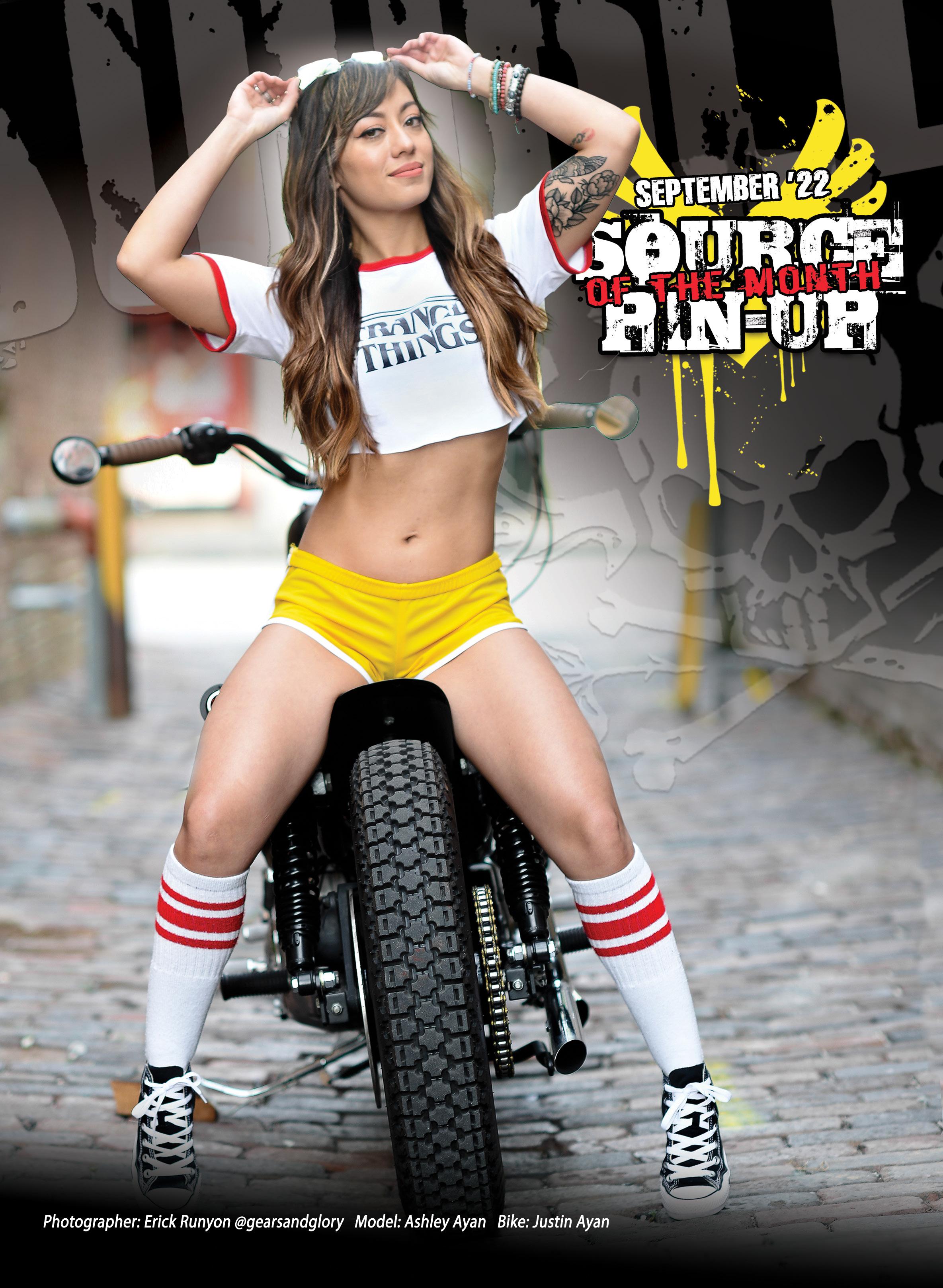
44 minute read
Pin-Up Of The Month

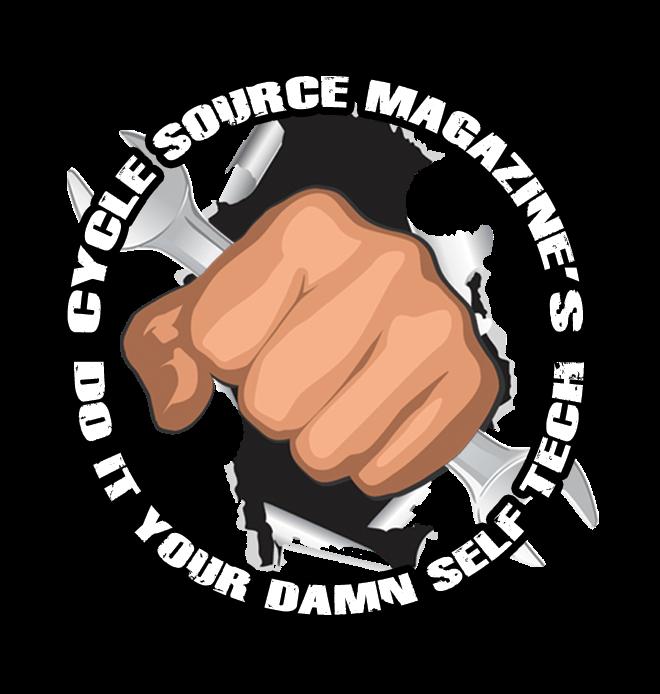
Advertisement
piston ring end gap…. It’s the gap between the end of the ring when it’s installed in the cylinder bore. This gap is necessary.... so, you can install the rings onto the piston. Gapping piston rings is important to the performance and reliability of the engine. The purpose of piston rings is to make compression and to transfer heat to the cylinder walls. Piston rings expand as the engine gets up to temperature. Too large of a gap allows blow by to the crank case and results in poor engine performance. Too small of a gap and the ring can over expand and cause cylinder and piston damage both are not good. So, setting ring end gap is crucial to any engine build. Take your time and go slow so your engine will go fast! On most OEM replacement style piston rings the ring end gap is preset to a specific bore size, but knowledge is Horsepower so check them. With aftermarket style piston rings, I prefer file fit rings, slightly larges so I can file fit them to the specific bore. Accurate end gap equals reliability and performance.
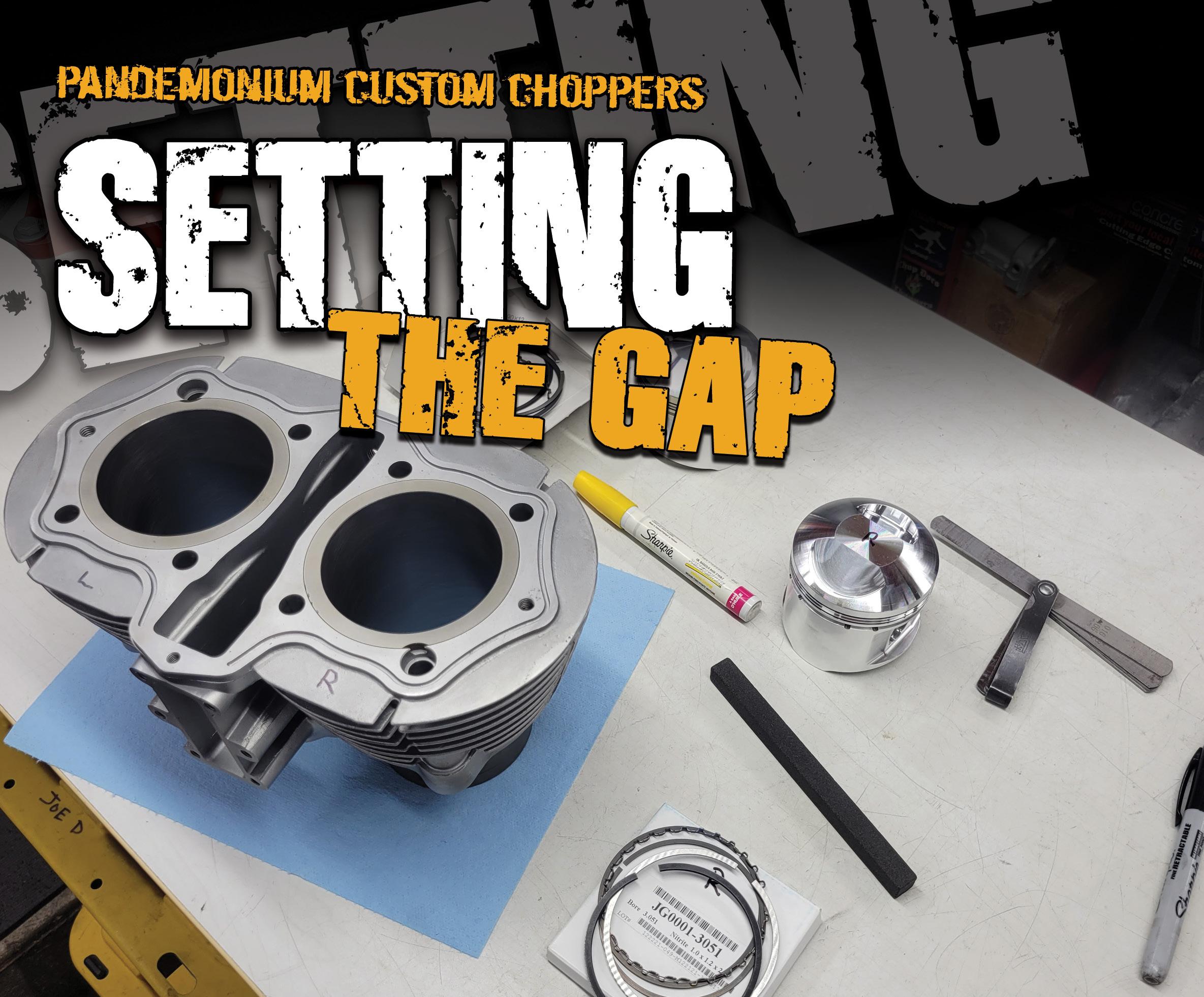
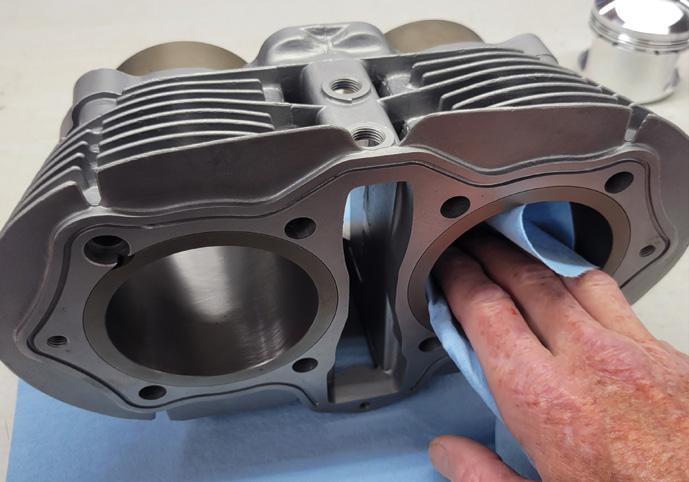
With my jug back from the machine shop, I’m installing aftermarket oversized pistons. I start the process by wiping the cylinder walls with a clean paper towel. Then I measure the bore. Typical rule of thumb for a gasoline engine is Bore X .0045 for the top compression ring. Then Bore X .0050 for the second ring. Both with a min of .015 gap. So, do the math and figure out what you need.
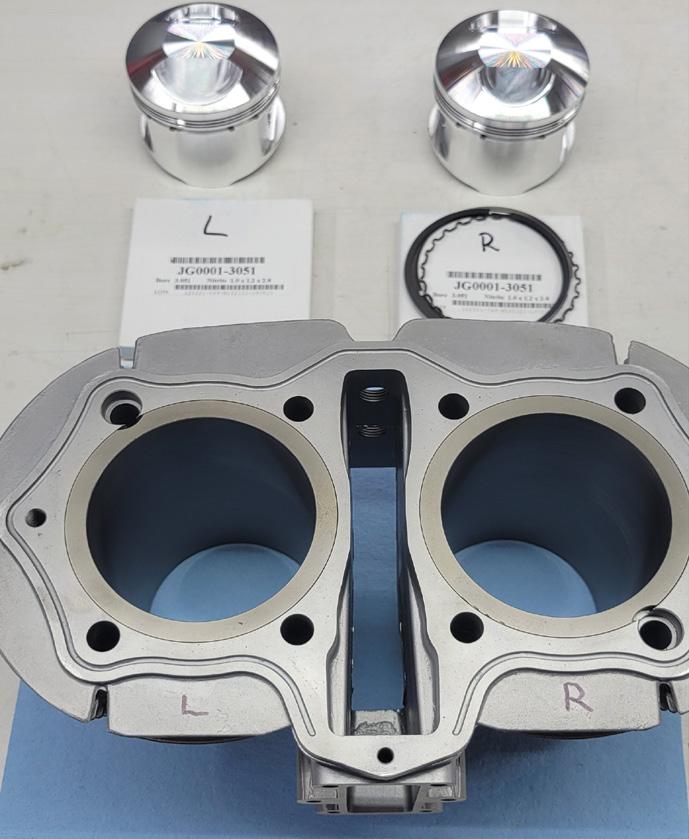
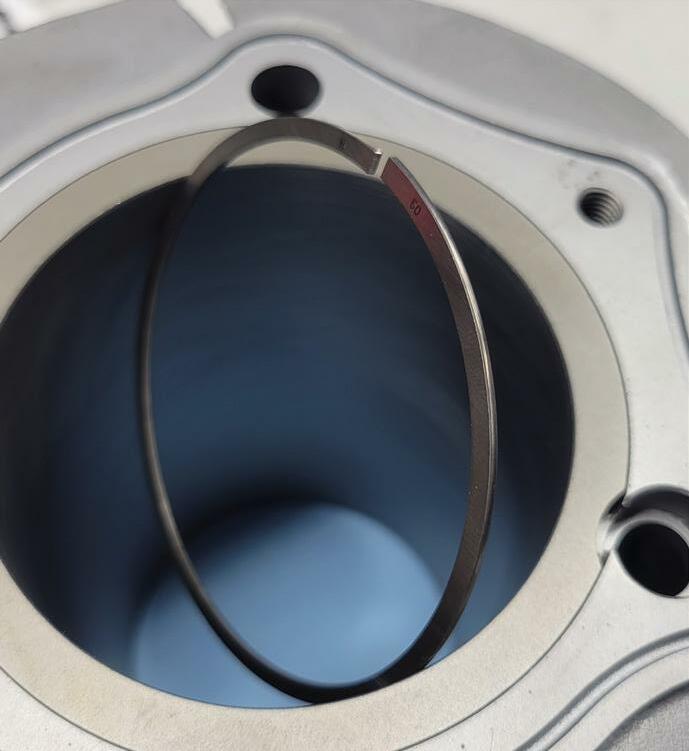
I insert the ring in the bore with the gap facing up and then rotate it into the bore. I then use my piston to square the ring into the bore about one inch down from the top. Now you can take a measurement using feeler gauges to see where your ring gap is at.
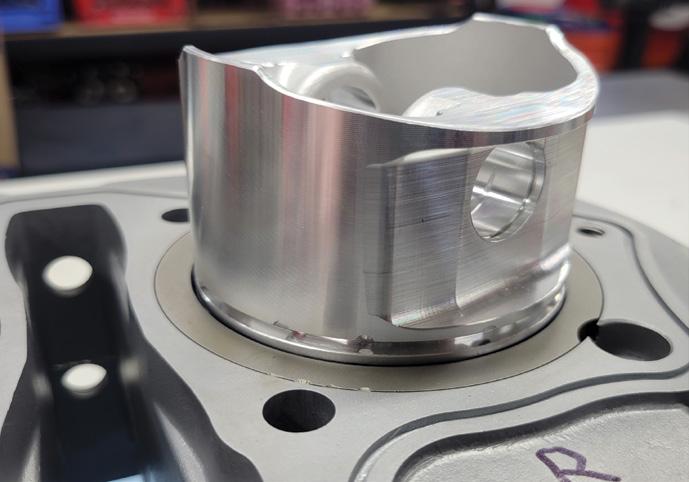

There are many ways to grind or file ring end gap. Always file inward with a file or stone. Filing outward can chip the outside sealing surface of the ring which is not good. I use an old school hand crank ring filer. It has a diamond wheel that removes ring material quickly. A couple of cranks can remove .001 no problem so I must go slowly. I then recheck the ring in the bore. Sometimes I

