A dverti $ er Component manufaCturing
“How Important is Training in Your Operation?”
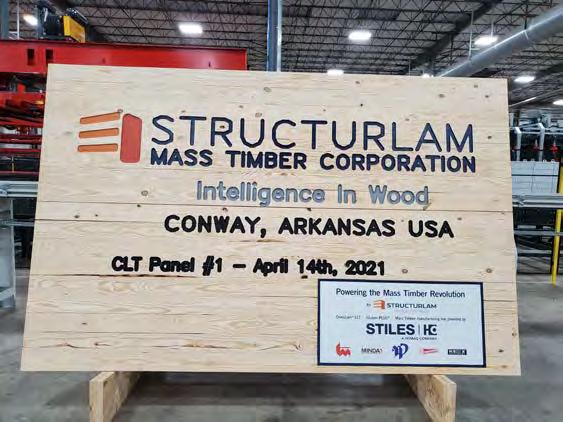
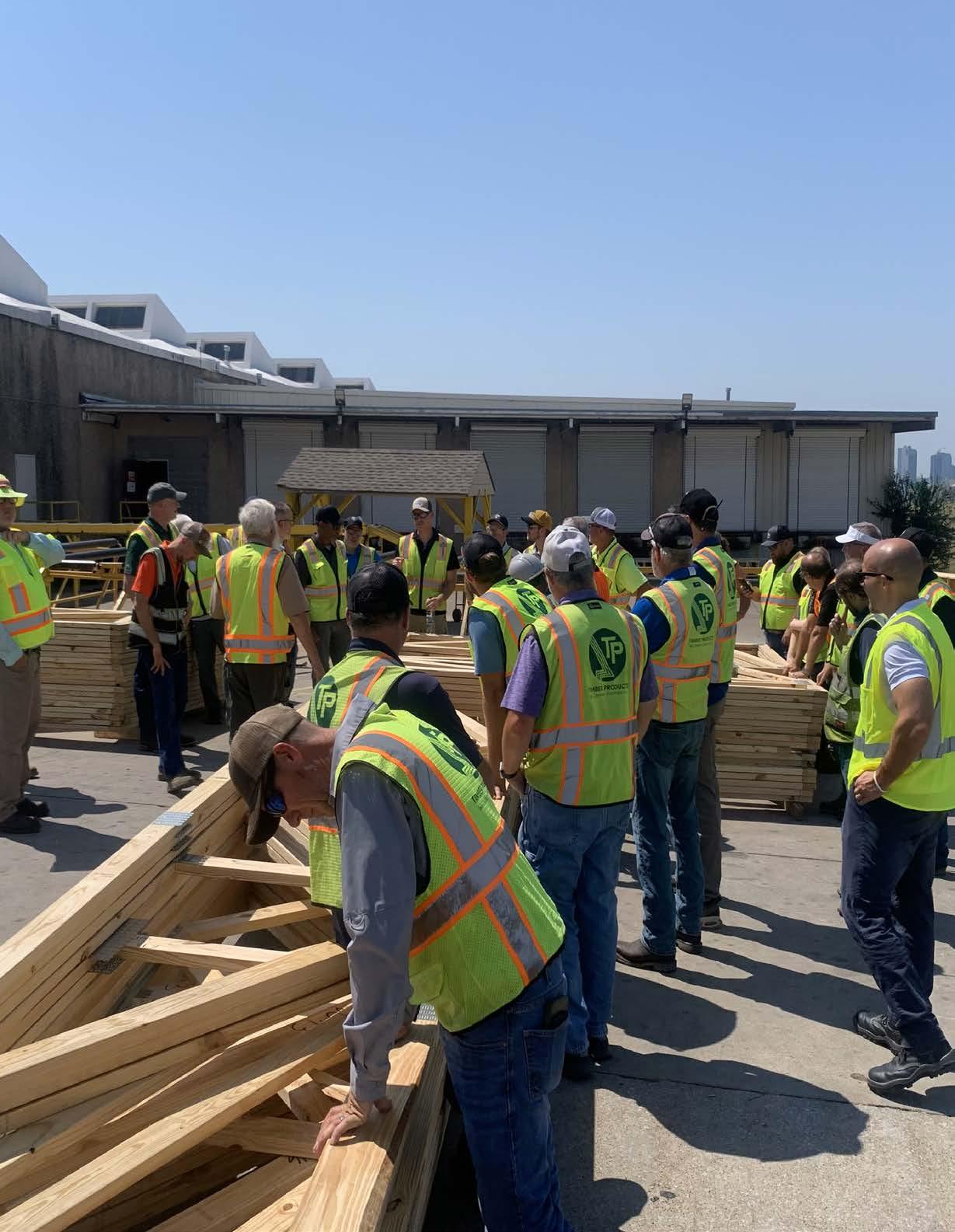
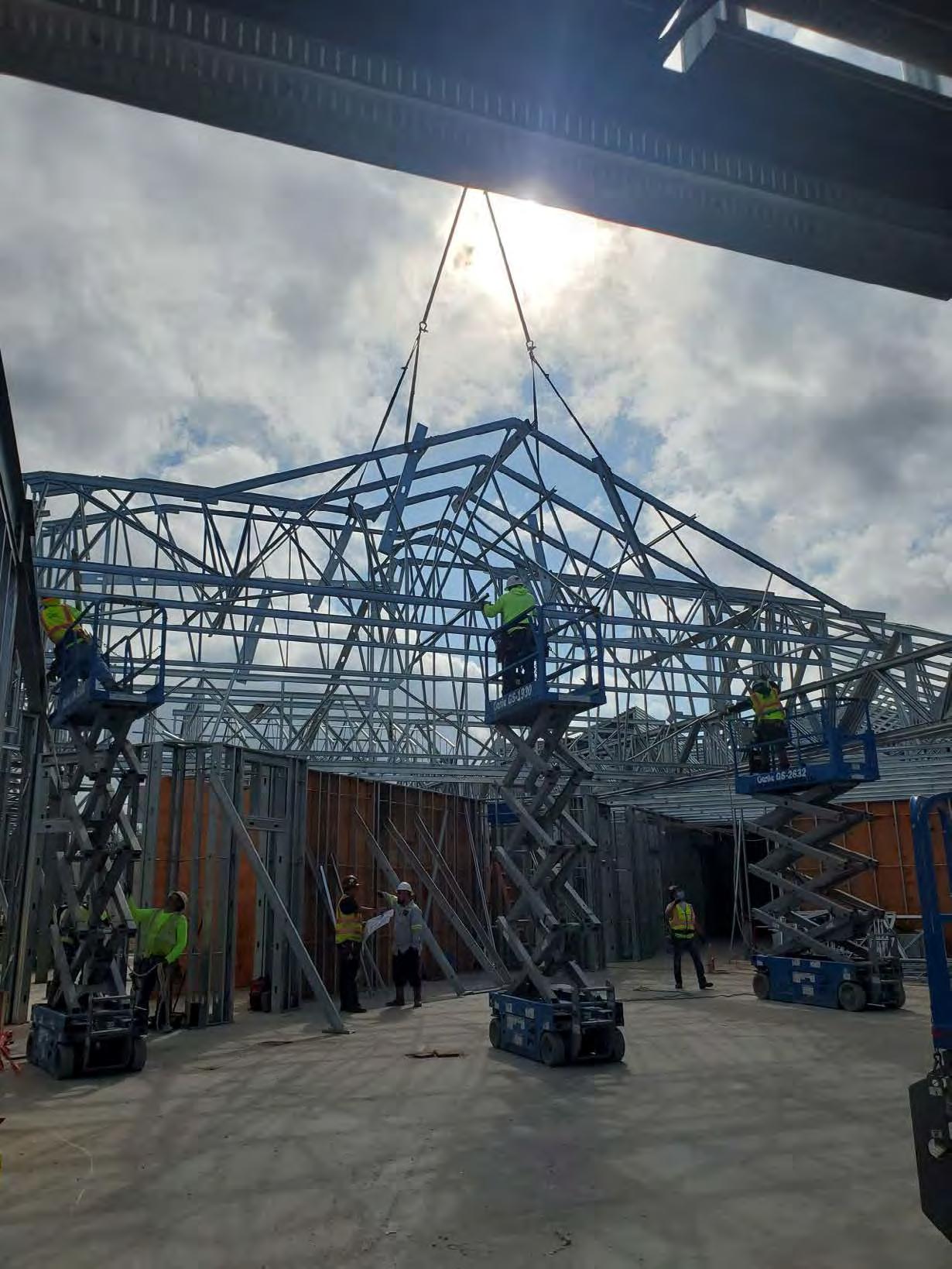
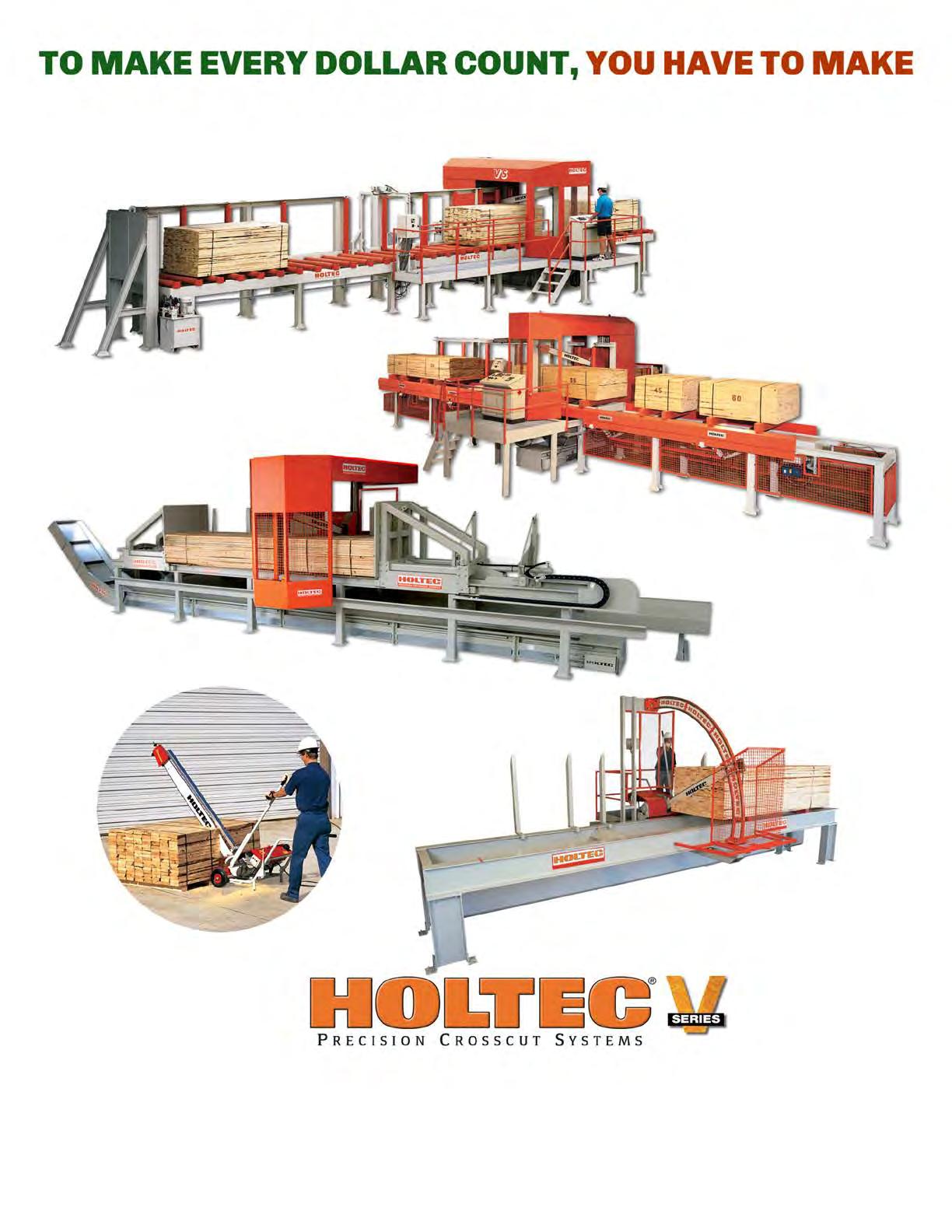
“How Important is Training in Your Operation?”
Anna Stamm – Advertiser Forum: True Colors
Joe Kannapell: Homebuilding Technology, Part III: Overcoming the Prefab Stigma
Wendy Boyd – Spida Machinery: Machinery Software That Works For You!
Todd Drummond Consulting, LLC: Leadership in Challenging Times
Glenn Traylor: How Important is Training in Your Operation?
Ed Lim – LimTek Solutions: Gear Up for Winter Work Just Like Winter Sports!
Triad | Merrick Machine Company: Planning for the Triad National Trade Show
Steve Schrader – Hundegger: Getting Up to Speed at Hundegger: The Future of Automation is Here
Ed Serrano– Vekta: An Ink-redible Advantage: The Vekta P3 Revolutionizes Frame and Truss Printing
Darrin Schramm –Stiles Machinery:
5 Reasons Why Your Wall Panel Production is Underwhelming
Carl Villella – Acceptance Leasing: Navigating the Workforce Shortage: How Technology and Equipment Financing Can Help
Thomas McAnally – TheJobLine: The Benefits of a 32-Hour Workweek for Truss Designers
Geordie Secord – Design Connections: Addressing the Truss Designer Shortage
Jay P. Jones, P.E – TPI: What the Latest ANSI/TPI-1 Updates Mean for Truss Designs
Frank Woeste & Joseph Loferski – All Things Wood: Existing Deck Inspection— A Must for Springtime Celebrations
MSR Lumber Producers Council: MSR Workshop Heads West for Valuable Learning Opportunity at Resort Destination
Craig Webb – Webb Analytics: Deals Report 2024: Tracking the Openings, Closings, and Acquisitions
MiTek Staff: MiTek Structural Products Compliance with New Building Codes
Simpson Strong-Tie Staff: Managing Uplift Reactions
Joe Kannapell – The Last Word: Home Depot’s Quest for the Pro Builder
Serving the Structural Building componentS induStry
New & Used Equipment
Saws
Truss Equipment
Panel Equipment
Trucks & Trailers
Misc. Equipment
Door | Stair | Window Equipment
Safety First
Calendar of Events
TheJobLine - Jobs & Candidates
Industry News
Directory
Hiring Zone
4Ward Solutions Group
A-1 Industries
Leasing & Financing
Acer, Inc
Advanced Component Solutions
All Points Technical Alpine
BuyMetrics
Clark Industries, Inc.
Eagle Metal Products
Eide Machinery Sales, Inc.
Element Equipment
Fitzgerald Group
HOLTEC USA
Hundegger USA
LFT Strategies
LimTek Solutions
MiTek
Panels Plus
Paragon
Precision Equipment
ROGworx Automation
Simpson Strong-Tie
Spida USA
Stiles Machinery
The Hain Company
TheJobLine
Timber
Todd Drummond Consulting, LLC
Triad | RUVO | Merrick Machine
Truss Builder Parts
Vekta Automation
Associates
Publisher
Thomas McAnally twm@componentadvertiser.org
Editor Anna L. Stamm 800-289-5627 x 3 anna@componentadvertiser.org
Distributed FREE Via e-mail subscription Download PDF or Read on line at www.componentadvertiser.com
News of Interest and Advertising inquiries can be submitted to: anna@componentadvertiser.org
An Open Forum for many sources.
Deadline 20th of each month. Articles, Trade Names, and Logos are the property of their respective owner or creator unless otherwise noted
Disclaimer: We reserve the right to refuse any advertisement or material that we deem not in the interest of the industry or the Advertiser. Permission to use content is the responsibility of the contributor including permissions to use any likeness of persons.
The Advertiser is provided “As Is” including typographical errors, omissions, and mistakes both intentional and unintentional.
Believe it at your own risk!
Copyright 2008-2025
Component Manufacturing Advertiser
The Advertiser 7586 Becks Grove Road Freetown, Indiana 47235 no reproduction in whole or in part without permission from the component manufacturing advertiser
Archive Copies Available On Line www.componentadvertiser.com
Anna L. Stamm Director of Communications and Marketing Component Manufacturing Advertiser.
Can you predict someone’s true colors by their resume alone? Probably not. The better indicator will always be actions. To the extent that a resume can capture past actions, it will help you get to know them. But, keep in mind that a complete picture will consist of more than bullet points.
Especially now that anyone can access virtual assistance in writing a description of who they are, what is presented in text will be a dim reflection of a person. So, what can you do? Here are a few things to consider:
1. Listen: When you speak with someone, actually listen to their answers. Sift out the expected replies and consider what else was said. Were the words said with a sense of humor? Or, was there arrogance and condescension? What additional information did they want to contribute?
2. Don’t Jump to Conclusions: It’s important to avoid a rush to judgment. An individual’s sense of humor can be misunderstood at first. Likewise, people can be nervous, shy, or apprehensive, and that will affect how they interact with others before feeling comfortable enough to relax and be themselves.
3. Consider Actions Not Just Words: Will a person assist in picking up a mess or simply step over it? Will they offer to help someone when there is no direct benefit to themself? What have their actions demonstrated?
Be it making friends or hiring employees, another factor will be what you’re seeking. If you’re filling a sales position, you may prioritize someone more focused on profits than people. Pursuing dollars first and putting everything else second is a working strategy…for some people. The question you need to answer is – which characteristics and goals do you value?
In my sister’s professional career, she always went the extra mile for anyone who needed help. She worked endless hours of overtime and sacrificed countless weekends, helping her authors from manuscript to printed page while also supporting her coworkers as best she could. Over time, she was not well rewarded for her job; rather, she was often disrespected and treated poorly. Yet she continued to persevere, because she had the heart and commitment to prioritize the needs of others, and she knew her work and skills had value. Reading the tributes to her now, it is readily apparent how much the people she supported truly appreciated her over the years. She is missed, not for the boxes she checked in a job description but for the personal connections she made. Were her sacrifices worth it? How you answer that question depends on what you value.
Monet DeSauw FWA 500 Floor Web Cutter
• Push Button Powered Blade Angulations
• Single Push Button Setting for 2 Blades per Side
• Electronic Digital Readouts
• Backup Mechanical Indicators
• Cuts 4 Angle Webs, Cantilever Webs (2 piece webs) & Square Blocks
• Magazine Lumber Feed for 3x2, 4x2 and 6x2 Lumber 12 1/2” to 48 1/2” Length Capacity (7” Minimum on Square Blocks)
• 60 Pieces per Minute
• (4) Internal 16” Blades & (1) External 16” Cut-Off Blade
• Pneumatic Blade Brake on External Blade
• Dust Hoods
• Belt Waste Conveyor (under saw)
• Add $4,300 for 12’ Incline Waste Conveyor (adjacent to saw)
• Add $2,100 for Extra Set of Blades
• 480 Volt / 3 Phase FOBMO Call For Pricing
• Automated (Truss Design Software Download) or SemiAutomated (Touch Screen Entry) Operation
• All Movements are Computer & PLC Controlled
• Comprehensive Setup Screens Display Each Piece with Setup Data
• 22” x 40 Tooth Blade on PAE Cut 1 or 2 Boards up to 20’ (2 Second Plunge Cut)
• Cut Chords, Webs, Rafters, Wedges & Stair Stringers
• Cut Long Scarfs by MultiPlunging
• Servo Positioning on Infeed, Angle & Outfeed Pusher
• Over Travel Protection
• Ink Jet Printer
• Lumber Optimization Program
• Belt Waste Conveyor
• 480 Volt / 3 Phase / 60 Amp
• Includes 5 Day Onsite Installation & Training
• Optional Monet DeSauw Live Deck, Bunk Feeder & Incline Belt Waste Conveyor FOB MO Call For Pricing
• Touch Screen User Interface with Backup Mechanical Controls
• 3 Operating Modes: Auto, SemiAuto & Manual
• All 20 Axes of Movements are Computer & PLC Controlled
• Comprehensive Setup Screens Display Each Piece with Setup Data
• Anti-Collision & Optimizing Programming
• Auto Calibration Productivity & Time Tracking
• Maintenance Diagnostics
• Variable Speed Conveyor (0-50 Flights per Minute)with Powered Hold Downs
• (1) 30” x 80 Tooth Blade (27 3/4” Scarf on PAE)
• (4) 16” x 40 Tooth Blades (13 1/2” Scarf on Centerline)
• Pneumatic Blade Brakes on all 5 Blades
• 16 1/2” to 20’ Length Capacity (11” Minimum on Square End Blocks)
• Vibrating Waste Conveyor Under Saw
• 480 Volt / 3 Phase
• Includes 4 Day Onsite Installation & Training
• Add $2,900 for Extra Set of Blades
• Optional Live Deck, Label Printer, Ink Jet Printer, Catcher Display & Incline Belt Waste Conveyor.
Automatic Truss Jigging System to drastically reduce setup times. Allows for 100% embedment on the table, with top & bottom chord pucks in the same slot. TopSider or standard configurations available for conventional kick-leg, walk-thru, or our new trackless 8' and 10' continuous table systems. Systems for other roller & hydraulic gantries are coming soon. Available in new machine installations or for retro-fitting your existing table. The TopSider is exclusively applicable for “kick or flip leg” style truss presses such as the Tri-Axis & Lumbermater®
• Capable of 100% On-Table Nail Plate Embedment
• Two Pucks Per Slot
• 24", 26", and/or 30" Spacing
• Compatible with all current major design software
• Multiple Simultaneous Layouts
That'sallthetimeittakes todrillstudsforrunningRomexorotherelectricalwireinthewallpanels
Motor: HeavyDuty5HP-3phase-220vor440v(Pleasespecifywhenordering)
MotorcarriagebearingandspindleassemblymountedonBlanchardgroundsteelplate LinealmotionishardenedandgroundVbearingsandrails
BlockSizes: 2x4through2x12infiniteheightsettingtocenter
AirSupply: 100psi10CFM
Drills: 2wing3/4'”CarbideTippedcanaccommodatesmallerorlarger
Spindles: AlloySteelpolishedandgroundprecisionshafting
Frame: 2"SteelWithPowderCoatFinish
Covers: 10Gauge(1/8"Thick)Aluminumremovable
Dimensions: Height-60inches,Width-33inches,Depth-33inches
Shippingweight: 750lbs.-(Includingcrate)
MADEINAMERICABYAMERICANS
By Joe Kannapell
Even though 500,000 prefab homes were built for World War II, builders were not committed to the prefabrication approach. But why not? These homes should have served as an entré to the future use of components by the hundreds of builders who constructed government housing in hundreds of communities. But the results of a 1943 survey showed that less than one-quarter of builders planned to use shopfabricated parts after the war. Many believed that wartime housing was of poor quality, regardless of the actual quality of any trusses used in them. There was opposition to ongoing governmental involvement in housing after the war, which builders felt was usurping their opportunities. And finally, those who built these half-million homes had to fabricate trusses under challenging jobsite conditions, which also discouraged the continuation of these practices.
Many of prefab’s quality issues arose from the type of housing that was constructed, which was designated to be temporary or demountable, intended to be disassembled after the war. While most of these housing units were fully componentized, the parts were mostly fabricated onsite, in all types of weather, at an extremely demanding pace. The panels were bolted together, and the trusses were set 4’ on-center, which deviated from standard framing practices and implied substandard quality. Few of the amenities associated with permanent structures were provided, further diminishing the overall quality. Thus, traditional builders generalized from that experience and cast dispersions toward all prefabrication. One survey of 40,000 dwellings being built in Los Angeles in 1946 found that “an overwhelming percentage were conventional in type and were being built by the same builders who had been erecting homes there before the war. Some of the prefab outfits, who turned out shoddy houses a year or so ago, are finding the going tough now that the conventional builders are underway.” Traditional builders’ animosity was surely compounded by the fact that their resistance to the use of components during the war years had severely restricted their opportunities during that time. Thus, this resistance plus the stigma of “poor quality” continued to taint prefabrication long into the future.
The government’s apparent preference for this “shoddy” type of housing even after the War also frustrated homebuilders. In an effort to alleviate the severe shortage of housing, President Truman signed legislation to expedite housing construction. However, a bureaucrat named Wilson Wyatt determined that up to 850,000 prefabricated units needed to be built by 1947. This caused a huge outcry by the National Association of Homebuilders and its local homebuilder affiliates, who already faced material shortages and were slowly recovering after the war years.
The experience also tainted the use of trusses specifically, mainly due to the complexity of their connections and the cost of their fabrication. On longer spans or when they were designed for higher loads, trusses were made of heavy, overlapping timbers that were attached using split-ring connectors. Joining the members was a daunting task, requiring routing and drilling matching surfaces at each overlap to receive the connector, and then installing bolts with 3” washers on the outer surfaces of members. Builders who had to deal with snow loads and/or restrictive urban building codes would naturally hesitate to use heavy, split-ring connected trusses, especially because most lacked powered lifting equipment onsite.
Despite the perceived disadvantages, some builders continued to pursue prefabrication and components while overcoming the challenges they presented. In particular, the Levitt family had learned the hard way how to use components. Although they had studied the use of prefabrication and built several componentized houses before the war, they were slow to start using them when they began building a 750-unit wartime housing project in Norfolk, Virginia. After falling behind, they began assembling components onsite, including split-ring trusses. That helped them develop the production-line approach that they followed in constructing the first two Levittowns (even though they decided not to use trusses in these). The Levitts set up a pseudo-assembly line in a shop onsite at both projects, where they plumb-cut rafters and butt-cut ceiling joists, as did many post-war homebuilders on large sites. When the Levitts were well into their third large project in south New Jersey, they surely influenced Lenny Sylk’s decision to enter the component business, leading to the lasting legacy of his Shelter Systems’ businesses.
Besides traditional builders, another large contingent helped overcome the stigma of components – the group led by James Price and his brother George. Building modest midwestern-style ranch houses before the war, they recognized the potential of prefabrication, telegraphing their ambitions by naming their company National Homes in 1940 and opening a prefab factory in Lafayette, Indiana. They made a bold bet at the start of the war, offering to supply up to 750 units per month for wartime housing, resulting in their successful supply of a total of 7500 units. While Price suggested that most of these homes were nothing but “glorified chicken coops,” they enabled his company to standardize parts, master pre-assembly, and perfect packaging and shipping, beginning the next phase of homebuilding technology – prefabrication.
Several developments in the sunbelt spurred the use of trusses more quickly there than by their counterparts in the north, because plywood gussets and bolts could be used instead of split-ring connectors. Such was the case in the Wynnewood Village project in Dallas in 1946, named after the Wynne family. Using plywood-gusseted and bolted connections, the Wynnes set up a shop onsite to precut truss parts and assembled them on ground-level wood tables, ultimately fabricating tens of thousands of mostly 30’-2” trusses for the 12,000 units they built by 1959. These types of repetitive housing projects in Dallas surely inspired a local lumber yard proprietor, Charlie Barns, to become one of the first truss fabricators in the country, ultimately leading to Dick Rotto’s storied success with Trussway.
Thus, prefabrication retained a presence in the homebuilding industry. Slowly but surely, it was proving its advantages. Although faced with many detractors and many challenges, prefab was evolving into a more acceptable practice, and that would accelerate over the 1950s and 1960s.
Next Month: Prefab Hits Its Stride
Get the industry-leading software and automation technology you need to scale your business. Overcome market challenges, boost productivity, and confidently meet demand when you choose MiTek as your solution partner.
Are you ready to scale your success?
Elevate Your Wall Panel, Floor Truss or Roof Truss
Manufacturing with 4Ward Design Solutions’
Precision Component Design Services!
When you work with us, you get: and best of all...
Speed and Scalability
Adjustable Hours
No Need for Training
Reduced Regulatory Burdens
Reliable Timelines
Extend your existing capabilities with 4Ward's design expertise. Without the hassle and expense of training your own designers, partnering with us guarantees that each wall panel, floor truss or roof truss will be designed for structural integrity and production and field efficiency.
Achieve cost efficiency without compromising on excellence. sensitive approach ensures maximum value for your investment.
Leverage our expertise, ensuring every component is attentively designed for optimal performance and durability.
We understand that every component project is unique. At 4Ward, we create custom designs, tailored to your exact specifications. Contact us today for a complimentary consultation.
As a longtime partner to the construction industry, Simpson Strong-Tie continues to explore and invest in advanced equipment. Around the country, manufacturers and LBMs are already gaining speed and accuracy with our EasyFrame automated marking and cutting system for wall panels. Now with Monet DeSauw truss machinery — a full line of precision component and linear saws — you have all you need from one source. Along with industry-standard connectors, fastening systems, software and professional design services, our cutting equipment is available nationwide. It comes with fast, onsite installation and in-depth training to get your team up and running, plus expert support. Learn more at go.strongtie.com/cs or contact your sales representative.
Wendy Boyd Chief Customer Officer Machinery Group Spida Machinery
Looking at the year ahead, a number of predictions have said the manufacturing landscape in the US is set to grow. This is being driven by several factors including advances in technology, increasing use of automation, and changes within the economy, as well as changes to the workforce with a growing number of skilled workers retiring.
These changes will force businesses to look inwards at their manufacturing operations and focus on key elements that will allow them to remain resilient, productive, and competitive. Now is the time to start looking at efficiencies within your own business and consider how software and automation can support you in realizing your 2025 goals. Here, we’ve highlighted some areas where our software can help you with this.
Spida Machinery is renowned for taking something that is quite complicated and making it simple – this applies to our software too. Our software is integral to everything we do and is cleverly designed to work in perfect tandem with our machinery and accommodate the nuances of different frame and truss manufacturers around the globe.
Brett Kinny, our Machinery Software Manager, explains what makes our in-house software so unique. “Our software isn’t just built to meet the demands of today’s manufacturing world, it’s designed to make a real difference for your business. With powerful features, intuitive design, and a deep understanding of manufacturing complexities, we deliver solutions that drive results, enhance safety, and streamline operations for maximum efficiency.”
Not only is our software designed to be simple, fast, flexible, functional, and feature rich, it’s also been developed with manufacturing complexities in mind. You know first-hand the common issues you experience within your manufacturing operation. Here are some examples and how our software can help.
