought occurs every five to six growing seasons. When drought hits, producers deal with many challenges beyond their control, such as the weather, access to water for irrigation, and how much water the soil can hold. But producers have options: installing or improving irrigation systems, changing how to manage their land to hold more water or switching to drought-tolerant crops. While increasing irrigation is the most likely to benefit crops in the short term, producers deciding to irrigate face
several challenges, such as figuring out if it’s profitable, getting access to water rights and dealing with less water during droughts.
While only 20 percent of agricultural land in the United States is irrigated, 54 percent of total U.S. crop sales are from irrigated acres. The use of irrigation has increased rapidly. From 1997 to 2017, irrigated acreage increased by 1.7 million acres, reaching over 58 million acres in total. While this is good news for agricultural producers looking to reduce risk and increase crop yields, it also comes at a cost: 42 percent of U.S. freshwater withdrawals were from irrigated agriculture. As shown in Fig. 1, this change in irrigated area is not the same everywhere. Irrigated agriculture is increasing significantly in areas with plenty of water, especially in the Mississippi Delta, eastern Nebraska and the Great Lakes. While irrigation is still increasing in parts of the western U.S., other areas have seen a decline, including the Texas panhandle and
California’s Central Valley.
These changes make sense because irrigation was first adopted in the West where crops needed irrigation water in order to be profitable. As irrigation equipment has gotten less expensive, the places where irrigation investment is profitable has expanded eastward. In the East, investment has rapidly occurred in areas with stable water resources and sandy soil. In the West, where the best land has mostly been irrigated already, growth has slowed down.
Another major factor in how irrigation works is water rights and how they influence a farmer’s ability to get water. In the West, most surface water is governed by prior appropriation doctrine. Prior appropriation is often referred to as “first in time, first in right.” This means that people who applied for water permits the earliest have the first priority for water. In areas where water is scarce, applying for a new water permit might not guarantee access to water. If all other users have their permits filled first, then
there may not be enough water left to fill new water users’ needs.
In the eastern U.S., surface water is largely governed by riparian rights doctrine. If land is next to a body of water, that land has full access to that water. This does require coordination across all water users; no water user can use so much water that others may not have “enough” (how much is “enough” varies across states). This means that new surface water users can apply for irrigation relatively easily. However, in times of drought, riparian rights can lead to complicated negotiations that prior appropriation doctrine avoids.
As irrigation equipment becomes more efficient and less expensive, and as droughts happen more often, more farmers will want to use irrigation. From what we see now, it is likely that this growth will be faster in the eastern United States. While there are more water resources available in the East, this could lead to a need for increased coordination across agricultural producers in order to ensure that all water users have sufficient water in times of drought.
Aug. 27
Crookham Onion showcase
Wilder, Idaho Crookham Company, (208) 459-7451
Aug. 28
Malheur Experiment station Onion Variety day
Malheur Experiment Station, 595 Onion Ave, Ontario, Ore.
Jan Jones, (541) 889-2174 or janet.jones@oregonstate.edu
Aug. 29
WsU Onion Field day
Hartley Farms, Prosser, Wash.
Tim Waters, (509) 545-3511 or twaters@wsu.edu
Nov. 13-14
Pacific northwest Vegetable association Conference and trade show
Three Rivers Convention Center Kennewick, Wash.
Sheri Nolan, (509) 585-5460 or www.pnva.org CalEndar
Agri-Stor Companies helps growers take control of their onion storage with Gellert’s Agri-Star Control Panel. Since 1964, Agri-Stor has designed and sold thousands of Agri-Star panels for a wide range of post-harvest products. Through these years of application experience and university-based research, AgriStor Companies has developed its most user-friendly, advanced control panel yet. Features include a full-color, interactive touchscreen, easy-to-understand programming and internet capabilities with an intuitive app.
Fully adaptable to growers’ onion storages, the Agri-Star panel can handle everything including curing mode, burners, humidity, refrigeration, airflow, temperature, carbon dioxide levels, heat and lights. When growers match the AgriStar panel with Gellert’s climate control equipment, their onions are wrapped in the perfect climate, extending their life and quality.
The newest onion bagger from edp, model EB-2218-DF, is the most accurate and highest capacity bagger built by edp Australia. This machine will accommodate most any open-mouth bag on the standard 9-inch bag holder. Most customers in the U.S. use this machine for a range of bags from 20 pounds to 50 pounds. Also available is the ability to fill cartons or crates with the optional cartonfilling attachments. Speed control of both feed belts, pneumatic bag clamps, batch counters and monitoring of weight averages are among the standard features on the EB-2218-DF.
