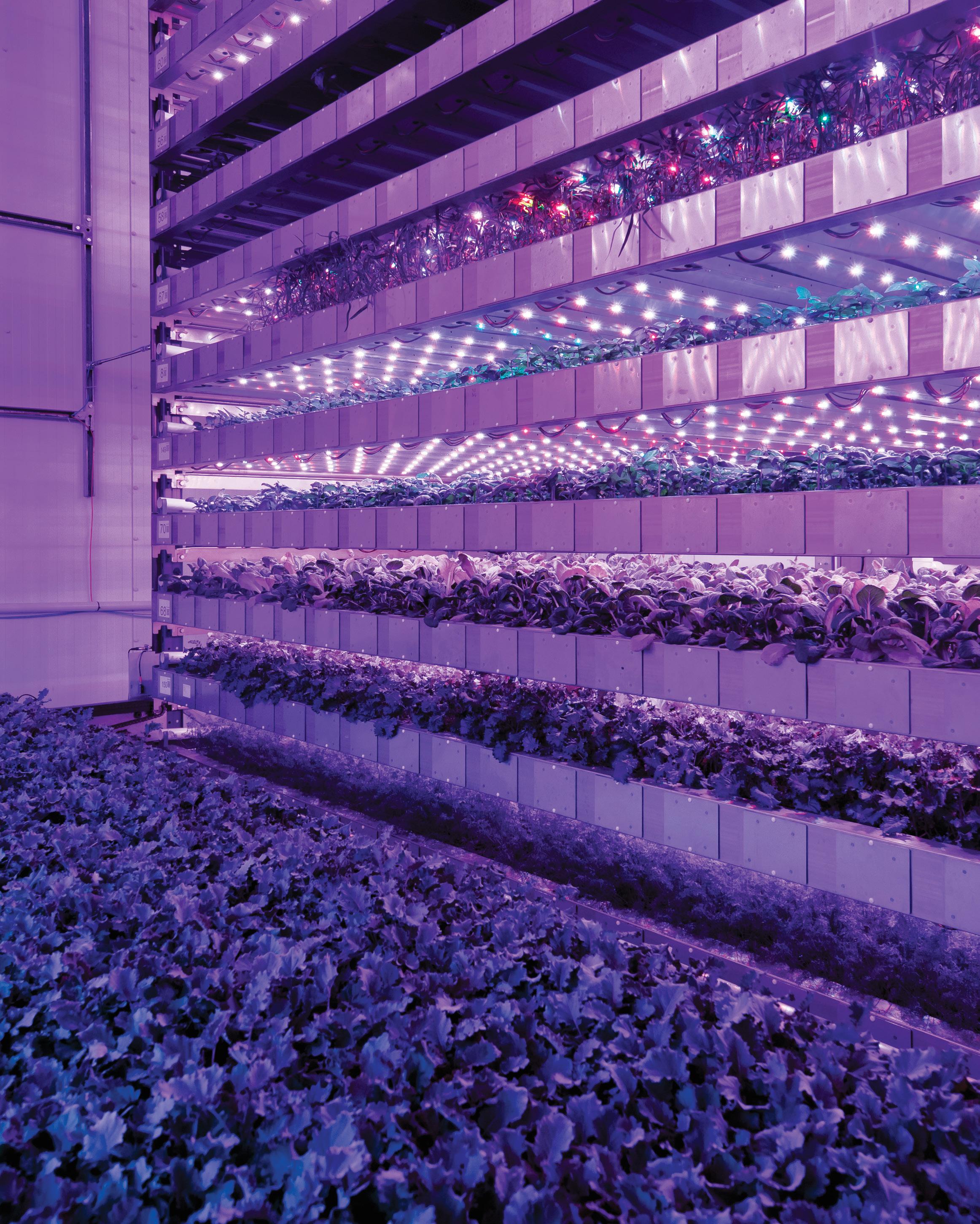
21 minute read
Project profile
IREPfarm
PROJECT NAME:
Vertical Farming Facility
CLIENT:
Madar Farms
LOCATION:
Khailfa Industrial Zone Abu Dhabi (KIZAD)
Green Shoots of Growth
BIG PROJECT ME SPEAKS TO KENNETH MCCRAE, MANAGING DIRECTOR OF INTERNATIONAL REAL ESTATE PARTNERS, ABOUT HIS COMPANY’S NEW VENTURE, IREPFARMS, AND THEIR WORK IN THE VERTICAL FARMING SECTOR, STARTING WITH THEIR FIRST VENTURE WITH MADAR FARMS
n November 2018, Mariam Hareb Almheiri, Minister of Climate Change and Environment for the UAE, unveiled the country’s National Strategy for Food Security, outlining 38 short and long-term initiatives, geared around five strategic goals that focus on: facilitating the global food trade, diversifying food import sources, and identifying alternative supply schemes.
The National Strategy aims to make the UAE the world’s best on the Global Food Security Index by 2051 and among the top ten countries by 2021. In order to do this, it looks to develop a comprehensive national system based on sustainable food production through the use of modern technologies, enhance local production, develop international partnerships to diversify food sources, activate legislation and policies
In the wake of this announcement, the UAE has seen an explosion of homegrown agricultural solutions, with several companies adopting a high-tech approach that integrates automation and vertical farming to create a resilient and sustainable regional food supply chain.
