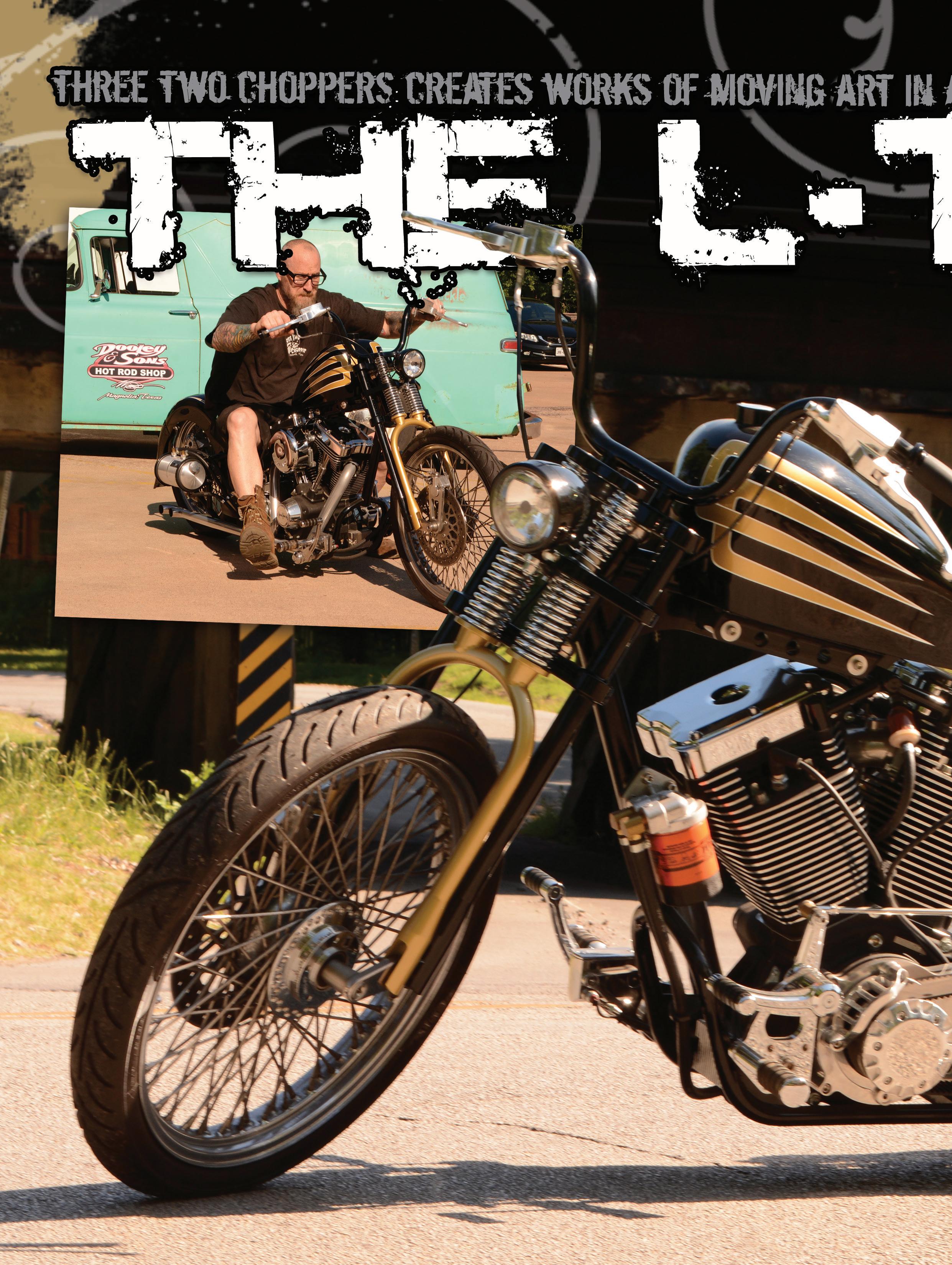
18 minute read
Three Two's No Drama Evo
or Jimmie Lee and JC Coen, it’s been motorcycles from day one. Their ability to work seamlessly together as both partners and family has allowed them to fine-tune the way they make motorcycles and parts. Two Three choppers started in 2004 as the full-time job after the full-time job with a goal of simultaneously building two show quality bikes in the time full shops would only produce one. It was their way of making a statement and declaring their intentions of staying for the long haul. Since then, they have strategically made the proper advances to move forward in the cutthroat industry that all but devours the independent motorcycle builder. Their first builds allowed them to set firm roots with a quality reputation showing that you don’t necessarily need to follow the masses to develop a strong customer base. While some builders still depend on repairs and customer fabrication work, these brothers solely rely on the builds themselves to drive Three Two into the future.
Jimmie Lee, a former 3-D animator, was able to sever the chains of his full-time gig in 2011 and JC a computer scientist held out until 2016 making the fulltime ongoings of the business
Advertisement
fbecome their only distraction. Since then they have moved on to developing affordable wishbone/ hoop conversions for Paughco springers and similar knockoff competitors. On top of the conversions, five years ago they acquired Redneck Springers and now produce roughly twenty front ends annually, always ready for custom orders. In 2015 a former customer returned looking for his second Three Two bike. It needed to be built for a smaller framed rider with a reliable, reliable drivetrain to match. The Coen brothers designed a drop seat frame using 1” tubing that would
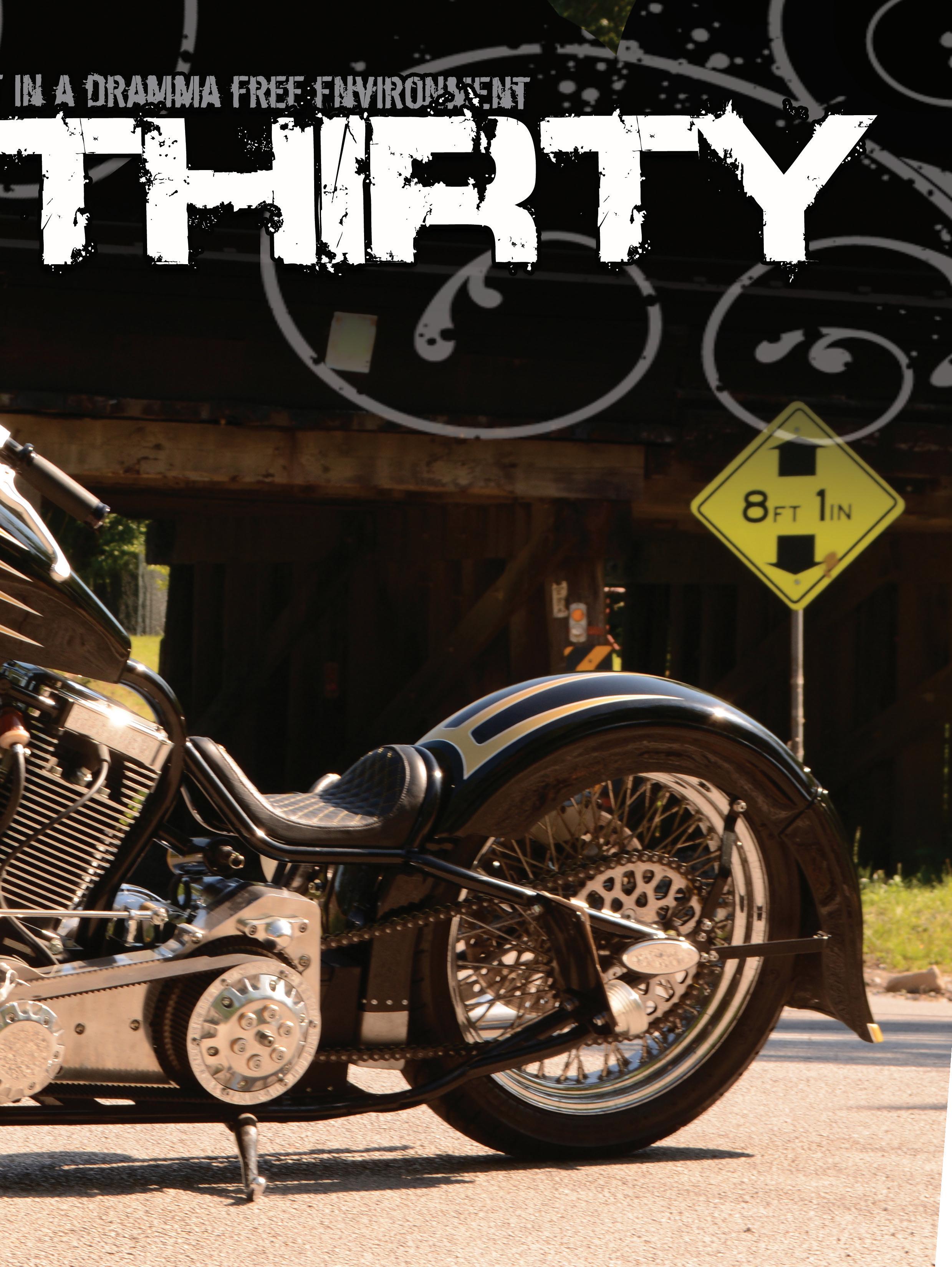
cradle an S&S 80” Evo motor with a matching Primo trans. The bike would be based off of the Three Two El Segundo frame with a 30-degree rake. This model would be named the L30. The idea was to have a nice tight bike that someone could easily throw around and that handled like a dream.
Three Two are entirely in-house from frame to sheet metal. They let their strong mathematics background be the foundation for every build because they know that if the math is dead on so will the handling of their products. Both JC and Jimmie Lee have their strong points, and they check the egos at the door; letting each other do what they are best at and allowing the other to double check the work. There is only one way anything leaves the shop, and that’s if it meets their standards and if each piece can stand on its own. There are no digital machines, no CNC to fall back, on everything is done entirely by hand and attacked with surgical precision.