● Inefficient Processes – reduce errors and rework by using our software control and automation. Also, reduce waste in your factory through optimization.
● Downtime on Machines – our high quality, robust machinery, coupled with our intelligently designed software and automation, means downtime in your factory is reduced.
● Staff Training Time – the intuitive design of the software and onsite training means your team will be up to speed quickly and skillfully operating your Spida machines. With the change in workforce dynamics and many skilled people retiring, training and growing knowledge will become even more important.
● Keeping Up with Technology – our software uses the latest technology, and with regular software updates available, you’ll continue to get the best out of your Spida machine.
You may ask why it matters and how you benefit from having us design, develop, and support all of our software. Well, when you choose Spida Machinery, you’ll reap the benefits of our in-house capability in more ways than one.
● Dedicated Software Team – we have a dedicated software team across the globe consisting of 10 personnel including automation engineers, software developers, and testers. This allows us to be involved in all areas from the design and development through to the support and continuous improvement of our software.
● Agility and Responsiveness – designing our own software allows us independence, which means we are agile and responsive and not constrained by an external software provider. Being free of third-party software suppliers allows us to be innovative, intuitive, and future focused.
● Supporting Your Needs – we pride ourselves on providing exceptional customer support, and with our experienced team with diverse skillsets, we’re well placed to promptly service your needs.
We provide complete end-to-end software for your manufacturing requirements, allowing you to benefit in these key areas.
● Simplicity – our software is easy to learn and easy to operate, with graphical representations on screen. Also, you’ll experience efficiency gains as the same software is used across the majority of Spida machines.
● Productivity – the automation and batch optimization will have positive effects on your throughput. You’ll see increased numbers without adding extra labor.
● Capability – our feature-rich software is designed for Just-In-Time or Batch-Based Optimization. Accurate and customizable printing and plate marking is available too.
● Flexibility – our software can be driven direct from the detailer’s desk or by the operator on the factory floor. Management can assign jobs to operators while sitting in their office.
● Reliability – developed over many years, our robust software is running on hundreds of machines worldwide. It excels in the tough operating environment of frame and truss manufacturing.
● Versatility – the software will cater to the jobs you have at hand! Whether you’re working on a small or large job, the software responds accordingly.
Tailor-made for our range of Spida machines, our TandemOne suite of software supports every step of the manufacturing process for our frame and truss customers. Our software modules include:
● Job Handling,
● Batching,
● Cutting,
● Frame Assembly,
● Truss Assembly,
● Reporting, and
● Diagnostics.
Fo r more details on these modules, please visit our Spida software page.
And, the best part is that you’re never “on your own” when you work with Spida! We’ve designed our software to allow for easy remote support. Instead of having to physically be onsite for diagnostics and troubleshooting, we can dial in remotely to diagnose issues and apply changes. The fact that our software offers comprehensive logging and remote support functionality means we’re always here to help.
With each new year comes new goals and new focuses for your manufacturing business. Whether you’re wanting to grow your production capability, maximize throughput, increase efficiencies, improve safety, or rely less on manual labor – then we encourage you to get in touch with us. The combination of our high precision, robust and reliable machinery with our initiative easy-to-use software is a perfect mix to help you achieve your goals.
We’d love the opportunity to talk more and support you in achieving your 2025 manufacturing goals. Please get in touch.
Line Upgrade with WizardPDS® Retrofit Tables With High Slope Lifters, Side-Off Rolls, and Truss Exiting Conveyor Systems.
Whether you’re looking to replace outdated components, add to your existing line, or replace an entire system, our expert team will ensure that your new equipment is installed and configured to work in harmony with your existing setups. Upgrade your line with the latest in automated table technology, reconditioned or New-Legacy Gantries, safety and control panel systems, and material handling solutions. Everything you need to improve performance, reduce downtime, and stay ahead of the competition. Upgrade With
Inspired by ten years of intensive field experience and the ample and detailed feedback of numerous customers, we’re pleased to introduce the most advanced, most enhanced and high-performance Terminailer yet-Terminailer V.8. Drawing on invaluable time in the trenches closely evaluating Terminailer’s performance under varying conditions, our engineers have incorporated critical learning and insight to enhance simplicity, performance and operator control. Just part of what V.8 offers includes:
•Vastly enhanced operator control for even greater productivity
•A redesigned nail-feed supplying EverWin PN90-PAL industrial nail guns
•Simplified pneumatics featuring direct air-supply to all six nail guns
•Even more sub-component profiles for wall design flexibility
•Rugged durability with pharmaceutical grade assembly
Developed by people who know well the mechanics, safety considerations and business aspects of wall-panel production, Terminailer V.8 combines more enhancements & operator-friendly features than ever to take your productivity to the next level and beyond. Contact us to learn even more and to put the V.8 performance in motion at your facility.
As the competition gets more aggressive and the markets have slowed, your company’s sales are inevitably slowing, and margins are dropping. Let us face the fact that these are now becoming challenging times, and leaders must face these challenges in a healthy way. Whether you are a line supervisor or the corporation’s CEO, your job will not get easier in the coming years. When sales and margins were flush, it was much easier to maintain the status quo and be viewed as doing a great job. But now that the markets are slowing, you really are going to know the true tests of leadership and having to shoulder all the burdens and blame that comes with your responsibilities. Let me give you just two crucial behaviors that will help you evaluate your strengths as a leader within your organization. Both are excellent examples that should make you rethink what and how you may be performing in your world of influence.
Yesterday’s Solutions Are Not Always the Right Solutions for Today’s Challenges — Relying on what you think is the most common solution for your current challenges may be the wrong thinking for every circumstance. Doing the same thing and believing it will always give you the same results when the market changes can be dangerous. Anyone who has read about the most successful leaders of sports teams or companies will be able to find plenty of examples of leaders who did not accept what was most common within their industry but thought outside the box. Within the building industry, many decision-makers are unaware of what things can, if any, be improved upon by thinking outside commonly accepted practices.
• Design — How many design managers feel the solution to meeting the ever-increasing demand for their work is more bodies to perform the same task? How many off-shore designers must a company hire, making them more bound to their vendor, and negating any bargaining strength? When was the last time the design process was reevaluated so that some other solution might assist and alleviate the burden on the design group? Never be so bound to any particular process that you think it cannot be improved upon. Are there ways to reduce and improve the design process that will significantly improve it? For most companies, the answer to that question is “yes,” but few are willing to make the effort and prefer to stay on their current course. For example, most quotes for roof trusses should take no more than ten to fifteen minutes to produce a reliable, accurate quote – can your company do that?
• Manufacturing — When capacity and labor issues are causing concerns, most believe the obvious solution is new automated equipment and facilities. For many, the “safe” decision is to go with the recommendations of their current vendor. These recommendations often include new processes that, on the surface, would theoretically reduce labor needs. However, the reality of what was promised and the end results are not always what was delivered, inevitably leaving the decision-maker at a loss as to what should have been done. I cannot state enough that what may seem straightforward may not be the right solution. So many companies are willing to spend millions of dollars on what they believe is the right solution but are unwilling to pay a fraction of the total to potentially get a far different perspective, make a more informed decision, and save tens of thousands of dollars. For example, a common mistake is believing that only two roof truss assemblers on a roller gantry table is the most economical setup. The frequent justification for two assemblers per workstation is because they use a board foot per work hour as the measurement. The result is no actual labor savings per truss and a severe reduction in capacity.
Safest Option — If you are responsible for a given area, whether a small group or an entire company, your job is to oversee the work getting done in the most efficient means possible to meet the company’s goals. This means you are responsible for the process that constantly needs updating and refinement for the entire group, not just the daily efforts for your order processing. Updating and refining takes effort and time, but many are unwilling to make this happen. The most common excuse is that they were too busy. If you are too busy to make meaningful changes because you are too busy, how effective do you think you are at your job? Time and time again, the companies that are struggling the most are the ones that did not make the changes needed to keep up with the changing times.
New vendor salespeople in our industry are surprised by the all too common actions of a potential client suddenly not responding to any of their communications. No matter how well they believed the previous conversations were going, all communications suddenly can stop without any explanation. Not even a simple reply to an email or text message is provided. Months or even years later, an explanation might reveal itself, but the most common reason is that they got caught up in their day-to-day business and no longer had time to make any decision or change they were contemplating. They believed they were too busy and could not take the time to even respond to the vendor salesperson. Seriously? One is too busy for the common courtesy of a simple email, “Thanks for your time, but we need to put this decision off until….” This has happened to TDC, and I have heard about it from every other vendor within our industry many times.
Solution — As markets and conditions change, do you want to play catch up or be the effective leader so that you can head off potential problems before they happen? Weeding out the best solution for both the near and long term while not getting too caught up in your daily tasks is the main challenge for every leader. What every leader needs from time to time is a new perspective and new ideas. The excuse we are too busy can not be acceptable. Now is always the right time to make changes and not allow inaction from doing what is best for your responsibilities. TDC sees this with every client, knowing there is no best one-size-fits-all solution for everyone and that everything must be tailored to the client’s needs. In my case, I don’t have to play internal company politics or favor any particular vendor, so I am able to pull people back from the trees and allow them to see the forest from a new perspective to offer the best-in-class solutions. Maybe it is time to remind yourself that getting a new perspective and best-in-class suggestions from a very successful solution provider called Todd Drummond Consulting is the right thing to do.
“If any of you lacks wisdom, you should ask God, who gives generously to all without finding fault, and it will be given to you.” — James 1:5
TDC is your best source for learning about proven and practical lean manufacturing best practices combined with industrial engineering principles to keep your company at the leading edge of competitiveness. Cost savings and net profit gains that usually take months or years can be accomplished in weeks or months with TDC. No one is better at providing your team with proven results for good employee practices, pricing, truss labor estimation, and so many other best-in-class practices. All areas are addressed, not just manufacturing. Please do not take my word about TDC’s services, though. Read the public testimonials many current and past clients with decades of expertise and experience have been willing to give.
Website: www.todd-drummond.com • Phone (USA): 603-748-1051
E-mail: todd@todd-drummond.com • Copyrights © 2025
Off-site construction solutions built around your business.
Build higher-quality components and modules more efficiently.
Stiles has been a trusted name in the U.S. woodworking industry for over six decades. Today, we continue to lead the way with a consultative approach to off-site construction, partnering with you to increase speed, precision, and productivity, while providing ongoing parts and service support when you need it.
Invest in equipment built to perform—and last.
Stiles is the exclusive North American provider of WEINMANN, the world’s leading machinery and equipment manufacturer for off-site construction. Whether it’s an individual machine or fully automated system, Germanengineered WEINMANN machines provide innovative solutions that revolutionize your production.
Make your good decisions work even better. Learn More
lnnovationen fur den Holzbau
HUNDEGGER
Hundegger leads the way in automation innovation for the truss component industry. Our advanced CAMBIUM software offers cutting-edge automation and digitalization solutions, revolutionizing operations, boosting productivity, and driving sustainable growth for manufacturers like you.
We go beyond standard mechanization; we champion true Automation. The Hundegger TD-II isn't just a saw-it's a transformative, comprehensive solution designed to streamline your production process. From retrieving lumber to optimizing, nesting, stacking, destacking, sorting, buffering, and precise delivery, our system ensures peak efficiency and productivity, tailored specifically to truss component manufacturing.
Harness the power of data with Hundegger's advanced CAMBIUM TACTICAL software. It meticulously tracks and optimizes your production, ensuring more automated operations and significant productivity gains.
We provide state-of-the-art automation and control solutions that set the industry standard. Our focus on industrial automation and robotics positions Hundegger as the leader in enhancing performance and efficiency in truss component manufacturing and beyond.
Hundegger products are essential for future-proofing your business. Elevate your productivity and secure your competitive edge with our advanced technologies and automation solutions, meticulously designed to meet the unique demands of component manufacturers today and tomorrow.
Don't get left behind. Invest in the future with true automation from Hundegger and see your business thrive.
• Servo Controlled Single Blade Linear Saw
• 7.5 HP Motor (230 Volt/3 Phase) with 20" Blade
• Touch Screen Computer
• Ink Jet Printer
• Powered Infeed Roller Tables & Outfeed Queue System
• (2) Manual Bunk Feeders (saw can be used with or without bunk feeders)
• Waste Conveyor (includes new belt which needs to be installed)
• 240 Volt / 3 Phase
• Motion Control Upgrade in 2018
• New Computer with Touch Screen in 2019
• T1 Axis Rod and Pillow Bearings replaced in 2023
• (4) T1 Linear Bearings replaced in 2023
• (4) Z1 Linear Bearing replaced in 2023
• (8) Belt Drive Linear Bearings replaced in 2023
• Several Belt Drive Wheels replaced in 2023
• New Z1 Actuator in 2023
• Spare Parts: 2 White Drive Belts, Spare Power Cable, Rebuilt Z1 Actuator
• Video available upon
2003 Alpine AutoMill RS Component Saw, Model 344
Computer controlled saw sets up in 2 to 19 seconds and downloads from a network or by using a touch screen for ease of operation. Five-head automated component saw works in both automated (downloading files) and semi-automated control via touchscreen input. It has [23] axes of automated movement, enhanced diagnostics, auto management reporting. The RS cuts from 13″ to 20′ long material in size ranging from 2×3″ through 2×12″, includes [3] 18″, [1] 22″ and [1] 32″ blades with air brakes, shaker pan waste conveyor to incline scrap conveyor, one set of spare blades and any available spare parts. (Infeed conveyor needs electrical service). 480v/60Hz/3Ph power.
$17,997 NOW $12,497 FOB AZ
Wood Tech Systems
765-751-9990
www.woodtechsystems.com
Striebig Optisaw, model Optisaw Automatic (Type # 5164) vertical panel saw station, with angled frame supporting material being cut: Max. cutting height (vertical) 5′-4″, max. cutting length (horizontal) 15′-1″, max. cutting thickness 2.36″. Both vertical and horizontal analog measuring scales on frame. Cutting head manually rotates from vertically to horizontally for rip vs. cross-cutting, adjustable spacers for repetitive cuts, 5.25 HP saw motor, 9.84″ diameter blade, guide bearings for travel , push button controls, e-stop button and dust extraction hose (no vacuum included). Overall footprint of station 19′-1″ wide x 4′7″ deep x 7′-10″ height. Sold for $36,000 new. 208 volt, 3 phase electrical required.
$14,490 FOB AZ Wood Tech Systems
765-751-9990
www.woodtechsystems.com
2000 Alpine AutoMill Component Saw 2000 Alpine AutoMill model 343H, (5) blade component saw, cuts lumber from 2×3 through 2×12, from 18″ to 20′, 4-angle floor webs from 18″. Includes powered length and angulation, digital readouts, (1) 32″, (3) 18″ & (1) 20″ blade, shaker under-saw scrap conveyor, incline, PC with Windows 98 o/s, and outfeed conveyor. Decommissioned in 2018. Stored indoors. 480 volt ,3 phase electrical required.
$10,497 FOB ON Wood Tech Systems
765-751-9990
www.woodtechsystems.com
Idaco Webmatic Saw
• Roof & Floor Web Saw
• Four 5 HP Saw Motors
• Cuts 2x4, 4x2 and 2x6 up to 16'
• Manual Angulation
• Waste Conveyor (under saw)
• Incline Waste Conveyor (adjacent to saw)
$8,500 FOB CO
Wasserman & Associates
800-382-0329
www.wasserman-associates.com
Hain 210' Powered Measuring System Adapts to Any Saw. Left or Right Hand Operation. Feet & Inches System (Stops at 12” Centers) or Inches System (Stops at 10” Centers). Motor: 1/4 HP Linear Actuator (110 Volt). Stop Rail: 2 x 4 x 1/4” Aluminum Extrusion. Stops: Jig Bored Steel. Stop Blocks: Machine Billet Aluminum. Optional Lengths from 5’ to 60’. Optional Gang Stop. Add $890 per 10’ Section of Heavy Duty Roller Conveyor with Stands
$8,990
Wasserman & Associates
800-382-0329
www.wasserman-associates.com
The truss industry relies on 3rd party quality assurance services to provide random visits to review the plants Quality Assurance program along with their operations. If your plant needs to comply with the IRC, IBC and to those who depend on solid, experienced QA expertise, we ask you to consider selecting Timber Products Inspection, Inc. (TP) as your choice for 3rd party inspections.
Proudly serving the forest products industry for over 50 years, TP brings the expertise you need to ensure your business is successful. As a responsible partner, TP delivers to clients, employees, and the industries we serve the confidence to drive value through the effective use of our diverse professional team.
TP would like to welcome the following authorized agents to our inspection team, each of whom have many years of experience in the truss industry! • Al Coffman
Jean Hart
Curt Holler
Chuck Ray
Glenn Traylor
Elliot Wilson
If you have questions about how you can make this selection, please contact your authorized agent above or Glenn Traylor at 919-280-5905 or trusguy@gmail.com. https://www.tpinspection.com/ https://www.tpinspection.com/auditing-services/truss
By Glenn Traylor
What do you think of when you hear the word “training”? A classroom with students listening to a teacher? A truss plant with a new hire following behind a seasoned truss builder? Or, maybe your first thought was sitting in front of a computer for an online course? The truth is that all of these forms of training serve a purpose, and we would do well to remember how important training is for a successful operation.
Some training is absolutely essential – onboarding should be included on that list. Onboarding training equips new employees with the knowledge they need to perform the jobs they were hired to do. Comprehensive onboarding training also may include a portion that measures new employees’ skills so that gaps can be identified. The end goal, of course, is to have well-trained workers, so that they are more effective and lead to better overall productivity for your business.
But what about “optional” training? Do you have a commitment to providing ongoing training for your employees? Some of the reasons why ongoing training can be critical to your business include these concerns:
• Regulatory compliance – As regulations are updated over time, it is important that your employees have a standardized way to learn what is needed to keep your company and its products in compliance.
• Equipment and/or software upgrades – Even if the latest upgrade seems obvious or expected, you should not ignore the need to ensure that your employees are aware of the changes and what they entail. Any change in the process or equipment should be accompanied by a training session. The length of the training depends on the complexity of the change, but the need to provide it remains the same.
• Productivity issues – Sometimes, the “problem” in your plant may be the engrained habits and SOPs that are inhibiting improved performance. To address the problems, you can provide training that focuses on making sure your workers are using the best methods and practices for their positions.
• Employee investment – Training is also a way to show that you are invested in your employees. By providing opportunities for your employees to learn and grow, you demonstrate your commitment to investing in their capabilities and their overall success with your company.
For many years, I have had the opportunity to work with several individuals from SAS, a world-renowned software company in Cary, NC. To demonstrate their commitment to employee development, SAS recommends that employees spend at least one week each year on training. Often that training will consist of classes, certifications or recertifications, extended reading, trade show programs, and other similar opportunities. All I have spoken to concerning SAS’s huge success agree that this ongoing commitment to training is an important component in their success.
Several truss plants in the US have great written training programs for their employees. Each program is designed to meet the needs of the position, and most will have each new hire closely guided by one or more people from their seasoned workforce. Many also have creative ideas for implementing their onboarding. For example, the “new guy” may be given a special colored vest to wear that reminds their coworkers that they’re new and may need assistance during the learning process. If done correctly, onboarding can help with teambuilding too.
Recently, SBCA has promoted training programs for folks who deal with Quality Control. I personally have been providing my clients onsite, hands-on training for their staff for many years. Often the training is extended to their shop supervisors, lead builders, cutting department managers, and even stackers. The classes are important because the information covered is essential for meeting ANSI/TPI-1 requirements. Unless the individuals involved in the process have had proper training, their knowledge level might be hit or miss. In-house training by Timber Products Inspection typically includes a four-hour program and has hands-on demonstrations and discussions that are extremely valuable for expanding the knowledge and understanding of your employees.
A recent training I conducted on ANSI/TPI-1 at Tindell’s Building Supply in Knoxville, TN not only increased their knowledge of the standard but also provided their team with specific recommendations on how to achieve positive results in their plant. General Manager Travis White commented, “our team found a lot of value …and look forward to continuing training.” Following a similar training for the Universal Forest Products Mid-Atlantic Division, Manager Jose Cuevas Lagunas commented on how immensely beneficial my training program was for their staff. After another recent training for Wilson Lumber in Madison, AL, President Josh Hendrickson said, “we are going to make this training an annual event “
These companies are all demonstrating their commitment to their employees by investing in training opportunities for them. The direct costs of the programs are far outweighed by the indirect benefits they’re receiving in enhanced productivity, efficiency, and quality. Are you investing enough in training in your company?
An ANSI/TPI 1 3rd Party Quality Assurance Authorized Agent covering the Southeastern United States, Glenn Traylor is an independent consultant with almost four decades of experience in the structural building components industry. Glenn serves as a trainer-evaluator-auditor covering sales, design, PM, QA, customer service, and production elements of the truss industry. He also provides project management specifically pertaining to structural building components, including on-site inspections and ANSI/TPI 1 compliance assessments. Glenn provides new plant and retrofit designs, equipment evaluations, ROI, capacity analysis, and CPM analysis.
Glenn Traylor
Structural Building Components Industry Consultant
http://www.linkedin.com/in/glenntraylor
Employee-owned
2004 MiTek Cyber A/T Component
2004 MiTek Cyber A/T Component Saw – Frame #398, Fully automated five-blade component saw, cutting performed by 2-16″ x 7 HP, 2-20″ x 7 HP, 1-32″ x 13 HP. Touch screen monitor w/Remote PC in enclosure. Belt scrap conveyor and gravity outfeed conveyor included. 240v, 3ph power / 90psi air required.
• Servo Controlled Linear Saw
• Touch Screen Computer
• Automated Infeed Deck
• Infeed/Outfeed Roller Table
• Ink Jet Printer (does not work)
• 230 Volt / 3 Phase
• Excludes: Outfeed Queue Rollers & Waste Conveyor
— Chase Barineau Vice-President Seminole Trusses, Inc.
•
• • Automated Setup via Download or Semi-Automated Setup via Touch Screen Input
• 23 Axes of Automation
• Sets up in 2 to 15 Seconds
• Five
• Waste Conveyor (under saw)
• Excludes Incline (adjacent to saw) and Live Deck (in
Safety Speed Manufacturing model 7000, vertical panel saw, 3 HP induction motor, 64 inch crosscut, 2 inch maximum thickness, accuracy within 1/64th of an inch, 10 foot welded steel frame with integrated stand and linear V-guides, enclosed counterweight system, adjustable vertical and horizontal rules. Quick changes from vertical to horizontal cutting. Includes machined aluminum material rollers, hold down bar, wheels, quick stop gauges and material hold downs. Dust collection ready. Options available include lower frame extensions, digital readouts, laser guide, stop bar, vacuum and midway fence. 208-230/460 volt, 3 phase electrical (208-230 single phase, 2 HP power optional +$100.00). $10,199 Base, FOB MN.
TStop
he Hain Systems Framer (HSF) will help you build square and accurate wall panels for residential or commercial construction applications. It will help you cut building costs by saving time and improving your quality. It’s a reliable, efficient and proven system that features a ruggedly simple design. The HSF is based on a proven design with over 20 years of actual production use and maintenance experience. It comes fully assembled and is designed for portable job site framing or in-plant permanent installation. The table has many optional attachments and will support Mylar Tape wall layout or any other type of layout. The optional gun rails can also be retro-fit to any table.
Stops:
Details:
Dimensions:
Ground and Polished Steel and Billet Aluminum
Table Construction: Thick-wall Structural Steel Tubing, Jig Welded for Accuracy
Length: 5 feet (60”) to 60 feet (720”)
Height: 12 inches
Air Supply: 90 psi (10 CFM Air Flow Recommended)
Depth: 12 inches
Electrical Supply: 120 VAC
Powder Coat: Industrial Gray
Dimensions: Height: 43”
Length: 16’ or 20’
Width: Adjustable 8’ to 10’ or 8’ to 12’
Shipping Weight: 3000 lbs
If you are looking for the fastest, most consistent way to measure and cut your product, then the Hain Measuring System (MEA) is your answer. The MEA changes from one length t any length instantly, up to 60’, without changing the operator’s position on the line. It is also highly accurate (+/- .010) and quickly moves from one length to the next in seconds. The MEA is designed for quick and easy setup and is simple to use. Even a first time user will be productive with little or no training required. It can adapt to any saw and can be mounted to any surface so that you can integrate the MEA with your existing setup. The MEA is versatile allowing “left” or “right” handed operation and measurement in “feet and inches” or “inches” depending on your preference. The MEA is also available in a “Skid Mounted” version.
Edmond Lim, P.Eng. LimTek Solutions Inc.
This winter season has been marked by severe weather conditions, including bitterly persistent cold and heavy snowfall. Thankfully, we’ve continued to install outdoor Lumber PickLines, which is a testament to the robustness and operational effectiveness of Enventek’s forklift lumber-picking replacement solution. Interestingly, there are only three Lumber PickLines completely under roof (along with lumber storage). These are large facilities. Of the more than forty outdoor PickLines, only five are under light Tee Sheds covering just the “lumber trough” and picker’s sidewalk on either side. Shown in the photo is a wider Tee Shed covering not just the “lumber trough” but also the bunks of picking lumber on either side.
The majority of our PickLines are fully exposed to the elements and so are the lumber pickers. Working in winter weather is a lot like hitting the slopes snowboarding and skiing or enjoying the outdoors snowmobiling or ice fishing. To enjoy winter sports, you need the right gear, mindset, and preparation to stay warm, safe, and comfortable. Providing High-Viz insulated winter gear for your lumber pickers including winter boots, gloves, and hats will ensure that everyone can stay comfortable, protected, and productive in freezing conditions. The cost of providing winter work gear (and cleaning) is way more cost effective than a new building addition!
Shown next is an overview of an outdoor 300 ft long Triple Lumber PickLine that’s just been upgraded from a Double PickLine with the addition of a RetroC saw fed from 60 ft live decks. To cover this PickLine and the nearby dense lumber storage would require a 100,000 sqft building addition, excluding the rail spur. This is already a huge 150,000 sqft component plant producing roof trusses, floor trusses, wall panels, and laminated columns, so they needed to upgrade without changing the size of the building.
Truss setup is now faster than ever with lumber spread out and organized for this 60 ft truss! All thanks to our warm lumber picker, keeping the RetroC fed with the SpeedCatch Cart System.
We can’t avoid winter – if we live in a seasonal climate, experiencing winter every year is guaranteed. What we can do is prepare for the elements to ensure that our production doesn’t suffer and neither do our employees!
When you’re ready to Feed Your Beast and see these efficient and effective systems for yourself, let us know! Inside and out, LimTek Process Organization Technology will help you squeeze out more truss production and deliver quality trusses with shorter lead times to better service your customers by organizing your truss fabrication processes to maximize your investment in automation. https:// limteksolutions.com/#solutions
To see meaningful labor savings, quality improvement and production gains, SL Lasers with their easy-to-see green light are nothing short of illuminating. They enhance worker accuracy and productivity, regardless of experience or primary language. They can reduce tedious setup time by up to 70%. No complex training or costly service agreements are required. And SL Lasers integrate seamlessly with any component design software and are quickly installed over existing equipment. We’ve been trailblazers in wood component laser projection since its very beginning, and we’re still delivering more rapid ROI for roof truss, wall and floor panel producers every day. Contact our enlightening team at Wood Tech Systems to see how SL Laser can deliver for you.
productivity of any
SAWS
2021 Powermatic Model 511 Panel Saw 2021 Powermatic model 511 panel saw. Vertical panel saw features a powerful 3HP worm-drive motor which rotates in the carriage, adding the versatility to perform rip cuts. The solid aluminum rollers assure smooth feeding of stock and perfect 90° cuts every time. This saw will handle panels up to 5-ft tall in unlimited length. Includes horizontal and vertical scales and casters for mobility, the counterweight system keeps the saw carriage in the desired position when loading or unloading panels. Features dual 4″ dust collection ports with nylon brush surrounding the blade for superior dust collection from the front and the rear side of the panel. 115v, 1-phase electrical required.
$6,799 NOW $1,999 FOB AZ
Wood Tech Systems
765-751-9990
www.woodtechsystems.com
2023 Northfield Model 410 Upcut Saw NEW 2023 Northfield model 410 upcut saw available for immediate shipment. 90/90 degree cuts to 4″ x 10″ capacity (fence forward position) to 2″ x 14″ (fence rearward position). Saw is configured for material from left to right, with 3″ x 6″ air operated cylinder, filter, regulator, lubricator, 10 HP motor, enclosed steel base with cast iron table, magnetic starter and adjustable operating speed from 20 to 60 CPM. Includes optional two-palm controls, additional 4″ dust outlet, NEMA 12 electrics with fused disconnect and two 18″ diameter 60 tooth blades with 1″ diameter bore. 460 volt, 3 phase electrical required.
$18,630 FOB MN Wood Tech Systems 765-751-9990
www.woodtechsystems.com
Whirlwind Model 1000 Cut-Off Saw
• 5 HP Motor with 14" Blade
• 2 3/16" x 8 1/4" Capacity
• Pneumatic Blade Guard/Lumber Clamp
• Foot Pedal Control
• Dust Collection Outlet
• 460 Volt / 3 Phase
• 1 Left Hand & 1 Right Hand Model
Available
$3,500 NOW $2,800 Each FOB NC Wasserman & Associates 800-382-0329
www.wasserman-associates.com
1982 SpeedCut MetraCut
Centerline Saw
26’, 32’ & 36’ sizes available, Split Rollers available too! 2 YEAR WARRANTY
ALL TRAILERS NOW AVAILABLE WITH OPTIONAL GALVANIZED ROLLERS
Scan the QR Code to take you directly to our website. For more information or to request a quote Call or Email: 1-800-237-5161 sales@precisionequipmfg.com
1982 Speed Cut Metra Cut, model SSA-11, centerline saw, 16″ blade, maximum cutting depth of 6″, maximum cut length of 31″, 164 deg. cutting range and 5 HP motor. Includes push-button on/off controls and analog angle measure on turntable with air stop, 20′ long infeed conveyor with OEM SpeedMeasure, 20′ long outfeed conveyor and one (1) spare blade. 208 volt, 3 phase electrical required (can be converted to 240v/440v).