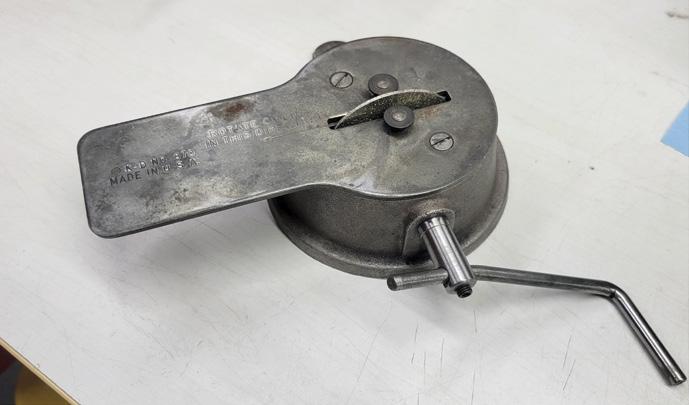

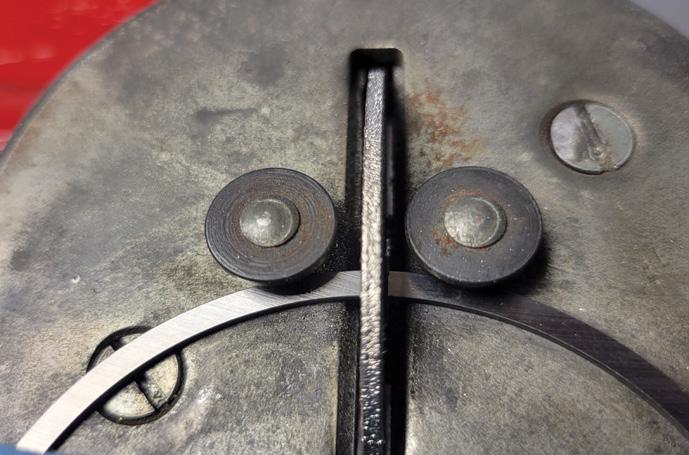
may have to do this multiple times to achieve the proper gap. You can buy reproduction versions of this ring filer on the internet.
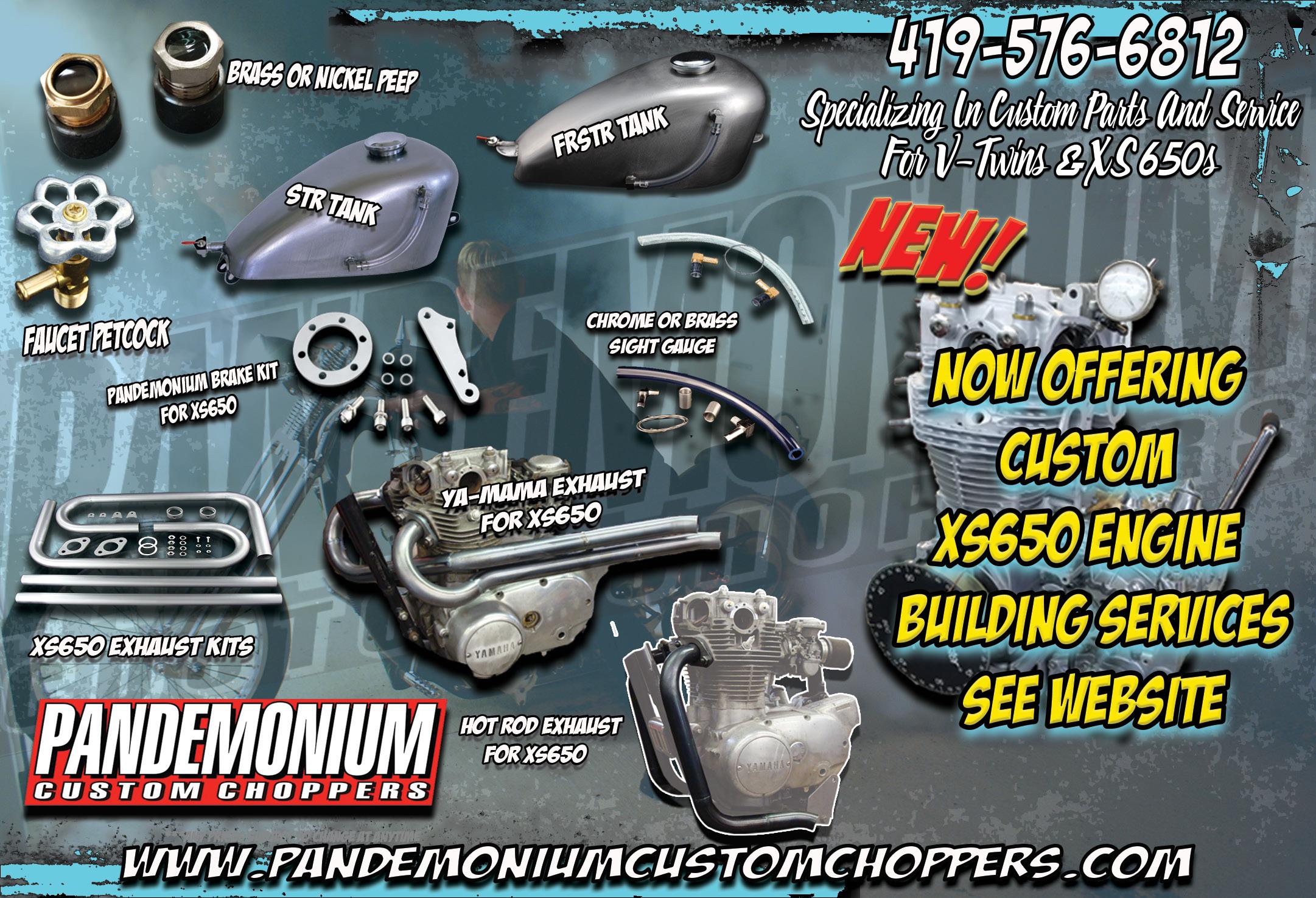
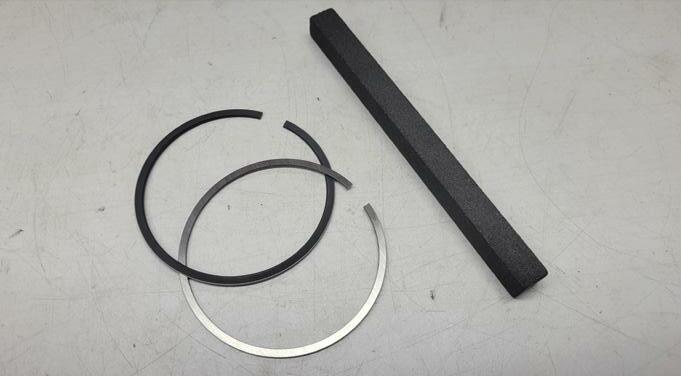
Once all the rings have been filed you will notice there is a slight burr on the filed edge. I use a hand stone to remove this burr. This is important so the ring can expand and contract with
heat and not be stuck in the piston ring groove because of the burr. Setting ring end gap is a particularly important part of a properly built engine. Take your time, be meticulous, and you will be rewarded with a great running and performing engine. If there is something that you would like to see a Tech article on? Please call me or email me with your idea! If you have any questions, please feel free to call me at the shop anytime 419-576-6812 Daniel Donley Pandemonium Custom Choppers Facebook- Pandemonium Custom Choppers Instagram – pandemoniumc2 happydandemonium@gmail.com pandemoniumcustomchoppers.com
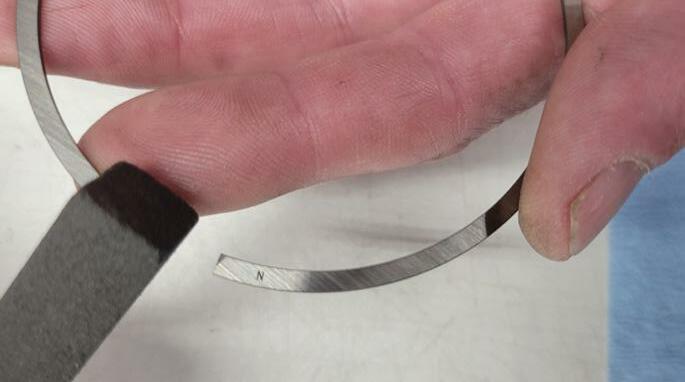
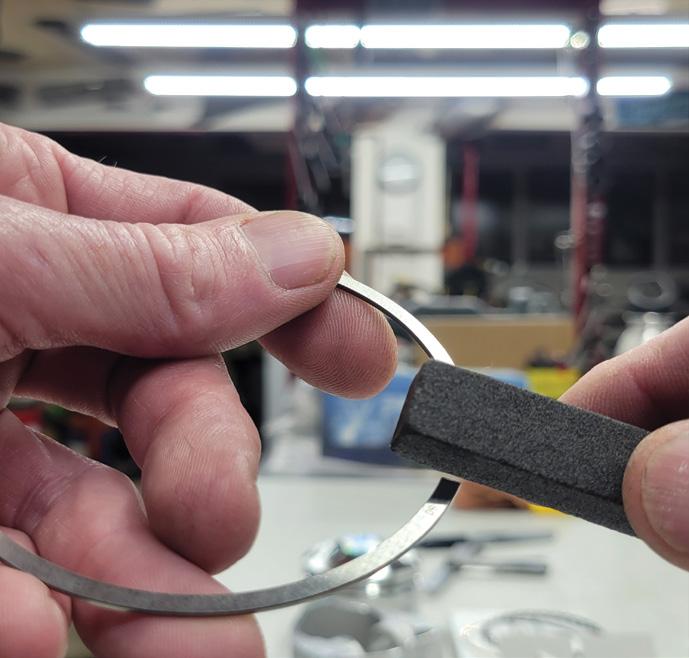
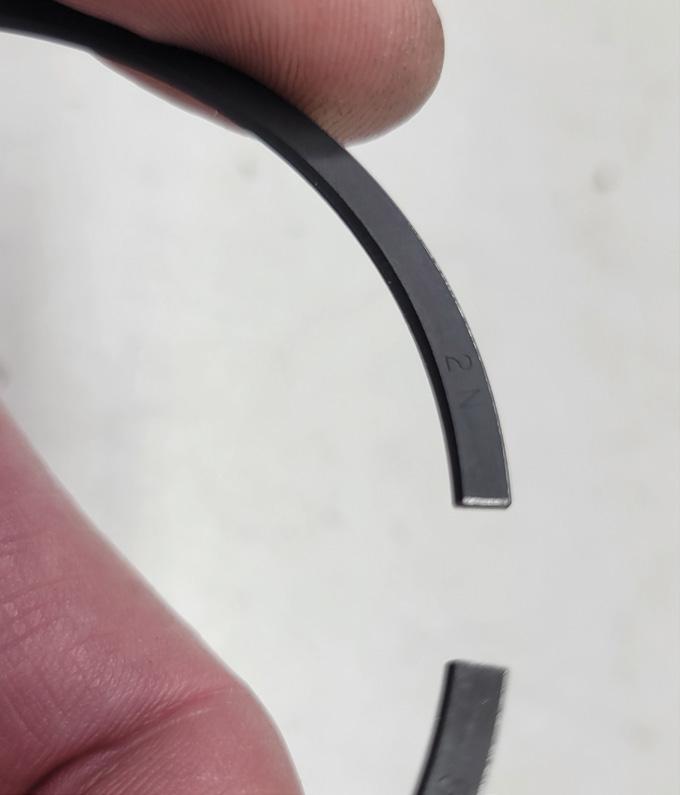
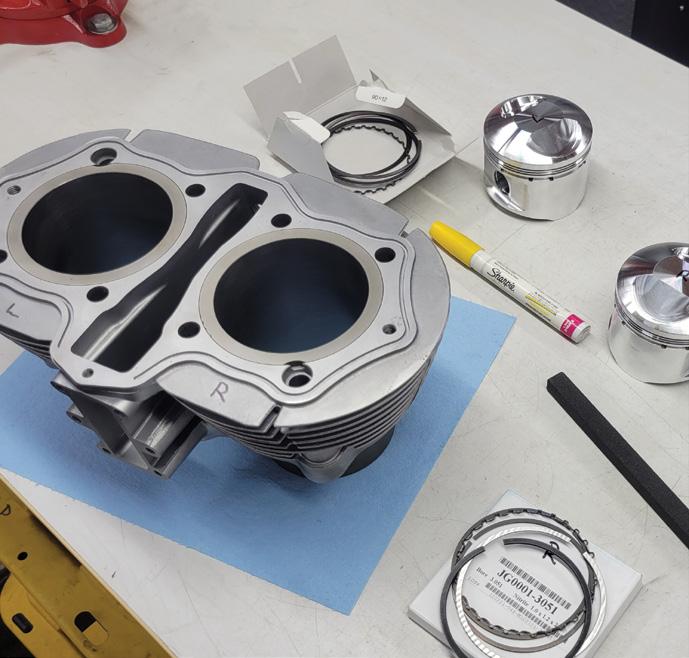
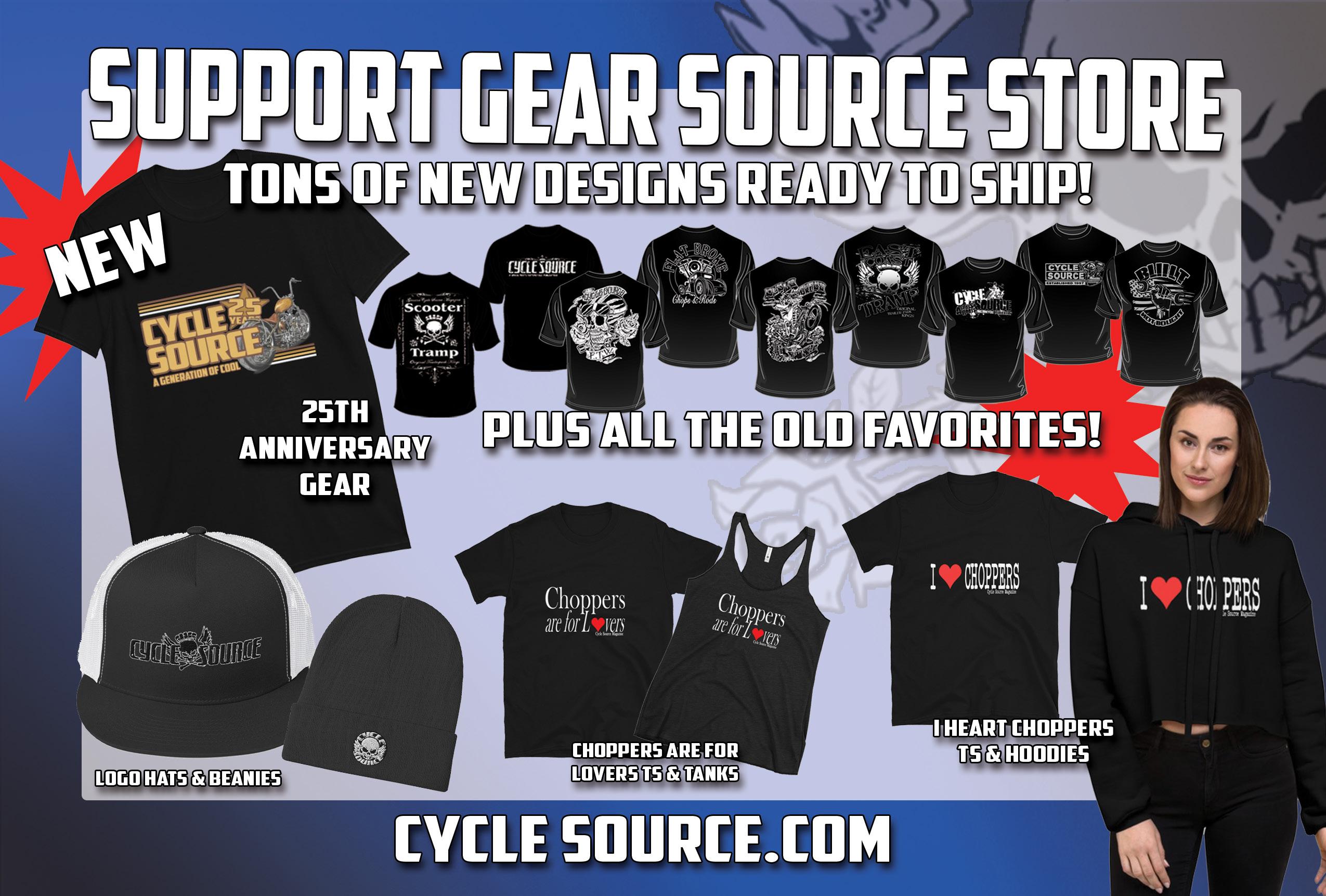
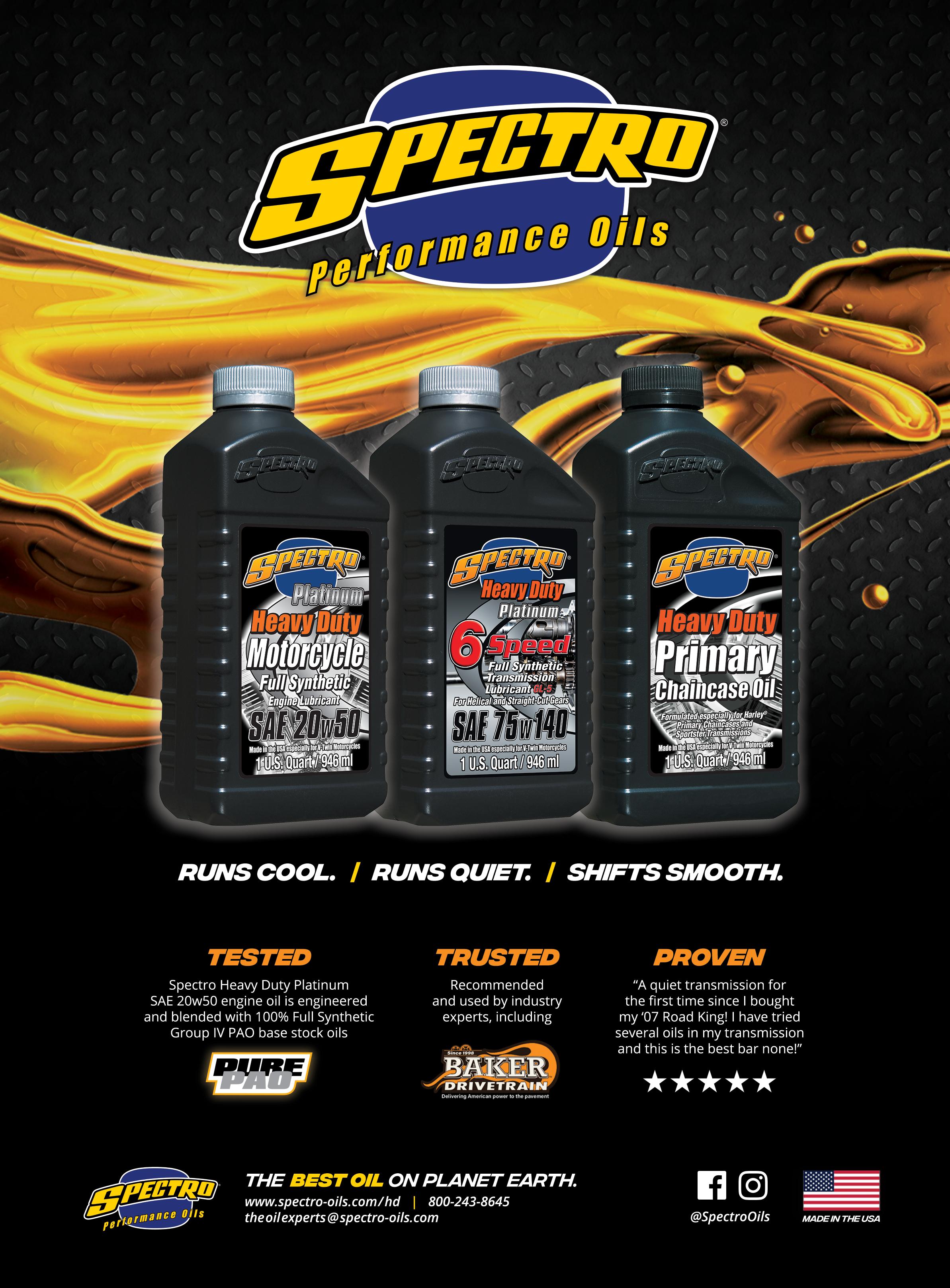
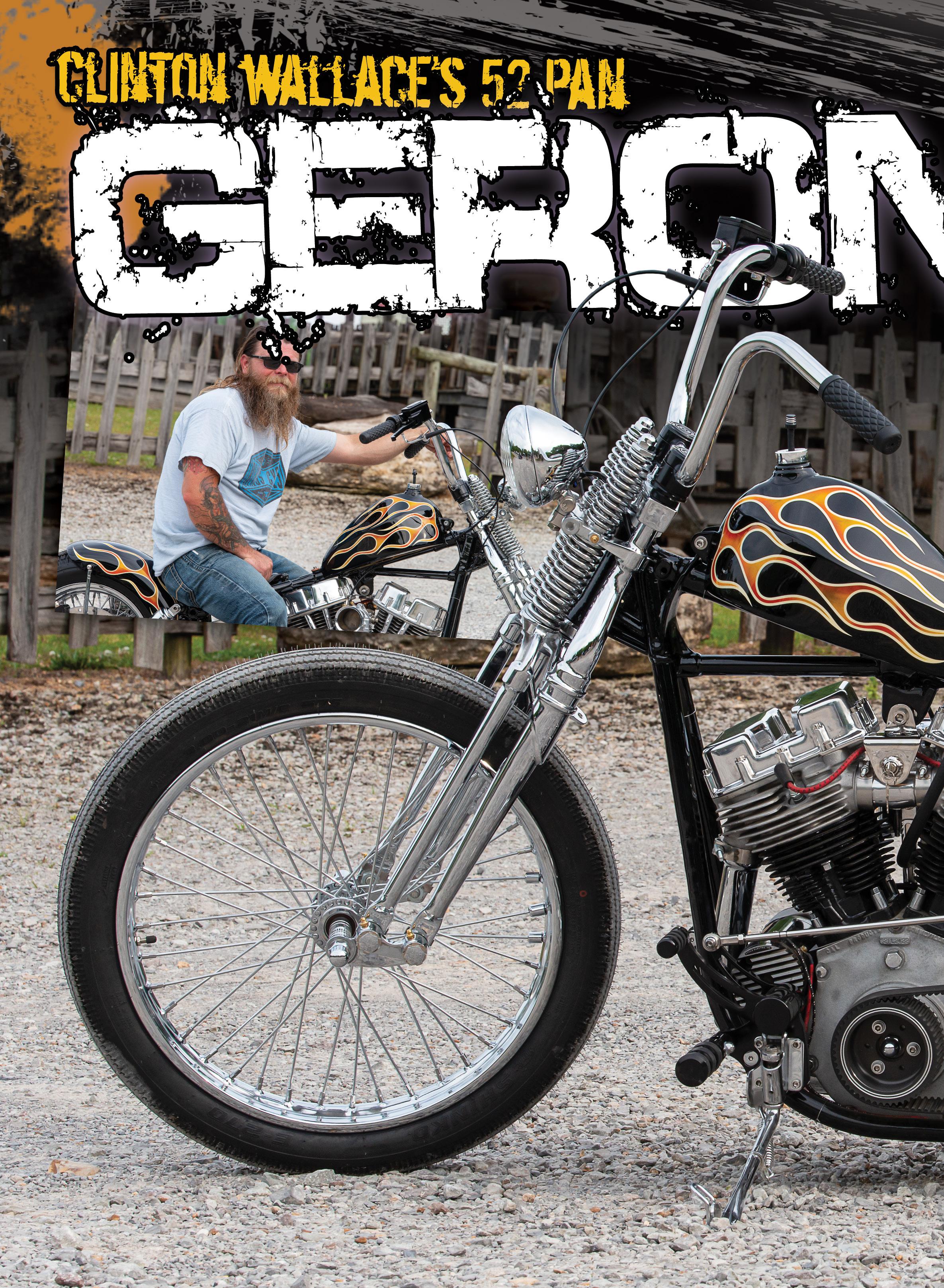
Article By: Roadside Marty Photos By: Melissa DeBord
for long-time readers of this magazine, you might recognize Clinton Wallace. We have featured a few of his bikes before. He’s definitely our kind of people.
Clinton and his wife Bobbi live in
Cleveland, Texas, and he makes his living working in the oil fields by day. At night he spends his time wrenching on bikes. In other words, he’s a lot like most of us. This build started like most, with a general idea of using a swingarm instead of a rigid frame. Clinton’s dad had a guy that worked for him that had a 1980 Shovelhead that he wasn’t gonna do anything with. So, naturally, Clinton inquired about it, and the guy said just come get it. Now, I’ve got to say, I’ve never had someone I didn’t really know give me a Harley-Davidson, but that’s precisely what happened. Clinton got the Shovel running but didn’t have any plans for it, so he eventually tore it down to the frame. Clinton has always been a big fan of Jeff Cochran from SpeedKing Racing. Jeff’s bikes are rideable customs that perform just as good as they look. So, it made sense that Wallace started with a drop seat conversion kit from SpeedKing. From there, he modified the frame at his home shop. The frame sat for about a year. While Clinton was looking at the selection of builders for that year’s Tennessee Motorcycles and Music Revival when low and behold, he saw his name included on the roster. He immediately called Bill Dodge from Bling’s Cycle to ask how he got
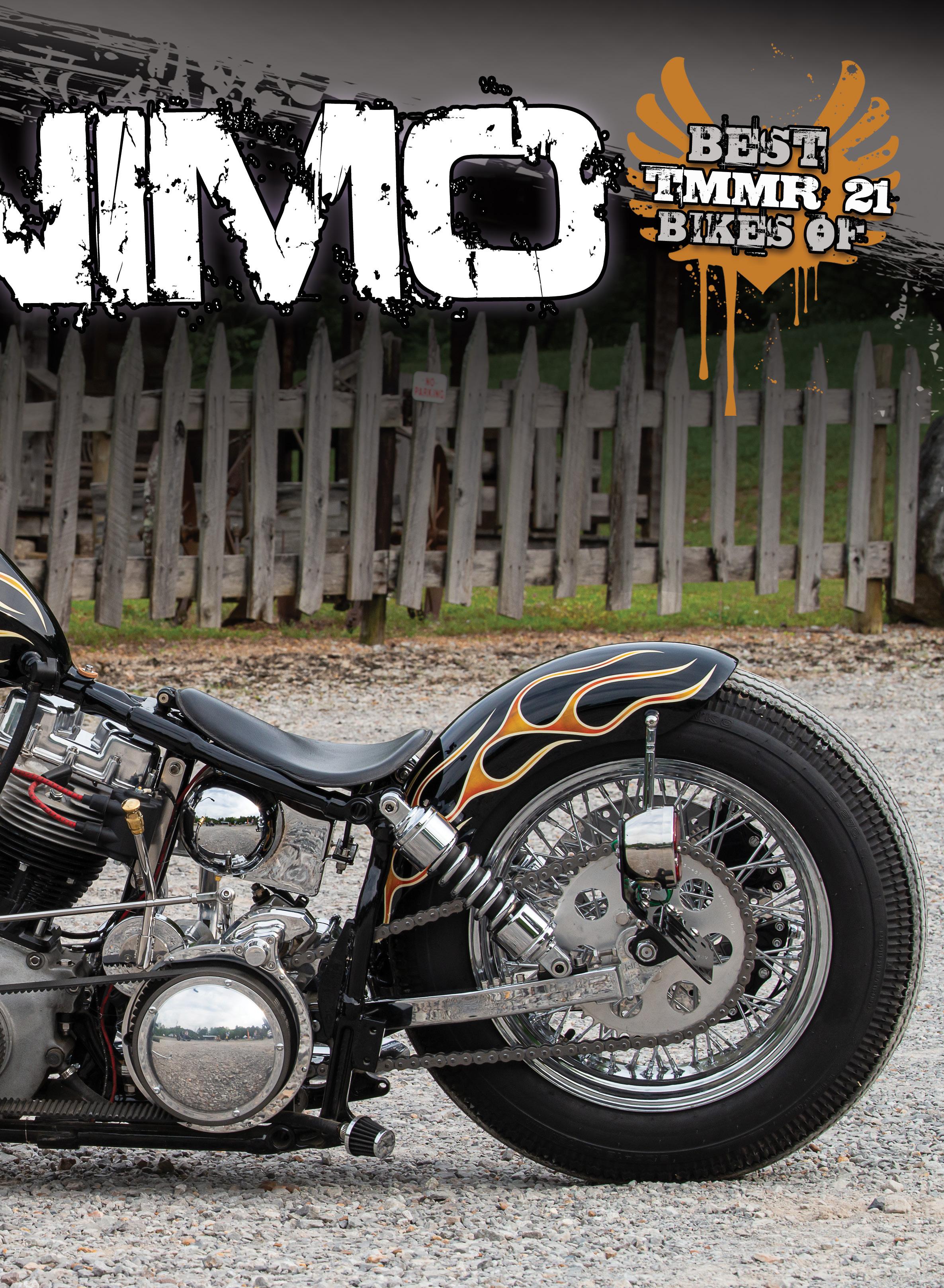
on the list. Bill responded by asking, “What are you gonna bring?” Well, you can’t ignore an invite like that, so Clinton kicked this build into high gear. Since the frame was already started, he decided to stick with some of Jeff’s other signature series parts. The first was the rear swingarm, which is fully adjustable, so you raise or lower your bike with simple adjustments instead of changing your rear shocks. Next up was one of Jeff’s Torpedo oil tank kits that Clinton mounted to compliment the curves of the drop seat conversion. OEM Harley frames from 1958 to 1964 are the original drop seat frames because Harley didn’t introduce an electric start until 1965, which required a new style of oil tank with a new location for the battery. The Torpedo oil tank gives enough clearance to run a late model starter and a smaller gel battery, giving you multiple options. I also think the dual rear caliper bracket Jeff sells, which allows you to operate one caliper from the rear master cylinder and the other by the traditional front master cylinder, is ingenious. It is a simple but highly useful combination.
The heart of this build is a 1952 Panhead motor that was rebuilt to stock specifications by Dan Carr from DC Choppers. Nothing wrong with larger displacement engines, but a stock 74” motor with a properly tuned S&S Super E carburetor is pretty hard to beat. Clinton fabbed up the exhaust to follow the lines of the bike. A 2” BDL belt drive connects the motor to the 1962 transmission, which is also the electric start version. The rear fender is another SpeedKing item that wraps around the rear wheel perfectly, as is the seat pan.
The cast aluminum tank is from Bling’s Cycle. It is
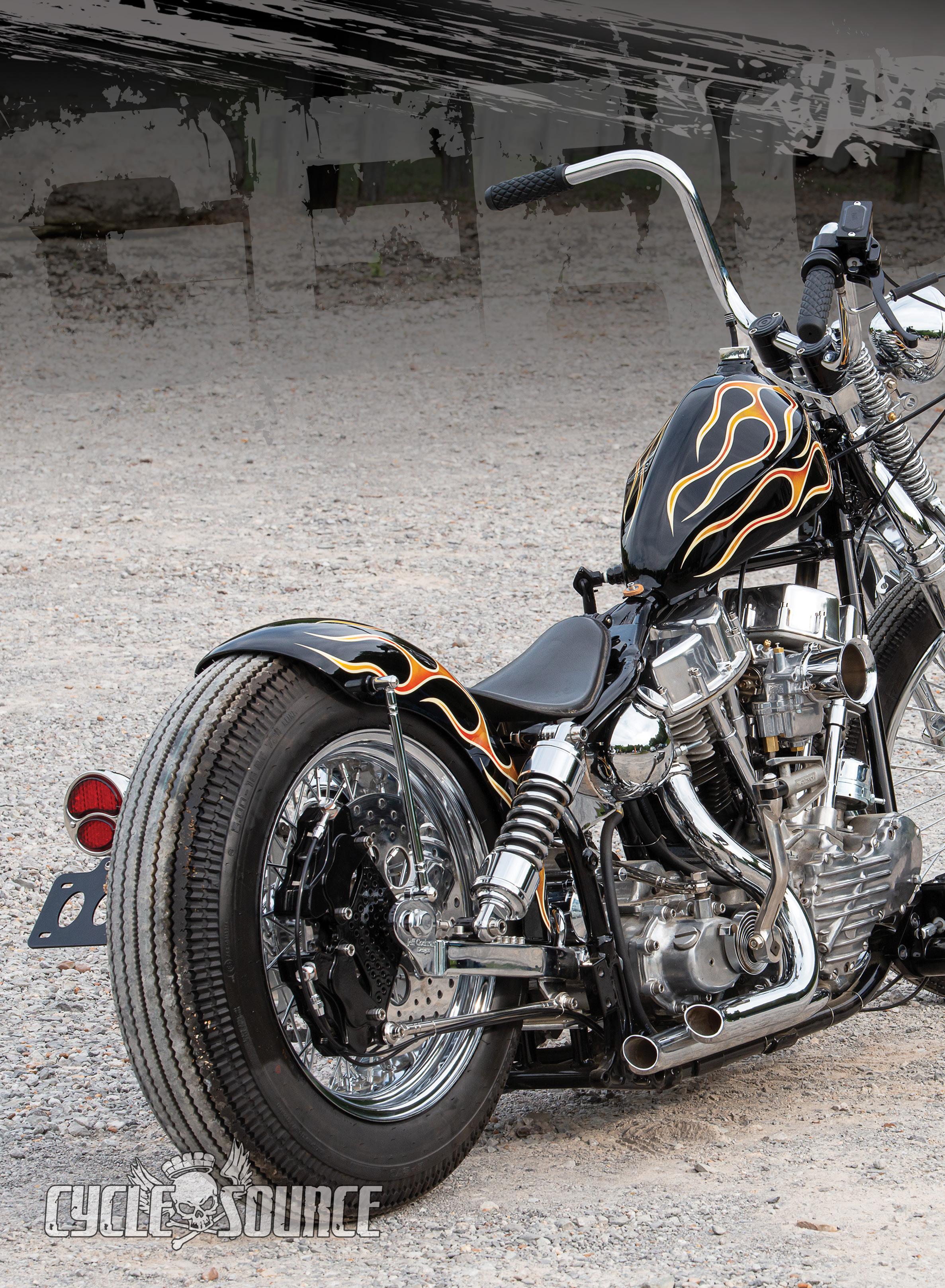
sold as a kit that comes in two halves so you can modify the tank to your frame’s backbone. When he tried to order the tank, Covid was in full swing, and Bill didn’t know when he would get any more material to make them. Dodge knew that a of his customers had purchased them but had no plans to use them right away. Luckily Clinton scored one thru that avenue...thanks, Willie! That awesome flame job was laid down by Scott at Chemical Candy Customs. Those Texas boys sure know what they’re doing. Chroming is always an issue with any custom build, but Speed Sport Chroming stepped up and got things done in a timely fashion. The front wheel is a spool 21’ with a 16” rear, which in my humble opinion, is the best combination for the perfect stance. A Mid USA reproduction springer was used and kept at stock length so that

Owner: Clinton Wallace City/State: Cleveland, Tx Builder: Clinton Wallace Year: 1952 Model: Panhead FL Value: $20,000 Time: 6 months ENGINE Year: 1952 Model: Panhead FL Builder: DC Choppers Ignition: Stock Displacement: 74in Pistons: Stock Heads: Stock Carb: S&S Super E Cam: Stock Air Cleaner: Exhaust: Clinton Wallace Primary: 2” BDL TRANSMISSION Year: 1962 Make: Harley Davidson Shifting: Jockey FRAME Year: 1980 Model: Harley Davidson FX Rake: Stock Stretch: None Forks Builder: Type: Springer Triple Trees: Extension: WHEELS Front Wheel: 40 Spoke Size: 21” Tire: Shinko Front Brake: Never Rear Wheel: Size: 16” Tire: Shinko Rear Brake: Dual Wilwood PAINT Painter: Chemical Candy Customs Color: Type: House of Kolors Graphics: Chemical Candy Customs Chroming: Speed Sport Chroming ACCESSORIES Bars: 12” APES Risers: Hand Controls: GMA Foot Controls: GMA Gas Tank(s): Blings Cast Tank Oil Tank: Speedking Front fender: None Rear Fender: Speedking Seat: Speedking Headlight: Throttle Addiction Tail light: TC Bros. Speedo: None Photographer: Melissa DeBord the adjustable rear swingarm keeps the bottom frame rails parallel to the ground instead of a grasshopper look. Both wheels use Shinko tires and have a traditional tread pattern.
For the bars, Clinton went with 12” traditional style ape hangers, giving the bike a timeless look and comfort. The front master cylinder and foot controls are GMA items that contrast nicely with the black frame and base coat. The headlight is a chopper style from the guys at Throttle Addiction, and the rear taillight is from TC Bros.
This bike is a good representation of its owner, a no-nonsense, clean custom that runs just as good as it looks. Thanks for sharing your bike with our readers, Clinton. We look forward to seeing what you come up with when you build that 1980 Shovelhead!