The L30’s rear fender was a vintage piece that was altered and fabricated to be accepted by the drop frame. The gas tank was made in-house, and a Moon Eyes oil tank was installed to compliment. The bars and risers which consist of 6-8 individual pieces welded solid are also Three Two Choppers along with the exhaust, and it goes without

saying that there is a deraked Redneck Springer leading the way. About 75% of the way through the build, the customer visited the shop to see how progress was moving. Three Two was in the middle of a 71 Triumph Daytona 500 build that was also roughly 75% complete. The customer expressed interest in the trumpet do to a family history with the same bike. A deal was struck, hands were shook, and a trade was made. The Triumph was now going to a new home, and the little Evo wasn’t going anywhere. The trade allowed the brothers to finish the bike how they saw fit. The build in total took somewhere in the range of eight or nine months; it’s hard to say with the ongoing distractions of everyday shop dealings and only the two brothers at the helm. But they wouldn’t have it any other way with no employees they also have no
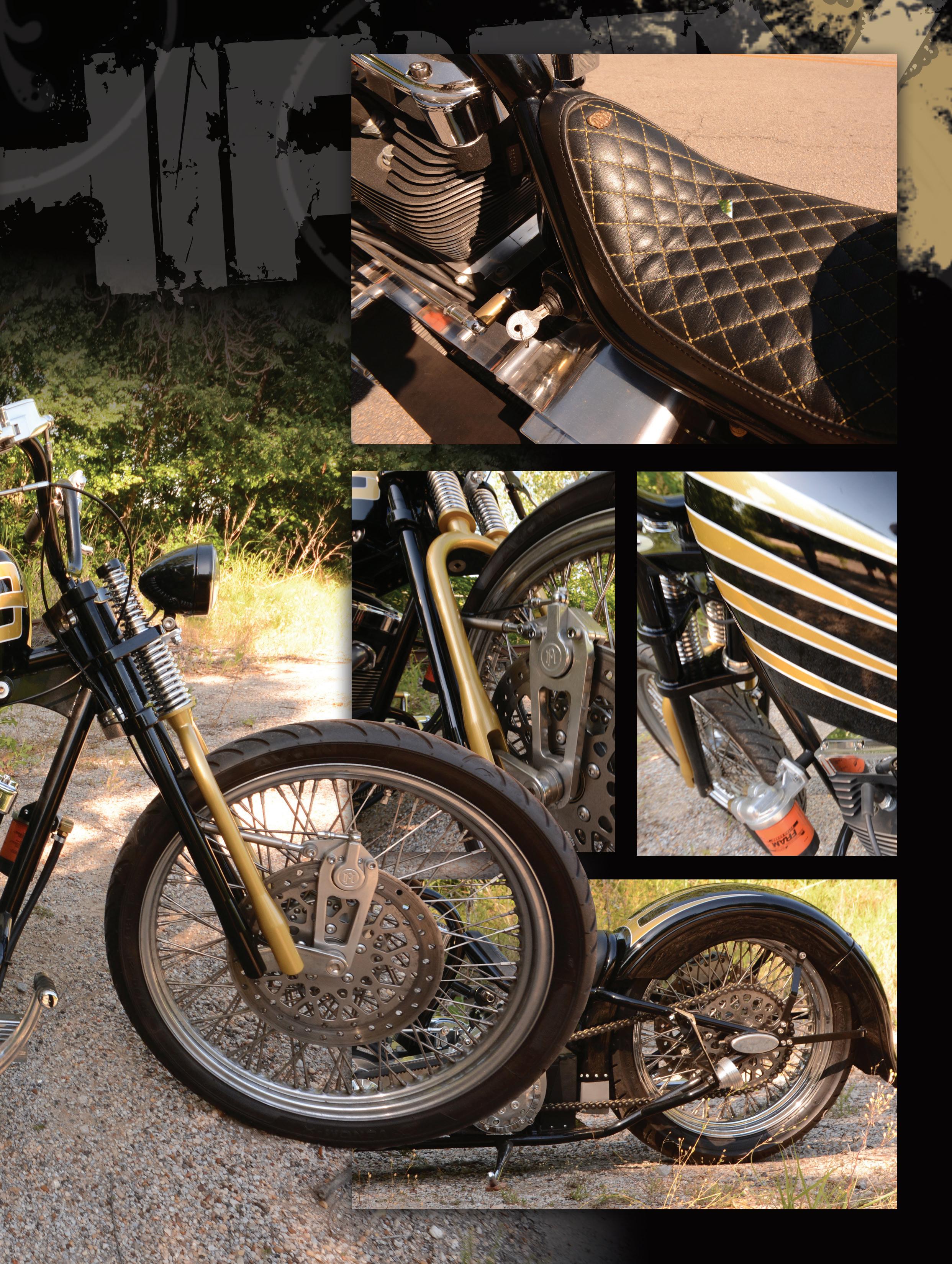
Owner: Brent Rehm City/State: Minnesota Builder: Three Two Choppers Year: 2017 Model: L30 Value: $30,000 Time: 518,400 Minutes
Engine Year: 2017 Model: Evo Builder: S&S Cycles Ignition: Super Stock Displacement: 1340cc Pistons: S&S Heads: S&S Carb: S&S Super E Cam: S&S Air Cleaner: S&S Exhaust: Three Two Choppers Primary: 2” Open
Transmission Year: 2017 Make: Primo Shifting: Standard
Frame Year: 2017 Model: L30 Rake: 30° Stretch: Forks Builder: Three Two Choppers Type: Redneck Springer Triple Trees: Extension: None
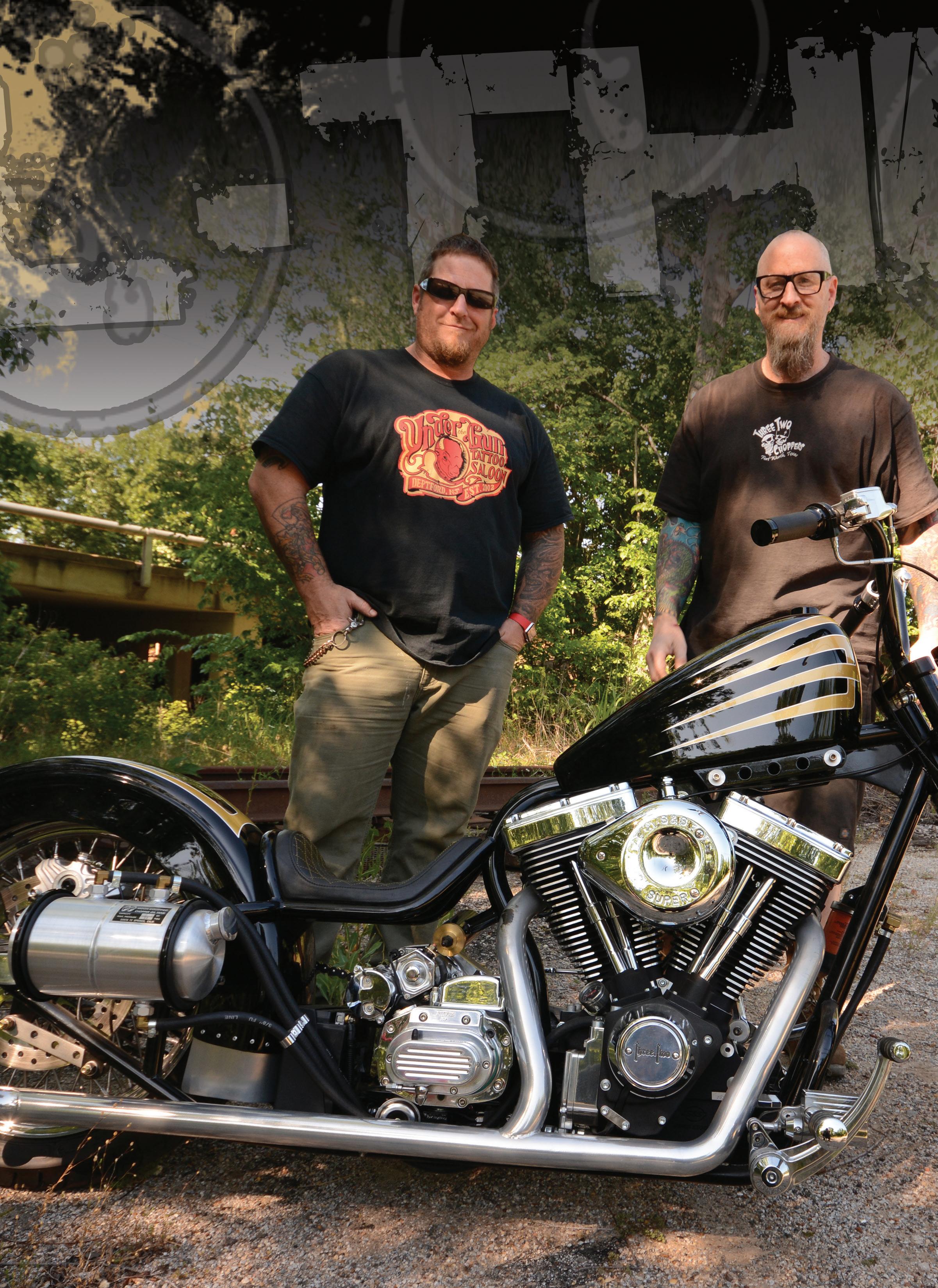
Wheels Front Wheel: Pickard USA Size: 21” Tire: Avon Front Brake: PM 2-Piston Rear Wheel: Pickard USA Size: 18” Tire: Avon Rear Brake: PM
Paint Painter: Other Side Customs Color: Black & Gold Type: Spray Graphics: Scallops Chroming: None
Accessories Bars: Three Two Choppers Risers: Three Two Choppers Hand Controls: PM Foot Controls: TR Gas Tank(S): Three Two Choppers Oil Tank: Moon Eyes Front Fender: None Rear Fender: Vintage Hinged Seat: Ranger Leather Headlight: V-Twin Tail Light: Three Two Choppers Speedo: Dakota Digital/Three Two Choppers Photographer: Chris Callen
quality issues or unneeded drama. Three Two Choppers sat on the bike for a little while with no real need to sell it when someone visiting their website inquired about the L30. The Evo finally found its home in Minnesota. Three Two Choppers is a fully functioning family business run top to bottom by the Coen brothers; they don’t need to answer to anyone and their blood and sweat ensure that every customer gets the absolute best they have to offer.
