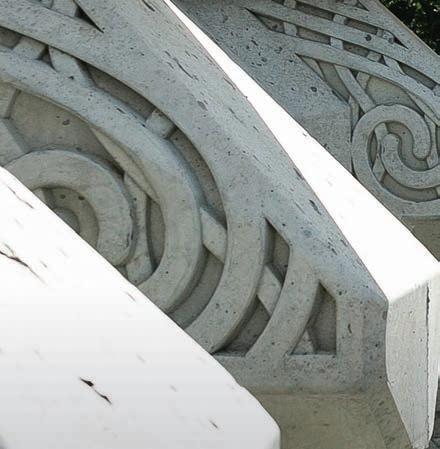
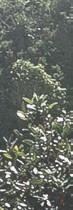
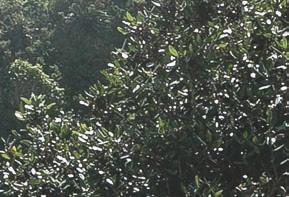
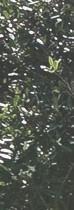

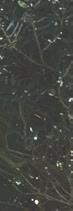
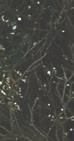

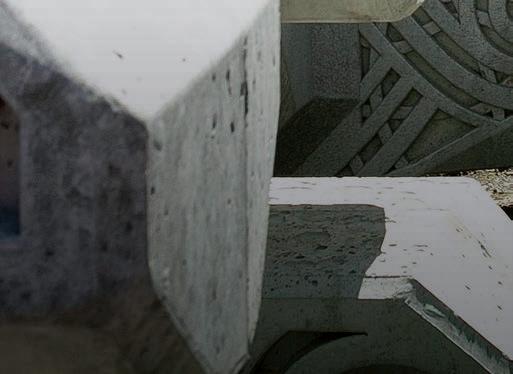
NGĀ ŪRANGA KI PITOONE - A PATH TO RESILIENT INFRASTRUCTURE
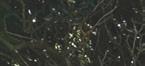


VOLUME 63 ISSUE 2
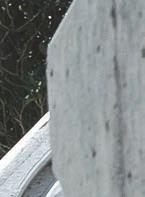
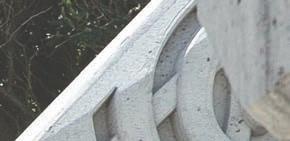
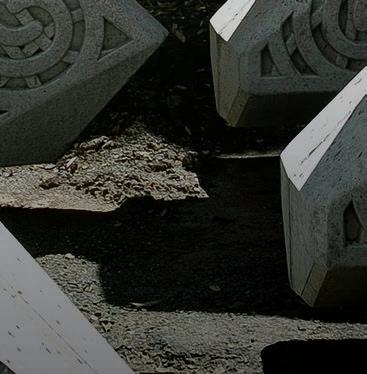
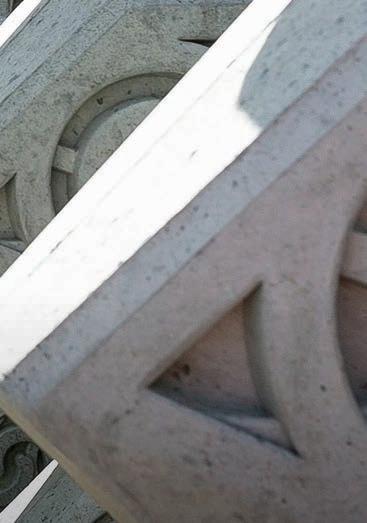
2050 ROADMAP TO NETZERO CARBON - STAGE 2 TRANSFORMATION
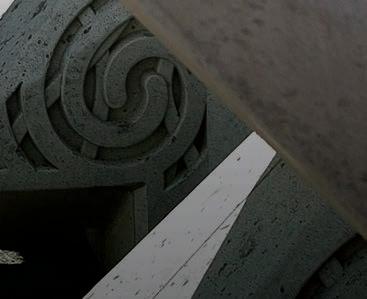

NGĀ ŪRANGA KI PITOONE - A PATH TO RESILIENT INFRASTRUCTURE
VOLUME 63 ISSUE 2
2050 ROADMAP TO NETZERO CARBON - STAGE 2 TRANSFORMATION
AS WE MARK THE ONE-YEAR ANNIVERSARY OF THE LAUNCH OF A NET-ZERO CARBON CONCRETE INDUSTRY FOR AOTEAROA NEW ZEALAND: ROADMAP TO 2050, IT’S AN OPPORTUNE MOMENT TO CONSIDER NEXT STEPS, WITH A RECENT EMPHASIS HAVING BEEN PLACED ON CARBON CAPTURE, UTILISATION & STORAGE (CCUS) ALONG WITH PROGRESSING RECOGNITION FOR CARBON UPTAKE.
The Roadmap sets out a pathway to producing net-zero concrete by 2050, tailored to the unique conditions and needs of the New Zealand concrete industry. This plan is not just an aspirational goal but a practical framework for reducing greenhouse gas emissions – targeting a 44% reduction in ‘direct’ and electricityrelated emissions by 2030, with the goal of achieving a 100% reduction by 2050.
Concrete NZ recently initiated Stage 2 of the Roadmap, which focuses on identifying the key change agents and transformations required to reach net-zero carbon. This stage is critical as it will lay the groundwork for developing targeted and granular strategies that will drive industry transformation.
The success of this stage, referred to as the Transformation Project, hinges on advancing the seven decarbonisation levers outlined in the Roadmap. Among these are the reduction of clinker factor, increasing the use of SCMs to replace a portion of Ordinary Portland Cement, and making small yet impactful gains across the electricity grid.
Additionally, improving efficiencies in concrete production and optimising design and construction processes will contribute to reducing emissions. See pages 22-24 for a closer look at the Transformation Project.
Substantial gains towards the 2050 goal of net-zero carbon concrete are also anticipated from embracing Carbon Capture, Utilisation & Storage (CCUS) technologies. By harnessing New Zealand’s lowcarbon electricity to capture process emissions from calcination (the conversion of limestone (CaCO3) into burnt lime (CaO) and carbon dioxide (CO2) during clinker production) and factoring in Carbon Uptake during the later lifecycle stages of concrete structures, concrete has the potential to become a net-negative emissions building material.
Aligned to the CCUS and Carbon Uptake levers, Concrete NZ recently responded to MBIE’s discussion document on the Proposals for a Regulatory Regime for Carbon Capture, Utilisation & Storage. In our submission, we emphasised the need for CCUS to be recognised as a permitted activity in New Zealand, supported by appropriate legislation. It’s essential that all emissions reduction options, including CCUS, are evaluated on an equal footing to ensure a cost-effective transition to a low-carbon economy.
Editor/Advertising: Adam Leach
+64 4 915 0383 adam@concretenz.org.nz
Subscriptions:
Angelique Van Schaik +64 4 499 8820 admin@concretenz.org.nz
concrete is published quarterly by Concrete NZ
PO Box 448 Level 7, 22 Panama Street Wellington NEW ZEALAND
Tel: +64 4 499 8820
Email: admin@concretenz.org.nz Website: www.concretenz.org.nz
ISSN: 1174-8540
ISSN: 1174-9374 (online)
Disclaimer: The views expressed in Concrete are not necessarily those of the Concrete NZ. While the information contained in the magazine is printed in good faith, its contents are not intended to replace the services of professional consultants on particular projects. The Association accepts no legal responsibility of any kind for the correctness of the contents of this magazine, including advertisements.
© Copyright 2024 Concrete NZ
Advertorial
Cover Image: Ngā Ūranga to Pito-One XBlocPlus units. Iwi cultural design lead Len Hetet created the bespoke ecological pattern, named Te Ripowai, which is grounded in the cultural narrative of Te Ara Tupua. NZ Transport Agency Waka Kotahi.
RECENTLY APPOINTED TO THE POSITION OF CONCRETE INDUSTRY TRANSFORMATION LEAD, VINEET BRINGS A WEALTH OF KNOWLEDGE AND EXPERTISE TO CONCRETE NZ.