The Kerian Speed Sizer sorts onions by size quickly, accurately and gently. The constantly rotating rollers help the turning flaps align the onions with the rollers so that they are consistently sorted by size. The Kerian Speed Sizer is proven in use for whites, reds, golds, browns, Spanish, pearl and many other varieties of onions.
Lee Shuknecht & Sons, Inc.’s SP-132 is a self-propelled twobed harvester that eliminates windrowing while simultaneously direct loading two beds, for a total production width of 132 inches using 47-inch chains. This low-maintenance mechanical harvester provides the highest percentage topping of green and/or dry onions of all Shuknecht’s onion harvesters while it harvests two to three tons per minute. Powered by a standard 190-hp Cummins engine, the solo operator seated in an air conditioned cab has complete control over blower speed, primary and rear elevator speeds, cutter bar speed and height and ground speed. The twobed harvester features a 4-foot high-capacity boom and easily controlled front pickup elevators with spring-assist floats.
Available options include a moveable 4- or 5-foot dipper, rotating cab, stainless blower housing liners and a 240-hp engine. Digital readouts for the blower, primary chain and ground speed can be included, as well as hydraulic adjustment front elevator gauge wheels. Ground sync primary chain control, a posi-traction fourwheel-drive system and hydraulic trash chain drive can all be built into the SP-132.
The company also custom manufactures pull-behind models with the same quality and topping system to accommodate smaller onion growers.
EFFICIENT UNDERCUTTING AND WINDROWING
• RIGID FRAME + FOLDING MODELS IN A WIDE RANGE OF CONFIGURATIONS
TOP AND CURE ONIONS IN WINDROWS
• HIGH CAPACITY
• GENTLE HANDLING
• STANDARD + XL MODELS
INDUSTRY LEADING TOPPING AND CAPACITY FOR OPERATIONS OF ALL SIZES
• SUPERIOR DIRT & DEBRIS ELIMINATION
• BEST IN CLASS RELIABILITY
• MODELS FOR ALL GROWING CONDITIONS
Turbo Top’s TT-248 is a self-propelled two-bed onion harvester. Green onions are one of Turbo Top’s specialties, allowing growers to start harvest earlier and control curing. Day or night harvest? Turbo Top is capable of both. Adverse conditions? Turbo Top can work through the toughest of conditions.
The TT-248 has dual 48-inch-wide pickup elevators for a total harvest pickup width of 132 inches, allowing onions to be picked up how they are grown without windrowing to reduce damage.
TT-248 is powered by a 330-HP John Deere Tier IV Final Package engine. It has infinite cab control of fan speed, primary chain speed, ground speed, load boom speed/movement, cutter bar height and front elevator depth. Its exclusive large topping area eliminates weeds and debris and allows even the greenest tops to be sorted before topping.
Turbo Top comes in different models and has many options to fit growers’ needs.
To produce a healthy, uniform crop, it is essential that young plants get a strong start. That’s why we developed the innovative B-Mox® seed enhancing process.
International research trials have shown that our priming technology enhanced with B-Mox® gives an improvement over standard priming, as seen in the development of the crop. Many growers have already experienced the advantages of B-Mox®, with stronger and more uniform crops and higher packout.
provides stronger, more uniform germination strengthens the plant in the earliest stage stimulates better root development reduces risks for growers in the vulnerable early growth stage makes plants more resilient throughout the growth period is permitted for use in organic agriculture
B-Mox® is available for onion, carrot, and rooted parsley, and always offered in combination with priming technology.
As the U.S. distributor for Upmann packaging machines, Rietveld Equipment is able to bring the planning, design, construction and final assembly of one of the leading manufacturers of weighing and packaging technology in Europe to the U.S.
Upmann offers fully automatic filling and sealing machines for net bags, trays, boxes and poly bags. Upmann’s product line offers everything from clippers and baggers to carton-fillers and robotic arms. Using one company to supply the entire packaging line, as well as the design of the line, assures that all aspects of the packing line work together seamlessly.
Symach has a long history of palletizing onions and innovating to provide customized modular designs guaranteeing a high stacking rate with maximum flexibility. From 50-pound bulk and baled bags to complex Octabins, Symach has solutions to handle all customers’ palletizing needs.
