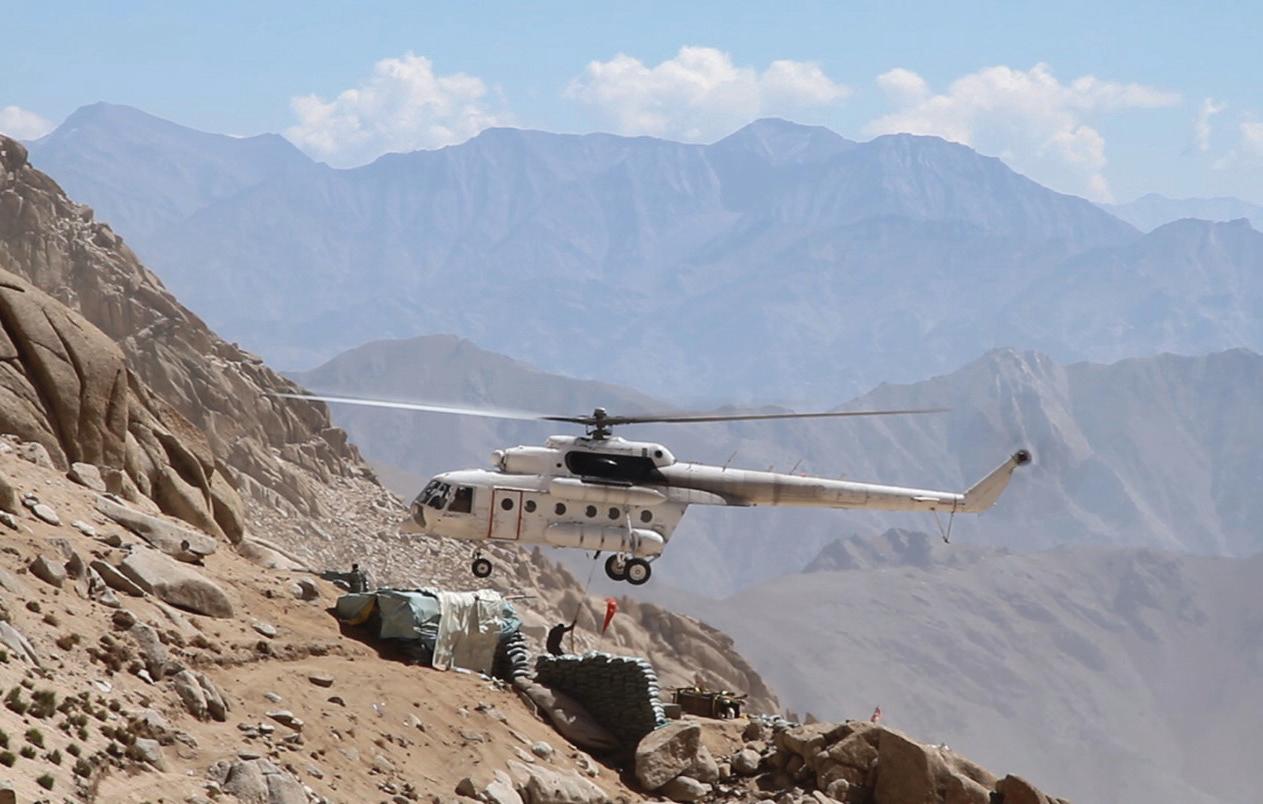
8 minute read
Drilling on top of Afghanistan’s roof
by Ibrahim Jafari, President & CEO at Afghanite Company
Afghanite Company (Afghanite) is the leading engineering service provider for the mining and infrastructure projects of Afghanistan. Its name comes from the mineral discovered for the first time in 1968 in the Badakhshan Lapis mines in Afghanistan. With many monumental track records, it has a very adventurous and exciting experience of working in a country which at first sight seems not that easy to operate in.
Advertisement
Afghanite has accomplished the largest ever topographical survey of Afghanistan using aerial LIDAR and photogrammetry techniques for a transboundary gas pipeline named Turkmenistan-Afghanistan-Pakistan-India (TAPI) pipeline. The surveyed area was a project corridor with a length of 815 km (≈ 506.41 mi) and a width of about 2 km (≈ 1.24 mi).