With a PhD in Civil Engineering from India, he has a deep understanding of the durability of concrete structures. Since relocating to New Zealand, Vineet has been on a mission to make a real impact on the construction industry by reducing the carbon footprint of the cement and concrete sectors.
Over the past six years, Vineet has led groundbreaking research at the University of Canterbury and Callaghan Innovation, focusing on developing sustainable binders, mineralizing carbon dioxide, enhancing the longevity of concrete structures, and promoting circularity.
Continued from P2
We also highlighted the challenges in legislating for the diverse and evolving range of CCUS technologies. To address this, we proposed that the capture, transportation, and utilisation of CO2 be managed through the New Zealand Emissions Trading Scheme (NZ ETS), with participants in CCUS activities receiving emissions units or a proportional reduction in their NZ ETS liability.
Moreover, we suggested incorporating Carbon Uptake into the CCUS framework, recognising the role of concrete structures in capturing and storing carbon, which is already integrated into international carbon accounting standards.
Concrete NZ repeated these recommendations in our response to the Ministry for the Environment’s Second Emissions Reduction Plan, and also raised them with Simon Watts, Minister for Climate Change, during a recent meeting.
The concrete industry is entering an exciting period as we work collaboratively with government to establish a foundation for making meaningful strides toward a net-zero carbon future.
Ngā mihi,
Rob Gaimster Concrete NZ Chief Executive
Now, as Concrete NZ’s Concrete Industry Transformation Lead, he is committed to driving the concrete industry towards a netzero carbon future by 2050.
Vineet’s dedication to sustainable practices and his vision for a resilient and environmentally conscious future align perfectly with Concrete NZ’s goals.
Vineet’s commitment to advancing sustainable practices in the concrete industry is to be admired, and Concrete NZ is excited to see the positive impact he will make in his new role.
Harness the increased durability of carbon nanotubes for your next concrete pour.
30 OF AOTEAROA NEW ZEALAND’S TOP ARCHITECTURE, ENGINEERING AND CONSTRUCTION STUDENTS RECENTLY COMPETED TO DESIGN AN AFFORDABLE AND SUSTAINABLE HOUSING DEVELOPMENT IN THE HEART OF ŌTAUTAHI CHRISTCHURCH.
The winners of this year’s ArchEngBuild challenge were announced by the Minister for Building and Construction Hon Chris Penk at a prizegiving at Christchurch Art Gallery Te Puna o Waiwhetū.
Ella Knapton, architecture student at Te Herenga Waka Victoria University of Wellington; Francis Orendain, construction management at Western Institute of Technology, and Douglas Goncalves, structural engineering at University of Auckland took home the top honour.
The judges commended the sheer complexity of the work: “They had 48 hours to work together to come up with an incredibly well-resolved concept and a depth of knowledge that was really impressive.”
Overall, the judges were impressed with the students’ optimism and creativity in solving
some of today’s biggest challenges – including resilience, sustainability and affordability in our buildings.
“The students we saw are going to change the building industry. Our industry can be tough – but these students are hitting the real world with the right attitude and a focus on collaboration and communication,” said the judges.
Minister Penk said: “New Zealand’s housing needs to be affordable, and it needs to be resilient. We have some of the most unaffordable housing in the world, with over a quarter of renters spending more than 40 per cent of their income on housing. This is hurting New Zealanders and it’s hurting the economy.
“Finding more efficient ways to build houses that are affordable, but also warm, durable, and safe
from natural hazard should be the key motivators for the building and construction industry.” he says. “These students are the future of the industry,”
ArchEngBuild is run by the Building Research Association of New Zealand (BRANZ) and Concrete NZ.
Claire Falck, CEO of BRANZ, says collaboration is the heart of the ArchEngBuild competition.
“Every year we challenge these architecture, engineering and construction students to work together, to help drive collaboration in the industry. It’s amazing what they come up with and how they work together,” she says.
“At BRANZ, we work to encourage collaboration across the building and construction industry to find solutions to challenges around housing. ArchEngBuild gives people the opportunity to work together and understand each other at the beginning of their career and take those skills into the industry.”
The ArchEngBuild Challenge is in its 11th year. Past ArchEngBuild students have described the challenge as one of the best experiences
of their studies and the only chance they had to understand how to work with other architects, engineers and construction managers in multidisciplinary teams.
The judges were:
•Cass Goodwin, Regional Manager at Batchelar McDougall Consulting Ltd
•James Woods, Managing Director at Image Construction & Image Projects
•Victoria Threadwell, Senior Building Scientist at Ministry for Business, Innovation and Employment
•Bernadette Muir, NZIA Fellow and Principal Academic Staff Member at Ara Institute of Canterbury
ArchEngBuild 2024 was sponsored by Concrete NZ, Metals New Zealand, WIDE, New Zealand Timber Design Society, and Southbase.
It is also supported by Te Kāhui Whaihanga New Zealand Institute of Architects, Te Ao Rangahau Engineering New Zealand and the New Zealand Institute of Building.
RALF KESSEL, CONCRETE NZ, HEAD OF ARCHITECTURE
TO TACKLE THE URGENT CHALLENGE POSED BY CLIMATE CHANGE, LOCAL GOVERNMENTS MUST FOCUS ON STRENGTHENING COMMUNITY RESILIENCE AS COASTAL EROSION, FLOODING AND EXTREME WEATHER EVENTS BECOME MORE COMMON AND SEVERE.
One strategy to boost resolve at a local level is the use of robust building materials, such as concrete, which is the backbone of durable and sustainable infrastructure.
This key message is at the heart of a 2024/25 Concrete NZ communications campaign, backed by our Readymix Sector Group, which promotes concrete as the sustainable choice for enduring infrastructure projects.
CURRENT CHALLENGES IN BUILDING CLIMATE RESILIENCE
Local Governments, including Regional Councils and Territorial Authorities, across New Zealand are grappling with a range of challenges as they seek to help their communities address climate change: Coastal Erosion and Sea-Level Rise
Many coastal areas are experiencing significant erosion and the encroachment of rising seas,
threatening properties and infrastructure. Authorities are exploring managed retreat, coastal defence structures, and land-use planning to protect these vulnerable areas.
The increased frequency and intensity of floods are major concerns for local authorities. To mitigate flood risks, there is a push to enhance flood protection infrastructure, improve stormwater management systems, and utilize natural flood management techniques, such as wetland restoration.
Infrastructure Resilience
Ensuring that essential infrastructure - including roads, bridges, water supply, and wastewater systems - can withstand extreme weather events is crucial. Local governments are conducting risk assessments and retrofitting or relocating vulnerable infrastructure to better handle these conditions.
Revising zoning laws and land use plans to prevent development in high-risk areas is a priority. This involves creating buffer zones, restricting new construction in flood-prone or erosion-prone
regions, and promoting sustainable urban planning practices that reduce vulnerability to climate impacts.
Comprehensive climate adaptation strategies are essential for building long-term resilience. These strategies often include community engagement, risk assessments, and collaboration with various stakeholders, including iwi, businesses, and community groups.
Emergency
Strengthening emergency response capabilities to deal with extreme weather events is a key focus. This involves updating emergency management plans, improving early warning systems, and conducting regular community drills to ensure readiness.
Sustainable
Encouraging the adoption of sustainable building practices, including the use of low-emission materials, energy-efficient designs, and green infrastructure, is vital. Local authorities are promoting low-carbon construction materials that can withstand climate impacts while minimizing environmental footprints.
At Fosroc, we know great construction demands solid foundations. We deliver tailored, functional construction solutions - both above and below ground. Talk to us to future-proof your buildings and infrastructure.
NZ 0800 657 156 fosroc.co.nz
Concrete is widely regarded as a superior material for construction due to its exceptional properties, making it well-suited for building resilient infrastructure and ideal for helping local governments meet the challenges of climate resilience.
Strength and Durability: Concrete is known for its ability to support heavy loads and withstand extreme conditions such as floods, earthquakes, and hurricanes without significant damage. This makes it a reliable choice for critical infrastructure that must remain operational during and after extreme weather events.
