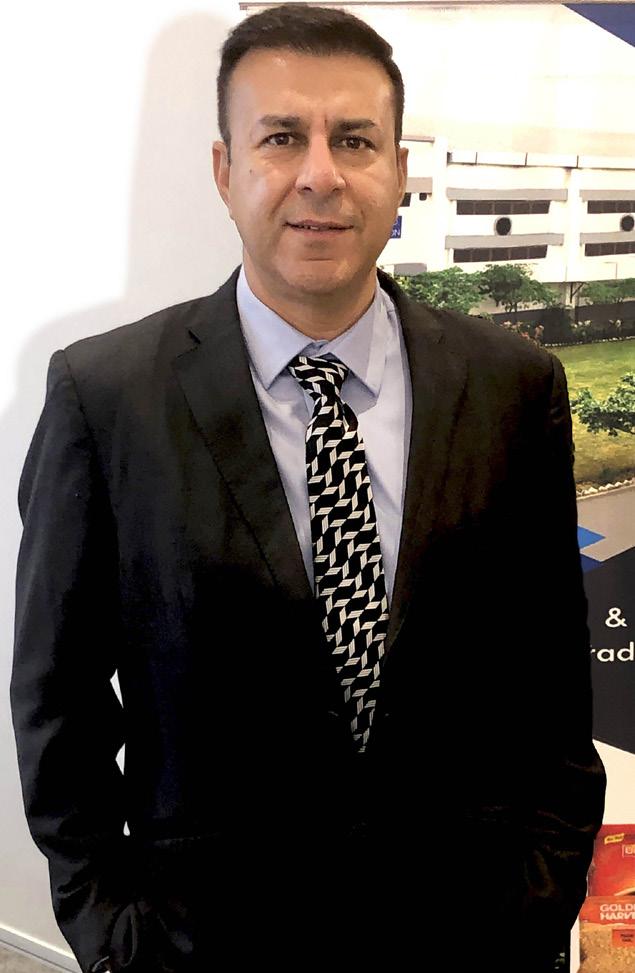
16 minute read
News from around the world
Premji Invest acquires a significant stake in SB Packagings, a leader in flexible packaging for Hygiene Segment
Delhi-based SB Packagings (SBP) has said Premji Invest has invested for a significant stake in the Company. The transaction primarily involves partial stake sale held by the existing shareholders in SBP and infusion of primary capital for capacity expansion and for inorganic acquisitions to enable faster scaleup of its product portfolio for both domestic and International markets.
Advertisement
Founded in 1989, SBP is a leading manufacturer of flexible packaging materials in India, supplying to major players in the Hygiene and Food industry including P&G, J&J, Unicharm, Kimberly Clark, Nobel Hygiene, Walmart, Future Group, PepsiCo, Dabur, and Tata among other leading brands. SBP has won various awards and global accolades for its innovation & printing excellence and is at the forefront in providing sustainable packaging solutions. SBP was founded by Mr. O.P. Banga and is currently managed by his son Mr. Amit Banga, who has been in the business for the past 30 years.
Post transaction, Amit will continue to remain a significant shareholder in the company and would continue to drive the business, supported by a professional management team further bolstered by the financial and strategic support from Premji Invest. Commenting on the deal, Mr Amit Banga, MD of SBP said, “We have grown steadily over the last decade, winning the trust and market share with our marquee global customers who have a very high threshold for quality and consistency. Innovation and Sustainability have been the core pillars of SBP’s business model. With the backing from Premji Invest, one of India’s leading PE investors, we look forward to further expanding our capabilities through organic and inorganic routes thereby strengthening our position in the Indian flexible packaging Industry."
Mr O. P. Banga, Chairman Emeritus stated that the seeds sown four decades back have become a big tree now and this partnership with Premji Invest has my best wishes and blessings towards our vision of building a business around the needs of the society.
Premji Invest is the investment arm of Azim Premji's endowment and philanthropic initiatives. It has been active in investing in the Indian markets for over ten years with large investment corpus.
The focus of investments has been to grow medium-sized Indian companies into large companies that can compete globally. Investments of Premji Invest is across sectors like consumer, financials, technology, and manufacturing and to name a few include, Fab India, Hygienic Research, ID foods, Lenskart, Policy Bazaar, Flipkart, Gold Plus Glass and Shubham Housing. Premji Invest is excited to partner with SB Packagings to help them scale to the next level of growth.
EY and Khaitan & Co. acted as advisors to SB Packagings on this transaction. Media Contact:
Kornit Digital Acquires Voxel8, Expanding Additive Manufacturing Technology Portfolio for Next Generation of Sustainable OnDemand Textile Production
Kornit Digital Ltd, a worldwide market leader in digital textile production technologies, announced today the acquisition of all associated assets of Somerville, Massachusettsbased Voxel8.