$6,990 FOB WY Wood Tech Systems 765-751-9990
www.woodtechsystems.com
New Monet DeRobo Linear Saw
New, DeRobo linear saw by Monet organizes "fill" boards to increase optimization of each board, can produce unlimited scarf cuts, cuts 1 or 2 boards at a time and cuts webs, chords, wedges, rafters and open-stair stringers. Works with all major connector plate manufacturer's software. Features include 22 inch blade, left-to-right feed direction standard, lumber push and pull grippers for more accuracy, ink marking on the 1 1/2" face of the incoming boards and small piece capture and delivery to the front of the saw for easy access. Infeed deck and bunk feed are shown as options only. 480 volt, 3phase.
$239,000, FOB MO.
Reliable automated machinery, built to last for generations!
“The equipment is extremely durable to stand up to the beating it takes in a truss plant”.
$330,000
Location: MO
New, Monet DeSawyer 2000, computerized, five-bladed component saw, sets up in 15 to 17 seconds, can run in manual mode, downloads projects from a network or manually using display screen controls. Features all powered movements, cuts from 15" 90/90 cuts to 20 foot length, 2 x 3" to 2 x 12" lumber depths and internal brakes are standard. Options include enhanced servo controls featuring autocalibration, catcher's display and either shaker or belt scrap conveyor and incline. 440 volt, 3 phase electrical.
Gain the advantage with truss design services from Simpson Strong-Tie. When you partner with us, we dedicate a regional team that knows the standards and practices in your area. Experienced project managers and designers take the time to learn, document and customize every job to your unique specifications. It’s easy to get started, because we assist in bringing current designs into our Component Solutions ® software that streamlines workflows. You also get IFC and 3D model files for seamless integration and review by local trades. Along with innovative hardware and cutting equipment, our truss design services are a smart way to build more business. Learn more at go.strongtie.com/cs or contact your sales representative.
By the Triad | Merrick Machine Company Team
s Triad celebrates 65 years in this great industry, we’re finalizing the plans for our 16th Annual Trade Show! The event is being held on April 9–10 at Merrick Machine Company in Alda, Nebraska.
Our product showcase will feature our latest machines, including the PreStage Framing Table, ProFusion Bridge, AI Component Nailer, VersaSteel Table, the all new Open Stringer Saw, and more. Several vendors also will be on site during the show to answer your questions.
What’s more, we’ll have educational sessions led by industry experts:
• New equipment maintenance service seminar
• Round table discussions focusing on
• Wood wall panel builders
• Steel wall panel builders
• Pro stair builders
These discussions will allow you to meet and talk face-toface with peers away from the show floor, for a more personalized experience.
For additional fun and networking, there will be an 18-hole golf scramble on April 8 at the Indianhead Golf Course. Then on April 9, we’ll have our annual awards presentation where we recognize the winners of our Life-Time Achievement Award and our Productivity and Efficiency Awards.
Involving four generations of the Merrick Family, we understand that we succeed by helping YOU to succeed. Founded in 1959, Merrick Machine Co has more than six continuous decades of helping our customers grow their own businesses. This event is by invitation only and you must RSVP to attend, so be sure to let us know if you would like to join us in April! www.triadmachines.com
Safety Speed Manufacturing, model 7400 XL*, vertical panel saw, 3 HP induction motor, 64 inch crosscut, 2 1/8" maximum thickness, accuracy within 0.005 inches, 13 foot long welded steel frame with integrated stand and linear V-guides, enclosed counterweight system, adjustable vertical and horizontal rules. Quick changes from vertical to horizontal cutting. Includes machined aluminum material rollers, hold down bar, wheels, quick stop gauges and material hold downs. Dust collection ready. Options available include digital readouts for vertical cuts, automated length measuring, laser guide, stop bar, vacuum and midway fence. 208-230/460 volt, 3 phase electrical (208-230 single phase, 2 HP power optional +$100.00).
2006 Alpine Speed Rafter Cutter
• Simplified compound cutting for hip, valley and jack rafters (double & single compound cuts)
• Two Worm-Drive Circular Saws (110 Volt / 30 Amps)
• Saw Turntable (for angle cutting)
• Saw Carriage (for up to 45 degree bevel cutting)
• Infeed & Outfeed Roller Conveyor with Stands
$4,900 NOW $4,250 FOB CA Wasserman & Associates 800-382-0329 www.wasserman-associates.com
Used - Metra Cut Radial Arm Saw (2x) Parts Machine
$500 – Make Offer
Eide Machinery Sales, Inc. 612-521-9193 www.eidemachinery.com
Used - 2005 Model 305 Infeed Conveyor Designed for use with all component saws. To include: Soft Start ~ Soft Stop Inverter System. Programmable load sensing; Overload / Jamb sensing shut down feature. Gear motor providing conveyor speed of 36' per minute. Forward and reversing controls for location at both ends of conveyor unit. Material capacity range - 4' through 24' lumber. Chain deck pedestals 20' long with cross bracing. Staging area at the saw independent of the live deck system. 30,000lb. Deck capacity. Call for pricing
Eide Machinery Sales, Inc. 612-521-9193
www.eidemachinery.com
New Monet FWA 500 Floor Web Saw
New, Monet five-head, floor truss web saw, cuts 4-angle, 4×2 floor truss webs from 13 inches and 90-90 blocks from 7 inches, to 4 foot long maximum length. Features 10-board magazine feed, powered, fixed-quadrant angulation, manual carriage standard, scrap conveyor and cut-off blade. Options available for longer carriage length, incline scrap conveyor, and choice of shaker or belt scrap conveyor. 440 volt, 3 phase, 60 Amp electrical. 50 PSI air at 5 CFM required.
$75,000 FOB MO Wood Tech Systems 765-751-9990 www.woodtechsystems.com
1995 SpeedCut Timbermill 620 Component Saw
1995 SpeedCut Timbermill component saw, model MH6G-20, six blades cut lumber from 2″ x 4″ through 2″ x 10″, 4″ x 2″ lengths from 5 feet to 20 feet, including four-angle floor webs from 5-feet. All powered movements. Saw includes (2) 30″, (2) 22″ and (3) 14″ blades, analog scales, chain-drag scrap conveyor with matching OEM long scrap incline. Scrap conveyor drive, brakes and wiring harness need replacement. 220 volt, 3 phase electrical required.
$7,993 FOB IN Wood Tech Systems 765-751-9990 www.woodtechsystems.com
New SpeedWorx Automated Sheathing Station by Safety Speed Manufacturing- Reduce labor and operator fatigue by taking advantage of the SpeedWorx automated vertical panel saw. This one-person station cuts wood sheathing sheets up to 50-inches x 10-feet, and up to 2-inch thickness, using a fast 1-button cutting setup with CNC accuracy to 1/32 of an inch (0.03125″). The photos of raw materials illustrate the drastic reduction of scrap material thanks to implementing the Rogworx saw station.
Visual user interface makes choosing the job and sheet cutting order easy to determine. Files are downloadable allowing for minimum waste. Saw station reads WBX file format (Alpine) or EHX file format (MiTek) or CSV files with manipulation.
Automated sequencing of sheets provides optimum usage of each sheet. The cutting chamber changes from ri to cross-cutting automatically. All this in a very small machine footprint, so it can fit easily into your existing building.
Visual user interface with standard ‘Auto Fill’ feature makes choosing the job and sheet cutting order easy to determine. System offers full optimization and sequence panel parts looking ahead through the job based on your specification. The cutting chamber changes from rip to cross-cutting automatically. All this in a 100 square foot footprint, approximately 25′ long x 4′ deep, so it can fit within existing facilities.
Includes advanced dust collection. Integrated Printing for labeling parts is available as an option. 208-230V volts, 3-Phase, 25 Amp electrical required, 5 CFM at 100 PSI air required.
By Steve Shrader, Business Development / Operations Hundegger USA
This is set to be a groundbreaking year for Hundegger as we continue to lead the charge in automation and smart manufacturing solutions. With innovation accelerating across the wood processing industry, Hundegger remains at the forefront—delivering intelligent, high-precision systems that redefine efficiency, accuracy, and productivity for manufacturers worldwide.
To support this momentum, we recently welcomed two key additions to our sales and technical team: Carlos Lozano and Brandon Schmidt. Their expertise strengthens our ability to support customers navigating the shift toward automated solutions.
Carlos, based in the Dallas-Fort Worth area, joins us as Sales Manager with over 19 years at Alpine and additional experience at House of Design. His deep knowledge of strategic planning and plant layouts makes him a perfect fit for Hundegger as we help companies optimize their operations. Brandon, our new Technical Sales Manager, brings 15 years of experience in robotics and automation, including 6.5 years at House of Design. His expertise ensures that our customers receive cutting-edge solutions tailored to their production needs.
Hundegger’s commitment to innovation is not confined to the U.S.—it’s a global movement. In late January, Carlos and Brandon joined me on an eye-opening trip to Hans Hundegger AG’s headquarters in Hawangen, Germany. Every time we step into the Hundegger factory, we are struck with an overwhelming sense of motivation and excitement. Seeing firsthand the latest advancements in precision engineering and automation is an electrifying experience that fuels our passion for bringing these cutting-edge solutions to our customers. We leave each visit more energized than ever, ready to share the latest innovations and demonstrate how they can revolutionize production environments.
Automation is no longer a luxury—it’s a necessity. Companies are facing increasing demands for higher output, lower waste, and more precise production, and Hundegger is answering that call. With our Cambium software, smart sorting, and fully integrated CNC processing, manufacturers can now streamline their workflow like never before. Our TD-II, Robot Drive, and PBA series continue to push the boundaries of what’s possible in mass timber, truss, and panelized construction.
Hundegger is poised to make 2025 the year where automation moves from concept to reality for many businesses still operating in traditional production environments. The future belongs to those who embrace intelligent manufacturing, and we’re excited to lead the way.
With new talent, new technology, and a renewed vision, Hundegger is more prepared than ever to help customers modernize, optimize, and thrive in an era of intelligent automation. We’ve even increased our spare parts warehouse along with our service department, so we’re ready to roll. The excitement we bring back from our visits to the Hundegger factory is contagious, and we can’t wait to share that energy with our customers. Stay tuned—exciting things are ahead!
For more information on how Hundegger can transform your production line, visit www. hundeggerusa.com.
The industry’s most powerful integrated component design, engineering, and management software for steel and wood-framed structures.
iCommand
Manage projects, customers, materials, pricing & inventory
iModel
Design truss layout & profiles
iDesign
Optimize material usage & engineer trusses
iPanel
Design wall layouts, panelize, bundle, break & stack
eShop
Maximize crew productivity & improve manufacturing efficiency
The IntelliVIEW Suite is a fully integrated software solution for the layout and design of a building’s rough framing elements—including roof and floor trusses, wall panels, solid sawn, EWP, sheathing and various ancillaries.
The IntelliVIEW Suite provides the industry’s most complete analysis of the design, cost information and bill of materials—promoting increased profits by reducing plate and lumber use.
Ask those who know. They’ll tell you about the people at Alpine who make a difference.
Used Hain Quick Rafter Cutter
• Reconditioned in December 2020
• Board Sizes: 2x4 and 2x6
• Motors: Two 1 HP / 220 Volt or 440 Volt / 3 Phase
• Saw Blades: 7 1/4" Carbide Tipped (set at 45 degrees)
• Angle Adjustment: Manual Rotation with Air Brake
• Air Supply: 90 PSI
• Carriage: Steel Rails with Steel Dual V Rollers
• Pedestal: 3/16" Formed Steel
• Saw Housing: 1/2" Billet Aluminum
• Covers: 10 Gauge (1/8" thick) Steel
• Fully Enclosed for Safety
$12,500 NOW $9,900 FOB AZ Wasserman & Associates 800-382-0329 www.wasserman-associates.com
Clary 329-2 4-Blade Component Saw
Clary Web Saw, model 329-2, cuts from minimum 18-inch long to 11-ft long, fourangle floor webs, and minimum 11-inch blocks at 90/90. Manually adjusted length and angles. Includes (4) 14″ diameter blades, incline, manual, any available spare blades, and chain-driven under-saw scrap conveyor. 230 volt, 3 phase electrical required.
$7,995 FOB AR Wood Tech Systems 765-751-9990 www.woodtechsystems.com
In answer to the demands of high-volume customers comes the Monet DeSauw FWA 500 CA (Automated Controls) floor web saw. The 500 CA is perfect for component manufacturers who routinely run floor trusses in high volumes with variable web geometry. Another primary feature is enhanced safety through automation which eliminates the need to open the saw motor cabinets other than for periodic service. The 500 CA includes automation for all blades, including the fixed cut-off blade for minimal waste. Lumber infeed speed is variable up to sixty (60) boards per minute, while the powered carriage utilizes rack and pinion drive with airlock for set accuracy throughout the production run. Your operator will easily download batches to the 500 CA saw from your design software via an ethernet connection to a MS Windows 10 industrial PC with a 17″ monitor housed in a stand-alone console. If you frequently batch floor web cutting, and if enhanced safety with increased productivity are a concern, then an automated Monet FWA 500 CA may be the right selection for you. More information Here
Price based on configuration.
That'sallthetimeittakes todrillstudsforrunningRomexorotherelectricalwireinthewallpanels
Motor: HeavyDuty5HP-3phase-220vor440v(Pleasespecifywhenordering)
MotorcarriagebearingandspindleassemblymountedonBlanchardgroundsteelplate
LinealmotionishardenedandgroundVbearingsandrails
BlockSizes: 2x4through2x12infiniteheightsettingtocenter
AirSupply: 100psi10CFM
Drills: 2wing3/4'”CarbideTippedcanaccommodatesmallerorlarger
Spindles: AlloySteelpolishedandgroundprecisionshafting
Frame: 2"SteelWithPowderCoatFinish
Covers: 10Gauge(1/8"Thick)Aluminumremovable
Dimensions: Height-60inches,Width-33inches,Depth-33inches
Shippingweight: 750lbs.-(Includingcrate)
MADEINAMERICABYAMERICANS
lnnovationen fur den Holzbau
HUNDEGGER
Hundegger leads the way in automation innovation for the truss component industry. Our advanced CAMBIUM software offers cutting-edge automation and digitalization solutions, revolutionizing operations, boosting productivity, and driving sustainable growth for manufacturers like you.
We go beyond standard mechanization; we champion true Automation. The Hundegger TD-II isn't just a saw-it's a transformative, comprehensive solution designed to streamline your production process. From retrieving lumber to optimizing, nesting, stacking, destacking, sorting, buffering, and precise delivery, our system ensures peak efficiency and productivity, tailored specifically to truss component manufacturing.
Harness the power of data with Hundegger's advanced CAMBIUM TACTICAL software. It meticulously tracks and optimizes your production, ensuring more automated operations and significant productivity gains.
We provide state-of-the-art automation and control solutions that set the industry standard. Our focus on industrial automation and robotics positions Hundegger as the leader in enhancing performance and efficiency in truss component manufacturing and beyond.
Hundegger products are essential for future-proofing your business. Elevate your productivity and secure your competitive edge with our advanced technologies and automation solutions, meticulously designed to meet the unique demands of component manufacturers today and tomorrow.
Don't get left behind. Invest in the future with true automation from Hundegger and see your business thrive.
Monet DeSauw model Desawyer ESC enhanced servo-controlled ( ESC) component saw with touch screen user interface with backup mechanical controls. Includes three operating modes: Auto (download setups from LAN or USB), Semi-auto (touch screen setup entry), and Manual (backup push-button switches for powering all movements). Includes over-travel protection, comprehensive setup screens, auto sequencing, auto-calibration and pneumatic brakes on all five () blades. One (1) 30” blade and four (4) 16” blades. Manual cut limits are 18” min., 11” min. square edge blocks, 20’ max cut. Belt under-saw waste conveyor. Voltage: 480 volt/3 phase/60 Amp. Air: 50 PSI at 5 CFM. One-year warranty included. Can be paired with a model PD-6 lumber feed system at an additional cost. Heavy duty 80 RIV chain feed system. 16’ wide x 20’ long x 36” deck height. Transfers 3’ to 20’ lumber. Includes auto-feed control, foot pedal override, forward & reverse, variable speed control with HD double-bearing construction. Other additional-cost options include, inkjet marking, label printing, backside screen display, spare blades and incline scrap conveyor.
$369,900 FOB MO
By Ed Serrano Managing Director VektaUSA
Pssst...do you want to know a secret? Not all printers (and their ink) are created equal.
If you are struggling with inaccurate or incomplete printing on your production line, you’re missing out on a crucial efficiency boost. The Vekta P3 printer is THE industry-shaking, custom-built print system designed to elevate your frame and truss production and take your business to the next level.
The Vekta P3 Printer, engineered specifically for the demands of frame and truss manufacturing, boasts the capability to print ANY image onto lumber with unparalleled precision and clarity. This versatility allows for maximum flexibility and customization within your production process.
Initially designed for wall panel fabrication (stud locations/lengths, opening sizes, panel junction marks, etc.), the P3 Printer’s capabilities have expanded significantly. Now, we can print a wide range of information directly onto truss components. This eliminates the need for cumbersome paperwork, laser projectors, or large screens, streamlining the workflow and minimizing errors.
Vekta is a licensed OEM partner with HP Inc (Hewlett-Packard). This relationship – based on innovation – has allowed us to design and manufacture the P3 to hold pace with our speedy top-of-the-line Razer saws. The P3 Printer opens a whole new world of possibilities for Vekta customers. Its modular design allows the range of printable information to be easily expanded over time to meet our customer’s changing needs. Vekta regularly adds more options as to what can be printed in real time and with precise accuracy on the lumber – a key factor in why our competitors haven’t been able to catch up.
The printer incorporates 16 individual, disposable print heads and prints onto two faces of the lumber. It automatically adjusts for different thickness material and self-checks to ensure the printer is in the correct position to avoid bottlenecks. Existing Razer systems can be easily upgraded to include a P3 Printer.
Now it’s time to think about ink as those previously mentioned cartridges can be a big deal. Those click-in cartridges as well as other low-cost consumables and parts make the P3 significantly cheaper and easier to reload, clean, and maintain compared to other systems.
You know the saying: “You get what you pay for.” This rings especially true when it comes to printing technology for your frame and truss plant. You may think third-party or remanufactured ink cartridges in your saw could be a good idea to save you money, but using these unreliable cartridges risks damaging your printer and creating unnecessary downtime for your production line.
Buying cartridges directly through the manufacturer ensures you have brand new, official HP cartridges that are consistently available, correctly stored and batch-tracked for your peace of mind.
Frame and truss plants that establish a regularly recurring ink cartridge order ensure they never run out of ink again and take advantage of bundled shipping rates with any additional spare parts orders they may need throughout the year.
Vekta remains committed to delivering cutting-edge automation solutions that empower our customers and drive industry-wide success in the new year, so we’re offering BIG savings on ink cartridges when buying in bulk, direct from the source. Order in volumes of over 50 or 100 to receive tiered price reductions or as we say, an “inkredible ink-centive.” Please contact support@ vektausa.com today to learn more.
A complete wood processing system proven to profitably feed cut lumber to truss plants of all sizes.
Easy to use, simple robust automation that is scalable with less labor. A RetroC holds calibration.
Auto-Feeding, no upper hold-downs (just 15 automation axes) with electronic braking. Efficient material handling that will significantly increase cut piece production with reduced operating costs and improve truss build times with consistently accurate cut pieces.
Catching labor is eliminated with our optional SpeedCatch cart system. Sophisticated SpeedCatch software enhances the efficiency of truss production by effectively collating and organizing the lumber at the truss tables. SpeedCatch upgrades the RetroC to a comprehensive one-person (sawyer) wood processing system.
Alpine AutoMill HP, model 349C component saw. Servo controlled computerized saw sets up in 2 to 19 seconds and downloads from a network, or by using a touch screen for ease of operation. Five-head automated component saw works in both automated (downloading files), semi-automated control (via touch-screen input) or manual mode. It has (23) axes of automated movement, enhanced diagnostics, and auto management reporting.
The HP cuts from 2′-6″ to 20′-0″ long material in size range from 2×3″ through 2×12″, and 4-angle floor webs from 2′-0″. Includes [3] 18″, [1] 20″ and [1] 30″ blades with air brakes, Windows 7 o/s and under-saw scrap conveyor. The Windows 7 o/s can be upgraded to a version of Windows 10 that will be supported until 2032, at an additional expense.
Also includes over $8,000 in spare parts. 480 volt, 3 phase, 100 Amp electrical required. 90 PSI @ 69 SCFM air required.
$129,997 - FOB OR
• 3 3/8" Maximum Thickness
• 13 1/2" Maximum Distance from Rip Fence to Outer Saw
• 100 HP Arbor Motor
• 2 HP Feed Motor
• 7 1/2 HP Dust Collector
• 480 Volt / 3 Phase
• Waste Conveyor with Short Incline
$35,000 NOW $21,900 FOB MN Wasserman & Associates 800-382-0329
www.wasserman-associates.com
STRAIGHT LINE RIP SAW
• 10 HP Arbor Motor
• 3 HP Variable Speed Feed
$10,500 FOB MI Wasserman & Associates 800-382-0329 www.wasserman-associates.com DANCO GANG-RIP SAW
• 4" Maximum Thickness (when using 18" Blade)
• 48" Throat
• Adjustable Rip Fence
• Overhead Holddown
• Automatic Chain Oiler
• Dust Outlets
Baumeister Lumber Splicer
• Vertical Hydraulic Press with 3"x 12" Platen Size
• 2x3 and 2x4 Lumber Material (3" x 10" maximum plate size)
• Magnetic Platens to hold plates in the correct position
• Working Pressure: 1600 PSI
• Dual press cycle activation for safety
• 208, 240 or 480 Volt / 3 Phase (10 HP)
• Video available upon request
• Excludes: Infeed/Outfeed Roller Conveyor
• Optional 2x6 Capacity (up to 16" long plate) Splicer is available
$29,500 FOB PA Wasserman & Associates 800-382-0329
www.wasserman-associates.com
40′ Tee-Lok Floor Truss Gantry (Video available here.)
40′ Tee-Lok floor truss gantry features gantry head with new 18″ diameter rollers with 3/4″ wall with removable shaft. Gantry head has a 7.5 HP motor with VFD. Table features fire hose clamping and pin ejectors (never used by seller). Build floor trusses from 12″ to 32″ deep. Includes all available spare parts. 230/460v, 3 phase power.
$49,890 FOB SC Wood Tech Systems
765-751-9990 www.woodtechsystems.com
New Monet 5-head, floor truss web saw, cuts 4-angle, 4×2 floor truss webs from 13 inches and 90-90 blocks from 7 inches, to 4 foot long maximum length. Features 10-board magazine feed, powered, fixedquadrant angulation, manual carriage standard, scrap conveyor and cut-off blade. Options available for longer carriage length, incline scrap conveyor, and choice of shaker or belt scrap conveyor. 440 volt, 3 phase, 60 Amp electrical. 50 PSI air at 5 CFM required.
765-751-9990
$77,000 FOB MO
www.woodtechsystems.com
• 10 Each - Standard 20 Ton Track Mounted Heads with 10" x 10" Platens (refurbished in 2011)
• 6 Each - 2011 Double 40 Ton Track Mounted Heads with 10" x 15" Platens
• 2 Each - 2021 Double 40 Ton Track Mounted Heads with 10" x 15" Platens
• 2 Each - 10 HP Two Stage Hydraulic Systems with Controls (230 Volt / 3 Phase)
• Track System for 55' Scissor & Flat Bottom Trusses
• 1 Each - Peak Head Track (perpendicular to base line)
• 2 Each - Movable Bottom Chord Tracks (to adjust for pitch)
• 8 Each - Floating Tracks for Top Chord Head
• Clamping Package: Peak, End Stop, Camber Stops & Air Clamps
• Air & Hydraulic Manifolds with Quick Connectors for Heads
• Pn eumatic Pop-Up Skatewheel Ejectors (for truss removal)
• 56' Powered Transfer Roller with Stands
• 26 Each - 14' Powered & Idle Exiting Rollers with Stands
$89,900 FOB AR
Darrin Schramm
Off-Site Construction Regional Manager
Any given fall Sunday, we get to watch our favorite football team and, if we understand the sport, we can see what they do well and where they are lacking. Each game is full of statistics, and the statistics tell us where our team ranks in relation to previous games, other teams, past years, and so on. During the week between games, we talk about how great their passing game has been or how little protection the QB has, so they are always on the run and never get in their offense. With all of the readily available statistics, we can see the strengths of our team as well as where they may have holes in their production and execution.
Most component manufacturers typically don’t have access to the same amount of information or statistics as sports teams do, or even know what is available to them to improve. In some of the facilities that I have visited, they can’t tell me for sure if they are even winning or not. They generally have an idea if they are meeting production needs, but they don’t know if they would be ready to meet demands for increased production. Issues may be easy to see from the outside looking in, but not always evident to those in the day-to-day operations. Solutions are not always evident, either.
The five reasons your wall panel production may not be winning:
5. Lack of consistent and trained labor.
Are you losing time each week because the right person wasn’t there? How much time is spent re-training because you have new hires with little to no experience? Is it difficult to plan production because you don’t know who will be there to produce?
It may be time to automate some functions in the line to minimize necessary labor and increase employee quality of life. With the right machinery, you could minimize the impact of workforce inconsistency and work more efficiently—with increased production and higher-quality finished products.
4. Not utilizing your design software to get the most production out of your line.
Are you able to maximize the capabilities of the design software that you pay for?
MiTek is probably the most popular design software for producing wall panels, but I cannot tell you how many times that I have asked a MiTek shop if they utilize the multi-wall function in their software only to get blank stares back at me. If you are unaware of what I am referring to, reach out to your MiTek rep.
WEINMANN machinery works extremely well utilizing the multi-wall feature. The goal is to keep the tables full and have the machines running continually. The multi-wall function helps maximize table usage so the machines can run more while starting over and re-calibrating less.
It may be time to also look at an MES software. MES stands for Manufacturing Execution System. It is a comprehensive, dynamic software system that monitors, tracks, documents, and controls the process of manufacturing goods, from raw materials to finished products. It will help you optimize your wall line. A great example of an easy-to-use MES is granIT Basic. Your existing design software provider may have an MES feature, as well.
For more on MES, I recommend reading our article in last month’s issue, “A Case for Manufacturing Execution Software (MES)” by my colleague, Dario Schmidt.
3. Processes or steps that are not adding value.
One way to gauge the effectiveness of your processes is to take note of how often people are moving without adding any value to the process. Examples include:
• Steps to get more studs. Are saws located close enough to the line?
• Steps to remove waste from cutouts of OSB that could have been minimized with the right panel saw.
• Steps to carry tools from one process to another. Again, can we automate the process?
• Two people required to lift heavy sheets of OSB that could be done by one person and a vacuum lift.
• Many people required to accomplish one step (manually framing walls, for example).
Making small adjustments to how things are done can greatly impact your efficiency and productivity over time.
2. Issues that affect your production (linear feet per shift).
The metric that we use to measure line production is linear feet per shift. Do you know your numbers and what factors affect them? A few things to consider:
• Interior versus exterior walls: We split out interior wall linear feet numbers from exterior wall numbers because interior walls do not require sheathing.
• Optimizing and precutting OSB prior to the line versus using full sheets.
• Manual framing versus using a frame station like the FRAMETEQ.
• Manually cutting top and bottom plate boards versus accomplishing this on the FRAMETEQ.
• Amount of blocking: Are you doing it in line or on site? Is it called for by engineering or for cabinets and towel bars? A lot of blocking means a drop in production—can you do less?
• The complexity of each wall design.
• Number of openings (windows and doors).
• Slow process for applying sheathing to the walls.
• How well you are utilizing multi-wall function in the software: Are you maximizing your line by maximizing your walls?
• How specialty walls you only do occasionally can bog down the line (raked walls, for instance).
• How many layers of sheathing are being done.
• Fastening process: Nailing versus staples versus screws.
• Sawing rough openings versus routing them.
All of these factors play into your production rates and need to be examined if you want to level up your production.
1. Your business has outgrown your machinery.
This is a big one for many businesses. For example, maybe you started out building wall panels by hand and then added a simple nailing bridge, but you are still manually framing walls. No matter what stage of growth or automation you are in, there are opportunities to be more efficient and productive. One or more of the following common questions may be ones you could be asking today.
“Can I take out my existing inefficient bridge and replace it with a WEINMANN multifunction bridge?” The answer is yes.
Replace your existing bridge with a WEINMANN WALLTEQ multi-function CNC bridge that fastens and cuts openings on the same unit. Incorporate the stud straightener with one of our tables and you can virtually eliminate shiners as well. Plus, nail depth and spacing, which are hot topics when dealing with ZIP sheathing, will no longer be issues as they can be set on the WALLTEQ and be executed with accuracy and precision every time.
“Can I add the FRAMETEQ and WALLTEQ and still utilize some of my existing tables?” Again, the answer is yes.
Add automated framing to your line with a FRAMETEQ framing station. The FRAMETEQ can be equipped with saws to cut your top and bottom plate boards to length without you doing anything. A properly equipped FRAMETEQ is a great addition to optimizing your line, and we can place a WALLTEQ over an existing table as long as that table can clamp the wall and hold it square.
“I don’t have a lot of room for new machinery. Will it fit?” Let’s look at the room and machines you are currently using. Sometimes one of our machines makes two of your existing machines unnecessary, allowing for more room. For example, if you currently nail your OSB on one table with a nailing bridge then move the wall to the next table/bridge to rout openings, we can save space by having both fastening and cutting openings happening on a single bridge.
“My process is all manual and reliant upon too much labor. Is it too much of a jump to go to an automated line?” Not at all—we will help you walk before you run.
Build in Phases: For example, start with one line that can do both interior and exterior walls. As production demands increase, you can add a dedicated interior line.
