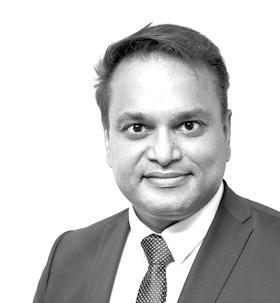
8 minute read
Comments
Industry insight
CHRIS MEIR
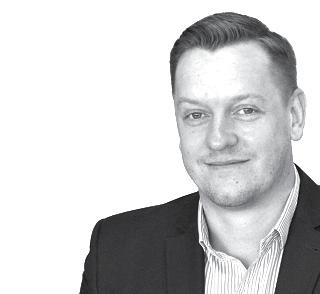
CONEX BÄNNINGER MIDDLE EAST
The Impact of True Value Engineering
Across the construction industry, many of us use the term ‘value engineering’. In fact, it’s often a topic that sparks hot debate between contractors and consultants, sometimes with different approaches to the practice. But do we know how and why value engineering was conceived?
Value engineering was first practiced during World War II as a response to skilled labour shortages and lack of raw materials. Lawrence Miles, an engineer at General Electric, noticed that some material substitutes were not only effective at reducing costs but also resulted in a final product of greater value and quality than before. And so, the methodical approach of value engineering was born.
In my opinion, value engineering is a term often used in the industry to justify cost cutting. However, this is a common misconception. Value engineering does not mean cutting costs for a cheaper overall outcome. In fact, the primary principle of the concept is that functionality and quality must be preserved, and not reduced, as a consequence of lowering costs.
Finding methods to lower costs is a welcome benefit, but the objective of value engineering is to add real value to the overall process. True value engineering should promote the planning and delivery of projects with improved performance.
In the construction industry, value engineering is a key exercise that should be considered across the supply chain. The aim is to reduce costs and eliminate risk while optimising design for an end result that benefits all parties involved, as well as the end user.
Challenges arise when value engineering is approached with a cost-first mindset that compromises on the functionality and quality of the product. With this approach, we risk a substandard finished product due to a singular focus on cost reduction. The regional construction industry is competitive – it is a price driven market in which companies often lose projects to competitors based solely on cost, rather than on their ability to deliver high quality, appropriate certifications or legislative requirements.
For example, a consultant may specify a highperforming solution based on project demands. However, the contractor may choose to disregard the original specification and opt for a cheaper solution. If costs are cut this way across the project, the contractor risks engineering the value out of the project. In the short term, this may have cost reduction benefits. In the longterm, however, moving away from the original specification can have negative consequences for buildings, developers and end users.
Certain products are selected because of their ability to provide a specific solution. True value engineering should defend the design by adhering to the specification in order to protect the integrity of the project. Moving away from the specification to save on capital costs can simply lead to a project that incurs additional costs down the line when it comes maintenance, durability, and safety.
Furthermore, compromising performance for lower costs may lead to health and safety issues. The role of every space we create is to maintain occupant comfort and protect public health. Opting for solutions that compromise on quality, or even basic function, can not only inconvenience occupants, but lead to potential health hazards such as pipe bursts, leaks or fires. Material substitution should be based on performance, rather than just price. Often, alternative products are selected based on price, even though they are not suitable for the given application. When quality is sacrificed, safety standards are jeopardised, which can have a detrimental effect on the building and its occupants. As we move forward, the construction industry is placing increased importance on health, wellbeing and sustainability. Creating human-centric spaces is integral to progressing the industry.
SANJEEVV BHATIA
NETIX GLOBAL BV
Connected Buildings Provide a Silver Lining to the Pandemic
The COVID-19 pandemic has been a crisis that affected the entire world. It left a particularly significant impact on the real estate industry, given that residential buildings needed to secure their occupants from an invisible menace, and most non-residential properties, still in use, were being used for essential services. Digital transformation was already making major inroads into the commercial real estate industry, when the pandemic struck. The immediate aftermath of the crisis proved to be clinching evidence that IoT and AI enabled connected buildings were far better suited to crisis management, than properties relying on legacy operational models.
Some of the key advantages that digitally integrated buildings were able to leverage, during the course of the COVID-19 pandemic, have been: • Remote visibility and monitoring: With social distancing restricting onsite staff, delivering on all the critical functions on which a modern building depends became one of the first post-pandemic challenges.
Connected buildings gave owners and facilities managers the ability to monitor and manage their assets remotely. This allowed them to perform several maintenance and management tasks remotely.
• Effective energy management through
live data feeds: Sustainability in real estate has been an area of focus, for some years now. In the aftermath of the pandemic,
with financial pressure on the commercial real estate industry at their zenith, effective energy management became critical to business outcomes. IoT and
AI enabled building portfolios were able to derive actionable insights from realtime data, and optimise energy usage.