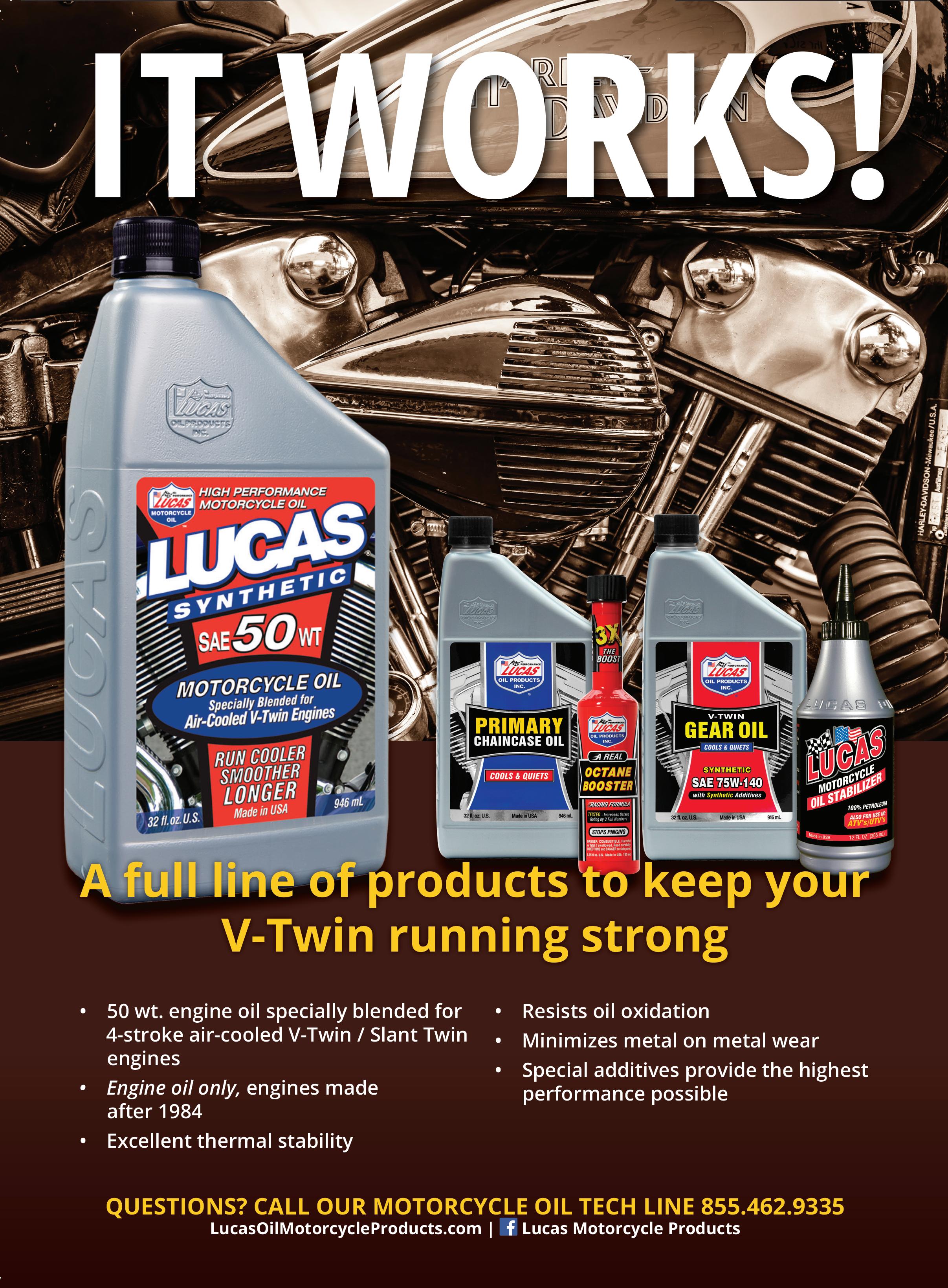
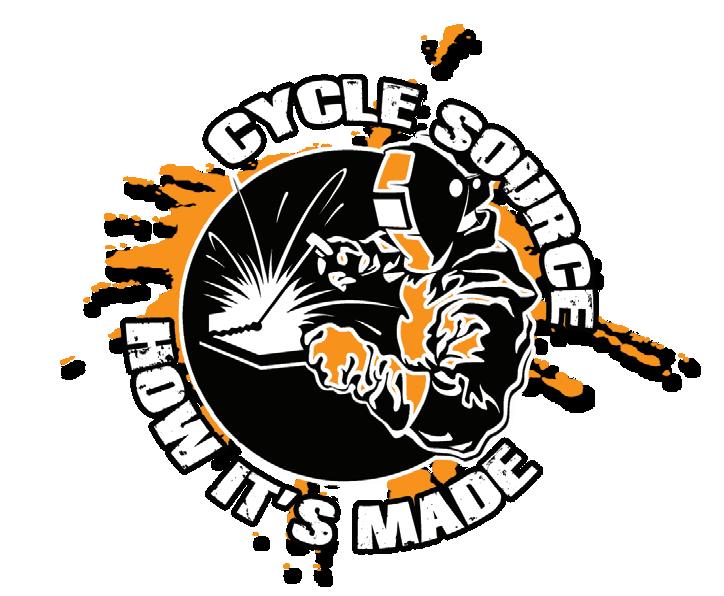
Article And Photos By: Will Ramsey www.faithforgotten.com
his month’s tech article illustrates a specific part relating to chopper frame construction. Although this particular set up may not be relevant to T everyone, I have chosen to take this opportunity to discuss both precision work on manual machines, and the process of thinking through a design, to accurately produce a part that fits into a set up. It is important to understand that precision is essentially infinite and to some this entire process may seem like over kill, while others may make note of certain procedures that could be far more precise. It is up to you as a designer, and as a craftsman, to determine the level of precision that both you and your design require. I personally enjoy the pursuit of precision and often find myself taking things a bit farther than necessary. Admittedly this is often done for personal pride and gratitude. It is also responsible for a great deal of frustration on certain days, but without frustration there can be very little learned. I always encourage those around me to strive for a bit more precision in their work in order to determine what they believe to be enough. The Axle locator is designed to secure the rear axle in the axle block and allow for adjustment in order to align the rear drive train. This diagram illustrates the specific design of this part. Although there are no tolerances listed, we are going to proceed with a fairly high level of precision in order to demonstrate precise measurement and procedures on manual machines.

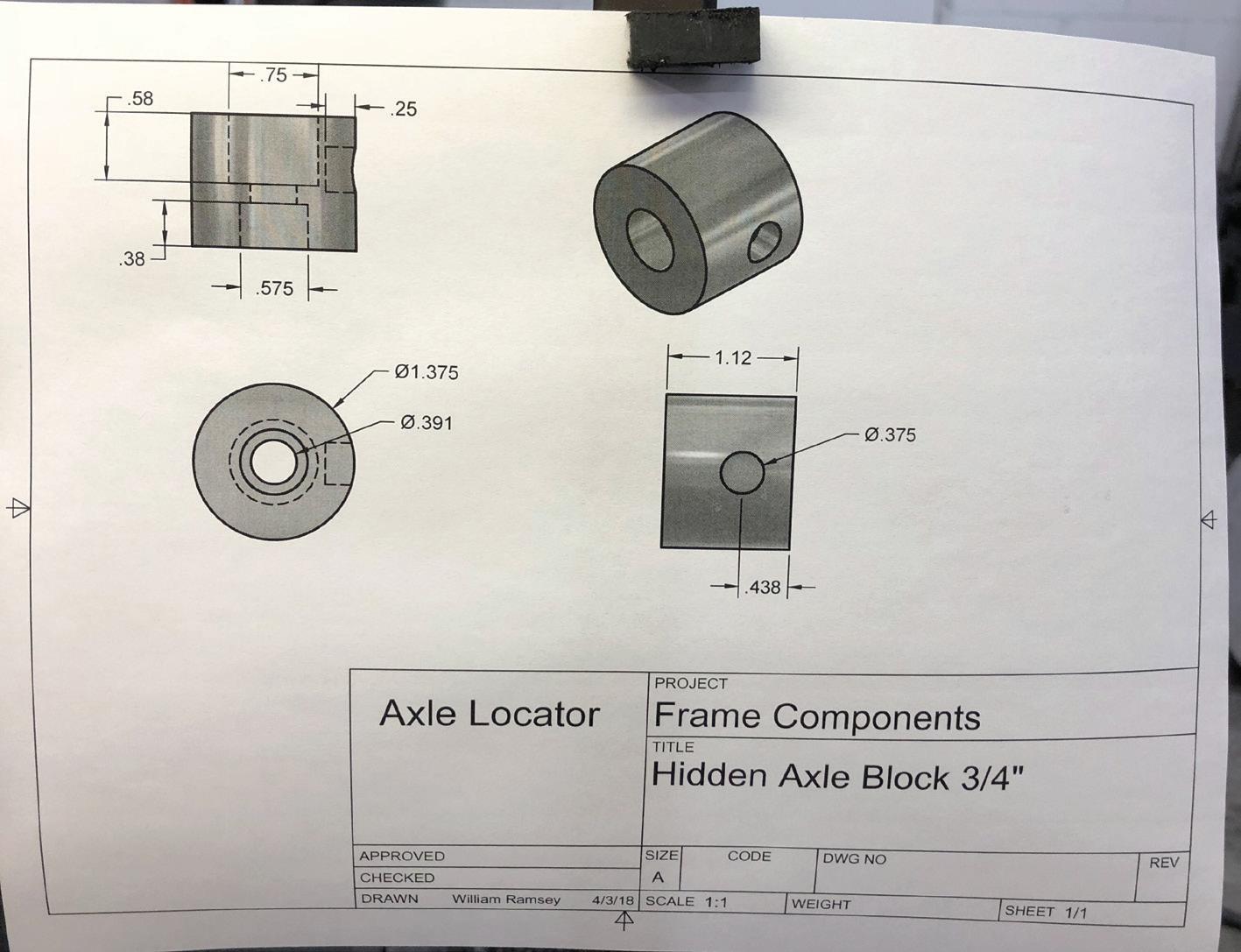
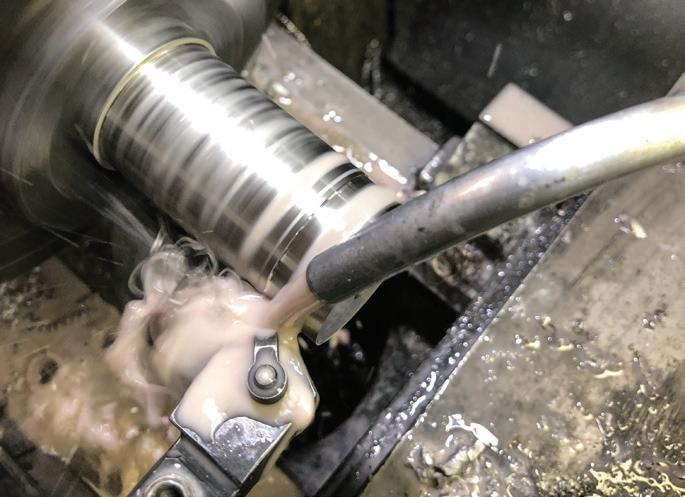
Starting with a slightly oversized piece of 304l stainless steel, the diameter is turned down to 1.375”. Although we could start with a piece of 1.375 mill finished round bar, the process of turning the diameter allows for both greater precision in the diameter, and a nicer finish.