With the UAE currently needing to import as much as 90% of its food, this approach is vital if it is to achieve its goals of self-sufficiency. Due to the country’s location, climate and water and land resources, investing in hightech agricultural solutions is the only way forward, says Kenneth McCrae, the managing director of International Real Estate Partners (IREP).
“We are very fortunate here that the UAE government have been very strategic and clever at attracting technology providers to the region. The plan is to create an agri-tech ecosystem that provides the right technologies to support a diverse population.
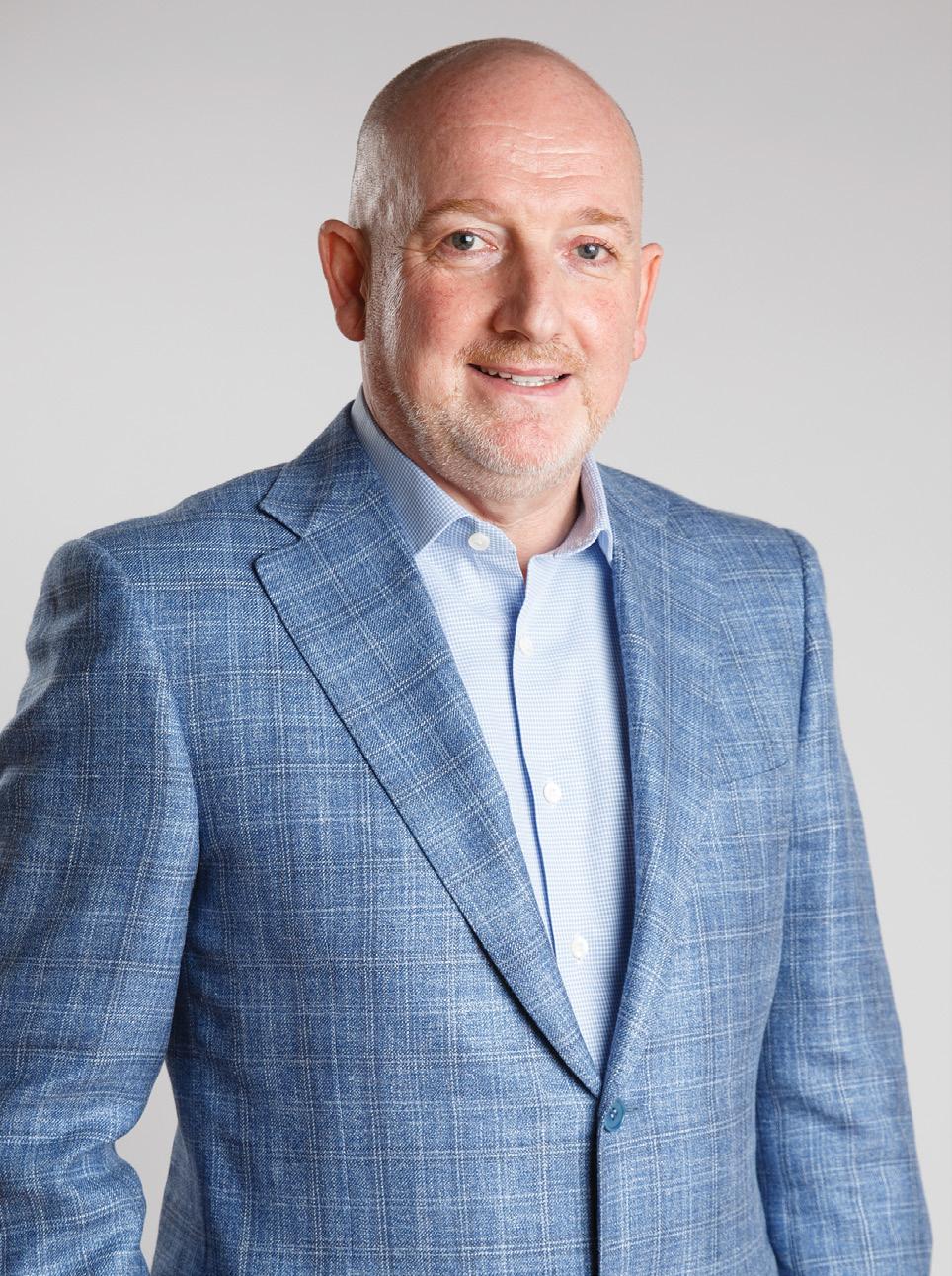
Homegrown solutions
The UAE government has been very strategic and clever in investing in high-tech agricultural solutions, says Kenneth McCrae.