Proper Training: Stiles Machinery offers Stiles University, a fully accredited training program with both online and on-site training. When purchasing machinery from Stiles, you will receive training at three stages:
• Pre-Installation: Online through Stiles University for general introduction prior to install.
• During Installation: Hands-on training with the WEINMANN install team at your facility.
• Post-Installation: On-site at a Stiles University location with an instructor for machinespecific training and maintenance/operation. Then, typically 2–3 months later, WEINMANN will send a trainer from Germany for 1–3 weeks to help with system optimization and work through the full use of your new machine in your environment.
“We are experienced with our machinery, but what should we do if the machines are outdated and insufficient for our sales and production goals?” Let’s look at your whole process and where you want to be by answering this question with some more questions:
• Are you planning a new facility or have an existing facility for new machinery? Do you have a CAD layout of the facility?
• Do you know what linear feet you need to produce today and where you want to be?
• Are there other areas of construction that you would like to get into, like floor cassettes or window installation?
• Do you need to process I-joists? A BEAMTEQ saw is the perfect solution for EWP processing.
• Is it time to bring in a consultant to help with decisions and processes for a new facility?
• Are you interested in robotic solutions?
By addressing even one of these critical factors, you can elevate your wall panel production to new heights and position your business for success in today’s competitive market. Stiles Machinery and WEINMANN can help with all of these questions and concerns. We welcome the chance to sit down and discuss which solutions are best to make your production line a winner. You can contact us at (616) 698-7500 or visit StilesMachinery.com/OSC to learn more.
Framing by hand costs time, manpower, and money. Boost your production potential and component quality by adding our automated WEINMANN FRAMETEQ framing station to your line.
• Free up your workforce by going from multiple framers to one operator
• Achieve unparalleled accuracy and squareness with NC-controlled precision
• Streamline framing and quality control with stud positioning, automatic width adjustment, and software-driven, one-click execution
Build on better with
Stiles has been a trusted name in US manufacturing for over 60 years and is the exclusive North American provider of WEINMANN, the world’s leading manufacturer of off-site construction machinery.
Contact us today to discover automated solutions that take your business to the next level.
Enhance your truss production with our advanced retrofit options, each equipped with the industry-leading WizardPDS® automation. Whether you need full automation on your entire line or just a 48’ section, our line of Retrofits & Upgrades achieves the same efficiency as the newest press lines in the industry! These automated options offer flexibility and breathe new life into any existing, new, or discontinued line.
Your table, automated.
We bring the best together!
Two C-Clamp Presses with Unistrut Jig Table
• Hydro-Air Mark-8 Mono Press (C-Clamp, Hydraulic Power Unit, Boom Assembly & Trolley)
• Panel Clip TK C-Clamp Press (C-Clamp, Hydraulic Power Unit, Boom Assembly & Trolley)
• Unistrut Jig Table/Stands (up to 80' long trusses)
• Electric Feed Rail
• Overhead Steel Beam
• Price is in US Dollars
$20,900 NOW $18,500 FOB MB Wasserman & Associates 800-382-0329 www.wasserman-associates.com
2021 CMF Floor Truss FRP with Conveyors
2021 CMF floor finish roller press for 3×2 and 4×2 floor trusses. Features 7-ft wide throat, with dual-sized rollers one half larger diameter rolls to press 3×2 material, the other half presses 4×2 material. Press includes 4″ diameter guide rollers, Dual (2) 5 HP drive motors, (2) safety bars, push button controls and e-stop button. Included are (19) 4″ diameter x 6-ft long, stand alone idler conveyors and (6) 6-ft long manual floor-truss stacking racks. 240 / 480 volt, 3 phase electrical required.
$29,997 FOB ON Wood Tech Systems
765-751-9990
www.woodtechsystems.com
2007 Clark Industries
Horizontal Truss Stacker
Model HVS, Two Unit, 2-Zone, 14’ Horzontal Stacking System. Two lifting units (one master and one slave) with integral electrics. A truss sensing system consisting of adjustable laser sensors mounted on slide rails. One indoor electric control enclosure & panel w/PLC and manual controls. A stacker-conveyor interface package comprised of (1) mounted 3-push button enclosure and (1) remotely mounted 2-push button enclosure (pause/ emergncy stop). Hand-held Wampfler Remote Control System. 8 stacking rails and 4 stripping posts. Stack 1 5/8” thick x 14’ tall trusses up to 30 high. Stack a truss in approximately 40 seconds (cycle time). Stack up to 55’ or longer trusses on each side of the conveyor with minor assistance for truss sag, shorter lengths can be stacked unassisted. Excludes 77’ Walk Through Conveyor System. Two systems available at $25,000 NOW $19,900 Each. FOB NE. Wasserman & Associates 800-382-0329
www.wasserman-associates.com
The
CUSTOM BUILT TO THE SIZE YOU WANT FOR ALL MAJOR TRUCK BRANDS
EMSI Field Repair Press
EMSI 10 Ton Field Repair Truss Press System. Complete with: 1/2 HP, 115 Volt, 50/60 Cycle Universal Motor – Operates at voltage as low as 60 volts. 10,000 PSI Portable Power Pack with Two Speed Operation – 200 cu in/min @ 0–200 psi, 20 cu in/min @ 200–10,000 psi and Externally Adjustable Relief Valve (unit weight 55 lbs.). C-Clamp Assembly with 8" Maximum Reach, 4" x 5" Pressing Platen (optional platen available for 4” x 2”). Independent 10 Ton Hydraulic Cylinder. 10’ Hydraulic Hose Assembly with Quick Disconnect Coupling. Handle with 24 Volt Remote Electrical Pendant. Call for Price Eide Machinery Sales, Inc. 612-521-9193 www.eidemachinery.com
• 14' Long x 4" or 5" (Inside Diameter) Schedule 40 Pipe
• Tube Steel Stands (7" Height Adjustment - Height to be Specified)
• 4 Bolt Flange Bearings
• Idle and Motorized Rollers
• 1/4 HP Motors (240/480 Volt-3 Phase) with Controls
• 1" and 1 1/4" Cold Rolled 24" Shafts Baffled
• 6 to 8 Week Delivery
From essential components to custom solutions, we’ve got everything you need to build trusses with precision and confidence. Our inventory includes parts for all leading truss jigging tables, OEM replacements, and custom components tailored to your needs. Choose from high-quality materials in custom lengths and widths, including durable plastic, unistrut, and steel.
We work with a nationwide vendor network, ensuring fast delivery. Don’t waste time searching – call us first to keep your projects on track.
Dave Walstad - Panama City Beach, FL
Dave.AllPoints@gmail.com
Carl Villella, CLFP President, Acceptance Leasing & Financing Service
The year 2025 sees businesses across industries grappling with a persistent workforce shortage. Finding and retaining qualified employees is a major challenge, impacting productivity and growth. However, technology offers a powerful solution, and equipment financing can make it more accessible than ever.
Several factors contribute to the ongoing workforce shortage. These include:
• Aging Population: Many experienced workers are reaching retirement age, leaving a gap in the workforce.
• Skills Gap: Rapid technological advancements mean that many job seekers lack the skills needed for modern roles.
• Changing Job Expectations: Workers are seeking more flexibility, better work-life balance, and opportunities for growth.
Investing in technology can help businesses overcome these challenges by:
• Automating Tasks: Automation can handle repetitive or manual tasks, freeing up employees to focus on more complex and strategic work.
• Increasing Efficiency: Technology can streamline processes, improve productivity, and reduce the need for additional staff.
• Expanding Reach: Remote work technologies enable businesses to tap into a wider talent pool, regardless of location.
• Improving Employee Experience: Modern technology can make jobs more engaging and fulfilling, leading to higher retention rates.
While the benefits of technology are clear, the upfront costs can be a barrier for many businesses. This is where equipment financing comes in.
• Preserve Capital: Financing allows businesses to acquire the technology they need without tying up valuable capital.
• Flexible Payment Options: Financing companies offer a range of payment plans to suit different budgets and cash flow needs.
• Tax Benefits: In many cases, businesses can deduct the interest paid on equipment financing, reducing their tax burden.
• Stay Ahead of the Curve: Financing makes it easier to upgrade technology regularly, ensuring businesses remain competitive.
The workforce shortage is a significant challenge, but it’s not insurmountable. By embracing technology and utilizing equipment financing, businesses can automate tasks, increase efficiency, and attract and retain top talent. Investing in technology is an investment in the future, ensuring businesses can thrive in the face of evolving workforce dynamics.
To see meaningful labor savings, quality improvement and production gains, SL Lasers with their easy-to-see green light are nothing short of illuminating. They enhance worker accuracy and productivity, regardless of experience or primary language. They can reduce tedious setup time by up to 70%. No complex training or costly service agreements are required. And SL Lasers integrate seamlessly with any component design software and are quickly installed over existing equipment. We’ve been trailblazers in wood component laser projection since its very beginning, and we’re still delivering more rapid ROI for roof truss, wall and floor panel producers every day. Contact our enlightening team at Wood Tech Systems to see how SL Laser can deliver for you.
productivity of any
$217,997 FOB AR
2005 Alpine RAM Easy-Rider roof gantry model 756A, side-eject, 14′ x 70′ working length table, slotted steel building surface with (9) ejectors, (1) 6-ft long parking station, electrical supply cord runs in trough, and all available jigging hardware. Gantry head with 24″ diameter gantry roller, 7.5 HP drive motor with gearbox, operator riding platform with joy-stick control, and (2) safety bars. (8) stand-alone receivers included. No finish-roller or exit conveyor included. 230/460v, 3 phase, electrical required.
$202,000 FOB MB
2008 Alpine C4 roof gantry line, model 757A, solid-top, trackless, side-eject, 14′ x 63′ working length table, slotted steel building surface includes (9) tables, (8) ejectors, (2) 6-ft long parking station, electrical supply cord running in trough, (6) powered roller conveyors, (6) idler roller conveyors, (20) exterior idler conveyors, and all available jigging hardware. Includes one gantry head with 24″ diameter gantry roller, 7.5 HP drive motor with gearbox, operator riding platform with joy-stick controls. No finish-roller included. 240 volt, 3 phase, 20 Amp electrical service required.
$389,795 FOB PA
(Video available here.)
2021 MiTek 40′ Auto-10 with Wizard PDS® automated pin system (commissioned Jan. 2022). The Auto-10 features a fully integrated 50 Ton hydraulic press with a 10’x24″ pressing platten (overall Gantry width 14’10”). Gantry features 4-Wheel Drive, and an operator platform with joystick control that travels up to 4.5′ per second. The Auto-10 press is capable of handling 2”x4”-12″, 4”x2”, and it is further optioned for 6″x2″ material with no adjustment. No finish press required, this system features a HDPE plastic/steel T-slot tabletop and includes a substantial quantity of auxiliary T-Slot jigging hardware. This state-of-the-art production system features (18) Wizard PDS® @ 16″ O.C. spacing with 36 jiggingpins covering 24′ of automated setup. Set up capabilities are further enhanced by manual T-Slot positions on either side of the Wizardsetup area , System is complete with (5) electrical control boxes, all cabling and gearbox drive components, main control box, computer kiosk, and system computer. System sold for $442, 300 new.
Buyer must provide appropriate voltage/amperage: Auto-10 – 230v, 3Ph , Wizard – 208v, 3Ph, 40A (3-phase transformer included), 120v AC clean power supply to control computer. Professional installation by OEM representatives required.
• 50 Ton Hydraulic Press with 10' x 24" Platen and Joystick Control
• Press Head Welds have been Repaired & Reinforced
• Raised Track with 4 Wheel Drive System
• 575 Volt / 3 Phase
• 10' x 56' Steel Slotted Top Table with Skatewheel Ejectors
• Wizard Automated Jigging (7 Control Boxes, 26 Rails)
• The Wizard was upgraded from GEN 1 to GEN 3 in March 2022
• Price in US Dollars
The TruStance Pedestal Jig System was developed to solve the problems associated with pedestal jig systems, while retaining and enhancing all the advantages. The system features track mounted pedestals with a track and lockdown design, movable pedestals, and a roller lift assembly. The pedestal tops are 30″ above the floor, creating a comfortable working height. The ability to configure the system in a very small footprint makes it ideal for any size truss plant. It is designed to use with a ‘C-clamp’ type press.
With the ability to install the interchangeable crossmembers and angle iron stops on both track mounted and movable pedestals, the system can be configured to meet the needs of even the most complicated truss designs.
Movable pedestals can be moved and locked down efficiently; the 4″ thick steel base provides the weight needed to keep them in position.
Bottom chord pedestals are installed on the steel track mounted to the floor. Pedestals are easy to move and rigidly lock into place with threaded rod locks.
The optional air activated roller lift assembly raises the truss above the jig to be easily ejected. Its versatile design allows it to be configured for any set-up.
TruStance recommends a (16) pedestal system for roof trusses to 60-ft in span. 120 volt, 1 phase, 20 Amp electrical required. 50 PSI air required.
Virtek LPS-6R Laser Projection Heads
• 8 Each - Virtek LPS-6R Laser Projection Heads
• Excludes: Computer, Virtek Software License & Service Agreement
$2,000 Each or $15,000 for all 8 Heads Price in US Dollars
Wasserman & Associates 800-382-0329
www.wasserman-associates.com
• E xcludes: Inside Powered Exit Conveyor, Finish Roller and Outside Conveyor
$61,900 FOB HI Wasserman & Associates 800-382-0329 www.wasserman-associates.com
Late 1990’s CMF Floor Truss
Machine
CMF Floor Truss Machine, trackless style, builds trusses from 12″ to 24″ depth and up to 40-ft long, includes built-in camber of 3/4″ over 40-ft, side-eject, air clamping, skate wheel transfer bars, 8-ft wide table x 48-ft long including parking areas. Gantry head includes 24″ diameter roll, pendant controls and dual-safety bars. 480 volt, 3 phase, 32 Amp electrical required. 100 PSI air required.
$78,997 FOB BC
New Wescana floor truss machine, available in side-eject or end-eject models. Builds floor truss depths from 12 inches to 26 inches, to 40-ft long. Features under-table cylinders powering the clamping system, built-in camber, truss flip arms, truss pop-ups, control valves for clamps, flip arms and pop-ups, with parking stations at each end of the table, and emergency shut-off bars on each side of the press head.
The Coeur d’Alene Golf & Spa Resort
115 S. 2nd St.
Coeur d’Alene, ID 83814
Hotel Deadline: March 31
Wednesday, 4/30
Golf Outing
Social Hour
Independent Dinner Thursday, 5/1
Educational Sessions
Tour: Mercer Mass Timber
Hosted Dinner
Friday, 5/2
Educational Sessions
Roundtable
“The Workshop puts you in front of the right people in one place to get answers to your questions about MSR, whatever they might be.”
—Ross Harter, Drexel Building Supply, Wrightstown, WI
“Sometimes we don’t know what we don’t know. Getting together at an event like the Workshop gives everyone a chance to keep their ears open for new opportunities and ways to become more efficient.”
—Mike Momb, Hansen Pole Buildings, Browns Valley, MN
“Lumber is your #1 used item –you need to know what you’re buying and using. The knowledge I gain about the lumber market and the forecast for the coming year is invaluable to my business.”
—Sean Kelly, Automated Building Products, Marshfield, WI
Featuring precision Gen. 2 controls, this system squares and sheathes wall panels ranging up to 16′ in length and up to 12′ -3″ wall height with dimensional material from 2×4 through 2×10. This late-model system includes a servodriven bridge with joy-stick controlled motion on the operator’s riding platform. The single, large-coil capacity tool carriage travels across the wall frame inserting sheathing fasteners at the spacing set by the operator. The stitchers will automatically insert fasteners through the sheathing into the top and bottom plates at your chosen spacing during the auto-return process. The bridge has 9 programmable presets for fastener spacing. Other features include: Single Beam Bridge, top and bottom plate stitchers, Operator Platform with Windows industrial touchscreen, and joystick control. Squaring table features a squaring edge, footswitch & push-button controls for telescoping side and horizontal outfeed rollers. 120 PSI at 60 CFM air.120 volt AC electrical required. Utilizes large-coil 15º wire-collated nails. (No nail tools included).
2022 Panels Plus Floor Cassette Station
• Assemble Dimensional Lumber, I-Joists & Open Web Floor Truss Panels from 12' Wide up to 45' Long
• Po wered (120 Volt/1 Phase) Telescoping with Foot Pedal Control
• Color Coded Joist Locators
• Pop-Up Skatewheel Conveyors
• Squaring Stops
• Price is in US Dollars
$55,000 FOB Ontario Wasserman & Associates 800-382-0329 www.wasserman-associates.com
2023 2-Head 30 mW LAP
www.woodtechsystems.com
• Automated Component & Linear Saws (2010 & Newer)
• Monet DeSauw or TimberMill Manual Component Saws
• Floor Web Saws
• Spida (Apollo) Saws with Truss Automation
• Bunk Cutters
Truss Equipment
• Roller Gantry & Hydraulic Press Systems
• Finish Rollers
• Truss Stackers
• Floor Truss Machines
• Lumber Splicers
• Jack Tables
• C-Clamp Presses
Equipment
• Pacific Automation or MiTek Mobile Home Press
&
By Thomas McAnally
TheJobLine.com
russ manufacturers looking to attract younger truss designers might want to think outside of the box. We have found one key issue affecting many Gen-Z truss designers and have a solution that may help entice them to your company—offering a Gen-Z-preferred workweek.
Consider this: Gen-Z has a different culture than Boomers, Gen-X, and even many Millennials. They value personal time with family, friends, and for themselves over work. They grew up during the “Great Recession” and started their career during COVID, so their experiences are different and it stands to reason that their values are not always aligned with ours. Not that it is bad, just different life experiences leading to different values. For Gen-Z, knowing they can plan a weekend getaway with their significant other or friends and not worry about a last-minute project on Friday that has to be done by Monday is likely to be more important to them than those of us who would be glad for the overtime. What’s more, many in Gen-Z would consider the last-minute work and deadlines stressful, and that stress can lead to burnout.
Offering a 32-hour work week, with full benefits, is an option that can yield significant advantages for both employers and employees. Many younger truss designers value work-life balance over a relentless race to the top, and they prefer a stable, supportive work environment where their personal lives are respected. The pressure of hoping they would have time off this weekend versus knowing they will is a big deal for some with commitments with friends and family. While we grew up hoping for overtime, or at least not turning it down when available, we scoffed at those too lazy to share the load. Many in Gen-Z have different priorities, and we should respect their culture if they get the job done. This shift in priorities allows companies to maintain high productivity levels in the hours worked without pushing employees to the brink of burnout.
A common objection from my clients’ perspective centers on cost-per-hour metrics. Reducing the hours worked naturally increases the hourly cost for fixed benefits such as insurance. However, by slightly reducing the base pay to spread these fixed costs over fewer hours, companies can enhance work-life balance without sacrificing productivity or cost metrics. In fact, at least one client has already adopted a full-time 32-hour workweek precisely for this reason. Not only do truss manufacturers benefit from this concept, but so can others in our industry. I recently spoke with Keith Dietzen, a long-time industry software entrepreneur, and the 32-hour week concept came up. He has been offering this option to his team for a few years and is very pleased with the loyalty and quality of work. Offering this brings calm to their lives, along with stability and respect. In return, the job gets done and done well.
“The 32-hour full-time with benefits option offers my people flexibility, lifestyle choices, and the independence to do their best work while maintaining accountability. They know their job and what we expect in a specific timeframe. This addresses problems we had with turnover and employee burnout.”
Traditionally, long hours were seen as essential for success, and some “fast-paced” industries still operate that way. But the next generation of technical professionals in our industry have adopted the post-COVID mindset of expecting more personal time and a balanced lifestyle. These employees will tell you they prefer stability and a supportive environment over the pursuit of money and status. While they are the minority, for now, they value having a personal life that remains separate from work, and they are content to “leave work at the office” when they clock out.
From a recruitment and retention perspective, a reduced workweek can be a significant competitive advantage. Top Gen-Z talent is increasingly drawn to employers who value their time and promote a balanced lifestyle. When a company offers a shorter work week with full benefits, it clearly signals that the organization prioritizes employee well-being. This advantage becomes particularly significant when competing against larger companies that might offer higher pay but demand much longer hours.
Moreover, a balanced work schedule reduces stress from overwhelming deadlines and excessive overtime. When employees feel valued and engaged, turnover rates decrease, and the overall company culture becomes stronger and more resilient. In essence, offering the 32-hour workweek option is not just about reducing hours; it’s about reshaping the work environment to prioritize quality of life in a new cultural change. For younger truss designers, this approach creates a sustainable career path—one that enables professional excellence while also allowing for a fulfilling personal life.
Thomas McAnally is President of The JobLine, a 32-year industry-focused recruiting company. His network of thousands of employers and candidates allows him to hear many perspectives. This article is about one perspective where we acknowledged that Gen-Z culture is shifting away from the 45–50 hour week plus Saturdays in peak season to a desire for a different work-life balance. Trying to force Gen-Z into existing expectations risks employers’ ability to attract and retain talented designers. Contact me if you would like more information on the 32 hour full time with benefits program.
This is the first, self-contained, truly portable FRP unit used to press metal truss plates into dimensional lumber at virtually any location. Wood component (roof and floor truss) manufacturers, as well as builders, frequently require a tool to repair metal plate connected, wood truss components. The complete unit is mounted to a wagon built from square tubular steel. Extremely compact at only 28” wide and about 32” long the wagon features four wheels on soft-rubber solid tires, and a steering axle on the front with a handle that makes the unit easily maneuverable. The wagon contains the hydraulic power unit and an area for a portable gas generator. A rack in the back securely stores the C clamp, a standard 25′ hydraulic hose, and an electric power-supply cable. The clamp is manufactured from T1 steel, cut into a C-shape with a steel tube welded to the front that securely holds the hydraulic cylinder. Pressing is easily performed with a 4×4 magnetized steel platen that holds and presses the truss connecter plates. The C-clamp that weighs less than 30 pounds, features a throat that opens to 4-1/2” inches to accept either 4 x 2 or 2 x 4 lumber. It has a push on and release off switch to cycle the unit. A 10,000-psi electric-over-hydraulic power unit pumps hydraulic fluid through a 10,000-psi hose to activate a 10-ton hydraulic cylinder with a 3.9 inch stroke. The unit can be powered by 120v electric power or an optional 120v, 2200-amp, gasoline powered generator, which can also act as a portable power supply out in the field for other single-phase equipment.
• Pressing Capability: 4.5” throat opening presses 2×4 through 4×2, includes a standard 25-foot, HD 10,000 PSI hose, with a 10 TON, 4”x4” magnetized pressing plates
• Electric/Hydraulic: SPX Hydraulic Technologies – Rockford, IL USA 10,000 PSI / 700 BAR. 10 ton pressing capability
• Power Source: 110V Dual Power via outlet plug in and/or optional gas-powered inverter generator at an additional price. Optional generator is a Honda EB 2200i Industrial, inverter motor, manual start, GFCI Protected,120 VAC at an additional cost of $1,450.00.
• Warranty: One year from date of purchase on manufactured unit, OEM warranties on hydraulic and gas motor.
New Wescana roof finish roller presses, available in either a 14-ft or 16-ft throat models. Travel speed of 2-ft per second. Both models feature 24″ diameter steel rolls with 3 1/2″ diameter shafts with baffles, (2) 5-horsepower drive gear motors with controlled motor drive systems for starting and stopping, along with taper-lock sprockets, sealed flange roller bearings and reversing magnetic starters.. Includes safety shutoff bars, electric eyes, amber running light, red reversing light with buzzer, and e-stop module. 240 / 480 /575 volt, 3 phase electrical required.
Price based on configuration
100 ton hydraulic gantry with 15 HP motor, and two stage pump. Drives on four 8″ dia. steel wheels with two individual hydraulic motors on two drive wheels running on 60# crane rail. Gantry speed up to 300 fpm. (2) 7″ x 5″ hydraulic cylinders. Pressing platten 24″ x 14″, 2″ thick steel. Includes (10) 14′ x 3′ 5″ tables with 1/2″ thick drilled and tapped steel tops. 5 ejectors included. 240v, 3 phase, 100 amp power.
$87,990 NOW $44,990 FOB MN Wood Tech Systems 765-751-9990 www.woodtechsystems.com
RolSplicer Chord Splicing System
• Splices 2x3 and 2x4 Lumber
• 3 to 4 Second Cycle Time
• 2 Recessed Push Activation Buttons
• 3 HP Gear Motor
• Excludes Infeed/O utfeed Roller Conveyor
$14,500 FOB TX Wasserman & Associates 800-382-0329 www.wasserman-associates.com
In 2025, SBCA is Offering Quality Bootcamps to All Component Manufacturers (CMs)
These two-day live events are being held in all six regions of the country, giving CMs the opportunity to learn from SBCA instructors on how to maximize the benefits of SBCA’s Digital QC software, enhance your quality management program, and better understand how to get the most value out of Third-Party Quality Assurance (QA) audits. Level up your Quality Management program, register today!
To learn more about when a Quality Bootcamp will be held near you, check out: sbcacomponents.com/quality-bootcamps
Price: $237,900
FOB: ND
The Terminailer all but shatters the stereotypical myth that sub-component equipment is essentially peripheral – unimportant. And it does so by quickly and accurately driving far more framing nails in your wall panel jobs than ever before. Whether in your shop or in the field, one operator sets the pace for production and quality, which reduces labor costs and other aspects of overhead.
The new Terminailer V.8 improves on the previous generation Terminailer in several key ways:
All new HMI/Software
• Siemens Pivoting HMI Touchscreen display to operate from either side
• On-screen tutorial for all menu items
• Operator now controls functions such as process speed, nail spacing, nail patterns, etc.
• Simplified input commands
Nail Feed Complete Redesign
• All new frame to allow for redesigned nail coil placement with direct feed path
• EverWin PN90-PAL industrial tools now standard equipment
• New nail guides with spring-loaded tensioners
• Nail coils move with vertical travel of the nail guns
Reengineered air system
• SMC “Soft–Start” Pneumatics
• Simplified air for control to all components: lift–cylinders, triggers, stop–gate, etc.
• Direct air supply to each nail gun for improved nailing performance
• All pneumatic elements are clearly labeled for EZ service and adjustment
Overall Features
• Pharmaceutical grade assembly, industrial grade durability
• “Block–wheel” redesign for 3X increased applied force
• Approximately 1,200# of applied clamping force resulting in straighter finished
• Subcomponents from even the poorest lumber
• Larger doors for easier access to interior elements including coil–nail spools
Terminailer is an event-driven, sub-component assembler that will quickly and accurately drive 30% to 70% of the framing nails in any wall panel job. In your shop or in the field, one operator sets the pace for production and quality. The Terminailer functions independent of design software, requires zero set-up time when switching between any configuration, and requires no special operator training.
The Terminailer is easy to move around the shop so its location can evolve as your shop evolves. With all of the nailing occurring in the closed main chamber, nail injuries and nail location misfires are eliminated, making your plant that much safer.
With nearly ten years of development from people that know machinery, it is assembled to exacting standards, well supported, and it is easily maintained with shelf-item parts. Terminailer: vetted, tested, and ready to drive maximum productivity for you. Be sure to check out our videos below for a quick review of this revolutionary machine!
240 volt, 1-phase, 30 (full load) Amps, 60 Hz electrical required. 50 SCFM @ 120 PSI air required. Net weight 7,000 lbs.
Klaisler 40′ Floor Truss System Model G2640 kick-leg, gantry head with 18″ dia. roller and push button controls and dual safety bars. System builds trusses from 12″ to 24″ depth and up to 40′ in length with built-in camber, side-eject, with air clamping, dual park areas. Twin 5 h.p. drive systems, 85lb.crane rail, includes festooned cable/power supply line with single support mast. 230/460v, 3 phase, 90lb+ PSI air required.
$29,920 FOB KY Wood Tech Systems 765-751-9990 www.woodtechsystems.com
• Klaisler Model GR1424 Gantry Roller
• Re cessed Floor Mounted Rail
• (5) 6' x 14' WEG-IT Tables with Ejectors
• 460 Volt / 3 Phase
• Excludes: Inside Exiting Conveyor, Finish Roller & Outside Conveyor
• Price in US Dollars
For many years, there has been a great deal of discussion at industry events, in component industry board rooms, and even in this publication about a looming shortage of design technicians. So, what is behind the wood truss designer shortage and why is it such a pressing issue? And, how can we address it?
First and foremost, one cause of the shortage is the natural course of time and the retirement of existing designers. Our designers with decades of experience and years of solving complex architectural and structural puzzles are now looking toward retirement. All of that knowledge built up in the minds of designers is the institutional knowledge that’s about to walk out the door. It’s not just about knowing the numbers; it’s about understanding the nuances of how wood behaves, the subtle tricks of the trade, and the gut feeling that comes from years of working with these systems. You can’t just download that kind of expertise. It’s built through years of projects, problem-solving, and seeing what works and what doesn’t. When those gray-haired designers retire, that knowledge goes with them, leaving a real gap in the industry. It’s like losing a library of unwritten best practices, and that’s a huge loss for any field, especially one as critical as component design.
Over recent years, there has been an accelerating discussion about the use of artificial intelligence (AI) to fill gaps in a wide range of applications. Now, you might think, “Well, can’t we just use AI to fill that component designer gap?” And that’s a fair question. AI is definitely making waves in a lot of industries, and there’s potential for it to help with truss design. But here’s the thing: architectural plans aren’t always crystal clear. They often rely on implied information, past practices, and a certain level of interpretation. The wood truss industry, like many traditional sectors, is built on a foundation of established practices and tacit knowledge. Think about it: a plan might show a general layout, but the specific details of soffit conditions, or how a truss connects to a wall or supports a roof, might be left to the designer’s judgement. AI, on the other hand, thrives on precise data. It struggles with ambiguity. This will make it difficult to translate into a format that AI can readily understand. Imagine trying to teach a machine to understand the subtle cues that an experienced designer picks up on intuitively. Add to that the many regional and client-specific variations in building and component design practices and the issue becomes even more complex. It’s a massive challenge. You can’t easily digitize that “feel” for the material, or the ability to read between the lines of a blueprint, or to incorporate the past experiences with a specific builder. So, while AI can definitely help with certain aspects of design, it’s not going to replace the need for human expertise anytime soon. We need skilled designers to bridge the gap between the fuzzy world of architectural plans and the precise attention to detail required for a safe and efficient wood truss.