Disaster Resilience: Concrete is essential for enhancing disaster resilience. For instance, pervious concrete pavements and permeable pavers effectively manage stormwater and mitigate flood risks, while advanced seismic technologies improve earthquake resistance. Additionally, concrete sea walls protect communities from the threats posed by rising sea levels, and sturdy concrete bracing elements help secure infrastructure against stronger wind loads and severe storms.
Fire Resistance: As a non-combustible material, concrete offers enhanced fire protection, safeguarding occupants and properties during fire incidents. This feature is particularly important in areas prone to wildfires. Unlike other building materials, concrete does not emit harmful combustion gases when exposed to fire.
Natural Carbon Sink: Exposed concrete absorbs CO2 from the atmosphere over its lifetime, helping to mitigate the urban heat island effect and contributing to efforts to combat climate change.
In addition to providing a product that offers resilience benefits, the New Zealand cement and concrete industry is committed to achieving netzero carbon emissions by 2050.
This pledge aligns with global efforts to mitigate climate impacts and positions concrete as an even more suitable material for sustainable construction.
By adopting innovative technologies and practices, the industry is reducing the carbon footprint of concrete, making it an environmentally friendly choice for organisations focused on sustainability.
Following guidance from its Readymix Sector Group, Concrete NZ is actively promoting concrete as a key solution for Local Governments seeking resilient infrastructure.
The 2024/25 communications campaign will emphasise the need to prioritise concrete in new builds and upgrades to enhance climate resilience and sustainability.
By advocating for low-carbon concrete and stricter construction standards, Concrete NZ aims to help communities develop durable, high-performing infrastructure that meet broader sustainability objectives and is better equipped to face future climate challenges.
Concrete NZ has created a leaflet for Local Governments that outlines the various benefits of low-carbon concrete for decision-makers focused on helping local communities adapt to climate change.
The leaflet emphasises the importance of comprehensive planning and stringent construction standards as key elements of community resilience. It highlights how durable, highperformance structures, designed for an extended service life, contribute to overall community wellbeing. Central to this approach is the use of concrete.
The leaflet is available for download on the Concrete NZ website - www.concretenz.org.nz
TIM KLEIER, CONCRETE NZ SUSTAINABILITY & POLICY DIRECTOR
“LOW-CARBON” CONCRETE IS GAINING TRACTION IN TODAY’S CONSTRUCTION SECTOR. DEFINED AGAINST INDEPENDENT SUSTAINABILITY ASSESSMENT ORGANISATION’S BASELINE DATA, THIS ECO-FRIENDLY MIX BOASTS A SIGNIFICANTLY LOWER GLOBAL WARMING POTENTIAL COMPARED TO TRADITIONAL ORDINARY PORTLAND CEMENT MIXES.
An important part of Concrete NZ’s engagement and advocacy work is communicating that industry has a clear and achievable path to become net-zero carbon by delivering “lowcarbon” concrete, and explaining exactly what makes this type of new concrete “low-carbon”.
New Zealand’s concrete industry has the ambition to reduce emissions, and in late 2023 unveiled
A Net-Zero Carbon Concrete Industry for Aotearoa New Zealand: Roadmap to 2050.
This plan reflects a commitment to the Climate Change Response (Zero Carbon) Amendment Act 2019 and its aim to meet the greenhouse gas (GHG) reduction targets under the Paris Agreement.
Put simply, the industry aims to achieve net-zero emissions by 2050, with the Roadmap providing a realistic pathway for all concrete stakeholders.
The chart below shows the actions (‘strategies’ or ‘levers’) that will be used to achieve net-zero GHG emissions from cement and concrete in New Zealand by 2050.
In addition to clinker factor reduction, replacing some Ordinary Portland Cement with Supplementary Cementitious Materials (SCMs), embracing carbon capture technologies, improving efficiency in concrete production as well as design and construction, and accounting for carbon uptake are expected to make the biggest differences. Industry also anticipates further small savings as the electricity grid continues to decarbonise.
Collectively, these strategies contribute to enabling low-carbon concrete. But how exactly do you measure, or rather specify, low-carbon concrete?
The term low-carbon concrete refers to concrete mixes with a Global Warming Potential (GWP-T) lower than a default Ordinary Portland Cement (OPC) mix of the corresponding strength class, as defined by, for instance, the Infrastructure Sustainability Council (ISC) or the Australian National Life Cycle Inventory Database (AusLCI) baseline data.
This definition is evolving as the industry progresses in its decarbonisation efforts.
It’s recommended to liaise with the ready mixed concrete supplier to review how low-carbon mixes can be optimised while meeting performance criteria.
An initial understanding of the GWP of available concretes can be obtained by evaluating, thirdparty verified Environmental Product Declarations (EPDs), although they do have limitations. Various methods to reduce the GWP of a concrete mix exist, however, when specifying low-carbon concrete for a construction project, it’s crucial to consistently denote a performance-oriented requirement based on the targeted reduction of GWP compared to a New Zealand concrete baseline (typically from the ISC or AusLCI).
This approach allows ready mixed concrete suppliers to use the most appropriate mechanisms, such as SCMs, to achieve the end product.
• Raw Material Production and Transport: Emissions from all ready mixed concrete production activities, including raw material production and transport, are considered.
• Cement Source: The specific cement source and associated up-front carbon are included.
• Geographical Constraints: Locally available aggregates can affect cement demand and should be taken into account.
Data is organised according to several modules, which are illustrated in the following diagram:
When specifying low-carbon concrete for a construction project, it’s crucial to consistently denote a performance-oriented requirement based on the targeted reduction of GWP compared to a New Zealand concrete baseline (typically from the ISC or AusLCI).
MODULES A1-A3: RAW MATERIALS EXTRACTION & PROCESSING, TRANSPORT TO CONCRETE PLANT, MANUFACTURING OF CONCRETE
The table below provides baseline GWP in kilogram CO2 equivalents per cubic metre of concrete for a range of common strength ratings:
Specifying a lower embodied carbon 25 MPa concrete may simply involve stating a 30% reduction in GWP from the ISC embodied carbon baseline of 313 kg CO2e/m3, resulting in 219 kg CO2e/m3
It's recommended to liaise with the ready mixed concrete supplier to review how low-carbon mixes can be optimised while meeting performance criteria.
DENKA CSA#20 is a shrinkage-reducing high-performance additive made with calcium sulfoaluminate consisting mainly of limestone, gypsum and bauxite mixed proportionally. With the above mineral composition, ettringite formation during hydration reactions allows drying shrinkage to be controlled in concretes and mortars. For many decades, Denka CSA#20 has been the ‘go to’ shrinkage control additive for large seamless slabs and the construction products industry.
Early in 2024, CSA#20 was replaced with a new version, Denka Power CSA Type S. Denka Power CSA S is a lower-dosage equivalent that leverages a higher free-lime content to allow it to produce shrinkage compensating ettringite at approximately 1/2 -2/3 of the dose of Denka CSA#20.
from Holcim and Golden Bay Cement. Results are available on request. Call the sole agent
Exposed surfaces of hardened concrete begin absorbing atmospheric carbon dioxide immediately, a natural process called "carbon uptake". Over time, at least 15% of the original emissions from cement production are taken up in concrete.
The Intergovernmental Panel on Climate Change (IPCC) formally recognised carbon uptake, or "recarbonation", as a CO2 removal mechanism in its 6th Assessment Report (AR6).
Concrete's thermal mass helps save on heating and cooling bills. Additional benefits of concrete include flood resilience, fire resistance, low vibration, acoustic separation, and a service life that can exceed 100 years.
When concrete is crushed during this stage, carbon uptake increases due to greater surface area.
Beyond its end of life, concrete in buildings can be:
•Reused: Building elements from demolished buildings can be incorporated into new buildings.
•Recovered: Demolition concrete can be crushed and used as clean fill for land recontouring after quarrying or infrastructure projects.
•Recycled: Research in New Zealand shows that crushed demolition concrete can be recycled into new concrete.
EPDs quantify the environmental impacts of building materials following a standardised framework under EPD International. They are a type of LCA that involves third-party verification of calculation methods and input data, published by recognised EPD operators like EPD Australasia.
Many New Zealand cement and concrete companies have EPDs for their products, generally published on EPD Australasia, which is searchable.
