Komatsu West Insider
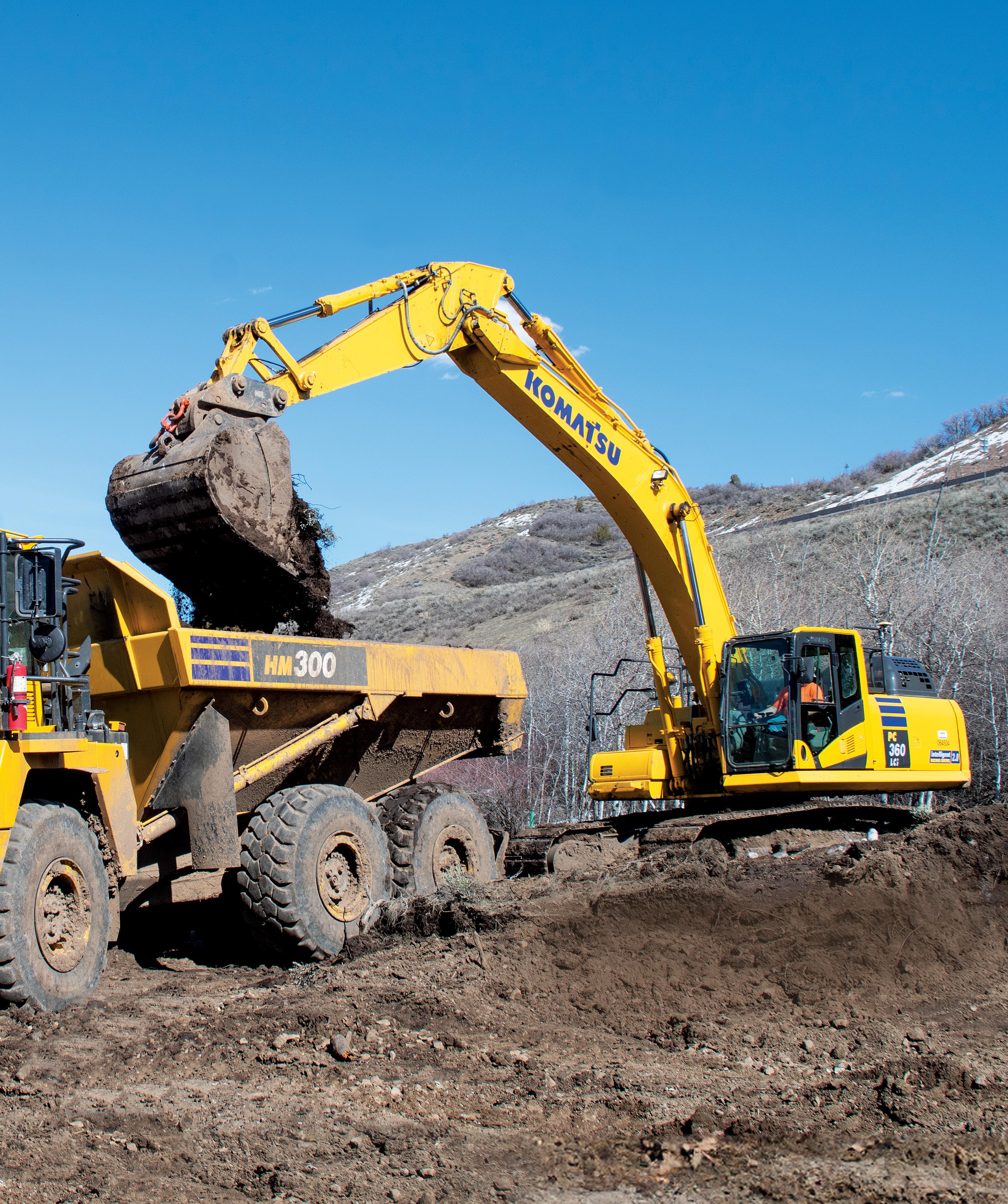
In this issue :
• Read JLR Contractors Inc.’s success story
• Boost productivity with Smart Construction
• Learn about Komatsu’s hybrid excavator
• Much more!
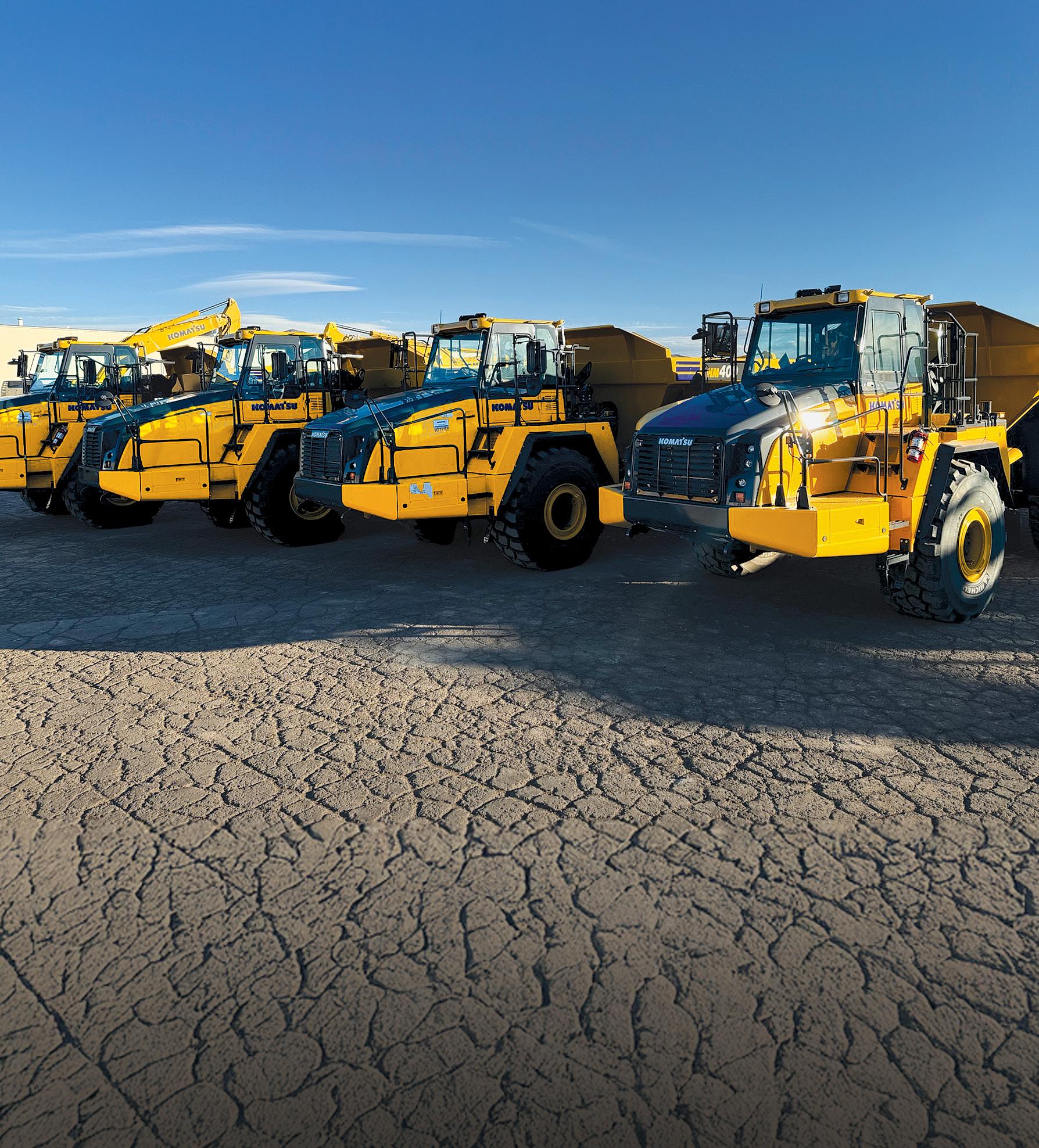
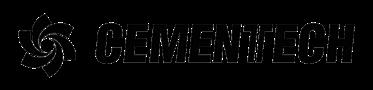
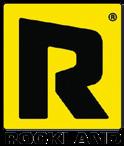
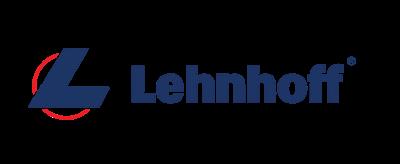

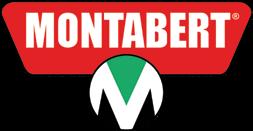
In this issue :
• Read JLR Contractors Inc.’s success story
• Boost productivity with Smart Construction
• Learn about Komatsu’s hybrid excavator
• Much more!
