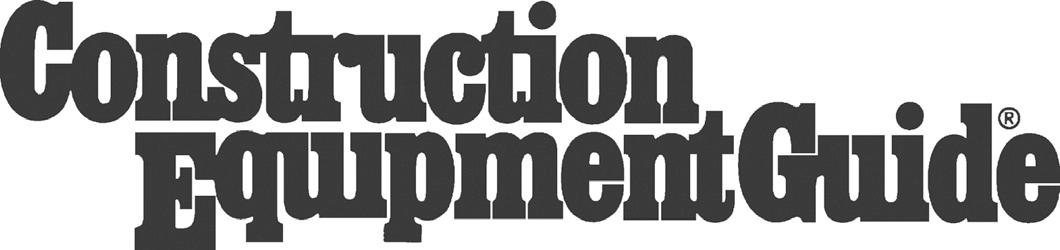
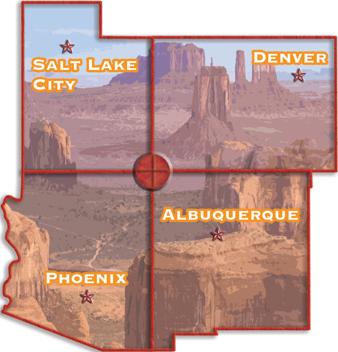
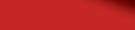
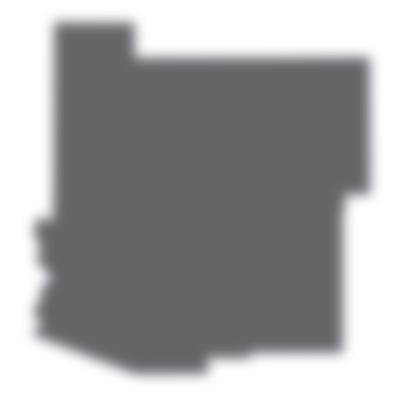
By Cindy Riley CEG CORRESPONDENT
To enhance safety and improve traffic flow, the Colorado Department of Transportation (CDOT) is constructing a diverging diamond interchange (DDI) at the intersection of Airport Road and Powers Boulevard (Colorado Highway 21 / U.S. Highway 24).
Work in Colorado Springs by contractor WW Clyde includes bridge and ramp construction, placing embankments, concrete paving, overhead sign structure installation, new traffic signal systems and permanent water quality ponds.
“With more than 50,000 vehicles traveling Powers Boulevard each day here at Airport Road, along with the Powers Corridor planning project, the need for an interchange at this location was indicated and was added to our 10-year priority project list,” CDOT Region 2 Transportation Director Shane Ferguson said. “This DDI will address congestion, improve safety and add multimodal facilities that will allow for a safer and more comfortable travel experience for cars, pedestrians and cyclists.”
Powers Boulevard (CO 21) extends from Colorado Highway 16 to Colorado Highway 83, conveying commercial and personal travel
By Eric Swan
SPECIAL TO CEG
Heavy highway asphalt paving is a highstakes dance of people, equipment, traffic, schedules and materials. It requires the best at it to be smart, organized and intentional.
It also doesn’t hurt to have a little attitude, be a little lucky — and have a whole lot of commitment — to the work itself and to the team around you.
Having spent time with the team from
Albuquerque Asphalt as they completed a deep mill and fill project on I-40 in Albuquerque — it is evident that the company has these traits in spades.
The project included a deep mill across two lanes of interstate and two lifts of fresh asphalt — all put down at night with the road being turned back over to the public at 5 a.m. every morning.
For Albuquerque Asphalt — a team of more than 200 people spread across asphalt, dirtwork, concrete, crushing and production crews
— it’s an extremely deliberate deployment of people and resources to ensure optimal asphalt quality while also working efficiently enough to make business profitable. That includes the timely and efficient performance of preventive maintenance (PM) activities.
Supported by Four Rivers Equipment, Albuquerque Asphalt restructured its PM work to move away from larger service trucks that required drivers to have a CDL and HAZMAT endorsement because it became increasingly difficult to find those drivers, and those who do
have the endorsements don’t always have the mechanic’s mindset to do PM work.
The solution: a two-person team matched with a truck hauling a Multi-Tank Oil [MTO] 690 trailer from Thunder Creek Equipment.
