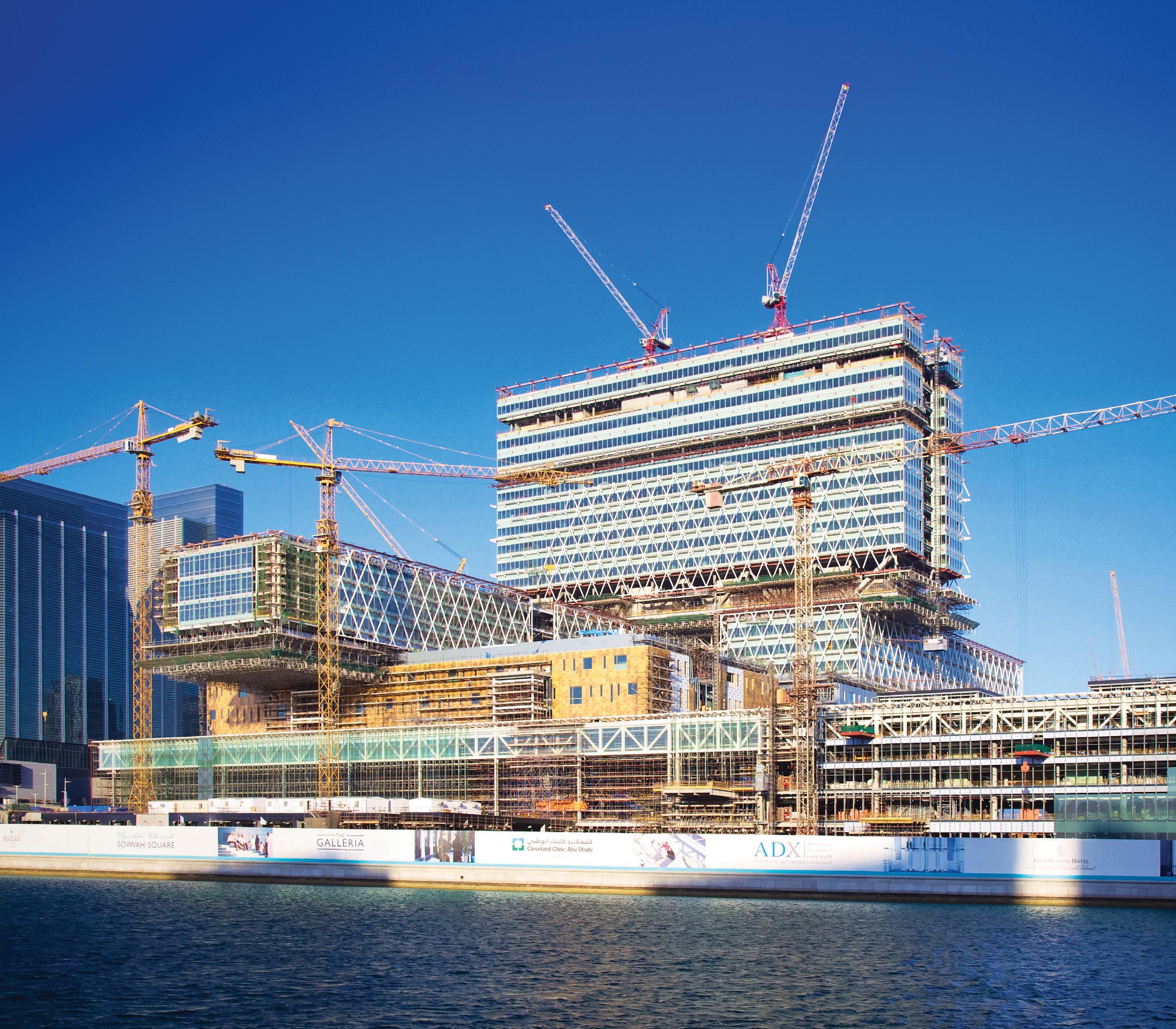
9 minute read
The briefing
Technology
Breaking Down Barriers
MIDDLE EAST Tom Boland, director at Zutec UK, outlines why digitisation is urgently needed for the regional construction industry
Why does the construction need industry to digitise faster? The construction industry is known to be unproductive, and it has been this way for decades.