In 2018, Afghanite accomplished the two largest geotechnical investigation projects of the country as well. The first one was the Geotech investigation of the same pipeline route (the TAPI gas pipeline) with thousands of meters of soil and rock drilling, around a thousand trail pits excavations, and another thousand geophysical field tests in addition to those needed on the collected soil, rock and water samples.
The other was a geotechnical investigation for a new tunnel in Central Afghanistan (Salang Pass) over the period 2018-2019. Nine boreholes with a depth around 220 m (722 ft) each had to be drilled on top of three pre-selected locations, as the candidate alignments needed to have more conducted investigations for the selection of the final option. Logistics were the most challenging part of the project. Almost all the drilling points had no ground access, and all of the major items had to be transported by a suitable helicopter. The heli-support for the drilling points was not easy.
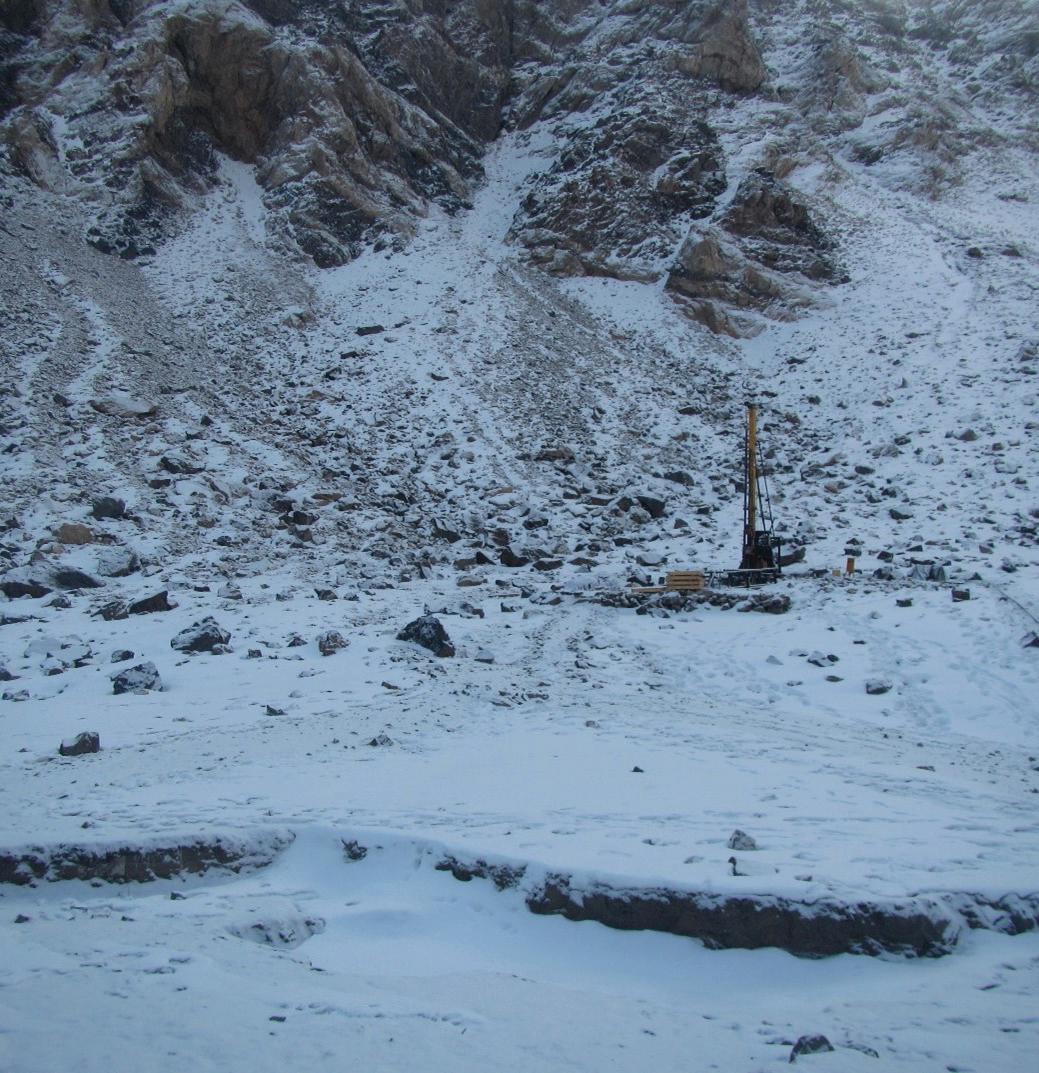
Up there about 4000 m (≈ 13 123 ft) above sea level, the winter season showed up when almost half of the work remained unaccomplished There were three major challenges: 1. the altitude; 2. strong wind and gusts; 3. making a capable helicopter available for the project timespan in the country.