As some published EPDs can be out-of-date, a more agile approach is to produce third-party verified LCAs. Ready mixed concrete suppliers should be able to provide customers with the latest LCA information for their products.
In short, Concrete NZ’s message is that low-carbon concrete refers to mixes with a GWP lower than standard OPC mixes, as defined by independent sustainability assessment organisations.
Concrete NZ also recommends that specifiers engage with local ready mixed concrete suppliers early in project planning to determine material availability and logistical capability.
Concrete NZ has developed a Briefing for members, which includes the contents of this article, along with the contact details of the Concrete NZ Technical Team.
Concrete NZ offers a wealth of experience and expertise in all aspects of concrete (structural, architectural and materials) while maintaining a strong emphasis on sustainability and low-carbon developments. The Technical Team is available to assist with queries direct from members, as well as from members’ clients.
The Briefing can be downloaded from the Concrete NZ website – www.concretenz.org.nz
1-DAY CONFERENCE 14 NOVEMBER 2024
EXCITEMENT IS GROWING AS NEW ZEALAND PREPARES TO HOST THE GLOBALLY RECOGNISED FIB SYMPOSIUM FOR THE FIRST TIME, FROM 1113 NOVEMBER 2024 AT TE PAE CHRISTCHURCH CONVENTION CENTRE.
Presented by Concrete NZ’s Learned Society, this prestigious event brings global experts together to share cutting-edge research and advanced practices in structural concrete.
It is a unique opportunity for local professionals to engage with world leaders in the field, exchange
ideas, and showcase New Zealand’s advancements on an international stage, fostering growth and innovation across the industry.
FIB SYMPOSIUM
The fib Symposium is an annual cement and concrete focussed event that provides a forum to present and discuss state-of-the-art practice, recent progress and research, standards and guidelines, and future perspectives relating to durability, sustainability and resiliency in structural and civil engineering.
The fib (Fédération Internationale du Béton/ International Federation for Structural Concrete) is a not-for-profit association formed by 42 national member groups and approximately 2500 corporate and individual members in more than 100 countries.
Its mission is to develop at an international level the study of scientific and practical matters capable of advancing the technical, economic, aesthetic and environmental performance of concrete
construction. The knowledge developed and shared by the fib (Bulletins, events, workshops, courses, etc) is entirely the result of the volunteer work provided by its members.
The organisation was formed in 1998 by the merger of the Euro-International Committee for Concrete (the CEB) and the International Federation for Pre-stressing (the FIP).
Concrete NZ’s Learned Society is a long-time National Member of fib
The fib Symposium’s technical programme will be headlined by five outstanding construction experts who are set to share their experience and knowledge across a range of subjects, including concrete and innovative materials, structural performance and design, construction methods and management, and outstanding structures.
• Laura Lowes is a Professor at the University of Washington, specializing in structural and earthquake engineering. Her research integrates numerical simulation with laboratory testing and field data to advance earthquake simulation models for concrete structures. She holds leadership roles in several National Science Foundation facilities and has received many awards, including from the American Society of Civil Engineers (ASCE).
• Steve Denton is the Executive Director and Head of Civil Engineering at WSP UK, leading a team of over 600 professionals. He chairs the CEN/TC 250 Eurocodes committee, guiding the development of structural standards across Europe. A Visiting Professor at the University of Bath, Steve is also Vice President of the Royal Academy of Engineering and serves on the fib Presidium.
• Agnieszka Bigaj-van Vliet is a senior expert in concrete structure safety and sustainability. She coordinates research at the Netherlands Organisation for Applied Scientific Research, focusing on sustainable, climate-adaptive concrete. She holds leadership roles in fib and the American Concrete Institute and is involved in national and international standardization of structural concrete.
• Des Bull is a Technical Director at Holmes Group with over 42 years of experience in structural engineering, focusing on concrete structures. A former adjunct professor at the University of Canterbury, Des is a Distinguished Fellow of Engineering New Zealand and has contributed extensively to the development of concrete design standards in New Zealand.
• Xilin Lu is a Professor of Civil Engineering at Tongji University, Shanghai, specializing in seismic analysis, dynamic testing, and vibration control for tall buildings. An esteemed researcher, he is a member of the Chinese Academy of Engineering and serves as Chief Editor for two SCI-indexed journals. Prof. Lu has also been recognised for his work by ASCE.
The Symposium Organizing Committee has strengthened the Technical Programme by including “Invited speakers,” selected for their expertise in specific topics. Their specialised knowledge and insights will deepen the discussion, complementing the keynote presentations and enriching the overall conference experience.
• Takumi Shimomura is a Professor of Civil and Environmental Engineering at Nagaoka University of Technology, Japan. His research focuses on concrete’s creep, shrinkage, and reinforcement corrosion. He has chaired the JSCE Concrete Committee and is currently President of the Japan Prestressed Concrete Institute. Takumi actively contributes to multiple fib technical groups.
• JohnProvis leads the Cements Group at PSI Paul Scherrer Institut and is a former Professor of Cement Materials Science at The University of Sheffield. His research explores sustainable and unconventional cements, particularly for nuclear waste disposal. John has published around 300 journal articles and holds fellowships in several prestigious organizations.
• Horst-Michael Ludwig is a Professor of Building Materials at Bauhaus-Universität Weimar and Director of the F.A. Finger Institute for Building Materials Science. He specializes in cement chemistry, recycled concretes, and concrete durability. With over 300 journal articles and extensive industry experience, he also organizes ibausil, Europe’s largest building materials conference.
• RaviKanitkar has over 30 years of experience in structural design and retrofitting, specializing in fiber-reinforced polymers for strengthening structures. He co-founded KL Structures Group and holds an MS in Structural Engineering from Washington State University. Ravi is also an active member and chair in multiple American Concrete Institute committees.
• Alper Ilki is a prominent structural and earthquake engineering expert at Istanbul Technical University. He chairs the Turkish Earthquake Foundation’s Executive Committee and has contributed significantly to Turkey’s seismic design codes. His prolific work includes numerous journal articles, conference presentations, and editorial roles in top engineering journals.
The fib Symposium format features a diverse range of sessions to engage participants. Oral presentations will deliver traditional structured talks from experts, covering a broad range of research developments and project profiles.
Special sessions are themed discussions offering in-depth exploration of specific topics, while Posters will provide visual displays, presented in designated areas, where attendees can engage with the authors.
As a new initiative, Monitor presentations will provide a dynamic platform for presenting live, or through pre-recorded videos to allow for ondemand viewing. This multi-faceted approach ensures a comprehensive exchange of knowledge and ideas across various formats.
Te Pae Christchurch Convention Centre is a state-of-the-art facility located in the heart of
Christchurch. Renowned for its cutting-edge design and world-class amenities, Te Pae offers flexible spaces that accommodate a wide range of events, from large conferences to intimate meetings.
Its striking architecture, inspired by the natural landscapes of New Zealand, includes panoramic views of the Avon River and surrounding city. The Centre is equipped with advanced technology, sustainable features, and exceptional hospitality services, making it an outstanding choice for hosting international events (such as the fib Symposium) and providing an unforgettable experience for delegates and visitors alike.
The fib Symposium has received tremendous sponsorship support, reflecting the event’s significance. With Holcim and Golden Bay as Platinum sponsors, and Pacific Steel, Sika, and Leviat as Gold sponsors, the backing is exceptional.
Silver sponsors include Building Point, Certus, Freyssinet, Reid Construction Systems, Ramset, and Fletcher Reinforcing. Additionally, support from the American Concrete Institute (ACI), WSP, the Building Construction Training Fund (BCTF), BCITO, and 30 other exhibitors highlights the industry’s strong commitment to this event.
The 2024 Concrete NZ Conference is taking on an exciting new format, condensed into an actionpacked 1-day event on Thursday, 14 November, immediately following the 11-13 November fib Symposium, both at Te Pae Christchurch Convention Centre.
Delegates, including researchers, industry professionals, and construction experts, will experience a dynamic technical programme featuring oral presentations and engaging 5-minute Lightning Talks.
The diverse speaker lineup will merge international and local perspectives on projects, research, concrete technology, design trends, low-carbon initiatives, and more.
