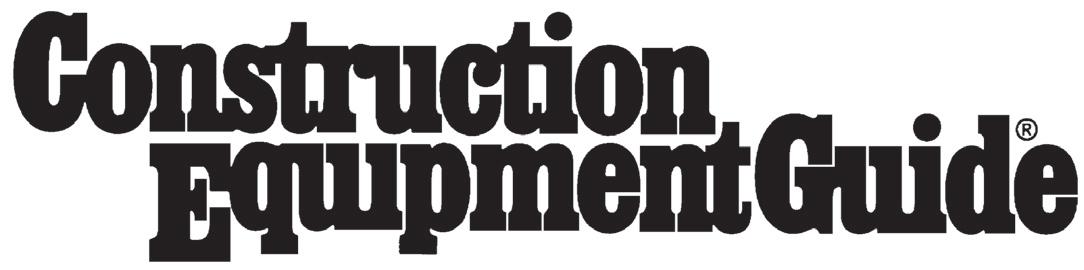
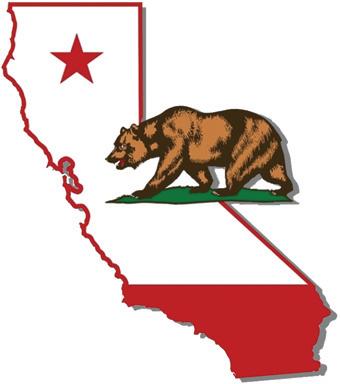
By Ruksana Hussain CEG CORRESPONDENT
The San Francisco County Transportation Authority said it is on schedule to complete the $126 million West Side Bridges Retrofit project on Treasure Island Road by addressing eight existing bridge structures that are seismically deficient with new retaining walls, roadways and a retrofitted bridge to meet current safety standards.
Construction began in June 2023 on the structures, which are a crucial connection between Yerba
Buena Island, Treasure Island and the Bay Bridge and will be completed by late 2026.
This is one part of a larger multimodal infrastructure improvement program on the Islands, the other two completed being the I-80 East Side Ramps Project (2016) and the Yerba Buena Island/I-80 Southgate Road and Interchange Project (2023).
The eight existing bridge structures are on the west side of Yerba Buena Island and comprise a viaduct along Treasure Island Road, just north of the San Francisco-Oakland Bay Bridge (SFOBB).
Furthering efforts to modernize California’s water infrastructure and improve public safety, the California Department of Water Resources (DWR) announced on Dec. 9, 2024, that it is starting construction on the $62 million Lake Perris Emergency Release Facility project in Riverside County.
Sukut Construction of Santa Ana, Calif., will build new infrastructure to safely redi-
rect water and protect the community should Lake Perris need to be lowered during an emergency event, like a major earthquake.
Planned improvements will include new levees, bridges and a local drainage system downstream of Perris Dam. With this additional infrastructure, water could be redirected from Lake Perris through levees into a drainage channel and ultimately into the
Perris Valley Channel. These upgrades, along with improved roadside landscaping and relocation of utilities, will protect the community and other infrastructure, including a local school, Interstate 215 and a water treatment plant.
“As earthquakes and extreme weather events are a constant threat to our infrastructure, DWR continues to modernize our facil-
ities to be resilient and protect the local community and California’s water supply,” State Water Project Dam Safety Services Manager David Sarkisian said. “The project’s improvements downstream of Lake Perris will provide additional protection for the community through the construction of drainage infrastructure.”
Global construction firm Skanska and joint venture partner Coffman Specialties announced on Dec. 12, 2024, the awarding of a contract by the San Bernardino County Transportation Authority (SBCTA) to carry out the $390 million Interstate 15 (I-15) Corridor Freight Improvement and Express Lanes Project.
The project involves the construction of two new express lanes with price-managed, tolled facilities on the median of both I-15 North and South, spanning a total of 10.8 mi.
“We, along with our partners Coffman Specialties and the San Bernardino County Transportation Authority, are excited to begin construction on these new express lanes along one of the region’s busiest interstates,” said James Bailey, executive vice president of Skanska USA Civil’s West Coast operations. “Once complete, these lanes will improve traffic flow, reduce congestion and save travel time for the over 200,000 daily commuters on this stretch of highway.”