90%
Percentage of food imported into the UAE
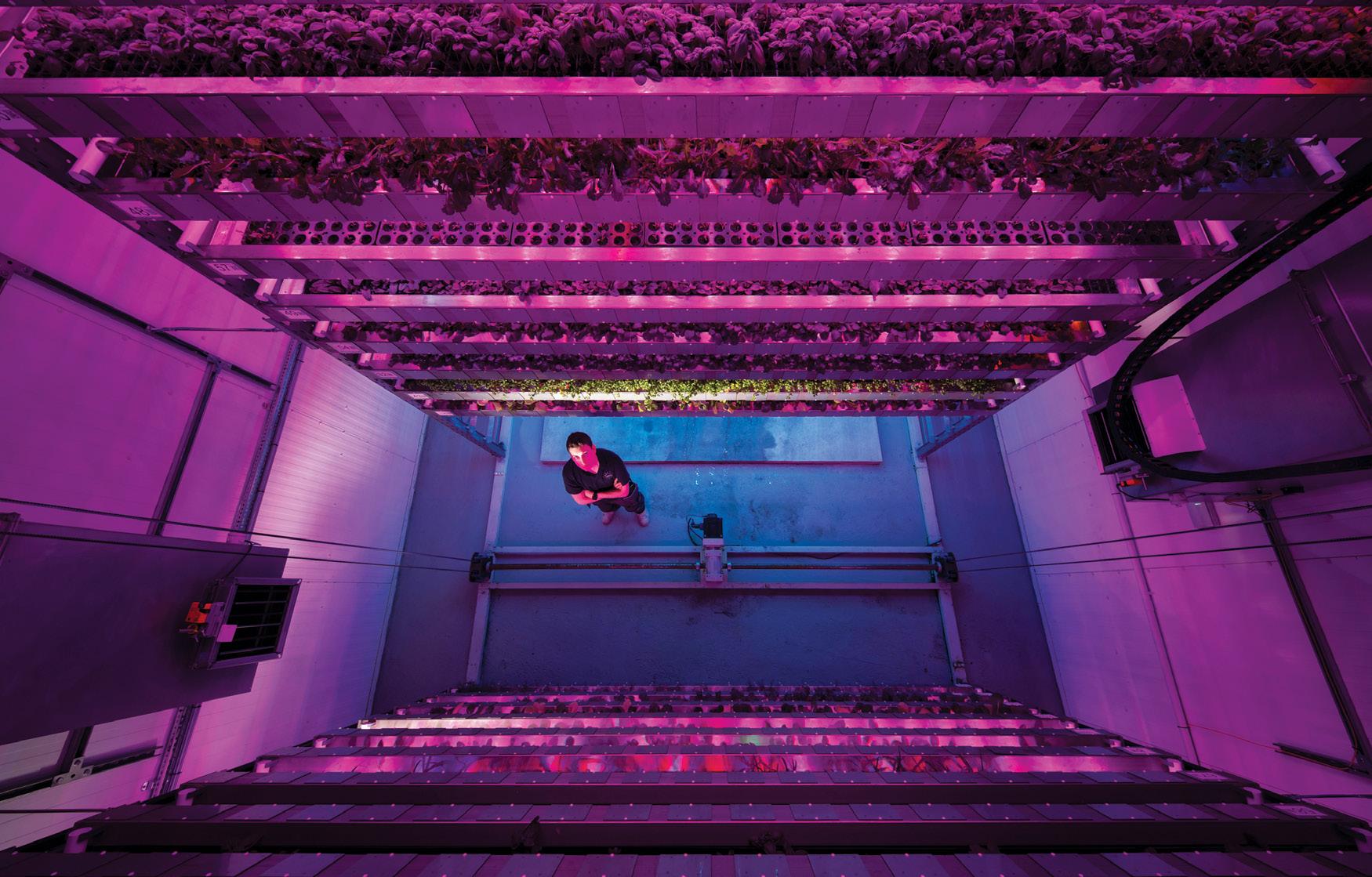
There is a real opportunity to embed the technology into food production systems right now, for a better future,” he tells Big Project ME during an interview at IREP’s offices in DMCC.
Noting that investor interest into vertical farming is on the rise, in March 2021 IREP launched a new venture called IREPfarm, which aims to bring an innovative, practical, knowledge and sustainability-led approach to the worlds of real estate and argi-tech solutions in the UAE and wider GCC.
McCrae explains that IREPfarm will be at the forefront of the movement to tackle the multitude of issues presented by climate change and its impact on the world’s food supply chain. Furthermore, the company will also look to improve the ability of governments, and the food industry as a whole, to provide for their populations and customers respectively.
The venture will see IREP work side-by-side with its long stand agri-tech partner, Intelligent Growth Solutions (IGS), he adds. This partnership will see IREPfarm develop its capabilities and improve its knowledge of the latest agricultural trends and techniques, the most advanced technological solutions, and the up-to-date developments in the real estate sector.
“Everything that we do is about doing things in the most effective and efficient way – so then, when you apply technology, and when you do it with the experience and expertise that we

have in facilities and asset management, technology and energy that we can wrap into a sustainable lifecycle,” says McCrae.
“We look at everything in 10-to-30year outlooks and then we create the most viable plan, with cost certainty from design, construction, and operation of the farms throughout their entire life-cycle. When you do that, that’s when your ROI comes in, because you’ve got a big picture financial view of what your real costs are, and what the impact is of how you manage your assets. Obviously, the technology today is so clever, you can do a lot of things a lot smart and react quicker to changes in the profile or the dynamics of the assets, the environment, or how they’re utilised.”
McCrae adds that working closely with IGS over the years made the IREP team aware of a number of pressing issues that are jointly facing the agri-tech and real estate industries. This is why it made sense to leverage the companies’ experience to create IREPfarm, allowing them to pool their expertise and deliver bespoke food security and real estate solutions to a broad client base that operates across a number of sectors and helps to deliver results on a large-scale and impactful basis.