And let’s not forget the human element. Component design isn’t just about crunching numbers. It’s about collaboration, communication, and understanding the client’s vision. It’s about working with architects, builders, and other trades to ensure that the final product is both structurally sound and aesthetically pleasing. That’s where the human touch really matters. AI can’t replace the ability to have a conversation, to ask the right questions, and to find creative solutions to unexpected challenges.
So, while we are exploring the potential of AI, we also need to invest in training the next generation of designers, to make sure they have the skills and knowledge to carry the torch. We need to actively promote this career path, feature the technology involved, and highlight the rewarding aspects of the job. It’s about building a sustainable future for the wood truss industry, and that means investing in both technology and people.
Do you see AI being a factor in our industry in the future? I would love to hear your thoughts.
If you want help finding that next perfect component designer or design job in Canada, please contact me. If your work is in the mass timber world anywhere in North America, I’d love to talk to you about connecting you to that next great job or candidate. You can reach me at secord@thejobline.com, or 800-289-5627 ext. 2. I’m also happy to engage at: LinkedIn.com/in/geordiesecord. www.thejobline.com
The MSR Lumber Producers Council (MSRLPC) represents the interests of machine stress rated lumber producers in the manufacturing, marketing, promotion, utilization, and technical aspects of MSR and MEL lumber. Suppliers, customers, and professionals may join as Associate members. Members enjoy:
• Online Marketing
• Networking Opportunities
• Reliable Market Data
• Education
“There is no question that the MSR Lumber Producers Council meetings are worth your time to attend. The information you will receive from the guest speakers and members of the Council is unparalleled!”
—Sean Kelly, Automated Products
Inc.
Pointer
Auto Return -Bridge Tilt at Sheathing Seams -Programmable Fastener Patterns -Pop-Up Skatewheel Conveyors
to 12’-5” Wall Heights
Squaring Stops
Floor Rails
• Wall Lengths to 20' / 6' to 12' Wall Heights
• Length Stops Position the Top & Bottom Plates for Nailing (as directed by Wall Panel Design Software output)
• Touch Screen Computer/Enclosure
• 4 Everwin PN80PAL Coil Feed Nail Guns
• Transfers Wall Panels from the Wall Extruder to the Squaring Table STUD EXTRUDER
• Nail C, L, U Sub-Assemblies and Double/Triple Studs
• Touch Screen Computer/Enclosure
• 2 Everwin PN80PAL Coil Feed Nail Guns
• Transfer Sub-Assemblies & Studs to the Wall Extruder Operator
• Squaring the Wall Panel before attaching Sheathing Excludes: Installation/Training and Annual Technical Support Fee EQUIPMENT FINANCING available from Fidelity Leasing $249,000 NOW $239,000 FOB AZ
The Industry-Leading Manufacturer of Panelized Wall Panel & Floor Cassette Equipment.
SERIES AUTOMATED SHEATHING STATION
The Platinum Series Automated Sheathing Station is the most automated sheathing station that Panels Plus offers and reduces the amount of time an operator needs to be hands-on during the sheathing process. This sheathing station is driven using MiTek Software and completely fastens sheathing to studs, blocking, headers, and sill plates to ensure quality panels every time. This model can be a stand-alone unit, or integrated into a larger system. Various sizes and configurations are available.
2007 VIKING 16' X 12' SQUARING TABLE WITH SHEATHING BRIDGE
• 16' x 12' Squaring Table with Powered Width Adjustment & Powered Chain Conveyor
• Wall Panel Lengths up to 16', Wall Panel Heights from 4'-0" to 12'-2"
• Swing Gates at Both Ends of Squaring Table
• Automated Field & Edge Nailing Driving by Panel Pro Event Software & Your Programmed Nailing Patterns
• Simple Touchscreen Controls
• 2 Tool Carriages for Sheathing Nailing with Tilt Function for Seams
• 2 Paslode Nail Guns with High Load Coil Tray
• Auto Sheathing Bridge Return
• Includes 4 Pallets of Magnum Coil Nails (2 3/8 x .113)
• 480 Volt / 3 Phase
$29,900 FOB KS.
Wasserman & Associates 800-382-0329
www.wasserman-associates.com
•
IBS Tilt Table
• 16' Length Capacity
• 7' to 12' Wall Heights
• Hydraulically Powered (3 Phase)
• Video available upon request $22,500 NOW $13,900 FOB WI Wasserman & Associates 800-382-0329
www.wasserman-associates.com
Prairie Mechatronics 12' Portable Sheathing Bridge
• Programmable Fastener Spacing with PLC Touch Pad Entry
• One Touch Selection for Field or Seam Pattern
• Gun Tilt at Sheathing Seams
• Laser Pointer for Stud Location
• Sensors to Detect Sheathing
• Nail/Staple 8' Wall in 6 to 8 Seconds
• Quick Tool Changeout
• Weight: 150 Lbs
• Extra Gun Mounts & Spare Parts
• Excludes Nail or Staple Guns
• 120 Volt / 1 Phase
• Includes Custom Pneumatic Supports (adjustable from 35" to 47" above floor)
• 2 Available at $18,500 NOW $14,500
& Associates
• 2022 Triad Mobile Diamond Quad Framing Table (never used)
• Wall Lengths up to 16', Wall Heights from 6'-9" to 10'-3"
• 2 Tool Dollies with Senco FP752XP Nail Guns
• Stud Locators at 16" and 24" Centers
• Pop-Up Skatewheel Conveyors
• Squaring Stops
• Telescoping Hitch System (pivots out of the way when framing)
• 4 Down Riggers
• Not DOT certified (to be shipped to the jobsite and moved around)
• Video available upon request
$79,500 NOW $75,500 FOB HI
• Wall Panel Lengths to 16'
• Powered Height Adjustment (3-11' to 12'-3" wall heights)
• Pop-up Skatewheel Conveyor
• Pop-Up Center Support (for transfer of window/door assemblies from the side)
• NO Tool Dollies, NO Stud Locators 20' ROLLER CONVEYOR WITH STANDS
• Wall Panel Lengths to 16'
• Powered Height Adjustment (3'-11" to 12'-3 wall heights)
• Multi-Tool Panel Bridge with Laser Pointer & Bridge Tilt
• Palode F350S Nail Guns (guns mounted on 6" centers with 3" shift)
• Industrial Router Motor Reconditioned by Doug Dodd in 2020 $47,500 FOB PA
• One section is on casters to accommodate variable wall heights IBS SQUARING TABLE WITH PANEL/ROUTER BRIDGE
• Wall Lengths to 12'
• Wall Heights to 40'
• Powered Height Adjustment
• Manually Adjustable Rake Side (0 to 12/12 pitch)
• Adjustable Squaring Stop
• Pop-Up Skatewheel Conveyors
• Stud Locators at 16" and 24" Centers
• Center Support Bar with Stud Locators
• Excludes Tool Doilies
• Price is in US Dollars
The Wood Wall Combo Station is an all-in-one system that frames, squares, and sheathes wall panels for quality panels every time. The Combo Station is designed for low-volume, entry-level operations and is compatible with lumber from 2×3 through 2×10. Designed with the rigors of a panel shop in mind, our equipment is developed with longevity and quality.
The Combo Station can be stand-alone or integrated into a full production line. Various sizes and configurations are available.
BENEFITS
• Ergonomic working height
• Improved squareness vs. traditional methods
• Superior wall panel consistency
• Flexibility with fastener spacing
• Fastens consistently and accurately
a blending of excellent services and products, with answers that work...!©
Not producing the results you need or want – getting conflicting info about what to do and the equipment and the systems you may need? Before you Buy - Ask yourself –do I need a salesman or a guide?
If you want an Independent Guide that has your bottom-line results as the #1 priority, Call Me. If the salesman will do - we'll talk later...
Also, don't let Financing Deals influence your best solution. FitzGroup can arrange – Zero down & No payments for 90 Days!
Please be assured that your investment with any of our selected partners will not cost one penny more with the Fitzgerald Group as your purchasing contact. In addition, you will receive the full advantage of our Partner Relationships and Services NOT offered elsewhere.
By Jay P. Jones, P.E. Executive Director, TPI
The ANSI/TPI 1 standard is a critical document that governs the design and quality criteria for metal plate-connected wood trusses. It serves as a guideline for truss manufacturers and engineers alike, providing the technical framework to design and construct reliable and codecompliant trusses used in residential, commercial, and industrial buildings.
As an ANSI-accredited developer, the Truss Plate Institute (TPI) follows a rigorous consensus-based process to ensure that ANSI/TPI 1 remains current and relevant to industry needs. The ANSI process mandates that the standard be opened for review and update at least every five years, allowing for advancements in engineering, materials, and construction practices to be incorporated. In keeping with this process, the standard was most recently updated in 2022, and the latest edition is now referenced in the 2024 ICC model codes.
The latest update to ANSI/TPI 1 included more than thirty changes, though most were clarifications that generally won’t impact truss designs. However, there were several changes that may have a significant impact on typical truss designs. Some of the most critical changes are discussed below and include:
• Person Loading
• Multi-ply Girder Load Distribution
• Web Reinforcement Design
• Extended-Chord Bearing Trusses
Person Load (ANSI/TPI 1-2022 Section 6.2.2.5)
This new provision essentially requires trusses spanning more than 18 feet to be designed to support a 300-pound concentrated load applied at the midpoint of each bottom chord panel. This check is to be done without environmental loads (such as snow or wind) and allows for a 1.6 duration of load factor. The provision was introduced to enhance safety by ensuring that the bottom chord can support a worker during temporary conditions, such as access for maintenance or installation activities.
Previously, multi-ply girder trusses were designed under the assumption that loads applied to one face were evenly distributed across all plies. However, extensive testing has shown that the ply closest to the applied load consistently carries a greater share of the load, regardless of the connection method used. To address this, a new provision in the standard now specifies the minimum percentage of load each ply must be designed to support. This change may lead to an increase in connector plate sizes for some girders and, in some cases, require higher-grade lumber. However, other updates to the standard, such as adjustments to repetitive member factors, may help offset the impact on lumber requirements.
A new design method has been added to the standard to provide an engineered approach for analyzing reinforced web members (e.g., T-braced and I-braced webs). Previously, web reinforcement was addressed prescriptively with a table in the BCSI, which imposed geometric limitations and often required highergrade lumber than necessary. The new provisions allow for more flexible and economical design solutions, as they can now be incorporated into truss design software, offering greater efficiency when web reinforcement is used in place of continuous lateral restraint (CLRs).
Another design methodology that was added to the standard is for extended-chord bearing trusses, also known as top-chord-bearing trusses. Previously, these trusses relied on a prescriptive table in ANSI/ TPI 1 to limit the reactions for specific top-chord-bearing conditions unless other values were determined through testing. The updated standard introduces new provisions that allow designers to analyze any topchord-bearing condition analytically, rather than relying solely on the prescriptive limits.
Since many plate suppliers have already incorporated in their software proprietary analytical methods for designing top-chord-bearing trusses, significant changes in truss designs may not be noticeable. However, the new provisions offer designers more flexibility in evaluating specific conditions.
Additionally, because of this new thorough analytical method, a new requirement has been added regarding lumber wane in the top-chord-bearing area. If wane is not managed through a quality control process during manufacturing, a new factor (Cwane) will be applied, reducing the reaction limit. Manufacturing plants that effectively limit wane in these areas can apply a Cwane factor of 1.00, meaning no reduction in bearing capacity.
The updates to ANSI/TPI 1 reflect TPI’s ongoing commitment to keeping the standard relevant and aligned with current engineering practices and technology. By incorporating new design methodologies and refining existing provisions, these changes improve the accuracy, efficiency, and safety of truss designs. Keeping ANSI/TPI 1 up to date is essential in maintaining the metal plate connected wood truss industry on a sound engineering basis. The 2022 edition of the standard is available for purchase from TPI at www.tpinst.org.
Stacking wall panels at the end of your production line can be a real labor-intensive and safety-challenging task. But it doesn’t have to be now, thanks to ProStack . This innovative wall panel stacker literally stacks from the bottom up, reducing awkward overhead lifting & placement, and the risk of head injury. Plus, ProStack frees up at least one worker to return more productively to your core task—building wall panels. Enhanced worker safety and productivity is what ProStack is all about.
By: DAK Automation
Setup and installation is easy too, without the need for complex training or disruption to workflow. So, free up your team to do what they do best, and you need to do most, and let ProStack stack your wall panels instead. Contact us to learn more today. For a ProStack demonstration video, scan the QR code below.
• Model SRDE6.5 Stock Reel
• Model RS35-4-12" Roller Straightener
• Model FR5-12 Feed Roll
• Hydraulic Press System with Three Feature Dies (36" Feeds)
• 22' Powered Entry Conveyor
• M odel 420 STR Rollformer (10 Forming Stations)
• Roll Tooling
• Beck Automation Controller
• Citronix CIJ Ink Jet Printer
• 3 5/8" and 6" R-Stud
• Coil Inventory
• Refer ence Uploaded PDF for Additonal Details & Layout
Wall Panel Lift
* 8’- 12’ Wall Height
* 1,000 LB Capacity
* Easy Adjustment
* Hoist and Crane Sold Separate
Handle Bar Router
* 8’ - 12’ Wall Height
* 2 Person Operation
* 3 ¼ hp Production Router
* 120 Volt /1 Phase/15 Amp
Lay-Up Tables
* 10’ x 10’ Working Area
* Lift & Extend Rollers
* Squaring Lip
* Nail Tray
Skate Rollers
* 15’ Standard Length
* Adjustable Height
* Sturdy Stands
* Custom Lengths Available
$13,900.00
$3,500.00 $3,000.00 $1,950.00
New Component Table with Skatewheel Conveyors
Lift & Extend Skatewheel Conveyors. 10' x 10' Work Area with Squaring Lip. Gun Holster & Nail Tray.
$13,900 FOB NE
Wasserman & Associates
800-382-0329
www.wasserman-associates.com
• 8' to 12' Wall Heights
• 1,000 Lb Capacity
• Weight: 120 Lbs
• Excludes: Electric Hoist & Freestanding Bridge Crane
$1,950 FOB NE
Wasserman & Associates
800-382-0329
www.wasserman-associates.com
Consider Panels Plus wall panel assembly equipment for manufacturers of wood or steel wall panels, floor-panels, and related framing components. Panels Plus is an employee owned, ISO certified, manufacturing company that builds state-of-the-art equipment featuring durable construction, with fit and finish second to none in the structural building component industry. The referenced base framing table allows you to assemble from 7-12 foot wall heights, at industry standard 16 foot lengths, at a working height of 29 to 32 inches. This framer design includes controls at each end of table, squaring stops and pneumatic clamping for consistent wall panel quality. Frames 2x4 or 2 x 6 walls, with color-coded, steel stud locators at 16 and 24 inches O.C. spacing. Includes pop-up skate wheels for easy transfer of completed wall frame. Framing table can be configured to receive wall framing light bars, other options include custom buildable wall heights, lengths and auto-indexing of optional 2 or 3 tool carriages.
Additionally from Panels Plus are sheathing tables with features that include foot pedal control at squaring end of table, with squaring stops, roller conveyors at both sides, single pendant controls for bridge, tool spacing at 6 inch centers with 3 inch bridge shift for offset nailing. Tool bridges can accommodate from 2 x 4 to 2 x 8 walls, with seam tilt being standard equipment Panels Plus Tool Bridges are available with single beam or dual beam design for two different tool mounts on one bridge. Squaring stations, sub-component tables, conveyors and panel lifts are also available to complete the configuration of the wall panel assembly line. Price includes factory installation and training. 50 CFM at 120 psi air. 120 or 230 volt, 1 phase electrical.
765-751-9990
Solving the problem of missed fasteners on exterior sheathing remains one of the primary reasons for call back charges and exceptions noted during jobsite building inspections. Clearly finding and resolving missed fasteners or “shiners” becomes mission critical before a sheathed wall panel leaves the production line. Our shop-proven, tilting conveyor makes the process safe, fast, and labor efficient. The ProStack tilt in-feed safely lifts wall segments to 45º in 5 seconds for inspection and on to 75º for easy to reach repairs. This tilt system is also excellent for installing blocking , windows, and other details in your wall panel segments. More information click here. 72,657 FOB ND
$37,525 FOB ND
ProStack powered in-feed conveyor was engineered to deliver wall panel segments at a matched speed and height into the ProStack automated wall panel stacker. Built for smooth operation and assembled with laser cut, powder-coated finish steel. Base model conveys wall panel segments up to 12’ in height and up to 16’ in length for wall segments up to 1,600 lbs. Extended length systems come in standard 20′ and 24’ length capacity. All models come with adjustable working heights and variable conveyor speeds.
Powered in-feed conveyor section, synchronized chain drive under top and bottom plate for open access, 5-HP, 208v, 3Ph power. Adjustable working height from 28” to 34”. 16′ length capacity.
By Frank Woeste and Joseph Loferski
common denominator for deck collapses is a special family event, such as a graduation, wedding, birthday party, or family reunion. A properly designed and constructed 14-ft x 24-ft residential deck floor, designed for a 40 psf uniform live load, should safely support 84 occupants based on an average occupant weight of 160 lbs. Knowing that a deck has been safely used for years by as many as 10 occupants, the practical question for the homeowner might be is the deck safe for a special event when 15, 25, 35, or more family and friends could occupy it? Absent an inspection by a qualified person, a homeowner would not know if their deck was safe for more than 10 occupants. Past “experience” alone can lead to an unfounded assumption that the deck will safely support more than 10 occupants during an upcoming “special event,” when in fact, it is not safe.
Applied occupant load is only one side of the structural safety equation. The load capacity of critically important deck connections can be reduced due to decay of the wood components and/or corrosion of steel fasteners made with nails, screws, lag screws. or bolts.
For an example of red rust corrosion, a ½-inch diameter carriage bolt removed from a 4x4 guard post connection is shown (Photo 1) next to a new bolt for comparison purposes. In this case, the bolt had been in service for 13 years. The homeowner was aware of coastal saltwater corrosion and attempted to remove the bolt when it broke. Without removing the bolt from the connection, the homeowner would not have known that the shank had been reduced to less than ¼-inch (or about 25% of the original area) and could not be relied on to secure the 4x4 guard post to the deck floor framing.
Further complicating the matter, a deck that seems to be new or cosmetically repaired (freshly painted) for appearances may not be safe. Some decks are built without a permit from the local building department and not inspected at the time of construction. Even when permitted and inspected, the deck code requirements adopted by the applicable state or local jurisdiction vary widely. For example, some jurisdictions require the deck guard post to be connected to the floor framing using a structural connector (Photo 2) to meet the IRC requirement of 200-lb concentrated load applied on the top rail. Other jurisdictions do not require a structural connector (such as depicted in Photo 3), allowing the deck contractor to use their judgement on how to construct the connection.
Photo 1. In a coastal saltwater setting, a ½-inch diameter carriage bolt was used to connect a 4x4 guard post to the floor framing. The bolt shank was reduced to less than ¼-inch after being in service for 13 years.
rim
applied 37.5” above the top of floor joists. The test setup shown was used to demonstrate that the connection to the deck framing would safely resist a code-required concentrated 200-lb load at any point along the top rail with a safety factor of 2.5.
The connection failed at about 40% of the target test load of 500 lbs when the rim joist pulled away from the floor joists (as indicated by the red arrows).
The guard connection in Photo 3 is made with two ½” bolts and washers and would appear to be strong and safe, but in fact, it is not because the rim joist was not adequately secured to the floor framing system. For this test, the rim joist was screwed to the end grain of the joists as is typically done in the field. When the top of the guard post is loaded in the outward direction, the screws are loaded in withdrawal from end grain, which is the weakest direction for fasteners in wood. [It should be noted that loading wood screws in withdrawal from end grain is not permitted by the National Design Specification for Wood Construction (NDS).]
Given the numerous uncertainties about your deck, from its construction through its time in service, existing decks should be inspected by a qualified person on an annual basis for safety. Do you know which codes and practices were used to construct your deck? Do you know the extent to which its wood framing and connections may have deteriorated due to outdoor moisture and rainwater? Have its fasteners and connectors experienced corrosion? For occupant safety concerns, an inspection of a deck for appearance alone should not be considered a meaningful deck inspection.
The purpose of this article is to recommend two deck construction and inspection educational resources that a homeowner, deck contractor, or design professional can use to learn about conducting a meaningful safety inspection of an existing deck. The primary objective of a meaningful safety inspection is to identify safety-related deficiencies that may lead to an occupant injury event.
As stated by Bruce Barker in Deck Codes + Standards (2024, 2nd Edition),
“If
you don’t know what a safety defect looks like, you will not find it.”
Because an existing deck (or even a new deck) may not be safe, a meaningful deck inspection requires the inspector to be knowledgeable about all deck elements that are critically important for occupant safety, deck construction details that are based on the current residential code (IRC), and good industry deck construction practices. Having this knowledge base about construction details that are considered “safe” for occupancy, the inspector has a standard or benchmark for identifying and evaluating potential life-safety deficiencies of an existing deck.
DCA6-2015 Prescriptive Residential Wood Deck Construction Guide , published by the American Wood Council (AWC), is an excellent (free) resource for a homeowner or deck contractor to learn about safe deck construction details. DCA6-2015, hereafter DCA6, is based on the 2015 IRC deck code requirements and good industry practices.
Presented in 22 sections, DCA6 gives the structural design requirements for joists, cantilevers, beams, decking, connections, support post, footings, bracing and lateral load requirements, guards, handrails, stairways, and detailed drawings that show the recommended type and size of fasteners or connector type and load rating. For example, DCA6 gives two safe options (Figures 8A and 8B) for connecting a deck beam to support posts.
Anyone may download the complete DCA6 in English or DCA6 in Spanish from the AWC website.
An excellent, one-of-a-kind resource for learning how to inspect an existing deck for continued safe use is Deck Codes + Standards (2024) by Bruce Barker, a longstanding American Society of Home Inspectors (ASHI) leader who has inspected decks for over thirty years. Available from Amazon, the author shares his inspection experience by boldly addressing myths about deck construction, common defects observed in the field accompanied by code-conforming requirements and details, why a permit and inspection is critically important for deck safety and the homeowner, and tips for homeowners (Appendix 2) on how to select a good and qualified contractor for deck repairs or replacement.
Deck components and elements as well as related code requirements are presented and explained in layman’s language supplemented with detailed illustrations (such as Photo 4). The applicable code requirements for different deck components and elements are presented and discussed using example photos of details that are proper and code conforming, and others that did not work and why.
The 127-page 8.5”x11” book includes a detailed Residential Deck Inspection Checklist that could be extremely helpful for a homeowner when addressing the reported deck deficiencies given in the inspection report, serving as a third-party assessment of the risk involved for different deficiencies. The Checklist is designed to document the condition of an existing deck and includes specific deficiencies and recommended actions for each condition/deficiency that may be indicated by the inspection. The recommendations for addressing specific defects range from:
• Recommend,
• Strongly recommend, to
• Do not use deck. Strongly recommend professional evaluation.
The standard practice for residential home inspectors when reporting a deck defect is to recommend further evaluation by a “qualified” or “licensed” contractor, or “design professional.” Homeowners should know that home inspections, per standard practice, are based on visual observations only. For example, a home inspector (by standard practice) is not required to remove a nail, screw, lag screw, or bolt to inspect for corrosion of the shank or to investigate potential defects beyond what is visually apparent. If a home inspection report indicates a deck defect, homeowners are strongly encouraged to heed the advice given for “further evaluation” by a licensed contractor, engineer, design professional, or other qualified professional.
DCA6 and Deck Codes + Standards (2024) can help an inspector gain knowledge of current deck code requirements, know what to look for and where to look for potential deck deficiencies, and report the results of the inspection in a manner that communicates the importance of the noted deficiencies with corresponding recommendations for the homeowner. Inspecting an existing deck for continued safe use is challenging because of potential deterioration of materials (lumber, decking), fasteners (nails, screws, lag screws, bolts), and connectors (joist and stair stringer hangers, beam to post or post to footing). Wood decay and/or corrosion of fasteners and connectors may not be visible and can reduce the strength of the critically important deck elements.
A unit on “Deck Inspection—Focusing on Life Safety Issues” will be presented at the April 2025 Virginia Tech short course, Structural Design of Wood Structures, being held on April 16–17 in Blacksburg, VA. For more information and to register, visit the Virginia Tech short course website.
Frank Woeste, P.E., Professor Emeritus, Virginia Tech (VT), conducted wood engineering research and taught wood design courses throughout his 26-year tenure at VT. In cooperation with other faculty and wood industry professionals, he has developed and participated in VT continuing education programs for more than 30 years.
Joseph Loferski is a retired professor from the Department of Sustainable Biomaterials at Virginia Tech, where, for 45 years, he taught classes and conducted research on wood, wood construction, and durability of wood materials.
2021 Panels Plus light gauge steel (LGS) framing station, builds steel stud wall panels from 6′-9″ to 16′-0″ heights, from 1′-0″ to 20′-0″ long. Includes four (4) Graber SuperDrive tools with mounts, two tools per dolly, adjustable top and bottom plate stops, squaring stops and pop up conveyors. 110 volt, 1 phase, 30 Amp electrical required. 80 PSI at 10 CFM air required. $71,993 NOW $59,000 FOB PA
• Pop-up Skatewheel Conveyor
• Powered Height Adjustment (6'-11" to 12'-5" wall heights)
• Fixed Squaring Stops
• Excludes Tool Dollies
• 110 Volt / 20 Amps
• Add $6,000 for Stud Locators at 16" & 24" O.C.
• Add $2,750 for 1 Pair of 15' Skatewheel Conveyor with Stands
• Add $11,900 for Sub-Component Layup Tables with Pop-up Skatewheel Conveyors
• EQUIPMENT FINANCING available from SLS Financial Services $38,750 FOB NE
2021 Panels Plus light gauge steel (LGS) framing station, builds steel stud wall panels from 6′-9″ to 12′-3″ heights, from 1′-0″ to 20′0″ long. includes four (4) Graber SuperDrive tools with mounts, two tools per dolly, adjustable top and bottom plate stops, squaring stops and pop up conveyors. 110 volt, 1 phase, 30 Amp electrical required. 80 PSI at 10 CFM air required.
$71,993 NOW $59,000
Reduced labor, increased safety, the benefits just keep stacking up. Stacking wall panels at the end of your production line can be a real labor-intensive and safety-challenging task. But it doesn’t have to be now, thanks to ProStack. This innovative wall panel stacker literally stacks from the bottom up, reducing awkward overhead lifting & placement, and the risk of head injury. Plus, ProStack frees up at least one worker to return more productively to your core task—building wall panels. Enhanced worker safety and productivity is what ProStack is all about.
Developed for commercial wall panel production facilities this is the remarkable ProStack, fully automated wall panel stacker. The ProStackrelieves your build team from creating a stack of wall panels and keeps them building walls instead. Stacks 2×4 through 2×8 walls up to 20′ in length and up to 12′ in height (taller by special order). The ProStack will automatically center or left or right justify each layer including multiple wall segments on the same layer. For ease of loading in your yard or on the build site, fork pockets are created in two ways: The operator can attach blocking up to 5″ tall to the last wall of the stack prior to entering the stacker, or two shorter walls can be spread apart prior to the second to last row of the stacker. Designed without any overhead frame or apparatus, so no crane inspections are required. The ProStack is “event driven”, so there is no need to read a file. Setup and installation is easy too, without the need for complex training or disruption to workflow. So free up your team to do what they do best, and you need to do most, and let ProStack stack your wall panels instead. ProStack can even operate with your existing powered conveyors or select our optional matching conveyors (see the video shown below). 208 volt, 3 phase, 43 Amp base model electrical required. No air required. Footprint is 26′-5″L x 19′-3″W.
By the MSR
Lumber Producers Council
In 1995, the MSR Workshop was born out of one man’s commitment to fulfilling what he saw as a real need to bring together those who produce MSR lumber, those who sell MSR lumber, and those who use MSR lumber, in order to develop a better understanding of each other’s challenges and share ideas to improve the supply chain. Thirty years later, as the MSR Lumber Producers Council prepares to welcome attendees to its 23rd Workshop, we are grateful for the vision of past leaders and the hard work of current members for continuing to plan this high-quality event.
The 2025 MSR Workshop will be held April 30 – May 2 at the Coeur D’Alene Golf & Spa Resort in Coeur d’Alene, Idaho. Participants will kick off the event with a golf outing, followed by educational and networking opportunities that include a tour of Mercer Mass Timber in Spokane Valley, Washington, and a sunset dinner cruise on shimmering Lake Coeur d’Alene.
“The last few years I have been on a mission to learn the lumber industry from all different levels and views,” says Adam DeBiasio of United Lumber Home Hardware Building Center, who attended his first Workshop last year in Charlotte. “I attended on the recommendation of a lumber supplier and the entire experience was valuable to me. I learned a lot – from the different presenters to the plant tour and just speaking with other participants.”
The Workshop committee has once again gathered a variety of knowledgeable speakers from across the supply chain to cover a range of important topics:
This session highlights the American Wood Council’s initiatives that promote wood carbon data collection and report, accounting for biogenic carbon in wood products, and the strategic use of wood products to decarbonize the built environment, showcasing their role in shaping a greener future for the industry at large. Rachael Jamison, who has served as AWC’s Vice President of Markets and Sustainability since 2021, will look specifically at the Environmental Product Declaration (EPD) program for solid sawn wood and provide an overview of the data collected and how the EPDs are created and used.
Get up to speed on the current state of the softwood lumber markets in Europe, including production levels and imports into the U.S., with Frank Turnbull from Mercer Timber Products. He will also look at how the war between Russia and Ukraine has affected the European lumber markets and what the future might hold for the U.S. market.