In addition to the practical convenience of nighttime paving — especially in New Mexico where the combination of hot asphalt and high
see 1-40 page 4
As Hitachi Construction Machinery Americas continues rapid growth and expansion in the construction and mining markets, there remains a commitment to provide customers with the lowest cost of operation. Parts availability and location are critical to minimizing downtime and lowering shipping costs for customers. Hitachi Construction Machinery Americas is committed to its customers and dealer network with $140 million in parts inventory spread across its warehouses in the Americas to ensure high parts availability.
To optimize regional dealer and customer support while further strengthening the supply chain, Hitachi Construction Machinery Americas announced the addition of a 173,000-sq.-ft. warehouse in Salt Lake City, Utah. This facility will provide support seven days a week and expedite quick shipping to dealers and customers in the construction and mining markets, according to the company.
The Denver Broncos broke ground on Aug. 29 on Broncos Park Powered by CommonSpirit, a $175 million headquarters and practice facility in Engelwood, Colo., according to msn.com.
The privately funded building is due to be completed in time for the 2026 season, msn.com said. It will be attached to the existing Pat Bowlen Fieldhouse.
“Designed in a contemporary style reflective of Colorado with a focus on enhancing player health and performance, the Broncos’ facility will bring together football and business operations in an inspirational, collaborative and modern environment,” the team said in a press release. “The three-story, 205,000square-foot training facility will mark a 30 percent increase in size over the existing facility.”
The new construction will replace an exist-
ing building dating to 1990. Owner Greg Penner told 9NEWS that the current facility has several spaces that are too small, including the locker room.
The project will include a large excavation where a grassy berm used by fans will be leveled and rebuilt on the field’s other side. The locker room and headquarters will go where the original berm was located.
Training camp will be a bit challenged in 2025, team President Damani Leech told 9NEWS. The team likely will add temporary stands to the parking lot, which may decrease capacity a bit.
Penner told 9NEWS that there were no updates on a new stadium. Empower Field at Mile High opened in 2001 and the ownership group had made some upgrades in recent years.
(All photos courtesy of Denver Broncos.)
ity for us, our goal is to improve the speed of delivery to our customers; maintain world class fill rates; and be a highly reliable partner,” said Jeremy Dieterle, vice president, parts Hitachi Construction Machinery Americas.
Parts and service support are key drivers of total cost of ownership. Investing in regional warehouses allows Hitachi Construction Machinery Americas to continue to lower the cost of ownership for its customers and ensure that downtime is minimized. Hitachi Construction Machinery Americas warehouses cover several time zones across the Americas to ensure parts are readily available when needed.
Now, when a machine down event occurs, the western region of North America will have quicker access to parts for their Hitachi machines.
“When we were deciding upon the location for this warehouse it was important for us to be close to our customers. While this requires additional investment and complex-
The operation of the Salt Lake City parts warehouse will continue to shorten delivery times for customers and demonstrate a continued investment in after-sales support, according to the company. The warehouse complements an existing supply chain network that stretches from Georgia to Indiana to Illinois and now Utah. Hitachi Construction Machinery Americas has invested in specialized technologies and equipment to efficiently handle all parts from the smallest O-ring to the largest EX8000 mining shovel parts.
For more information, visit www.hitachicm.us/support/.
The Arizona Department of Transportation is moving forward with a project in 2025 that will reconstruct and widen Interstate 10 between Kino Parkway and Country Club Road southeast of downtown Tucson.
On Aug. 16, the State Transportation Board awarded the design-build project to SundtJacobs. At $600 million, it will be the largest highway construction project in southern Arizona history.
The project will include:
• Widening I-10 to three lanes in each direction between Kino Parkway and Alvernon Way, and to four lanes in each direction west of Kino Parkway.
• Reconstructing the interchange at Kino Parkway.
• Removing the existing interchange at Palo Verde Road.
• Constructing a new interchange Country Club Road that will provide access for traffic that currently uses the interchange at Palo Verde Road to allow for safer traffic move-
ments to and from I-10.
• Constructing a new westbound on-ramp at the Alvernon Way interchange.
• Constructing an I-10 undercrossing to connect the North and South Kino Sports Complex.
Construction is expected to begin in mid2025 and continue through 2028.
The project will be the first to result from a study completed in 2020 that recommended how to best improve mobility along a roughly 10-mi. stretch of I-10 from I-19 to Kolb Road. The study also identified an alignment for an extension of State Route 210 (Barraza Aviation Parkway) along Alvernon Way that will connect I-10 to downtown Tucson.
