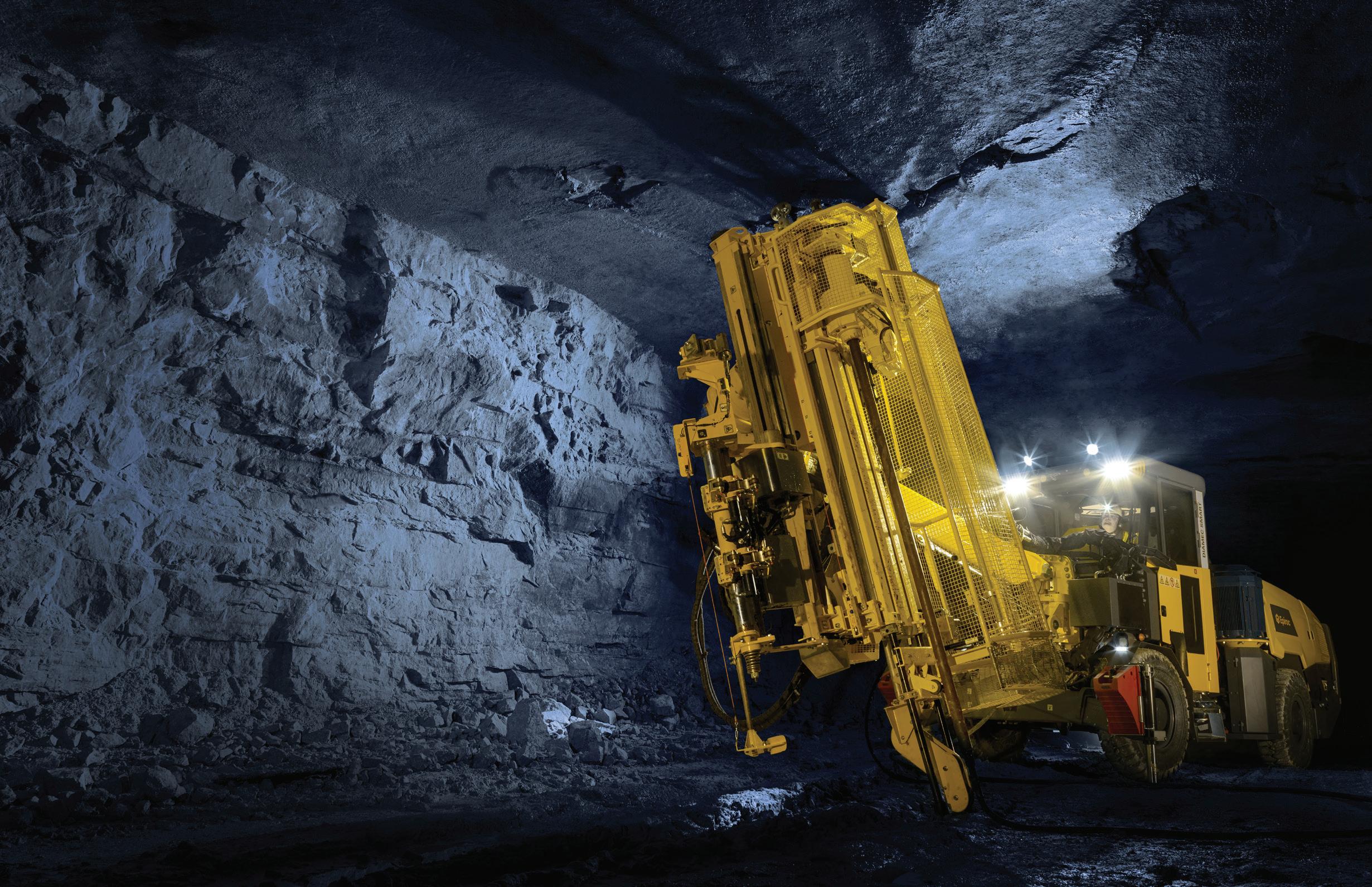
7 minute read
Drilling into the autonomous future of the industry
by Maksim Mayer, Editor at Coring Magazine
Artificial Intelligence (AI) offers a convenient solution to the ongoing qualified driller shortage in North America and elsewhere. Almost all of the leading experts Coring Magazine has talked to in the past years foresee automation becoming central to exploration drilling sooner rather than later. But in the current situation, does this panacea to the struggles of the industry seem too good to be true?
Advertisement
The autonomous drill rig
The emergence of autonomous drill rigs seems obvious given their history. One of the first rigs with a programable logic controller was the Diamec 264 APC. It was introduced in the mid-90s by Craelius, a division of Atlas Copco. The rig had a digital display and rudimentary automation functions. A decade later, in the 2000s, the drill rigs with computerized controls appeared. One of the first such examples was the Diamec U6 APC. Over the next years, manufacturers made huge leaps in improving the performance and responsiveness of the controls. Around 2015, the Rod Handling Systems were integrated to the control panels, allowing for more complete automation of tasks, and thus increasing safety. Three years later, data logging from the rig became an option as well as automatic functions, such as auto-drilling and rod running, improving drilling and operations further.