Duane Vaagen from Vaagen Bros. Lumber will examine how sustainable forestry techniques, such as selective logging and forest thinning, support both environmental health and the production of high-quality MSR lumber. He will discuss why small logs make better lumber, strategies for timber sales with MSR lumber in mind, and how product-focused logging practices contribute to the viability and efficiency of lumber mills.
WoodWorks, a non-profit organization that provides free project support, education, and resources related to wood design solutions of commercial and multi-family wood buildings, is actively initiating a significant and transformative change in the way buildings are designed and constructed. Senior Director Janelle Leafblad will explore the way in which she and her team accomplish this on a regional level as well as driving scale in the national marketplace.
Take a deep dive into the most recent MSR Production Survey with Crystal Gauvin from Forest Economic Advisors (FEA). Since the MSR Lumber Producers Council (MSRLPC) began tracking data in 1994, this annual production survey has become a valuable tool for both monitoring the progress of the industry in North America and promoting the use of MSR lumber worldwide.
FEA’s Crystal Gauvin will help you gain a clear understanding of the U.S. economic outlook and its impact on the wood products industry. She will provide answers to questions about where the U.S. economy is headed and how residential construction markers will fare, so that you can better anticipate the effects of inflation, interest rate fluctuations, and housing market
trends. In addition, Crystal will explore the future of lumber production in Canada and how timber supply constraints across North America could impact lumber markets in the year ahead.
Led by Dan Uskoski of Metriguard Technologies, this roundtable is a great way to revisit and ask questions about the valuable content from other sessions so you can depart with a plan to integrate it into your business plans.
In addition to the educational sessions, participants in the 2025 MSR Workshop will tour Mercer Mass Timber (MMT) in Spokane Valley, WA, which commenced production in August 2021. MMT produces cross-laminated timber (CLT) and glue-laminated timber (GLT) for the North American market at its three plants in Washington, Arkansas, and British Columbia. The roughly two-hour tour of this state-of-the-art facility generally follows the product’s flow through the factory, starting on the front end of the mill at the transverse high grader and sort bins, making its way through the production flow process, and finishing out at the post-CNC finished CLT panels/quality assurance lab. Attendees will enjoy a look at a variety of robust automation technology throughout the operation as well as one of the world’s largest CLT presses.
Last year, attendees traveled from as far as Sweden to participate. Mats Wedell from LIMAB AB in Göteborg, Sweden, says he attended the MSR Workshop “to learn more about the trend and need for MSR in North America.” He says he appreciated meeting so many experienced industry professionals and “valued the open and interesting discussions.” He and a colleague from LIMAB plan to travel to this year’s Workshop in Idaho to enjoy more learning and networking opportunities.
Full details and registration information are available on the MSRLPC website. The Early Bird Deadline is March 15, so register today and SAVE! To see a list of MSRLPC members or to join, please visit our website.
The MSR Lumber Producers Council (MSRLPC) represents the interests of machine stress rated lumber producers in the manufacturing, marketing, promotion, utilization, and technical aspects of MSR and MEL lumber. Suppliers, customers, and professionals may join as Associate members to enjoy:
• Online Marketing
• Networking Opportunities
• Reliable Market Data
• Education
“There is no question that the MSR Lumber Producers Council meetings are worth your time to attend. The information you will receive from the guest speakers and members of the Council is unparalleled!”
—Sean Kelly,
Automated Products Inc.
Lumber Waste Clean & organized Job sites
Reduce DumpSTER Fees
Global warming –why produce excess waste?
Speed. Efficiency. Cost Savings.
You can have it all with the EZWALL® Innovative Framing Solution™ from A-1 Industries. Our precision-cut, pre-labeled wall framing kits revolutionize construction, ensuring faster builds with minimal waste. Reduce on-site cutting and unexpected delays, and realize 20% faster cycle times than conventional framing methods. That means more homes and more profit for builders and framers.
2022 Peterbilt 579 S/A Day Cab Truck #1
Paccar MX-13 / 12.9L / 405 HP Engine
249,300 Miles / 5,566 Engine Hours Auto Transmission Engine Brake
12,000 Lb Front Axle / 22,700 Lb Rear Axle / 34,700 Lb GVWR Air Trac Air Ride Suspension
148 Inch Wheelbase Dual Fuel Tanks Tires are Very Good
$35,000 FOB PA Wasserman & Associates 800-382-0329
www.wasserman-associates.com
Reconditioned Lakeside 36'-51' Stretch Roll-Off Trailer
• Self-Contained Hydraulic Front End
• Sliding Tandems
• Roller Locks
• Headache Rack
• New Axles (Undercarriage)
• New Wheels, Tires & Brakes
• New Hydraulic System
• New Wiring & Light Sockets
• Sandblasted & Epoxy Painted
• DOT is Current $40,000 NOW $29,900 FOB ME
Wasserman & Associates 800-382-0329
www.wasserman-associates.com
2004 Pratt 42'-60' Stretch Roll-Off Trailer
• Hydraulic Front End
• Sliding Tandems
• Spring Suspension23900
• Roller Locks and Brakes
• Winches and Straps
• Headache Rack
• New Battery & Battery Tender for Hydraulic Unit
• Replaced 20 I-Beams in 2018/2019
• Replaced 2 I-Beam Crossmembers in 2022
• Replaced 2 Hydraulic Lift Cylinders in 2023
• Tires - Drivers Side: 1@14/32", 2 @12/32", 1@8/32"
• Tires - Passenger Side: 3@14/32", 1@8/32"
$23,900 NOW $21,500 FOB IN Wasserman & Associates 800-382-0329
www.wasserman-associates.com
2021 Big John Extendable Pole Truss Trailer
Extendable pole trailer
Used for 60' span roof trusses, peak down Retracted length - 35'. O.A.
Extended length - 45' O.A.
Adjustable 2' Increments
Outer tube frame - 8" square tube
Inner tube frame - 6" square tube
Axles - (2) 25,000 LB Capacity Each Axle width -102"
Anti-lock brake system
Parking brakes on both axles
Wheels - 10 stud outboard drums
Tires - 11 R 22.5 radials
Rims - 22.5 steel unimount (8) alum wheels
Suspension - Watson air ride with dump valve
Landing gear - 2 speed
Bumper - standard
Lights - DOT Specs, LED Package (2) truss stands (4) winches with straps
$29,900 NOW $23,900 FOB SC Wasserman & Associates 800-382-0329
www.wasserman-associates.com
1995 Pines 45' Chip Trailer
• Modified by LMI TENN
• 8" Floor Cross Members
• Reinforced Roof
• 22.5 Tubeless Tires
• Sl iding Tandem Axle (for weight distribution) (FOB PA) $9,900
Wasserman & Associates
800-382-0329
www.wasserman-associates.com
1997 Lakeside JDH Trussmaster
36-51 ft Stretch Trailer (OR-1)
1997 Lakeside JDH Trussmaster 36′51′ – Lakeside trailer features 5th-wheel connection, sliding tandem axle, locking rollers and hydraulic lift neck. Current DOT inspection September 2023. 50% brakes and 50% tire tread remains. 26,000 GVWR $28,997 NOW $21,997 FOB MO Wood Tech Systems 765-751-9990
www.woodtechsystems.com
axle, hydraulic lift neck, and ABS brakes, currently DOT certified with all lights working. Brakes have an estimated 50%+ life remaining, tires have an estimated 50%+ life remaining (no locking rollers). GVWR 68,000 lbs.
$27,850 FOB MI Wood Tech Systems 765-751-9990
www.woodtechsystems.com
Used - 2014, R157 48” Roll -Off
Precision Trailer
Tandem Axles | Air Ride Suspension : Air Operated Load Control, Air Operated Pin Locks | Mesh Between Rollers | Beaver Tail | Strap Locks and Winches | LED Lighting | 11.4 Ton Self Contained Power | (1) Heachache Rack
$17,500 NOW $12,500 Eide Machinery Sales, Inc. 612-521-9193
www.eidemachinery.com/equipment/ trailers
Used - 2014, R156 48” Roll -Off Precision Trailer
Tandem Axles | Air Ride Suspension : Air Operated Load Control, Air Operated Pin Locks | Mesh Between Rollers | Beaver Tail | Strap Locks and Winches | LED Lighting | 11.4 Ton Self Contained Power | (1) Heachache Rack
$17,500 NOW $12,500 Eide Machinery Sales, Inc. 612-521-9193
www.eidemachinery.com/equipment/ trailers
2015 JLG G10-55A Telehandler Lift
• 10,000 LB Capacity
• 55' Lift Height
•
•
•
•
•
•
•
2004 and 2005 Pratt 53' Roll-Off Trailers
Hydraulic Front End
Sliding Tandems
Roller Locks
Winches and Straps
Headache Rack
Tool Box
Several cross member have rust holes and need to be replaced
$12,500 Each or $24,000 for Both Trailers
Wasserman & Associates 800-382-0329 www.wasserman-associates.com
2022 Stoll 36-ft TrussTran
Gooseneck Truss Trailer (Red)
2022 Stoll 36′ TrussTran roll-off truss trailer, model STOT-2022, features remote control operation for hydraulic lift/tilt function, GVWR 10,896, integrated load straps, locking, split rollers for delivering roof truss up to 50′, floor trusses, and material packages. Has current DOT inspection in January ’25.
$41,997 FOB IN Wood Tech Systems 765-751-9990 www.woodtechsystems.com
1993 JDH Trussmaster 48'-70' Stretch Roll-Off Trailer
• Fixed Tandem
• Spring Suspension
• Roller Locks
• Winches & Straps
• Headache Rack
• Tires are Good (less than 5,000 miles on tires)
• DOT is Current
• Video available upon request
$19,900 NOW $13,900 FOB IN Wasserman & Associates 800-382-0329
www.wasserman-associates.com
1995 ASI 48'-70' Stretch Roll-Off Trailer
• Slanted Profile
• No Hydraulic Lift (has been removed)
• Fixed Tandems
• Spring Suspension
• New Landing Gear and New Springs/ Shackles on the rear axles within the last year
• Tires are Good (4 new tires in Summer of 2024)
• Roller Locks
• Headache Rack DOT is current (February 2025)
$12,800 FOB WI Wasserman & Associates 800-382-0329
www.wasserman-associates.com
2003 JDH TRUSSMASTER SIDEOFFLOADING TRUSS TRAILER
10,000 Lb Tandem Axles (Dual Wheels). 26,000 GVWR. Deliver Trusses Vertically. Stretch from 18' to 38'. Raise Loads Hydraulically. Air Brakes.
$6,900 FOB CA Wasserman & Associates 800-382-0329 www.wasserman-associates.com
2000 Haulin 36' Truss/Panel Roll-Off Trailer
• Bed Length: 36'
• GVWR: 26,000 Lbs
• Battery Operated Hydraulic Tilt
• Electric Brakes
• Locking Rollers
• Trailer Inspection is current
• One location needs steel plate/weld repair (reference photo)
$19,900 NOW $10,900 FOB PA Wasserman & Associates 800-382-0329 www.wasserman-associates.com
Used Precision 50’-70’ Stretch Trailer Tandem Axles | Air Ride Suspension, Air Operated Load Control, Air Operated Pin Locks | Mesh Between Rollers | Beaver Tail | Strap Locks and Winches | LED Lighting | 11.4 Ton Self Contained Power Unit | (1) Heachache Rack
$27,500 Eide Machinery Sales, Inc. 612-521-9193
www.eidemachinery.com/equipment/ trailers
2012 Precision Equipment
36' Gooseneck Roll-Off Trailer
• 10,000 Lb Tandem Axles with Dual Wheels
• Self Contained Hydraulic Lift
• Roller Locks
• Extra Roller on Gooseneck
• Electric Brakes
• Price in US Dollars
$29,900 FOB Ontario Wasserman & Associates 800-382-0329
www.wasserman-associates.com
Webb President, Webb Analytics
ne deal did all the difference in construction supply’s M&A world in 2024. The Home Depot’s purchase of SRS Distribution’s 769 locations turned last year into the most active year for LBM facilities acquired since at least 2018. But when you exclude that buy, 2024 turns out to be the slowest year for M&A this decade in facility terms and second slowest for number of deals. Greenfield openings also were slightly behind the pace set in 2022 and 2023.
The Webb Analytics Deals Database counts construction supply facilities where home builders or remodelers would be likely to shop for wood products and goods that generally go into the construction of the building envelope. It also counts hardware stores and similar places where remodelers and DIYers would go. Among these stores, we’ve seen 4,203 facilities acquired since 2018. Lumberyards and truss companies account for nearly a third of all acquisitions since 2018, followed by roofing and gypsum locations. For 2024 alone, The Home Depot’s purchase of SRS Distribution dramatically increased the share of facilities acquired that sold roofing, landscaping, and pool supplies. As for the 1,164 greenfield openings, hardware stores and roofing specialists made up half of the new stores between 2018 and 2024 and nearly two-thirds of the activity in 2024 alone. The flooring numbers belong almost exclusively to fast-growing Floor & Decor.
A total of 214 lumberyards and components facilities got new owners, opened anew, or were closed in 2024. Several longtime, well-known dealers sold out, most notably Colorado’s Alpine Lumber, New Mexico’s RAKS Building Supply, Minnesota’s Simonson Lumber, and Alabama and the Florida Panhandle’s Townsend Building Supply.
All told, 103 facilities were purchased, 32 had greenfield openings, and 13 were closed (often as part of consolidations into new yards). Contract Lumber bought three yards and opened four greenfield facilities. The biggest single acquisition of truss companies mainly involved Canada, when RONA bought All-Fab Group. Another sort of components operation—door shops—saw Foundation Building Materials buy the 15-unit United Door & Hardware.
The complete 2024 Deals Report is available as a free download online.
Webb Analytics is a data and research consultancy that helps executives in construction supply spot the trends, threats, and opportunities that matter most. It’s led by Craig Webb, one of the nation’s best-known industry figures and the former editor-in-chief of ProSales, the construction supply industries most honored publication. Aside from the annual deals report, Webb Analytics also produces the Construction Supply 150, consults with dealers, publishes research reports, and speaks at industry events.
& TRAILERS
2022 Stoll 36-ft TrussTran Roll-off
Gooseneck Truss Trailer (Black)
2022 Stoll 36′ TrussTran roll-off truss trailer (Black) STOT-2022, features remote pendant-control operation for hydraulic lift/tilt function, GVWR 10,896, integrated load straps, Locking, split rollers for delivering roof truss up to 50′, floor trusses, and material packages. Has current DOT inspection in January, 2025.
$41,997 FOB IN Wood Tech Systems 765-751-9990
www.woodtechsystems.com
2021 Big John Extendable Truss Pole Trailer
2021 Big John peak down extendable pole trailer. Transports up to 60′ peak down trusses with a retracted length of 35 ft. O.A., and an extended length of 45 ft. O.A. Adjustable in up to 2 ft. increments. Outer tube frame is 8″ sq. tub and inner frame is 6″ sq. tub. Features 2 axles with anti-lock brake system and parking brakes on both axles. Trailer features air ride suspension with dump valve and 2 speed landing gear.
$23,890 FOB NC Wood Tech Systems 765-751-9990
www.woodtechsystems.com
• Automated Wall Panel Parts Cutting & Marking as directed by Wall Panel Design Software Output
• 20' Roller Conveyor with Servo Motor Controlled Length Stop/Plate Pusher
• 10' Infeed Roller Conveyor
S
MiTek Blade linear saw, includes (5) lumber carts, (4) lumber magazines, overall beam length of 50-ft with end column supports, footprint of 50′ x 52′. Pick head is screw-type. Includes light-curtain perimeter beam, operator’s console, perimeter safety fencing and rails for carts.
$81,995
• 24" Lenovo Touch Screen Computer (Windows 11 Pro OS)
• ASI Bas ic L Plate Cutting/Marking Operating Software
• 4 Head Ink Jet Plate Marker (marks 2 plates on edge)
• 110 Volt / 1 Phase
• Includes Onsite Installation & Training
• Excludes Saw & Dust Collector
• Approximately $50,000 USD with DeWalt Sliding Miter Saw including Freight, Customs Brokerage Fees & Installation
• Other Saw Options Include: Existing Saws, ASI Radial Arm Saw, Lauderdale Hamilton Up Cut Saw & Vista Angle Boss Saws
• Video available upon request
EMSI Teeter Cart
Width – 46” / Length – 73” / Load Capacity
– 2850 pounds / Pneumatic tires – 14.5 inch / Maximum utility in truss plants, panel plants, and lumber yards / Quick Assembly by bolting parts together / All hardware is supplied / Upright 2 x 4’s not supplied / Medium duty tires rated at 1500 lbs each are included.
Call for Price
Eide Machinery Sales, Inc.
612-521-9193
www.eidemachinery.com
Used - Quincy 25 Horsepower Screw Compressors (2x)
Taken from service | Optional: Refrigerated Air Dryer - $500 $3500 each
Eide Machinery Sales, Inc. 612-521-9193
www.eidemachinery.com
Used MiTek Conveyors with Stands (30)
Total of (30) MiTek OEM conveyors, 14-ft long rollers (18 Idler / 12 powered) consisting of QTY (9) 4-inch rollers with stands, QTY (21) 5-inch rollers with stands, QTY (9) 120v motors, and QTY (3) 480v motors. (30) pairs of stands – (60) pcs total. All motors were operational when removed from service in November ’24.
$24,890 FOB GA Wood Tech Systems 765-751-9990 www.woodtechsystems.com
NEW GALVANIZED STEEL STRAPPING
1 1/4" wide x .035 thick. $95 per coil. $1,900 per skid (21 coils). FOB PA. Wasserman & Associates 800-382-0329 www.wasserman-associates.com
AMI's industrial floor trucks (material carts) are designed of hardwood construction, fitted with space-age phenolic, roller-bearing wheels, and ball bearing swivel casters for strength and durability. AMI's phenolic wheels resist shock without chipping. They are non-sparking, non-marking, and can be operated continuously between -50℉ and 260℉. They are unaffected by grease, oil or debris on your shop floor.
Our swivel casters are precision built with perfectly aligned raceways. All cold-form parts are made to exacting tolerances from heavy-gauge steel, and are hardened for severe service and long wear. Series B-4 carts include four casters, one at each corner, to prevent "tri-cycling" of long lumber loads.
Standard Models Available Max Load Weight (lbs.)
2748 27" x 48" Series "B" & "C" 2500
3248 32" x 48" Series "B" & "C" 2500
3260 32" x 60" Series "B" & "C" 2800
3660 36" x 60" Series "B" & "C" 2800
3672 36" x 72" Series "B" 4000
4072 40" x
3696
*Other models and sizes are available on request. FOB NC. Wood Tech Systems 765-751-9990 www.woodtechsystems.com
2005 Koorsen Connector Detector (For Repair or Parts)
6 detection zones to locate missing plates. Horn & zone lights indicate missing plates. 12" to 60" adjustable height from floor. 110 Volt / 1 Phase. New control panel switches & lights in 2014. Needs circuit board repair or replacement and new tower light. Includes 4 extra detection zone boxes.
$2,500 NOW $1,500 FOB NE Wasserman & Associates 800-382-0329
www.wasserman-associates.com
1996 Holtec Transcut II Electric Yard Saw
1996 Holtec Transcut II – Portable electric yard saw for pre-cutting bunks of lumber or EWP to length for processing. 10 HP motor, 460v, 3ph, 14.5 Amp, 60 Hz power, .404 pitch saw chain, extended electrical lead, auto-oiler, hard-rubber wheels, cuts 63” x 9mm kerf for processing up to 40″x44″ lumber bunks. Includes general purpose HD transformer for 230v > 460v service.
$6,890 FOB IN Wood Tech Systems 765-751-9990 www.woodtechsystems.com
•
•
•
Champion Valve Plus Compressor
2023 Atlas Copco Compressor in Container Housing
2023 Atlas Copco type G7FF rotary screw compressor with internal dryer and external tank. Compressor capacity is 145 PSI, has a 10 HP motor, external air tank includes bleed valve and manual output valve. System comes contained in a custom shipping container with locking entry door, thermostat controlled electric fans, throughwall induction vent grills, interior lighting, electrical panel and utilities for a second compressor. Container size is 8′ width x 10′-6″ long x 8′-8″ height. Hours as of 19 September ’24 were 986. 480 volt, 3 phase / 120VAC electrical required.
$34,490 FOB AZ Wood Tech Systems 765-751-9990 www.woodtechsystems.com
Champion Valve Plus – Reciprocating twostage compressor, model 7.5–V80E, with Eaton controls, 7.5 HP motor, 80 gal vertical tank, rated for 22 cfm @ 175 PSI. 208/230/ 460 volt, 3 phase electrical required.
$2,495 FOB AZ Wood Tech Systems
765-751-9990
www.woodtechsystems.com
2023 Triad Flow Through Component Nailer
• Assembles Trimmers, Partition Leads, Corners, Headers, Ells, Jack Studs
• Length Capacity: 10'-2"
• Clamp Opening: 3" x 3" to 12" x 12"
• Vertical & Horizontal Clamping Pressure: 300 Lbs at 100 PSI
• Foot Pedal Control
• On/Off Switches for Each Nail Gun
• Pop-Up Stop
• Nail Trays
• 10' Infeed & 10' Outfeed Roller Conveyor with Stands
• Excludes Nail Guns
$19,900 FOB ON Wasserman & Associates 800-382-0329
www.wasserman-associates.com
• 2 Each - 35' Span Gantry Bridges with 1 Ton Harrington Electric Hoists
• 20' Height
• Internal Electric Bus Bar (eliminates festoon system) $45,000 NOW $35,900 FOB AZ
Alpine Lumber Carousel
• 7 Bunk Capacity (up to 12' Lumber)
• Pushbutton Control Station
• 10 HP / 3 Phase Motor
• In working condition when removed in August 2023
$11,900 FOB Manitoba Wasserman & Associates 800-382-0329
www.wasserman-associates.com
2002 Atlas Copco Rotary Screw Air Compressor
• Model GX11FF
• 15 HP Rotary Screw Air Compressor (230/460 Volt - 3 Phase)
• 13,443 Hours
• 51.7 CFM at 128 PSI
• 80 Gallon Tank
• Built-in Air Dryer does not work
• Includes separate 2012 Pneumatech AD-50 Air Dryer (1 Phase)
$4,250 FOB TX Wasserman & Associates
800-382-0329
www.wasserman-associates.com
Improved model ProDirector 7, green-color laser projection system from SL-Laser. Projects roof truss, floor truss and wall panel design images accurately onto building surface for faster setup and fabrication times. New employees are productive more quickly, with less training required. Each laser head provides 21′ projection length (at 15-foot ceiling heights). New model PD7 projector heads are smaller in size than previous models, have diodes that are easier than ever to swap out and maintain, and project an even clearer line onto the building surface. System includes projector heads, cables, mounting hardware for attachment to customer’s structure, factory installation, training, and options for computer controls. Works with each connector plate manufacturer’s design software. Modular nature of the laser heads allows for easy future expansion of system length. 120 volt, 1 phase.
FOB NC
Wood Tech Systems
765-751-9990
www.woodtechsystems.com
New Monet Power Deck Infeed Decks
Heavy-duty, 5-chain feed system to bring material to the infeed of the component saw. 16′ wide x 20′ long x 36″ high. Transfers 6′ to 20′ lumber lengths. Option for 6-arm Power Deck available at an additional cost. Features auto-feed advance, foot pedal override forward and reverse, variable speed control, double bearing construction, softstart and soft-stop and e-stop cable. Base price shown. 480 volt, 3 phase, 15 Amp electrical required. (Prices start at $31,000.)
Wood Tech Systems
765-751-9990
www.woodtechsystems.com
Electrical Supply: 110 VAC
Motor: 1/4 HP, 110 VAC, Linear Actuator
Highly Accurate: +/- .010 Inches
Stop Rail: 2 x 4 x 1/4 Aluminum Extrusion
Stops: Jig Bored Steel
Stop Blocks: Machine Billet Aluminum
Internal Components: Hardened, Ground and Polished Steel and Billet Aluminum
Dimensions:
Length: 5 feet (60”) to 60 feet (720”)
Height: 12 inches
Depth: 12 inches
If you are looking for the fastest, most consistent way to measure and cut your product, then the Hain Measuring System (MEA) is your answer. The MEA changes from one length t any length instantly, up to 60’, without changing the operator’s position on the line. It is also highly accurate (+/- .010) and quickly moves from one length to the next in seconds. The MEA is designed for quick and easy setup and is simple to use. Even a first time user will be productive with little or no training required. It can adapt to any saw and can be mounted to any surface so that you can integrate the MEA with your existing setup. The MEA is versatile allowing “left” or “right” handed operation and measurement in “feet and inches” or “inches” depending on your preference. The MEA is also available in a “Skid Mounted” version.
BAM “Ovation”
Door Machining Center (DMC)
New Builders Automation Machinery
“Ovation” series, door machining center (DMC). Fully programmable, two-stage door machine featuring (27) axes of operation. Can be specified with either two or four front machining heads. Machine is side-eject, direct-drive with helical gear racks and gear protection from dust. The door loader is driven by an absolute encoder; no stepping motors, belts or exposed ball screws are used.
More information Click Here
Price based on configuration Wood Tech Systems
765-751-9990 www.woodtechsystems.com
Since 2006, we've been helping businesses of all kinds build their online presence. We make websites and software for the construction industry to empower companies to reach a wider customer base and engage their audiences. Companies all around the world work with us to make websites and apps that people actually want to use. Reach out to Wolf X Machina if you're a business and you want a website that actually drives results.
Builders Automation
Machinery (BAM) door loader, model 2001. Allows you to stack door slabs horizontally and feeds them into a horizontal door machine like the BAM model 996E-TS. Mechanically adjusts door stack height vertically as slabs are fed into machine. Clamp automatically adjusts to type and size of door slab: steel, solid-core or hollow-
manages the
By MiTek Staff
n 2024, the MiTek Building & Product Regulations team completed a tri-annual project to update all MiTek structural product evaluation reports to establish compliance with the new 2024 I-Codes. Building codes in the U.S., also known as the I-Codes, are developed on a 3-year cycle. Each building code edition may introduce new technical requirements based on revised referenced standards. States and local jurisdictions in the U.S. will begin adopting and enforcing the 2024 I-Codes over the coming months and years, depending on their adoption schedules and amendment processes.
MiTek maintains a comprehensive portfolio of over 30 structural product evaluation reports, fire listings, environmental product declarations, and over 50 city and state supplements, addressing code compliance for thousands of products. The Building & Product Regulations team worked closely with the two primary building product certification bodies, ICC Evaluation Service (ICC-ES) and IAPMO Uniform Evaluation Service (IAPMO UES), to update our reports to the requirements of the new 2024 International Building Code® (IBC) and 2024 International Residential Code® (IRC).
MiTek is now fully prepared for adoption and enforcement of the new 2024 IBC and IRC, with code-compliant evaluation reports for our Metal Truss Connector Plates, Posi-Strut Metal Webs, Lateral Systems, Structural Connectors, Ultra-Span Truss Sections, and Triton Board products. MiTek is committed to maintaining up-to-date evaluation reports, creating new reports as new MiTek structural products are developed, and providing technical training for building officials and design professionals; and the MiTek Building & Product Regulations team’s experts in codes and standards diligently ensure that MiTek’s code reports remain in continuous compliance to meet future building code and standard development cycles.
In 2024, the Building & Product Regulations team also worked to improve the MiTek website evaluation report directory, organizing and uploading our current evaluation reports, listings, and Environmental Product Declarations (EPDs), including the subjects for each report. This makes it easier for building officials, design professionals, and builders to find the critical information they need.
Specifiers and building officials are encouraged to review the entire product evaluation report. The issue date and the building code edition to which the products have been evaluated should all be current. Our updated Evaluation Reports and Environmental Product Declarations can be found in Services – Engineering – Evaluation Reports and Fire and Acoustic reports are available in Services – Engineering – Engineering Details on the MiTek website, www.mitek-us.com
For additional information, or if you have questions, please contact the MiTek Building & Product Regulations team or the MiTek Engineering department.
• Sources for MSR Lumber
Filter by species, grade and dimension to locate products from MSRLPC members.
• Educational Resources
Find helpful information for current and potential MSR lumber users.
• NEW! Design Values
Comparison Tool
Compare MSR lumber reference design values with visually graded dimensional lumber by species. The MSRLPC website is a
to make informed purchasing decisions as well as those exploring design optimization with MSR Lumber. Check it out!
Builders Automation Machinery (BAM) model 2220, stair wedge saw station automatically produces wood wedges used to lock stair treads and risers into slots cut into the stair stringers…
Price based on configuration FOB FL
765-751-9990
www.woodtechsystems.com
BAM Pre-Hung
Door Machine
Titan Series
Builders Automation
Machinery (BAM) Titan series pre-hung door machine. Designed to produce between 150 and 250 doors per day. Multi-function door machine capable of doors 1′-6″ to 4′-0″ in width, and both 6′-8″ or 8′-0″ door heights. Processes both 1 3/8″ and 1 3/4″ thick door slabs. Machines the door, hinge jamb and strike jamb all at the same time. Capable hinge sizes include 3 1/2″ x 3 1/2″, 4″ x 4″, 4 1/2″ x 4 1/2″ with 5/8″ radius. Cycle time with flush hinge routing is 45 seconds. 10′ long x 7′-6″ wide footprint. Shipping weight 4,000 lbs.
More information Click Here
Price based on configuration
765-751-9990 www.woodtechsystems.com
BAM Staircase
Assembly Clamp
Builders Automation
Machinery (BAM) staircase assembly clamp, model 2210, accommodates up to 20 foot long stringers with a maximum width of 54″…
Price based on configuration FOB FL
It takes all the right players to build a winning team. That’s why Simpson Strong-Tie provides truss and component manufacturers with a broad selection of versatile hardware products. Choose our code-listed truss connector plates, framing angles and straps, heavy-duty girder hangers and holdowns for strength and durability. Secure them with speed and ease using Strong-Drive ® structural fasteners, along with our Titen HD ® heavy-duty screw anchor and other mechanical anchors. Along with software, cutting equipment and professional design services, our hardware is widely available and backed by expert support. Learn more at go.strongtie.com/cs or contact your sales representative.