Symach also offers options to stabilize the pallet at the end of the line, including wrapping and double stacking, and palletizing within the margins of the pallet to ensure ease of loading during the shipping process.
The 2024 XTR continues to be Top Air’s most capable onion topper loader. Available in two- or four-bed models, the XTR combines high capacity with superior handling. Featuring a high-performance rotary cutting system, this harvester outperforms in the most challenging harvest conditions on both short- and long-day onions.
Top Air is now taking reservations for 2025 models.
Unisorting, a brand of Unitec Group, develops and manufactures lines for onion sorting that combine high efficiency in the process and preservation of product integrity during each stage.
Onions Sort 3 and Uniq Onions are the latest systems, 100 percent developed in house, for external and internal quality selection of all varieties of onions. These solutions allow users to select the valuable or non-valuable characteristics of any type of onion without damaging the integrity of the product.
An accurate selection of external quality and internal quality, in addition to the detection of weight, optical size and shape, offers high performance solutions for every need. The dedicated technologies, semi-automatic or fully automated, are designed to offer the best possible result and give customers a highly reliable product without internal defects.
With 30 years of experience in building one-row onion harvesters, Univerco has introduced its new two-row onion harvesters.
The two-row models are available in both short-day and long-day onion versions. Both units have a similar harvest capacity per day, a steering axle to reduce turning radius on headlands and a system of three cameras so operators can easily monitor the key functions of the machine.
The short-day model has even more options available such as a sorting table, brushes under the topper table to keep the rollers clean at all times, and more angle and speed adjustments of the topper table. These improvements were made in an effort to minimize mechanical damage to onions.
By Jared Gutierrez, Volm Companies
In today’s market, it’s fair to say that everyday pressures aren’t the exception but the norm. Employment costs, labor shortages, sustainability, inflation, production issues and so on are creating challenges far and wide. As with any complex situation, there’s no one-size-fits-all solution. But in both my roles as president of the National Onion Association and general manager of the Pasco, Washington, division at the Volm Companies, I can tell you that innovation is proving to be a sensible way forward. Automation, in particular, has been a great way to proactively innovate while adapting to the changes we’re seeing in the market. These developments are particularly timely as we continue to see an industry-wide shift from bulk packaging to more consumer bags 10 pounds and under. But the costs involved here cannot be overlooked. Investing in
research, development, sustainability and other efforts are all worthwhile endeavors. The reality, though, is that none of them come cheap.
When it comes to automation, for example, growers and packers must make considerable, up-front investments in equipment, sufficiently train their employees and adequately maintain each piece of machinery. I’m not going to lie – there’s a brief moment of sticker shock. But I’m also going to tell you that once these initial growing pains are over, the return on investment is well worth the cost and effort. Consider businesses that have installed Volm’s MD series of weighers. Not only are these machines fast, but they are highly accurate. Sheds that have welcomed them into their equipment lines have been able to drastically cut down on expensive labor as well as significantly reduce their giveaway. So that initial investment is paying off in the present and will continue to do so in the foreseeable future.
Cost impacts are a critical factor on any given day, but they’re especially important now. We’ve all been feeling the pinch of inflation, and the rising cost of goods and services hasn’t been easy on anyone. Like many growers and packers, Volm knows what it’s like to feel squeezed by those cost pressures. And we also believe in managing our costs as best as possible. I truly feel that this is a shared responsibility. Growers, packers, suppliers, retailers and everyone else who plays a role in our food chain shares a responsibility to reduce waste, minimize inefficiencies and manage their dollars as responsibly as possible so that costs don’t simply get handed down to families sitting at the dinner table. At Volm, we are doing our part in a number of ways, and this includes sourcing competitively, leveraging strategic partnerships and ensuring that our facilities are run as efficiently as possible. Recently, we started applying lean strategies to drive internal process improvements throughout the business. As a part of this, we’re identifying and eliminating waste in all forms with the intent of creating value for customers
through reduced order processing times and improved quality. In Pasco, in particular, new processes were implemented to improve domestic Leno costing, lead times and delivery.
These solutions include the Volmpack Wicket Bagger for all-mesh consumer bags, the AutoPack for larger Leno bags and the AutoMesh Baler for packing consumer bags into roll-stock Raschel mesh master bags.
It’s important for all of us to continue to make positive changes. In the Pacific Northwest, I’m seeing more and more growers and packers replacing costly, timely and demanding manual labor with quick and easy equipment solutions.