Delegates can register for just the 1-day Concrete NZ conference if they wish, however, registration for the 3-day fib Symposium includes the 1-day event as complimentary.
HONOURING EXCELLENCE
This year marks a continued evolution in Concrete NZ’s awards framework, following its 2022 revision
to better recognise and promote achievements in the concrete industry.
Concrete NZ members have submitted entries for the 2024 Conference Awards, which include categories such as:
• Producer - Extra Distance
• Producer - Technical Excellence
• Inclusion & Diversity
• Health, Safety & Wellbeing
• Carbon Reduction
The awards will be presented during the formal dinner on Wednesday, 13 November, at Te Pae Christchurch Convention Centre, celebrating:
• Honorary Life Members
• Outstanding Contributors
• Plant Audit Scheme - Gold Status
• Concrete Industry Apprentice of the Year
• Concrete Cricket Bat Competition
These awards, distinct from the Concrete Industry Awards, are open to members across all Concrete NZ’s Sector Groups and the Learned Society.
Hosted by Concrete NZ’s Learned Society, the fib Symposium is scheduled for 1113 November at Te Pae Christchurch Convention Centre. It is followed by a 1-day Concrete NZ Conference, also at Te Pae. Visit the Symposium website for all the details - www.fibsymposium2024.org
CONCRETE NZ ACKNOWLEDGES THE SUPPORT OFFERED BY ALL THE EVENT SPONSORS
STUART L. MATTHEWS FOR FIB
THE MODEL CODE (2020) – FIB MC (2020) – IS A SINGLE CODE DEALING WITH BOTH NEW AND EXISTING CONCRETE STRUCTURES; THAT IS, BOTH THE DESIGN OF NEW STRUCTURES AND THE VARIOUS ACTIVITIES ASSOCIATED WITH THE ASSESSMENT, INTERVENTIONS UPON AND LIFE-CYCLE MANAGEMENT OF EXISTING CONCRETE STRUCTURES. THIS AMBITIOUS PROJECT HAS BUILT UPON THE ACHIEVEMENTS OF FIB MC2010 (PUBLISHED IN 2013), THE PREVIOUS EDITION OF THE FIB MODEL CODE FOR CONCRETE STRUCTURES.
The fib (Fédération Internationale du Béton/ International Federation for Structural Concrete) is delighted to announce that the new Model Code is now available.
Concrete is the most used construction material in terms of annual tonnage, being used for innumerable buildings and structures over some 2000 years. Globally, it provides a very adaptable means of creating the facilities and assets required to meet the needs of society. Furthermore, this has been done largely using locally available material resources. Modern concrete technology has extended those inherent advantages, creating an extensive family of concrete types with a diverse range of properties and performances, allowing concrete to be tailor-made for a great variety of uses.
While concrete has a low CO2-eq value per unit weight, its prodigious global usage has resulted in it becoming a significant contributor to climate change, which has been described by the United Nations as “the defining issue of our time”. This
has served as a compelling catalyst for change and the increased emphasis on sustainability in the fib Model Code for Concrete Structures (2020), also known as fib MC (2020). This distinguishes it from the foci of preceding editions of that fib Model Code.
fib MC (2020) takes sustainability as a fundamental requirement for design, based on an all-inclusive treatment of societal needs and impacts, lifecycle cost and environmental impacts. The Code adopts an integrated life-cycle perspective, which means that the requirements for social performance will have defining implications for subsidiary performance requirements that are crucial in designing new structures and extending the useful life of existing ones. These performance requirements include aspects such as human and environmental safety, serviceability, durability, robustness of the structure, resilience of its functionality, aesthetics, adaptability, maintenance and reducing CO2-eq emissions.
The Code presents new consensus guidance on developments relating to concrete structures and structural materials, as well as providing a basis for future Codes for concrete structures. It addresses significant advances made on a range of issues –including those relating to structural design and analysis methods, seismic design and assessment procedures, durability, structural monitoring, service life design, structural assessment throughlife and making interventions to adapt existing structures or enhance their performance to accommodate revised requirements or extend their useful life.
As with previous editions of the Model Code, fib MC (2020) not only specifies requirements and recommended practices but also gives explanations in the adjoining informative column of the document. The comprehensive Code takes a holistic life-cycle perspective considering both design and life-cycle management aspects. The overall goal is for the new version to be better able to support designers and other construction
professionals involved in the creation and lifecycle management of concrete structures to meet complex future demands and the very challenging circumstances that they are expected to encounter in the years ahead.
fib MC (2020) will be supported by various Bulletins and associated publications, which will provide additional technical background and guidance to supplement the Code’s detailed information. It has involved contributions from over 1400 technical experts from 67 countries, which, taken with the support of fib’s 42 national member bodies, make it an exceptional and truly global effort.
The fib Model Code can be accessed online via annual subscription. There is a 50% discount on this option (CHF 140) until 31 December 2024 – https://fib-international.org/publications/modelcodes/model-code-2020.html
Hard copies can also be purchased directly from fib, but at full price (CHF 130 + CHF 83 postage) – https://fib-international.org/publications/fibbulletins/fib-model-code-2020-detail.html
fib is a not-for-profit association formed by 42 national member groups and approximately 2500 corporate and individual members in more than 100 countries. Its mission is to develop at an international level the study of scientific and practical matters capable of advancing the technical, economic, aesthetic and environmental performance of concrete construction. The knowledge developed and shared by the fib (Bulletins, events, workshops, courses, etc) is entirely the result of the volunteer work provided by its members. The organisation was formed in 1998 by the merger of the Euro-International Committee for Concrete (the CEB) and the International Federation for Pre-stressing (the FIP). These predecessor organisations had existed independently since 1953 and 1952, respectively.
Concrete NZ’s Learned Society is a long-time National Member of fib, with Moustafa Al-Ani the current New Zealand fib Head of Delegation.
The fib Symposium Organising Committee is pleased to announce that a Model Code workshop will be held at Te Pae Christchurch Convention Centre during the morning of Thursday 14 November. Visit the Symposium website for all the workshop details, as well as information about “other events”www.confer.co.nz/fib2024/other-events/
Those members wishing to purchase a hardcopy or gain online access to the fib Model Code should contact the Learned Society convenor – Adam Leach – learnedsociety@concretenz.org.nz
ROB GAIMSTER, CONCRETE NZ, CHIEF EXECUTIVE
A YEAR AFTER LAUNCHING ITS 2050 ROADMAP TO ACHIEVE NET-ZERO CARBON, THE NEW ZEALAND CEMENT AND CONCRETE INDUSTRY, LED BY CONCRETE NZ, IS REFLECTING ON THIS MILESTONE, GAUGING PROGRESS AND PLANNING NEXT STEPS.
2050 ROADMAP – 1-YEAR ON
Our industry is determined to significantly reduce greenhouse gas emissions, ensuring New Zealand meets its international climate obligations. The Roadmap outlines a clear plan for how we will do this and play a major role in building a sustainable future.
Part of a global initiative recognised by the United Nations (UN), the Net-Zero Carbon Concrete Industry for Aotearoa New Zealand: Roadmap to 2050 sets out the industry’s strategy to create sustainable concrete, targeting all key players in the concrete value chain, from cement manufacturers to construction companies, designers and specifiers.
By 2030, the goal is to cut direct and electricityrelated emissions (Scope 1 and 2) by 44% from 2020 levels, with a total emissions reduction of 29% when indirect emissions (Scope 3) are included. This will equate to around 400,000 tons of CO2 emissions reductions annually.
By 2050, the industry aims to produce net-zero carbon concrete, or potentially negative emissions.
In the near term, the focus is on increasing the use of supplementary cementitious materials (SCMs) and alternative fuels. From 2030 to 2050, attention will shift to deeper emissions reductions through CCUS technologies and natural carbon uptake via concrete recarbonation.
Key strategies (or levers) include reducing emissions from clinker production (9% by 2030 / 12% by 2050), cement binders (29% / 28%), and improving efficiency in concrete production (2% / 9%) and design & construction (5% / 10%).
Carbon Capture, Utilisation and Storage (CCUS) technologies are expected to account for 34% of the total reductions by 2050.
Over the past year, the availability of low-carbon SCMs, such as ground granulated blast furnace slag (GGBS) and fly ash, has significantly increased.