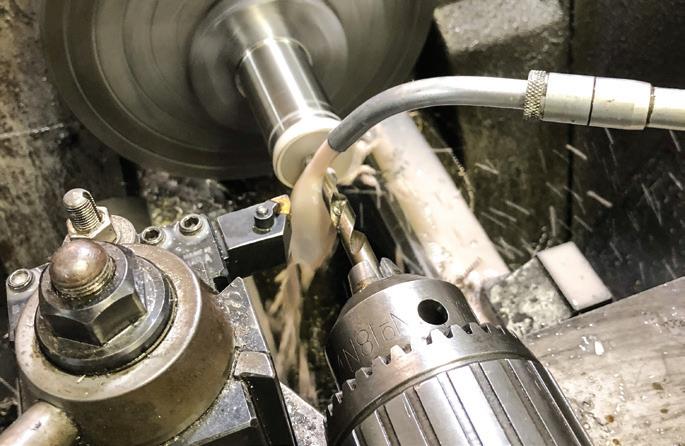
The next step is to drill out clearance for the 3/8” bolt. A drill is not a precision tool, it is used for roughing out material in order to allow for precise machining to follow. However, in the case of a clearance hole for a bolt a drill is well within acceptable tolerance.

The design for the axle locator calls for a counter bore that allows the head of a socket head cap screw to sit just below the outer surface of the part. In this operation a tool specific to this operation is employed. The counter bore tool is essentially an endmill with an indexing guide. As the guide centers the tool on the drill hole, the cutting face of the endmill squarely removes material to allows clearance for the head of the bolt. This process is more precise than drilling, but it is not as precise as using a boring bar.
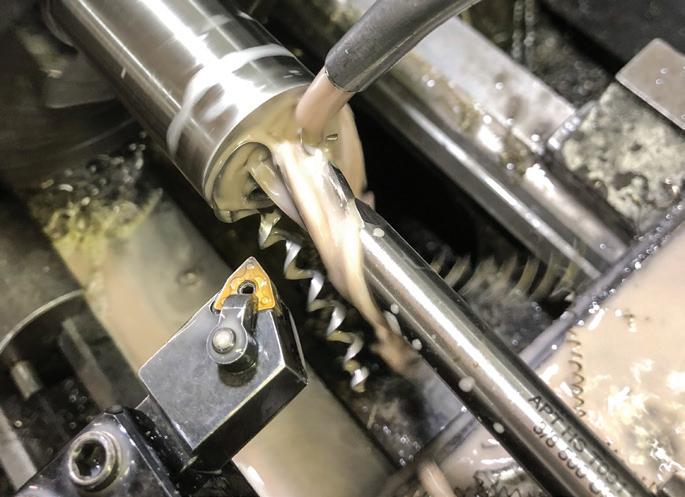
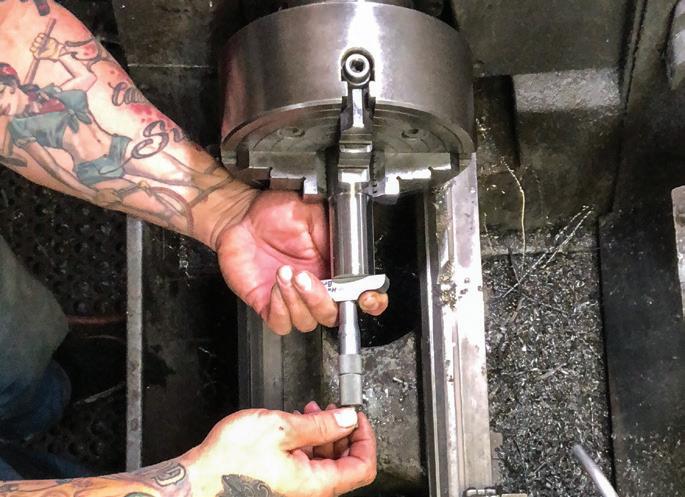
The dimension we are most concerned with in the counter bore is the depth. Since the tailstock is not as precise
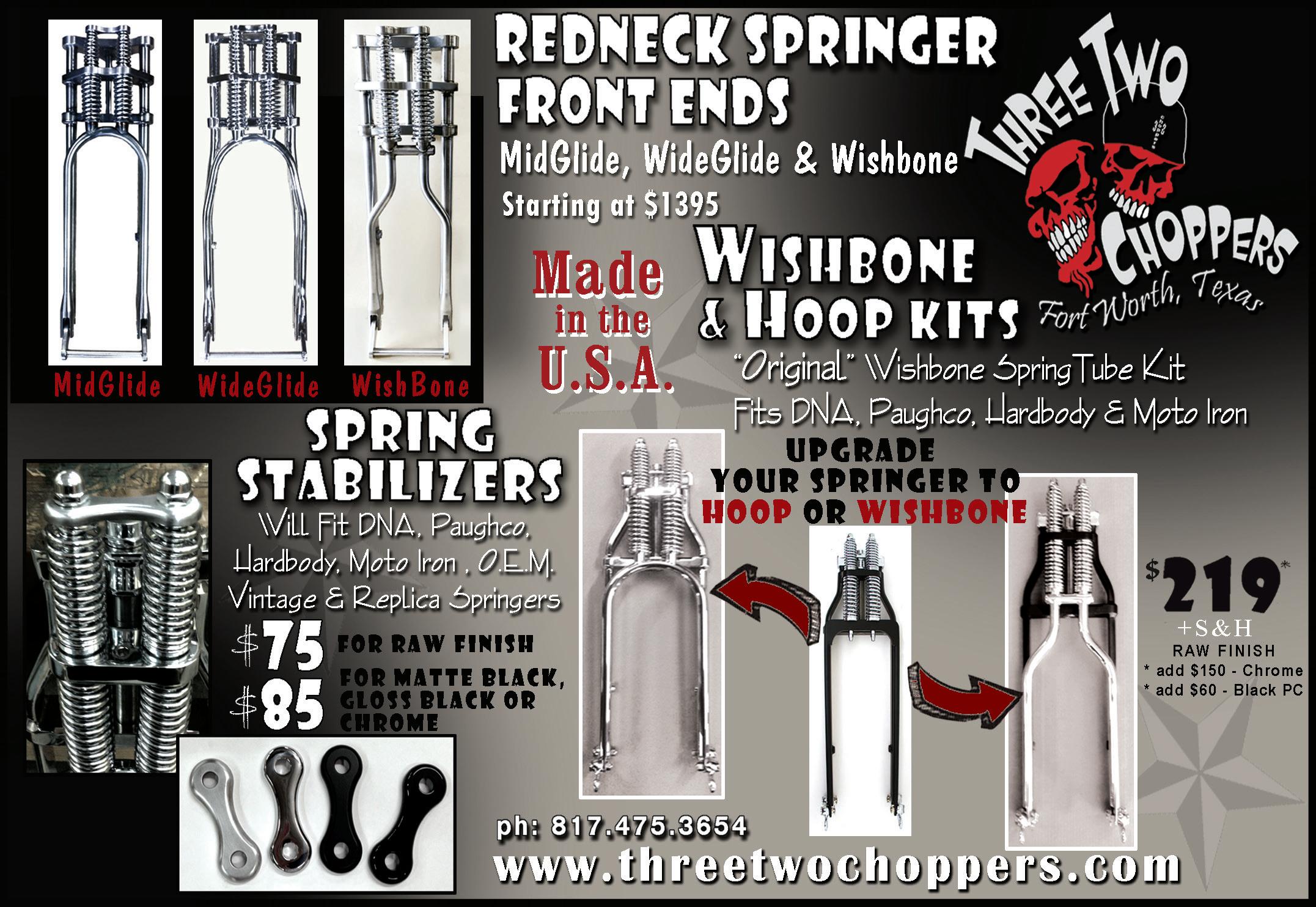
and measurable as the carriage on a manual lathe, it is important to manually measure with a depth micrometer and adjust accordingly.