The additional express lanes will join existing lanes
just south of the San Bernardino/Riverside County line and extend to Foothill Boulevard, encompassing the cities of Eastvale, Jurupa Valley, Ontario, Rancho Cucamonga and Fontana, Calif. Drivers will be able to enter and exit the I-15 Express Lanes from multiple points.
When completed, the express lanes will require a transponder for access, with toll pricing varying based on demand and distance. Drivers will be able to enter and exit those lanes from multiple locations.
Work includes the widening of both the inside and outside lanes of the roadway, modifications to bridge structures, installation of retaining walls, improvements to drainage and electrical systems, concrete and asphalt paving and earthwork.
The project will begin in January 2025 and is expected to be completed in July 2028.
The project funding comes from federal, state and local sources, including Measure 1, a half-cent sales tax San Bernardino collects for transportation improvements.
Liebherr Container Cranes Ltd. announced on Dec. 11, 2024, its first-ever contract to supply ship-to-shore (STS) container cranes to the West Coast of the United States.
TraPac Oakland, a container terminal operator in California, awarded Liebherr the contract for two STS cranes, marking an important milestone in the company’s history.
While Liebherr has previously supplied STS cranes to terminals on the East Coast, this is the first West Coast shipment of its STS cranes.
The cranes boast a 216-ft. outreach, a 173.83-ft. lift height, a span of 100 ft. and a lifting capacity of 66 long tons in twinlift mode.
The company said the contract underscores Liebherr’s growing presence in the U.S. market and its dedication to supporting the evolving needs of port operators through innovative technology and exceptional customer service.
“We are delighted to partner with TraPac Oakland and bring Liebherr’s innovative crane technology to the U.S. West Coast,” said Declan O’Sullivan, general manager –sales at Liebherr Container Cranes. “This milestone reflects our continued commitment to providing world-class container handling solutions tailored to the needs of terminal operators globally.”
The company said the cranes are equipped with advanced technology and semi-automation systems. Together with the latest anti-collision systems, these technologies ensure operational visibility, safety and precision in terminal operations.
“TraPac Oakland’s decision to invest in Liebherr’s advanced STS cranes marks a major milestone for our presence on the U.S. West Coast,” said Shane Kuhlmey, divisional director at Liebherr USA Co. for Liebherr Maritime Cranes. “This first-ever STS sale on the West Coast underscores not only the exceptional quality and innovation of our cranes but also Liebherr’s ability to support customers in this region.”
TraPac’s investment in new Liebherr cranes is part of a larger program to modernize and expand its Oakland terminal. Following a $67 million expansion in recent years that nearly doubled the terminal’s size, the new cranes will sup-
port increased cargo volumes and larger vessels while enhancing operational flexibility and berth productivity.
“This partnership marks the next exciting milestone for TraPac Oakland as we continue our journey of upgrading our service levels and exceeding customer expectations,” TraPac CEO Cameron Thorpe said. “Liebherr’s cranes, known for their exceptional quality and innovative design, will be instrumental in enhancing the efficiency and capability of our terminal. The collaboration with Liebherr and their
local team has been seamless, and we look forward to a successful long-term relationship.”
Liebherr USA Co, which is based in Newport News, Va., provides sales and service on behalf of 10 different Liebherr product segments, while Liebherr Container Cranes Ltd. of Killarney, Ireland, is one of the world’s leading manufacturers of ship-to-shore container cranes, rail-mounted gantry cranes and rubber tire gantry cranes.
(All photos courtesy of Liebherr Container Cranes.)
The stretch of rolling hills between the Napa Valley and Sacramento, Calif., is a picturesque place that’s rich in history and known for exceptional produce. Yolo County is a lively and flourishing home to more than 220,000 people across four cities and about a dozen unincorporated communities.
With a local economy that depends largely on its climate for agricultural success, it makes sense that the county’s strategic plan heavily promotes environmental stewardship. In fact, the Yolo County board of supervisors passed a resolution in 2020 to achieve a carbon-negative footprint by 2030.
As part of its progress toward that goal, the Yolo County fleet is one of the first in the United States to put a new VolvoDD25 Electric compactor to use.
California has some of the country’s most progressive clean air regulations and incentives, which led Yolo County to establish a Climate Action and Adaptation Plan that outlines more than 180 actions aimed at reducing greenhouse gas emissions and improving climate resilience.