By Simpson Strong-Tie Staff
plift reactions are the result of a set of conditions that generally includes load types, load combinations, bearing locations, and web patterns. In most cases, especially those involving wind load combinations, uplift reactions are relatively small and can easily be resolved through the specification of standard Seismic and Hurricane Ties, such as Simpson’s H2.5A. In other cases, such as drag load combinations, uplift reactions can be relatively or extremely high (> 10,000 lbs). Furthermore, gravity load combinations in conjunction with interior bearings that are relatively close to an exterior support can create high uplift reactions that require additional design considerations: the allowable loads for Simpson’s Seismic and Hurricane Ties, as well as Girder Tie-downs, are based on a 1.60 Load Duration Factor, and specifying tie-downs for a gravity uplift condition requires that the duration of load associated with the load combination creating the uplift condition be taken into account.
Alerting the truss designer that a high uplift condition exists during the design phase of the component may have benefits. In some cases, the design can be altered to alleviate the high uplift condition. And, if the component design cannot be changed to alleviate the high uplift condition, the truss designer can alert the Building Designer or EOR that the condition exists and that additional design considerations may need to be accounted for when specifying a connection; this is especially true if a high uplift reaction occurs at a hanger support.
Options to control uplift may be set in EnvData and applied to individual bearings in the Bearings dialog. This functionality allows designers to adjust truss designs to alleviate uplift reactions at bearings.
The sample truss shows the EnvData option set to True. Uplift reactions are reduced at the interior wall bearings.
Additional benefits of uplift functionality include:
• Choose where required connections for uplift will exist:
o Adjust uplift for selected bearings
o Adjust uplift for continuous bearing trusses
• Allows the truss to deflect upward, instead of being anchored to the support, for any load combination where uplift would otherwise occur.
Simpson Strong-Tie’s Component Solutions® CS Truss Studio™ software has the ability to manage uplift reactions. Contact your Simpson Strong-Tie Representative or email CSHelp@strongtie.com for more information.
Copyright © 2025 Simpson Strong-Tie Company Inc. All Rights Reserved
Inspired by ten years of intensive field experience and the ample and detailed feedback of numerous customers, we’re pleased to introduce the most advanced, most enhanced and high-performance Terminailer yet-Terminailer V.8. Drawing on invaluable time in the trenches closely evaluating Terminailer’s performance under varying conditions, our engineers have incorporated critical learning and insight to enhance simplicity, performance and operator control. Just part of what V.8 offers includes:
•Vastly enhanced operator control for even greater productivity
•A redesigned nail-feed supplying EverWin PN90-PAL industrial nail guns
•Simplified pneumatics featuring direct air-supply to all six nail guns
•Even more sub-component profiles for wall design flexibility
•Rugged durability with pharmaceutical grade assembly
Developed by people who know well the mechanics, safety considerations and business aspects of wall-panel production, Terminailer V.8 combines more enhancements & operator-friendly features than ever to take your productivity to the next level and beyond. Contact us to learn even more and to put the V.8 performance in motion at your facility.
Back injuries account for about one in every five job-related injuries in California workplaces. Disabling back injuries are no laughing matter for workers who lose time from work or from personal activities. The sad truth is that most of the pain and lost time can been prevented if you are aware of how the back functions and how to lift safely to protect your back.
The back is a network of fragile ligaments, discs, and muscles which can easily be thrown out of order. The back’s complex design breaks down when it’s forced to perform activities it was not designed to do. Lifting with the back twisted or bent just begs for a pulled muscle or ruptured disc. One sure way to risk injuring the back is to lift heavy or bulky loads improperly or unassisted. Never be afraid to ask for help with loads that you know you cannot lift safely. Lift with good sense and a little extra help from a co-worker or mechanical aid when necessary.
If you decide you are capable of lifting a light load, make sure you lift correctly.
• Move in so that your feet are close to the base of the object to be lifted.
• Face the object squarely. Bend your knees and squat over the item to be lifted. In this position, the back gets added lifting strength and power from the legs and arms.
Las lesiones de la espalda constituyen una de cada cinco lesiones relacionadas con el trabajo en California. Las lesiones a la espalda que resultan en incapacidad no son chiste para los trabajadores que pierden horas de trabajo o de actividades personales. La triste verdad es que la mayoría del dolor y el tiempo perdido pueden evitarse si se sabe cómo funciona la espalda y cómo levantar de forma segura los objetos pesados para protegerse la espalda.
La espalda es una red frágil de ligamentos, discos y músculos que pueden lastimarse con facilidad. El diseño complejo de la espalda deja de funcionar correctamente cuando se le fuerza a ejecutar actividades para las cuales no ha sido diseñada. Levantar objetos pesados con la espalda doblada es una forma fácil de estirarse un músculo o romperse un disco de la columna vertebral. Una manera sin falla de lastimarse la espalda es levantar un objeto pesado o voluminoso incorrectamente o sin ayuda. Nunca tenga temor de pedir ayuda para levantar objetos que usted sabe que no es capaz de levantar en forma segura por sí solo. Levante los objetos pesados aplicando el buen juicio y con la ayuda de un compañero de trabajo o ayuda mecánica cuando sea necesario.
• Move up close to the item, because the backbone must act as a supporting column, and it takes the least strain close in.
• Tilt the item on edge with its long axis straight up so that the center of the weight is as high as possible above the ground.
• Still squatting, the feet should be set with legs pointed right at the load, with the back straightened, the worker may then grasp the load with both arms and slowly stand up with it, pushing up with the leg muscles. If you can’t lift slowly, you can’t lift safely.
A good way to learn the right from the wrong way to lift is to practice lifting correctly a few times. You will notice that the correct way to lift is the easiest way to lift the load, with the least strain and awkwardness. To lift the wrong way will, over time, cause injury and pain. The back can be damaged quickly but can take a long time to heal.
The above evaluations and/or recommendations are for general guidance
based solely on the information provided to us and relate only to
implied, that your workplace is safe or healthful or that it complies with
Si usted decide que es capaz de levantar una carga ligera, asegúrese de levantarla de la forma correcta.
• Colóquese de manera que tenga los pies cercanos a la base del objeto a levantar.
• Sitúese directamente de cara al objeto. Doble las rodillas y haga cuclillas sobre el objeto a levantar. En esta posición, la espalda recibe la potencia de izar adicional que le brindan las piernas y los brazos.
• Colóquese cerca del objeto, porque la columna vertebral debe funcionar como una columna de apoyo, y estando cerca del objeto recibe menos esfuerzo.
• Gire el objeto hasta tener el eje longitudinal vertical para que el centro de gravedad esté lo más alto posible sobre el suelo.
• Aún de cuclillas, los pies y las piernas deben estar apuntando a la carga, con la espalda recta, el trabajador debe sujetar la carga con ambos brazos y pararse lentamente, haciendo la fuerza con los músculos de las piernas. Si no se levanta lentamente, no se está levantando de manera segura.
Una buena manera de diferenciar entre el método correcto y los incorrectos de levantar es practicar la forma correcta varias veces. Observará que con el método correcto es más fácil levantar la carga, con el menor esfuerzo y menos torpeza. Con el tiempo, el levantar objetos pesados incorrectamente puede ocasionar lesiones y dolor. La espalda se puede lastimar en un instante y tomar mucho tiempo para sanar.
March 2–4
Multifamily Executive (MFE) Leadership Summit Vail, CO
March 4–6 Ace Hardware Spring Convention San Antonio, TX
March 5–6 2025 Lean Summit Atlanta, GA
March 5–7
Southeastern Lumber Mfr Assoc (SLMA) 2025 Spring Meeting & Expo Savannah, GA
March 6–8 Lumbermens Merchandising Corp (LMC) Annual Meeting Phoenix, AZ
March 10–12 LBM Advantage 2025 Annual Buying Show Lake Buena Vista, FL
March 10–13
March 11–13
North American Wholesale Lumber Association (NAWLA) University of Innovative Distribution Indianapolis, IN
Structural Building Components Assoc. (SBCA) & National Framers Council (NFC) Open Quarterly Meeting (OQM) Charleston, SC
March 13–14 American Institute of Building Design (AIBD) Design & Build North Myrtle Bch, SC
March 17–21 Southern Pine Inspection Bureau (SPIB) Spring Training Pensacola Beach, FL
March 18–20 National Hardware Show 2025 Las Vegas, NV
March 21–23 Do it Best Spring Market Orlando, FL
March 21–23 True Value Reunion 2025 Orlando, FL
March 25–27 Atlantic Builders Convention (ABC) 2025 Atlantic City, NJ
March 25–28 2025 Global Forest Investment Conference Luxembourg City, LUX
March 26–27 PA Housing Research Center (PHRC) Housing Conference Harrisburg, PA
March 27–29 JLC LIVE Residential Construction Show Providence, RI
Mar 27 – Apr 3 BUILD25: AWCI Convention + Expo Charlotte, NC
April 2–4
April 2–4 Natl Frame Bldg Assoc (NFBA) Annual Conference & Expo
April 7–10 Modular Bldg Institute (MBI) World of Modular Conference & Tradeshow Las Vegas, NV
April 8–10 AGC—The Construction Assoc. Annual Convention Columbus, OH
April 9–11 Structural Engineering Institute (SEI) Structures Congress Phoenix, AZ
April 16–17 Virginia Tech Short Course: Structural Design of Wood Structures Blacksburg, VA
April 27–30 LBM Advantage NextGen Leadership Conference 2025 Grapevine, TX
April 27–May 2
North American Wholesale Lumber Assoc. (NAWLA) Executive Management Institute (EMI) Evanston, IL
May 5–7
May 6–7
May 19–21
Builder 100 Leadership Summit Dana Point, CA
Engineering News-Record (ENR) FutureTech 2025 San Francisco, CA
Building Innovation Conference 2025 McLean, VA
May 26–30 LIGNA 25 Hannover, Germany
May 27–30
University of Texas Building Professional Institute (BPI) Irving, TX
June 4–6
June 4–7
June 8–10
June 10–13
June 10–13
Structural Building Components Assoc. (SBCA) & National Framers Council (NFC) Open Quarterly Meeting (OQM) Washington,
American Institute of Architects (AIA) Conference 2025 Boston, MA
Groundbreaking Women in Construction (GBWIC) Conference San Diego, CA
National Assoc. of Home Builders (NAHB) Spring Leadership Meeting & Legislative Conference Washington,
Pacific Coast Builders Conference (PCBC) Anaheim, CA
June 22–26 World Conference on Timber Engineering (WCTE) Brisbane, Australia
Don’t see your event? Increase attendance and participation by listing your industry focused events here! E-mail details and event web-link to Anna@componentadvertiser.org. We can’t guarantee space for all events, but all industry related events will be added on a space available and interest to our reader priority.
The truss industry relies on 3rd party quality assurance services to provide random visits to review the plants Quality Assurance program along with their operations. If your plant needs to comply with the IRC, IBC and to those who depend on solid, experienced QA expertise, we ask you to consider selecting Timber Products Inspection, Inc. (TP) as your choice for 3rd party inspections.
Proudly serving the forest products industry for over 50 years, TP brings the expertise you need to ensure your business is successful. As a responsible partner, TP delivers to clients, employees, and the industries we serve the confidence to drive value through the effective use of our diverse professional team.
TP would like to welcome the following authorized agents to our inspection team, each of whom have many years of experience in the truss industry!
• Al Coffman
• Jean Hart • Curt Holler • Chuck Ray
Glenn Traylor • Elliot Wilson
If you have questions about how you can make this selection, please contact your authorized agent above or Glenn Traylor at 919-280-5905 or trusguy@gmail.com. https://www.tpinspection.com/ https://www.tpinspection.com/auditing-services/truss
4x10
Are you a skilled Truss Designer or Wall Panel designer seeking a better work-life balance? Look no further! Our client is offering a unique opportunity for talented designers like you to thrive in an environment that respects your personal and professional needs.
In this position, you'll have the flexibility to choose from various working arrangements to accommodate your lifestyle. Some of our employers offer a 32-hour workweek with full benefits, allowing you to strike a perfect balance between your career and personal life. You can work in the office, remotely, or in a hybrid setup, depending on your location and skill level.
More Details Here
Measures 9 areas of Skills and Experience Compairs Results to National Averages Identify Strengths and Areas For Improvement
$145 per Exam (Volume Discounts Available)
Test your design team to have a better understanding of individual strengths and areas for improvement.
Use your team's results to measure potential new hires!
Truss Designer J15357
East Texas
Remote Multifamily Truss Designer J15356
Texas
Sales Representative - J15355
Central Ontario
Truss & Wall Panel Designer J15226
Northeast
Remote Truss Designer J15307 Full Time Remote
Truss Production Manager-J15354
Greater Toronto Area
Truss Designer - MiTek - Remote or OS J15312
Florida, AL, or GA for Remote
Remote Truss Designer - Alpine J15246
Midwest Candidate preferred
Senior Truss & Wall Panel Designer - MiTek J15352
Midwest
Remote Truss Designer - Alpine Software J15350
Remote
CFS Truss Designer | Wall Panel Designer J5323
Midwest
Outside Sales - Truss/Lumber J15345
Southeast
Truss Designer - On-site - MiTek J15346
Florida
Truss Designer J15348
South
Senior Truss Designer - J15342
Mountains
Remote Truss Designer J15313
New England
Truss Designer J15339
New England
Project Coordinator J15272
TN
Remote Truss Designer - MiTek J15228
Florida
Truss Designer J14165
Carolinas
Implementation and Support Specialist J15306
100% Remote - Northeast
Software Territory Sales Representative – Component Manufacturers J15336
Kansas, Missouri, Oklahoma, and Northern Arkansas Territory
WE WORK WITH OVER 100 LOCATIONS IN THE UNITED STATES AND CANADA SOME ARE HIRING NOW AND SOME ASK US TO CALL WHEN QUALIFIED CANDIDTES ARE AVAILABLE
WE RESEARCH OPPORTUNITIES FOR YOU! Strictly CoNfidENtial!
ID: C18426
Remote Truss Designer
Relocation: Colorado, Illinois, Indiana, North Carolina, South Carolina, Texas, Utah, Maryland, Florida, Georgia, Nebraska, REMOTE, Costa Rica, Pennsylvania, Tennessee, Virginia, Wisconsin, Wyoming, Washington DC, Rhode Island, Saskatchewan, Oregon, Ontario, North Dakota, New York, New Mexico, New Jersey, New Hampshire, Nevada, Montana, Mississippi, Minnesota, Massachusetts, Kentucky, Delaware, Conneticut, California, Arizona, Alaska
Offshore Truss Designer with MiTek experience. The candidate is a civil engineer with 6 years' truss design experience for companies in Texas and Florida. Prior work for BFS and smaller manufacturers. Bilingual Spanish/English with a company set up to make paying easy. Scored 89 on our truss design skills evaluation, which is near the senior designer level. He is also SBCA I & II certified. He is willing to go to work immediately.
Compensation: $65-75k as a subcontractor, no benefits or taxes.
We haven't represented offshore candidates in the past but feel this candidate is worth a shot. Please contact Thom for additional details.
ID: C18549
Remote Wall Panel Designer
Relocation: USA - ALL States Wall panel designer with 10 years' experience including production builders, single family custom and small to MegaMultifamily projects. MiTek Sapphire software experience.
ID: C18836
Truss Designer / Wall Panel Designer / Design Manager
Relocation: USA - ALL States Intermediate level designer with wall and roof truss design skills using MiTek software. Candidate has both MiTek Sapphire Structure and Management, plus AutoCAD experience. Products include wall panels, roof and floor trusses for single family custom, tract, and small commercial/ multifamily projects. Estimating roof and floor trusses, with my speed I could keep about 7-9 new projects a week
ID: C10122
Designer/Design Manager - Truss Relocation: Iowa
Senior Designer. - Advanced. Candidate has 24 years Truss Ddesigner experience and 5 years Truss Design Manager experience. Products include floor trusses, roof trusses, I-Joists, and hardware. Markets include single family, custom, high end, multi-family, light commercial, and agriculture. Primary duties include design, layout, optimization, cutting/production documents, and takeoff.
Secondary duties include checking others work, repairs, customer service, inside sales, software maintenance, training, and filling in for the Design Manager as needed. Software experience includes MiTek and Keymark. Training received includes WTCA Level 2. Education: High School Graduate and Batchelors degree.
Motivating factors: advancement, compensation, benefits, work location, job security, and relocation.
ID: C18604
Truss Designer - Remote (MiTek) Relocation: Alberta
I currently design & layout roof trusses, floor trusses, I-Joists and EWP from PDF plans and specifications for pricing. Also does engineering using MiTek, then uploads to Management or MBA in the past. Once sold, and field measurements are provided, I update the project and clean up the layouts, trusses and release them to the shop. I also answer questions from sales and the shop as needed as well as training newer designers. Most of my projects are single family, but I have also done several apartments, hotels, assisted living centers, and other commercial projects. I want to grow, learn, and become a better designer to be a valued team member.
ID: C10968
Senior Wood Truss Designer - Part Time Relocation: Florida, Alabama, Georgia, REMOTE
Candidate desires to use his career long industry experience to be the best Part Time Remote Designer you have. Prior truss plant owner for 10 years, strong production and operations management background, and JobLine Senior Designer rating in truss design using MiTek software. Also has FASTBeam experience. Products: floor & roof trusses. Markets: Single family custom, multi family, tract and light commercial. Was successful in creating strong teams in production, design and customer service, but the local economy and overwhelming competition was more than he could overcome from a small plant perspective. Degree: BSEE
Compensation: Based on employee or 1099 status.
Thom's Notes: I have worked with this candidate as an employer for years. Very detail oriented. Fair, honest, and customer service oriented. Very design/liability conscious. Scored 98
ID: C10853
Remote Design Manager | Remote Offshore Design Project Manager Relocation: Texas, Georgia, USA - South
Top level Engineering/Design Management candidate, 14+- years experience Truss, 4+- Panel experience. Has experience
building and integrating offshore design resources with internal design departments and training design managers to better utilize offshore capabilities. Large volume manufacturer experience. MiTek Sapphire design/layout proficient. Too confidential to go into more detail.
Compensation: $120k+
ID: C11370
General | Plant Manager/Operations - Truss/ Panel/Framing Package Relocation: Texas, Arizona
20 years' experience. Started in production, advanced to Saw Supervisor, Production Manager, Plant Manager, now General Manager. As General Manager operated a $125M truss plant. Tripled output and reduced errors and labor cost. Developed and implemented standards and procedures to manage quality and costs. As Plant Manager (4 years), manage all the operation of the manufacturing plant, such as Productivity, logistics, efficiencies, costs. As Production Manager (12 years), manage all the areas of the manufacturing across the plant. Safety, quality control, efficiencies, HR, etc... Software: MiTek, Word, Excel, OptiFrame. Products: R & F Truss, Panel, Framing package. Markets: Single Family, Multifamily, Custom Homes. Bilingual English/Spanish spoken and written. Degree in Industrial Engineering.
Compensation: $90's+ bonus ($100k min)
ID: C10897
Design Manager/Senior Designer/PE/ Optimizer - Truss/Panel/EWP Relocation: REMOTE
30 year industry veteran, started as a Truss Designer, earned his way to Design Manager over 20+ designers. MiTek - Advanced, AutoCAD proficient. BSCE - PE.
Compensation: Open??
Thom's Notes: PE with Mid Atlantic seals
ID: C18565
Designer: Truss/Panel, Wood/Steel, BIM Relocation: North Carolina Material take-offs, proposals, job-site meetings, Submittal Tracking, Excellent Problem-solving Skills, Material Ordering, Field Measuring, 3-D Modeling Program (3-D and 4-D BIM in-house), Generated material take-offs from the BIM model, Coordinated RFI's thru the BIM model, Clash detection between wood trusses, structural steel and LVL's. 3-D Scan's of job-sites. Scheduled / Distributed work to 6 designers Cross-trained all designers in roof floor and wall panels for whole-house design.
ID: C18370
Plant | Location | General Manager - Truss/ Panel
Relocation: California, Nevada
Highly experienced (20+ years) roof and floor truss, and wall panel manufacturing manager. Started in the plant as builder, then sawyer, supervisor, truck driver, maintenance manager, designer, outside sales, plant manager, operations manager, and general manager. OSHA trained, developed and implemented safety programs. Successful turn around experience, hands on ability to work with departments to combine individual strengths into one team effort, lower costs, and meet quality and volume expectations. Past experience negotiating better vendor programs to lower costs and improve inventory turns.
ID: C10507
Senior Management - Truss/Panel/Lumber/ Installed Services
Relocation: USA - Western
I am a Diverse driven individual seeking a position in the fast paced construction component industry where my professionalism in sales, business and leadership skills along with a strong proven background in, General Management, Operations, Sales Management, strategic alliances, business development, team building, P&L experience and Customer Satisfaction will play an integral part in growing new business, nurturing existing business or developing company operations to meet the highest level of efficiencies, standards and safety while having fun doing it!
Posted February 18, 2025 on NAHB Now | The News Blog of the National Association of Home Builders Reprinted with permission.
Builder sentiment fell sharply in February over concerns on tariffs, elevated mortgage rates and high housing costs.
Builder confidence in the market for newly built single-family homes was 42 in February, down five points from January and the lowest level in five months, according to the National Association of Home Builders (NAHB)/Wells Fargo Housing Market Index (HMI) released today.
“While builders hold out hope for pro-development policies, particularly for regulatory reform, policy uncertainty and cost factors created a reset for 2025 expectations in the most recent HMI,” said NAHB Chairman Carl Harris, a custom home builder from Wichita, Kan. “Uncertainty on the tariff front helped push builders’ expectations for future sales volume down to the lowest level since December 2023. Incentive use may also be weakening as a sales strategy as elevated interest rates reduce the pool of eligible home buyers.”
“With 32% of appliances and 30% of softwood lumber coming from international trade, uncertainty over the scale and scope of tariffs has builders further concerned about costs,” said NAHB Chief Economist Robert Dietz. “Reflecting this outlook, builder responses collected prior to a pause for the proposed tariffs on goods from Canada and Mexico yielded a lower HMI reading of 38, while those collected after the announced one-month pause produced a score of 44. Addressing the elevated pace of shelter inflation requires bending the housing cost curve to enable adding more attainable housing.”
The latest HMI survey also revealed that 26% of builders cut home prices in February, down from 30% in January and the lowest share since May 2024. Meanwhile, the average price reduction was 5% in February, the same rate as the previous month. The use of sales incentives was 59% in February, down from 61% in January. Derived from a monthly survey that NAHB has been conducting for more than 35 years, the NAHB/Wells Fargo HMI gauges builder perceptions of current single-family home sales and sales expectations for the next six months as “good,” “fair” or “poor.” The survey also asks builders to rate traffic of prospective buyers as “high to very high,” “average” or “low to very low.” Scores for each component are then used to calculate a seasonally adjusted index where any number over 50 indicates that more builders view conditions as good than poor.
All three of the major HMI indices posted losses in February. The HMI index gauging current sales conditions fell four points to 46, the component measuring sales expectations in the next six months plunged 13 points to 46, and the gauge charting traffic of prospective buyers posted a three-point decline to 29. Looking at the three-month moving averages for regional HMI scores, the Northeast fell three points in February to 57, the Midwest moved two points lower to 45, the West edged one-point lower to 39 and the South held steady at 46.
HMI tables can be found at nahb.org/hmi. More information on housing statistics is also available at Housing Economics PLUS
Posted February 19, 2025 on NAHB Now | The News Blog of the National Association of Home Builders Reprinted with permission.
Constrained housing affordability conditions due to ongoing, elevated interest rates led to a reduction in singlefamily production to start the new year.
Overall housing starts decreased 9.8% in January to a seasonally adjusted annual rate of 1.37 million units, according to a report from the U.S. Department of Housing and Urban Development and the U.S. Census Bureau.
The January reading of 1.37 million starts is the number of housing units builders would begin if development kept this pace for the next 12 months. Within this overall number, single-family starts decreased 8.4% to a 993,000 seasonally adjusted annual rate; the January pace was 1.8% lower than a year ago. The multifamily sector, which includes apartment buildings and condos, decreased 13.5% to an annualized 373,000 pace.
“As mirrored in our latest builder survey, high construction costs, elevated mortgage rates and challenging housing affordability conditions are causing builders to approach the market with caution,” said Carl Harris, chairman of the National Association of Home Builders (NAHB) and a custom home builder from Wichita, Kan. “The uncertain policy environment in terms of a better regulatory climate and impending tariffs offers both upside and downside risks in the near-term.”
“The single-family home building market is facing competing concerns and opportunities for 2025,” said NAHB Chief Economist Robert Dietz. “Given persistent affordability concerns, reducing inefficient regulatory costs would offer the best policy path to improve attainable housing supply and bring down shelter inflation.”
On a regional basis compared to the previous month, combined single-family and multifamily starts are 27.6% lower in the Northeast, 10.4% lower in the Midwest, 23.3% lower in the South and 42.3% higher in the West.
Overall permits increased 0.1% to a 1.48 million unit annualized rate in January. Single-family permits were at a 996,000 annual unit rate, remaining unchanged compared to the previous month. Multifamily permits increased 0.2% to an annualized 487,000 pace. Looking at regional permit data compared to the previous month, permits are 6.1% lower in the Northeast, 1.8% higher in the Midwest, 0.1% lower in the South and 2.3% higher in the West.
The number of single-family homes under construction in January is down 6.3% from a year ago, to 641,000 units. The number of multifamily units under construction is down 22.1% from a year ago, to 768,000 units. There were 669,000 multifamily completions in January, up 11% from January 2024. For each apartment starting construction, there are 1.8 apartments completing the construction process.
February 25, 2025—Simpson Manufacturing Co., Inc., an industry leader in engineered structural connectors and building solutions, announced its financial results for the fourth quarter and full-year of 2024.
“During 2024, we grew revenues modestly in a challenging year where housing starts in both the U.S. and Europe declined,” commented Mike Olosky, President and Chief Executive Officer of Simpson Manufacturing Co., Inc. “In North America, I am very pleased that volume growth in pounds shipped exceeded U.S. housing starts by approximately 600 basis points. In Europe, sales were flat despite a difficult demand environment.”
Mr. Olosky continued, “In 2025 we believe a low single-digit recovery in U.S. housing starts is possible and European housing starts to be consistent with 2024 levels. As part of our commitment to maximizing shareholder returns, we have revised our financial ambitions to continue above market growth relative to U.S. housing starts on a trailing twelve-month basis, maintain an operating income margin at or above 20%, and drive EPS growth ahead of net revenue growth. While the midpoint of our 2025 guidance range for operating income margin is below our ambition, we are working to offset significant input cost increases over the past three years and will carefully evaluate avenues to preserve our profitability. We believe our business is capable of achieving a 20% operating income margin or higher with modest market growth and continued above market volume growth. We continue to believe in the mid-to-long term prospects of the housing market and are well positioned to take advantage of future growth.”
2024 Fourth Quarter
• Net sales of $404.8 million increased 4.4% from $387.8 million due to incremental sales from the Company’s 2024 acquisitions and a modest increase in sales volumes.
• Gross margin remained 47.0% as lower material costs were offset by higher factory and overhead as well as warehouse costs, as a percentage of net sales.
• Income from operations of $85.4 million increased 7.0% from $79.8 million. The increase was primarily due to higher gross profit, partly offset by higher operating expenses. The operating expense increases were driven by higher personnel costs, which were partly offset by decreased variable incentive compensation.
2024 Full-Year
• Net sales of $1.7 billion increased approximately 1.1% from 2023 due to higher sales volumes.
• Gross margin decreased to 49.0% from 50.3%, primarily due to higher factory and overhead as well as warehouse costs, partly offset by lower material costs, as a percentage of net sales.
• Income from operations of $439.6 million decreased 7.1% from $473.2 million. The decrease was primarily due to lower gross profit as well as increases in operating expenses. The operating expense increases were driven by higher personnel costs, computer software and hardware costs, and professional fees, which were partly offset by decreased variable incentive compensation.
For the complete press release, visit www.strongtie.com.
Pleasanton, Calif., February 11, 2025 — Simpson Strong-Tie, the leader in engineered structural connectors and building solutions, has opened the application process for its annual Student Scholarship program, a part of the company’s Strong-Tie Undergraduate Fellowship. The $3,000 scholarship encourages the design and building of safer structures in our communities by supporting education for students majoring in structural and civil engineering, construction management or architecture in the United States.
Scholarship recipients must be undergraduate students at participating colleges and universities entering their junior or senior year. The online scholarship application for the 2025–2026 academic year can be found at strongtie.com/scholarships. The deadline to apply is March 21, 2025.
Scholarship recipients become participants in the Strong-Tie Undergraduate Fellowship, which provides access to industry contacts, relevant training, job leads, peer connections and community, plus an insider’s look at Simpson Strong-Tie’s leadership in structural systems research, testing and innovation. Through their involvement, awardees can build the industry knowledge and network to help maximize their future professional growth and success.
Up to 120 scholarships will be awarded for the 2025–2026 academic year to university students from more than 100 participating schools. Awards do not automatically renew, but students may reapply to the program each year they meet eligibility requirements. Since the Simpson Strong-Tie Student Scholarship program began in 1999, the company has provided over $1.8 million to more than 1,100 students at hundreds of colleges and universities across the country.
The Simpson Strong-Tie Student Scholarship is administered by Scholarship America, the nation’s largest designer and manager of scholarship and tuition reimbursement programs for corporations, foundations, associations and individuals.
Learn more at strongtie.com/scholarships.
About Simpson Strong-Tie Company Inc.
Simpson Strong-Tie is the world leader in structural solutions — products and technology that help people design and build safer, stronger homes, buildings, and communities. As a pioneer in the building industry, we have an unmatched passion for problem solving through skillful engineering and thoughtful innovation. Our structural systems research and rigorous testing enable us to design code-listed, value-engineered solutions for a multitude of applications in wood, steel, and concrete structures. Our dedication to pursuing ever-better construction products and technology and to surrounding our customers with exceptional service and support has been core to our mission since 1956. For more information, visit www.strongtie.com and follow us on Facebook, Twitter, YouTube and LinkedIn.
