
10 minute read
Key points to successful use of inkjet digital
As print providers and food manufacturers strive to ensure the safety of food labels and packaging, demand is growing for capabilities and compliance of inkjet solutions that won’t negatively impact food or human health.
Advertisement
Memjet’s water-based pigment inks offer high-quality output, durability on a wide range of substrates, and safer ingredients than alternative technologies and are making inroads into label printing, and are emerging in flexible packaging, folding cartons, and corrugated packaging as well.
Clean-up and maintenance with waterbased cleaning agents also reduces workplace hazards and air permitting costs.
New Revenue Streams:
Savvy printers are building new revenue models leveraging increased performance, reduced waste and regulatory costs, and the capability to create short run products to capture new customers and markets.
Flexibility:
Hybrid printing solutions give label printers much greater flexibility. They can still use their flexo presses to produce longer run jobs, while the hybrid option extends their capabilities to include customized labels and packaging, higher graphic content, smaller lot sizes, and the faster cycle times client’s demand. Hybrid printing has the added benefit of supporting a sustainable circular economy, by extending the life of existing equipment while ramping up the use of more environmentally friendly technology.
Print Quality:
Print quality can vary amongst inkjet print solutions. In general, a high resolution printhead with a small drop size will provide the best image quality (fine details and smooth transitions). Powered by Memjet print solutions with 2.1 pL drop size and true print resolution of 1600 dpi, provides unrivalled inkjet print quality along with the durability needed to satisfy the most demanding markets.
1. What are the pitfalls to watch out for?
Reliability is a key requirement for any print solution. Automated packaging and job processing systems that run at high-speed with high print quality specifications mean each print job element is critical.
You cannot afford to find out that your roll of printed media has job elements missing when you get to the next step. So, you either have expensive and complex integrated vision systems to “watch” the job run real time or put the requirement of reliability on the printhead technology.