One solution is digitisation, which can drive productivity and profitability. Its advantages span from mobility—no more struggling to keep track of each component of the paper trail—to the Internet of Things and advanced analytics. Cloud-based software can help construction professionals manage the entire construction process digitally, from the design phase through to handover. Further, digitisation minimises errors and risks, and helps professionals to maintain compliance by keeping project records secure and scheduling customised inspections. Such tools also help companies to assess their digital processes when it comes to maintaining building safety standards, as well as meeting decarbonisation goals and shifting to green construction.
Lastly, digitisation in the industry is set to improve data and transparency, making it easier for architects, developers, contractors and subcontractors to collaborate and see how every aspect of their project is being managed and how it’s progressing. There are also new
1970
The first BIM software tools emerged in the late 1970s and early 1980s
Breaking barriers
Digitisation is breaking down barriers in the construction industry by improving transparency, minimising errors and risks, and maintaining standards and performances.
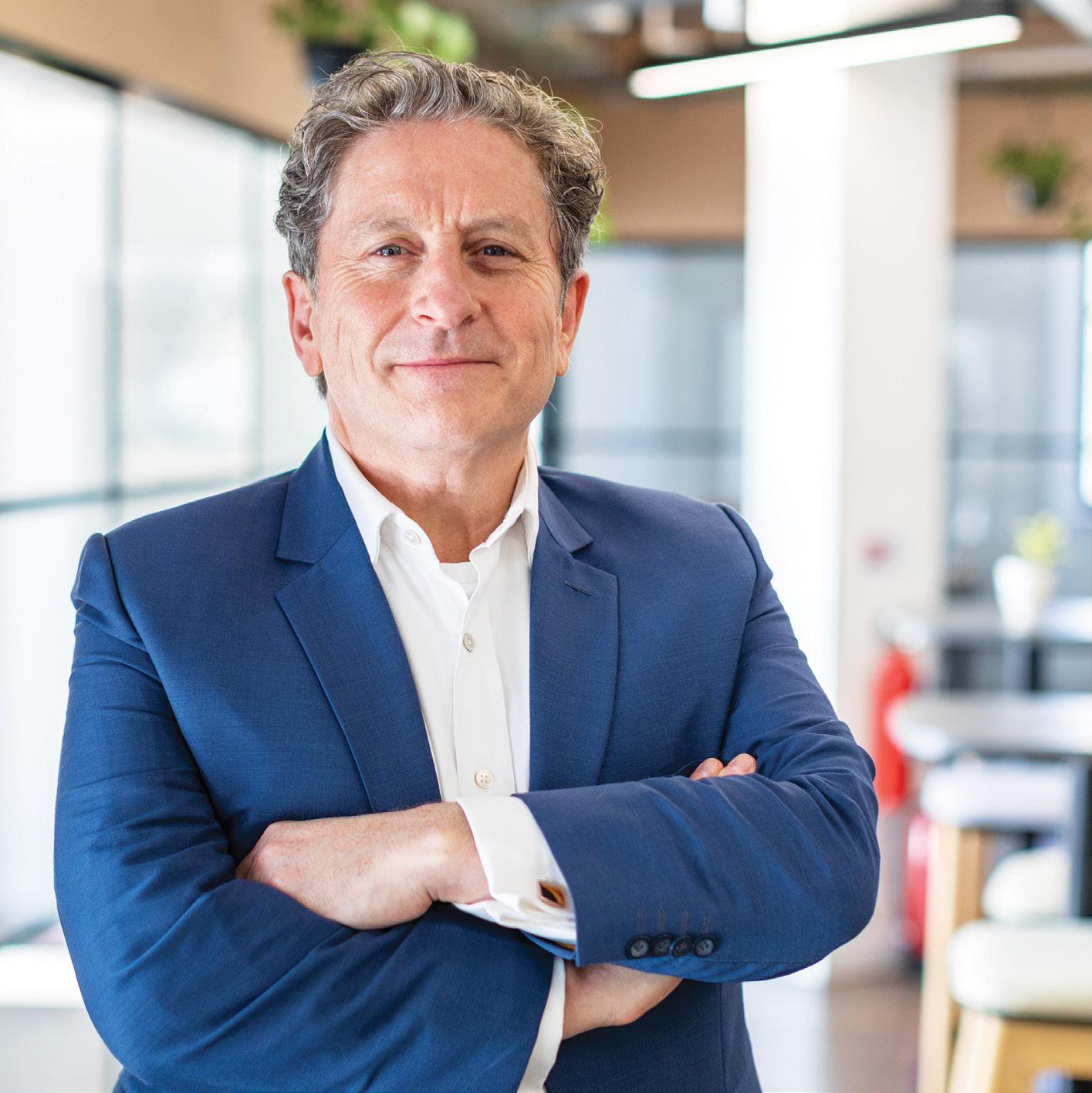
Data democratisation
Tom Boland says that the Middle East construction industry can benefit hugely from the democratisation of data. tools, such as the Value Toolkit being launched in the UK, which are designed to assess the real value of projects and how they will benefit society, the economy and the environment in the long run, thus completely transforming the way the sector carries out its work.