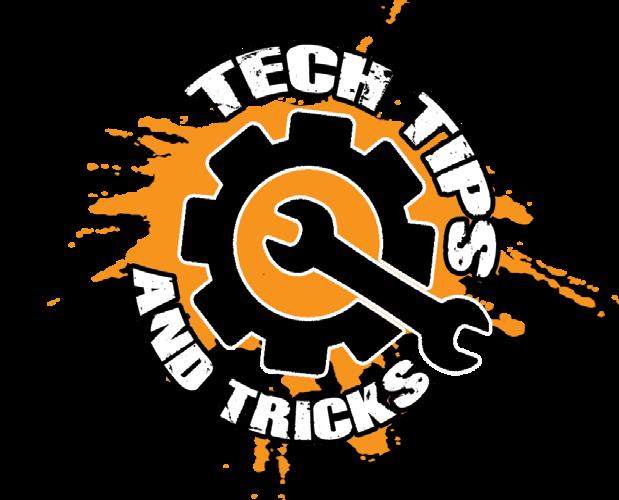
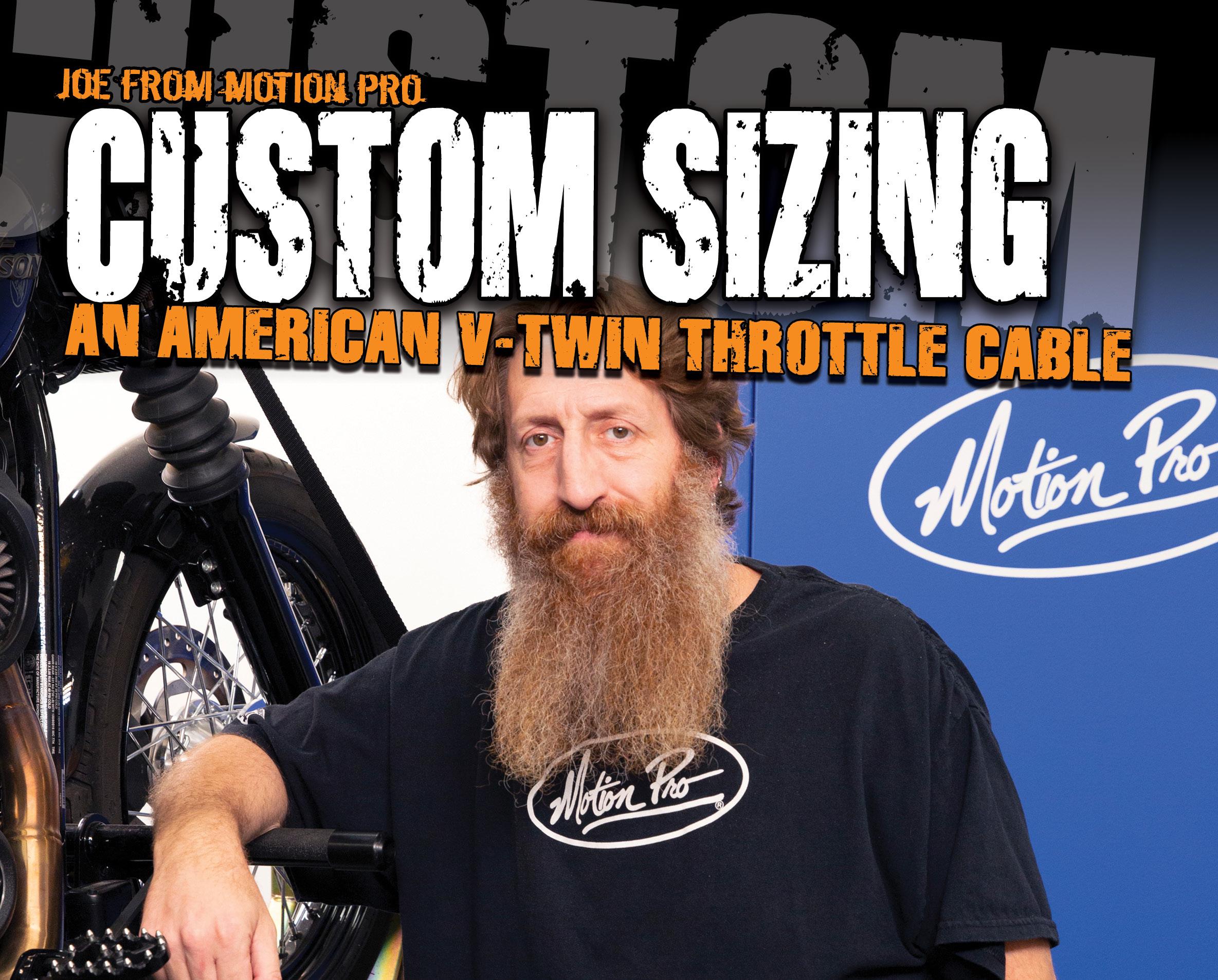
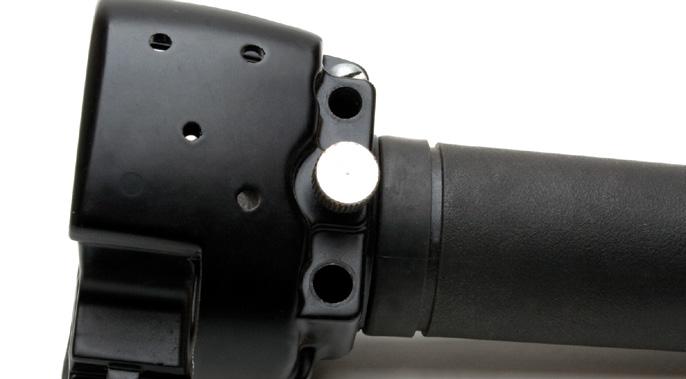
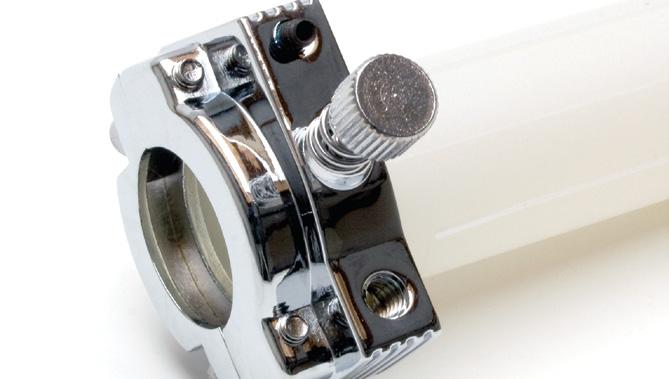
otion Pro stocks a huge number of American V-Twin cables, and often times they have the right cable in stock and ready M to ship. If they don’t have what you need, the Motion Pro custom cable shop can make just about any cable configuration. There are many variations in cables, and getting the correct cable is their top priority.
To determine the right specifications for a throttle cable you need to know what type of throttle and carburetor is being used, how long the cable needs to be, and what type of elbow is required so it can be routed properly.
The first thing you need to determine is what type of throttle assembly is being used. Is it a singlecable pull-only twist throttle or a pushpull using two cables? If it is a single cable pull-only throttle, what is the thread pitch of the fitting that goes
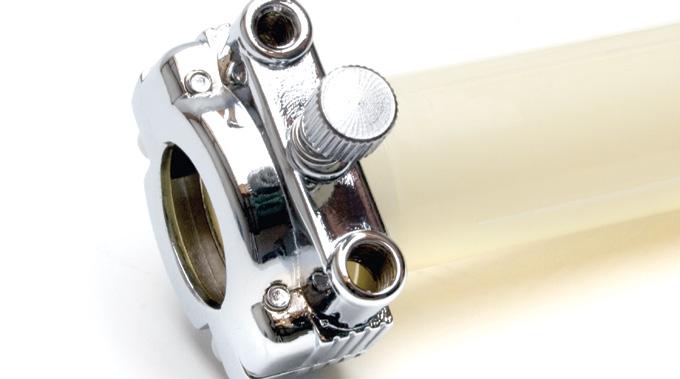
Article And Photos By: Motion Pro
into the pull throttle assembly? Is it 1/4-20 or 5/16-18? Early model OE style pull-only throttles had a 1/4-20 thread pitch. This design was stock on 1980 and earlier H-D® models. However, many aftermarket pullonly throttle assemblies have a 5/16-18 thread pitch. This allowed OEM replacement pull cables to fit 1981-1995 H-D® models.
If it’s a dual cable push-pull throttle – does the throttle have a screw-in fitting or the snap-in style? Push-pull screw-in throttle assemblies were used on H-D® models from 19811995 and have a 1/4-20 thread pitch on the idle cable and 5/16-18 thread pitch on the pull cable. Pushpull snap-in throttle assemblies are used on H-D® models from 1996 to present.
With the throttle identified, the next item to identify is what bend is needed for the throttle elbow.
81-95 PUSH-PULL SCREW-IN
1980 EARLIER PULL ONLY

Motion Pro stocks American V-Twin used with the stock throttle cable throttle cables elbows in 90, 70, and found on 1992 and later big twin CV 45-degree bends. 90-degree elbows are used mostly on Dyna® and Softail® models, 70-degree elbows are used on bagger models, and 45-degree elbows are used mostly on Sportster® models. Any of these bends can be used on any of the throttle references in paragraph 3. This part comes down to what the best fit for the bike is.
Once the throttle and elbows have been identified, the next thing to confirm is the specific carburetor. While most carbs used share the same cable components, determining the correct carburetor is critical for identifying the proper cable. If it’s a Mikuni carb, it needs to be confirmed which Mikuni carb is being used. While the Mikuni HSR carb is the most common, there are two different designs of this carburetor. Is it an old or new style Mikuni HSR carb? Mikuni carburetors. The Mikuni HSR carbs introduced the new HSR carb many will have a white plastic wheel that years ago and designed it to be the throttle cable inner wire wraps
around and is located on the right side of the carburetor. The old-style Mikuni HSR does not have the white plastic wheel, and the throttle cable bracket is located on the left side of the carburetor. Other Mikuni carbs are used on American V-Twin applications. Their usage has slowed considerably, like the Mikuni HS40 (TM40-6) and Mikuni 5/16-18 FITTING 1/4-20 FITTING SNAP IN FITTINGS VM round slide carbs. If it’s an S&S carb, it’s generally going to be a Super E or G model, you will need to 90 DEGREE ELBOW verify if the carb has the tall or 70 DEGREE ELBOW short bracket. In 2000, S&S started providing their carbs 45 DEGREE ELBOW with two cable brackets. The shorter bracket was designed for 1981-1989 big twin model applications carbs and will generally work with stock cables for these machines. The tall bracket was designed to be used with the stock cables found on 1990 and later big twins with a CV carburetor. S&S offers other carbs like the Super B,

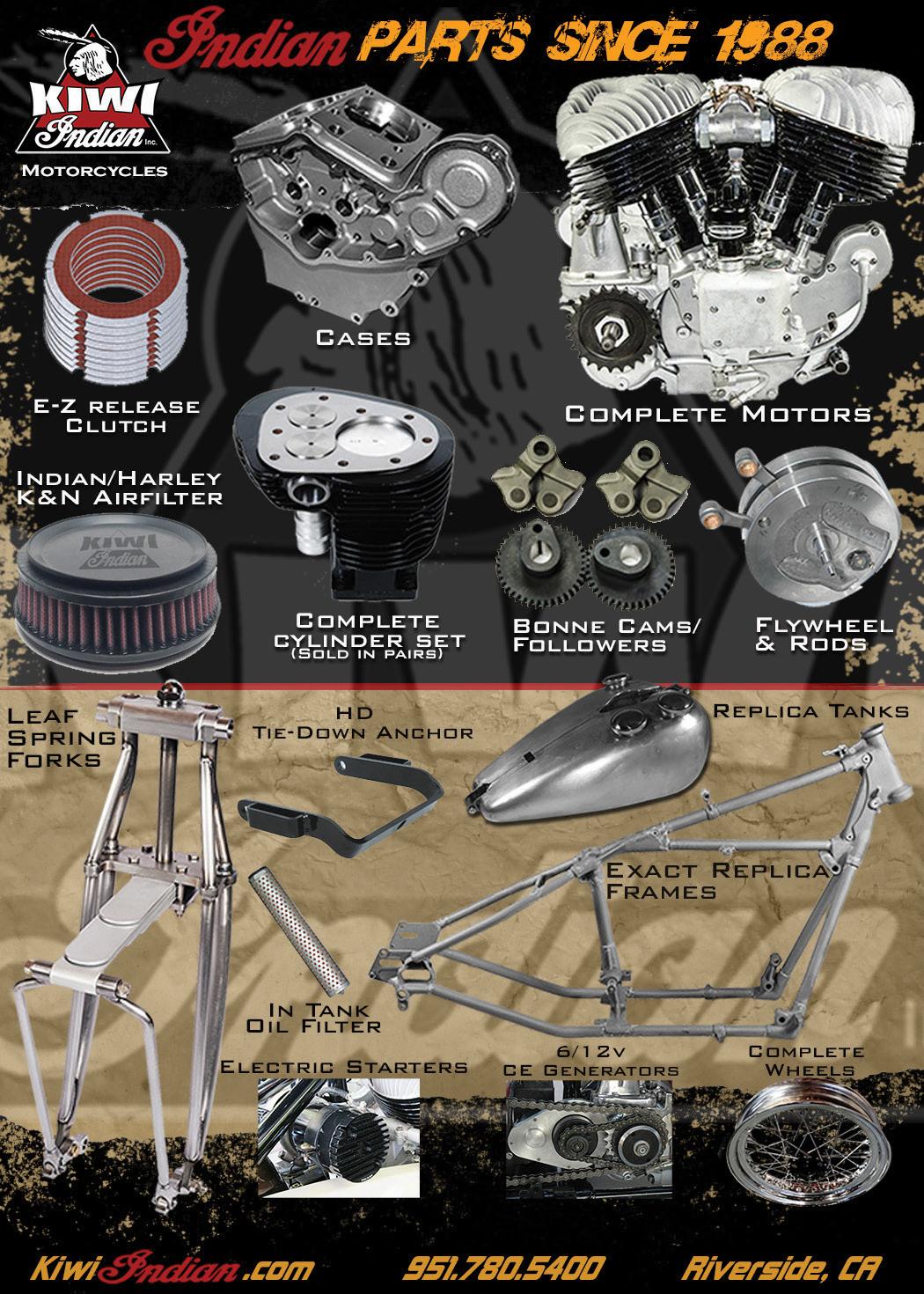
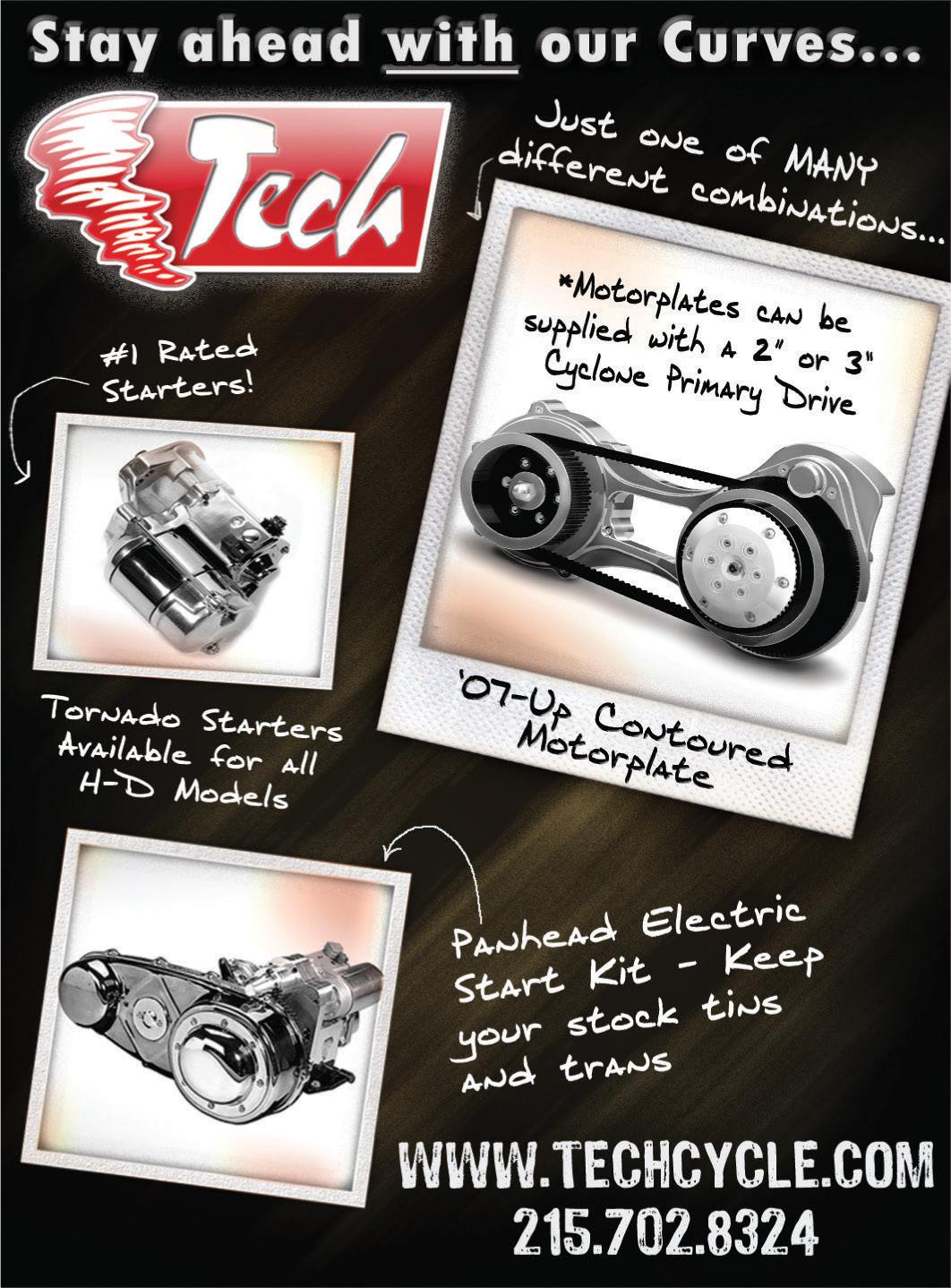

MIKUNI HS-40
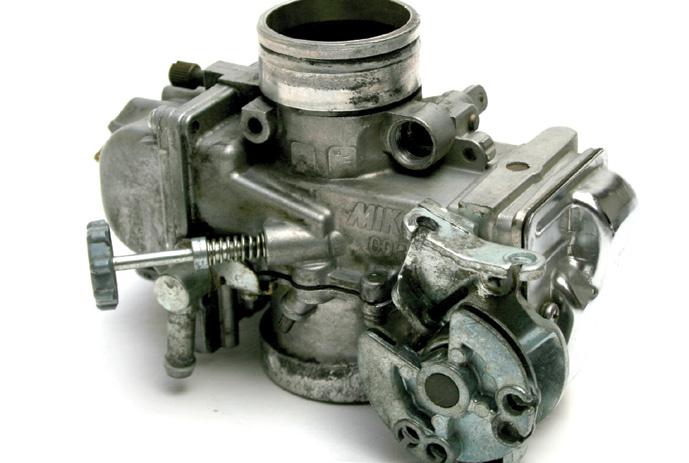
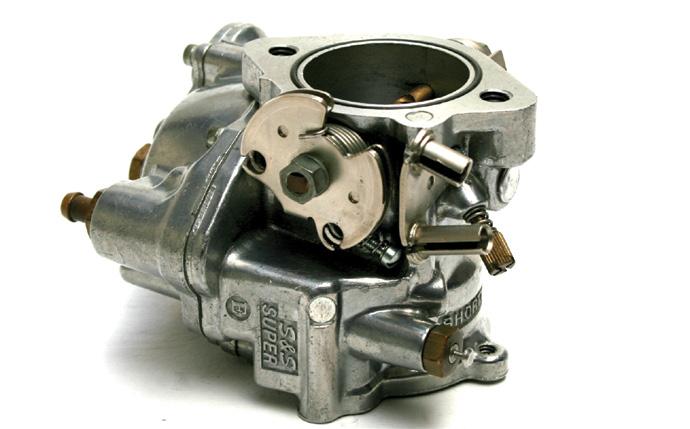
MIKUNI HSR042-45 ALT1
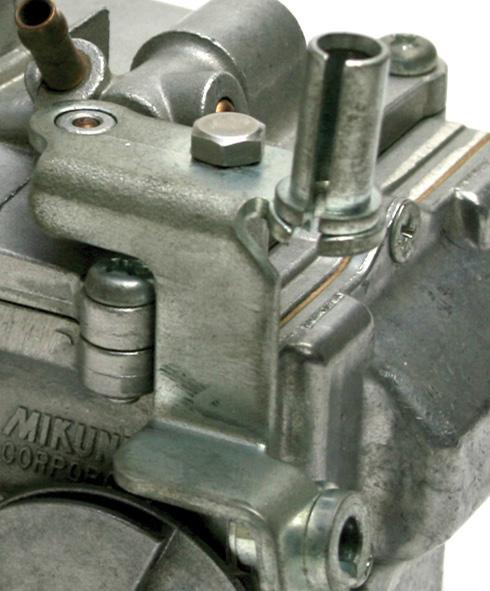

MIKUNI HSR042-45 NEW MIKUNI HSR-42

S&S.SUPER BRACKET 1
S&S.SUPER E WITH TALL BRACKET and Super D. The Super B carb uses a set screw to hold the cable inner wire and does not require a cable with a defined free length. Motion Pro rarely gets requests on machines using Super B carbs because a replacement cable for these carbs can easily be made by finding a cable with the correct throttle elbow fittings and the correct housing length and then cutting the wire fitting off the carb side of the inner wire.
With the carburetor, throttle and elbows identified, the only thing left is to confirm the housing length. This needs to be determined by the individual working on the bike. This cannot be determined with confidence by supplying handlebar and riser information; there are just too many variables. The cable needs to be long enough to allow for proper routing and allows the handlebars to be turned lock to lock without tensioning the cable. Also, the customer will not want the cable to be too long to interfere with the bike’s operation and/or other cables and wiring.

proper measurment for ordering a throttle cable
To measure V-Twin throttle, measure the housing length, including the housing end fittings that are straight with no bends, excluding the elbow fitting that goes into the throttle. The cable housing is the exterior vinyl portion of the cable.
Motion Pro throttle elbows are 4 inches long, but not all manufacturers’ elbows are the same length.
The easiest way to determine the correct cable length is to determine the length of the existing cable. Suppose you need a longer than stock cable. In that case, the best way to determine the additional length required is to leave the stock cable installed into the carburetor and routed properly, then measure the extra length needed to reach the throttle and allow for proper movement of the handlebars.
With all the above information, the next step is to see if Motion Pro has an off-the-shelf cable that meets all the necessary criteria. An off-the-shelf cable will cost less than a custommade cable and can be shipped right away. If all the information is confirmed and no cable is available off the shelf, Motion Pro can always custom make it. Custom cable builds generally take at least a week or more to complete.
Need further assistance? Visit our Custom Cables section or give us a call, and they will be happy to walk you through the process. Contact Us: 650-594-9600 cables@motionpro. com