Memjet’s DuraLink printhead design uniquely address this issue with builtin nozzle redundancy for each vertical line of print. What this means in terms of reliability is that we can have many nozzles contributing to each image line blocked with minimal change in print quality or optical density. This allows our customers to print every packaging job element with confidence until the next maintenance cycle is applied to the printhead returning it to 100% functionality for the next image line. The fact that our industry leading resolution is so fine means that single missing droplets have significantly less impact. Other systems with lower resolution and therefore large droplets will mean a large white space when the printhead nozzle does not fire, and as every print provider knows, there are always nozzle outs.
Watch out for claims about “low migration” inks. Food Contact Materials (FCM) compliance is a function of ink ingredient selection and
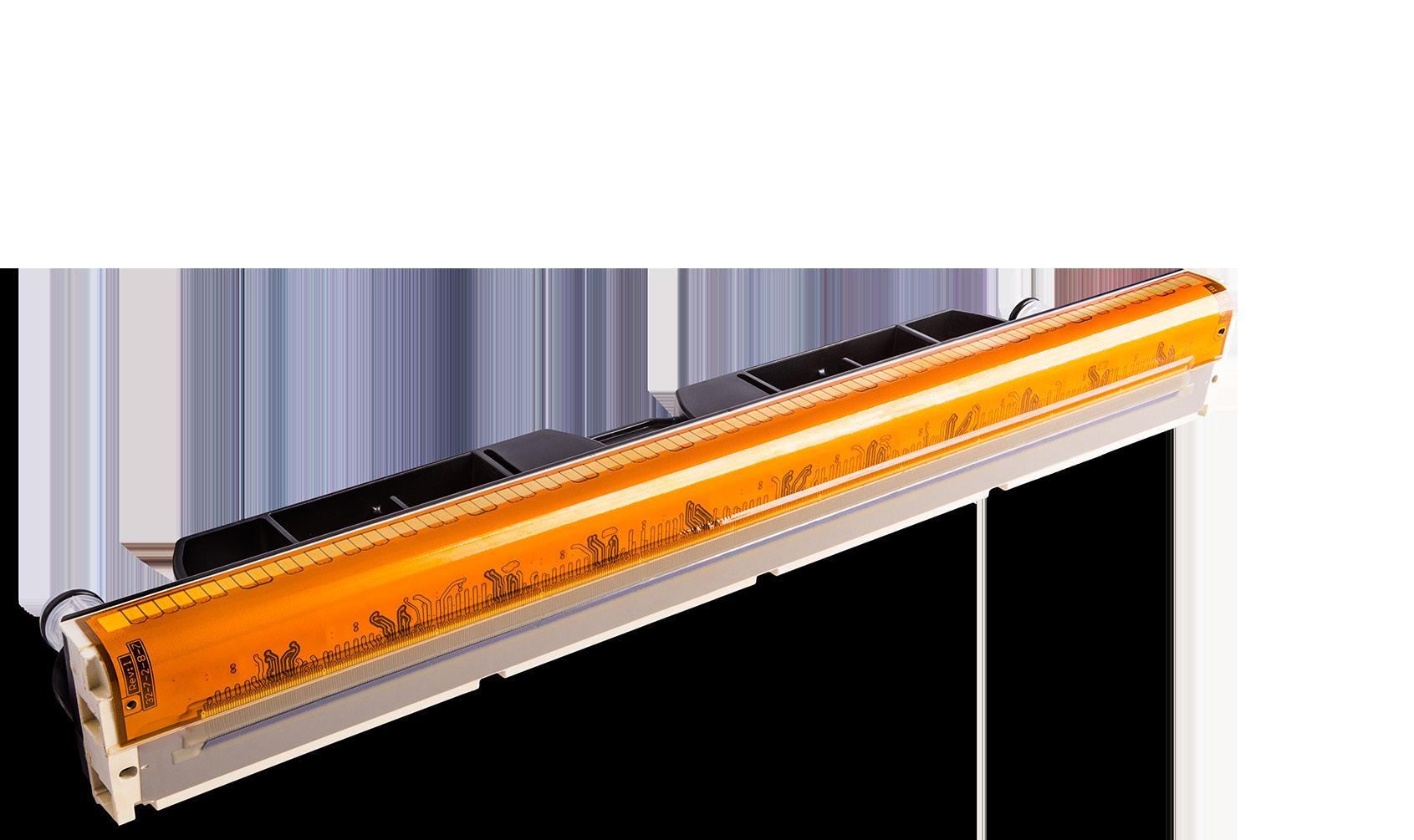
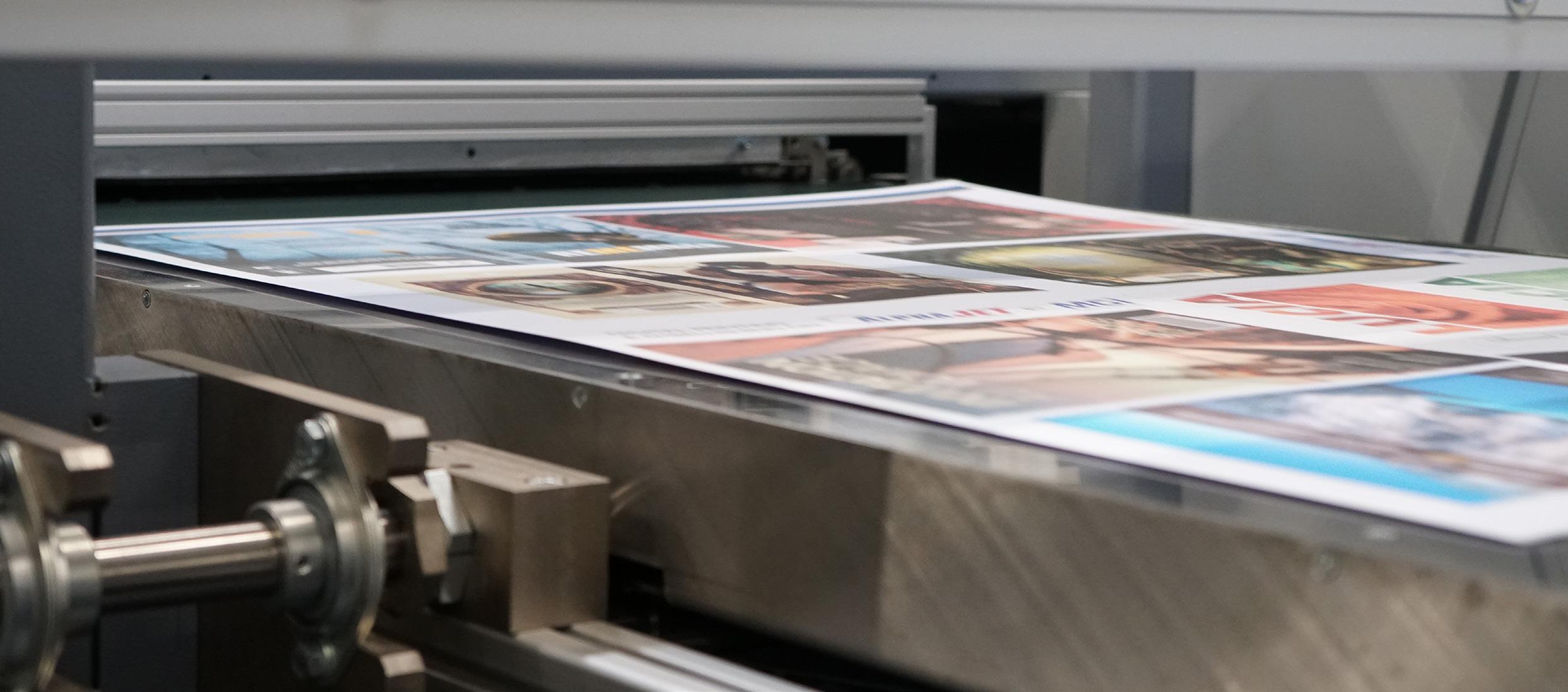
migration testing on specific substrates. Look for systems where providers have proven satisfactory migration results on specific use cases and media.
Adopting a stand-alone inkjet press in addition to existing analog printers, while providing value, can bring about too many other challenges for the business like having to retrain employees, developing new sales strategies and new digital workflows. A hybrid press can be the answer, and provide benefits of inkjet printing while reducing the risks and challenges that can come with adopting a standalone inkjet press. It also supports a sustainable circular economy. Some examples of solutions from our Powered by Memjet partners include Colordyne’s 3800 and PCMC’s ION retrofit.
Most of the substrates commonly used today are only optimized for analog print processes and inks, so they do not perform well with inkjet devices where the print processes and inks are fundamentally different. Memjet’s OEM partners are already benefiting from our investment in the research and development of coatings and primers and are investigating ways to integrate near-line and/or in-line treatment solutions to facilitate highquality printing for paper and filmbased applications for the growing packaging market.