A critical action on the list is electrifying the county’s fleet of on- and off-road equipment. In addition to the DD25 Electric compactor, the team has six electric forklifts and two electric pickup trucks with three more in the works.
“We’re taking a bold step forward in our commitment to sustainability by adding this electric compactor to our fleet,” said Lucas Frerichs, chair of the Yolo County board of supervisors.
“This pioneering addition not only supports our carbonnegative goal, but also exemplifies our dedication to innovative solutions that protect our environment and improve the quality of life for our residents. We are proud to lead by example, showcasing how electrification can enhance operations while fostering a cleaner, greener future for our community.”
Ben Lee, fleet superintendent, County of Yolo Fleet Services, said county employees prioritize selecting and utilizing equipment that aligns with the agreed-upon sustainabil-
ity initiatives, so the small electric compactor was a logical choice.
“The DD25 Electric will help us achieve our goals in several ways: by reducing emissions, lowering noise levels, being more energy-efficient, improving working conditions and promoting environmentally friendly practices,” he said.
Developed and built by Volvo Construction Equipment, the double-drum compactor will help Lee’s team with a variety of projects.
“We’ll use it to compact soil, gravel and other base materials for road and foundation projects, as well as rolling out and leveling asphalt during road construction and resurfacing,” he said.
Earlier this year, Lee was invited to an open house event at the Volvo Construction Equipment and Services (VCES) dealership in San Leandro, where he first learned about the manufacturer’s electric machines.
“The VCES team played a key role in this decision by helping us assess how the DD25 Electric would meet our specific operational needs and sustainability goals while working with our budget,” he said.
Scott Nadell, a government sales rep at VCES, said the machine and available funding were a good match for Yolo County’s needs.
“After discussing the features and benefits of the DD25 Electric plus the upcoming Clean Off-Road Equipment [CORE] Voucher Incentive program, Ben was very interested, and I knew it would be a good fit,” said Nadell. “This model is great for the light-duty applications like patch rolling and smaller paving jobs they do.”
Lee and Nadell discussed how a CORE voucher could subsidize the purchase, and because it was a first-come, firstserved opportunity, they knew they’d need to act quickly. By initiating the purchase through Sourcewell, Nadell was able to give Lee the best possible price and have everything ready to submit as soon as the voucher program opened.
“Fortunately, they were approved for the grant, and we had a machine already being built at our factory in Pennsylvania that met the fleet’s requirements, so the rest is history,” said Nadell.
Yolo County’s DD25 Electric compactor will need to charge no more than a few overnights per week using an existing Level 2 AC charger at its fleet facility. The machine will typically operate for three to four hours a day, and the charge is expected to last for at least six to eight hours.
“There are some remote areas in the county, so we’re looking into a mobile, self-contained charging unit as well, so we wouldn’t have to bring the machine back to the yard each night during a long-term project,” said Lee.
One feature that helps the DD25 Electric (and all Volvo electric machines) run longer is the fact that it does not idle. By turning off automatically when not in use, the machine preserves battery life — unlike a diesel machine that continues to burn fuel as it idles.
Another perk that Lee’s team is looking forward to is simplified maintenance. Because there is no engine or fuel system, filters and diesel exhaust fluid are not necessary. The usual hydraulic oil and grease are all that’s needed.
The absence of an engine also makes the DD25 Electric quieter than its diesel equivalent, and its smoother ridehelps operators feel less fatigued at the end of a shift.
Luckily, these benefits do not come at the cost of power or performance. In fact, the combination of Volvo’s proven compactor platform and a 48-volt battery provides about 33 hp and 24 kilowatt hours of available power, which is 30 percent more than the diesel model, according to the manufacturer.
The drum frequency can be adjusted from 3,500 vpm (55 Hz) to 4,000 vpm (67 Hz) to cater to different applications.
“My team is excited to utilize cutting-edge technology like this that actively promotes more sustainable construction practices,” said Lee.
Yolo County also is in the process of developing a Zero Emission Vehicle (ZEV) action plan to identify gaps in infrastructure, recommend locations for new infrastructure development, assess the electrical grid’s capacity to sustain increased ZEV usage and recommend improvements, identify funding sources for future implementation and more. A Municipal Fleet Transition Plan will be part of this larger strategy, outlining a path to expanding the county’s electric fleet.