What are other technologies that need to be embraced by the industry? While BIM has been around since the 1970s and has increasingly been put into use over the years, newer forms have come into play recently, which are used across the entire life cycle of a building rather than in the design phase alone.
For example, ‘Field BIM’ manages construction data in an information model and uses it to inform accurate construction, operations, or maintenance on site. With this, handheld mobile devices become essential tools in accessing shared information and collaborating in real-time with colleagues at the office. The process saves time, minimises the risk of error, builds trust, ensures coordination, and boosts visibility. When used in conjunction with CDE modules, companies can get the full picture regarding their projects and can streamline everything from design collaboration to accountability and site safety.
Other technology includes inspections protocols and tools—ranging from non-specialist tools such as Zoom and MS Teams, to specialist platforms like Zutec—AI, which is particularly useful when looking at data, patterns and trends for business, VR and AR, which are commonly used at the design stages, but can also be used on site, and drone inspections, which are becoming increasingly commonplace, especially on the QA/QC side of projects.
What are some of the biggest barriers to entry when it comes to digitisation in the industry? For many years, one of the biggest known barriers to entry when it came to digitisation in construction was cost. However, this barrier has been greatly reduced and access to connectivity has dramatically improved. It’s currently cheaper than ever to bring on board, and run, digital tools.
Along with being more affordable, today’s tools are also smarter, and don’t need total connectivity at all times. For example, with a Field BIM tool, quality and compliance related checklists can be created on site and without an Internet connection.
Another barrier is the large number of people who still have minimal digital skills or are reluctant to adopt them. They worry digitisation will involve a massive change in how they do business and that it will be too complex. This becomes a problem at all levels, such as when major contractors ask subcontractors to use digital tools in their projects—if they don’t have these capabilities, they’ll miss out on jobs.
This barrier is steadily being removed due to a digitally savvy younger generation moving up the career ladder. To continue breaking it down, however, training programmes and regular courses should be offered.
Why is it important to democratise data and can this truly be achieved in the Middle East? The end principle of any project should be that the client owns the data involved in the construction of their assets. One of the benefits of more transparent use of data is de-risking: if people are recording their actions and are accountable for them, this can drive up standards. Further, one’s digital fingerprints are all over every aspect of the project he or she is involved in, therefore, by sharing data, it will make one’s day-to-day life easier, smoother, and better all around. It will also alleviate the historic problem of construction being adversarial and litigious.
While there may need to be changes around contract law and culture in terms of working with other companies, everyone will benefit from digitisation.
In terms of the Middle East, construction is a key driver for growth, and companies in the region need to be leading this adoption to stay relevant. Lean construction processes and off-site manufacturing are forecast to both reduce site effort and increase delivery speed.
Furthermore, off-site manufacturing and DFMA (Design for Manufacturing and Assembly) will become a globalised commodity and value opportunity. Regionally, as a delivery hub, the Middle East can give forward-thinking local firms the opportunity to provide products and services outside of the region.