Highlighting the importance of partnership pg. 5
Read a letter from Todd Gaspers, Vice President, Komatsu Company Stores West.
More than a century of success pg. 6
See how JLR Contractors Inc. has built a legacy based on its track record of delivering excellence.
Driven by precision pg. 12
Meet Lead Technician Jordan Webster, who supports Komatsu West's Salt Lake City branch through technical knowledge and mentorship.
A sustainable future together pg. 15
Get a glimpse of MINExpo 2024.
Optimize your operations with technology pg. 16
Figure out which Smart Construction solution is right for you.
Promote sustainability pg. 20
Check out the highly productive Komatsu HB365LC-3 hybrid excavator.
Bring 3D to conventional excavators pg. 23
Drive productivity with Komatsu's Smart Construction 3D Machine Guidance.
Updated My Komatsu pg. 24
Delve into My Komatsu's new features and updates.
Demo in the desert pg. 27
Explore Komatsu's Quarry Days, an event that took place at Komatsu's Arizona Proving Grounds.
Dear Valued Customer:
We’re excited to share the first issue of the Komatsu West Insider magazine with you. We’ve strived to create an informative magazine that highlights the importance of partnership. Creating a strong partnership takes more than great equipment and innovative solutions; it takes trust and results.
Our employees are the foundation of our success. Our experienced technicians and professionals bring unmatched expertise in heavy construction equipment and work hard to keep our operations thriving. Their knowledge is built on years of hands-on experience and a strong commitment to safety. Like our valued dealers, Komatsu prioritizes safety and strives for zero harm, helping to ensure the well-being of our team while supporting your needs.
Whether you are purchasing new or used equipment, our customer support team is here to help maximize uptime for your equipment while helping to lower operating costs. Komatsu offers industry-leading digital technology to help you stay ahead of your competition. Our digital solutions enhance your equipment's efficiency and productivity while helping lower project operating costs. Intelligent Machine Control (IMC) is available factory-installed and integrated into our crawler dozers and hydraulic excavators. We also have retrofit products for non-GPS machines.
With My Komatsu, you get free access to parts ordering, telematics data, essential documentation like service manuals and more. My Komatsu is meant to make your operations run smoother than before. Komatsu Care maintenance programs are also designed with that core objective in mind. Our cost-per-hour programs can also limit uncertainty in owning and operating costs for your Komatsu machines. Partner with us to monitor and manage your maintenance schedule to preserve your machine warranty coverage and help maximize resale value.
Purchasing used equipment can be a cost-effective way to add to your fleet. Take advantage of the benefits of used equipment as well as Section 179 and bonus depreciation, which reduced to 60% in 2024 and will continue to drop 20% per year until it reaches 0% in 2027. This tax savings program is still in effect for new and used equipment that’s in service by the end of the year. Connect with us if you have questions or need support leveraging this tool.
We hope you enjoy this premier edition of Komatsu West Insider. As always, if there’s anything we can do for you or your team, please reach out or visit us at one of our 8 branch locations. We are here to support you!
Sincerely,
Todd Gaspers Vice President Komatsu Company Stores West
Provo-based JLR Contractors Inc. has built a legacy based on its track record of delivering excellence
Through 112 years and four generations, one thing has held true for JLR Contractors Inc. — there is no substitute for excellence.
“That motto encompasses everything we believe in, from the highest quality and craftsmanship of our work to how we treat our employees, customers, vendors and our trade partners such as subcontractors and suppliers,” said President and CEO Scott Roberts. “Not only do we want to deliver excellent products and projects, but we want to build excellent relationships, too. Those relationships build on each other, create lasting opportunities and work, and allow people to be helped and our industry to grow. It also goes along with our commitment to bettering the communities we live in and serve.”
Both Scott and his brother Tyler, the chief operating officer of the Provo, Utah-based firm, emphasized that those ideals have held true since their great-grandfather John Lyne Roberts Sr. founded the company in 1912 as a homebuilding and remodeling business. His first client was his high school shop teacher, who was so impressed with his skills that he asked him to build him a house. That was the beginning of J. Lyne Roberts & Sons, now known as JLR Contractors.
Customer snapshot
Company: JLR Contractors Inc.
Location: Provo, Utah
Employees: 100
Established: 1912
Areas of expertise: Residential/commercial remodel, public works and industrial, architectural woodwork
Komatsu equipment: D39PXi-23 IMC dozer, D61PXi-24 IMC dozer, PC160 excavator, PC210LCi-10 IMC excavator, PC360LCi-11 IMC excavator, WA270 wheel loader
Komatsu technology: My Komatsu, Intelligent Machine Control (IMC)
John Lyne “Jack” Roberts Jr., the next in line, expanded the company's services to include commercial building and remodeling. His son, John Greg Roberts, further diversified the business by leading its expansion into public works construction and the establishment of JLR Contractors’ architectural woodwork manufacturing facility. This facility is where the company excels in millwork, assembly and finishing of various materials.
“The reality is that we’re diversified on purpose," said Tyler. "Being in multiple trades and self-performing in them has helped us be successful and pick up work when needed. We are in a good position with outstanding people on staff and the ability to now perform so much work because when one market is down, we can ramp up in another and vice versa.”
Scott and Tyler grew up around JLR Contractors, often spending time with their grandpa Jack, who taught them how to build things in the company shop, do small grading work and put together concrete forming, among other tasks. The brothers often talked about leading the firm one day. Still, before they eventually moved into their current roles at the helm of JLR Contractors, they left to work for other companies, with Scott going to Texas to focus on commercial construction and Tyler being locally employed by a land developer.