These materials replace a portion of traditional Portland cement, lowering the carbon footprint of concrete and aligning with sustainability goals.
The hat’s hard.
The decision isn’t.
bcito.org.nz
New Zealand’s leading building site.
2021/22 SUSTAINABILITY REPORT
Progress along the Roadmap’s decarbonisation levers will be gauged in part through Concrete NZ’s Sustainability Report, the first of which was released in early 2024.
The Report sets a clear baseline for measuring progress, underscoring a commitment to address our environmental and social footprints.
It details recent efforts in energy consumption and emissions, water use, waste management, and health and safety. The Report also examines how concrete aligns with the UN’s Sustainable Development Goals and explores mechanisms for improvement.
Data collection is now complete for the 2023 followup Report, which will be shared with stakeholders in the cement and concrete industry, as well as the broader construction and infrastructure sectors in late 2024.
Concrete NZ is now moving into the next stage of the Roadmap – the Transformation to a Net Zero Carbon Concrete Industry project (Transformation Project).
With funding from the BRANZ Building Research Levy and the Ministry of Building, Innovation and Employment’s (MBIE) Building Innovation Partnership and Concrete NZ, the primary aim of the Transformation Project is to gain a deeper understanding of the Roadmap’s levers and assist with their implementation.
To manage this effort in partnership with industry, Concrete NZ has appointed Tim Kleier as Sustainability & Policy Director and Vineet Shah as Concrete Industry Transformation Lead.
Defining the meaning of “low-carbon concrete”, determining how to specify it to ensure acceptable performance despite regional material variations, and identifying necessary changes in Standards based on a detailed understanding of its engineering properties are all key Transformation Project objectives.
A review of BRANZ project ER661 and international decarbonisation experiences will also be undertaken, with a priority on implementing SCMs and low-carbon clinker for immediate impact.
Quick-win strategies in design and construction using low-carbon concrete (e.g. stronger, thinner structural elements) will be identified, while the carbon reduction achieved on projects that specified low-carbon concrete will be assessed.
With an important milestone in the journey to a net-zero carbon future having been reached, the Transformation Project is set to enable the ambitions set out in the 2050 Roadmap.
The project promises to refine our understanding of low-carbon concrete and translate that knowledge into actionable strategies and tangible results.
With the support of industry experts and key stakeholders, Concrete NZ is committed to achieving a future where sustainable concrete is the norm.
The advancements and innovations that emerge from the Transformation Project will drive us forward to a more sustainable construction sector.
The future of low-carbon concrete is becoming a reality, with the momentum built over the past year just the beginning.
1.Mackechnie, J.R. (2021). ER66 Removing the barriers to the use of significant levels of SCMs in concrete production in NZ. BRANZ (Building Research Association of New Zealand). https://www.branz.co.nz/documents/3386/ER66_SCMs_in_ concrete_production_in_NZ.pdf
You can create truly amazing spaces with confidence using PFL 699 (SuperBlack). That’s because all of our colours use top quality Bayferrox® Oxides, which have been trusted by the ready mix industry for over 30 years.
The Declare label on our product packs lets you know our PFL 699 (SuperBlack) Oxide is socially and environmentally responsible too.
Colours may look different on print, so order some actual samples before making your final decision.
THE MASONRY SECTOR GROUP HAS RELEASED A CHINESE TRANSLATION OF THE CONCRETE MASONRY - SITE PRACTICE AND WORKMANSHIP GUIDE TO ENHANCE SKILL LEVELS ACROSS THE MASONRY TRADES.
Intended for all members of the building team, the Guide including site supervisors and brick and block layers, particularly within the growing Chinese construction community.
The Guide covers key aspects of masonry work, offering clear steps for preparation and execution on site. Extracts from relevant Standards and Codes of Practice are included for easy reference and features an action checklist to ensure highquality workmanship.
By following the Guide, builders can achieve durable and consistent brick and blockwork that requires minimal maintenance throughout its design life. All components, including mortar, grout, and rebar, must meet the standards set by the New Zealand Building Code.
Visit the Concrete NZ website to download a copy – www.concretenz.org.nz
Contech is proudly NZ-owned with over 60 years of local knowledge and experience, complemented by our membership in the international BBR Network of specialist concrete engineering contractors. Find out
Future Roads is an annual two-day conference for the New Zealand roading sector providing a forum for strategy, discussion, and execution. It is New Zealand’s largest dedicated roading conference with an expected attendance of over 300 for 2024.
Date: Wednesday 20 and Thursday 21 November 2024
Location: Claudelands Events Centre, Hamilton
Theme: Optimising your roading investment
Key topics include:
• leadership and strategy
• technology
• materials
• smart traffic signal technologies and control centres
• procurement
• network futureproofing
The target audience includes road owners (NZTA, councils, PPP partners), contractors, consultants, service and supply-side, regulators and aggregate producers. It attracts many delegates from local government.
Concrete NZ’s key messages to these important stakeholders will be:
Compared to asphalt over a 30-40-year lifespan, concrete roads are:
•more cost-effective with minimal maintenance,
•lower in embodied CO2, and
•less vulnerable to price volatility, reducing procurement risk.
THE CONCRETE NZ PLANT AUDIT SCHEME, WHICH ENSURES PRODUCERS MEET THE HIGH STANDARDS NEEDED TO COMPLY WITH NEW ZEALAND’S BUILDING CODE, AND WHICH SAVES TIME AND MONEY FOR ENGINEERS AND THEIR CLIENTS, HAS REACHED ITS 60-YEAR ANNIVERSARY.
Concrete New Zealand (NZ) chief executive Rob Gaimster says: “We’re delighted that the Plant Audit Scheme has stood the test of time and proven its worth.”
The Scheme was set up six decades ago to provide an independent audit of a ready mixed concrete plant’s own quality systems.
Concrete for consented construction projects must should building Standard NZS 3104 Specification for
Concrete Production. This provides assurance that the concrete will achieve its strength and durability requirements in application.
“The easiest way to do that is to purchase concrete from a plant that’s a member of the Concrete NZ Plant Audit Scheme,” says Rob.
“Without the Scheme, purchasers and specifiers would be faced with a costly and time-consuming audit of concrete quality for each construction project.”
The Plant Audit Scheme audits Concrete NZ Readymix Sector Group member’s concrete plants as defined in NZS 3104:2021 Specification for Concrete Production. The Scheme provides a rigorous audit of the quality systems in place at a ready mixed concrete plant.
FOR A FULL LIST OF SCHEME MEMBERS AND THEIR AUDITED READY MIXED CONCRETE PLANTS VISIT THE SCHEME WEBSITE www.rmcplantaudit.org.nz
In 1964 the Scheme, then operating under the New Zealand Ready Mixed Concrete Association’s banner, had 30 foundation plants, while 1963 statistics indicated that the average national quarterly production was around 134,464 m3 (175,873 yd3).
This year, the Scheme boasts around 200 plants and average quarterly production nationwide of close to 1 million m3
Audits are carried out by the Plant Audit Committee of five or more registered engineers, with members including a representative from Engineering New Zealand (ENZ).
Among performance criteria audited are:
• Mean concrete strengths and coefficients of variation
• Aggregate quality by testing and monitoring
• Weigh scale calibration and accuracy
• Mixer efficiency tests
• Laboratory equipment calibration
• Production and testing record keeping
• Technician training
• Plant operator performance
• Effectiveness of plant engineer’s monitoring of quality controls
The Scheme is certified to ISO 9001 and undergoes an annual external validation audit by the New Zealand branch of Bureau Veritas, a global leader in testing, inspection and certification services.
“Concrete NZ’s Plant Audit Scheme remains the go-to mechanism for producers to demonstrate that their product meets the required industry Standards,” says Rob.
For more information about the Scheme and for a list of audited plans, visit the websitermcplantaudit.org.nz
• Made in Belgium
• Remote wireless operation
• Rear wheel steer
• 3D Laser Kit option
• Distributed, supported and serviced here in New Zealand by
THE NGĀ ŪRANGA KI PITO-ONE (NGAURANGA TO PETONE) SECTION OF TE ARA TUPUA IS A KEY COMPONENT OF THE GROUNDBREAKING THE PROJECT AIMED AT BUILDING A SAFE, SCENIC, AND SUSTAINABLE SHARED PATHWAY, AND IMPROVING RESILIENCE BETWEEN WELLINGTON AND LOWER HUTT.