SEEDWAY_Onion World_Oct2021_Layout 1 10/4/2021 2:52 PM Page 1
Equally exciting are some of the equipment solutions that have recently entered the market. The MoNo Clipper is a new clipping machine that demonstrates that less is more. That’s because the bag is made without a metal clip, eliminating the need for clipping wire.
UNITED STATES
UNITED STATES
MEXICO
MEXICO
California (661) 699-0055
Lancaster & San Joaquin Valley (661) 978-5342
Irapuato
+52 (462) 220-0453
Torreón, Coahuila (461) 117-3878
Desert Southwest (928) 446-7737
California, New Mexico (661) 300-9109
Colorado & New Mexico (970) 396-9728
Southern California, Arizona (760) 791-0325
Idaho, East Oregon, Utah & Nevada (208) 941-1421
Colorado (208) 550-7733
Idaho, Eastern Oregon, Utah, Nevada, North Dakota (208) 941-1421 (208) 550-7733
Skagit Valley, Washington (360) 941-7503
Rio Grande Valley & West Texas (956) 618-5574
Washington, Western Oregon (509) 820-9887
Texas (956) 618-5574
Torreon +52 (461) 117-3878
Colima, Col. (461) 104-0134
San Luis Potosi (461) 140-9452
Chihuahua +52 (648) 109-1597
Chihuahua (461) 171-9401
San Luis Potosi +52 (449) 196-1848
Tamaulipas (461) 134-2421
Tamaulipas +52 (461) 346-1531
Irapuato, Gto. (461) 546-5792
Colima +52 (461) 104-0134
Another standout addition is the BD808 Case Packer, which is a compact, high-speed and fully automated case packing system. Here, consumer bags are dropped into an intermediate chamber, where they are staged ahead of a final deposit into the master carton. Depending on the bag size and other variables, this method produces pack rates of up to 80-85 bags per minute.
Palletization is also an exciting area where we’re seeing tremendous benefits for the onion industry. This is because the latest generation of equipment solutions offers superior stacking quality, despite onions’ well-earned reputation of being a difficult-to-stack product. The latest palletizing solutions are highly adept at containing and compressing each layer. This method of palletization prevents shifting of product and successfully achieves a strong and sturdy stack.
On packaging, there continues to be lots of interest in products that minimize waste and reduce our environmental impact. For onion packers, ecofriendly netting is available, including compostable knitted or extruded netting and lighter weight nets that use less raw material to produce. Also worth mentioning are the benefits of using all-mesh packaging, which allows for the breathability that onions need. Mesh helps to maintain a longer shelf life, which prevents unnecessary food waste. For bag closures, the CloseIt Bio-Clips are our more sustainable offering. This clip is biodegradable and contains 100% USDA certified bio-based content. Compostable wineglass labels are also an option.
The list of innovations entering the market gets more extensive all the time. And the good news is, as the industry continues to invest in the future, we can count on seeing more offerings down the road.
Predicting the future of the onion market is a bit like predicting the weather; there are never any guarantees. But one thing remains clear. If today’s challenges have taught us anything, it’s that businesses that innovate will continue to thrive today, tomorrow and beyond.
We take perfect care of
Do you need the ability to accumulate boxes with multiple SKUs? Scan the QR to watch our flagship machine VPM-VHV stack pallets at blistering speeds or visit verbruggen-palletizing.com
harvest in the West will be here before you know it. That’s why we included the Harvest Essentials Buyers’ Guide in this early summer issue (see pages 12-17), and it’s also why we gathered harvest photos from the Onion World photo archives for this issue’s 40th anniversary celebration.
None of the harvest equipment pictured here is GPS-enabled, nor does it operate on its own or provide yield data, but it did the work it was meant to do. These machines are probably all retired now, many set out to an unused corner, reminding us of a simpler time. We’re hoping this nostalgic look at equipment, working in its prime, brings you fond memories, or possibly relief that you have better technology today.
If you have an old photo that you think would make a good addition to an upcoming 40th anniversary issue of Onion World, please email it to editor@columbiamediagroup.com.
proven accurate seed placement is why growers
TELONE™ II is the world's best defense against destructive plant parasitic nematodes that negatively impact onion production, including stubby-root, rootknot, lesion, stem & bulb, as well as pesky wire worms. Applying TELONE™ before planting leads to healthier plants, higher yields, and improved quality. A custom blend of TELONE™ (to combat nematodes) and chloropicrin (to target soil borne diseases such as pink root) is an effective one-two punch.