• Ability to deliver on enhanced protocols,
despite fewer onsite staff: Sanitation and access management has assumed unprecedented importance, in the post-
COVID era. Delivering on the enhanced protocols was a challenge, with limitations on the number of deployable staff members.
Remote monitoring, workforce coordination and verifiable digital records have proved to be indispensable in ensuring compliance.
• Minimised facility management
operational costs: Several commercial properties bore a barren look, with lockdowns and quarantine measures in effect, across the globe. Those residential buildings, to which people were restricted, were also impacted by rent waivers, in many locations. Under these circumstances, connected buildings proved to be far more capable of lean and agile operations, which addressed occupant safety and comfort, while also lowering operational costs.
• AI and IoT based automation upgraded
buildings to ‘smart’ status: The commercial real estate industry has long been aware of the need to upgrade its assets, so they are brought in line with the coming age of smart cities. The pandemic accelerated the rate at which building portfolios were digitised, upgrading existing buildings to a
‘smart’ status, thanks to digital retrofits.
The World Health Organisation (WHO) along with other international medical bodies, and subject matter experts, have all stressed on the fact that the COVID-19 contagion could well be the first of more global pandemics, in the modern era. This most recent pandemic has underscored the sheer scale and speed, with which a global crisis can impact our hyper-connected world.
One of the silver-linings to this crisis has been that connected buildings have proven their capacity to respond effectively to such challenges. An already compelling argument, for the adoption of digitally integrated commercial real estate operations, has now become indisputable.
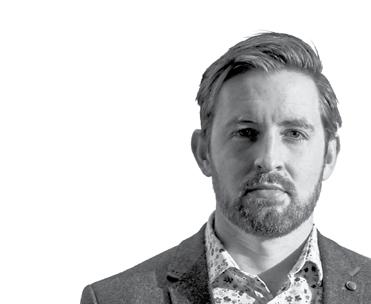
RUPERT TAIT
PROCURIFIED
Building the Future: How Digital Technology is Impacting Construction
The effects of Covid-19 forced every industry to adapt to new ways of working and much of the past year’s stratospheric pace of adaptation has been enabled by digital innovation. It had to be – with the world working remotely, there was no other choice.
But while many digital solutions allowed work to continue as normal – such as remote video-conferencing – necessity was the mother of invention when it came to transforming established industry practices.
Construction, with its historic reliance on paper trails, has always been notoriously resistant to change, but Covid-19 proved to be a tipping point.
Even as recently as last year, my consultancy firm, Smith Tait was being asked for its electronic submissions on CD by construction companies. Most computers don’t even have CD drives any more.
Information was flowing slowly, which was impacting my business. I realised it was impacting every stakeholder in the process, an ‘a-ha’ moment. I knew I could build something to help my team, but I realized in order for it to make a game-changing impact it would need to help everybody.
Decision-making in the construction industry has always relied on face-to-face meetings, with procurement heavily rooted in paper-based submissions laboriously inputted and compared using traditional desktop spreadsheet software such as Excel.
Procurified, founded with my business partner Marc Lemmens in 2020, streamlines the entire procurement and estimation process, by connecting suppliers and manufacturers with contractors on a cloud-based user-friendly interface. Data such as costs, timelines and quantities are uploaded into a centralised system that can be instantly and automatically reviewed.
Every building has to be designed and requires products and materials to be purchased on time and on budget. How efficiently the procurement process is achieved has a huge impact on cost. With our effective procurement processes and tool, we allow our customers to save up to 80 percent of their time traditionally spent on this process, while enabling them to reach out to ten times the number of vendors.
Our customers such as ALEC FITOUT and BK Gulf, are saving 80% of their time when prepping and reviewing estimations. That’s the benefit. Procurified replaces the hugely time-consuming need to use dozens of separate spreadsheets and PDFs.
We have already achieved an impressive $17million of transactions to date and was awarded first prize of $10,000 by start-up accelerator company CSA7.
It’s an exciting time to be in construction, as I believe the industry is finally experiencing its own ‘Uber moment’.
For example, on-site surveys used to involve a group of people walking around a construction site, recording everything manually with a camera and spreadsheets.
Now, there is a platform attached to a camera that takes live 3D images of the site, which can be uploaded to the cloud, labeled and progress compared. Meanwhile, there is a company that has developed a way to measure how concrete is setting using specialised sensors.
We see changes at every level of the industry that are underpinned by advances in digitally based technology. To be positioned at the vanguard of change in the global construction industry is incredibly exciting.