When Scott and Tyler returned to JLR Contractors, they made a conscious effort to further push diversification by expanding the company’s earthwork capabilities. They took over operations in 2006.
“My primary responsibility with the developer was to work hand in hand with the excavation companies to ensure that work was being
done, so we decided to put my experience to use and focus on growing our excavation side,” Tyler recalled. “It has been a huge benefit, because performing that work allows us to control our schedules and budgets better. That led us to start doing concrete in-house as well.”
Scott added, “We always had small equipment around to do final grading or prep for concrete, but we didn’t do any large-scale earthmoving or site prep. I was always interested in it, and with Tyler’s experience, we decided it was a good move to add it.”
JLR Contractors now does full site preparation on its own building projects and has expanded into doing large-scale, earthmoving-only projects both as a general contractor and a subcontractor. The company self-performs everything from land clearing to finish grading, including utility installation of sewer, water, storm piping, and pump and lift stations.
“Our niche is really those projects with dirt work and some type of structure, and that’s where we really excel because we can complete the entire project as a general contractor and be a one-stop shop,” said Scott.
A current project highlighting JLR Contractors’ full capabilities is the campground it is constructing for the Utah Department of Natural Resources at Jordanelle State Park, located about 40 miles east of Salt Lake City and at an elevation of more than 6,100 feet. The contract calls for JLR Contractors to turn what has become a wilderness site next to the reservoir into a finished area with roads, pad sites,
pavilions, restrooms and a fee station. During the winter months, JLR Contractors installed about 4 miles of utility lines, which involved the excavation of more than 250,000 yards of dirt.
“There was a campsite here that was built in the 1980s, and it lasted about four years before it got washed away,” noted Lead Superintendent and Fleet Coordinator Marc Sucher. “It was rebuilt in the early 1990s, along with some restrooms. At that time, all the utilities came across a bridge that crossed the nearby river. Another big runoff came and took the bridge out. Things were basically left until we started. In addition to connecting utilities from the hill nearby, we are building up the site to keep it from getting washed out again.”
Marc continued, “It’s been a challenge because the water table is high. It doesn’t take much moisture to make it squishy. We were shut down for several months last summer, which necessitated us doing pipe install in the winter. We had to put the water main in 7 feet deep because of frost up here.”
“We are looking for reliability and service when it comes to equipment, and Komatsu has been incredible in both respects. If we have an issue, Komatsu stands behind us and helps us find a solution as quickly as possible.”
- Scott Roberts, President and CEO of JLR Contractors
Saving with IMC equipment, My Komatsu
Earthwork operations on the Jordanelle State Park project are being performed with a mix of Komatsu wheel loaders, excavators, haul trucks, and Intelligent Machine Control (IMC) excavators and dozers. Komatsu equipment has been a staple in JLR Contractors’ fleet since the Roberts decided to expand the company’s capabilities.
“We are looking for reliability and service when it comes to equipment, and Komatsu has been incredible in both respects,” said Scott. “That’s why we have a long-term relationship that started in 2006 with the purchase of a PC160 excavator and has continued because the machines run every day. If we have an issue, Komatsu stands behind us and helps us find a solution as quickly
JLR Contractors tracks its fleet with My Komatsu, a comprehensive digital hub that allows users to monitor their assets for utilization, fuel usage, health and production information. Equipment Manager Blake Carter began using My Komatsu about three years ago and said the time savings have been a big advantage.
“All the data is there, and it’s made it much easier and quicker for me to track compared to how I was doing it before, which was with a spreadsheet that I would text to our field personnel and going to the job site as much as I could,” commented Blake. “With My Komatsu, I can track our Komatsu equipment from my laptop or with the mobile app and get up-to-date information practically anytime and anywhere.”
While My Komatsu is a newer component of JLR Contractors’ push toward adopting more technology into its earthwork practices, the first was the introduction of IMC equipment about a decade ago when JLR Contractors acquired a D39PXi-23 IMC dozer with factory-integrated GPS grade control that it still uses today. The company has since added a D61PXi-24 IMC dozer and PC360LCi-11 and PC210LCi-10 IMC excavators.
“Scott, Marc and I had a lot of discussions with Tim about adding IMC machines, so we could utilize them and be more effective and efficient,” said Tyler. “We’ve seen a significant increase in production through their use and the accuracy they provide. There is a lot less rework.”
Marc credits Tim with helping JLR Contractors adopt GPS grade control and include IMC equipment in its practices.
“Our first IMC dozer — we believe it was the first D39i in Utah — gave us phenomenal savings because we were pulling string lines and putting in stakes to grade concrete, and that was basically eliminated,” said Marc. “Tim's help getting us set up with GPS and the dozer performance convinced us that IMC was the way to go. Overall, we’re probably saving more than 30% in time and material compared to traditional methods with stakes and grade checkers.”
Jeff Kennedy believes IMC makes him a better, more efficient operator.
“It’s easy to navigate and change grades when needed, and I think it makes things smoother,” explained Jeff, who ran the D61PXi-24 dozer on the Jordanelle State Park project. “The plan is in the machine. All I have to do is turn the machine on and GPS on, wait for it to load and calibrate, then it’s ready to rock and roll. I’ve run other integrated systems, and Komatsu is much more user-friendly. There are a lot less steps to go through in the GPS. The machine itself is maneuverable and works well, even in tight spaces. I was loyal to another brand to work for JLR and got into Komatsu. It’s an amazing machine.”
“Our first IMC dozer gave us phenomenal savings because we were pulling string lines and putting in stakes to grade concrete, and that was basically eliminated. Overall, we’re probably saving more than 30% in time and material compared to traditional methods with stakes and grade checkers.”
-Marc Sucher, Lead Superintendent and Fleet Coordinator at JLR Contractors
JLR Contractors added the PC210LCi-10 six years ago to do mass excavation, site grading, and cut intricate contours and shapes. The company also uses its PC210LCi-10 and its PC360LCi-11 to cut utility trenches and install pipe. Both semi-automatically limit over-excavation and trace the target surface. Once target elevation is reached, the excavator won't allow it, no matter how hard the operator tries to move the joystick to lower the boom. The PC360LCi-11 IMC 2.0 excavator has second-generation features, including auto tilt bucket control and bucket angle hold control. “It simplifies things because I can switch back and forth between digging subgrade and placing
bedding without having someone to constantly check grade,” said Chance Hansen, who used the PC210LCi-10 for pipe trenching on the Jordanelle State Park project. “I know my pipe has to be 6 feet below grade, and there are 6 inches of bedding. I set the grade to 6.5 feet, and it won’t let me dig past that. There’s no guesswork.”
Marc added, “I honestly think the PC210LCi has saved us 35% to 40% on pipe, just in time. That’s in addition to cost savings from not over-excavating or putting in too much fill. We had been renting a PC360LCi for quite some time for larger and deeper jobs such as sewer lift stations before buying one this year, and we are seeing similar results with it.”