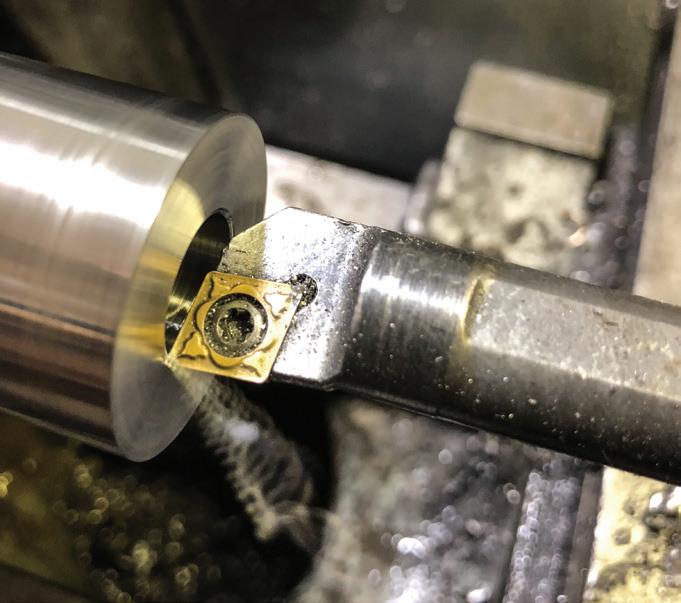
After completing the counter bore a boring bar is used to simple cut a small chamfer using the cross slide. There is really no precision in this operation. It is done to break the sharp edge and give the part a more finished look and feel.
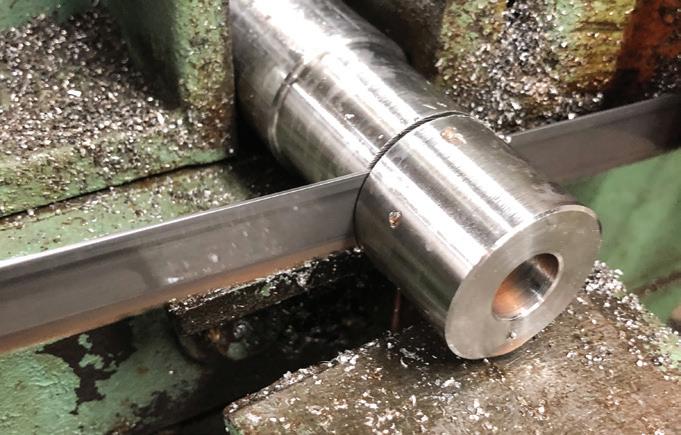
Although a parting tool can be used to cut the part to length, I have decided to rough cut the part in the band saw before returning to the lathe to face the part to length.

The length of this part is fairly critical as the design calls for it to sit just .005” behind the cover plate. In order to obtain this length accurately it is important to use a quality micrometer and adjust the facing operation accordingly. The next step in the design diagram is a counter bore for the axle to index. This operation is performed with a boring bar. It is always best to use the shortest and thickest boring bar in order to reduce tool flex. Tool flex is the crux of boring and is a process certainly worthy of its own tech article.

There are many ways to accurately measure the diameter of a bore. A set of bore gauges can make the process very fast and extremely accurate. The ability to “feel” the final fit makes the bore gauge set invaluable in certain situations.

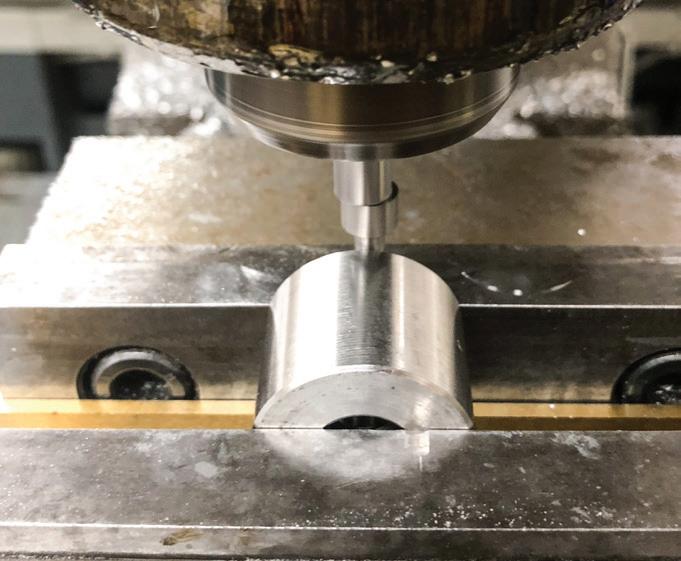
With the lathe procedures complete, the part is moved to the knee mill in order to cut the hole for the axle adjuster to index. The Center finder is used to find the center and the outside edge of the part.
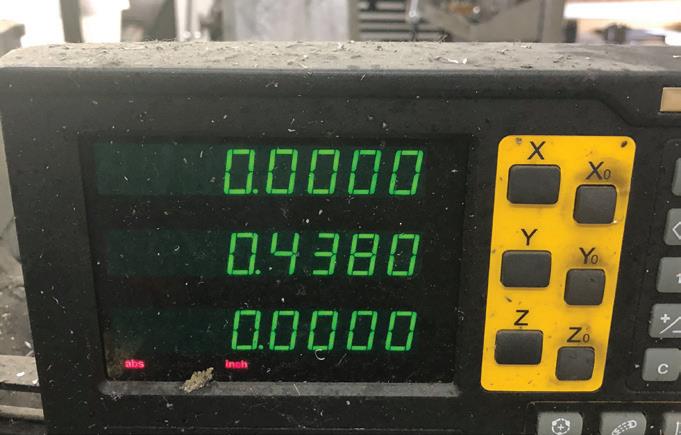
Once the spindle is centered over the edge, the mill table is moved .438” along the Y axis per the dimension listed in the diagram. An on-size .375” endmill is used to machine the hole. In order to accurately obtain depth, the quill is locked and the knee is advanced along the Z axis.


Our final part is inspected and checked for fit with a high strength alloy bolt used to secure the axle. It can be quite gratifying to maintain a level of precision that you intend using a manual machine and then hold the finished part in your hand. This is where the passion and the reward are discovered.
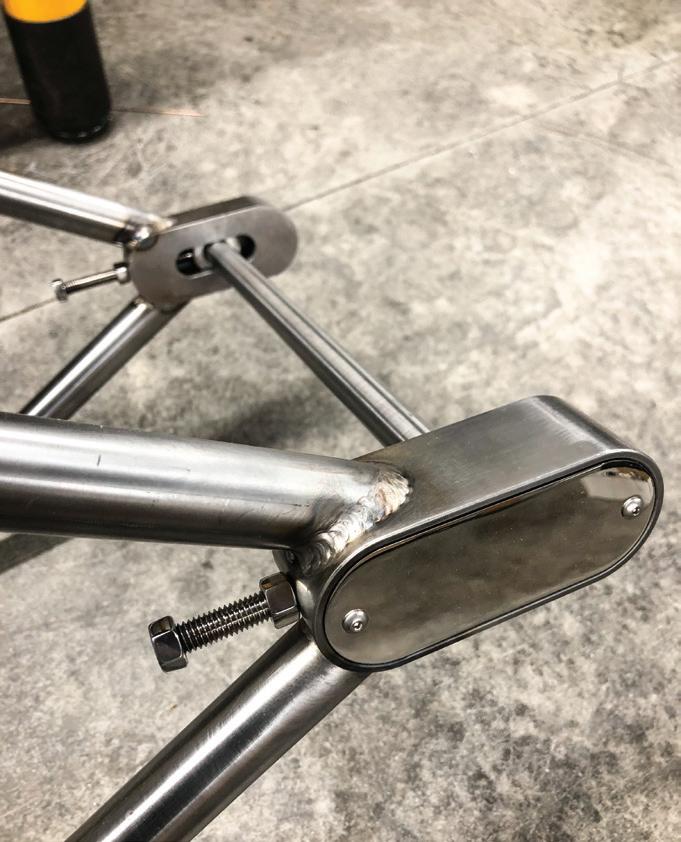
Although the final part is covered once the entire set up is assembled, the functionality of the part will still remain directly correlated to the accuracy and precision with which it was machined.