Lee views electric equipment as an essential step in reducing emissions and energy consumption, especially as communities and industries work toward meeting stricter regulations and sustainability goals.
“Environmental sustainability is important to our residents, and we have been a leader in the Green Movement for over 40 years,” said Lee. “Yolo County’s commitment to sustainability could certainly lead to increased procurement of electric equipment.”
For more information, visit volvoce.com.
(All photos courtesy of Volvo.)
BRIDGES from page 1
The project limit is approximately 2,000 ft. northward toward Macalla Road. The bridges were constructed between 1937 and 1964 and were determined to be seismically deficient so the Transportation Authority, in cooperation with the California Department of Transportation (Caltrans) and the Federal Highway Administration, is working to bring the bridge structures, retaining walls and roadways up to current seismic safety standards.
The project is funded using federal (Highway Bridge Program and Rebuilding American Infrastructure with Sustainability and Equity), Federal Congressionally Directed Spending, state (Proposition 1B) and local (Treasure Island Development Authority, Bay Area Toll Authority, Local Partnership Program and Proposition K Sales Tax) funds.
Construction consists of the following seismic retrofit strategy, which was determined to be the most cost-effective approach: demolishing seven bridge structures, realigning the roadway into the hillside, constructing six retaining walls and one undercrossing structure, and seismically retrofitting one bridge structure.
The project includes a bike path and will allow for the development of a dedicated transit-only ramp to the SFOBB, providing better transit access to the Islands’ residents.
“It’s geared for increasing the durability and reliability of the roadways as Treasure Island continues to develop. The plan, from a housing perspective, is 8,000 additional residential units,” said Carl Holmes, Transportation Authority’s deputy director of capital projects. “We are working on the backbone infrastructure to support and be ready for the increased residency on the island.”
This project will ensure the resiliency of transportation for Yerba Buena and Treasure Islands and provide unimpeded access to United States Coast Guard Sector facilities for homeland security. It also will improve roadway safety for drivers, transit users, pedestrians and cyclists on the island.
And it will support the ongoing economic redevelopment of Yerba Buena and Treasure Island that will transform the islands to a vibrant new neighborhood with 27 percent of the 8,000 units Holmes mentioned being affordable housing.
The project contract delivery method is construction manager/general contractor (CM/GC) with Golden State Bridge/Obayashi JV (GSB/O) chosen during a CM/GC selection process in 2018 to provide preconstruction services, including cost estimating, risk analysis and constructability review. After the completion of the final design in late 2022, an agreed price to perform construction was determined, and GSB/O was contracted to construct the project.
Key subcontractors include Farwest Safety; Crystal O’Neill Electric; Access Limited Construction; Chrisp Co.; Team EES; Coral Construction Co.; Bay Cities Paving and Grading; West Coast Drilling; Oliveira Fence; DeesHennessey; Silverado Contractors; and Gonsalves & Santucci. WSP is providing resident engineering/construction management, inspection services, construction staking and material testing services.
Specialty labor has included carpenters, pile drivers/drillers, laborers, ironworkers, operating engineers, electricians and Teamsters. Construction materials include 6,300 cu. yds. of structural concrete; 2,200,000 lbs. of reinforcing steel; 6,500 linear ft. of steel piling; and 9,600 linear ft. of drilled piling, along with specialty materials that includes 200 cu. yds. of shotcrete; 368 tiebacks/ground anchors each; and 11,600 linear ft. of soil nails. A variety of heavy construction equipment is being used including drill rigs, cranes, excavators, loaders, dozers, concrete pumps and trucks.
“What the CM/GC contract method did is allowed for us to engage with a general contractor while we were finalizing the design. The benefit is we were able to better ascertain some of the risks that the design may not have treated in the best way,” Holmes said. “For example, when it came to some of the bridge demolition, looking at some of the risks and making sure it’s done with a certain level of safety, productivity and speed. It’s been a true collaboration.”
The project now requires the full closure of Treasure Island Road until project completion in 2026. This allows for a more efficient and shorter construction duration. To facilitate local traffic, the Transportation Authority coordinated with local development teams to construct the Forest Road Detour, which provides full access from Treasure Island to Yerba Buena Island and the eastbound and westbound on ramps to the SFOBB. Upon completion of the project, Treasure Island Road will be reopened.
