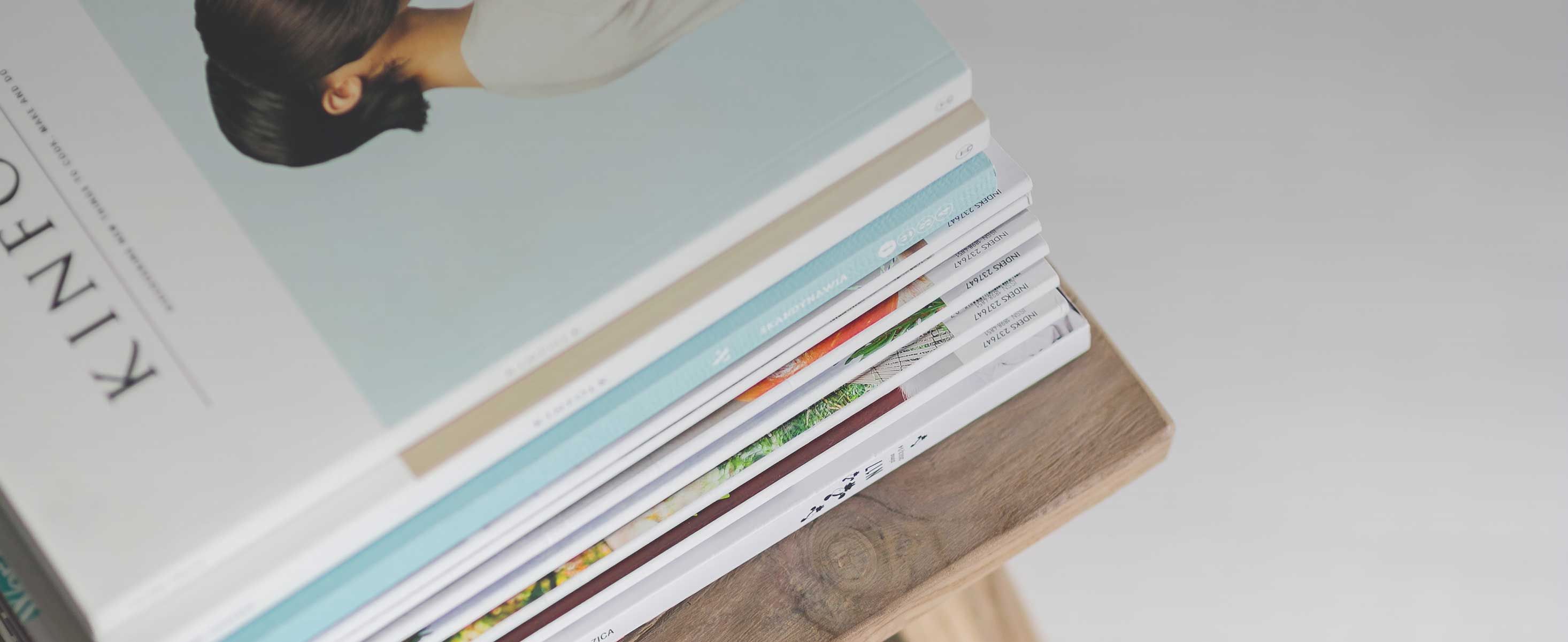
3 minute read
OCCUPATIONAL HEALTH AND SAFETY
Occupational Health And Safety Policy
For Comer Industries, people are at the center of the sustainable development strategy, and the ability to achieve sustainability goals depends on them. Therefore, the protection of health and safety in the workplace is an indispensable factor in the performance of any activity.
The Company decided to tackle it with a systematic approach and implemented a Health and Safety Management System that complies with the ISO 45001:2018 standard, a system that helps prevent occupational injuries and illnesses by integrating risk management into decision-making processes. The system is certified by accredited bodies and involves 96% of workers. The rationale behind the model is to identify and prioritize risks so that corrective actions can be planned and executed more systematically. Risk assessment extends to all factors with an impact on work: from hazards related to specific processes to the characteristics of the environment and its evolution, such as changes in the regulatory framework or environmental conditions.
In defining the action plan, promoting the participation of the workers involved through cross-site working groups at each site, the Company identifies the technical, organizational, and procedural prevention and protection measures to be taken as per the following hierarchy: a. Eliminate the hazards b. Replace them with less dangerous processes, operations, materials, or equipment c. Use technical-design measures and reorganize the work d. Use administrative measures, including training e. Use appropriate PPE
The effectiveness of the actions is constantly monitored through the analysis of performance indicators and periodic audits performed by both the production staff of each site and the functions of the headquarters in order to identify any deviations and implement timely corrective actions.
The continuous improvement of performances and of ever safer and more ergonomic workplaces is underpinned by an inclusive approach, based on the participation of all workers in the identification of dangerous situations, through initiatives aimed at the widespread awareness of risk and the active role of workers in improvement processes.
As soon as they join the Company all workers are involved in a structured training program to establish a culture of safety and respect for the rules, promoting responsible behavior. A system is in place at all sites through which all workers can identify and report potential hazardous situations before any negative event has occurred, e.g., unsafe behavior or conditions or near misses (i.e., situations in which a negative event has occurred but produced no effect (injury)).
Each report is analyzed and processed by a technical team to implement related risk mitigation actions and communicate feedback to the person who identified the hazard, with the understanding that continuous action on hazard reports and causes can help progressively reduce the number of injuries.
In 2022, 3,184 prior warnings of potential danger were recorded, or 0.84 warnings per capita, and more than 250 audits were performed.
The same high safety standards are also applied to all those who access the Company's premises in any way, be they contracted suppliers or simple workers. Those entering the Company must always first receive instructions supported by audiovisual and digital media illustrating the risk areas and the rules and criteria to be observed while on the Company’s premises. The visit of contractors is always preceded by a preliminary assessment of technical fitness and training. Even thereafter, the Company employees accompanying the visitor constantly monitor their behavior and work.
Problem Solving
In the event of an accident, systematic analysis procedures based on a structured problem-solving methodology are initiated, aimed at removing the root cause so that the event does not happen again. Subsequently, with a view to prevention and the dissemination of best practices, the possibility of extending the identified corrective solution to other areas or production sites is assessed. The same approach is also proactively applied to near misses.
Health Management
Capitalizing on the experience gained in the management of the Covid-19 pandemic, the Company continues to consolidate its health measures, also consistent with the evolution of each country's national regulations.
More specifically, the main activities are:
• Adequate information on appropriate conduct within the workplace.
• Workplace access procedures for employees and outside companies.
• Hygiene measures and sanitization.
• Adoption of PPE even beyond the requirements of national regulations.
• Changes in the organization of work.
• Management of possibly symptomatic people in the Company.
• Health surveillance.
Actions taken to facilitate the proper implementation of the measures taken include the installation of facial thermoscanners for taking temperatures, daily distribution of protective masks, and shift planning aimed at ensuring spacing between operators.
In some sites, especially in Germany, preventive tools such as the distribution of free infection testing and the organization of vaccination campaigns have been added to the above measures. In cases of infection, coordination with Health Authorities continues to be ensured, contact tracing where necessary, and providing maximum cooperation in resolving the cases identified.