Some OEMs are using this technology to develop solutions for totally new applications like direct-to-shape where the print surface is not flat.
With so many technologies now available, what criteria should a printer look at when considering an investment in inkjet?
When evaluating the printing costs of inkjet compared to conventional analog printing, many companies are surprised to find that inkjet is competitive beyond short-run or prototyping. In one recent TCO analysis, a corrugated box printer was able to show that inkjet was competitive at production-scale, in the tens of thousands of boxes
per month, by eliminating expensive platemaking, multiple steps of laborintensive prep, handoffs, inventory, and waste/spoilage
To capture the full impact of both the print and non-print costs, most printers will build a full ROI (returnon-investment) model to accurately capture both new and eliminated costs, from electricity to labor – as well as changes in ink costs and waste. Printers who switch to inkjet will also find their regulatory and environmental (e.g. emission permits, waste stream reporting) costs go down. In many cases, we’ve seen savvy printers also build new revenue models with capacity and opportunity factors to capture upside potential.
Inkjet printing technology meets the quality and production speed requirements for the entire box – not just marking and coding, and inkjet is competitive beyond short-run or prototyping
Just as consumers are paying attention to the impact their choices have on the environment, businesses and brands are putting much more emphasis on the environmental impact they have across their entire supply chain. Regulators are placing more emphasis on climate change, waste management and disposal, supply chain social responsibility and plastics consumption.
With digital inkjet printing, printers and converters eliminate waste in their processes by removing plate preparation, make ready processes, and produce shorter runs, that eliminate obsolescence waste from demand / alternative technologies and are making inroads into label printing, and are emerging in flexible packaging, folding cartons, and corrugated packaging as well.
