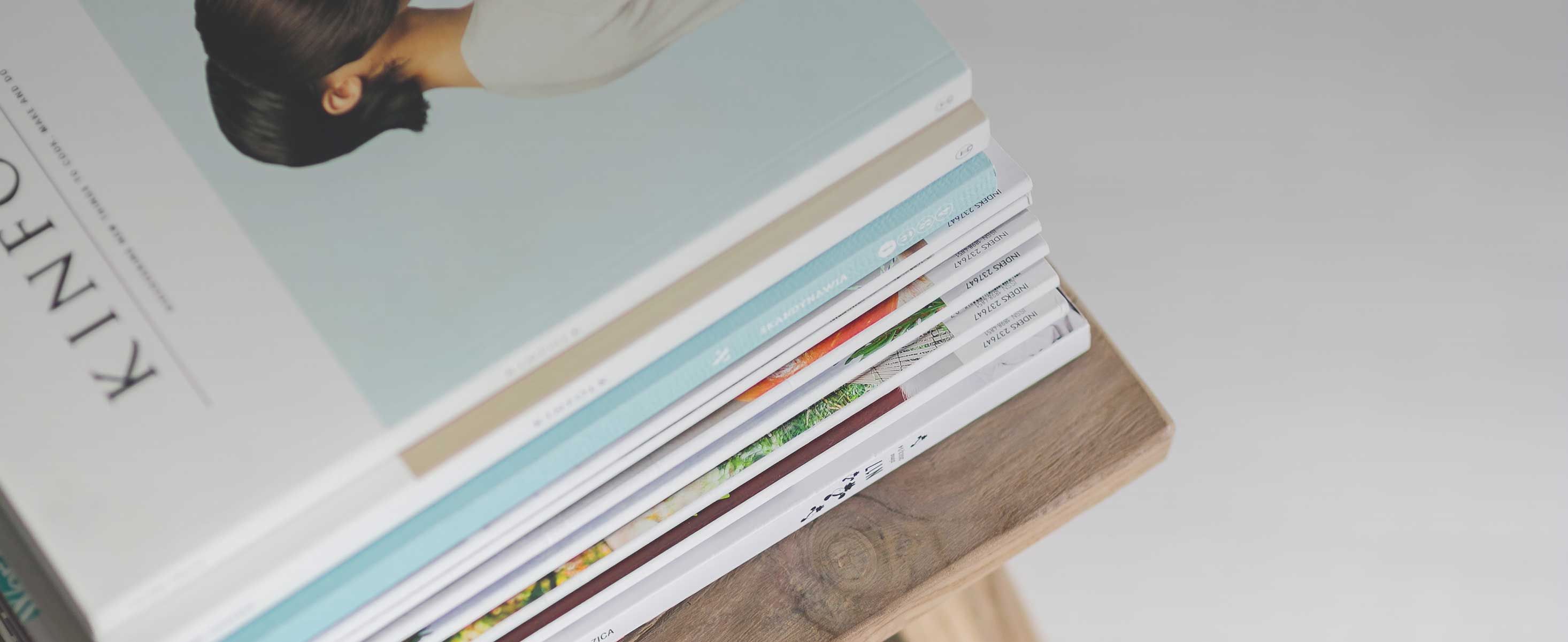
1 minute read
ENGLISH News Technologies
Koenig & Bauer and Celmacch: unique features for the ChromaCUT X Pro
The partnership between Koenig & Bauer and Celmacch S.r.l. joins more than 40 years experience in the corrugated cardboard-processing industry and more than 200 years of printing technology on a variety of substrates. Koenig & Bauer has technologically developed and successfully placed in the market 2 highly-automated machineries: ChromaCUT X Pro and Chroma X Pro. With the ChromaCUT Smart and the ChromaCUT HighTech, a semi-automatic machine and a fully-automatic line were added to the product portfolio thanks to the partnership with Celmacch. Therefore, Koenig & Bauer Celmacch offers a wide product range for all prices and performance levels. The ChromaCUT X Pro rotary die-cutter is Koenig & Bauer Celmacch’s top-of-the-range rotary die-cutter. It was designed for the highest performance rotary manufacturing of die-cut corrugated products in ultimate flexo post-printing quality. It has a running speed up to 12,000 sheets per hour thanks to its fast job changes. The ChromaCUT X Pro offers many important features. Its Easy Job Change in combination with a presettable rotary die-cutter, the automatic anilox roll changeover, and its digital workflow, enable quick nearly entirely automated job changeovers with waiting times reduced to an absolute minimum. When the customer has two similar jobs that can be processed without changing die-cutting tools, the Flying Job Change feature implies that even non-stop changeovers are at last a reality. Operators can keep track of jobs due to the machine’s press control via a flexible Profibus system, and its touchscreen allows operators to focus on jobs due to its integrated error diagnostics and online remote maintenance. These options let the customer handle even the smallest batch sizes and to accommodate market demands for the just-in-time production of ever shorter runs. An Active Air Management System interacts with the controls for 20 separate drying zones per drier to realise significant reductions in energy consumption. BCT values are up to 15% higher when the Non-Crush Feeder without feed rolls is used, paving the way for reduced paper use without compromising box strength. More sustainable and cost-optimised production is an immediate benefit and it ensures that customers are always one step ahead of the market.
Advertisement