ADOT is planning to share more detailed design plans for the corridor and provide an opportunity for the public to speak with members of the design team at a community open house event in early 2025.
For more information, visit I10KinotoCountryClub.
1-40 from page 1
daytime temperatures can be brutal — Albuquerque presents a unique logistical challenge as it relates to traffic: There are only so many bridges that cross the Rio Grande River. Minimizing traffic disruption is critical.
Albuquerque Asphalt plans each day of milling/paving intricately to ensure that it can get the day’s work milled and covered with at least one lift of asphalt so that it’s drivable by 5 a.m.
With the deep mill on this project, each section works in a three-day cycle: Day 1: Mill a section and pave lift one; Day 2: Mill a section and pave lift one; Day 3: Pave the final lift across the previous two days’ work. All equipment is lined up in the interstate median during the day and brought back to life again after dark to repeat the cycle.
The company has been at the forefront of many trends in the industry that have allowed larger paving companies to streamline operations. It owns its asphalt plant — controlling the production, quality and access to asphalt.
It also does its t quality testing at an in-house lab. And it has been longtime leaders in recycling crushed and milled materials, including using it as road base and by introducing a certain percentage of millings into the hot mix.
With its growth has come more equipment and greater scrutiny on uptime. And a changing mindset on how to perform PM work. The previous method involved larger lube trucks that required drivers with a CDL and HAZMAT endorsement.
As the fleet grew, it became more difficult to find those drivers, and if they did find them — they were not always interested in doing PM work.
“You can find CDL/HAZMAT drivers, but you’ve got to find the CDL/HAZMAT drivers willing to do this type of work,” said Jacky Spencer, vice president of operations, Albuquerque Asphalt. “We’ve taken younger people with more of a mechanic background and a good work ethic, and we train them to this specific task.”
It was this challenge that led Four Rivers Equipment to introduce Albuquerque Asphalt to the MTO 690 trailers. The com-
pany now owns three.
“The last few years you can’t find anyone,” said Robert Wood, president and partner, Albuquerque Asphalt. “So, if you limit yourself to CDL-driven service trucks, that limits your pool of employees. My manager said, ‘We can’t find CDL drivers’, and these were available, and we thought it was a good idea.
“Now we have three of these units, and we haven’t bought any more service trucks.”
Spencer and Joseph Otero, a superintendent with the company, have spearheaded much of this new approach to PM. It revolves around the MTO 690 and a two-man crew that pulls up to the median, right-of-way (or wherever the equipment might A Roadtec SB-2500e material transfer vehicle
be staged), and they go methodically from machine to machine performing PM work.
One fuels while the other greases. One fills diesel exhaust fluid (DEF) while the other blows out air filters. One does a walkaround of the machine to identify any issues while the other tops off fluids. And then they move on to the next machine.
The Thunder Creek MTO 690, with its ability to hold critical service fluids in combination up to 690 gallons, is the centerpiece of this operation. Towed behind any of the company’s pickup or service trucks, the trailers easily navigate each job site and allow each team member to get close to the equipment they are working on.
“If you take a big lube truck, and you take this setup — this is still a lot easier to get inside of [safety] barrels and get next to stuff,” Spencer said. “I like that they’re not climbing up and down the side of the truck all the time. That’s a big deal for me. Everything is really accessible.”
The standout feature: Because each fluid compartment holds less than 119 gallons (115 gallons is the max), the trailer does not require a HAZMAT endorsement — and when matched with the right truck, does not require a CDL. Albuquerque Asphalt outfits each of its trailers with a combination of diesel, engine oil, hydraulic fluid, DEF, a greasing system and an oil reclaim system — allowing each team to perform all critical PM work in the field. The on-board air compressor helps with numerous tasks, including blowing out filters.
“What’s nice about the Thunder Creeks is, when we go to do oil changes, you get the reservoir where you suck it up and put it in the tank as opposed to putting it in buckets — makes everything more efficient,” Otero said. “Greasing, fueling, oil changes. Then, at the end of the day, we regroup and dump everything out. It’s just rolling, rolling, rolling — it’s all
Albuquerque Asphalt equipment awaits a day’s work.
productive.”
The two-person crew gives the company flexibility in its staffing and helps ensure that PM work is completed promptly each day — versus being short-handed if a driver is unavailable. If one of the crew calls out, they can be substituted by any team member. This also has helped prevent unnecessary downtime on the weekends.