The $348.7 million Ngā Ūranga ki Pito-One section is a 4.5-kilometre pathway along the shores of Wellington Harbour, connecting Wellington City to Lower Hutt from the Ngauranga Interchange to Honiana Te Puni Reserve in Pito-One.
It will join with the completed Pito-One to Melling section of Te Ara Tupua to the north and the Thorndon Quay / Hutt Road project to the south.
Main construction works began in 2023, with project completion expected in 2026, involving up to 100 workers at peak times as
the workforce fluctuates with the project’s progress.
This pathway will serve as a link for cyclists and pedestrians, enhancing safety and accessibility while providing views of the harbour and the surrounding landscape.
By 2030, NZTA estimates over 2,100 weekday bike trips on the path, along with 360 walking or running trips and 290 e-scooter trips.
The project is part of a broader effort to promote sustainable transportation options and improve public health through increased physical activity.
Over its entire length, Te Ara Tupua is more than just a connecting route; it represents a forwardlooking integration of innovation, environmental stewardship, and sustainable design. The project underscores the importance of enhancing the coastline while respecting the ecological needs of the surrounding marine environment.
The overall project is being delivered by the NZ Transport Agency Waka Kotahi in partnership with iwi mana whenua, Taranaki Whānui ki te Upoko o te Ika, and Ngati Toa Rangatira.
The name Te Ara Tupua was gifted to the project by Kura Moeahu (Te Āti Awa) which references to the two tupua Ngake and Whātaitai who according to the traditional narrative created Te Whanganuia-Tara (Wellington Harbour).
At its heart lies the intricate use of concrete in various forms along the Ngā Ūranga Ki PitoOne section - including seawalls, tide pools, reef pyramids units and the innovative XBlocPlus. These concrete elements are not just structural necessities; they are vital to achieving the project’s goals of resilience, durability, and environmental harmony.
NGĀ ŪRANGA TO PITO-ONE – KEY ELEMENTS
• Shared Path - A 4.5km shared path with a 5m wide sealed surface on the seaward side of the Hutt Valley Railway Line.
• Ūranga (Landings) - 6 spaces will be built along the shared path enabling planting and creating areas for people to use.
• Shared Path Bridge - A new architecturally designed bridge at Ngā Ūranga provides access over the railway for pedestrians and cyclists. See above for rendering.
• Embankments - Sloping embankments (known as revetments) built of either boulders or concrete XBlocPlus units, will protect the path, road and rail line from wave erosion.
• Seawalls - Six vertical seawall segments protect the shared path and are approximately 600m in length. Seawalls are used where necessary to avoid building revetments over highvalue habitat areas.
• Offshore Habitats - Two small offshore habitats for coastal bird life, constructed of naturalised rock forms, at least 40m horizontal distance from the shoreline.
• Tide Pools - Constructed from concrete, the pools are installed in the waterfront embankments (revetment) and Offshore Habitats to provide for marine life and serve as educational tools.
• Enhanced Reef - Enhancing underwater reef habitats using natural or artificial structures, like concrete reef pyramid units, to support marine biodiversity and promote habitat diversity.
Concrete plays a fundamental role in the Ngā Ūranga Ki Pito-One section of Te Ara Tupua, providing the structural backbone for several key components, including seawalls, tide pools, reef pyramids and the innovative XBlocPlus units. These elements are crucial for ensuring the pathway's durability, safety, and environmental compatibility.
Concrete NZ Readymix Sector Group members Firth Industries and Higgins Concrete were key suppliers to the project, while Precast Sector Group member Preco Precast Concrete manufactured the XBlocPlus units at its Otaki plant.
SEAWALLS:
Ngā Ūranga Ki Pito-One provides extra resilience to the crucial infrastructure corridor between Ngā Ūranga and Pito-One. This includes State Highway 2 and the railway corridor. The project provides significant protection from Wellington Harbour’s harsh coastal environment, characterised by strong winds and powerful waves. To withstand
these conditions, the project includes robust seawalls made from high-quality concrete.
The seawalls are constructed from concrete to provide durability, minimal maintenance, and protection against ocean battering and shoreline erosion, crucial for serving the community for decades. Their design also considers aesthetic appeal, ensuring they blend seamlessly with the natural surroundings while offering robust protection.
Concrete NZ member Higgins Concrete supplied the Ngā Ūranga seawalls, with barge being the only viable delivery option. When sea conditions were favourable Higgins Concrete dispatched 2-4 trucks with a bespoke mix design with extended slump life, high durability, macro synthetic fibres and stabiliser. A Higgins Concrete technician was always on standby to dose mixes with an accelerator to ensure set times were met within timeframes.
The six seawalls 600 m total length was a significant contributor to the 2,700 m3 of concrete used during the overall construction of Te Ara Tupua.
Ngā Ūranga Ki Pito-One also includes concrete tide pools along the pathway and on the two small offshore habitats. These pools are crucial for enhancing marine biodiversity. Crafted from specially designed concrete forms, the pools replicate natural rock pools, providing habitats for various marine life.
Concrete’s versatility allowed the pools to be moulded into different shapes and textures, enabling the creation of realistic and functional habitats for marine species. Moreover, concrete’s durability makes it ideal for withstanding the harsh marine environment.
Perhaps the most innovative use of concrete in the project is the incorporation of 6,800 interlocking XBlocPlus units as part of the protective coastal embankments which are also constructed in part using 144,000 tonnes
of natural rock quarried in Golden Bay and the Central North Island.
Xbloc® is the company that led their original development, with Dutch company Delta Marine Consultants (DMC) tailoring the Xbloc for Te Ara Tupua as the XblocPlus units, which were manufactured in Otaki at the Preco yard with ready mixed concrete supplied by Higgins Concrete, and colour (Bayferrox 330 black) by Peter Fell Ltd.
These concrete blocks, designed to protect the pathway from wave action and prevent coastal erosion, form an interlocking "armour" that provides a resilient coastal edge.
XBlocPlus is a relatively new technology that offers several advantages over traditional coastal protection methods. Unlike conventional concrete blocks, which rely on mass and weight to resist wave forces, XBlocPlus units are designed to dissipate wave energy through their unique interlocking shape. This efficient design reduces costs and environmental impact while providing superior protection against wave action.
Starting from a standard design, variations of the blocks (including colours) have been developed with coastal engineers, marine ecologists and iwi cultural design lead Len Hetet. The result was a bespoke ecological block pattern grounded in the cultural narrative of Te Ara Tupua, named Te Ripowai, meaning ‘the rippling waters’, which is about how we capture the aspiration around guardianship. Beneath the water the patterned surfaces provide opportunities for marine life to grow.
Weighing between 2.4 t to 3.1 t depending on the shape, the interlocking design of the XBlocPlus allows for easy installation and maintenance, reducing the long-term costs associated with
traditional coastal protection methods.
These also contribute to the project’s environmental and ecological mitigation measures alongside the offshore habitats and the enhanced reef units.
In addition to the XBlocPlus units, the project also includes the use of concrete reef units, also referred to as ‘Pyramids’, which were designed to mitigate the loss of rocky reef habitat from building the pathway. These reef units are strategically placed as part of the Reef Enhancement project element to encourage the growth of marine flora and fauna, enhancing the ecological value of the area.
The reef units were designed by Australian company called MMA Offshore who are leading subject matter experts in marine enhancements with over 35 successful artificial reef projects across the world.
MMA Offshore utilised a local precast subcontractor, Brian Perry Civil, to fabricate (and later install) the reef units at its local Seaview plant with ready mixed concrete supplied by Concrete NZ member Firth Industries. The 560 m3 of low-
carbon concrete mix contained 30% fly ash as cement replacement, and was high strength, selfcompacting and reinforced using steel fibres1
The reef units are constructed from concrete and designed to encourage the growth of marine organisms, such as plants and shellfish. Over time, these structures will become encrusted with marine life, creating vibrant underwater ecosystems that support a wide range of species.