Print quality can vary amongst inkjet print solutions. In general, a high resolution printhead with a small drop size will provide the best image quality (fine details and smooth transitions). Powered by Memjet print solutions with 2.1 pL drop size and true print resolution of 1600 dpi, provides unrivalled inkjet print quality along with the durability needed to satisfy the most demanding markets.
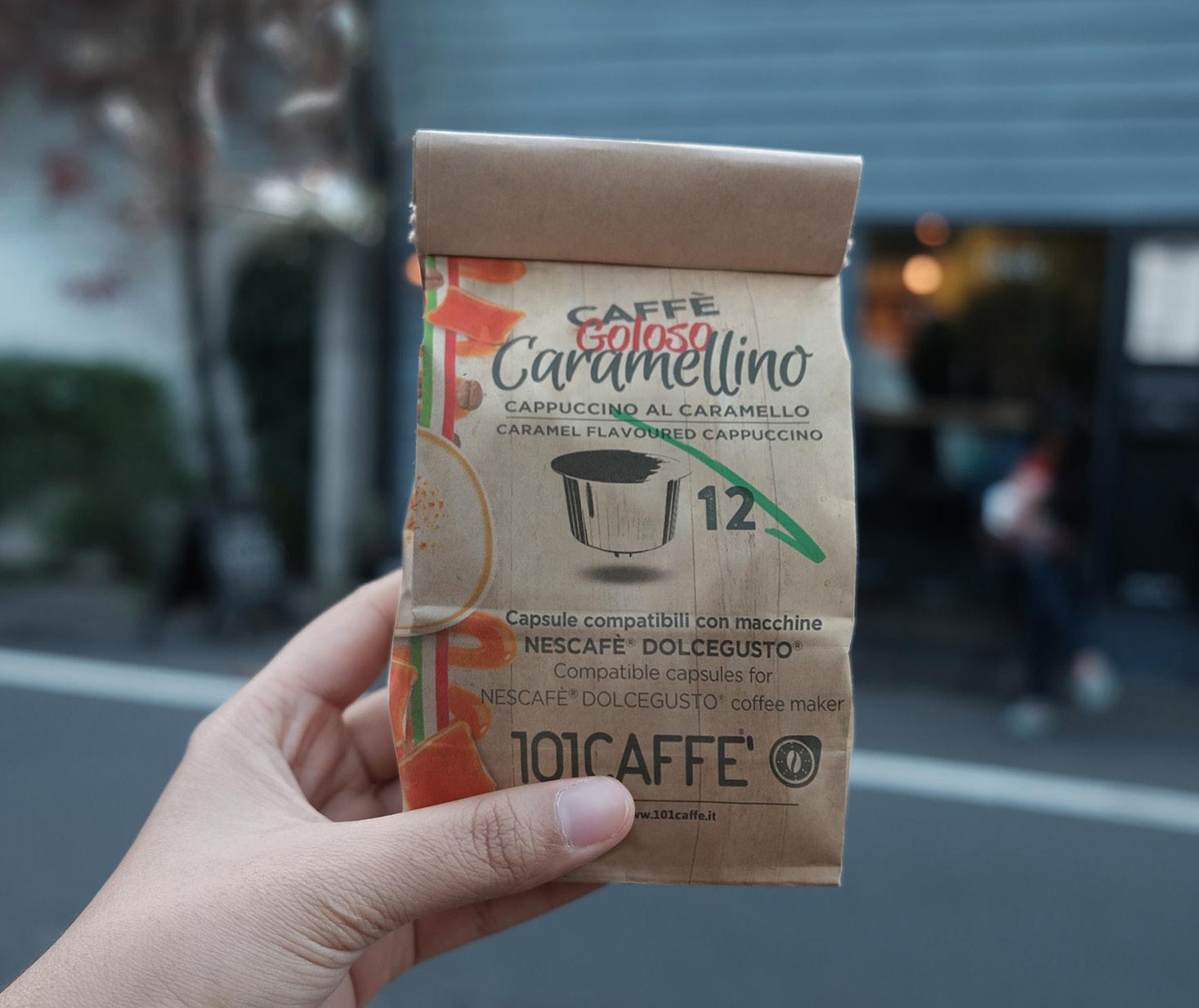
supply mis-match. Inks when created from components that aren’t on watch or restricted lists also play an important role in sustainability.