Therefore, the essential areas where IREPfarm’s collective of experts will support clients include: Updating clients’ knowledge of farm management and operational knowledge; Boosting clients’ understanding of commercial supply avenues for farm products; Managing numerous contractors across multiple disciplines and budgets; Meeting assurance, compliance and industry standards at manageable costs; Introducing a greater focus on design to enhance the use of farm facilities through restaurants, education centres and community spaces; and finally, providing ongoing asset management to ensure the optimised life cycle of its solutions.
“The introduction to IGS was through the technology – we saw the technology
Food security
IREPfarm’s close relationship with IGS has allowed it to deliver bespoke food security and real estate solutions to a broad client base.
38
Number of initiatives proposed by the UAE’s National Strategy for Food Security
in the lighting. IGS wasn’t just looking at the farming sector, they were also looking to sell lighting as a service product as well, because of its super efficiency and its ability to become an IoT enabler. We saw that IoT technology could be attached to lighting, and it was a real win-win technical solution.
“That was the initial push, and then we started to do the background research – this was three years ago – and we started the IGS relationship with the Middle East as the UAE currently imports 80% to 90% of its food due to a number of issues, including a lack of water, high temperatures, and the lack of arable land. This needs to change, which makes IGS’ vertical farming technology a very attractive solution for this region.”
As the UAE emerges from the shadows of the pandemic, the last 12 months have highlighted the substantial need to secure local and sustainable food supply chains in the GCC. With the GCC’s population set to increase
considerably, the importance of precision-based agri-tech solutions, backed by scientific crop research will be key to addressing these challenges.
“There are many technologies out there that will help deliver the demand from the region,” says McCrae. “I believe that it’s important to create an ecosystem, but the huge benefit with the IGS technology, that will help with the demand, is that it’s scalable and modular. Many clients like to start with four towers and scale as the demand requires, which is something that is very easy to do with IGS technology.
“A basic four-tower arrangement takes up 307sqm of land. The towers can either be six metres, nine metres or 12 metres high. We recommend an additional 500sqm for the service area, which may need to expand if more growth towers are later added to create a larger operation. A 12-metre-high superstructure is recommended as it will deliver the greatest return on investment and yield per square metre footprint.”
McCrae points out that IREPfarm’s first towers are going up in KIZAD, Abu Dhabi, with the company’s client, Madar Farms, which is a local Emirati company that has already developed a range of premium quality indoor grown crops to supply to the local UAE retail market.
The deal is the first to introduce IGS’ technology to the UAE and is in line with the client’s vision of creating sustainable food supply channels to the UAE population, while reducing

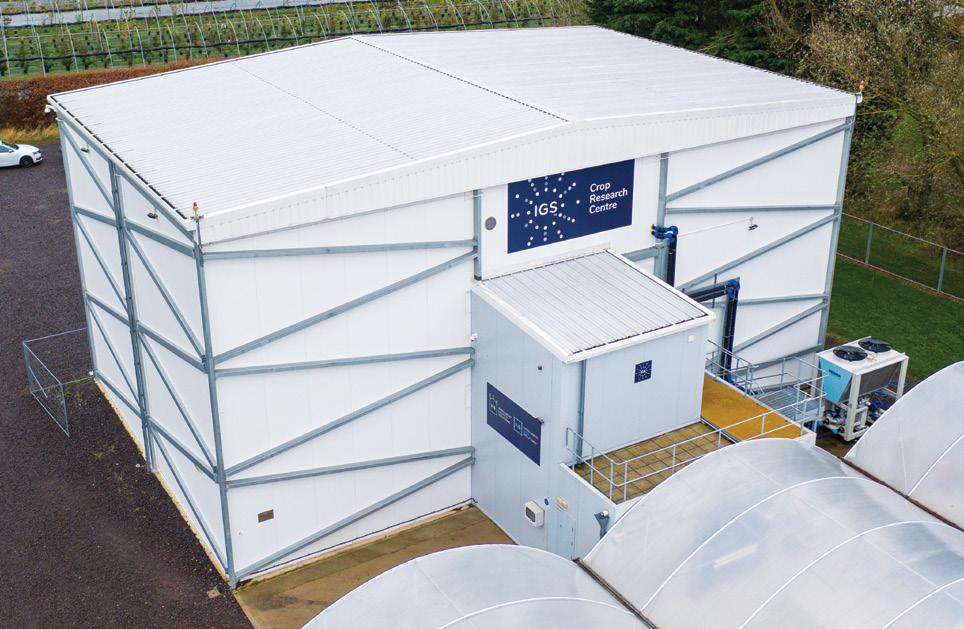
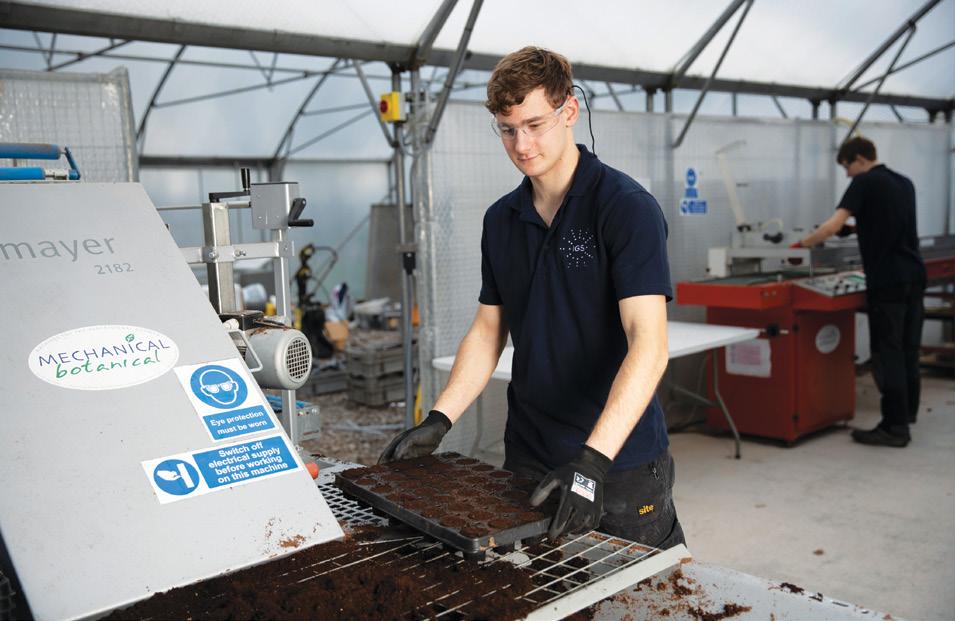
Growing space
A 12-metre-high superstructure is recommended for the best return on investment and yield per square metre footprint.