Over 5 ha there are 54 submerged units placed in clusters of three, which are 4 m long by 4 m wide, and 5 m tall, weighing approximately 22 tonnes. They will be 7-10 metres below sea level with a minimum 2 m clearance from the top of the pyramid unit.
Ngā Ūranga Ki Pito-One showcases the versatility and low-carbon sustainability of concrete by carefully selecting types that minimise the environmental footprint while optimising durability and performance, and by incorporating recycled materials into the mix to further reduce environmental impact.
1 https://www.firth.co.nz/news/concrete-reef/
Moreover, the project’s focus on creating new habitats and enhancing biodiversity demonstrates a commitment to environmental stewardship. By using concrete to create structures that support marine life and protect the coastline, the Ngā Ūranga Ki Pito-One illustrates how this material can be part of a sustainable and environmentally friendly solution.
Ngā Ūranga Ki Pito-One is a testament to the innovative use of concrete in modern infrastructure projects. By incorporating concrete seawalls, tide pools, XBlocPlus units, and reef pyramids, the project ensures the durability and safety of the pathway and also enhances its environmental and cultural value.
The careful consideration of the material’s properties and its impact on the environment reflects a broader trend in infrastructure development, where sustainability and resilience are key priorities.
As Te Ara Tupua progresses, it will serve as a model for future projects, demonstrating how concrete can be used creatively and responsibly to build a better, more sustainable future.
Te Ara Tupua Alliance has been formed to design and construct the project. The Alliance is a team comprising Waka Kotahi and their design and construction partners Downer NZ, HEB Construction and Tonkin + Taylor.
Waka Kotahi is partnering with Taranaki Whānui ki te Upoko o te Ika and Ngāti Toa Rangatira as iwi mana whenua. Our other partners include KiwiRail, Hutt City Council, Greater Wellington Regional Council, and Wellington City Council.
Concrete NZ members Preco Precast Concrete, Higgins Concrete and Firth Industries also lent their expertise to the project.
ENVIROCore is a range of cement replacements available for concrete manufacturers to deliver performance concrete with a lower embodied carbon impact.
ENVIROCore is a range of cement replacements available for concrete manufacturers to deliver performance concrete with a lower embodied carbon impact.
ENVIROCore is a range of cement replacements available for concrete manufacturers to deliver performance concrete with a lower embodied carbon impact.
ENVIROCore is a range of cement replacements available for concrete manufacturers to deliver performance concrete with a lower embodied carbon impact.
ENVIROCore provides manufacturers the opportunity to lower the carbon of concrete by replacing General Purpose cement with these alternatives. All products within the ENVIROCore range meet the New Zealand Standards.
ENVIROCore provides manufacturers the opportunity to lower the carbon of concrete by replacing General Purpose cement with these alternatives. All products within the ENVIROCore range meet the New Zealand Standards.
ENVIROCore provides manufacturers the opportunity to lower the carbon of concrete by replacing General Purpose cement with these alternatives. All products within the ENVIROCore range meet the New Zealand Standards.
ENVIROCore provides manufacturers the opportunity to lower the carbon of concrete by replacing General Purpose cement with these alternatives. All products within the ENVIROCore range meet the New Zealand Standards.
ENVIROC ore 100
ENVIROC ore 100
ENVIROC ore 100
ENVIROC ore 100
Granulated Blast Furnace Slag to provide heightened durability in high wear and harsh areas including marine and highly acidic or alkaline environments.
Granulated Blast Furnace Slag to provide heightened durability in high wear and harsh areas including marine and highly acidic or alkaline environments.
Granulated Blast Furnace Slag to provide heightened durability in high wear and harsh areas including marine and highly acidic or alkaline environments.
Granulated Blast Furnace Slag to provide heightened durability in high wear and harsh areas including marine and highly acidic or alkaline environments.
ENVIROC ore 200
ENVIROC ore 200
ENVIROC ore 200
ENVIROC ore 200
Fly Ash Products sourced from reputable suppliers to provide improved workability, lower heat of hydration in large mass pours.
Fly Ash Products sourced from reputable suppliers to provide improved workability, lower heat of hydration in large mass pours.
Fly Ash Products sourced from reputable suppliers to provide improved workability, lower heat of hydration in large mass pours.
Fly Ash Products sourced from reputable suppliers to provide improved workability, lower heat of hydration in large mass pours.
LISTED BELOW IS A SELECTION OF RECENTLY ACQUIRED MATERIAL BY THE CONCRETE NZ LIBRARY. MEMBERS CAN EMAIL LIBRARY@CONCRETENZ.ORG.NZ TO BORROW THESE ITEMS.
SACRED MODERNITY: THE HOLY EMBRACE OF MODERNIST ARCHITECTURE
BY JAMIE MCGREGOR SMITH
Sacred Modernity documents the dramatic shift in ecclesiastical architecture across post-war Europe. Spurred on by the modernising impulses of the Second Vatican Council in the early 1960s, and in search for an appropriate architectural language that showed that the Catholic Church was still relevant to the modern world, this was the period when the church married the atheist architect and bore a child of pure form. Among these structures, some exude a joyful antagonism, while others emanate a cold minimalism. Boldly designed, outrageous and provocative for their time, the aesthetic of this period still ignites great debate between modernists and traditionalists.
Half a century on, this study traces how their materials and ideals have matured and patinated. Remaining amongst the most unique buildings within our public sphere, they are future visions from the near past that seem to anticipate societies current shift away from organized religion towards an individual spirituality. The book represents the first attempt by a photographer to collate the religious architecture of the mid-century high modern years that took many forms, from Brutalism to Structural Expressionism, under a singular artistic vision.
ICE HANDBOOK OF CONCRETE DURABILITY: A PRACTICAL GUIDE TO THE DESIGN
BY MARIOS SOUTSOS (EDITOR)
This 2nd edition is a comprehensive practical reference for professionals involved in the design and maintenance of concrete structures of all types. With contributions from a range of international experts,this text combines a thorough but accessible exposition of the principles of durable concrete design with a hands-on approach to its application in construction projects. Extensively revised and updated throughout, this edition includes four new chapters, including chapters on non-destructive testing and structural health monitoring, and lessons learnt by expert witnesses involved in construction disputes, as well as new case studies of durability problems and solutions.
CONCRETE JUNGLE: TROPICAL ARCHITECTURE AND ITS SURPRISING ORIGINS BY GESTALTEN
Combine concrete’s stoicism with luscious vegetative environments and you get to the language of tropical modernism. In continuity with its founding principles from the mid-20th century, today’s architectural visionaries renew the use of raw materials, such as exposed concrete, to explore functionality rather than aesthetics.
Regardless of whether projects are created in total symbiosis with the tropical landscape or surrounded by flourishing nature, Concrete Jungle presents the dichotomy of the rough material being softened through its interaction with the interior and exterior. When grey meets green a never-ending range of impressions awakens.
Go in the draw to win a copy of Sacred Modernity: The Holy Embrace of Modernist Architecture by Jamie McGregor Smith answer the following question:
Across 11-13 November Concrete NZ’s Learned Society is hosting the fib Symposium at Te Christchurch Convention Centre. What does the acronym “fib” stand for?
Email your answer to library@concretenz.org.nz
Entries close Friday 15 November 2024.
Congratulations to Sebastian Bach of Skid Row Concrete, who correctly answered the Vol. 63 Iss. 01 Library Quiz to receive a copy of Raw Concrete: The Beauty of Brutalism by Barnabas Calder.
Concrete NZ
Readymix Sector Group
Ph (04) 499 0041
Chair: Kerry Newton
Convenor: Rob Gaimster
Concrete NZ
Masonry Sector Group
Ph (04) 499 8820
Chair: Dene Cook
Convenor: Ralf Kessel
Concrete NZ
Precast Sector Group
Ph (04) 499 8820
Chair: Richard Flanagan
Convenor: Dave McGuigan
Concrete NZ
Learned Society
Ph (04) 499 8820
President: Rick Henry
Convenor: Adam Leach
Concrete NZ Reinforcing Stakeholder Group
Ph (04) 499 8820
Chair: Peter Ensor
Convenor: Dave McGuigan