As print providers and food manufacturers strive to ensure the safety of food labels and packaging (40% of packaging is for food and beverages), demand is growing for capabilities and compliance of inkjet solutions that won’t have an impact on food or human health. Memjet’s waterbased pigment inks offer high-quality output, durability on a wide range of substrates, and safer ingredients than How will the technology and application scope for inkjet digital package printing develop over the next five years?
When digital printing technology first came to packaging, it was focused on prototypes, short runs, and personalization. With inkjet, those runs can be expanded and now the quantities aren’t hundreds, but thousands, and even tens of thousands. That allows digital to take on some of the work currently being done by conventional processes, and that helps compress timelines and increases inventory efficiencies. The compact nature of Memjet’s inkjet combined with the low cost and high performance capabilities enables customers to streamline processes to reduce cost. By combining or eliminating process steps to effectively print just what you want, when you need to, you eliminate a lot of substrate movement, work in progress, and ultimately inventory.
On-Demand -- Companies are revolutionizing box-making with “on-demand” right-sizing solutions that create custom-size boxes to eliminate inventorying multiple sizes, reduce voids/wasted space inside the box, better protect contents from contamination, improve sustainability, and reduce shipping costs.
We will see printing being done during the creation of the package instead of printing with analog technology, shipping the printed media to a filler and then they make the final product with the pre-printed media. For example, Powered by Memjet partners Rigoli and V-Shapes are doing this.