307
Average footprint, in sqm, of a four-tower facility
the strain on scarce water supplies. There are five growth towers initially planned, each standing six metres high, offering a growing space of up to 150sqm and the ability to produce up to 30 tonnes of crop per annum.
Madar Farms says that it selected the IGS plug-and-play vertical farming platform after a rigorous competitive market assessment to significantly enhance the quality and quantity of produce it can supply to businesses and leading retailers across the region.
Initially, commercially sold produce will include a range of premium leafy greens and herbs, which will be enhanced by other crop varieties in the near future. The partnership will also allow a greater capacity for research and development, particularly in the propagation of tomato seedlings, which is a significant focus in region. The client will utilise the high levels of precision in the IGS system to enhance early-stage quality seedling production which would then be moved into an indoor growing environment to complete the full growth cycle.
This would ensure predictable growth of high-quality tomato plants with the greatest level of consistency and flavour, without using any pesticides. As the IGS system continually recycles water, it will also minimise water usage.
Installation of the systems took place earlier this year, and the growth towers are operational as of November 2021.
McCrae points out that ensuring the efficiency and performance of the farming facilities comes down to the concept design, selection of materials and MEP equipment, as well as the predictive maintenance and the monitoring of the facility’s systems through technology, so that the team knows what’s happening.
“The sensors, the IoT, and the feedback that we get from them to understand whether the lighting, motors and controls, the humidity and so on, are all being managed to their optimum, that’s where IREP as a company comes in, because that’s our bread and butter.
“We also have a number of projects in the pipeline and are quoting and putting together proposals to put into action by the end of the year. 2022 is going to be a busy year for IREPfarms,” adds McCrae.
“The biggest obstacle to starting a vertical farm is the high capital cost, mainly related to the technology. When people and companies do invest that capital, they often have to arrange debt funding from lenders as few have the resources to buy it up front. That means pressure to generate profit and cashflow, to repay that debt and/ or generate a return, which is why, at IREPfarm, we have come up with a lease model that removes some of this pressure from the client.
“We work with our finance partners to help offer this as a solution to our clients, and it is already showing to be very popular,” he says.
“Our approach is to provide complete transparency over the whole lifecycle of the farming facilities, with a very high degree of financial certainty. We have the systems and processes embedded into our DNA, to offer the solution from an asset management and energy management POV, including planned and predictive maintenance strategies to guarantee the reliability of the farms, resulting in the highest quality of food products, with absolute minimum of waste.
This is an extremely high-tech solution, with a proven track record of delivering on our promise to our entire customer base on a global scale. It’s a good marriage,” he asserts.