Considering the very simple fact that with the increase of the altitude, the air density and accordingly the lifting power of helicopters drop dramatically, finding a solution for sling loading the drilling machines and other equipment in the project area at 4000 m (13 123 ft) above sea level altitude was quite tricky. During the evaluation of the different capable options (the helicopters KA-32, MI-17, Chinook, etc.) different factors had to be considered, such as cost of lease, cost of operation, maneuverability and availability of crew.
At the end of the day, with a little bit of support from drilling machine engineers in the reduction of total weight to the lightest possible package, the decision was made to hire an MI-17 helicopter for the mission. Of course, the aviation market of Afghanistan and the region was not particularly reliable and after a failed attempt, a trustworthy service provider got involved.
In the closed V-shape glacier valleys, the drilling points were adjacent to the rocky sides. This was a very limiting factor for the pilots. It was risky because they would need to consider the wind speed of 5 to 10 knots and wind gusts of up to 40 knots. There was a very brave pilot who took the risk and started operating. After the transportation and assembly of the rigs and accessories, drilling activity with a very high requirement (over 95% core recovery) was on the agenda. To meet the criteria in a very tectonized and lithologically diverse ground, the triple tube wireline drilling system was decided to be the most practical. The drilling sizes were mostly H-size with some cases of N-size for the deeper runs. Simultaneously with the progress of drilling, some in-situ tests had to be done in the boreholes. The major ones were Lugeon Permeability and also Televiewer tests, scanning of all the length of BHs.
Considering the lack of similar experience in the country and the hurdles in finding the needed solutions, the project activities schedule entered the fast-approaching cold season. The costs of operation, which were considered for normal weather, had to be increased exponentially to keep the project running and have it accomplished as per the requirements. At a temperature of around -15°C (5°F), it was critical to decide whether to bear the extra costs of labor and equipment as well as the increased fuel consumption or leave the
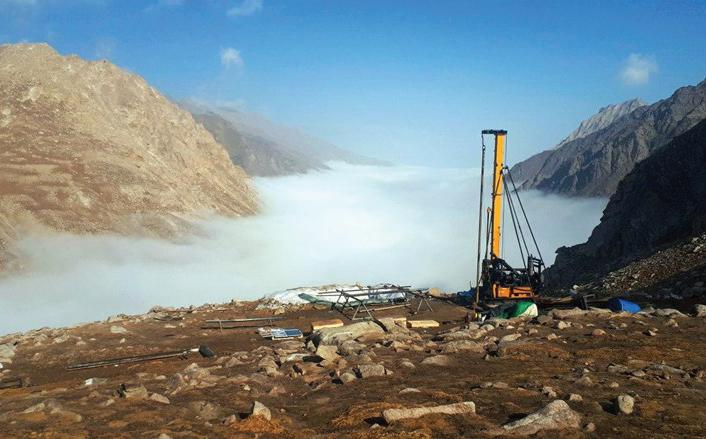
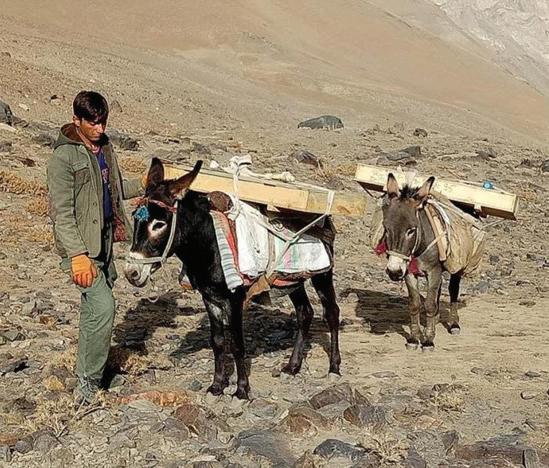
The daily support of the drilling points was done by the local people and their donkeys. The rent of a donkey up there would be more than the renting rate of a modern car in Kabul city. The collected core samples, which were about 2000 m (6562 ft), were the most valuable asset of the project. They should be used carefully to get the needed information.