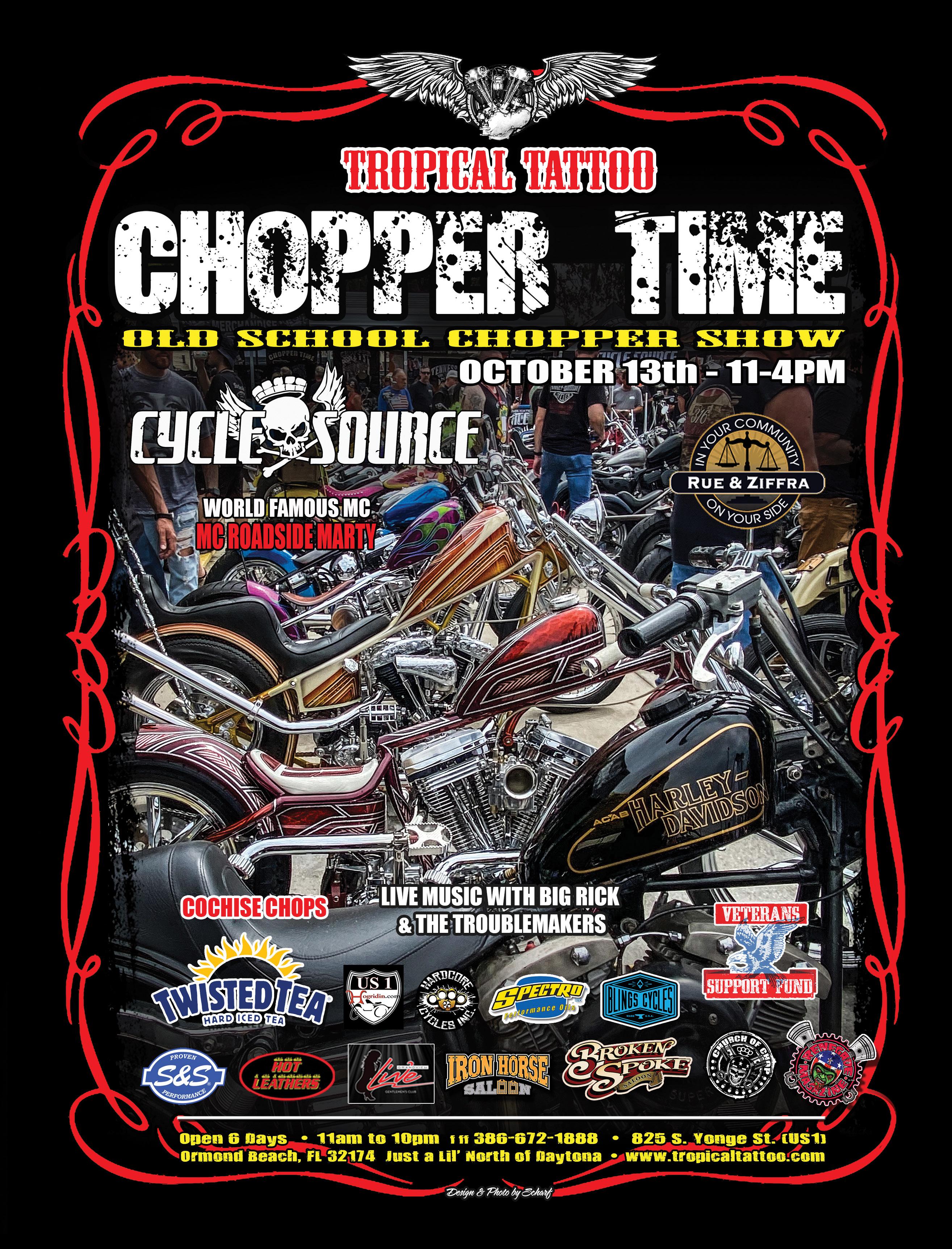
Article By: Heather Callen Photos By: Heather Callen & Marjorie Kleiman
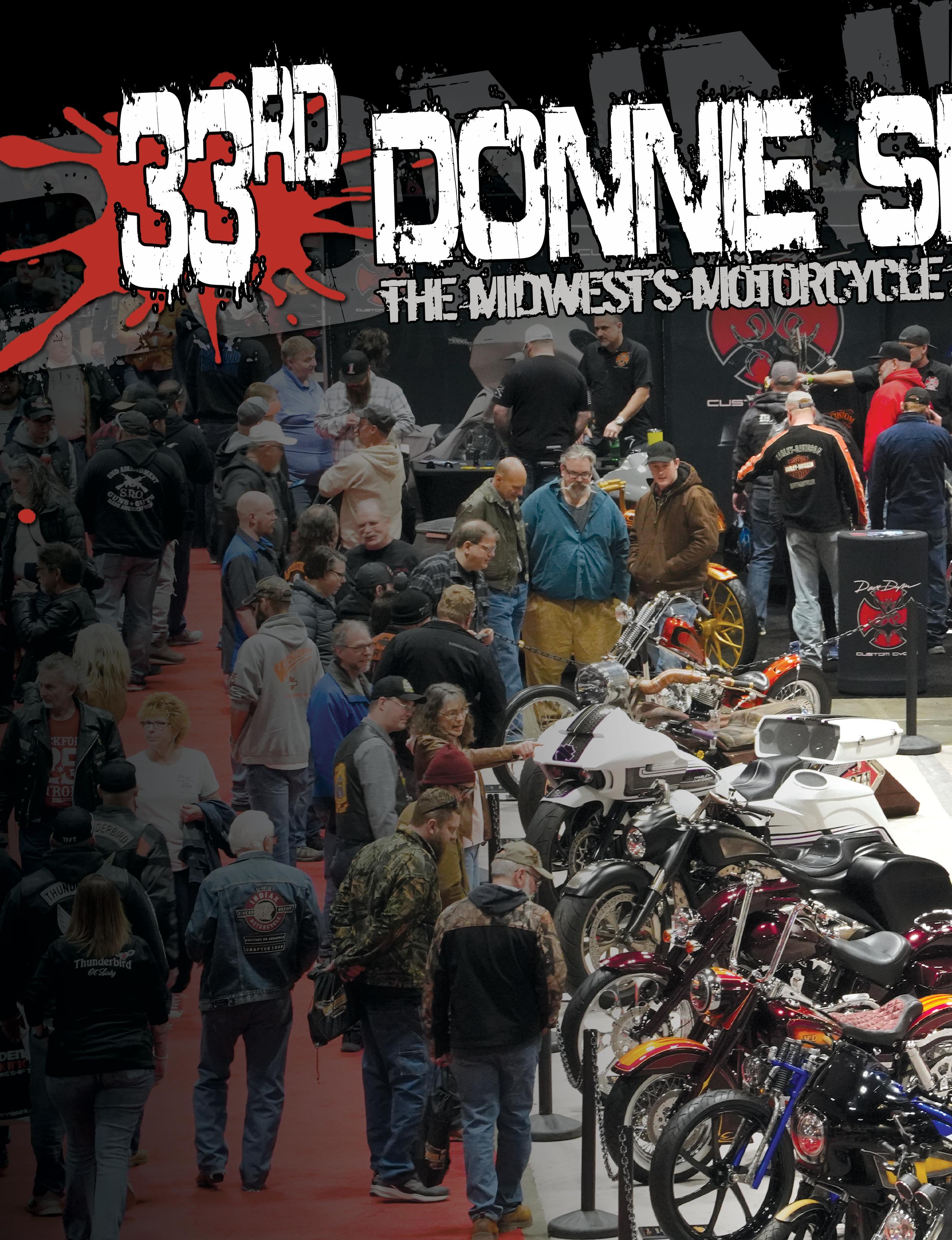
let me set the scene for you. It’s the end of March. Chris and I had just spent 10 days in glorious 80-degree temps in Florida, ushering in the motorcycle season at Daytona Bike Week. From the Sunshine State, we headed 1500 miles north to St. Paul, MN. Fun fact, not only is St. Paul home to Charles Schultz’s Peanuts, but also the Donnie Smith Bike show. Ok, ok, back to arriving in St. Paul… can you say shock? It wasn’t just cold in St. Paul, it was “freeze your face off cold,” literally 70 degrees colder than where we had just come from. The cold quickly became more tolerable after the warm welcome we received upon arriving in the capital city. Chris and I were fortunate enough to score a room at the historic Saint Paul Hotel just around the corner from the venue. It was beautiful, and the service was terrific.
The 33rd Annual Donnie Smith Bike Show was one for the history books, not just because it was the first one since the pandemic hit, but it was also a celebration of Donnie Smith’s 80th birthday.
Those two things alone were cause for celebration but add in the reason we were all gathered at the St. Paul River Centre, the love of motorcycles… it was an outstanding event. Sit back, and let me tell you why St. Paul is home to such a fantastic annual show in the middle of the cold months. You see, this show is more about celebrating the motorcycle community in this part of the country than it is about showing off custom bikes. Don’t get me wrong, there are plenty of out of this world motorcycles, but the custom scene has been a long and storied tale of resilient men and women who are as passionate about their motorcycle community as they are their bikes. A few hundred motorcycle enthusiasts from all over the MidWest shook off the ice crystals and woke their two-wheeled wind therapists from their winter slumber to share them with the masses. The diversity of motorcycles displayed throughout the exhibit halls
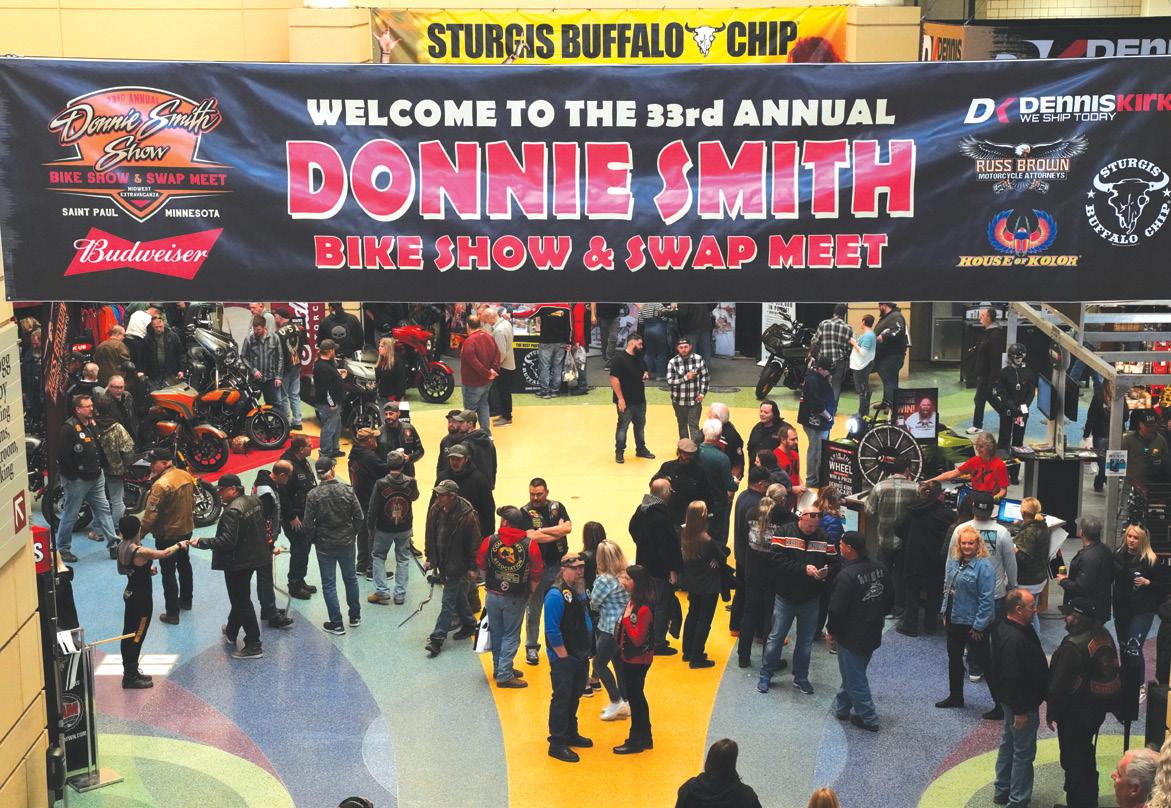
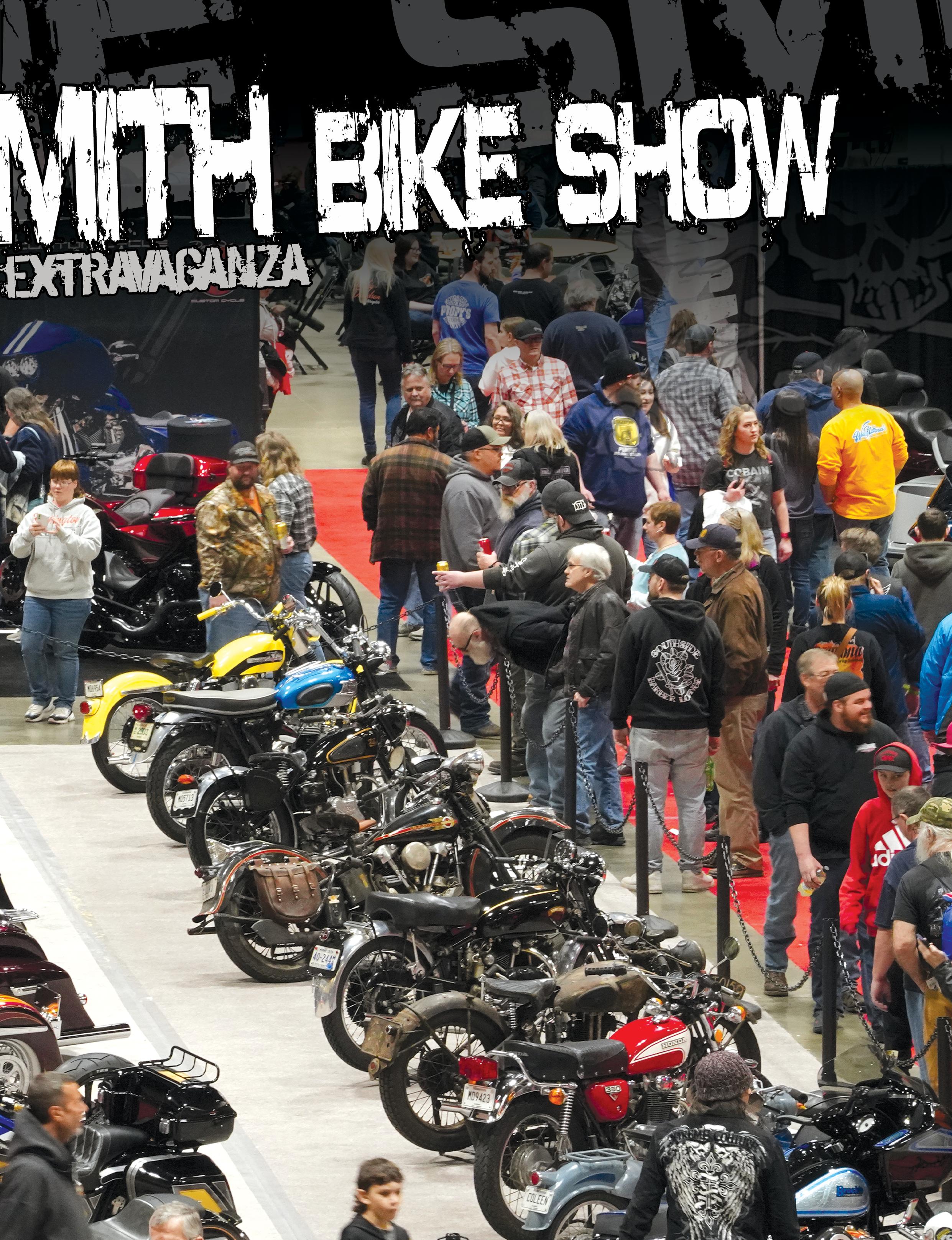
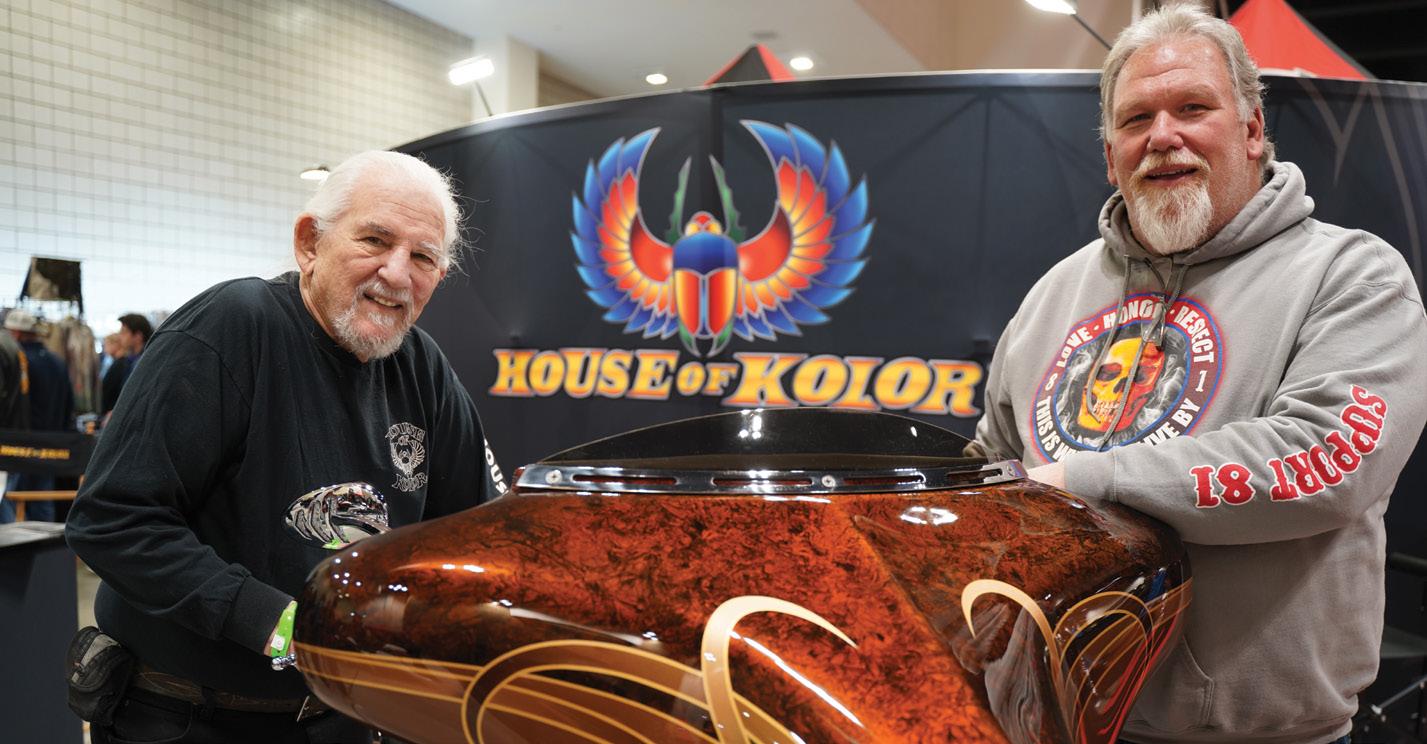
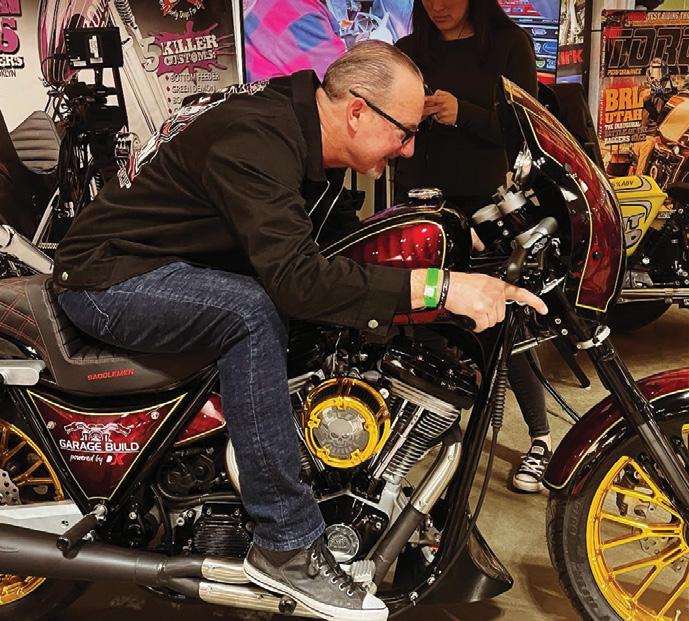
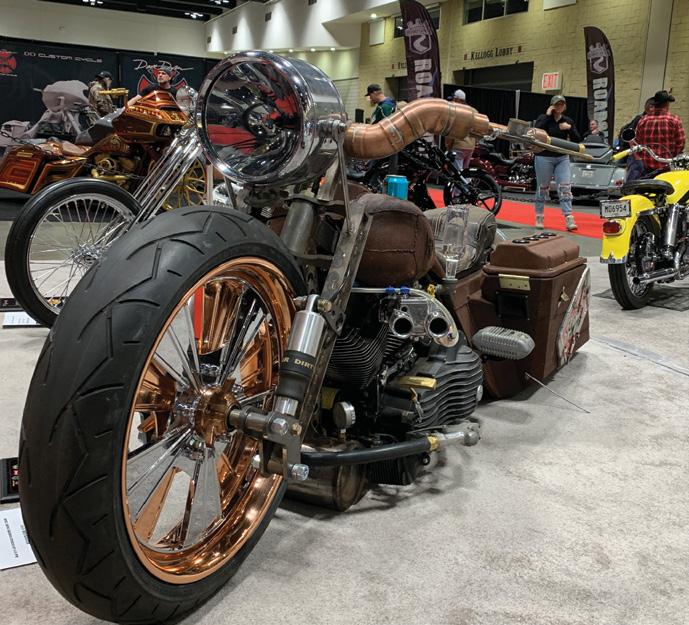
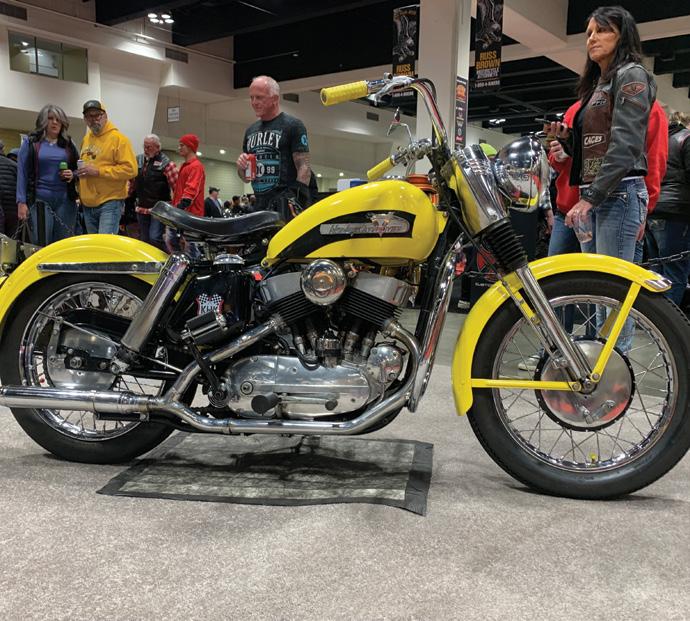