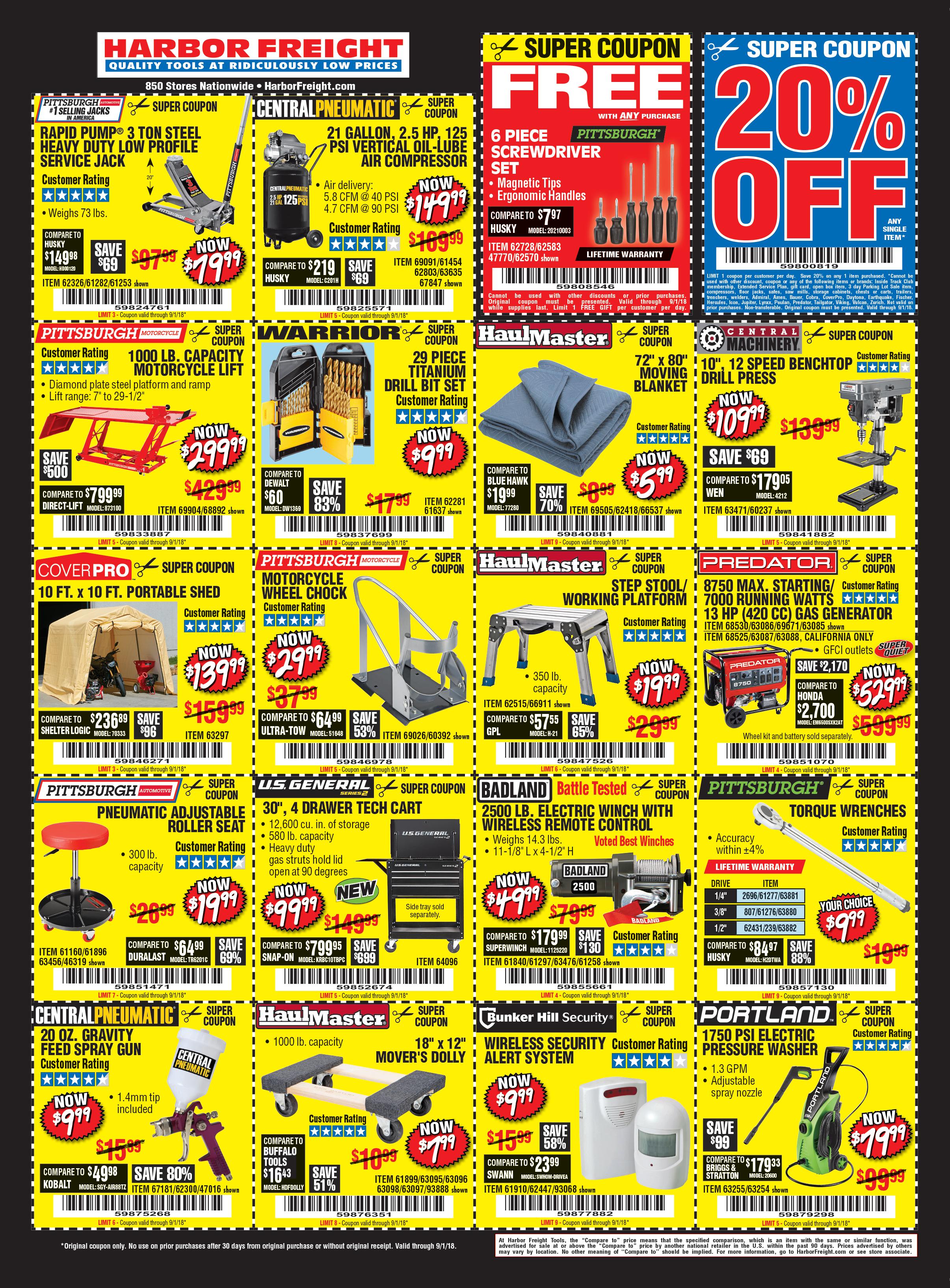
Article And Photos By: Charlie Weiselearly March in Colorado is not typically considered a great time to embark on a multi-day motorcycle adventure. In fact, it’s a risky time for most parts of the country which is the main reason why I’ve never bothered with the Daytona Rally in Florida...or should I call it the Greater Daytona Area Motorcycle Get Together? I’ll get back to that later. The likelihood of bitter cold temperatures, spring rains, and even snow are well beyond possible, it’s almost guaranteed, and this trip would prove that multiple times over. My departure from home was about as expected, better even, with temperatures in the mid 40’s and a gale force westerly wind I was thankful that the thermometer had clipped north of 32 and the roads were dry, but this would all change on me soon enough. Eastbound on I-70. I chose to blaze across Kansas as quickly as humanly possible, I’ve learned from previous experience that back-roading Kansas doesn’t gain a person much but added hours of wheat field viewing. I’ve already checked “see 1000 wheat fields” off my bucket list so the interstate it was. My unofficial destination for the day was somewhere in southeast Kansas but with my late start I chose to aim for Marion, Kansas where I knew my friends Roger and Pam would have a warm meal and bed for me, they are good people like that and my next morning’s experience would further prove that stop to be priceless. You see, I had set my alarm rather early to
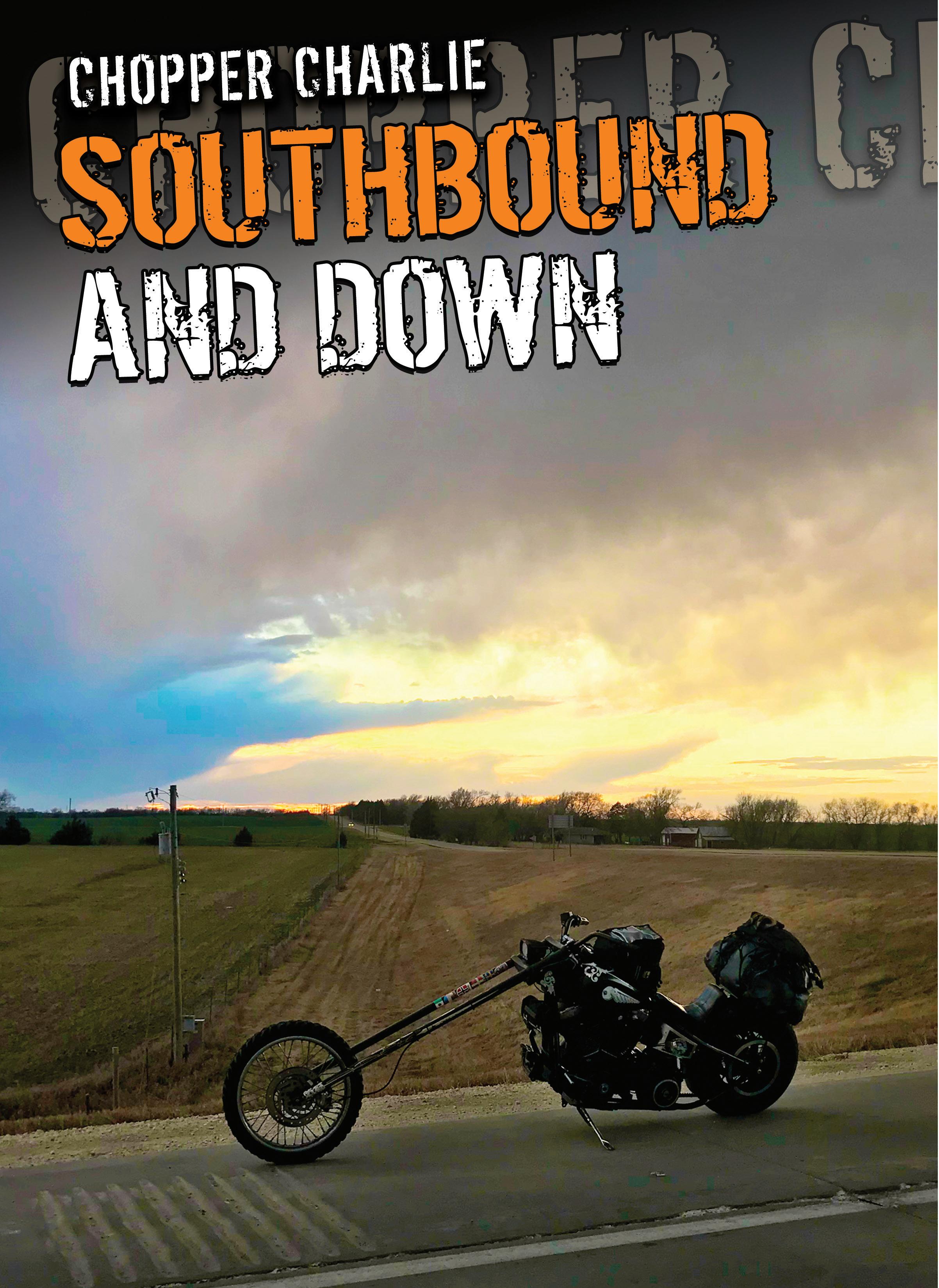

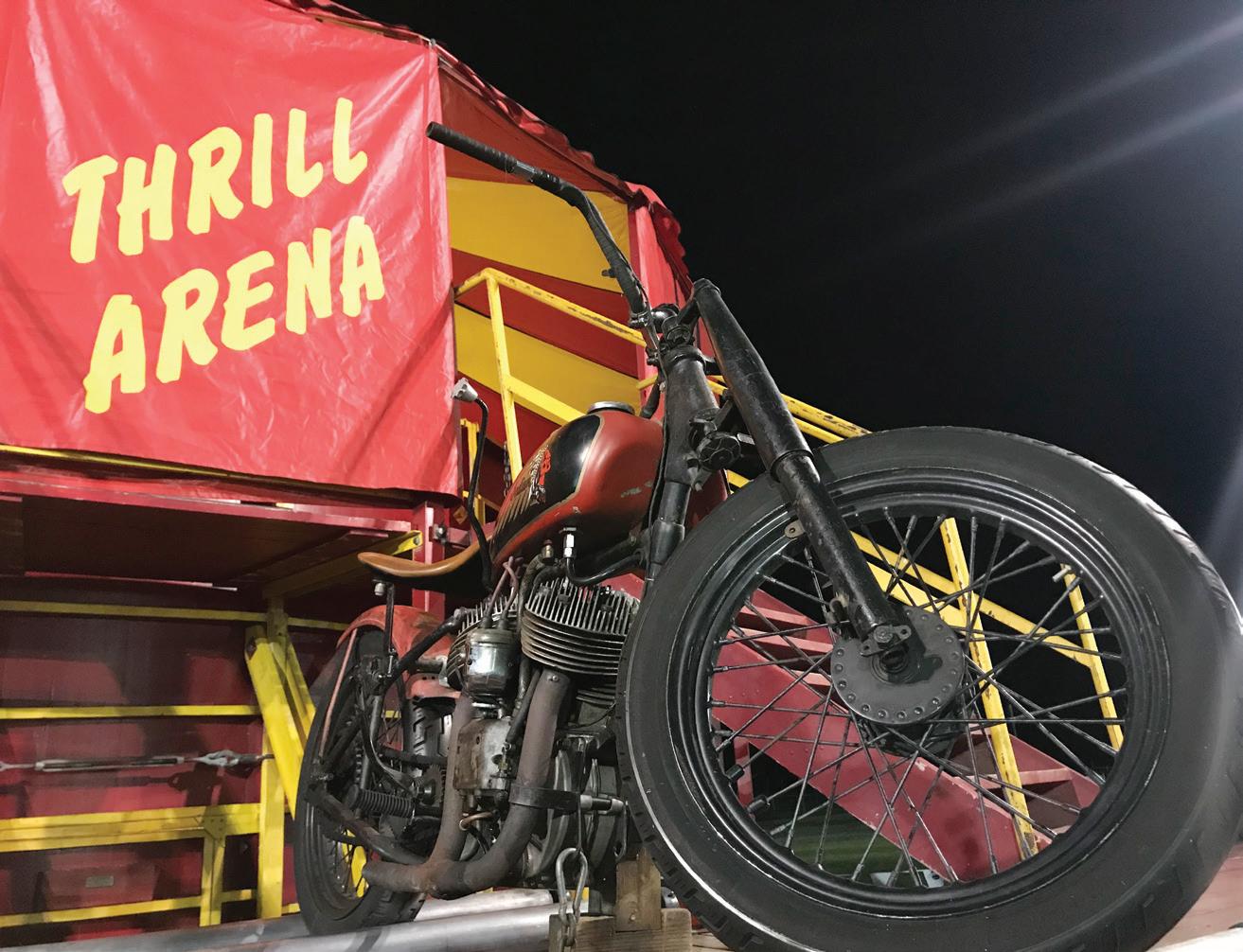
get a jump on the sunrise as I hoped to ride from sun up to sun down that day, but my plan was foiled when all my bike gave me was some pathetic half-assed attempt to start itself when depressing the starter solenoid. Crap. My bike has a funny way of doing that; it runs like a champ for 500ish miles to Rogers house then decides it wants to sit put for a day. Maybe she partied all night in the garage with the other motorcycles and was too hungover to do anything but sit, who knows, but she was sounding a little puckish. But, like so many times in my life, I was wrong, and it turned out, after a few of hours of head scratching, that my starter had gone bad. This resulted in a roasted battery and my feeling guilty for accusing my beloved motorcycle of having a substance abuse problem. Miraculously, the Harley-Davidson dealer down in Wichita had a new starter so off we went on the 180-mile round trip drive to procure said item. Meanwhile, Dylan of DFS Moto in Canton, KS, who made a house call to Rogers place I might add, removed my old starter. At this point in the game, I