A complete 3-meter H-size granite core recovered from the depth of over 150 m (≈ 492 ft) in a drilling run
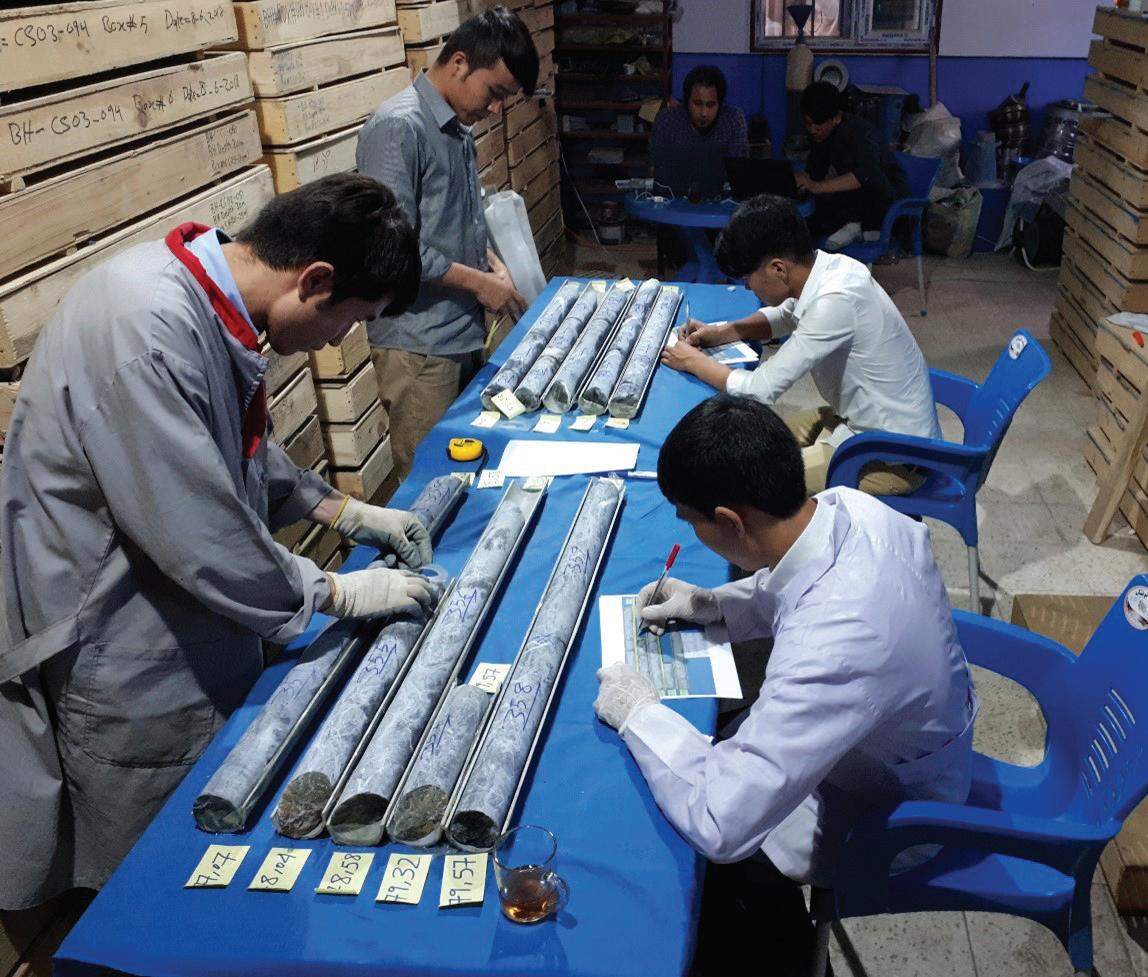
project unaccomplished. Afghanite management decided to finish the project no matter what it took.
Afghanite lab, having an ISO 17025 and also a US Army Corps of Engineers Certificate, did a great job to prepare a detailed lithological log of a whole length of collected cores. In addition to that, multiple highly sophisticated tests were conducted on the collected samples. These tests were petrographical studies of the rocks, Compressive Strength (Uniaxial and Triaxial), Cerchar Abrasivity Test, Ultrasonic waves velocity tests, direct shear of the weak surfaces, point load index, indirect tensile strength, XRF chemical analysis, and many other required tests.