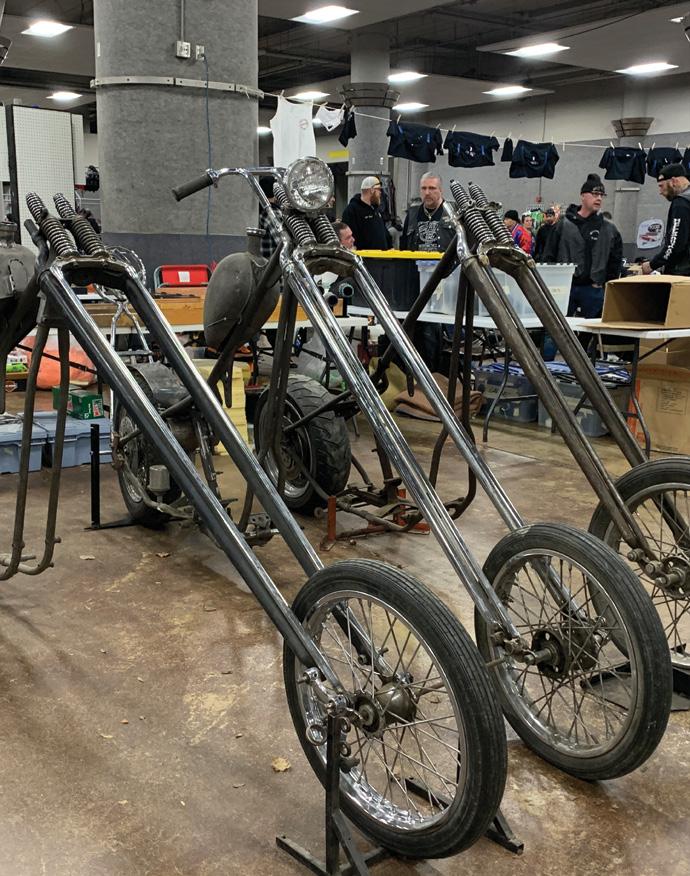

was amazing. You could admire motorbikes of all ages, shapes, sizes, makes, and models. Some were in original condition, while others were full-on custom builds from stem to stern with everything in between.
Now, I have to be honest, I’ve never been a fan of convention center shows. They always seem a bit slow to get rolling and stuffy. The end of the day always feels like it drags on forever because the attendees have left early to grab dinner, so you eagerly await the closing bell. Whelp, that’s absolutely not the case at the Donnie Smith Show. The lines before the show even opened were filled with hundreds of eager patrons that steadily streamed in throughout the days. And closing time..well, they damn near had to kick out a few hundred folks at the end of the night! The promoters certainly knew what they were doing when they hosted happy hour and a stellar band to close out the day.
The Donnie Smith show isn’t just a place to go look at a variety of killer bikes, it’s also one of the best places to peruse a giant swapmeet looking for parts to upgrade your scoot, mancave, or wardrobe. Parts swappers galore filled the giant hall. One could find just about anything they could possibly need to feed their motorcycle habit. Heck, you coulda scored a 70’s Honda Digger that Smith Brothers & Fetrow (verified by Donnie himself) had built the frame and springer for! I kept having to check Chris’s location throughout the weekend, fearing that we would need to rent a U-Haul if he was left to wander the swap meet alone. Thankfully we got away relatively unscathed with a few stickers and a super cool Visible Twin Cam engine model.
It wasn’t just parts swappers on hand showing off their wares. Show goers could check out the latest from Klock Werks, House of Kolor, Dennis Kirk, NAMZ, Kuryakyn, Deadwood Custom Cycles, and Brock’s Performance, just to name a few. If that weren’t enough, attendees were able to meet the faces behind the big names. Folks like Donnie Smith, Brian Klock, John Kosmoski, Brock Davidson, and Dave Perewitz were on hand to talk to and shake hands with those that have looked up to them
and their products for years. I know a highlight for Chris was when he interviewed the founder of HOK. I enjoyed watching Mr. Klock usher his younger staff around the show hall, imparting the knowledge he’s garnered over his 25 years in the industry.
All in all, the two-year sabbatical that was forced upon the midwest’s motorcyclist didn’t seem to slow anyone down. In fact, if anything, I saw a core group of motorcycle lovers reinvigorated and ready to share their passion with likeminded people. Not only were they celebrating the end of a long strange trip, but the reason we had all gathered..the motorcycle. Next March, when you’re itching to break the cabin fever, meet us at the Donnie Smith Bike Show. You won’t be disappointed. If I’m wrong, I’ll buy ya a drink! Be sure to stay up to date on what they’ve got planned for 2023 by visiting www. donniesmithbikeshow.com
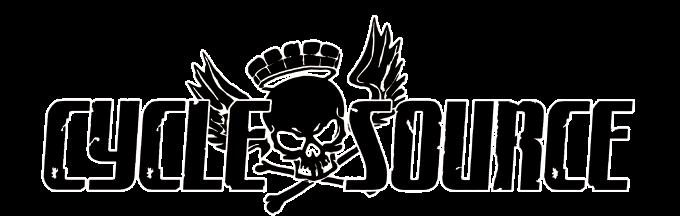
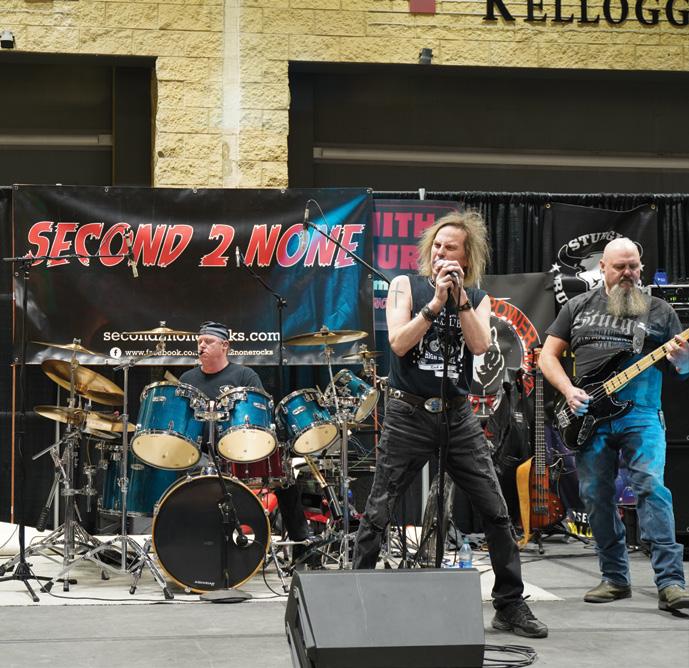

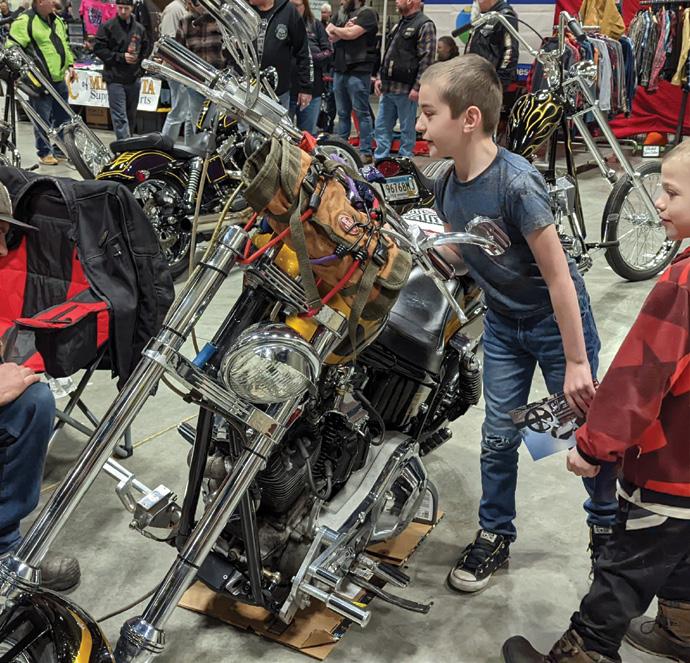
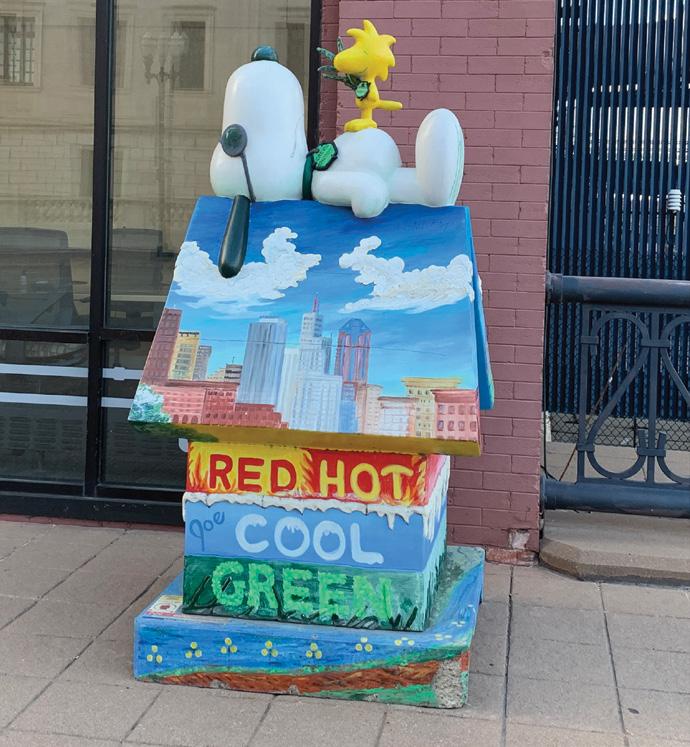
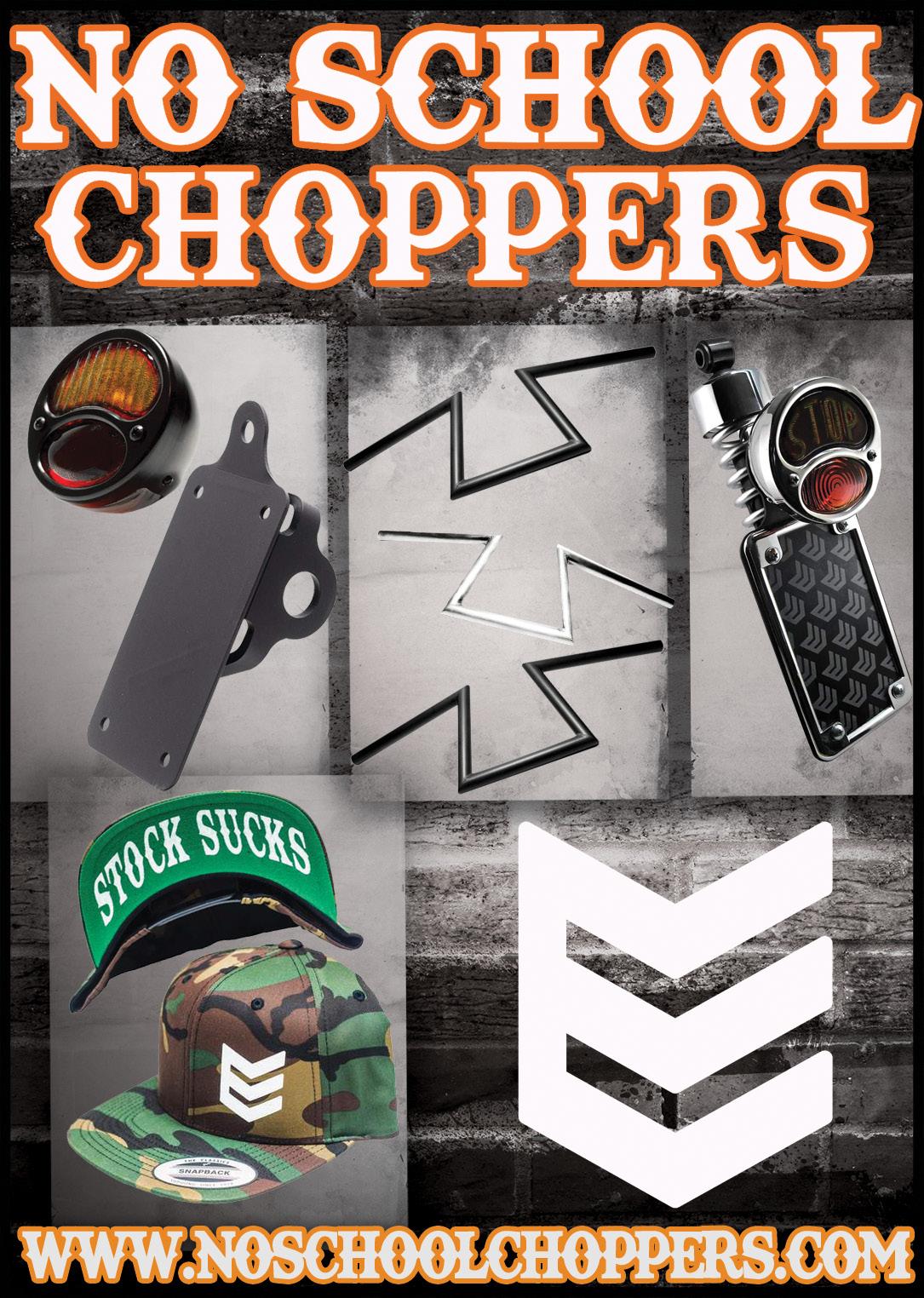
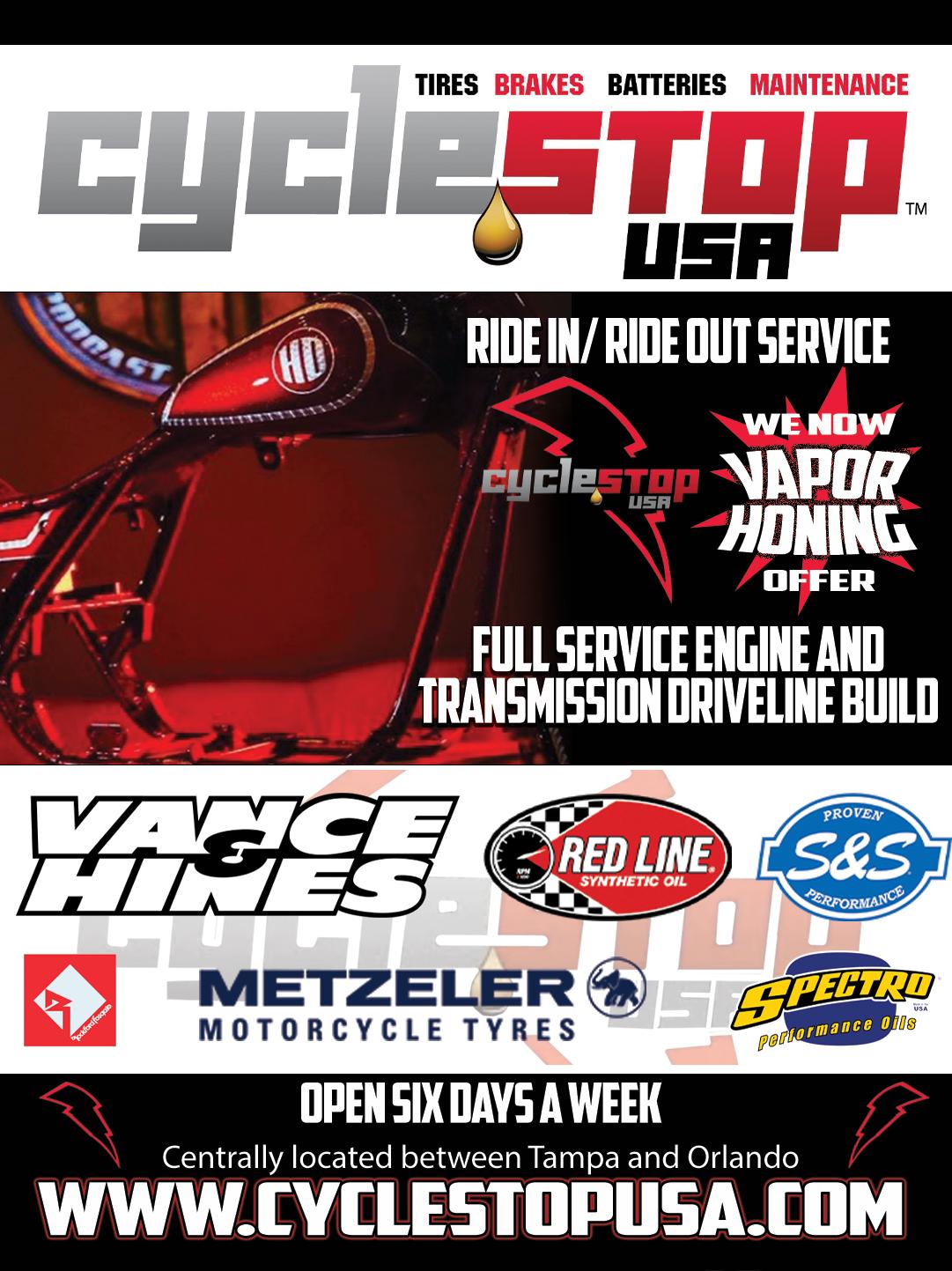
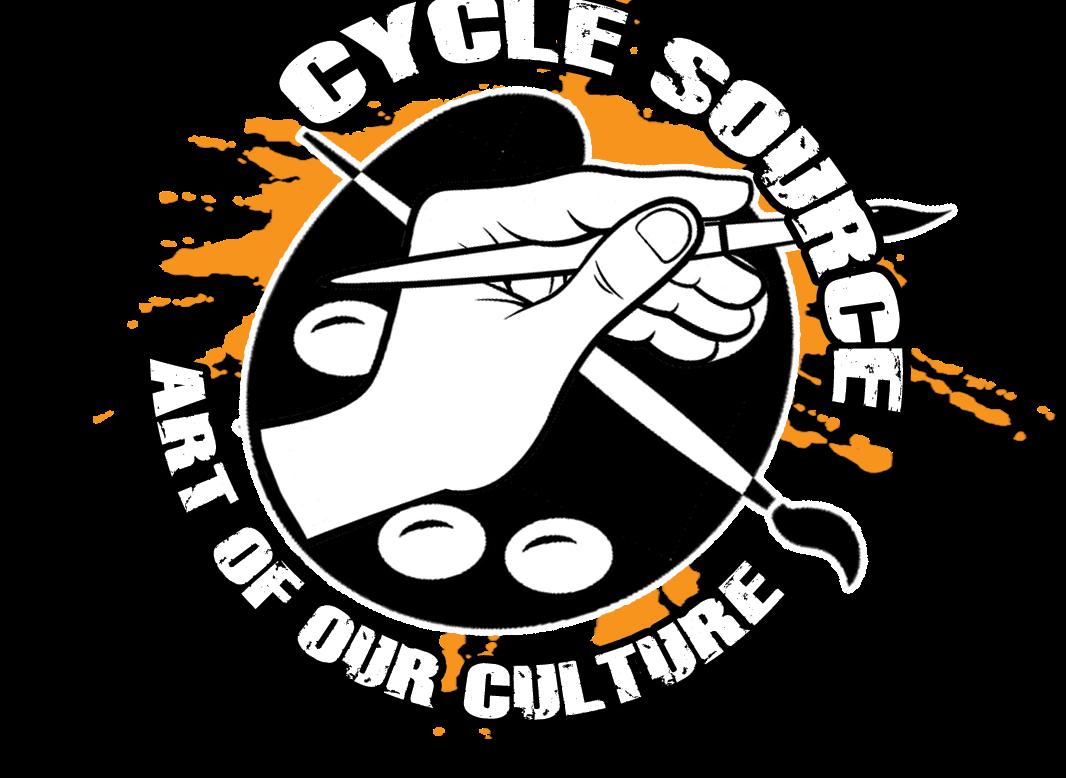
t all started in a pizza shop. In 2013 the family of Pedro The Engraver decided to open a brick oven pizza place. Of course, Pedro designed the business logo and, at the request of his motherin-law, did some pattern grinding on the aluminum that would go behind her prep area. After a few more engraving-type projects for her, it turned into something more substantial for him. In that same year, he, unfortunately, lost his youngest sister. As a way to deal with his grief, Pedro dove head first into creating. The “grind art” he was making at the time was the only way he knew how to push through his emotions. He gave
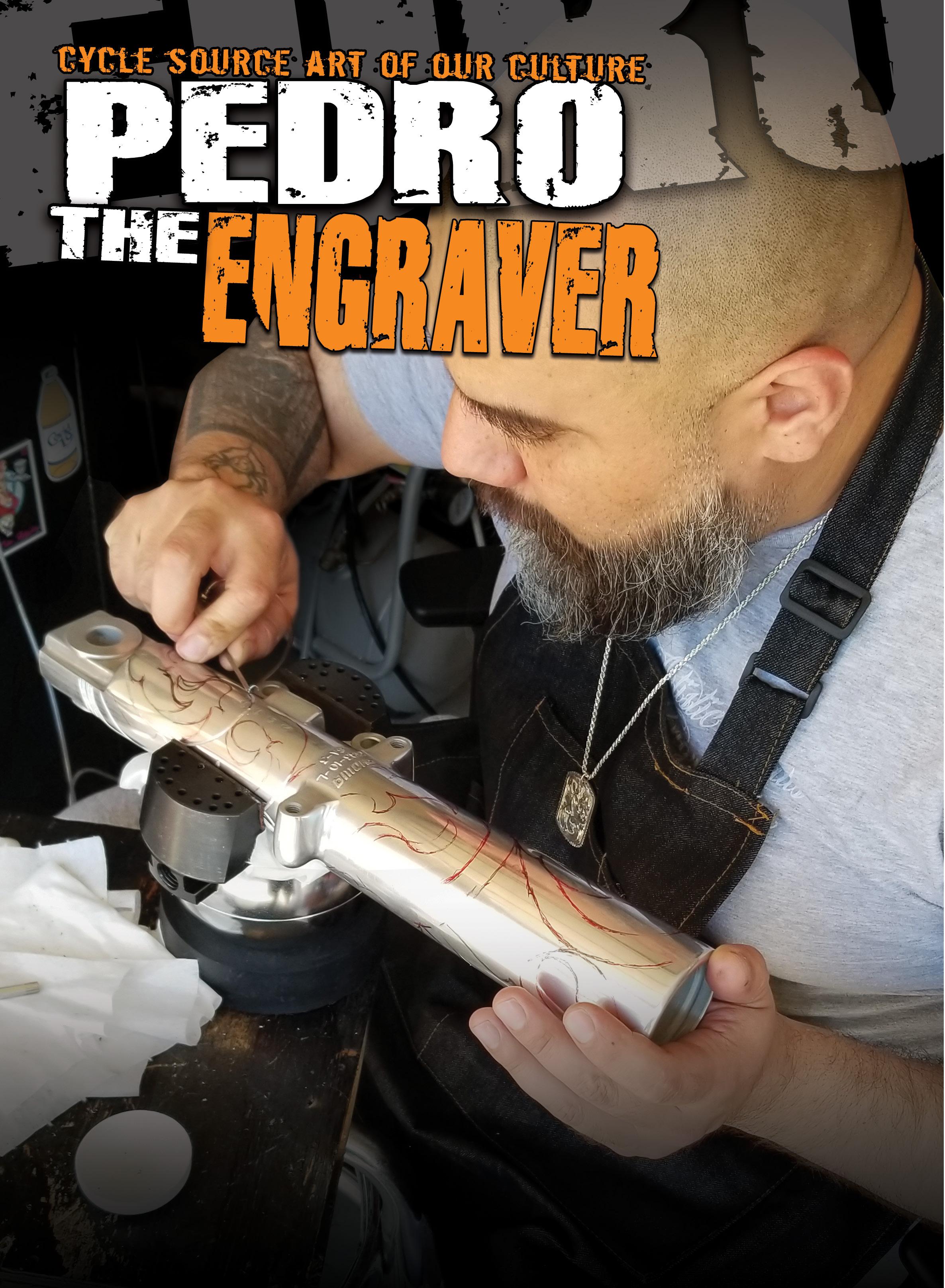
iaway most of his art for free or for very cheap. For the next 4 years, he continued this way, using a Dremel and a die grinder to create art and give it away. It felt good to give to others and make people smile. It soon became a full-blown addiction of sorts that eventually turned into professional hand engraving. In 2016 he started buying Sam Alfano’s Hand Engraving DVDs. While he saved money to buy his first GRS Hand Engraving System, he studied various scroll design books by Ron Smith and Lee Griffith. He was so enthralled with the craft that he actually was let go from one of his part-time jobs for drawing scroll designs at work. Two years later, in August 2018, he officially opened Artistic Metals Engraving. In 2020. Pedro quit his part-time job to focus on his business full time. 2016 is also when he started working his way into the motorcycle industry thanks to a late friend of his, Gabe Adame. Gabe paid Pedro to engrave his horn cover with a Dremel. This is definitely not how it’s supposed to be done, but it led him to figure out what he was supposed to be doing, and his style has been growing ever since.
Motorcycles also quickly became his favorite medium to work with. He says that people in the industry
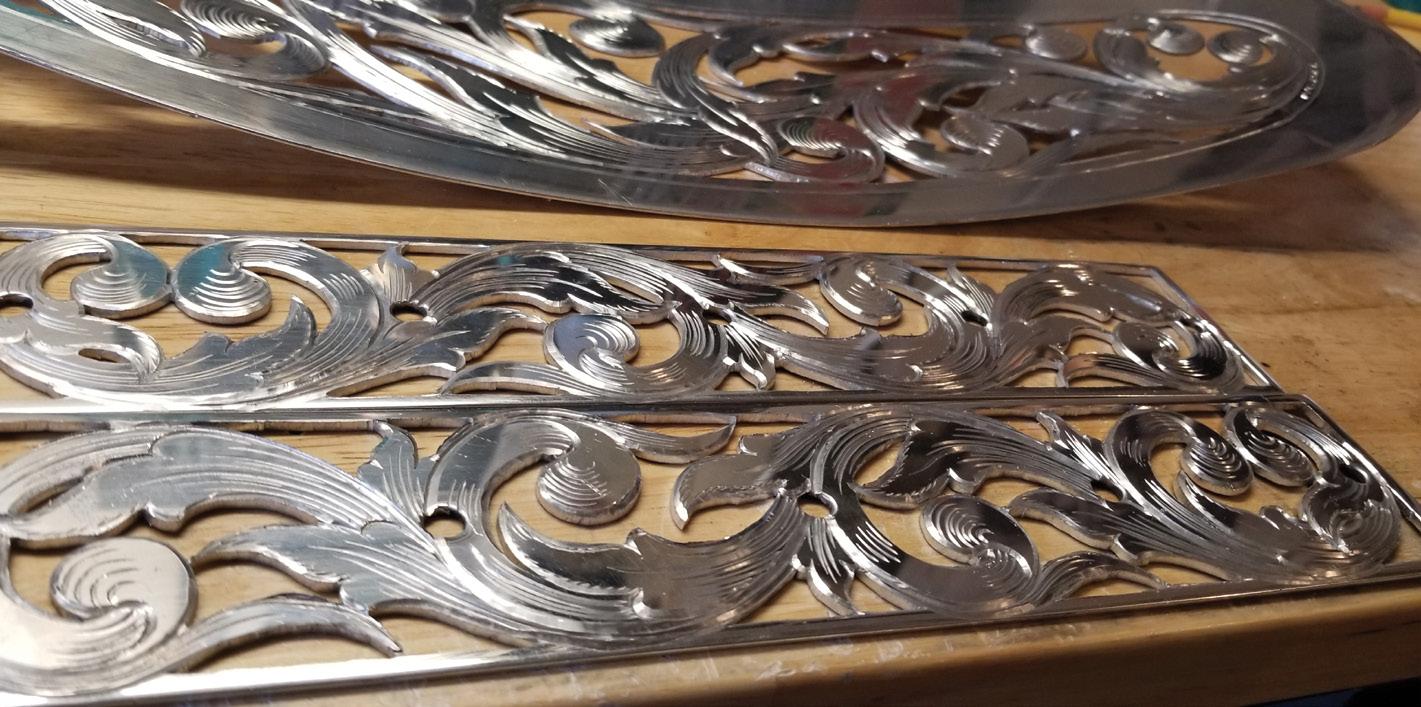
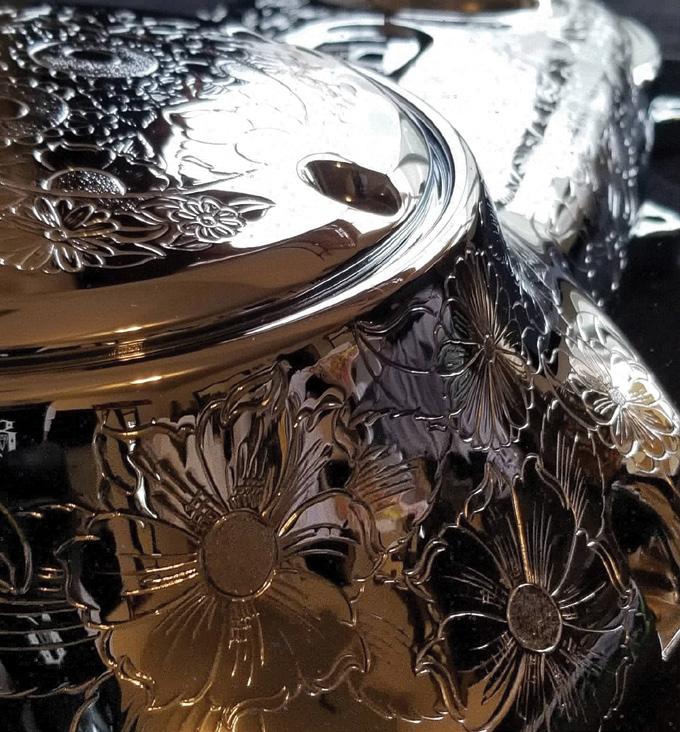