thought that if we got this fixed quick enough, I could still hit the road that day, wishful thinking on my part, especially considering that I had a perfectly pleasant place to stay for a second night if needed. Upon our return with the part, Dylan had it installed in no time and problem solved. I chose to stay another night and leave in the morning as it was approaching 6 pm at this point and another night with friends is not something one should pass up. 6 am alarm, again, felt a bit like Groundhog Day except that this day my some-what trusty steed would fire up beautifully and I would be on my way. The downside was that it was dramatically colder than the previous morning with my departure temperature being a mere 23 degrees and no signs of it warming up
anytime soon. It wasn’t until noon that I regained feeling in my fingers, somewhere in Arkansas if memory serves, but my brain resembled something like a snow cone at that point, so I can’t be held responsible for remembering any details before 1 pm that day. Regardless, Arkansas is always a treat with its endless supply of snaking tarmac, grand vistas of the Ozark Mountains and a plethora of roadside oddities. The kind of roads that make you want to twist the throttle a bit more and test the limits of your tires, and I did. Pushing my way down roads that barely resembled roads at all and leaving me wondering if I was even going the right direction, I finally arrived in Hot Springs, Arkansas where I decided to call it a night. The sun had dipped below the horizon at this point, and that roadside Hibachi Grill food truck was calling my name. Day 3. I was excited; I knew that I might actually find some warm weather, and I did, well, warmer anyway. Someplace near Jackson, Mississippi, the temps started to creep into the 50’s, the skies were clear, and the southern drawl was thick in the air. I could sense that I was starting to get somewhere and that’s always a good feeling. This is also about the time my mind began to clear, the stresses of everyday work life began to shed its weight, and I could really sink into the rhythm of travel. Typically, this only take a few tanks of fuel to achieve but work life has been beating me into submission like never before and losing a day in Kansas didn’t help. Southbound and down I went, deep into the heart of Dixie, and now hellbent on making the always oh-so-good Cycle Source chopper show, I cranked out the miles. 300, 400, 500 and upwards to 780 miles for the day. This was my target number for no other reason than I knew it would put me within 200ish miles of the show and it’s 11 am opening the following morning. I was raised with a military father, so punctuality is thick in my blood. If you aren’t 5 minutes early, you’re late. I made it by noon, an hour late...oh well.