As the savings add up, JLR Contractors is considering adding more IMC machines and other Komatsu Smart Construction solutions to drive productivity and efficiency further.
“We had a conversation not long ago about adding drone mapping, but right now we are focused on IMC; if we could get every machine in the IMC version, we would,” stated Scott. “They really give our operators more confidence in grading without the need to
constantly get out of the machine and check grade. If you think about it, that increases safety too, because the fewer times they climb on and off a machine, the chances of something happening are reduced. As a company that values and cares about its people, making sure they get home safely to their families at the end of the day is a great benefit.”
One of those people is Scott’s son Cade, who joined JLR Contractors full time about a year ago. He’s learning the business from the ground up and currently works in the field as an operator.
“The IMC machines are great, especially the 2.0 PC360LCi,” commented Cade. “It’s smooth, and I can go in and build a model for an area without leaving the cab and continue to cut grade. I love the Komatsu equipment. I’m having a good day when I’m running it.”
Cade is part of a potential fifth generation of leadership for JLR Contractors. Like his father and his uncle Tyler, he and his brothers talk about one day taking the reins. They have also spent time outside of school learning about the business.
According to JLR Contractors:
• 35% to 40% time savings on pipe using the Komatsu PC210LCi IMC excavator
• Cost savings realized from not over-excavating or putting in too much fill
• 30% time and material savings using the Komatsu D39PXi-23 IMC dozer
• Substantial time savings from using My Komatsu for fleet management and IMC technology
“I love it, especially moving dirt,” declared Cade. “I would like to see more growth, especially on the excavation side. I think there are a lot of cool things we have done and that we could do in the future as we continue to grow in all aspects of our company.”
Scott said he hopes that’s the case. He’s seen Cade and his younger sons keenly interested in all parts of the business, including concrete and woodworking.
“I love the Komatsu equipment. I’m having a good day when I’m running it.”
-Cade Roberts, Operator at JLR Contractors
“I have always felt like it’s my job as a father to teach them how to work and let them decide what they want to do,” stated Scott. “Each has spent time around the business and gravitated to different aspects of the company that we do, and if the younger ones choose to come on board with Cade and take leadership, that could be a real strength.”
For now, Scott and Tyler will continue to move the company forward with a steadfast focus on slow growth driven by delivering quality work on time and on budget.
“We are very fortunate to be a part of a fourth-generation business; it’s an amazing feat for sure,” said Tyler. “It’s rare across the world. I think the future continues to allow JLR to grow. The demand and opportunity in the industry are there if we continue to work on building a business that lifts everybody to a higher standard.” ■
*The opinions expressed here are from the end user as quoted. The results described herein are those of these end users under certain conditions. Individual results may vary.
Maximize productivity on your job sites with advanced automation technology. Komatsu’s Intelligent Machine Control (IMC) can help you get the most from your machines, crew and carefully designed plans.
• Get new operators up to speed quickly
• Go from mass excavating to finished grading faster than ever
• Helps eliminate potential damage to design surface
• Empower operators to work efficiently, pass after pass
Jordan Webster, Lead Technician at Komatsu West’s Salt Lake City branch, has built a career that blends hands-on expertise with a dedication to improvement and teamwork. Raised on a dairy farm in Utah, Webster was surrounded by heavy machinery from a young age, fostering a natural affinity for the industry.
“Growing up, my family owned a gravel pit and a heavy equipment company,” Webster recalled. “I’ve been around equipment my entire life, so moving into this field was a natural fit for me. Working in construction didn’t hold the same interest for me, though — I was more drawn to understanding how things worked.”
“I was drawn to Komatsu because they’ve always felt like the underdog in the industry but have equipment that outperforms other brands."
-Jordan
Webster, Lead Technician
While many in his family worked as equipment operators, Webster felt he could make a stronger impact in a technical role.
“I like the fixing side of it more than just running the machines,” he shared. “It’s fun doing something not everyone else can do, bringing equipment back to life and making sure it looks and works like it did straight from the factory. It’s fun to see a machine come back through that I worked on five years ago and to see the quality of the work still holding up.”
After spending nearly six years working at a copper mine in Nevada, Webster joined Komatsu West in 2015, where he quickly advanced from a service technician to a lead technician. His role now involves managing day-to-day operations, providing troubleshooting guidance and supporting multiple departments.
“I was drawn to Komatsu because they’ve always felt like the underdog in the industry but have equipment that outperforms other brands,” commented Webster. “Komatsu’s equipment quality speaks for itself. I wanted to be part of proving that Komatsu has just as much to offer as anyone.”
Webster attributes much of his success to the support network within Komatsu and the training opportunities that have helped him grow his technical skills.
“When I joined, Komatsu provided lots of training to ensure I could work on any machine,” Webster explained. “The support has been continuous, and they’ve always given us the tools to succeed. Whether through hands-on work or access to resources, Komatsu invests in its employees.”
Now approaching a decade with Komatsu, Webster appreciates the camaraderie and support within his team, which he describes as feeling more like a family than just colleagues.
“It’s easy to keep coming to work here,” said Webster. “Komatsu is family-oriented, and they take care of us. The environment is fun. We work together well, and that makes every day rewarding.”
“Komatsu is family-oriented, and they take care of us.”
- Jordan Webster, Lead Technician
Outside of work, Webster’s life revolves around family and supporting his children’s athletic endeavors, particularly soccer. He and his wife, Jenna, who works at their local school, are busy keeping up with the demands of raising three active kids.
“My sons play on traveling soccer teams, so we’re constantly on the go for games and tournaments,” Webster shared. “It keeps us on the move, but we
enjoy it. Komatsu has been incredibly supportive of my need for flexibility to balance work with family commitments.”
In addition to his work and family, Webster has a surprising passion: collecting Nike sneakers, a hobby that amuses his family and coworkers alike.
“I have a closet full of rare Nike shoes, and some of them are worth thousands of dollars,” he said with a laugh. “My wife teases me about it, but it’s something I really enjoy. The younger guys at work think it’s fun, and it’s become a bit of an inside joke around the office.”
Looking ahead, Webster envisions a future in training or technical support, where he can share his knowledge with newer mechanics in the industry.
“I like the idea of helping others learn, especially in an industry where we’re seeing fewer skilled technicians,” he reflected. “It’s a field that needs passionate, knowledgeable people. I’d love to help guide the next generation and pass on the skills I’ve gained.”
Webster concluded, “I want to make sure I leave things better than I found them, both in my work and with the people I work alongside. That’s what makes it all worthwhile.” ■
48% more productive* with more HP, a larger bucket and three selectable work modes
40% more efficient* with Tier 4 engine technology and enhanced hydraulic circuits
10% more engine HP* to handle heavy-duty tasks with ease
11% stronger bucket digging force* to tackle tough materials efficiently
Cutting-edge equipment and technology that balance productivity and sustainability showcased during MINExpo 2024
The theme of MINExpo 2024 was “A sustainable future together.”
With one of the show’s largest and most comprehensive booths, Komatsu shared its vision for sustainable mine optimization, which has been born out of a collaboration with customers to unlock the full potential of Komatsu’s solutions and technologies.