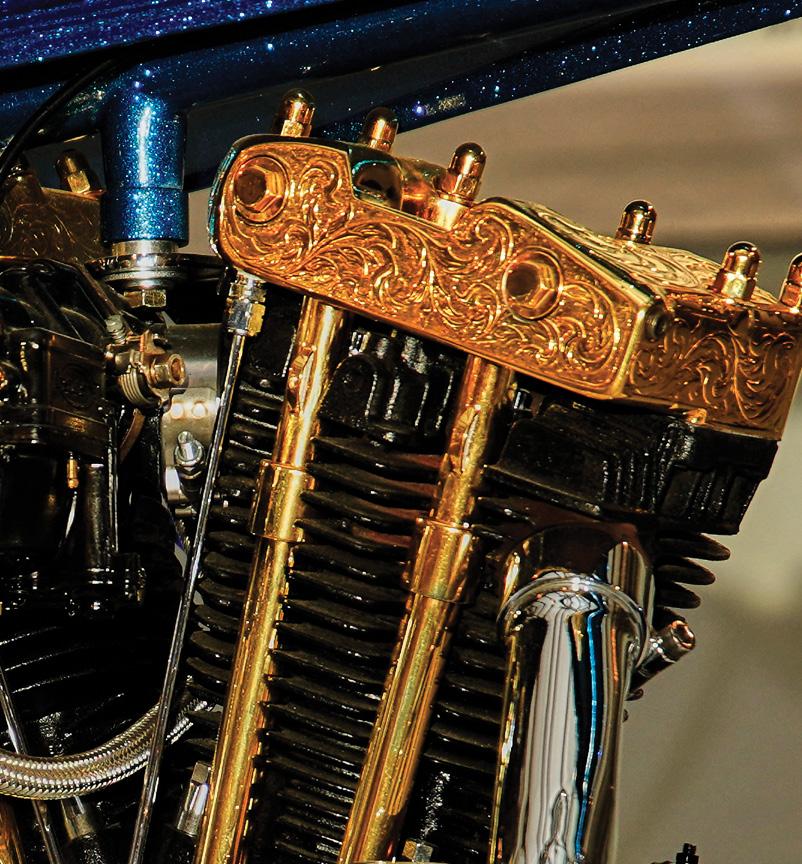
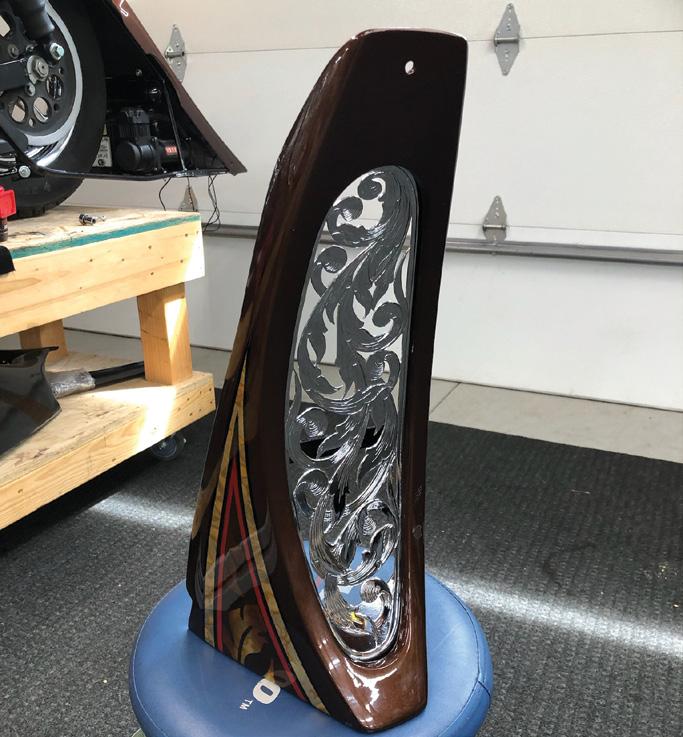


are some of the kindest he’s met and are the ones that have allowed him to show his true creativity with the designs he creates. All the folks he’s found in the motorcycle industry have evolved from struggle and built positive, fulfilling lives for themselves and their families through the people they meet and their interactions. Those are the ones that saw a new artist and decided to give him a shot; for that, he will be forever thankful.
For a bit of backstory, Pedro was born in a small farming community in Washington state, with a population of 28,000 and a bit of a desert. He was a typical child of the 80s, but as the 90s rolled around, he turned into a bit of a troublemaker. He hung around with a rough crowd and almost died from stab wounds in his gut. It was pretty serious. Pedro ended up paying for it with over 20 years of his life working at hard, grueling labor. After being hurt doing construction, his doctor advised him to quit and go to school. So he did. At 29 years old, he got his GED (well done!) and went to college for a couple years before deciding it wasn’t for him. Through all that, his art kept him going and made him excited to wake up the next day. He had dreams of one day not having to work for a big company or someone else, and here he is today!
His inspiration for his work definitely comes from his wife, who has made everything work through all the adversity. Their marriage of over 25 years and their working towards building even more for their future is what drives Pedro to create and continue on his journey.
Speaking of that future, Pedro’s plans are to learn more, hone his skills and start teaching others what he has learned. He wants to be able to give back to his community in some way, and teaching others his art form is what he knows best.
When it comes to where his art has taken him/where he’s going with it, Pedro’s first feeling is gratitude. If it wasn’t for his wife and the amazing people around him who support him, he wouldn’t have been able to do half the things he has today.
Suppose you want to see more of his amazing work or even commission a custom piece yourself. In that case, you can find him on Instagram @ pedrotheengraver, facebook Artistic Metals Engraving, or email him at artisticmetalsbypete@gmail.com.
LATE BREAKING NEWS FOR SMOKEOUT FANS
WITH LESS THAN A MONTH TO GO HERE’S THE NEWS YOU NEED TO KNOW
Article And Photos By: Chris Callen
t seems like just a minute ago that we were talking about how I cool it would be to bring SmokeOut back to the Rowan County Fairgrounds where it started in Salisbury, North Carolina. Well in truth, it’s been over a year and man has the time flown by. Good thing for us, we have been busy getting things ready. I figured it would be a good time to go over some of the last minute additions to the lineup. Of course, the full schedule will be up on the SmokeOut rally web site but let’s take a look at some of the highlights. The Shade Tree Boys will be holding old time bike games on Friday Sept. 9th. Trophies for 6 games and a championship belt for the overall winner will be awarded.
Of course, there will be one main show, the ride in custom bike show with over 30 classes. This will be on Saturday the 10th. Tons of prizes and bitchin handmade trophies for all classes, a full feature for best of show PLUS A Denver’s Springer as the grand prize!! Also, on Saturday the Perewitz Paint Show “Old School Edition” rolls into SmokeOut. Dave and Jody will be on site to hand out some killer hardware for the best dressed bikes of the day. This is thanks to our good friends

at Tobacco Road HarleyDavidson. Friday is no slouch for shows either with the Hardcore Cycles Performance Show. John O’Brien and his crew will be on hand to pick out the best muscle in the crowd. On that same day the Led Sled Crew will take a break from their antics to hold the Sportster Showdown SmokeOut.
On the midway on Friday will be a throwback to old SmokeOut and the Anvil toss, the Strongest Biker Worlds. A Biker Strongman Competition officiated by the very man that started the Anvil Toss; Ralph “Hammer” Janus.
Thursday night starts off with a meet and greet with the builders of the Legacy Invitational and official gallery opening but changes gears to a ride in movie and later that night a bonfire. SmokeOut has plenty of racing too. Not only have we convinced Tim Gelay, Jive Turkey Racing, to come in with a whole host of minibike games and the all-time favorite mini bike races, we have added Chopper Dirt Drags to this year’s event. There will be an official Christmas Tree and prizes.
Oh yes, there has always been a hell of a wet t-shirt contest at the SmokeOut and there will still be one. You know the deal, it’s wild and registration is open.
I n conjunction with Ed Kerr, Founding Member of the Hamsters we are proud to introduce TankFul. Just because someone has successfully reached the status of senior citizen doesn’t mean that they live carefree days. In 2019, 5.6 million seniors struggled with food insecurity. Many of them, 63%, have to make the difficult choice between filling their bellies or their prescriptions.
We’ve gathered some of the best motorcycle artists in the country to help make a difference. Through the generosity of Paughco, who donated all the blank tanks, each artist has donated their time and talent to TankFul. Each masterpiece will be on display in the Legends Gallery and will be auctioned off through an online live auction.
We are honored to have the following artists join us: Jace Hudson of Fast Life Garage, Robert Pradke of Custom Auto Design; Scott Takes Of Underground Art Studio; Casey Kennel of The Paint Chop; Fish Alcorn of Alleyway Kustoms; Cory Mroz of Mr. Oz Designs; Darren McKeag of McKeag Art, Steve Gibson of Air, Oil and Lead, Dave Perewitz, Jody Perewitz of Perewitz Cycle Fab, Mo Diaz of Mo’s Custom Image, Kristian Baena, Ron Tonetti of RT’s North Hills Cycles, John Gates of JAG Paint; Eric Malotke of Open Throttle Customs; Ronnie Melendez of Weights and Paints; Frannie Drummond Of The Paint Zoo; James Patience Of Ground Zero Customs, and Clint Kiddle of SpeedFreak Motors. The bidding is open now, go to https://app.galabid. com/tankful22/items to help out!
Jack Schit has signed on to be the ring master for this circus and will be on stage providing regular entertainment and insights throughout the weekend. We are thrilled to have him on board with us. Also, in for the mix are some of your favorite bartenders in the all new SmokeOut Roadhouse provided by Twisted Tea. Did I mention way more camping than ever before in Salisbury, all the art by Richie Pan and the Motorcycle Art Extravaganza that will be in the Legends Gallery. And what about the bands.... Well, we have what we think is a stellar lineup. They are listed below and while this is pretty much all we have for now, keep checkin in at SmokeOutRally.com
the Shadley Brothers, Mark and Paul, have been responsible for some of the most beautiful custom motorcycles of our time. In their incredible facility in Whitman, Mass, they have gone about the work of creating oneof-a-kind custom motorcycles now for the past 42 years. They joke that this has been the longest overnight success in history. Seriously though, it was something that started because neither of them wanted to go get a job, so at Paul at 17 and Mark at 23, , they pitched in 700 bucks a piece and agreed that when it was gone, they’d give up. Well, the good news for them and for us is they still have that 1400 bucks and, at the same time, have contributed to a substantial part of the custom culture, made great friends, and have finally settled into a place where they have a limited number of customers that they build for, and that’s enough. Great stories come out of a place like this, a man’s man type of business where you know you are dealing with real people. Where everyone has a dream and a special plan. Every once in a while, however, there is a special case. A story that is so important that everyone stops to hear it. Such is the case with The Lyon’s Share.
Paul Lyons is the type of selfmade man you would describe to
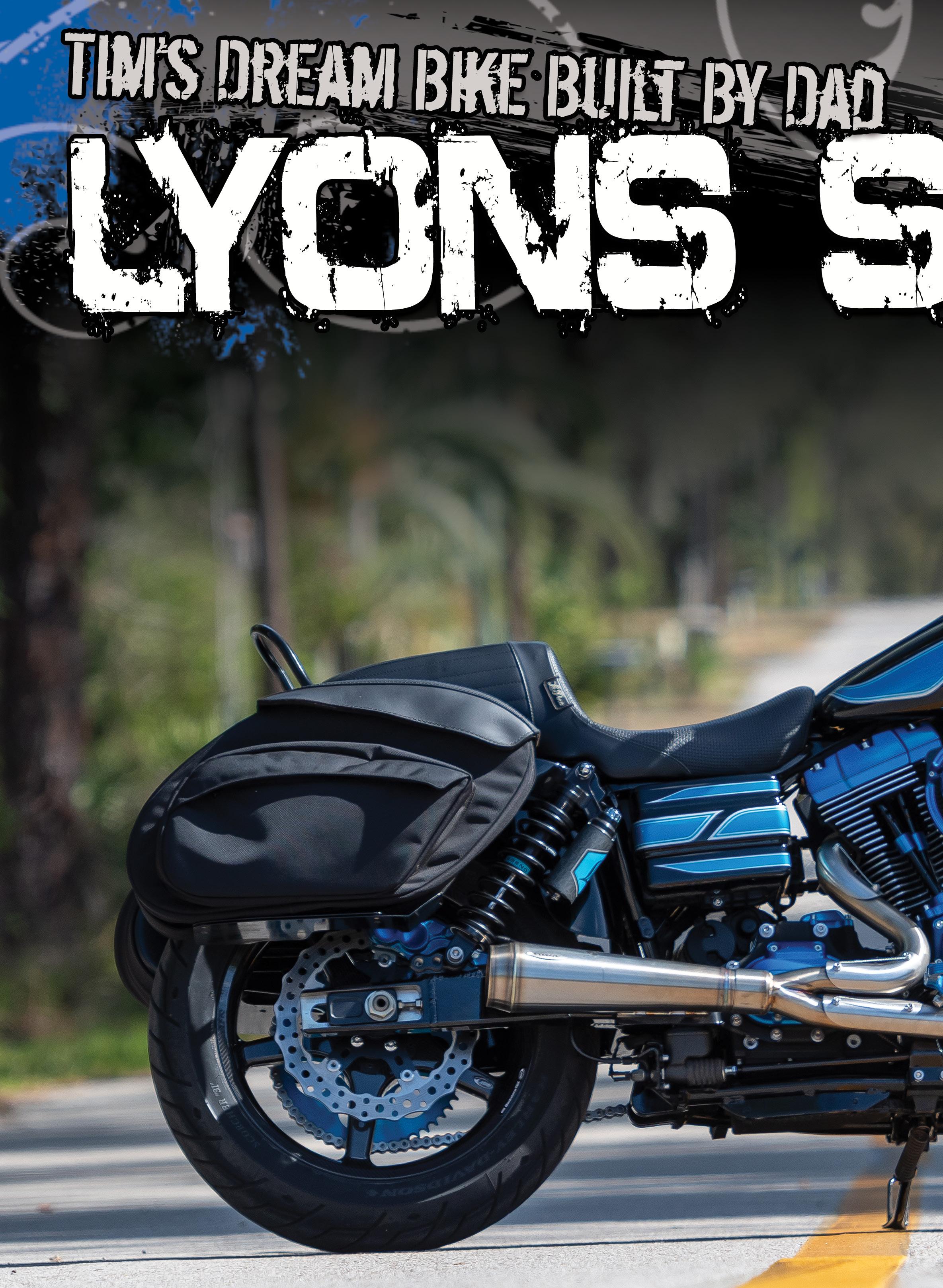
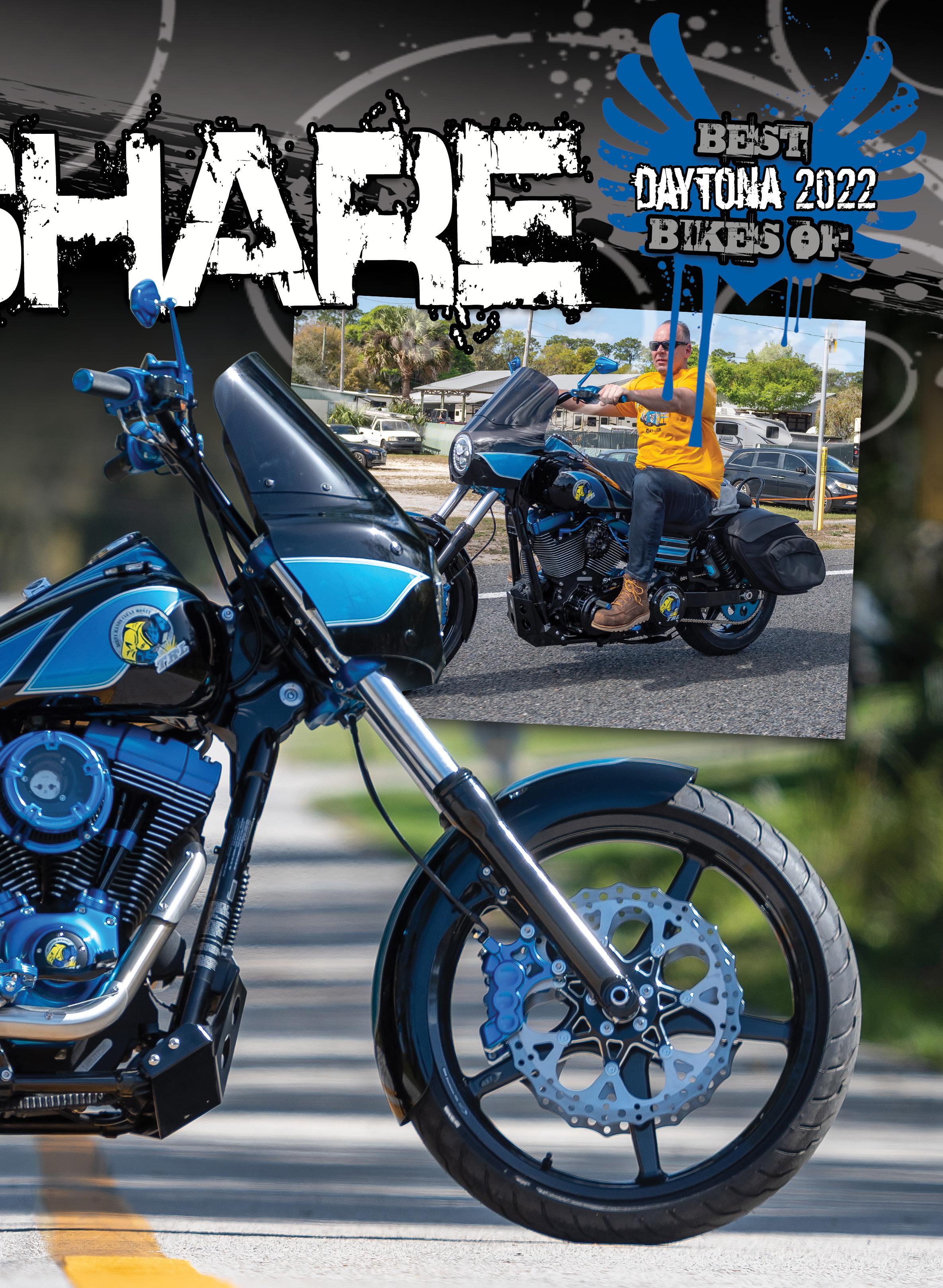
other people as a baller. A heavy hitter or an OG. He has a company called North East Mechanical that services accounts like Gillette Stadium and the Boston Garden, to name a few. Truth is, most of the giant buildings in that region have their plumbing and HVAC installed, serviced and maintained by Paul’s company. Despite that, Paul was raising his son Tim to have good values, and all indications were that he was doing so successfully. Tim was as blue-collar as they came, and the mantra on the tank, “Dirty Hands, Clean Money,” was his daily reminder that hard work is a way of life. His dad let him do his own thing too. A welder by trade, just like his father, Tim didn’t get a free pass just for being the boss’s son. He made his own way and, in turn, was his own man.
Paul has a handsome collection of motorcycles, but nothing like the bike you see featured here. This is all what Tim liked. Tim had taken his bike to the Shadley’s a few times for work like cams and stuff, but he had the budget of a young man, so the parts you see on it now weren’t in his wheelhouse just yet. He had other habits too, as young men do, like rolling coal from his pickup, and he loved four-wheelers. This is, unfortunately, where this story takes a devastating turn. On a trip to Maine for a four-wheeler adventure, he was involved in an accident that took his life. On his 22nd birthday, 7/16/22, Tim was taken from this world just as he was getting started on his path. As you can imagine, this was a severe blow to his father. In some ways, the project of building Lyon’s Share may have been a coping mechanism. He went to the Shadley Brothers and laid out a plan to build the bike of his late son’s dreams. They gave the motor a little more heat with a 585 cam and some roller rockers. Got it up to the 110 level and had a nice little torquey ride. All the best parts were used in the build, the latest tricks and spared no expense in making a rolling tribute to Tim. Now, the list
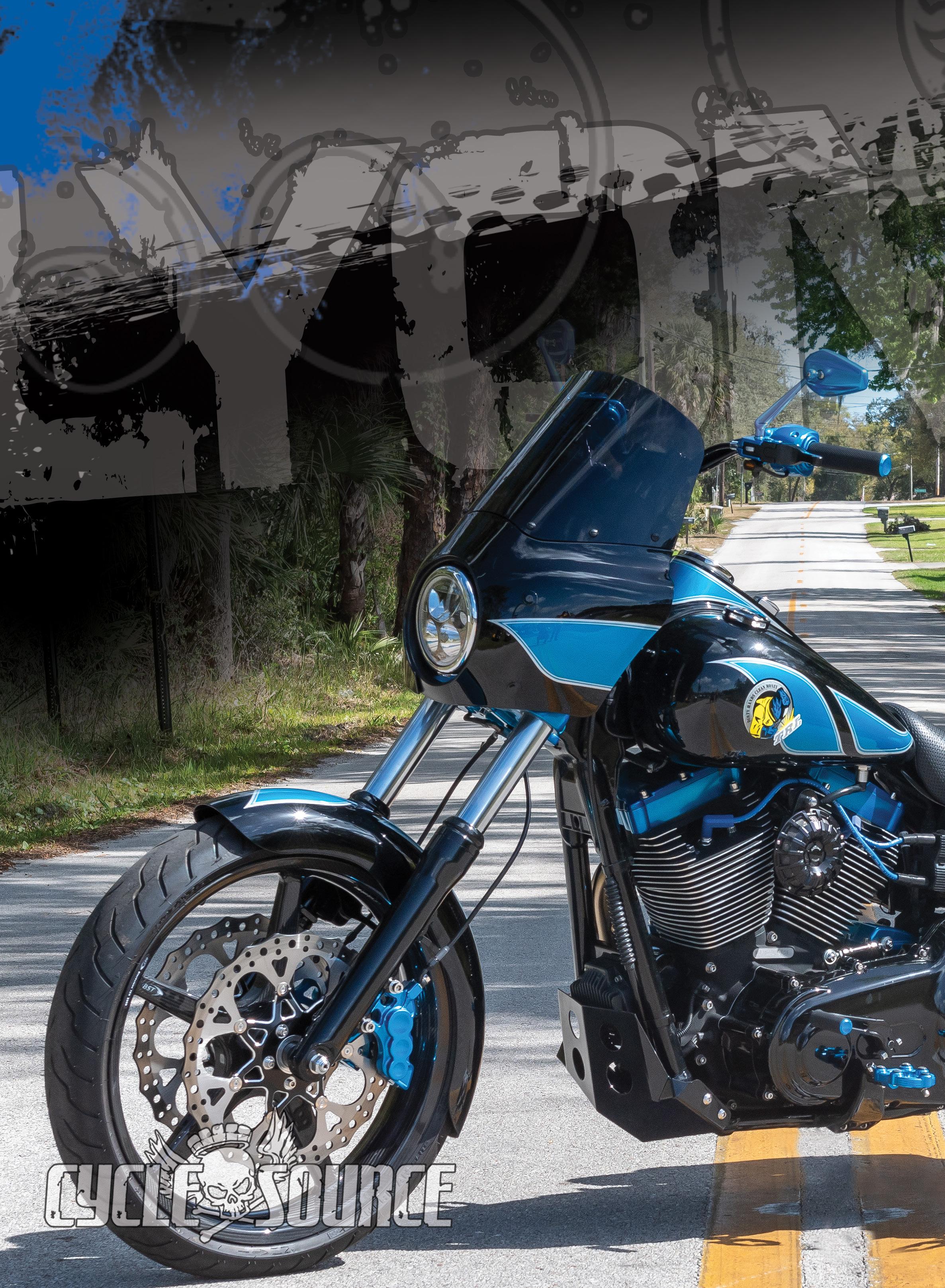
of parts is impressive, with some of the best names in the industry like BST, Legends, Arlen Ness, but the story is in the simple logo that adorns the tank and points cover. A picture of a welder, words that read “Dirty Hands, Clean Money,” and the initials TRL for Timothy Richard Lyons. A reminder that this was Tim’s bike and will always be.
Credit for that graphic goes to John Hartnett, who does all of the Shadley’s graphic work. They laid out the blue paint, and if you look closely at the silver, you will see some hand-painted diamond plate. This was another of Tim’s signatures. Apparently, anything that could have diamond plate bolted to it in his world got it, so of course, the bike had to have some as well. From there, they Used a Brocks Performance swing arm, frenched in the plate and the taillight, and moved the blue color across the rest of the bike. Some of this was anodized, some of it in powder, all keeping in line with the color scheme from the tanks. The