Given the amount of interest and focus on the vertical farming sector in the region, McCrae highlights the
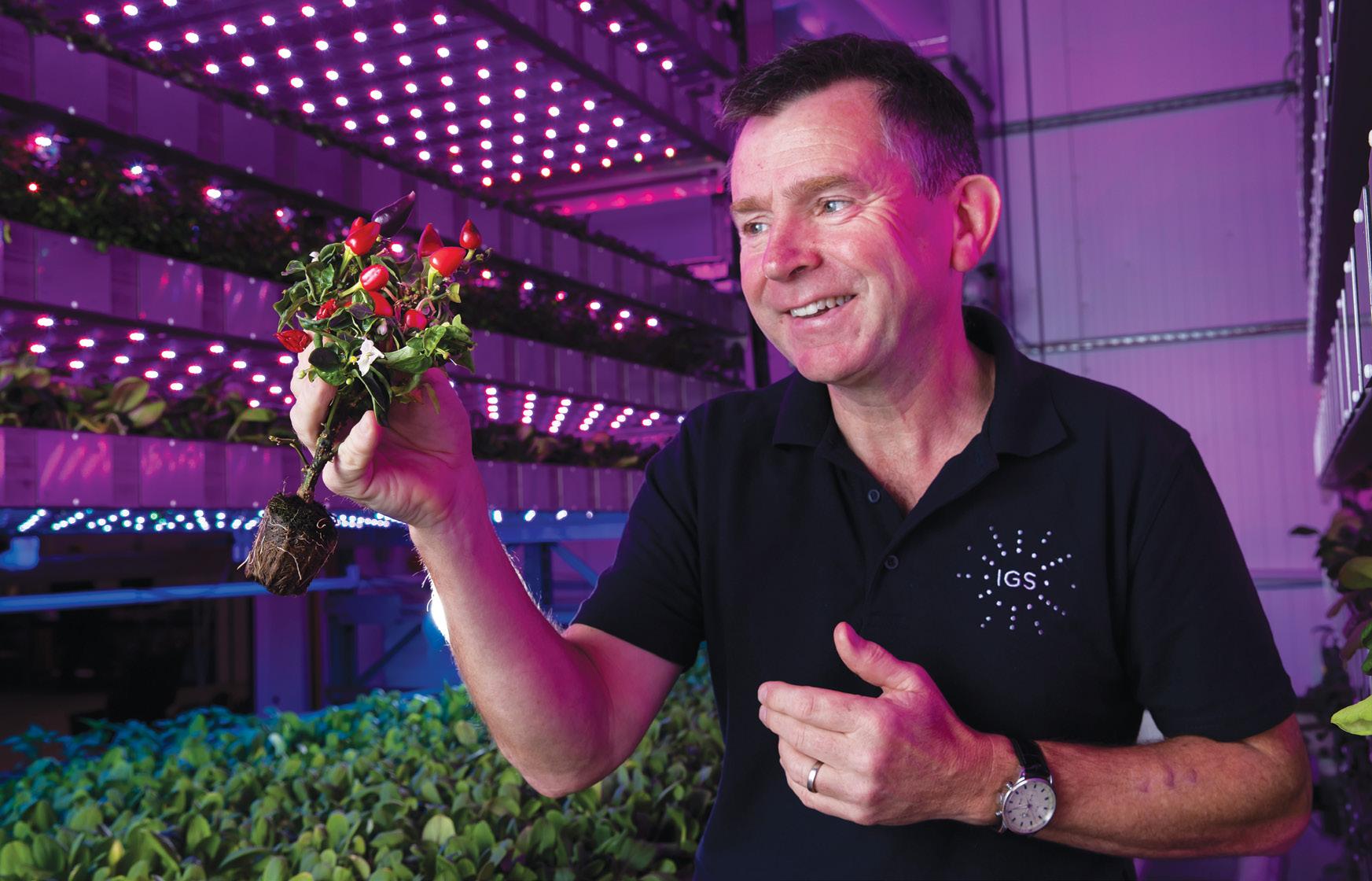
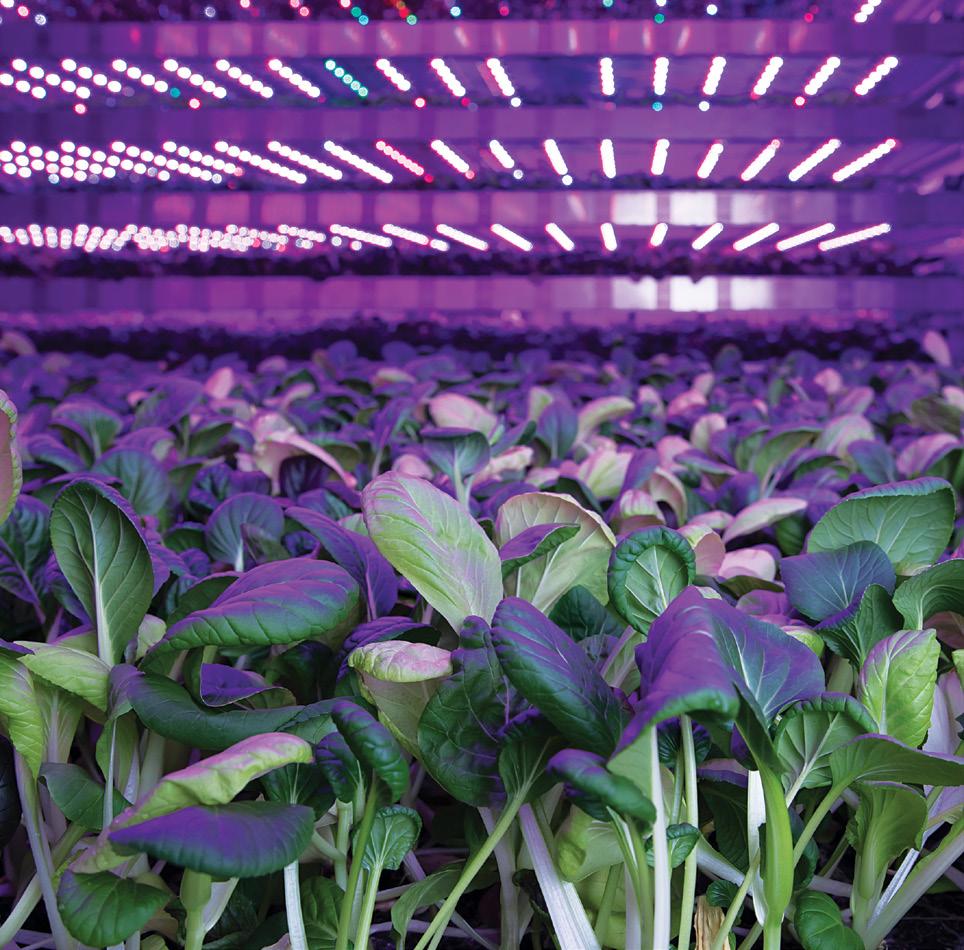
number of opportunities available to the construction sector. With Dubai aiming to become a hub for future clean tech-based food and agricultural products, there are already a number of new developments in the pipeline, such as the 1.67 million sqm Dubai FoodTech Valley, which is under construction in the Warsan area of Dubai.