Successful brands will keep pace with trends and market drivers to consume less, create less waste, and provide a healthier work environment for employees in their supply chains. With digital inkjet printing, printers and converters eliminate waste in their processes by removing plate preparation, make ready processes, and produce shorter runs, that eliminate obsolescence waste from demand / supply mis-match.
The challenge is to design printheads that are simple enough for nonprinter designers to use, like packaging machinery companies, while also being flexible enough to allow design differentiation for the big printer brands.
Allowing our customers access to print engines that can do all of their printing on demand or as late as possible in their manufacturing is key to enabling the personalisation to which everyone is becoming accustomed to and now expecting.
Taking a technology that can produce photo-quality images at an industry
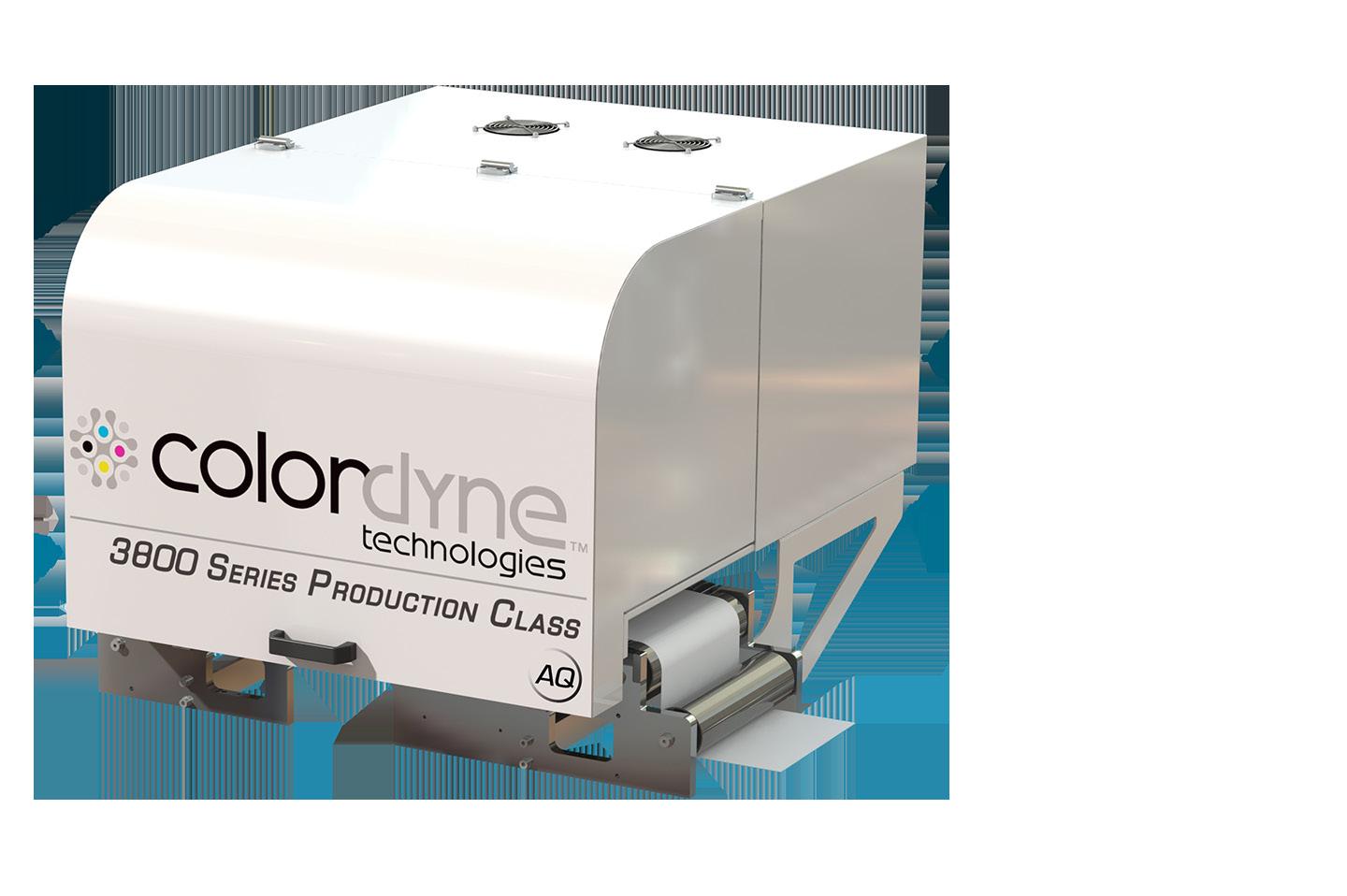
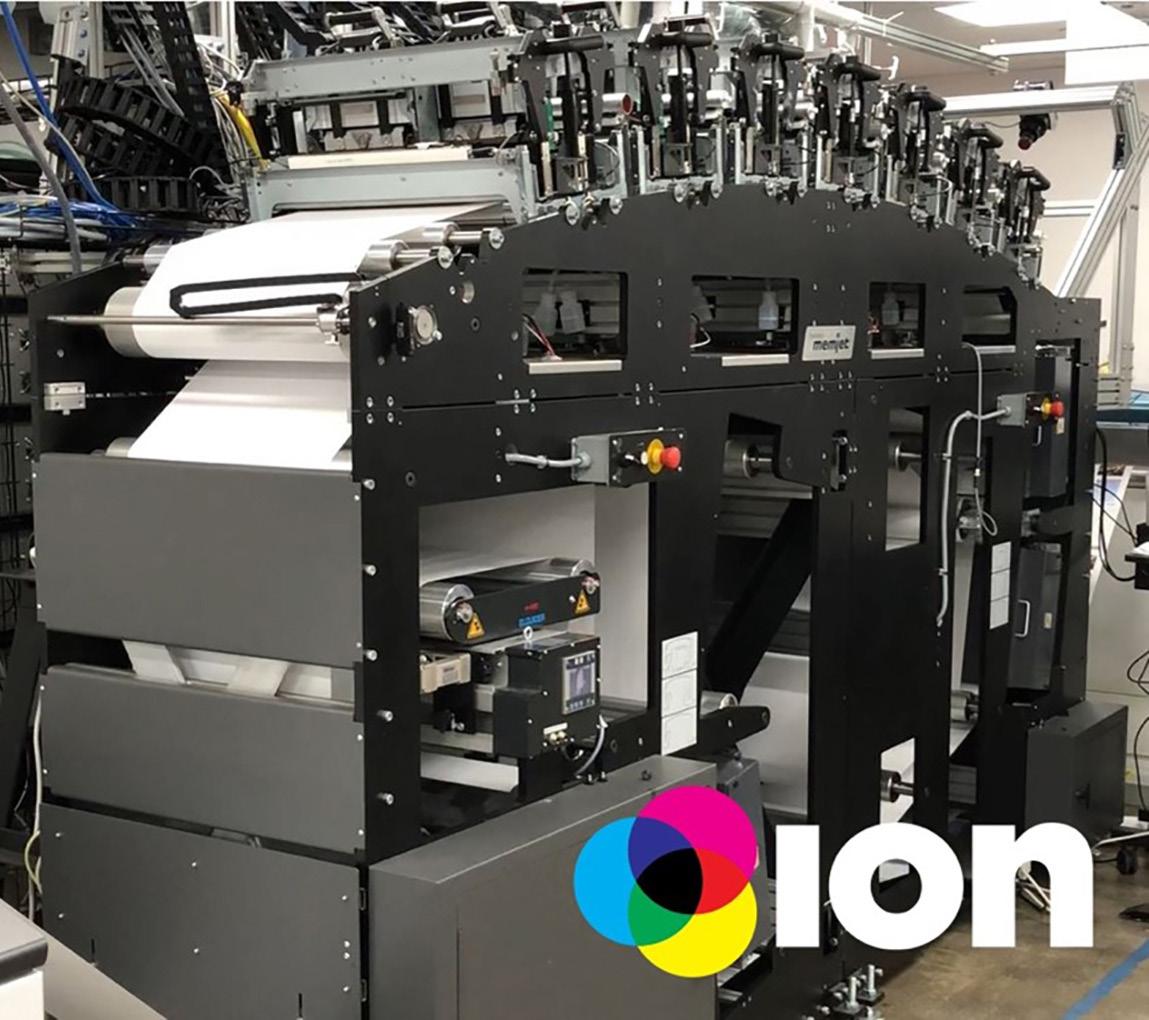
leading resolution and scale it to provide industrial applications at more than 200 m/min is non-trivial, but this is a challenge that Memjet is taking head on and succeeding.
How will UV and water-based inkjet
evolve over this time? Prompted by increased data, NGOs, and customer demands, regulators around the world are tightening rules regarding the use of hazardous chemicals often found in UV inks and associated cleaning solutions. This restriction will make innovation increasingly difficult for UV printing technologies.
UV inks will become obsolete for packaging in the coming years based on several driving forces and restriction. UV photo-initiators are inherently toxic and carry significant long term exposure health risks to employees and operators. Because of the hazards associated with their production, there also have been several disruptions in supply in the last few years.
- Supply chain social responsibility requirements will continue to highlight the risks of “process chemicals” in large brands’ and print will begin to gain more visibility.
- Even where photoinitiators are not required, hazards with UV ink monomers exist including sensitization. UV inks claim low VOC’s, however, cleaning fluids for wash up and maintenance are typically solvent based and hazardous.