Owner: Paul Lyons City/State: Walpole, MA Builder: Shadley Bros. Year: 2013 Model: FXDWG Time: 9 Months ENGINE Year: 2013 Model: Twin Cam Builder: Shadley Bros Ignition: Power commander 5 Displacement: 110CI Pistons: S&S 10.5 to 1 forged Heads: CNC Ported and set up by S&S Cam: S&S 585 Air Cleaner: Arlen Ness Method Exhaust: Trask Primary: HD TRANSMISSION Year: 2013 Make: HD Shifting: 6 Speed FRAME Year: 2013 Model: FXDWG Rake: 32 Degrees Stretch: NA FORKS Builder: Shadley Bros. Type: HD 49mm w Race tech front end Triple Trees: HD Stock Extension: WHEELS Front Wheel: Brock BST Twin Tek Carbon Fiber Size: 21x3.5 Tire: Dunlop American Elite 130/60/21 Front Brake: 2 Arlen Ness 6 Piston Calipers / 14” Ness Procross Rotors Rear Wheel: Brock BST Twin Tek Carbon Fiber Size: 17x4.5 Tire: Michelin Scorces 180/60/21 Rear Brake: Arlen Ness 4 Piston Rear Caliper / Arlen Ness Rear 11.8 Jagged Floating Brake Rotor PAINT Painter: Shadley Bros Color: Black / Dahlia Blue Metallic / Chopper Blue Sunglow Type: PPG Graphics: Jon Hartnett powder coat: Advanced Powder Coat ACCESSORIES Bars: Todd’s Cycle Low Moto Risers: Todd’s Cycle 8” Bone Bar Handlebar Clamp and Riser kit Hand Controls: Powerstands Racing Lever Set, Arlen Ness Fusion Grips, HD Switches Foot Controls: Arlen Ness / Thrashin Supply Shifter Arm Gas Tank(s): Stock, HD Oil Tank: Stock, HD Front fender: Arlen Ness Profile Rear Fender: HD / Shadley Bros. Seat: Le Pera Headlight: Drag Specialties Taillight: RWD Speedo: Screamin’ Eagle speedo with Tach. Swingarm: Brock Performance Suspension: Legends Revo ARC 13” Piggyback Photographer: Nathan Schultz bike saw its first action in Daytona, where we ran into it and got to bring it to you. As for the future of it, Paul will probably only bring this bike out on special occasions, keep it nice and close at hand. We send our deepest condolences and, at the same time, congratulations to Paul, both for having such an amazing young man as his son and for the way he chose to remember him.
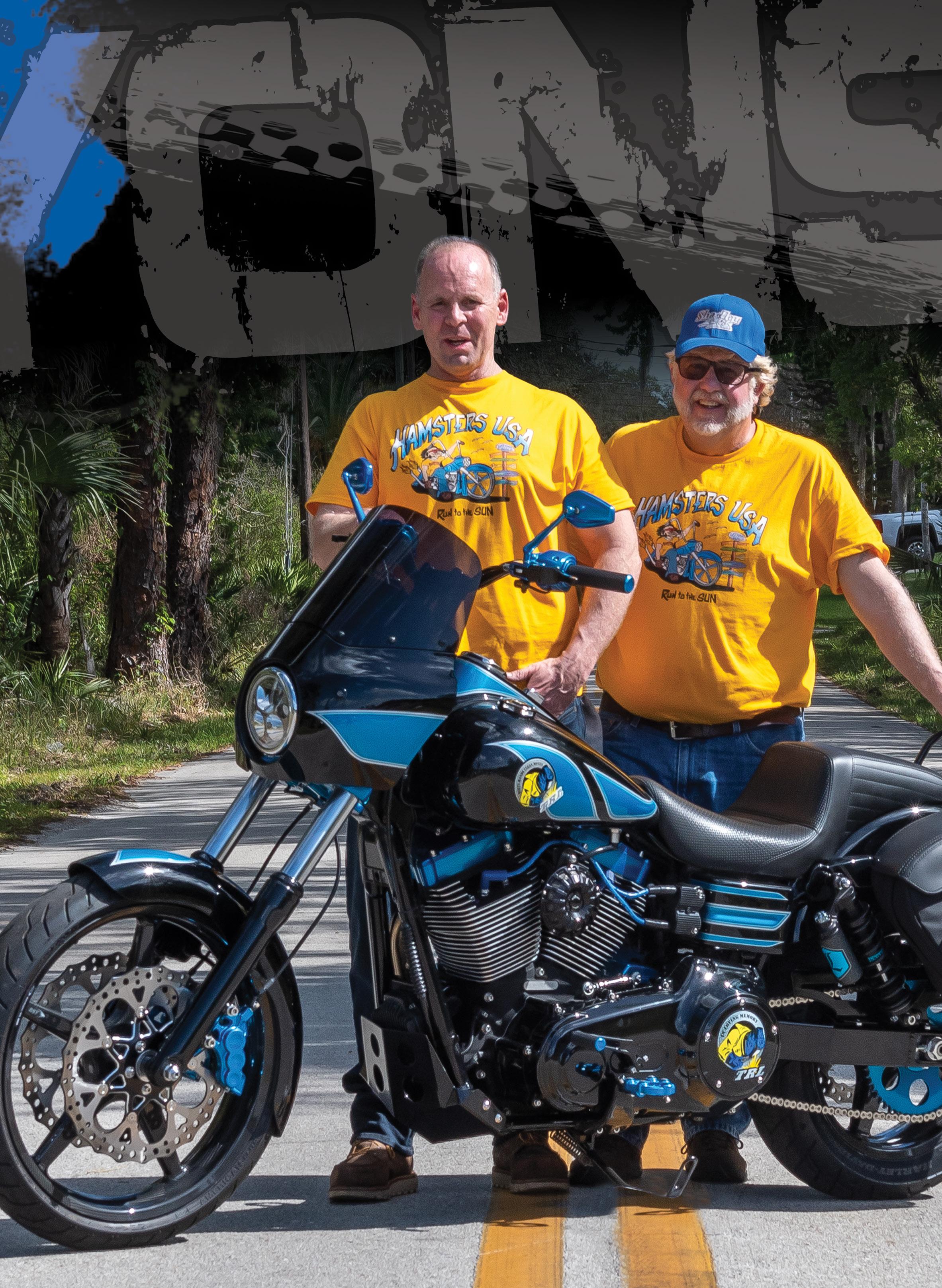
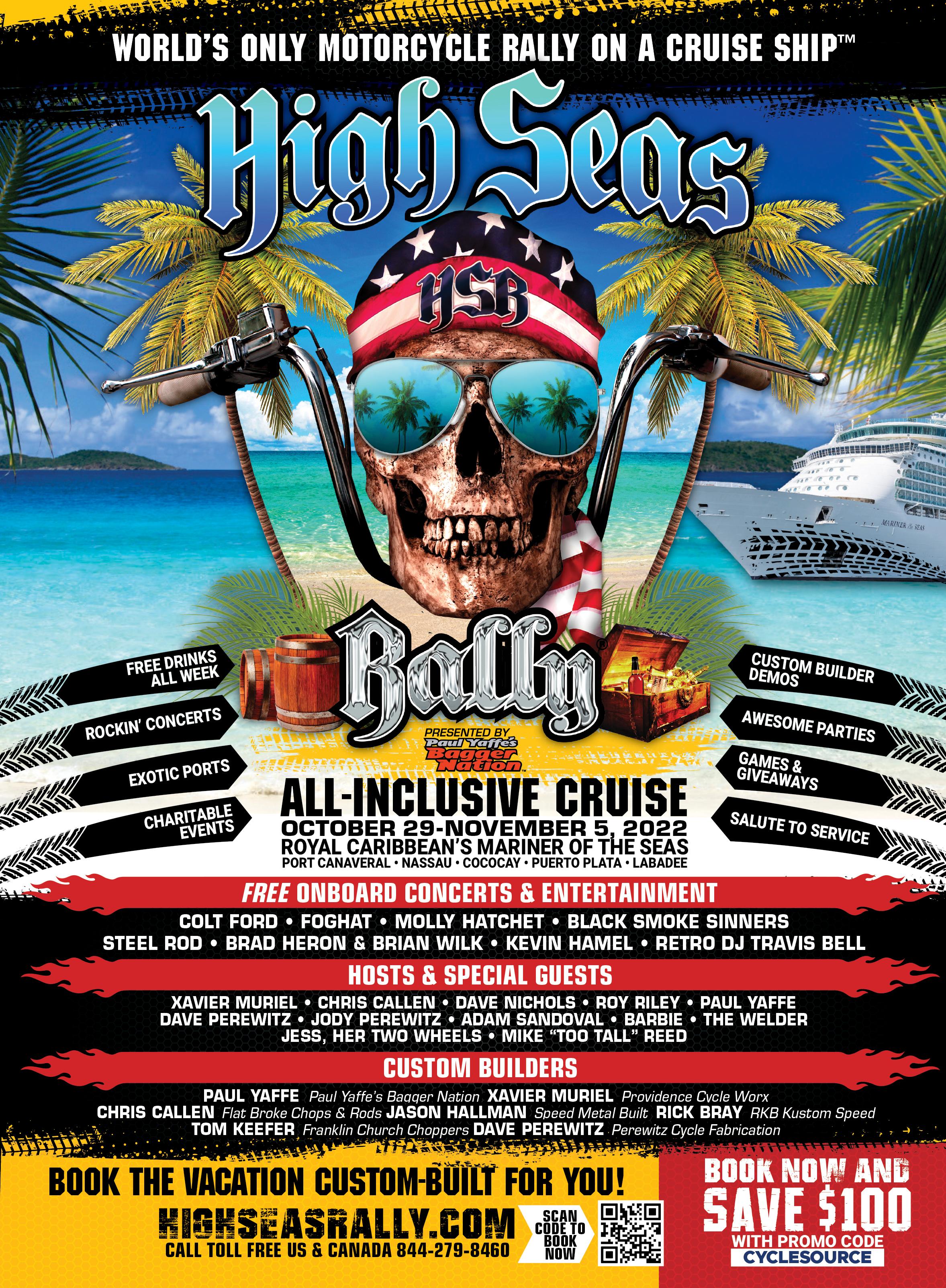