“One of the construction companies we use is Al Tayer Stocks, who are currently involved in a number of agri-tech projects in the region. There are a lot of new technologies coming to the market, so there is learning to be done in how these facilities can be built and installed, and the construction improvements that can be made.
12m
Ideal height for a growth tower
Opportunities in the sector
There are a number of opportunities in the vertical farming sector, especially for MEP contractors and climate control specialists.
“I think that construction companies need to adopt and adapt. Data Centres are a big target (for construction companies), but so is Vertical Farming. To be part of it, you need to do some learning and understanding – what to specialise in, what’s different about it, and so on. You need to learn about things like airlocks, and the rationale behind the designs and all that.
“From an MEP point of view, there needs to be considerable amount of care and attention going into the projects, because of the commercial impact,” he adds.
“There is a downside in the agri-tech space – many people have come from outside the farming and technology industries and thrown money at the sector, but they don’t actually have a commercially viable technology solution. The frightening fact is that people are buying into this and are making very expensive mistakes.
“Like everything, this will take time to mature, and that’s what we’re seeing in the marketplace as well.
Construction is a part of it, and there will be specialists – the go-to guys who understand how to do things efficiently, have value engineered it, and understand the processes and supply chain, entrance, all the way through to the output side. They’ll know how the dynamics work, what materials to utilise, and what works in this region,” he predicts in conclusion.
Industry insight

DIDEM SEZGIN
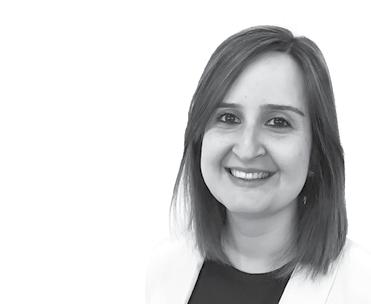
ROBERT BOSCH MIDDLE EAST
The evolution of Work 4.0
Did you know that the Work 4.0 concept was under formation before the pandemic? Very few companies had acknowledged Work 4.0, and some had only considered implementing it in the future once fully proofed. But no one knew it would move from its conceptualisation to the implementation phase overnight.
New Work or Work 4.0 is a philosophy that translates to office space design and transforming the way we work in a dynamic and adaptable way. It means adopting new and innovative ways to collaborate, more flexible approaches to performing and organising (office-type) work by simply putting people and their needs at centre stage.
While applying the philosophy of New Work to office space layouts and designs, architects play a significant role in it. According to the
Fellowes Workplace Wellness Trend Report, 87% of the respondents would like their current employer to offer healthier workspace benefits, with options ranging from wellness rooms, company fitness benefits, sit-stands, healthy lunch options, and ergonomic seating.
The mindset of architects in a postpandemic world has changed dramatically to adapt to today’s modern workspaces. With the introduction of new technologies and work ethics, employees’ well-being has become the main priority for employers. It has been proven time and time again that if employees are happy, healthy, and comfortable in their work environments, productivity soars.
Though working environments changed overnight due to the pandemic and employees were obligated to adopt new working styles to continue the smooth functioning of business, we have noticed that these new working styles have positively contributed to companies’ efficiency and business. The policies of return to work from office led to the creation of modern and quality workspaces and elimination of rigid structures enabling a more productive and less stressful atmosphere.
The option to work from home or even working remotely from outside the office has become a non-negotiable part of our modern working environment, especially due to the effects of the pandemic. As technology continues to evolve, access to several communication tools has enhanced the experience of connecting employees in the office with those working remotely.
We can also consider how working remotely can be of great benefit to employees who would normally have a tiring, lengthy commute to the office building. A decrease in commute would also be an advantage to the environment since light traffic equates to less pollution and as a result a positive contribution to reducing carbon footprint. We believe in designing models for the future. A combined potential of working onsite and offsite is a new hybrid model of the future work, which we call ‘Smart Work’.
With the acceleration of digitisation, we are not far from a future where smart office buildings could be connected to smart mobility solutions. For once imagine that your smart building carpark knows that you’re on your way in your electric car and automatically guides you to a space that is equipped with a charging station- unnecessary stress will be avoided from the start of your day to work.
Smart buildings could also be fed with the information about a person enabling the smart applications to learn who exactly has entered a building to assist in guiding a route towards the elevator to the floor of the employee’s office. This would mean that the employee would no longer need to use an access card at each entry point or even press a button on the elevator. The future is smart and connected if we all collaborate smartly in the present to build an automation that would help our generations to come.
CHRISTOPHER NICOLAS
TBH
Planning to deliver
When it comes to starting construction projects, any company of any size or value has reason to be wary of the potential for delays, overruns, conflicts, defects and failures. According to a McKinsey & Co. Inc. survey, large projects across asset classes typically take 20% longer to finish than scheduled and are up to 80% over budget.