Coring Magazine has covered this progression throughout the years. Some examples include the Epiroc’s Diamec Smart line of drills - perhaps the most well-known (reviewed all the way back in Issue 1). Another is Comacchio’s CX line (see Issue 15) offering remote control via radio signal and their innovative ComNect™ telemetry system, which gives users real-time equipment status.
There is a plethora of other solutions from manufacturers and many contractors have also developed their own customized rigs with additional AI functionalities. Drillers have been reaping increasing benefits from these features over the years. Now several manufacturers have taken this even further, creating fully autonomous exploration drill rigs and even more companies are slated to present their solutions within the next months and years.
The promises are lofty: the autonomous systems would be able to control drilling with infinite precision, their improved telemetry would help making complex decisions almost instantaneously without human input, and all data and performance information would be available immediately for analysis and adjustment. Significantly less risk for the workforce and reduced downtime are just the most obvious advantages autonomous drill rigs could bring. Avoiding the costly human errors equals lower costs to repairs, while also generating higher quality core samples – the very thing clients care about.
The examples from the automation of the Mining industry seem to indicate that these rich promises are possible to reap. In 2018, Rio Tinto has reported that their autonomous haul trucks have reduced hauling costs by 15% and on average, each vehicle has operated 700 hours more than their manned counterparts. Another example is the Garpenberg mine in Sweden – the oldest in the country that is still in use. With the help of
tele-remote Epiroc drills, the mine has begun living a second life, as the operators conduct their work from remote and extremely comfortable underground offices. The goal is to increase production from 2.5 million tonnes of ore to 3 million, while also tremendously improving safety. So far, the results are more than promising.
While AI can make more informed - or as some companies boast ‘better’, decisions - fully autonomous drills are still technologically new, expensive and do more complex tasks. This means that there are many kinks and quirks that need testing and fixing before the autonomous rigs could start drilling away at a project near you. Early adoption, the process of trying out new to the market products, is a risky, costly endeavor and presents a set of new and unexplored before questions. What happens if the AI software faces some sort of a critical issue whilst working in the wilderness where there’s no signal? Is it a simple ‘turn off and on’ solution, or do contractors have to fly in a tech support to the field? And what about updates, patches, and fixes? Even the most rudimentary software reveals bugs and limitations when deployed in unique environments that demand unique use cases. Many contractors worry that without a simple and robust way to fix or update the software performance of autonomous rigs, they could find themselves stuck with a giant hunk of metal that does not work for their specific needs.
There is also the matter of adoption hesitancy within the industry. Many drillers, perhaps rightly considering the early capabilities of AI, believe that manual control is better. If there is a risk of injury, human reactions may be faster and more accurate. Humans can shut down the rig in specific risky situations, where the AI control may fail to recognize these situations as such and continue drilling.
All these questions, as well as countless others concerns, are on the minds of contractors looking to upgrade or purchase new drill rigs, thanks to the increased interest in the industry. The answers require extensive field testing, data analysis and feedback for manufacturers. However, the good news seems to be that the industry, particularly the leading companies, are open to becoming early adopters of the autonomous drills. Almost all of the ten biggest contactors by drilled meterage for 2019 are investing into the field, some are also conducting field rig tests in partnership with manufacturers.
With millions of funding into AI, in several years, maybe more and more contractors might become comfortable with the notion of adopting the technology.
Artificial intelligence drilling software
While the wide adoption of autonomous drill rigs might seem some ways off, AI and autonomous software have been helping the exploration industry for some time now. In its nature, AI is driven by data and lots of it, so as long as there is enough available, it can do just about anything programmers and engineers can envision. There are more than 30 solutions on the market with various automated and/or AI functions with new ones being frequently released by both equipment manufacturers and independent software companies. Generally, the drilling software falls within two loosely defined categories: • Drilling optimization software gathers and organizes data from drilling, geostatistics, geophysics and anything else of relevance. They make plans that aim to manage and/or maximize drilling in order to improve efficiency and save money. Objectivety.ca’s DRX, covered in Issue 16, is merely one such example. It relies on data modelling to create more efficient hole plans and/or to reduce the number of meters drilled, while retaining volumetric conversion. • Drilling safety software is used to monitor the performance of drillers and their equipment, assessing potential safety risks, project challenges or mechanical issues. Many of the newer drill rigs come with such solutions built-in and some of the leading contractors have used custom safety software to achieve zero loss time injury milestones. One such example is the Epiroc Exploration Manager, a tool analyzing drilling and operation data and enabling users to make informed decisions and actions to improve.