“We cut down the cost, as far as hours,” Otero said. “Instead of working 60-70 hours, you include these bad boys and break up the work evenly … everything gets done across the board and it’s not slowing us down.”
Four Rivers has helped Albuquerque Asphalt every step of the way — serving as both fleet consultants for the equipment and fleet management consultants as it relates to PM.
“Four Rivers is always looking for a way to improve our business,” Spencer said. “When they have new products, they don’t push them on us, they bring them to our attention. A big part of our success right now is because of Four Rivers. They always answer the phone. They’re available 24 hours, seven days a week, because that’s what we run. Having somebody like Four Rivers is huge.”
For Spencer, the new approach to PM and the flexibility of the Thunder Creek trailers are critical to the company’s highway paving success.
“They’ve been a game-changer for us,” he said. “Servicing equipment is a fast-paced job. Everything’s got to be checked. Fueled up. Oil levels checked.
“With the Thunder Creeks,” Otero said, “everything’s done, everyone’s happy, and we don’t have to worry about anything.”
Eric Swan is the territory sales manager of Thunder Creek Equipment.
(All photos courtesy of Albuquerque Asphalt.)
CDE, one of the leading suppliers of sand and aggregate washing solutions for the waste recycling and natural minerals processing sectors, has commissioned a wash plant for Granite Construction Co. at the company’s Coyote Pit in Grantsville, Utah.
On Oct. 23, CDE and Granite will present the innovative 550-plus tons per hour (TPH) sand and aggregate wash plant to the industry, along with CDE’s preferred partner Goodfellow Corp., as part of an open house preview.
Granite, one of the largest diversified construction and construction materials companies
in the United States, is a full-suite civil construction provider that delivers infrastructure solutions for public and private sector clients throughout the United States.
Granite’s operations include 35 aggregate and 59 asphalt plants across seven western states and one province, including Utah, Nevada, Arizona, Washington, Oregon, Alaska, California and British Columbia, Canada.
“Our goal is to efficiently produce the highest quality aggregates in our market to support our customers and their projects,” Granite Materials Manager Ric Skinner said. “It’s exciting to be partnered with CDE to build a plant
that does exactly that.”
“Projects of this scale require all parties to pull together, with meticulous planning, attention to detail and commitment,” Plant Manager Stormy Watne said. “We are very proud of our new wash plant and look forward to welcoming everyone to tour our operations.”
CDE Business Development Manager Ryan O’Loan elaborated, “The Salt Lake City metropolitan area is expanding at a rapid rate and resources are in high demand, which is the backdrop to this important Grantsville development. Granite’s latest materials operation can ensure a consistent and reliable supply of sand
and aggregates in the local market for many years to come, and we’re proud that it will be CDE technology that underpins the operation to help maximize its lifespan and realize its potential.
“With companies like Granite investing in CDE’s materials washing solutions, together we can address the global sand shortages, through proven design, efficient processing, optimized operations.”
The open house event takes place on Wednesday, Oct. 23 from 8 a.m. - 4 p.m. (MT).
For more information, visit cdegroup.com.
(All photos courtesy of CED.)
and functioning as part of the National Highway System. Airport Road serves as an east-west travel route through Colorado Springs and is a critical access point for the west gate of Peterson Space Force Base.
A DDI crosses traffic to the opposite side of the road across an interchange, so vehicles have unimpeded movement onto ramps. Left-turn movements which are a challenge with standard four-way interchanges are eliminated, reducing delays, conflict points and wrong-way entry to ramps.
Safety and mobility for passenger and
commercial vehicles traveling through El Paso County is essential, especially along a corridor that’s seen exponential growth over the past several years. Of the 103 crashes from 2018 to 2022, nearly 60 percent were rear-end crashes, which will be improved significantly by removing the signalized intersection on Powers Boulevard, thus eliminating stops on Powers Boulevard.
“It’s very rewarding to be a part of the team making tangible progress, from detention ponds to the erection of a bridge,”
CDOT Project Engineer Patti Henschen said. “The project will provide significant
benefits to the area, such as safer multimodal options and better traffic flow.”
Two DDIs have already been built in the area.
“The Powers/Research interchange has not been opened long enough to have solid data about its performance from a safety perspective, but it is operating effectively in greatly reducing the delays on Powers Boulevard at the once highly congested intersection,” CDOT Region 2 North Program Engineer John Hall said. “Full conversions of at-grade signalized intersections to DDIs are less common — more often
Crews are working on excavation, embankment, drainage, utility relocations, erosion control and preparing for bridge substructure work.
converting an existing interchange, but nationwide data shows expected total crash reductions of 24 percent.”