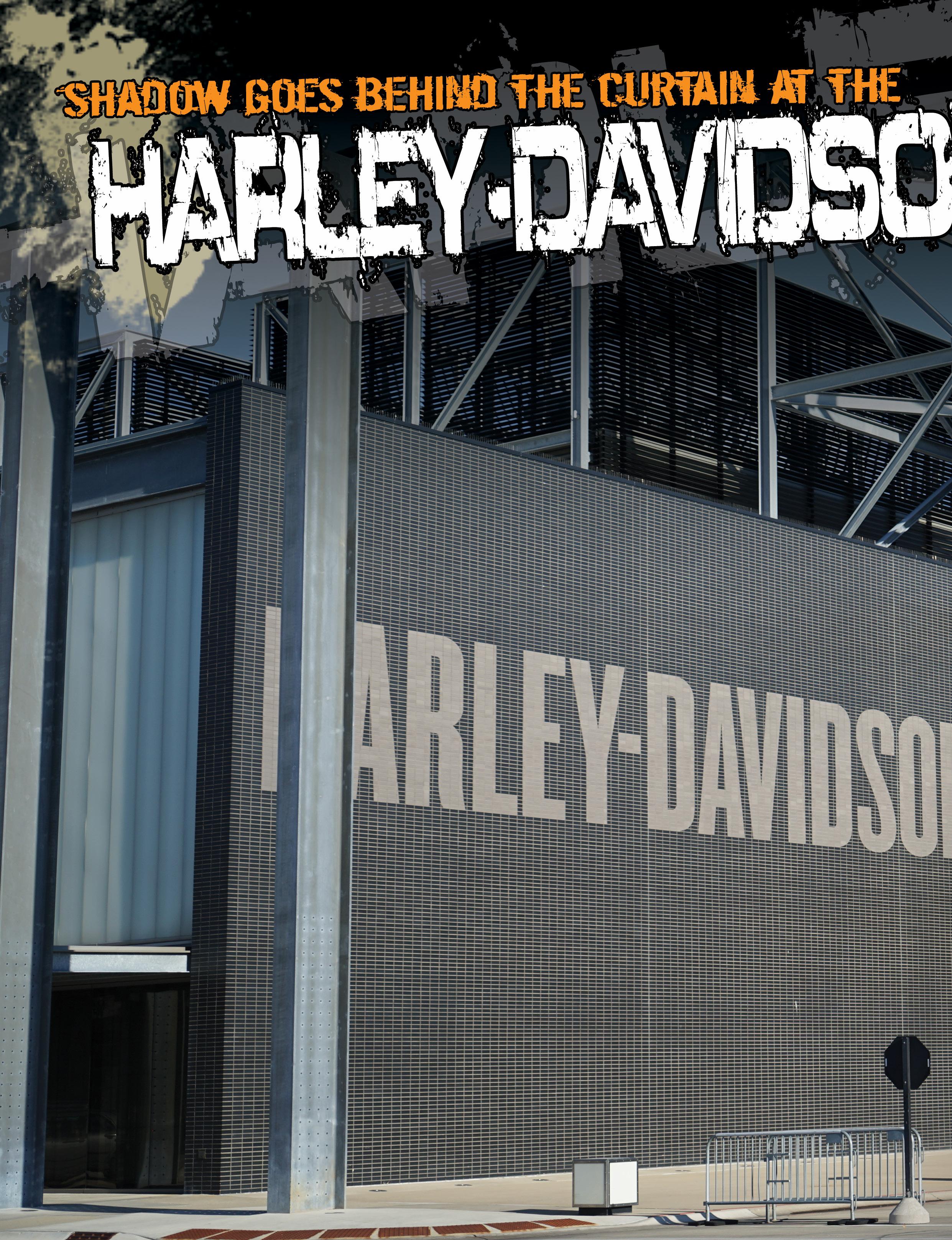
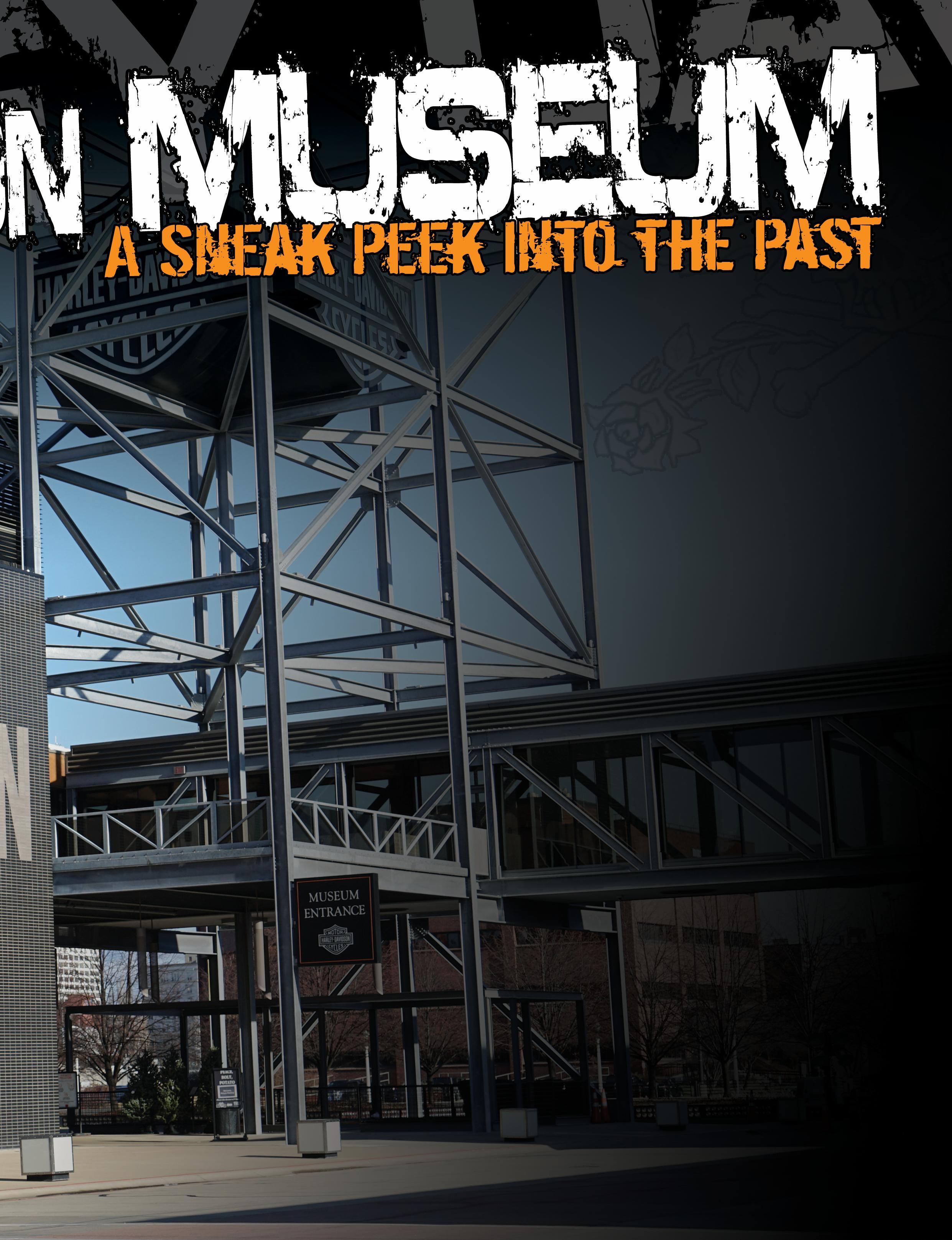
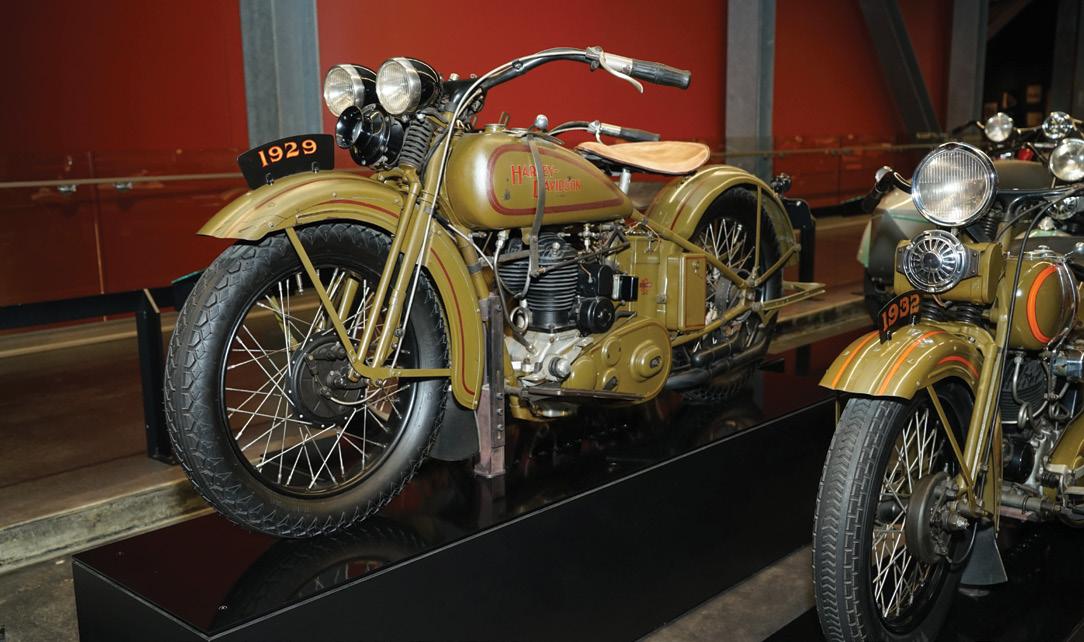
ince it first opened in 2008, the Harley-Davidson Museum has been a must-see attraction not only to the Harley faithful, but visitors to the great city of Milwaukee in general. My first visit was during the Harley-Davidson 105th Anniversary Celebration, and I’ve made it my business to stop by and pay homage to this great American motorcycle brand and its founders at least once a year. The Museum is not just a static display of old motorcycles; exhibits change, new structures are added, and a wide variety of activities take place throughout the year, making for new discoveries and diversions every time we visit.
Although I’ve seen pretty much everything the 20-acre Museum campus offers to the public, I’ve never seen the archives. Sure, I’ve taken the elevator to the third floor of the annex building and peered into the archives area, but I’ve always wanted to see, up close and personal, what’s behind the metal grate. Our Milwaukee visit in December for the Mama Tried show last year proved the perfect opportunity to do just that. Arrangements were made for Alan Magyar and me to get a private tour of the archives.
Adding to our excitement uncovering what goes on behind the scenes, to our good fortune, Bill Rodencal, Lead Museum Collections, agreed to conduct the tour. We couldn’t have asked for a better guide. In January, Bill started his 19th year with Harley-Davidson and was involved during the Museum’s opening
son July 10, 2008. A month later, the Motor Company celebrated its 105th anniversary, which saw 25,000 people on the Museum grounds! Since that year, the Museum has served as the focal point for each of H-D’s quinquennial anniversary celebrations. Our tour began on the main exhibit
Article By: Marjorie Kleiman Photos By :Alan Magyar
floor of the Museum, where we stopped to admire Serial Number 1—not HarleyDavidson’s vintage-inspired electric bike, but the first known Harley-Davidson motorcycle built in 1903. Bill explained, “We know this is not the first motorcycle they built. What we do know is that there are components on it that came from the first casting run. These are what we call early six-bolt cases, so there’s six bolts holding the crankcases together. There is no VIN, but we know they’re very early. The frame is a bit later. There’s a lug on the headstock, and that’s to mount a sidecar, and that doesn’t turn up until mid-1905. So it’s a little conglomeration of stuff, but it’s very, very early. We know for sure the majority of this bike was still built in the 10’ x 15’ shed. I’m sure the carburetor was; I’m sure the crankcases were; the cylinder—it’s an extremely early bike, and the most valuable bike in the collection by far.” As we stroll through the main exhibit floor, Bill described the HarleyDavidson’s philosophy. He told us that every year, H-D saves at least one bike brand new off the assembly line. Pointing at two early models, he gives some examples: “That 1915, and that 1913, are brand-new bikes which have never been restored. So that’s why you’ll see damage, nicks, scrapes, and dings, but that’s original paint, original nickel. Sometimes the organics, like belts, seats, and grips, have to be replaced. That ‘13, outside of tires, is the way it came out of the box. No miles, never been run.” Throughout the Museum is Harley-Davidson memorabilia of all types. Bill pointed out some Walter Davidson artifacts, such as his trophies and the brass and horns that he won in 1908 in the FAM reliability trial, where he had a perfect score. He said, “They saved all these things over the years—the posters you see, the literature. We saved copies of those in multiple languages, and they go into our small archive, our small artifact collection.” I ask if there
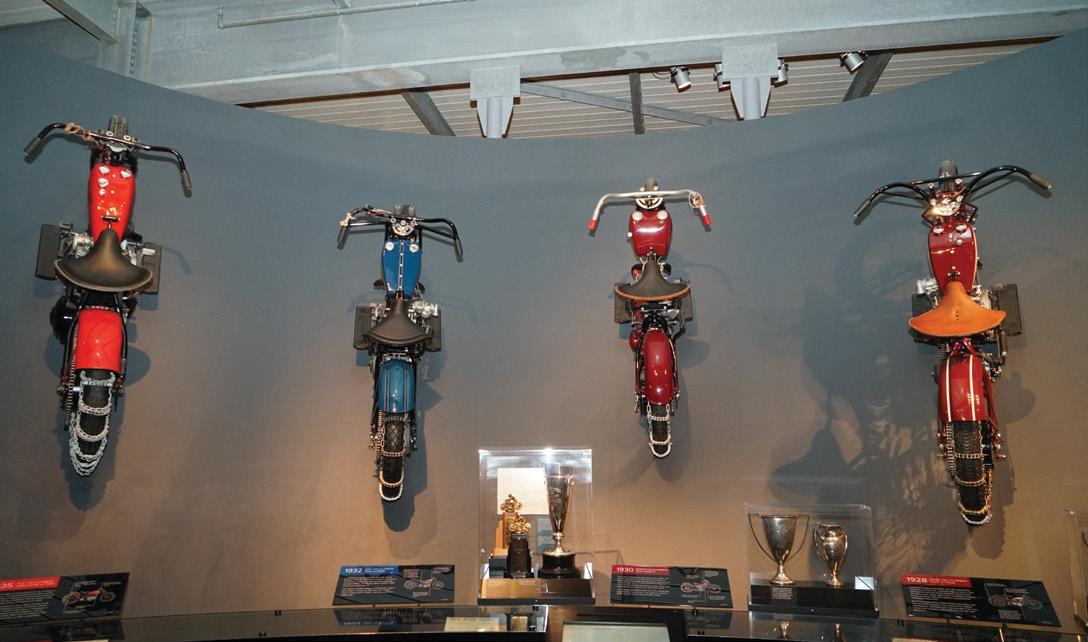
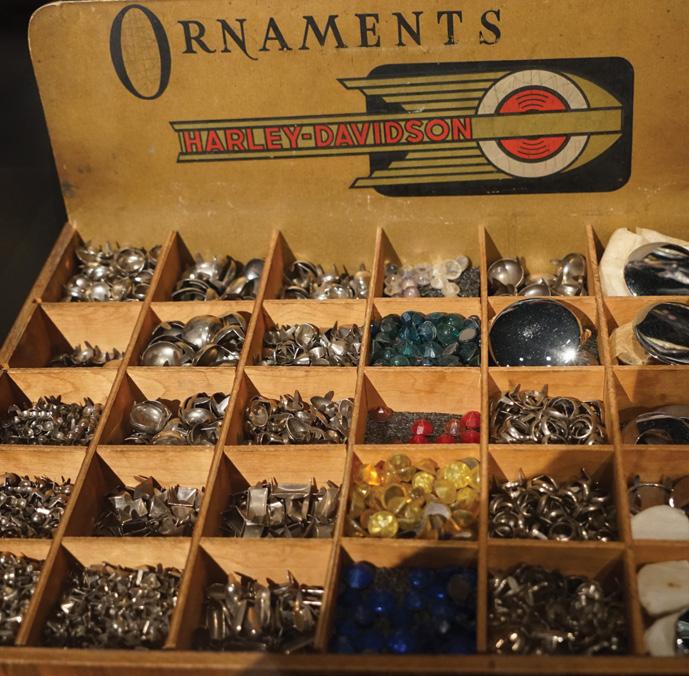
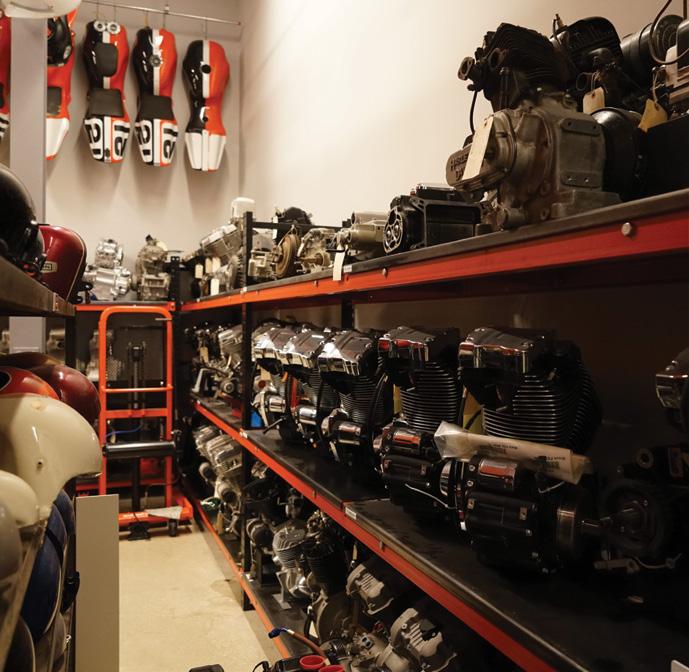
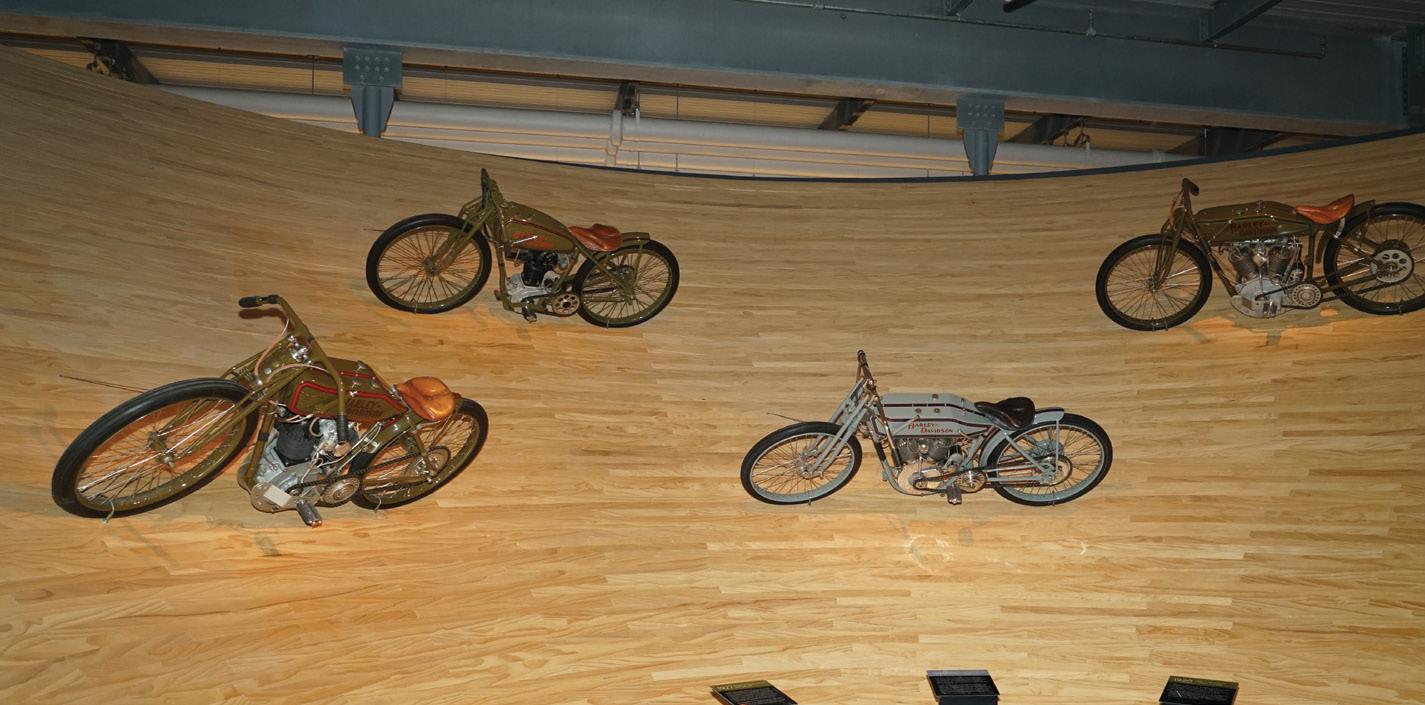
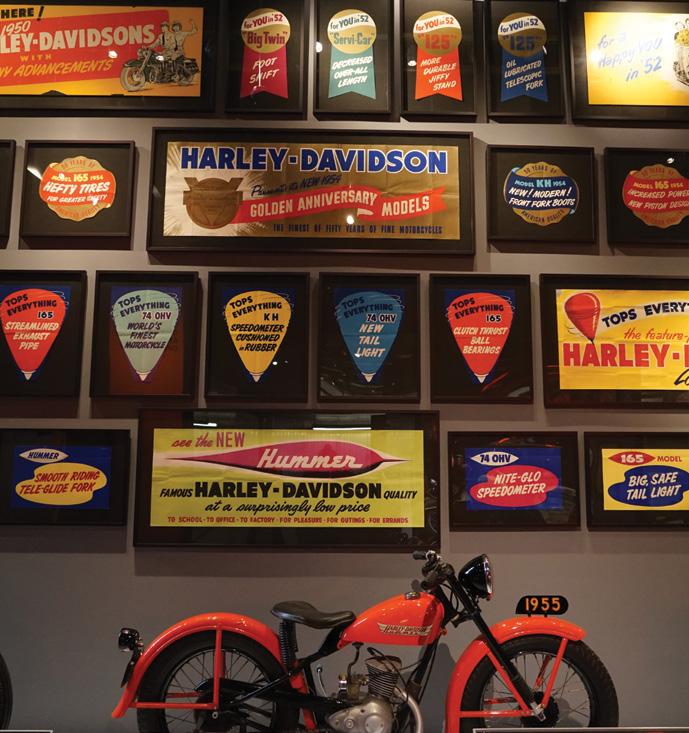
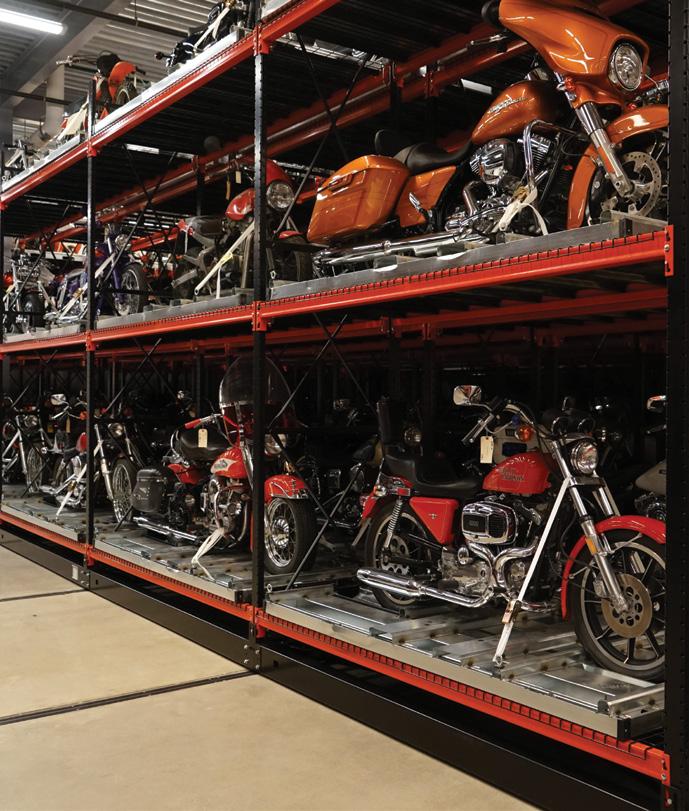
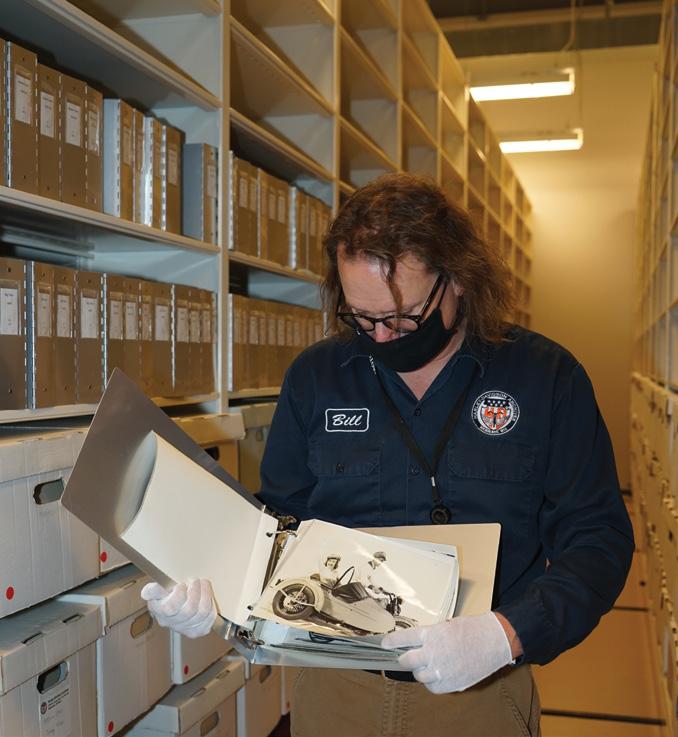
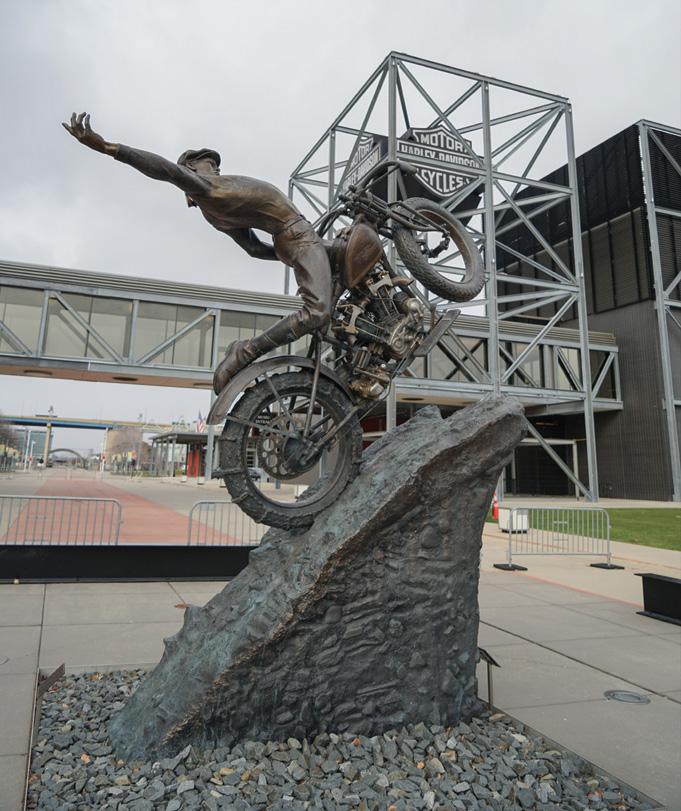
was any recognition early on whether these things were worth saving. Bill responds, “Well, we don’t know. They didn’t document why or how. We always say that they were Scotsmen and were real frugal, so they didn’t throw anything away.”
We are amazed to learn that there are 2,500 artifacts in the Museum, 151 bikes, and probably over a million artifacts in the Museum collection. Bill wondered, “What do you put in, and what don’t you put in?” That’s a real hard thing to determine. What’s nice is having such a rich collection and having multiple copies. We can rotate items so we have good conservation. Some of the colors in the posters we don’t want to fade so we can pull ‘em down, unframe ‘em, put another one in, and stay on a pretty normal rotation.”
As we cross the walking bridge from the Museum proper to the archives, we see one of the temporary exhibits displayed on the walls, including some original blueprints and drawings from the H-D headquarters on Juneau Avenue. When they were given to the Museum from H-D headquarters, the archives staff knew the company had photographed the construction of the buildings and documented it well, so the Museum staff thought they would make a great exhibit. Bill pointed out some details: “Here they are, literally digging the foundation and hauling it out one steam shovel at a time. What’s so interesting is that you go back and look at this courtyard. It hasn’t changed. It still looks like that. There’s the hold still in there; that’s the loading docks. Now it’s headquarters and cubicles, but in its day, it was automated screw machines and gear blank cutters and rows of them because they were cranking this stuff out all day long.”
Entering the restricted area behind the gate, the first area to the left is the shop where Bill works on the Museum bikes and prepares the models to be exhibited. He impresses upon us that “we don’t do any restoration. If we do anything, it’s conservation. We take ‘em apart, clean ‘em, and put ‘em back together, but we don’t repaint or replate.” The Motor Company saves at least one and sometimes two models annually. For the model year 2020, a Sportster S and a Pan America were saved to add to the collection.
Bill tells us about one bike that had been restored twice in its history—the first time in the 1970s and again in 1998 for HarleyDavidson’s 95th anniversary. He said, “They actually took some letterheads and some early photographs that we have and tried to get it more correct to how it would have come out originally.”
Rows and rows of enclosed shelves occupy a large part of the archives space, and inside those shelves are owner’s manuals, service manuals, service bulletins, recall notices, and the like. Bill tells us, “We got a big project now, a big donation, that we’re sorting out and putting on the shelves. It was all just lumped together.”
Also in the area are photographs and publications of the day. If a picture was
taken, the negative was saved. Some of the photos Bill points out illustrate marketing photos shot in a studio, parts manuals shots, and more. And we learn that the manuals in the archives can be electronically searched!
One of the archives artifacts that delight us is a set of Evel Knievel’s X-rays! History tells us that he had broken 433 bones by the end of 1975, so we had to try to identify all the fractures revealed on the X-rays, which was a fun little exercise. Another part of the archives stores artwork and many of the larger, oversized shelves. Bicycles are hung on the wall because they’re lighter. And along the back wall is a Topper!
The balance of the motorcycle collection not on the exhibit floor involves motorcycles, engines, and other components stacked on racks that are three shelves high. Bill says, “There’s a little bit of everything in here. They rotate onto the floor, and we use them for a lot of different things like part fitment. This is basically my area, my shop. I’ll do the part fitment; believe it or not, we have service parts that go back into the teens, so when they need fitment of a part, we’ll check it out. If they need, say,’ 01-’07 Sportsters, I’ll fit it on an ‘01, ‘05, ‘07, you know, make sure it fits accordingly. And from there, the vendor can go ahead and make it, rather than making 10,000 of them, and then they don’t fit.”
Since the Museum opened, Harley-
Davidson has been making incremental improvements, including the recent groundbreaking of a new, year-round event space. The all-new Garage comprises over 8,000 square feet and has floor-to-ceiling glass doors. The Museum Shop, which offers H-D Museum-branded merchandise, authentic reproductions, accessories, and gifts, will move across to the former Garage, allowing it to expand and triple in size. The new Shop will also offer demos on Serial 1 e-bikes and IRONe electric balance bikes. Once the move has been completed, the former Shop will house H-D’s first, and only Factory Shop for discontinued Motorclothes products. And the Experience Gallery inside the Museum will be completely revamped. During the warmer months, events held at the Museum include Thursday night Bike Nights and weekly BBQ & Blues at the Motor Bar & Restaurant are on Saturday nights. There are also parties and races along with complementing events like the Mama Tried Motorcycle Show and more. And we’re looking forward to celebrating Harley-Davidson’s 120th anniversary at the Museum next year. See you there!
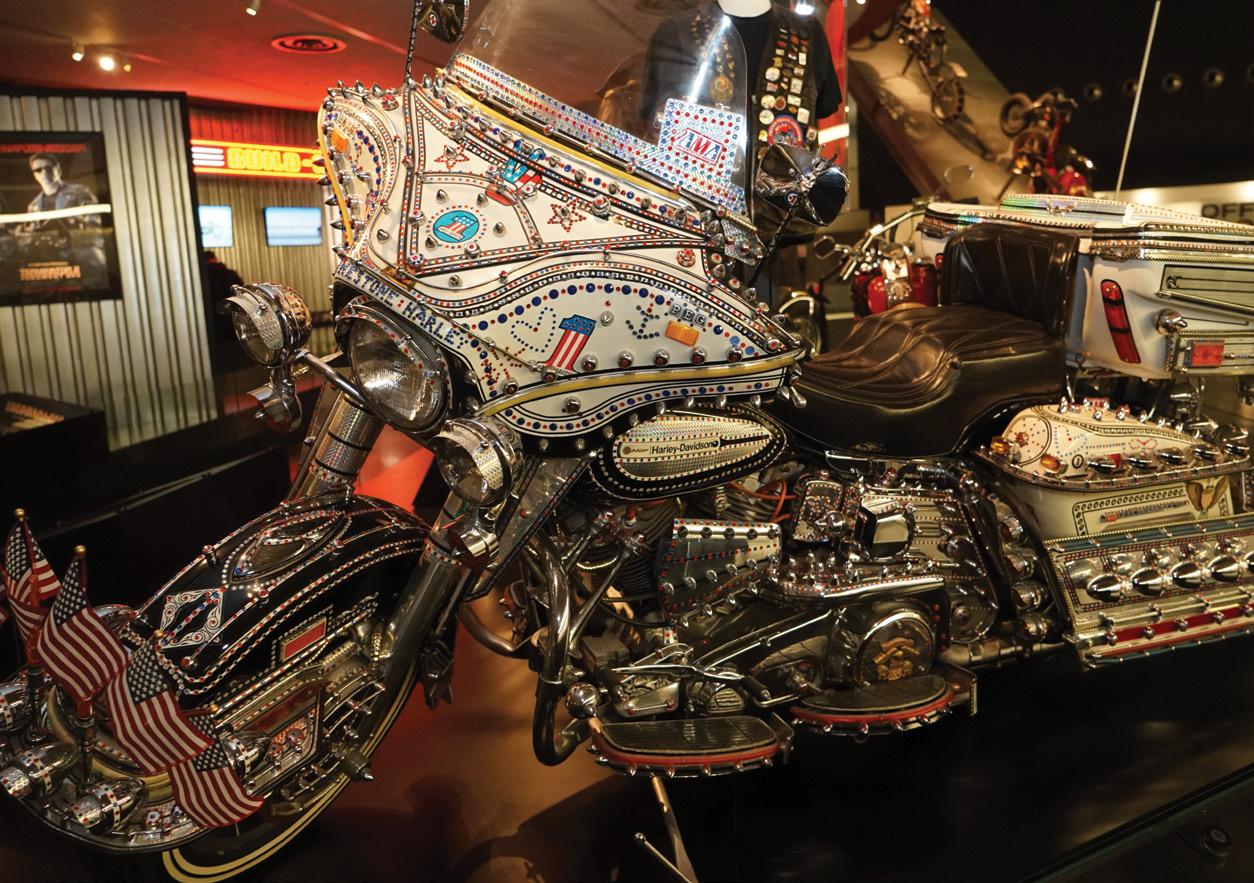
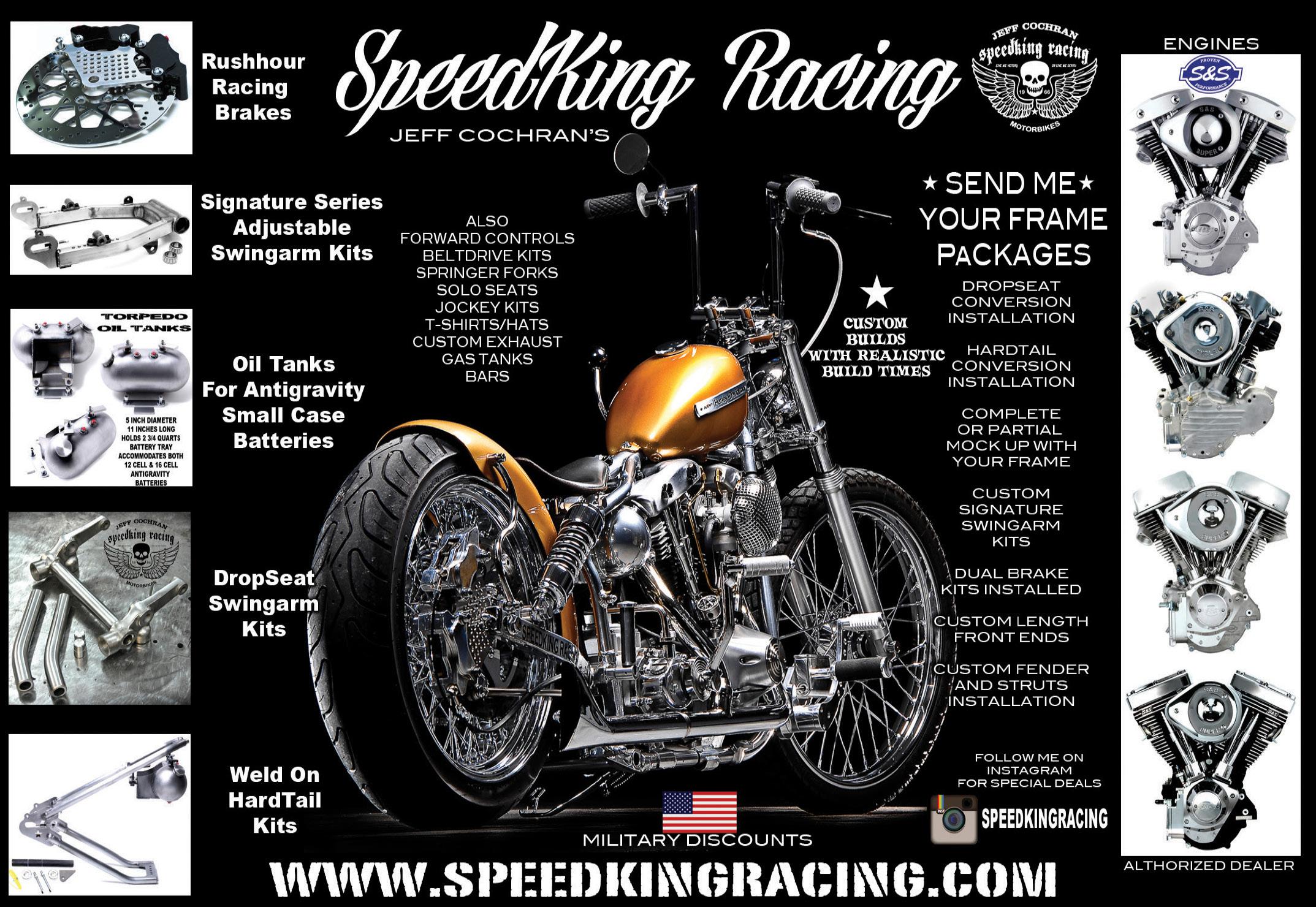