The project has witnessed some challenges with ground conditions when excavating for retaining walls, but soil boring tests completed earlier in the process helped anticipate the issue.
Construction of retaining walls and the vehicular box culvert will continue over the next two years. Holmes also shared that local artist Muzae Sesay provided the design for a decorative retaining wall, adding a local arts touch to the project.
“We’re actively in construction right now building retaining walls. We completed most, if not all, our bridge demolition. We have about a third of the island roadway closed but we have a detour that has been in place before we had the closure so there are ways to still traverse through the island,” Holmes said.
“It’s good that we were able to shut down a portion of the roadway because not having to worry about impacting the public is helpful. A significant amount of work is being performed on the steep hillsides of Yerba Buena Island. Access constraints and careful planning by the contractor to develop site access for the equipment to construct, material deliveries and worker safety has been key to successful construction to date.” CEG
(All photos courtesy of the San Francisco County Transportation Authority. The three renderings are the artist Muzae’s design for the retaining walls.)
PIRTEK Power Inn
4191 Power Inn Road, Suite D Sacramento, CA 95826
916-737-7777
PIRTEK
San Leandro
1997 Burroughs Ave San Leandro, CA 94577
510-568-5000
SFO
121 S. Maple Ave #4 South San Francisco, CA 94080
650-532-9200
LAKE from page 1
More than 100 meetings have been held with the community, county, city, utility companies and fairgrounds since 2013 to discuss the project and its impacts. Access to the southeast side of the Lake Perris State Recreation Area and the Lake Perris Fairgrounds will be maintained as they will remain open during construction. Localized noise and increased activity at the site are expected during construction.
The Lake Perris Emergency Release Facility project is planned for 2027 completion and is part of the larger Perris Dam Modernization Program.
The first phase included the Perris Dam Remediation Project that strengthened the dam’s foundation and was completed in 2018. The Outlet Tower Improvements Project to enhance water releases during normal and emergency operations is the final project planned for completion in 2029.
Lake Perris, built in 1974, is the southernmost State
Water Project (SWP) reservoir and receives more than 1 million visitors yearly. The SWP, spanning more than 700 miles, consists of a system of canals, dams, reservoirs, pumping plants and power plants that provide water to 27 million Californians and 750,000 acres of farmland throughout California.
(All photos courtesy of the California Department of Water Resources.)
The California Coastal Commission approved a plan to build a $175 million seawall along San Francisco’s coastline as a means of protecting the city’s infrastructure, Newsweek reported.
The 3,200-ft.-long wall reaching 55-ft. deep will be one of the largest construction projects in the state’s history. It will be designed to prevent shoreline damage caused by climate change, according to a report by Construction Briefing.
San Francisco’s Public Utilities Commission developed the proposal, citing fears that global warming could lead to rising sea levels and cliff erosion; that, in turn, could impact the city’s structure near the coast — especially the Lake Merced Tunnel along the San Francisco coast, which is a vital part of the city’s drainage system, Newsweek reported.
“It’s the Lake Merced Tunnel. It’s large enough you could drive a truck through it. Its 14-foot diameter tunnel, it carries stormwater and sewage from that side of the city to the oceanside treatment plant,” Anna Roche, senior project manager of the SFPUC, told 7News.
Rubble and temporary rock barriers will
be removed from Ocean Beach before the wall can be built. In addition, the shoreline will be widened by more than 20 meters, Construction Briefing reported. A seaside trail, parking lot and other features would be added, 7News reported.
Upon completion, the seawall will require maintenance via sand replenishment approximately every five years. Each application will cost about $5 million.
City officials will permanently close part of the Great Highway to make room for the project. That road runs for about 4 mi. on the beach, a road that runs almost four miles along Ocean Beach. Public trails and pedestrian access may also be impacted, Newsweek reported.
The Surfrider Foundation opposed the plan, saying the construction would restrict public access to beaches and to the sea — and possibly allowing for more coastline construction.
Extreme weather has heightened fears of climate change in California. Days after the seawall was approved, an atmospheric river of concentrated moisture from the Pacific brought heavy rains and flooding to the state’s coastline.