Afghanite Company is trying to diversify its range of services in Afghanistan and enter into new fields, such as aerial geophysical surveys, while serving the mining and infrastructure projects with its drilling, field works, lab testing and consulting capabilities. Being of assistance and a partner to a couple of most reputable Geological surveys of the world, Afghanite has shown that in the new era which Afghanistan is entering in, it can be a reliable partner to the international community and investors as well as domestic investors to work easily on the targets they are interested in.
Afghanite Company having the experience of such sophisticated and challenging projects is looking towards expanding its activities in the neighboring countries, as well as other frontier markets where there are high technical expectations to meet and different risks and challenges to be managed. C
For more information
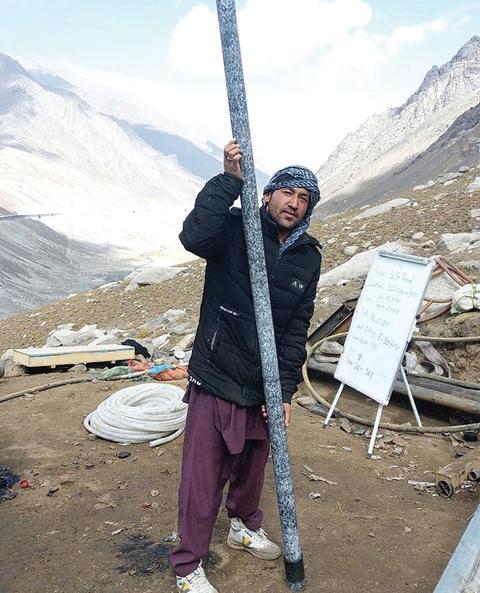
Explore the difference with RX-4
: keep doing the best, proudly
Levent 2002 RX-4 is designed by taking into consideration comfortable controls and ease of use to enable more e ective drilling. This rig also has a hold back feature, which enables much longer bit life. The mast and feed features are powerful and stable and present minimum vibrations directly into boreholes, making lifting and holding easier. The rod guide with a telescopic mast allows easier transportation. Telescopic mast The telescopic mast makes the drill easy to transport while the dump feature allows mounting on platforms of various sizes. Rotation unit The rotation unit has four speeds (funk), which enable the required torque and rpm speed levels necessary for coring. It can drill e ectively from 45° to 90° angles, make and break rods (by using the control panel), and it also incorporates safeguards. Rod holder The rod holder opens hydraulically and closes using gas pressure. In the event of a loss of hydraulic pressure, the drill string is immediately blocked by the rod holder stopping the drop of the drill string into the hole. Wireline hoist The wireline hoist is mounted on the chassis and has an adjustable level wind angle. It does not need to be moved when changing drilling angle.There is an automatic winding system to prevent the rope from making straight or mixed winding. Power unit The Cummins engine is acclaimed for its prolonged durability, high e ciency and low fuel consumption even in the most challenging drilling operations. The engine conforms to Tier III/ Stage 3A. A Stage V diesel engine is available far US and European markets

Levent 2002 RX-4® surface coring rig Advantages
• A fully hydraulic surface coring rig; • Designed for exploration drilling; • With three types of carriers: trailer-, skid- and crawler-mounted. • A remote control feature that enables the driller to operate from a safe distance What makes Levent 2002 RX-4 unique is the awless combination of veri ed concept and durable components. The rig adopts the most advanced technology for diamond core drills and the latest developments, in order to carry out e ective drilling. Levent 2002 RX-4 has all the necessary features and safeguards to protect the driller from the hot and moving parts. Self-contained control panel
The rig has a self-contained control panel, a mast dump, hydraulic jacks, and a telescopic mast, which allow an easy setup. Its ergonomics and safety bring a serious advantage; both for the driller and for the environment.
The bellow drill depth capacities only serve as guidelines and refer to vertical down drilling. SON-MAK cannot guarantee that these results can be achieved in all drilling conditions
Drilling depth guidelines
The rotation speed, power and rotation unit aperture of Levent 2002 RX-4 are made to present optimal performance in 60-122.6 mm (2.36 - 4.83 in) (B-P) diameter wireline or conventional drilling. As far the spindle bore, its diameters is 127 mm (5 in).
Size B Wireline N Wireline H Wireline P Wireline
Meters Feet
Kayapa I. Organize San. Bölgesi, Kayapa Sanayi Bulvarı, BURSA, TÜRKIYE Tel : +90 224 440 0 555; Fax : +90 224 482 44 39 tr;