The I-25/Fillmore Street DDI was a conversion of the existing interchange and opened fully in 2017. Comparing five years of data before and after construction found a 50 percent reduction in all crashes and a 44 percent reduction in injury crashes.
With almost 100 years of experience building projects across the Intermountain West, WW Clyde is equipped for the project.
“WW Clyde is no stranger to complex projects that require attention to detail, meeting and beating schedules and providing owners with the best quality products,”
WW Clyde Project Manager Brooke Miller said. “Our production moves fast, but ensures the quality is met throughout all operations.”
WW Clyde Senior Project Manager Jim Klemperer said that maintaining traffic is the main challenge for the project.
“Ensuring the safety of construction crews and the traveling public is of the utmost importance to us, CDOT and all subcontractors.”
Crews are working on excavation, embankment, drainage, utility relocations, erosion control and preparing for bridge substructure work. Initial construction began in late June, with crews working the northeast and northwest corners of the intersection to clear the land, relocate utilities and perform a significant amount of excavation and embankment work.
Major construction and site work are required to build the new DDI. This
involves grading, bridge construction, electrical and signalization, walls and paving. The job requires moving 385,000 cu. yds. of embankment.
Klemperer said most of the work that will take place is off the mainline and will not significantly affect motorists.
“Temporary concrete barriers were placed prior to the project start during overnight hours to lessen impacts on traffic and congestion. There are now 24/7 shoulder closures to ensure the safety of construction crews and the traveling public.
“A portion of the initial phase of work required the closure of the northbound onramp to Powers Boulevard, which negatively impacted Peterson Space Force Base staff during the afternoon shift change. CDOT and our team worked closely with Peterson security and leadership staff to pivot and allow the ramp to be open from 3 to 6 p.m. during peak times of traffic.”
According to the Department of Defense, Peterson Space Force Base has more than 8,700 activeduty military personnel, 1,300 reservists, 10,000 family members, 1,900 civilians and 23,000 military retirees. Space Base Delta 1 also is headquartered here.
before the runoff enters adjacent waterways,” Klemperer said. “The proposed ponds will be located on CDOT property adjacent to the new interchange.”
Somewhat unexpected for crews is a significant amount of utility relocation work to be carried out by crews, who also must be aware of the forecast throughout construction.
“The Pikes Peak region experiences wide shifts in temperature from well below freezing in the winter to peak temperatures of 95plus degrees,” Klemperer said. “Snow and low temperatures affect concrete pavement cure rates. Project phasing has been developed to account for typical weather patterns,
A Caterpillar 299D3 compact track loader works on the diverging diamond interchange project.
“Peterson Space Force Base is one of three military installations in El Paso County and is a top employer for Colorado Springs,” Klemperer said. “Providing smooth traffic flow for personnel is crucial to the economy for Colorado Springs and surrounding communities.”
Bridge and ramp construction will be a significant undertaking. The two bridges are being built over busy Powers Boulevard. It will be a two-span bridge that will use two phases to get the superstructure work accomplished by shifting traffic during a series of night shifts to minimize impacts to motorists.
For concrete paving, crews will be using slipform paving equipment to pave most of the work, as well as hand pouring smaller sections. Also, to prevent pollution and degradation of waters from roadway pollutants, CDOT requires the installation of permanent water quality control measures that are selected, designed, installed, implemented and maintained using good engineering, hydrologic and pollution control practices.
“Water quality ponds are shallow depressions designed to protect the environment by filtering pollutants from stormwater runoff
but some delays may occur. Apps on cellphones will be used by all crews on the job to plan for upcoming inclement weather.”
Construction milestones include bridge girder placement, pouring the bridge deck, bridge completion and final traffic shifts on to the new DDI. Once the new interchange alignment is in place, old roadway segments will be abandoned and demolished.
Earthwork heavy machinery on site includes scrapers, dozers, loaders, trucks and excavators. For the construction of the bridges and ramps, concrete paving equipment, cranes and asphalt paving equipment will be required.
For Klemperer and the construction team on site, building the DDI will be time-consuming but well worth the investment.
“It’s rewarding to be a part of providing a safe way for people to get through the area in an organized interchange. This project will also help economic growth in the area by keeping traffic moving.”
The new intersection is being built away from the existing one, with work expected to be completed in 2026. CEG
(Photos courtesy of WW Clyde.)