This is where things started to get weird, but keep in mind I’ve never been
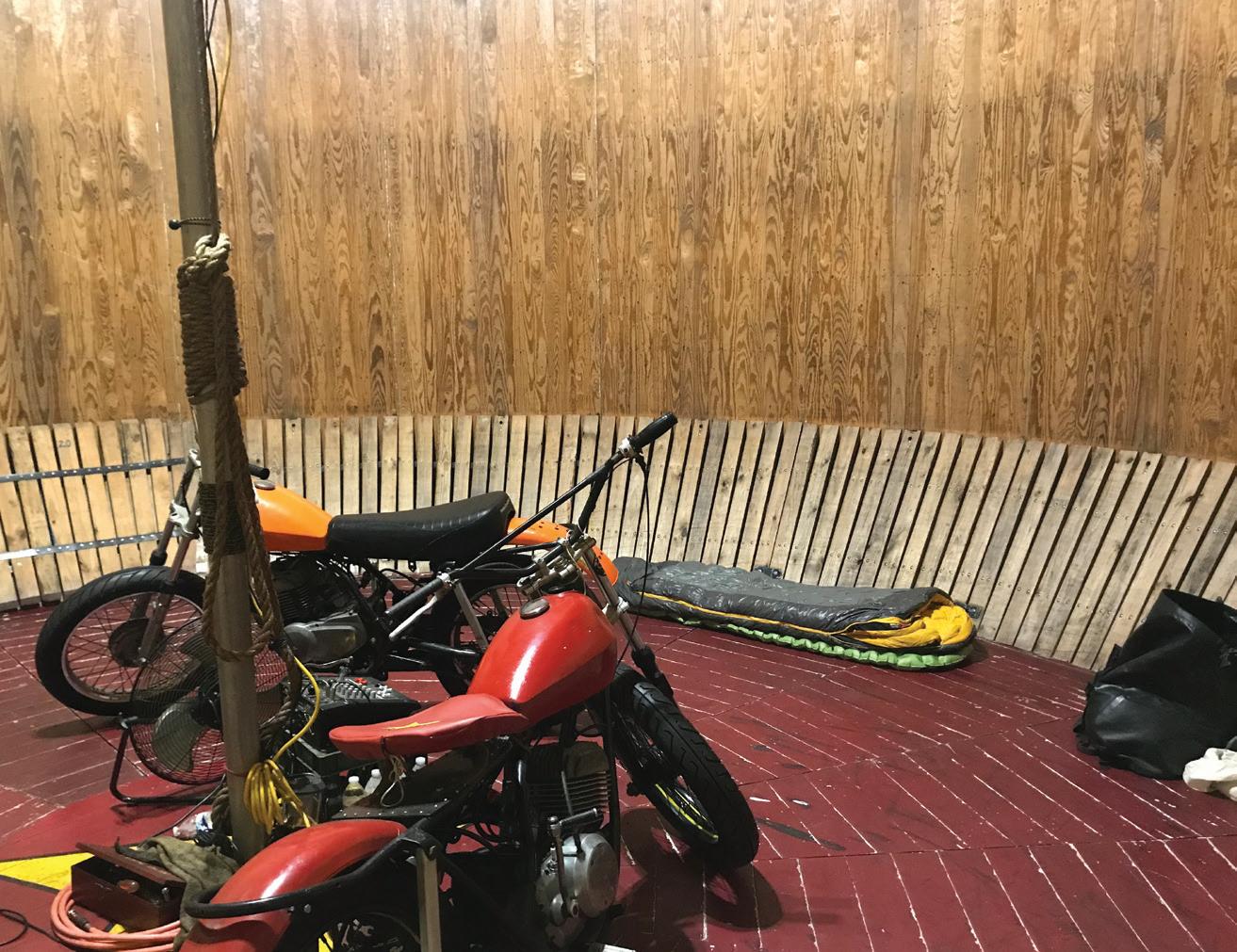
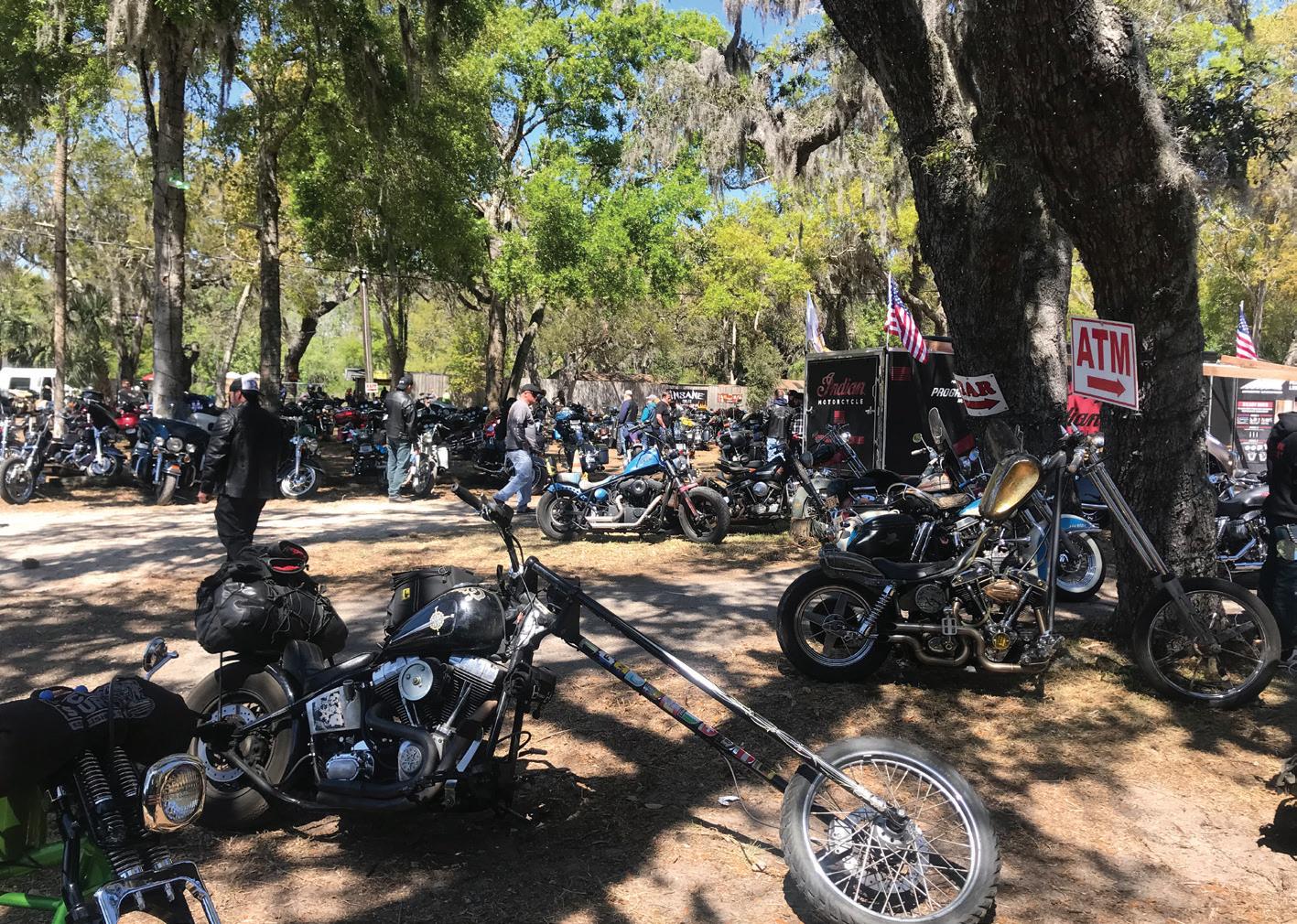

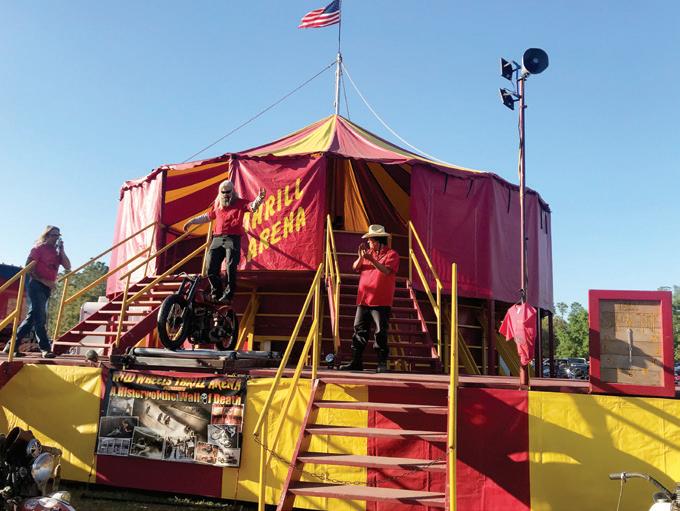
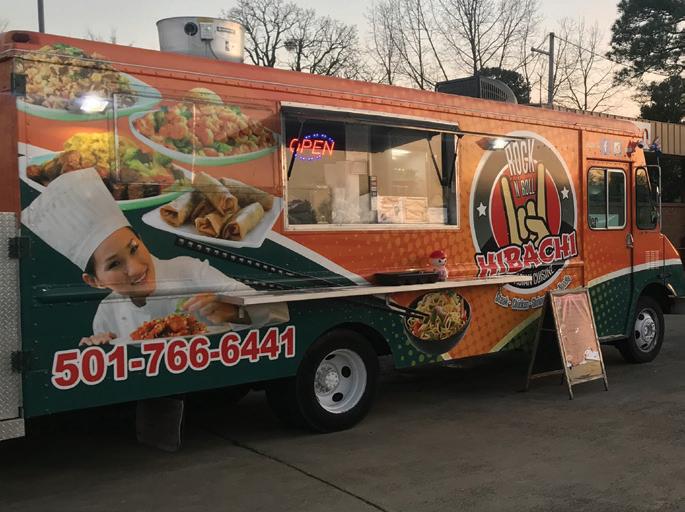

to the Daytona “Rally.” I expected to roll into Daytona and be greeted by an onslaught of thousands of bikers, complete with scantily clad woman strapped to their Street Glides and Def Leppard blaring from there onboard stereo systems, but no, not at all. I did however almost immediately get taken out by a group of riders that chose to blindly change lanes in front me as I approached in the left lane, so that made it feel more like a rally, but that was it. Where was the event? I thought to myself as I pulled into the Broken Spoke Saloon. It still felt like I was on the outskirts of town. I pulled in, parked my bike, and after making all the appropriate greetings, I inquired as to where the rally was. Turns out, and many of you may already know this, that the “rally” is spread out over 20 miles...that’s dumb, and almost immediately killed my enthusiasm for the entire thing, not that I’m much into big events anyway. So, on that note, I chose to stay for the show, one of 4 main reasons why I came to Florida in the first place and enjoy the company of great people I only get to see once in a great while.
Wait, four main reasons for going to Florida? Yes. The Cycle Source show was one, seeing my friend Lee ride the wall in the Wild Wheels Thrill Arena was two, getting to Key West to seal the deal on having choppered to both ends of Hwy 1 was three and visiting my buddy Fletch in St. Petersburg was four. I would successfully accomplish the tasks but let’s not get ahead of ourselves. The immediate next step from the Broken Spoke Saloon was to find my way to the Cackleberry Campground where I would meet up with the aforementioned Lee, witness him whip that vintage Indian around the wall of death and spend a night inside the motordrome, or sleep with the legends as they say. As I crawled into my sleeping bag and closed my eyes I could feel the history in the air, the distant cheers of crowds of days gone by and the smell of those old bikes, just feet away, calling out to be ridden. I’ll leave you with that for now and continue the saga on the next go around until then, go out and create your own stories, live the life you dream of, explore the world around you.
For more photos of this trip and others, visit me on Instagram @ charlietravelingchopper
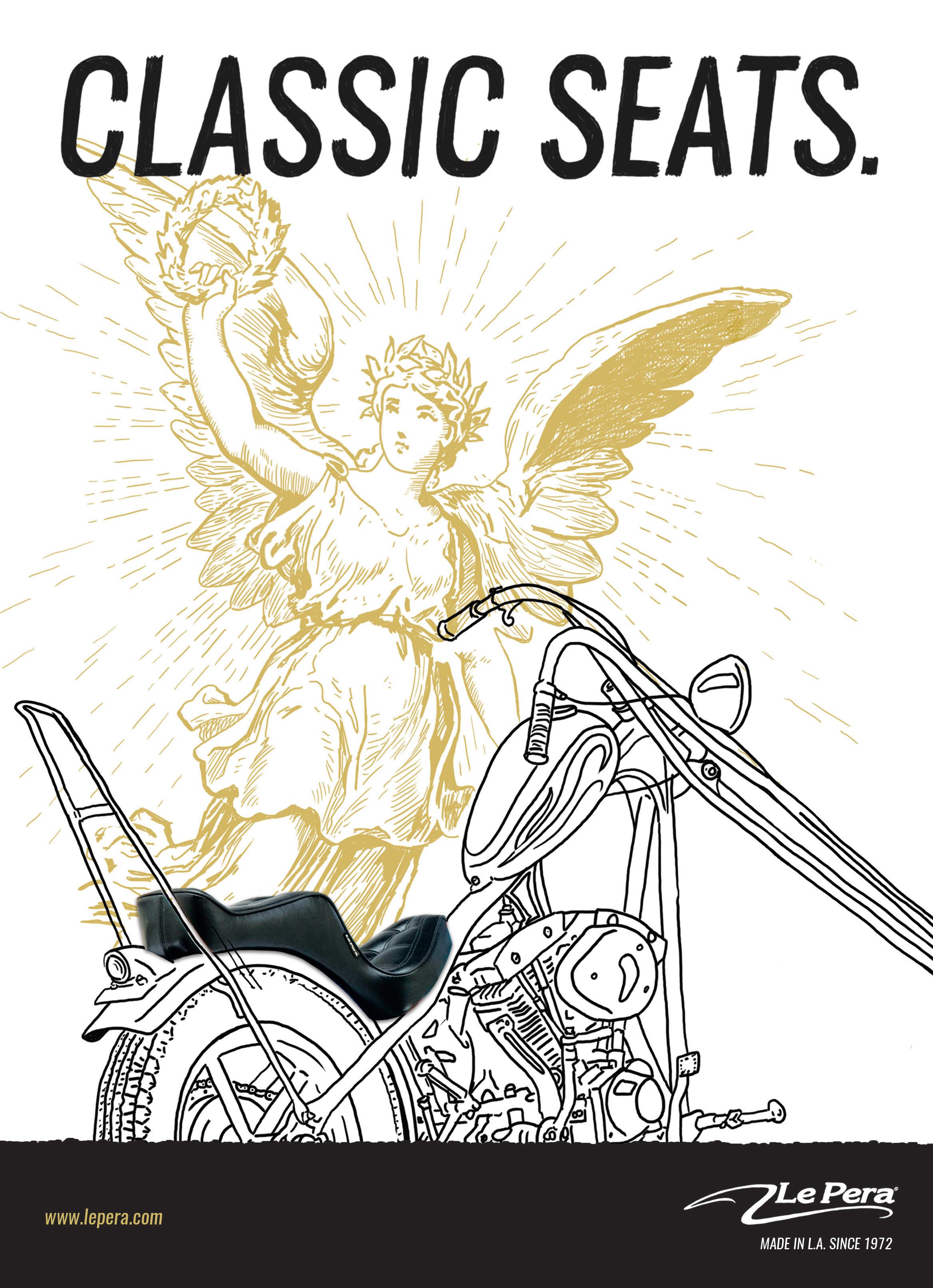