“We’re excited to show our vision for sustainable mining and optimization of mines, and how we intend to work with customers to help them tackle key challenges in their mines,” said Peter Salditt, President and CEO, Komatsu Mining Corp. “There is a tremendous effort, will and interest in looking at sustainable mining and decreasing our carbon footprint. We feel that we are particularly well-placed to address electrification as many of our products have been electrified for a long time.”
Innovative machines
Featured products during MINExpo included the PC4000-11E electric drive hydraulic mining excavator and the Power Agnostic 930E haul truck. The PC4000-11E delivers the powerful digging force operators need and expect from high-performance diesel machines while reducing emissions. The 930E is built on Komatsu’s modular power agnostic platform that will allow for a transition from diesel to battery or even hydrogen fuel cell power sources. This innovative truck also supports dynamic charging and trolley assist options to reduce fuel consumption and emissions further.
During the show, Komatsu gave customers a firsthand look at two teleoperation advancements for its blasthole drills and mining dozers that can help drive mine safety, productivity and operational interoperability. These new features mark a significant step toward the future of remote-controlled equipment, allowing operators to manage heavy machinery from an off-site location. Komatsu’s drill automation technology is designed to reduce operational variability, leading to improvements in blasthole quality and fragmentation through the precise execution of drill patterns. Customer benefits include more consistent production output, reduced machine wear from less experienced
operators and improved downstream process efficiencies.
Teleoperation of a D375A-8 mining dozer used technology that integrates Modular ProVision machine guidance with automatic blade control. This offers precise and reliable remote operation, even in the most hazardous environments. The advanced system eliminates the need for operators to endure high-risk conditions, including high-vibration environments.
Standard machines geared toward high-production mining were also on display, including:
• GD955-7 motor grader
• ZT44 blasthole drill
• D475A-8 surface mining dozer
With a focus on long-term partnerships, Komatsu remains a trusted name in mining and is dedicated to advancing the industry through products, services and technological innovation. ■
Smart Construction solutions can help you increase productivity, track it and make faster critical decisions
Technology use in the construction industry has grown rapidly during the past decade and includes both on-machine technology as well as software designed for each stage of project management. Choosing the right technology to move your business forward comes with many questions, and the correct answers depend on what technology your company has already adopted.
Komatsu has long been a technology proponent. It was among the first manufacturers to incorporate telematics into its machinery, with its Komtrax remote monitoring system that enabled customers to monitor fuel usage, idle time, location and more. During the past two decades, Komtrax has expanded to include additional comprehensive information that helps with proactive fleet management, to help reduce downtime as well as owning
“For our customers, Komtrax was a great introductory option down the technology path, and it continues to be a great feature,” said Jason Anetsberger, Director of Customer Solutions, Komatsu. “On our new machines,
it’s easily accessible through our My Komatsu platform and lets you monitor any piece of equipment.”
Anetsberger continued, “Now, the question is: what’s the next step that is right for you in this technological journey? Fortunately, we have many Smart Construction solutions depending on where you are at the moment. We offer solutions that can support a small operation that is currently not using any technology, as well as solutions for large multinationals that have fully embraced machine control and project management systems.”
Anetsberger provided some helpful tips for how to determine which Smart Construction solutions could be beneficial and when the right time to add them is. All of the solutions can be accessed and viewed through your My Komatsu account.
No solutions? IMC is a good introduction If you are not using any of Komatsu’s Smart Construction solutions, Intelligent Machine Control (IMC) dozers and excavators may be a good starting point, according to Anetsberger. When Komatsu introduced its first IMC dozer more than a decade ago, it was the original Smart Construction solution. Several new models and
Intelligent Machine Control (IMC) dozers can help increase productivity. For those looking for an introduction to Smart Construction, IMC equipment may be the best fit.
next generation machines have been added that feature fully factory-integrated GPS machine control, which helps increase productivity and efficiency by reducing surveying and staking costs and eliminating the masts and cables of traditional aftermarket GPS add-on systems.
With seven sizes of IMC dozers, ranging from the 105-horsepower D39i-24 to the 354-horsepower D155AXi-8, there is a fit for practically every construction site application. The IMC 2.0 dozers have advanced features such as proactive dozing that enables operators to cut/strip automatically from existing terrain as well as lift layer control, tilt steering control, and quick surface creation.
On the excavator side, there are IMC machines ranging from the 20-ton-class PC210LCi-11 to the 50-ton-class PC490LCi-11. All have semi-automatic functions that go beyond simple guidance to semi-automatically limit over-excavation and trace a target surface. Once target elevation is reached, even if the operator tries to move the joystick to lower the boom, the excavator doesn’t allow it, reducing wasted time and the need for expensive fill material.
IMC 2.0 excavators feature bucket angle hold control, which automatically holds the bucket angle to the design surface during arm operation. It’s less fatiguing for operators, so they can be more productive, and it produces a better finish-grade surface. Plus, auto tilt bucket control assists operators by aligning the bucket parallel with the slope, so that finish grading can be accomplished without needing
to align the machine with the target surface. Testing has shown that these latest generation models help improve accuracy by up to 33% and efficiency as much as 63% compared to conventional excavation and grading methods.
“We have more than a decade of proven success with IMC machines saving time and material costs, to help increase profitability,” said Anetsberger. “IMC was our first Smart Construction solution, and we have built a suite of additional beneficial solutions, including our Smart Construction 3D Machine Guidance for standard excavators. This technology is a good entry-level system for someone who may be considering GPS but is not ready to fully commit to integrated machine control.”
Smart Construction 3D Machine Guidance is an add-on, indicate-only system that offers many of the benefits of IMC. It’s three-dimensional, so operators get the advantage of seeing where they are on a project, as well as their relation to target elevation. They can set audio alerts that change tone the closer they get to finish grade. That, along with the visual representation on the app, helps keep operators from digging too deep, saves time and lowers costs.
From site to office and vice versa
Additional Smart Construction solutions can help customers better manage their projects from pre-bid to final close out.
“Knowing which one to use is a matter of assessing your goals,” Anetsberger stated.
“Do you want faster, more accurate mapping and progress tracking? Do you want to move to 3D digital plans and combine drone data with 3D design data to confirm quantities? Do you want better labor management and cost tracking and to be able to do it remotely?”
A couple of solutions Anetsberger suggested for those who now have IMC machines are Smart Construction Remote and Smart Construction Dashboard. Remote allows users to remotely send design files to targeted machines in the field and remotely support operators without driving to the job site, saving time and fuel expenses. With remote access, contractors can help their operators troubleshoot issues in real time by viewing the same visuals as in the machine.
To help users with tracking cut/fill progress, Dashboard allows remote visualization of job site terrain progress, with the aim to have a digital twin of the job site material movements. It combines data from multiple sources into one comprehensive picture and provides a 3D graphic visualization of all design, drone and machine data to measure cuts/fills, quantities and productivity. Users can confirm pre-bid and topographical map data, track site progress in near real time, document job site conditions as evidence for change orders, and quickly and easily measure quantities.