February 7, 2025—UFP Industries marks 70 years in business on February 9, never failing to turn a profit in each of them. Founded in 1955, its leaders say the keys to success in all these years are its ability to recruit and retain high-achieving employees, its down-to-earth company culture and its unique incentive system that aligns employee interests with shareholders.
“Our company’s motto is, ‘No mission statement; just people on a mission.’™ Every day, our people show up and get to work, demonstrating the determination and grit that drives our company forward. And we want to take this special year to honor their outstanding leadership,” said CEO Will Schwartz, who took the helm at UFP in late December. “I’m honored to join five other CEOs who worked their way from the ground up—I’m living proof that UFP is the place for self-made men and women. We measure our people by their hard work and the fire in their belly. The only person who holds you back is yourself.”
UFP Industries, founded in 1955 by William “Bill” Grant as Universal Forest Products, started as a small wood-products manufacturer. Over the decades, it expanded its portfolio to include a wide variety of materials and products, focusing on innovative solutions for the construction, retail, and industrial markets. In 2019, the company rebranded as UFP Industries to better reflect its diversified global business operations.
The retail segment houses UFP’s flagship treated lumber brand, ProWood—the largest supplier of treated lumber in North America— as well as its luxury composite decking line, Deckorators. The packaging segment powers the modern economy by providing crating and custom packaging solutions for a wide variety of specialty products from food and agriculture to technology, batteries and solar panels. The construction segment, with its concrete forming, site built and factory built business units, has helped build countless homes and neighborhoods and contributed to some of the world’s most recognizable skylines and institutions.
“Our 70-year history is a testament to our stability and ability to generate consistent returns. We’ve consistently pursued excellence and achieved above-market results through economic cycles,” said executive chairman and former CEO Matt Missad. “Our proven track record, coupled with our innovative spirit, strategic vision, and willingness to outwork our competition, positions us to realize stronger-than-ever success in the future. Our commitment to employee ownership has been a fundamental driver of our success, fostering a deep sense of personal responsibility and personal reward for the company’s performance.”
“As UFP Industries celebrates its 70th anniversary, we stand as a testament to American manufacturing ingenuity, transforming from a humble lumber company into a global manufacturing powerhouse. For seven decades, UFP has been at the forefront of innovation, consistently delivering products that support the world’s physical infrastructure, keep markets moving, and improve people’s lives,” said Schwartz.
February 17, 2025—UFP Industries, Inc. announced fourth quarter 2024 results including net sales of $1.46 billion, net earnings attributable to controlling interest of $68.0 million, and earnings per diluted share of $1.12. The company also announced net sales of $6.7 billion and earnings per diluted share of $6.77 for fiscal 2024. These results include the impact of impairment charges and severances of approximately $0.11 per diluted share (net of income taxes) associated with ongoing actions to reduce capacity and personnel costs due to lower overall market demand, and a gain on the sale of real estate of approximately $.03 per diluted share (net of income taxes).
“The second half of 2024 proved more challenging than expected, as we continued to face softer demand and a more competitive pricing environment in the fourth quarter,” said Matthew J. Missad, executive chairman. “Despite these market headwinds, 2024 marked the 70th consecutive profitable year for the company, which highlights the resiliency of our businesses and our people. It has been an incredible pleasure to work with and help lead such a great team, and I am grateful for their hard work and determination, with the goal of always being the best. In times like these, they are addressing challenges head-on and making the tough decisions that will enable us to grow further and faster when our markets find a more stable footing. Although we expect the challenging economy to persist in 2025, our balanced business model, variable incentive compensation program, growth and improvement strategies, and strong balance sheet will help drive our success. I am very confident that Will Schwartz, Mike Cole and our great team of leaders will drive even greater success in the future while maintaining the team culture of employee growth and opportunity in pursuit of elite performance.”
On December 29, 2024, Will Schwartz replaced Matt Missad as CEO, and Landon Tarvin succeeded Will as president of UFP Retail Solutions. Additionally, Will added the role of president, and CFO Mike Cole expanded his duties to include president of corporate services.
“I feel honored to step into the role as CEO at UFP Industries and help build on the company’s incredibly rich history,” said Will Schwartz. “Our team is focused on investing in our most promising growth opportunities and businesses that will generate the highest long-term returns. Bringing new, value-added products to market remains a key focus across the enterprise, and we’ll showcase a few of our latest innovations, including our new Deckorators product lines made with Surestone technology, at the International Builders’ Show next week. We’ll also prioritize improving the value we bring to our customers and driving returns across our portfolio through investments in automation, new value-added product introductions, and plant optimization. Finally, as we manage through this uncertain environment, we will carefully manage our profitability and remain on track to achieve cost savings of $60 million by the end of 2026.”
Fourth Quarter 2024 Highlights (comparisons on a year-over-year basis except where noted):
• Net sales of $1.46 billion decreased 4 percent due to a 4 percent decrease in selling prices.
• New product sales of $102 million were 7.0 percent of total sales compared to 7.7 percent in the fourth quarter of 2023.
• Net earnings attributable to controlling interests of $68.0 million represents a 34 percent decrease from last year.
• Adjusted EBITDA1 was $132.7 million in the quarter or 9.1 percent of sales, compared to $165.6 million or 10.9 percent of sales for the same period a year ago.
For the complete press release, visit www.ufpi.com.
February 20, 2025—Builders FirstSource, Inc. reported its results for the fourth quarter and full year ended December 31, 2024.
All Year-Over-Year Comparisons Unless Otherwise Noted:
• For the fourth quarter, net sales were $3.8 billion, an 8.0% decrease, primarily driven by lower core organic sales and commodity deflation, partially offset by growth from acquisitions and one additional selling day
• For the fourth quarter, gross margin decreased 300 basis points to 32.3%, primarily driven by ongoing SingleFamily and Multi-Family margin normalization.
• For the fourth quarter, net income was $190.2 million, or diluted EPS of $1.65 compared to diluted EPS of $2.83 in the prior year period. Net income as a percent of net sales decreased by 347 basis points to 5.0%.
• For the fourth quarter, Adjusted EBITDA decreased 28.0% to $493.6 million, primarily driven by lower gross profit, partially offset by lower operating expenses after adjustments.
• For the fourth quarter, Adjusted EBITDA margin decreased by 360 basis points from the prior year period to 12.9%, attributable to lower gross margin and reduced operating leverage.
• For full-year 2024, cash provided by operating activities was $1.9 billion, compared to $2.3 billion in the prior year period, primarily driven by lower net income. The Company’s free cash flow was $1.5 billion, a decrease of $0.4 billion compared to the prior year period. The decrease was primarily driven by lower net income.
• For full-year 2024, the Company repurchased 8.9 million shares of common stock at an average price of $170.74 for $1.5 billion, inclusive of applicable fees and taxes, reducing total shares outstanding by 6.8% in 2024.
“Our fourth quarter and full year results demonstrate our resilience and ability to drive results in the face of a complex operating environment, while maintaining our focus on building for the future. The strength of our differentiated platform and our operational excellence initiatives drove a mid-teens EBITDA margin in 2024. Results this year are further proof that our success is driven by the dedication of our hardworking team members and support of our customers,” commented Peter Jackson, CEO of Builders FirstSource.
Mr. Jackson continued, “By continuing to invest in our value-added solutions and our installation business, along with leveraging cutting-edge technology, we are addressing customer challenges and serving as the supplier of choice. Our investments today in organic growth opportunities and value-enhancing acquisitions position us to perform well in any environment.”
Pete Beckmann, CFO of Builders FirstSource, added, “Our fourth quarter and full year results reflect our ability to execute our strategy by leveraging our exceptional operating platform and financial flexibility. Our business generates consistently strong free cash flow through the cycle, which we deploy under our balanced capital allocation strategy. This disciplined capital deployment framework remains in place: maintaining a fortress balance sheet, investing in organic growth, making value-enhancing acquisitions, and returning capital to shareholders through share repurchases.”
For the complete press release, visit www.bldr.com
January 31, 2025, Clearwater, Florida – Dave Stauter, President and Chief Operating Officer, has announced his retirement after 21 Years with Tibbetts Lumber (and the former Cox Lumber Co.). Tibbetts Lumber announces the promotion of Joe Sanchez to Chief Operating Officer and assumes day-to-day leadership of the company. Joe, a lumber industry veteran, joined Tibbetts Lumber in January 2024 as Regional Manager for the Southern Region of Florida. Joe previously worked for Cox Lumber Co. and has 29 years of experience in the Lumber and Building Material industry managing sales and operations in both single and multi-unit locations.
“It has been an honor to rejoin the Tibbetts Lumber team and serve as Regional Manager. I am tremendously proud of everything we have accomplished so far. I am extremely thankful for all the support given to me by the entire Tibbetts Lumber team, and I am excited for the great things I know we will accomplish going forward,” said Sanchez.
Dave Stauter will serve as Senior Vice President / Director and work closely with Joe throughout 2025 to ensure a smooth and successful transition. Dave’s 21 years with Tibbetts Lumber (and the former Cox Lumber Co.) has been instrumental in the success of the company.
“The Board is extremely confident that Joe is the perfect fit to lead our company as we continue our aggressive growth plan. Russ Hallenbeck, Vice Chairman and CEO of Tibbetts said. “As a 29-year veteran of the industry, Joe’s extensive leadership, expertise, and relationships will take our company to the next level. We are blessed to have him as our next Chief Operating Officer.”
Tibbetts Lumber serves regional and custom/semi-custom builders and remodelers with ten locations in Florida – Largo, Land O’Lakes/Tampa, Ocala, Crystal River, Lecanto, Palm Bay/Melbourne, Lehigh Acres/ Ft. Myers, Englewood, Milton and Pensacola, Florida. Tibbetts’ primary business lines include roof and floor trusses, lumber and building materials, interior and exterior doors, millwork and trim, windows, siding, and specialty items for new home construction and remodeling.
Tibbetts Lumber was started in 2009 by Kyle Hooker, his grandfather, Linton N. Tibbetts, OBE, and his family after their former company, Cox Lumber Co., was acquired by a subsidiary of The Home Depot in 2006. Cox Lumber Co. was originally purchased by Mr. Tibbetts in 1949 and operated 28 locations in Florida until the sale.
Eighty Four, PA, February 6, 2025 – 84 Lumber continues to expand its services in the Mid-Atlantic with the opening of another component plant in Newark, Delaware.
The company’s newest plant, at 10 Aleph Drive, is a 21,113-squarefoot building on 3.12 acres. Formerly Warren Truss, 84 Lumber acquired the facility in June 2024 to manufacture wall panels and floor trusses to meet the growing market demand in Delaware, New Jersey, and the greater Philadelphia metro area.
“We now have three locations to service these markets,” said Sean O’Connell, general manager of the New Britain, Newark, and Bloomsburg truss plants. “This includes our facilities in New Britain and the recently opened truss plant in Bloomsburg, Pennsylvania.”
The plant began operating in January with 10 associates. The company plans to hire a total of 50 associates by 2026.
84 Lumber offers a ladder of opportunity that involves the company’s production manager trainee (PMT) program. The program is designed to prepare an apprentice in the components sector for a production manager position. The 12-month training program prepares the PMT with a mix of on-the-job and classroom training, leadership courses, a Lean Green Belt program, and emerging leadership training. The most current example is Jose Colindres, who completed the PMT program at the company’s Winchester, Virginia facility and was promoted to production manager at Newark. The Newark plant manager, Dylan McDevitt, started as a manager trainee at an 84 Lumber store before transitioning to the company’s New Britain truss plant, working his way through the ranks, and being promoted to his current position.
“84 Lumber has career opportunities for high performers. If you’re willing to commit and do the work, you’ll find a fulfilling, life-long career with us,” said Dylan McDevitt.
To learn more about the production MT program, click here . For information on available career opportunities at 84 Lumber, including the production manager trainee position, visit https://careers.84lumber. com/current-openings
84 Lumber is the leading supplier of building materials, manufactured components, and industry leading services for single and multifamily residences and commercial buildings. The company operates more than 320 facilities in 34 states and is continuing to grow. To learn more, visit www.84lumber.com or follow 84 Lumber on Facebook, Instagram, or LinkedIn for more information.
DE
Eighty Four, PA, February 3, 2025 – 84 Lumber is pleased to announce a new national partnership with The Home Builders Institute (HBI). This collaboration will enhance HBI’s BuildStrong Academies, a network of community-based trade schools designed to prepare individuals for successful careers in the residential construction industry.
With a shared commitment to workforce development, HBI and 84 Lumber aim to provide critical opportunities to individuals seeking careers in the skilled trades, including addressing workforce shortages in high-demand areas. As part of this partnership, 84 Lumber will support HBI’s mission to educate, inspire, and prepare individuals for careers in the building industry, particularly through scholarships and community engagement.
“The Home Builders Institute (HBI) is thrilled to strengthen our partnership with 84 Lumber to build the next generation of skilled tradespeople,” said HBI President Ed Brady. “Their support and collaboration underscore the critical importance of investing in workforce development and equipping individuals with the skills needed to succeed in the construction industry. Together, we are not only addressing the skilled labor shortage but also creating meaningful opportunities for careers that transform lives and strengthen communities. With the generous support of 84 Lumber, HBI can continue Building Careers and Changing Lives.”
“84 Lumber is deeply committed to supporting the communities we serve and creating pathways to success for individuals in the skilled trades,” said Amy Smiley, vice president of marketing at 84 Lumber.
“Partnering with HBI allows us to contribute directly to the development of a highly skilled workforce while helping to provide HBI graduates with meaningful career opportunities within our organization. 84 Lumber also offers training programs and career development opportunities, which means even if you’re starting in a skilled trade or looking to advance, there are options for growth within the company,” said Smiley.
HBI has BuildStrong Academies in Orlando, New Orleans, Sacramento, Houston, Charlotte, and Phoenix, HBI offers a robust curriculum in trade skills, job readiness, and career development. These academies provide training and certifications that are industry-recognized, ensuring that graduates are well-prepared to meet the needs of employers. They aim to provide comprehensive training and placement services to individuals from diverse backgrounds, including opportunity youth, veterans, separating military, and justice-involved individuals. HBI has plans to expand to 10 other locations in the next five years. This partnership between HBI and 84 Lumber represents a powerful collaboration that will not only strengthen the skilled trades workforce but also support economic development in communities across the country.
84 Lumber is the leading supplier of building materials, manufactured components, and industry leading services for single and multifamily residences and commercial buildings. The company operates more than 320 facilities in 34 states and is continuing to grow. To learn more, visit www.84lumber.com or follow 84 Lumber on Facebook, Instagram, or LinkedIn for more information.
February 12, 2025—West Fraser Timber Co. Ltd. reported the fourth quarter results of 2024. All dollar amounts in this news release are expressed in U.S. dollars unless noted otherwise.
Fourth Quarter Highlights
• Sales of $1.405 billion and loss of $62 million, or $(0.80) per diluted share
• Adjusted EBITDA1 of $140 million, representing 10% of sales
• Lumber segment Adjusted EBITDA1 of $21 million
• North America Engineered Wood Products (“NA EWP”) segment Adjusted EBITDA1 of $127 million
• Pulp & Paper segment Adjusted EBITDA1 of $(10) million
• Europe Engineered Wood Products (“Europe EWP”) segment Adjusted EBITDA1 of $2 million
• Repurchased 311,523 shares for aggregate consideration of $27 million
Annual Highlights
• Sales of $6.174 billion and loss of $5 million, or $(0.07) per diluted share
• Adjusted EBITDA1 of $673 million, representing 11% of sales
• Lumber segment Adjusted EBITDA1 of $(82) million, including $32 million of export duty expense attributable to finalization of AR5
• North America Engineered Wood Products (“NA EWP”) segment Adjusted EBITDA1 of $744 million
• Pulp & Paper segment Adjusted EBITDA1 of $4 million
• Europe Engineered Wood Products (“Europe EWP”) segment Adjusted EBITDA1 of $8 million
• Repurchased 1,799,217 shares for aggregate consideration of $144 million
“The fourth quarter of 2024 saw continued resiliency in our NA Engineered Wood Products business, where supply and demand fundamentals remained relatively well balanced on the back of solid new home construction demand. We also realized modest improvement in our Lumber segment this quarter as we monetized some of the benefits of our portfolio optimization strategy that allowed us to migrate more production from higher cost to lower cost mills within our platform. In Europe and the U.K., we continued to experience somewhat challenging markets as that region appears to be undergoing a protracted recovery,” said Sean McLaren, West Fraser’s President and CEO.
“Relatively high mortgage rates remain an affordability challenge for consumers and housing markets, impacting demand for our wood building products. Further, potential for the U.S. administration to impose broad-based tariffs on Canadian exports adds another element of demand uncertainty for the products we ship to the U.S. from Canada. However, while we cannot control the threat of such tariffs, we can be proactive, creating a stronger organization with a continued focus on improving the cost position across our mill portfolio and investing capital to modernize mills where it makes sense. You should also expect West Fraser to continue to return excess capital to shareholders when prudent, and maintain a strong balance sheet that will provide us with the financial flexibility to take advantage of opportunities that fit our long-term strategy.”
Several key trends that have served as positive drivers in recent years are expected to continue to support medium and longer-term demand for new home construction in North America. The most significant uses for our North American lumber, OSB and engineered wood panel products are residential construction, repair and remodelling and industrial applications. Over the medium term, improved housing affordability from stabilization of inflation and interest rates, a large cohort of the population entering the typical home buying stage, and an aging U.S. housing stock are expected to drive new home construction and repair and renovation spending that supports lumber, plywood and OSB demand. Over the longer term, growing market penetration of mass timber in industrial and commercial applications is also expected to become a more significant source of demand growth for wood building products in North America.
The seasonally adjusted annualized rate of U.S. housing starts was 1.50 million units in December 2024, with permits issued of 1.48 million units, according to the U.S. Census Bureau. While there are near-term uncertainties for new home construction, owing in large part to the level and rate of change of mortgage rates and the resulting impact on housing affordability, unemployment remains relatively low in the U.S. Further, the most recent rate hiking cycle is generally believed to be over as the U.S. central bank recently began to cut rates and Federal funds futures indicate prospects for one additional rate cut by the end of 2025, though there are evolving risks related to the new U.S. administration’s tariff and other policies, which could be inflationary. These developments notwithstanding, demand for new home construction and our wood building products may decline in the near term should the broader economy and employment slow or the trend in interest and mortgage rates negatively impact consumer sentiment and housing affordability
In Europe and the U.K., we expect a relatively modest market recovery over the near term. Looking further out, we continue to expect demand for our European products will grow over the longer term as use of OSB as an alternative to plywood grows. An aging housing stock is also expected to support long-term repair and renovation spending and additional demand for our wood building products. In the current environment, inflation appears to have stabilized and interest rates have begun to decline, which is directionally positive for housing demand. That said, ongoing geopolitical developments and the lagged impact of prior inflationary pressures may adversely impact near-term demand for our panel products in the U.K. and Europe. Despite these risk factors, we are confident that we will be able to navigate demand markets and capitalize on the long-term growth opportunities ahead.
The Company is providing the following operational guidance for 2025:
• Spruce-pine-fir (“SPF”) shipments are targeted to be 2.7 to 3.0 billion board feet
• Southern yellow pine (“SYP”) shipments are targeted to be 2.5 to 2.8 billion board feet
• N.A. OSB shipments are targeted to be 6.5 to 6.9 billion square feet (3/8-inch basis)
• European and U.K. OSB shipments are expected to be 1.0 to 1.25 billion square feet (3/8-inch basis)
• Costs for inputs, including resins and chemicals, are expected to remain relatively stable, while contract labour availability and capital equipment lead times are expected to continue to improve
• Capital expenditures are expected to be $400 million to $450 million
As the U.S. administration’s tariff and other policies evolve, we will evaluate the impact of the tariffs on our operations and consider whether any revisions to our shipment estimates are warranted. Refer to the discussion in our 2024 Annual MD&A under “Risks and Uncertainties – Trade Restrictions” for a detailed discussion of the risks and uncertainties associated with the imposition of tariffs which may impact our operational guidance and our profitability during 2025.
The complete press release may be viewed online at www.westfraser.com
February 13, 2025—Overall, investment in building construction rose 1.9% (+$408.1 million) to $21.8 billion in December, with gains recorded across all components. The residential sector grew 2.2% to $15.1 billion while the non-residential sector was up 1.3% to $6.7 billion. Year over year, investment in building construction grew 4.7% in December.
On a constant dollar basis (2017=100), investment in building construction increased 1.5% from the previous month to $13.0 billion in December and was up 1.6% year over year.
Multi-unit component drives residential sector gains in December
Investment in residential building construction was up 2.2% (+$323.9 million) to $15.1 billion in December. Single family home investment edged up 0.8% (+$60.7 million) to $7.3 billion in December, marking its fifth consecutive monthly increase. Investment in multi-unit construction rose 3.5% (+$263.2 million) to $7.7 billion in December, rebounding from two significant and consecutive monthly declines.
Investment in non-residential construction increased 1.3% (+$84.1 million) to $6.7 billion in December. Monthly increases were recorded in eight provinces and one territory, with Ontario (+$54.3 million) leading the growth and marking its 10th straight monthly increase. The industrial component was up 1.8% (+$26.2 million) to $1.5 billion in December. Quebec (+$15.9 million) led the growth, followed by six other provinces and two territories. Commercial construction investment edged up 0.6% (+$20.2 million) to $3.3 billion in December. Gains in Ontario (+$24.9 million) were tempered by decreases in Alberta (-$10.6 million) and British Columbia (-$3.3 million). In December, institutional construction investment rose 2.0% (+$37.7 million) to $1.9 billion with seven provinces and the three territories recording increases. Quebec (-$12.5 million) drove the monthly declines across the remaining three provinces.
Investment in building construction grew 1.0% (+$654.1 million) to $64.5 billion in the fourth quarter, marking the sixth consecutive quarterly increase. The quarterly increase in investment in building construction in the fourth quarter was primarily led by the non-residential sector (+$580.7 million to $19.8 billion), which accounted for 88.9% of the total growth in the quarter. The institutional (+$244.8 million to $5.7 billion) and industrial (+$224.6 million to $4.3 billion) components drove the increase in the non-residential sector, while the commercial component (+$111.3 million to $9.8 billion) contributed less to the increase. Investment in the residential sector edged up 0.2% to $44.8 billion in the fourth quarter. Growth in single family home investment (+$1.3 billion to $21.7 billion) was almost entirely offset by declines in the multi-unit component (-$1.2 billion to $23.1 billion).
For more information on construction, and for the complete press release, please visit the Construction statistics portal.
For more information on housing, please visit the Housing statistics portal
707-333-4507
Truss Designer 25-0227-1
Posted on Thursday, February 27, 2025
Employer: Company: Villa Truss
Wooden Roof and Floor truss designer. Should be versed in the Mitek Software. Experience preferred.
Remote Multifamily Truss Designer J15356
Posted on Thursday, January 30, 2025
Employer: Client Confidential
We have a client in Texas who needs Remote Multifamily Truss Designer(s) familiar with the Houston, San Antonio, Austin, and DFW areas. In addition to Texas, they sell to multiple other states. They have multiple plants and are bringing on another plant this year. If you inquire about this job, know that we will represent you to the best of our ability. With over 30 years of experience, The JobLine is your source for career moves that offer advancement and better-than-average compensation.
Truss & Wall Panel Designer 20-1130-1
Posted on Friday, April 12, 2024
Employer: Woodhaven Lumber
Located in central coastal NJ is a growing truss and wall panel manufacturer looking for an experienced truss & wall panel designer. The ideal candidate would be local to our central NJ market, but remote design is also a possibility. Previous experience with the Mitek suite of software is a plus.
We offer a competitive salary, paid holidays, paid time off, medical/ dental/life/disability insurance, 401k and profit sharing.
Truss Designer J15339
Posted on Thursday, August 01, 2024
Employer: Client Confidential
We seek Truss Designers to join our client's team and support their New England office. In this role, you will design various truss products, focusing on floor and roof trusses for single-family custom projects. Experience with MiTek software is highly desirable, and panel experience, while not required, is a valuable asset.
Truss Designer J15307
Posted on Wednesday, January 08, 2025
Employer: Client Confidential
Truss Designer - Single Family, Custom, and Multifamily. Experience required: 5 years industry experience, 3 years experience in this position, and will consider a move up if qualified. Primary duties include design, layout, optimization, cutting/ production documents, and takeoff. Work Schedule: Monday/Friday, limited Saturdays, average 40-45 hours a week, and work from home - full time if qualified. Your hours can be semi-flixible. Components include: floor trusses and roof trusses. Markets include Single Family, Custom, and Multifamily. Educational requirements: GED and High School graduate. Compensation Relocation is acceptable with limited assistance and open to negotiation. Remote if you are qualified.
Truss Designer J15312
Nestled in the serene landscapes of Central Florida, away from the hustle and bustle of the city, their location offers a picturesque setting with abundant lakes, perfect for boating, fishing, and outdoor enthusiasts. (Iused to live there and know it is truer) If you
For Additional Information twm@componentadvertiser.org or Call: 800-289-5627 x1
Visit our website: www.componentadvertiser.com/Hiring-Zone
appreciate the balance between work and the great outdoors, you've found the right place.
Our client, located in Florida, is seeking two Truss Designers. Remote is acceptable if you live in Florida, Alabama, or Georgia as they are able to offer benefits if you live in one of these three states.
Get the industry-leading software and automation technology you need to scale your business. Overcome market challenges, boost productivity, and confidently meet demand when you choose MiTek as your solution partner.
Are you ready to scale your success?
Joe Kannapell, P.E.
contract hauler drives in on a six-lane roadway, stops at predetermined locations, receives a full load of lumber and building supplies, and then heads out to a nearby jobsite. That driver has just passed through a warehouse that mimics the efficiency and abundant stocks of an Amazon.com facility. The shiny concrete floor that he traversed is kept that way by a ride-on floor sweeper that operates 24 hours a day. His straight-line, in-and-out experience is nothing like when he has to navigate the maze of added-on sheds at legacy lumberyards, waiting to be loaded. At least, that is the intent of Home Depot’s quest to gain a bigger share of the pro builder market, ultimately reaching 90% of U.S. customers with same-day and next-day delivery, like Amazon does.
Since 2020, Home Depot (HD) has been erecting 600,000 to 1.2 Million sq. ft. Flatbed Distribution Centers (FDC) like this one in Dallas, Texas, with a reported 17 more either finished or under construction, out of a planned 40 facilities. Their associates proudly proclaim that they’ll soon have these impressive edifices in all cities with an NFL franchise, except, perhaps, Buffalo. Their aim is two-fold: to capture more of the professional builder sector and reignite their growth, since they have saturated most markets with their big box stores (considering that, in 2024, they added 12 new stores to their 2341 existing facilities, which expanded their floor space by barely 0.5%), and to take further advantage of their B-to-B online enhancements.
HD believes that this $1.2 Billion investment will increase their share of the professional builder segment from their current 15% to 17% share and bring it closer to the 50% share they have earned in the consumer do-it-yourself market. But where will they obtain this new business? Will it come from the LBMs or the independent building supply yards?
Their biggest potential source of this new revenue is Builders FirstSource (BFS), which is one-tenth the size of HD but dwarfs its competition like HD. Yet, over the last ten years, BFS has maintained a strategy designed to increase its truss sales, which has raised its share of total revenue from 19% in 2014 to 27% in 2024. And, BFS claims that their increased truss sales contribute much more to profitability than lumber and sheet goods, giving BFS an advantage that HD doesn’t have without truss manufacturing.
It is significant that HD began this new venture in Dallas, which is a stick-framed single-family market, where their inability to source trusses in-house is not a significant disadvantage. Perhaps HD still is reticent to manufacture trusses, after their abortive ownership of Cox Lumber and Williams Brothers nearly two decades ago. However, as they have opened facilities in Atlanta and Charlotte, offering trusses and EWP has become more important. They currently stock 11-7/8” I-joists and LVLs and have discussed stocking deeper EWP and trimmable open web floor trusses. But they also will need a source of roof trusses, and that may be Universal Forest Products, since Universal buys $50 Million of retail products from HD currently. However, a two-step approach is not ideal.
At the opposite end of the revenue spectrum are the privately owned lumber yards without truss plants, which seem to be more likely prospects. HD has invested heavily in software to enable online purchasing, has a decided advantage in stock levels and delivery times, and apparently is able to provide material take-offs. It remains to be seen if they will be able to deliver the personal service and the specialty products that smaller builders require.
The material handling advantages inside these HD FDC’s are compounded by the outside facilities. Three separate rail sidings service HD’s property. Two separate tracks run parallel to the eastern face of the building, separated from the building by 200 ft. of yard storage. The third track runs directly into the building with enough length to accommodate eight rail cars.
Opposite the indoor rail spur is adequate space to hold the contents of a trainload of material, prior to transferring it into cantilever racks that extend nearly to the 30 ft. ceiling height.
This initiative to gain pro sales by Home Depot is reminiscent of the opposite action taken by Lowes, who basically abandoned their pro business 30 years ago and followed HD into the retail business. Ironically, when Lowes embarked on this initiative, a group of associates recognized the need for a specialized pro-oriented business, just as HD has done today. Those associates created Builders FirstSource, which may soon be HD’s competition.
The Industry-Leading Manufacturer of Panelized Wall Panel & Floor Cassette Equipment.
SERIES AUTOMATED SHEATHING STATION
The Platinum Series Automated Sheathing Station is the most automated sheathing station that Panels Plus offers and reduces the amount of time an operator needs to be hands-on during the sheathing process. This sheathing station is driven using MiTek Software and completely fastens sheathing to studs, blocking, headers, and sill plates to ensure quality panels every time. This model can be a stand-alone unit, or integrated into a larger system. Various sizes and configurations are available.