- Memjet’s ink technology is solely water-based, and we intend to remain so in the future as an important driver for human health and safety as well as sustainability efforts.
2. What are Memjet’s latest and greatest developments in inkjet digital printing? What are the USPs of this technology and how will this shape the future for inkjet digital package printing?
Over the past couple of years, Memjet has launched two new modular inkjet technology platforms. DuraFlex enables delivery of light production units, while DuraLink is a good fit in high volume production needs. Memjet's inkjet technologies provide a solid foundation for OEM partners to meet the needs of a variety of print applications and media types especially in regards to packaging. As a result, more package printers/converters can leverage the value of inkjet for labeling and packaging applications – from industrial high-volume to benchtop applications yielding higher resolutions, faster speeds, and profitable print devices.
These solutions have the speed and affordability that print providers need right now. They have raised the bar for beautiful, high-quality output that packaging providers demand, producing sharp images, smooth gradations, and an expanded color gamut with resolutions up 1600 x 1600 dpi.
Memjet's newest technologies use water-based pigment inks which are safer for the earth and the people handling them. These inks are ideal for packaging applications because they can achieve offset-quality output on a wide range of coated and uncoated substrates while being resistant to light and moisture.
They contain no toxic or reactive chemistries, are formulated using components listed on the Swiss Ordinance and are in alignment with the Nestlé Guidance Note on Packaging Inks, Additionally, for those concerned about sustainability, Memjet’s inks are unlikely to impact recycling.

By: Gianluigi Rankin, Director Product Management at Memjet