Value from Building Data and Analytics
MIDDLE EAST Facilio’s Prabhu Ramachandran on how you can extract even more value from building data
The US Department of Energy’s four-year Smart Energy Analytics Campaign recently presented findings that found analytics software had led to a median of 9% energy savings, in six and a half thousand buildings studied across the US. In the last few years, the consensus around the impact of operational analytics software for buildings – in predictive maintenance, energy management, commissioning etc – has become nearly universal in the commercial real estate industry.
Although this mainstream acceptance is a welcome first step, it is also becoming obvious that to truly optimise the power of analytics, the industry needs to become better at implementing the insights it unlocks. Let’s take a look at how improvements in software can enhance this leap from insights, to actionable outcomes.
GETTING MORE FROM ANALYTICS Analytics are not a standalone ‘magic’ solution. For software to transform your operations to be more data-driven, you need to have a team that can drive the journey from insights to action, with empirically measurable results. So, one of the critical capabilities, which a great O&M software must have, is allowing all stakeholders and vendors to collaborate effectively.
But that’s just a start. Prescriptive insights either uncover physical or system level issues. The first kind - that is, physical issues – usually need active human involvement to be resolved. Human intervention in system-led control issues, on the other

Personalised experiences
The demand for greater automation, control and personalised experiences will continue to grow in smart buildings.
9%

Average energy savings using analytics software in a recent US study
hand, is much more complicated. Any enhancement needed in the Three S’s - Sequences, Setpoints, and Schedules – requires the reprogramming of local automation software. This is far from straightforward, and even if a local control system is improved, the process will need to be repeated for all systems in your portfolio.
As emerging smart building technologies add to the solutions you employ, this process will only get more complex. Especially since greater automation, more sophisticated control sequences, and the ability to deliver ever more personalised occupant experiences, will continue to escalate. The need for O&M teams to drive efficiency across every process, performance metric, and workflow, makes a strong case for cloud-based portfolio automation software. This portfolio-wide approach allows management software to be consolidated, and control sequences to be made more effective, at scale. Let’s consider the advantages of the approach:
• Ownership of portfolio
optimisation process: For fully optimised operations, O&M teams need control over data, as well as sequences, setpoints, and schedules.
Legacy control software is unable to provide this, because it was designed to be used by vendors. Cloud-enabled software platforms overcome these limitations, taking into account inputs from all stakeholders, including occupants, to achieve full spectrum enhancement that ticks every box.
• Portfolio scale consolidation of
management software: Legacy building management software systems depend on separate applications for each function. The new generation of cloud-based software platforms enables portfoliowide unification and eliminates redundancies. Challenges, such as the recent pandemic, or the introduction of new regulatory guidelines and standards, can be overcome far more easily by replacing obsolete control sequences through over-the-air upgrades.
• Cloud-enabled control sequences:
Just like cloud computing enhances
the power of analytics to crunch data, cloud-based machine learning unlocks the ability to constantly upgrade control sequences - predictively and proactively. The ability to take all real-time data and all sources across a portfolio into account results in much more comprehensive control sequences.
A NEW BENCHMARK Analytics applications leverage advances in cloud computing, to crunch all the data created in local control systems, to generate insights. The next step in this evolution is to leverage the cloud for control sequences as well. A portfolio automation software will use cloud-based machine learning algorithms to create predictive and proactive control sequences, replacing the reactive control sequences of the past. They will be able to leverage data from any system, in the building or the cloud, instead of just the data available in the local controller, to improve the effectiveness of the control sequence.
For example, whereas the state of the art local control system needs occupancy sensors to tailor ventilation to actual occupancy, a cloud-based portfolio automation software will make use of the best available occupancy data, whether from an occupant app, WIFI access points, people counting device, or access control system.
To reach the benchmark, the cloud-based portfolio automation software needs to be paired with a secure and intelligent edge, to monitor for local connection issues and mitigate in real-time.
Next, the software needs to be capable of implementing supervisory control for all building systems: state of the art sequences, continuously updated, with self-service management and modifications of schedule and setpoint standards.
The new benchmark requires a strong roadmap focused on ML capabilities, to make predictive and grid-interactive enhancements, while enabling open integrations and workflow automation, to enable modern O&M use cases.