“Dashboard and Remote are complementing solutions to IMC,” said Anetsberger. “The visual representation and the ability to track job site progress more easily from practically anywhere, can lead to faster decisions and potentially better bottom-line outcomes. They are easy to implement, user-friendly, and the cost
savings have been significant for companies using them.”
Further building your solutions portfolio As any project manager knows, job sites often evolve and plans change, which makes staying on schedule and on budget a challenge. Smart Construction Office is a project scheduling and management solution that serves as a central hub for all your jobs and can help replace manual production and cost tracking with streamlined daily automation. It delivers timely updates, insights and auto-forecasting schedules, and cost estimates throughout a project’s life cycle.
“Office is a project management tool that gives you reliable forecasting and insight into budget versus actual costs,” explained Anetsberger. “Another consideration is Smart Construction Field, a mobile app that uses data to track spending and allows contractors to quickly view current conditions and progress. You can break it down by labor, equipment, materials, receipts, timecards, and much more. Both Office and Field are brand-agnostic, so they can be a great solution for contractors with mixed fleets.”
Additional Smart Construction solutions include Design, Drone and Fleet, which can help replace paper plans with digital files, accurately map job sites, and collect data for fleet optimization.
“There are so many easy ways to implement technology solutions into your operations,” concluded Anetsberger. “We encourage anyone who wants to streamline and optimize their operations to learn about Smart Construction solutions by talking to their distributor about how to get started.” ■
BETTER COMPACTION STARTS WITH THE BEST TRACTION OF ANY MACHINE ON THE MARKET.
The BOMAG BC 1173 RB-5 delivers a quad pump drive and 30 degrees of oscillation in the center joint, keeping all four wheels on the face at all times. Unlike two-wheeled designs that can lose contact on uneven slopes and surfaces, a BOMAG refuse compactor keeps all four wheels on the ground for full-coverage compaction on even the toughest terrain.
The BOMAG BC 1173 RB-5 delivers a quad pump drive and 30 degrees of oscillation in the center joint, keeping all four wheels on the face at all times. Unlike two-wheeled designs that can lose contact on uneven slopes and surfaces, a BOMAG refuse compactor keeps all four wheels on the ground for full-coverage compaction on even the toughest terrain.
Polygon ring design offers optimal kneading, crushing and shredding forces that normal paddle-style wheels don’t. Premium hardened tips provide exceptional lifespan and are backed by our 10,000-hour warranty. Built-in wire cutters and cleaners keep wheels debris free and prevent wheel wrap.
Polygon ring design offers optimal kneading, crushing and shredding forces that normal paddle-style wheels don’t. Premium hardened tips provide exceptional lifespan and are backed by our 10,000-hour warranty. Built-in wire cutters and cleaners keep wheels debris free and prevent wheel wrap.
Unlike competitive rigid frame machines, our heavy duty oscillation joint provides 15 degrees of oscillation to the right and left, ensuring constant compaction by keeping all four wheels engaged and conforming to the working face in even the worst conditions.
Unlike competitive rigid frame machines, our heavy duty oscillation joint provides 15 degrees of oscillation to the right and left, ensuring constant compaction by keeping all four wheels engaged and conforming to the working face in even the worst conditions.
Powered by Cummins
The BOMAG BC 1173 RB-5 refuse compactor has a Cummins X15 engine for all the horsepower and reliability you need for the life of the unit. BOMAG ECOMODE technology reduces fuel consumption while ECOSTOP avoids unnecessary idle times.
The BOMAG BC 1173 RB-5 refuse compactor has a Cummins X15 engine for all the horsepower and reliability you need for the life of the unit. BOMAG ECOMODE technology reduces fuel consumption while ECOSTOP avoids unnecessary idle times.
Ease of Serviceability and Safety
Easy to operate full tilt engine compartment hood allows for simple daily maintenance inspections from the same point on our wide, sturdy walkway platforms. No need to open multiple panel doors and climb around the entire machine for your daily inspections.
Ease of Serviceability and Safety
Easy to operate full tilt engine compartment hood allows for simple daily maintenance inspections from the same point on our wide, sturdy walkway platforms. No need to open multiple panel doors and climb around the entire machine for your daily inspections.
Hybrid HB365LC-3 excavator offers significant fuel savings, reduced emissions and improved productivity over a standard excavator
Looking for ways to increase production while reducing costs? In today’s economy with diesel prices higher than ever, using a hybrid excavator such as Komatsu’s hybrid HB365LC-3 is a solid solution, according to Kurt Moncini, Senior Product Manager, Komatsu, who recently retired. The HB365LC-3 provides fuel savings, reduced emissions and improved productivity compared to a standard excavator.
“Hybrid technology continues to grow and be adopted in the automotive world, and the construction industry is coming around to the benefits such as lower fuel costs and emissions,” said Moncini. “The HB365LC-3 offers increased fuel efficiency without sacrificing power, so the overall performance is outstanding. A topper on the cake is the added benefit of reduced emissions that lowers your carbon footprint and promotes sustainability.”
Moncini continued, “Based on EPA’s (Environmental Protection Agency) CO2 formula, the hybrid potentially offers an up to 20% reduction in CO2 emissions compared to the standard PC360LC-11. It’s a big win all around.”
Komatsu introduced the 36-ton hybrid HB365LC-3 — the industry’s first true hybrid in that class size — in 2017. Since then, thousands have been used around the world for all types of excavation, loading trucks and to perform other tasks. The HB365LC-3 followed the introduction of Komatsu’s first hybrid excavator, which was launched in 2008.
In addition to the fuel savings and reduced emissions the HB365LC-3 provides, customers noted that one of the main decision-makers when choosing the hybrid excavator was the improvement in productivity.
“The hybrid HB365LC-3 has equal or better performance than our standard PC360LC excavator, but with fuel savings that could be as high as 20%, depending on application,” said Moncini. “It’s a great fit for construction companies that use excavators in high-swing applications, as well as for feeding crushers in quarry, recycling and demolition applications where swing is a constant.”
An electric swing motor captures and regenerates energy as the upper structure slows down and converts it to electric energy.
Moncini explained, “It’s using energy that would normally be wasted and makes it available to do work, contributing to increased efficiency and decreased diesel usage.”
The energy captured during each swing braking cycle is stored in the hybrid HB365LC-3’s ultracapacitor. Each time the excavator swings, the capacitor discharges electric power to the electric swing motor.
“A traditional battery requires time for the chemical process that releases electricity to occur,” stated Moncini. “The heavy work nature of construction equipment places a much faster demand on power transfer. The ultracapacitor’s ability to store and discharge energy quickly makes it ideal.”
He added, “When it comes to the boom arm and bucket, the capacitor drives the swing, and all available engine horsepower can go
into the hydraulic system. This creates faster cycle time and a very quick, responsive swing. It’s snappy.”
In addition to powering the swing motor, the ultracapacitor sends electric energy to the engine via the motor-generator. This energy is used to accelerate the engine from an ultra-low idle speed of 700 revolutions per minute (rpm) and improve hydraulic response.