Successful construction projects can be completed through a variety of techniques, but the overriding themes include effective preplanning, ongoing regular oversight, cooperation and anticipating problems before they arise. This means that issues can be addressed and managed before they impact the project
Whilst every project is different, the detail is always in the planning. Employing the following measures can help set your project up for critical success:
1. Setting a realistic project timeline
from the start: Starting a project under undue time pressure, will inevitably see the project suffer the long-term consequences as a result of poor planning.
A realistic timeline for a construction project should be driven by the scope and needs of the project.
This includes careful consideration of the scope, completeness of the design, overall project sequencing and achievable construction productivity. This also includes factoring in well thought out site logistics, and interfaces within and external to the project. Further, constructability must be considered in light of the project budget to ensure accurate timelines are established that consider integrated time and cost.
2. Regular monitoring and reviews:
Ensuring that a close eye is kept on the progress of the construction timeline is vital. From commencement, the project needs to be monitored through regular reporting of progress.
Planning, performing, measuring performance, evaluating measures, and acting upon variances helps in identifying risks early so that mitigation strategies can be considered and implemented in a timely manner. This promotes continuous improvement and provides effective communication of information in a way that can assist management in predicting and influencing outcomes and executing informed decision making.
3. Compliance of the parties’ contractual
obligations: It is of course important from the beginning to ensure that each party is committed to complying with its contractual obligations in a timely manner, as set out in the contract. The Client, Engineer, Contractor and other project stakeholders can unduly critically delay progress due to a number of factors including the late provision of information, delayed appointments, and prolonged review and approval periods.
The inclusion of key contractual obligations in the project timeline, and the ongoing monitoring of these obligations, is vital in ensuring that any deviations are addressed in a timely manner to avoid exacerbating project delays. 4. Timely resolution of disputes: Ultimately, this is about identifying the potential for delays so that remedial action can be initiated. Regular reporting will identify the critical work and identify those activities that are in need of attention in order to prevent them from becoming critical delays to the delivery timeline.
Invariably when delays, cost over-runs or scope changes occur, disputes, claims and counter claims can develop between parties involved. Left unchecked, a disagreement between two or more parties can escalate into lengthy legal cases that are both expensive and distracting.
The early adoption of a proactive approach to achieving commercial resolution to contractual matters eases the pressure of protracted disputes amongst the project participants. Instilling a culture of pre-emptive claims avoidance from the outset through contract drafting and the establishment of mechanisms in the Contract promotes the timely resolution of major disputes, easing the risk of protracted and costly litigation.

ALLISON WICKS
QUALITAZ
The meaning of quality
There are often misconceptions about quality and its definition that appear rife in our industry. With the constant narratives circulating that: “quality is ISO9001”; “a laborious exercise”; “it is final snagging and handover stage” and “if we have time we will do it”, it is not always understood and given the importance it deserves and brushed under the carpet.
In this short article we will examine the actual meaning of quality using practical examples, and will demonstrate how it applies to everyday life situations at work.
QUALITY OPERATES AS THE CENTRAL NERVOUS SYSTEM Everything we do is governed - to a certain degree - by a set of standards, that we set (subconsciously). From the way you communicate and treat others, to your attention to detail at work. Standards are based on our own beliefs, opinions, experience, culture and even from our frame of mind on the day. They affect everything we do, and everyone around us.
Our inefficiencies could cause delays in work processes, product and service delays, and of course defective work which may lead to non-conforming products or those which are not fit for purpose.
The consequences of our actions are in direct relation to our own belief system. We may feel our standards are high, after all what do we compare our own standards to. Other people? Worldwide etiquette? Best practice?
The standards we are referring to are quality standards. Everything is affected by quality because the result of our actions affects the final outcome. QUALITY IS IN EVERY SINGLE ACTION OR ACTIVITY How can we apply quality standards and regulate our work in construction to a unified standard? You may be familiar with the terms ‘quality assurance’ (QA) and ‘quality control’ (QA). Despite the name, QA doesn’t actually assure quality, it ensures the processes that assure quality are followed. Likewise, QC doesn’t control quality, it measures quality and accepts or rejects it based on a specified requirement.
It starts with your processes and standards. If these are not established, then consistent quality standards cannot be achieved. You will be unable to check the final product if all parties collectively are unclear of all the requirements. Your version of ‘acceptable’ may be different to your clients or your colleagues.
Smaller businesses may rely heavily on verbal procedures. This works for a small group of employees, however, the problems start when the organisation expands due onboarding of new employees. If the employer is unable to define the procedures and the roles, then how would you expect the employees to perform them?
HOW DO WE APPLY ‘QUALITY’ STANDARDS TO OUR PROJECTS AND ORGANISATIONS? Your quality system works like an instruction manual. You will take all of the information available and plan out the ways in which you will minimise errors and defects, in each part of the process during the project lifecycle, from initial planning, through to design, construction, DLP and maintenance period.
It is essential that businesses define and communicate their company standards, objectives and targets, and agree on how they will run their operations, to ensure they meet/exceed the requirements of all of their customers, both internal and external.
Once defined, this has to be embedded into the organisation, so that employees and new joiners understand their responsibilities and involvement in the overall delivery. Employees should be fully engaged and empowered to positively contribute.
It is usually those at grassroots level who hold the key to critical process details, as they have to overcome the day-to-day challenges, rather than those at senior management level.