The average improvements to operations from AI drilling software are hard to measure. Most of the developers claim anywhere from 10 to 50% depending on the purpose and the use cases of the software. Many of the solutions are cloud-based and are available on phones, tablets and computers (even through measurement devices, as is the case with DeviCloud), allowing much easier access for all parties involved. Saving precious time and being able to make decisions, without the burden of countless sheets of documents, or an office for that matter, is considered a tremendous, albeit hard to measure, advantage by most industry executives.
AI drilling software does have similar difficulties as autonomous rigs. Bugs, stability and updates are always a point of uncertainty, as well as pricing, accessibility and ease of use. With the vast choice of

applications, contractors must do careful research before choosing to employ a certain software to their drilling operations.
Conclusion
Artificial Intelligence, despite still being relatively new to the industry, is developing quite a track record for improving both safety and productivity. Drilling software offers a vast number of solutions to most of the tricky, laborious and time-consuming issues within exploration drilling. Autonomous drill rigs, while still some ways off, appear to be a natural continuation of the development of AI. But uncertainty around their applications, functions and viability in the field needs to be properly addressed.
A recurring theme of this article is the quality and stability of software. The increasing use of AI, both in the shape of autonomous drills and apps, has created the need for more data analysts and software engineers for the industry. Their growing role in the upcoming automation cannot be overstated.
In Michael Bay’s 1998 Armageddon, NASA decides that it would be easier to train drillers to become astronauts than the other way around. After 20 years, this notion remains absurd, but there is a grain of truth to it. Experienced drillers have unique skills. Even with the workflow improvements from AI software, even with autonomous rigs, in extreme conditions or on complex jobs, human drillers cannot be replaced completely. But their work and safety can simply be improved. C Courtesy of Comacchio
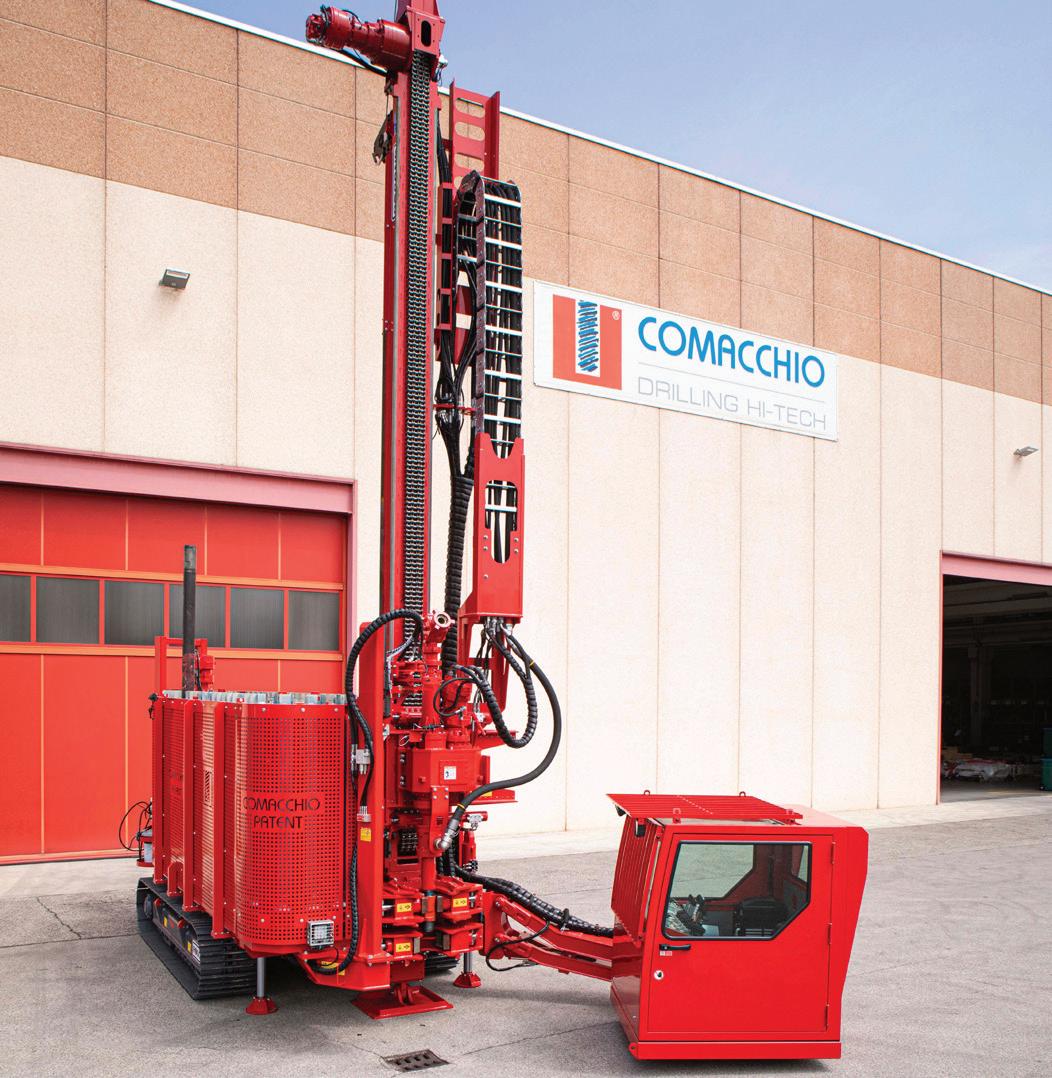
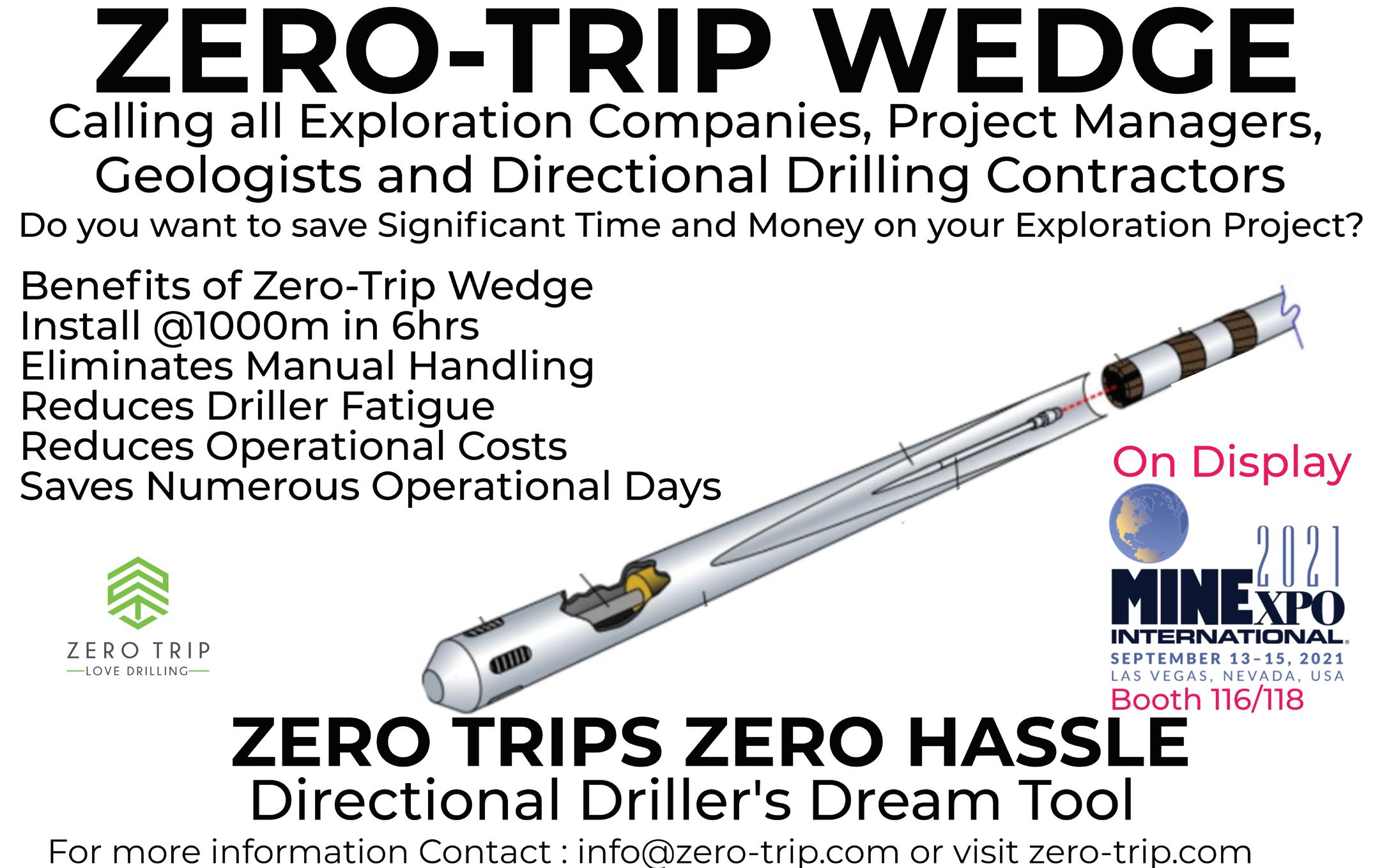