Tier 4 and more
Komatsu recently improved the warranty on the HB365LC-3’s hybrid components. The special hybrid component warranty term is now up to seven years or 15,000 hours and covers the electric swing motor, motor-generator, capacitor and inverter. If you sell the excavator, the warranty is transferrable.
The hybrid HB365LC-3’s 269-horsepower engine is a six-cylinder with a Komatsu aftertreatment system that meets U.S. EPA Tier 4 Final emissions regulations. A Komatsu Diesel Particulate Filter (KDPF) and selective catalytic reduction (SCR) work together
to inject diesel exhaust fluid (DEF) and decompose nitrous oxide into non-toxic water and nitrogen.
Komatsu Care comes standard, including one complimentary KDPF exchange and one SCR service during the first five years. It also covers scheduled maintenance for the first three years or 2,000 hours. All work is done by factory-trained distributor technicians.
Hours and key performance data can be tracked remotely with Komtrax. Operators can see the information first-hand on the 7-inch, color LCD monitor, including a capacitor charge gauge, DEF levels and a rear-view camera. Komtrax has an Operator Identification System that records machine-operation and application data for up to 100 individual ID codes.
Operators will also appreciate lower noise levels in the spacious ROPS (roll-over protective structure)-certified cab. Features include vibration-dampening mountings and a fully adjustable, air-suspension seat and arm rests. A Bluetooth AM/FM radio is now standard on new machines. ■
Gain versatility and agility in your quarry operations with Montabert’s unique variable energy breakers and a wide range of tools. Whether you need primary or secondary breaking, block splitting, crusher assistance or recycling, Montabert breakers can efficiently handle the job.
For more than 100 years, Montabert products have been designed for productivity, reliability and safety.
Montabert breakers and Lehnhoff couplers are available through Komatsu Company Stores West. Contact us for more information.
Drive productivity by giving operators high-precision data with Komatsu’s Smart Construction 3D Machine Guidance
Are you looking for an easy way to improve your conventional excavator’s grading performance? Access to 3D advantages offered by Komatsu’s Smart Construction 3D Machine Guidance can help by quickly providing operators with the latest design data, effectively measuring payload volume and load counts as well as monitoring production from the office.
Smart Construction 3D Machine Guidance is an entry-level technology solution that brings 3D to conventional excavators, giving operators in the field and managers in the office access to 3D design and topography data that help drive accuracy and promote optimized operations. Using a global navigation satellite system, a machine can determine where it is on the job site and what the target grade is as well as eliminate the need to set up a laser or bench every time the machine moves.
“3D Machine Guidance is an indicate-only system that plays nicely between a standard excavator and Komatsu’s Intelligent Machine Control excavators with factory integrated semi-automatic grade control,” explained David Yim, Solutions Manager for 3D Machine Guidance with Komatsu’s Smart Construction team. “A major benefit of 3D Machine Guidance is that the operator can dig only what’s needed, so there’s no wasted production and reduced material handling. That allows the operator to be more efficient, saving time and money in the operation.”
Yim noted that Smart Construction 3D Machine Guidance — formerly Smart Construction Retrofit
— has new features such as 3DMG Basic that will eliminate the need for a project file.
“After a project has been localized, an operator can touch the bucket to the ground to create a flat plane surface directly from where the cutting edge is,” said Yim. “They can also touch point A then point B and create a sloping surface. Another new feature is the Steer To Indicator that offers horizontal guidance along with vertical guidance. That’s a powerful tool for those working in utility applications.”
Smart Construction 3D Machine Guidance helps lower the costs of bringing technology into your operations with compact and modular kits that fit most sizes of Komatsu excavator models, including the HB365LC-3 hybrid excavator.
“It is now available as a factory-installed option on new machines or as an add-on through your Komatsu distributor,” Yim indicated. “3D Machine Guidance can also be installed and used on many OEM brands of excavators. We encourage anyone who’s looking for a system that will improve the production and efficiency of their conventional excavators to contact their distributor about adding 3D Machine Guidance.” ■
New features improve fleet management to help you get the critical information you want in fewer clicks
Fleet management is essential to maintaining your equipment’s health. Properly maintained equipment helps increase uptime and lower overall owning and operating costs. Staying on top of fleet management can be challenging, especially if you are still relying on end-of-day field reports or drives to the job site to check hour meters.
Digital solutions such as My Komatsu can change the game by giving you real-time machine data that can be accessed from practically anywhere, as well as tools that give you the capability to order parts and more. Recent updates make it easier to navigate, so you can quickly get the information you need to help make proactive fleet management decisions.
“Filtering capabilities have been updated to help users more quickly access the information they are looking for,” said Andrew Casey, Digital Solutions Analyst, Komatsu. “It’s more like a dashboard where you can get information in
fewer clicks, which is something our customers wanted. Using their feedback, we made changes to make the interface more user-friendly. Customers who already have a My Komatsu account will see the updates automatically.”
Casey said one of the priorities based on customer feedback was a redesign of the My Fleet page, emphasizing that its substantially different look and easier navigation enable users to see their entire fleet of registered machines all on a single page without having to go through multiple tabs.
“We also expanded the ability to filter by idle time percentage, SMR range, model type, manufacturer, and much more,” Casey added. “A new sync map feature lets users zoom in on a particular territory, click the sync map to list button, and see machines just in that territory.”
Another major change is the addition of component tracking, according to Casey.
My Komatsu lets you monitor your fleet from anywhere at any time and helps optimize fleet management — with real-time data that can help you make proactive decisions.
The new functionality allows users to monitor component health, so they can more proactively plan for replacements.
“Users can set an interval based on last service date or SMR hours of the machine, then create an alert that notifies them when a component is due for replacement,” Casey explained.
Machine health and fleet monitoring are now easier, faster and more efficient with new alerting features, including additional alert types for abnormality codes, coverage, Komatsu Oil and Wear Analysis (KOWA) samples, and more. Consolidated and customizable views of your alerts can be set with the alerting dashboard. With My Komatsu, you can choose how to receive notifications — by web, mobile app, email or SMS.
Telematics information (Komtrax) in My Komatsu remains a vital feature that works with Komatsu and other brands that you have registered in your My Komatsu account. You can view machine location, fuel consumption, and machine health, which includes maintenance history.
Additional features available in My Komatsu include:
• Publications – View parts and support manuals for your machines
• E-commerce parts stores – Easily order parts and solutions that you can pick up in store, have shipped to your shop, or get delivered directly to your job site
• Digital solutions – Sign up for and access your Smart Construction accounts such as Dashboard, Design, Drone, Field, Fleet, Office and Remote
If you don’t already have a My Komatsu account, you can sign up for one by visiting https:// mykomatsu.komatsu. Once you have an account, your dealer can help you get set up and work with you on how to best utilize the platform.
“Proactive fleet management results in less downtime because you have a clear picture of your equipment’s health at all times,” said Casey. “You can better plan for routine service and component changes, address excess idle time, train your staff, monitor job sites and machine performance, schedule part orders, and much more.”
One of the highlights of Komatsu’s Quarry Days is the ability to get in the operator’s seat and put equipment to the test.
“I think it’s a very good thing for Komatsu to do for operators and businesses that are looking for equipment,” said Brad Disrud, an operator with North American Coal at its Coyote Creek Mine in Zap, N.D. “I currently run a PC2000, and the ability to get in the new one and make a comparison is valuable. The electronic over hydraulic controls is nice.”
The 1,046-horsepower PC2000-11 surface mining excavator was one of more than a dozen Komatsu machines that attendees could operate or see in action at Komatsu’s Quarry Days, an event that took place at Komatsu’s Arizona Proving Grounds. Among the machines was Komatsu’s new GD955-7 motor grader with a standard 18-foot blade.
“You can definitely tell the GD955 is a game-changer,” said Mauricio Vallejos with Titan America. “It could allow us to do work in fewer passes.”
In addition to the PC2000-11 and GD955-7, attendees were able to operate several other Komatsu machines, including a PC900LC-11 excavator; an HB365LC-3 hybrid excavator;
Attendees test out Komatsu excavators at Quarry Days, including a PC2000-11, a PC900LC-11, and an HB365LC-3 hybrid model. Watch the video
WA900-8 and WA475-10 wheel loaders; a D475A-8 surface mining dozer; a D71PXi-24 Intelligent Machine Control (IMC) dozer; and HM400-5, HD785-8 and HD1500-8E0 trucks. A ZT44 drill and an RF-5 reclaim feeder were on display as well. Attendees could also talk with product experts from Montabert and Tramac about breakers and Hensley Industries about its Kprime tooth system. Montabert, Tramac and Hensley are all Komatsu-owned companies.
“We have solutions at Quarry Days that represent many applications within a customer’s job site — from stripping, to loading and haulage, to drilling, blasting, breaking, processing, and dozing, it’s all here,” said Joseph Sollitt, Director of Mining Support Equipment, Komatsu. “It gives customers a chance to put the machinery to the test and see firsthand what it can do in a real-world setting. The feedback has been overwhelmingly positive. These types of events are beneficial for the customer, as well as for us to learn more about them and what we can do to help them enhance their operations.”
James Van Remmen with Interstate Earthworks specifically wanted to operate the recently introduced 204,148-pound, 543-horsepower
PC900LC-11 excavator, which is designed for heavy construction, demolition, material handling, deep digs, large mass excavation and quarry/mining applications.
“The speed was very fast for a machine that big,” said Van Remmen.
With more bucket and lifting capacity, the PC900LC-11 can increase productivity by up to 40% compared to its predecessor, the PC800LC-8.
“The PC900LC-11 is designed for those working in applications that involve moving large amounts of material efficiently,” said Casey Zbinden, Product Marketing Manager, Komatsu. “It’s been a popular attraction at Quarry Days because customers can see so many potential uses for it. With an optional counterweight removal system, it can be more easily transported.”
Smart solutions
In addition to equipment, Komatsu representatives from its Smart Quarry solutions and My Komatsu teams were available to show customers the advantages of incorporating technology into their operations.
“Smart Quarry is designed to drive improved and optimized production, which includes site studies and our new Smart Quarry Site,” said Craig McGinnis, Senior Business Solutions Manager, Komatsu. “What’s great about Site is that it’s brand-agnostic, so it can be used with Komatsu and non-Komatsu equipment. It’s plugged into the machine and transmits actionable data that can be used to help improve practices and promote productivity.”
McGinnis continued, “For example, we did a case study and identified that a quarry was only putting about 89 tons on a 100-ton truck during loading. We determined that if they added about six more tons that it would equate to more than 13,000 tons per month in added production with the same fuel burn and time.”
Great conversations
Another advantage of events like Quarry Days is the ability to network with other contractors doing similar work, according to Moroni Wardell, who along with his three brothers owns and operates Wardell Brothers Construction in Morgan, Utah. The full-service construction company manages two gravel pits and currently operates several Komatsu loaders and excavators.
“Sharing information is very valuable because it gives us insight into how others are using the equipment and the production they get from it,” said Wardell. “All new iron looks pretty and runs really well — but talk to a customer
that has 10,000 or 12,000 hours, and you will see where the results really are. We have been able to network with a lot of other customers that stand behind Komatsu equipment.”
Chad Mikulec, Regional Operations Manager with Permian Basin Materials, said another positive aspect of Quarry Days was the ability to talk with Komatsu personnel.
“The attentiveness of the people out here, wanting to talk to us and hear what we have to say and be actively engaged is very meaningful,” said Mikulec. “It makes me feel good as an end user that they listen to us. Our opinion matters." ■
Choose reduced fuel consumption, high performance and a warranty you can count on with the HB365LC-3 hybrid excavator from Komatsu.
• Up to 20% reduced fuel consumption*
• Up to 15% improvement in productivity*
• New 7-year/15,000-hr transferrable warranty on hybrid components
Articulated Truck
Model number: HM300-5
Year: 2020
Hours on machine: 5,051
Location: Las Vegas, Nevada
Price: $300,000
Excavator
Model number: PC130-11
Year: 2022
Hours on machine: 1,568
Location: Salt Lake City, Utah
Price: $93,000
Excavator
Model number: PC210LCi-11
Year: 2019
Hours on machine: 6,369
Location: Salt Lake City, Utah
Price: $104,000
Model number: D37EX-24
Year: 2023
Hours on machine: 163
Location: Salt Lake City, Utah
Price: $124,000
Excavator
Model number: PC130-11
Year: 2022
Hours on machine: 1,500
Location: Salt Lake City, Utah
Price: $120,000
Model number: PC650LC-11
Year: 2019
Hours on machine: 7,297
Location: Las Vegas, Nevada
Price: $325,000
Contact us for more information Sean Harding Remarketing Sales Representative
801-952-4770
sean.harding@global.komatsu
Motor Grader
Model number: GD655-5
Year: 2011
Hours on machine: 5,769
Location: Casper, Wyoming
Price: $99,000
Excavator
Model number: PC210LC-11
Year: 2022
Hours on machine: 2,579
Location: St. George, Utah
Price: $138,000
Model number: PC800LC-8E0
Year: 2018
Hours on machine: 5,647
Location: St. George, Utah
Price: $430,000
Nevada
Address: 4450 P&H Dr, Elko, NV 89801
Phone: (775) 753-7557
Address: 3825 Losee Rd, Las Vegas, NV 89030
Phone: (702) 399-1004
Address: 900 Marietta Way, Reno, NV 89431
Phone: (775) 356-1334
Utah
Address: 1486 S Distribution Dr, Salt Lake City, UT 84104
Phone: (801) 972-3660
Address: 1409 East 3850 South, St. George, UT 84790
Phone: (435) 986-1000
Wyoming Address: 1180 Iron St, Casper, WY 82636
Phone: (307) 223-4660
Address: 10790 South Hwy 59, Gillette, WY 82718
Phone: (307) 682-1445
Address: 405 Jonah Dr, Rock Springs, WY 82901
Phone: (307) 686-1300