Voxel8’s advanced additive manufacturing technology for textiles allows for digital fabrication of functional features with zonal control of material properties, in addition to utilizing high-performance elastomers adhering to inkjet technology. “Voxel8’s innovative technologies and talent will help us accelerate the execution of our 4.0 strategy to digitize sustainable, on-demand textile production,” said Ronen Samuel, Kornit Digital Chief Executive Officer. “With this advanced and proven 3D technology, we will disrupt the business of fashion, empowering completely new creative decorative concepts and never-before-seen functional textile applications, while exploring new lucrative opportunities in the functional apparel and footwear markets.”
"By integrating Voxel8’s technology into Kornit’s product roadmap, we will be able to transform numerous market segments and verticals, accelerating our collective visions and technology advancements," said Kobi Mann, Kornit Digital Chief Technology Officer. “Voxel8 offers
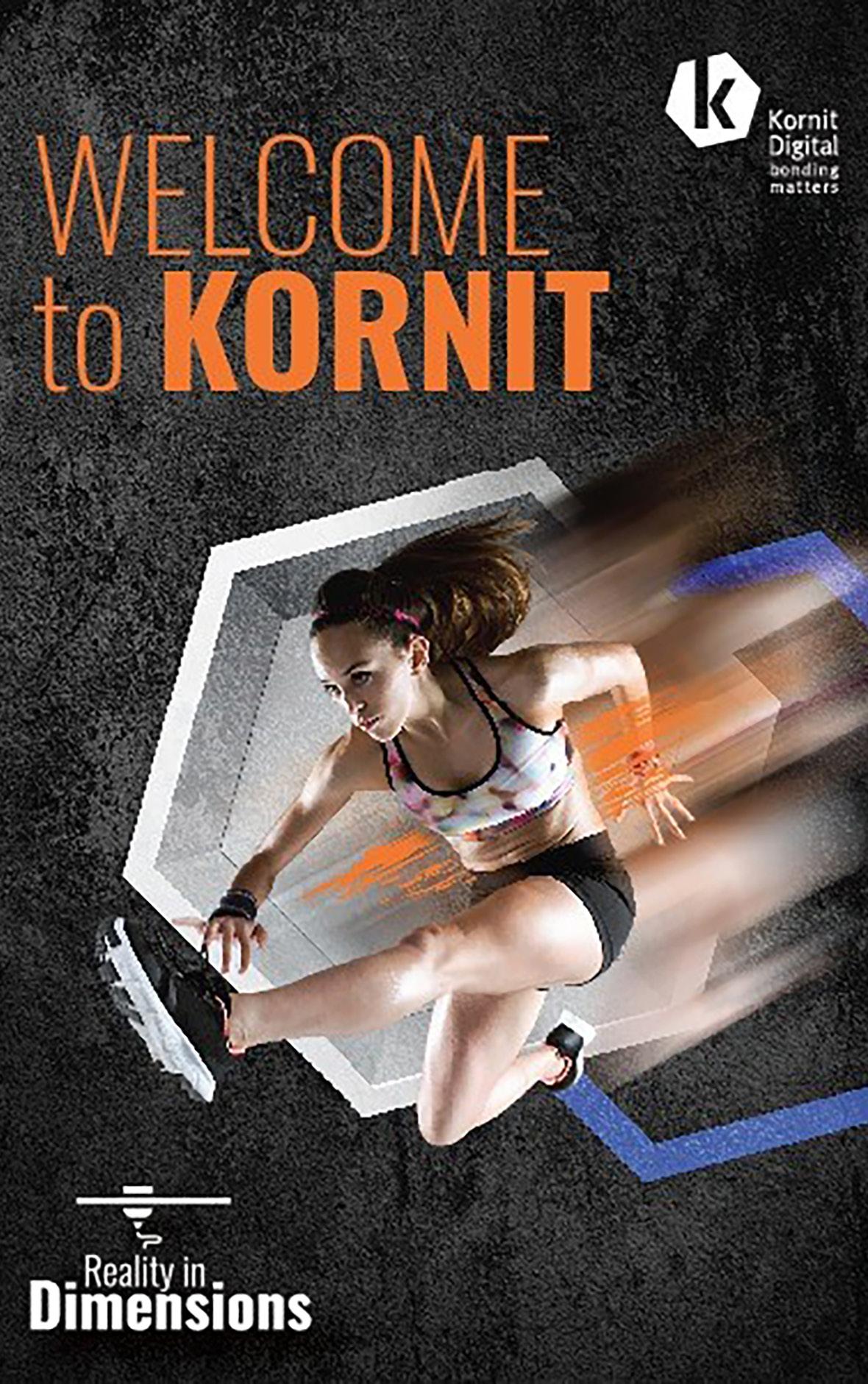
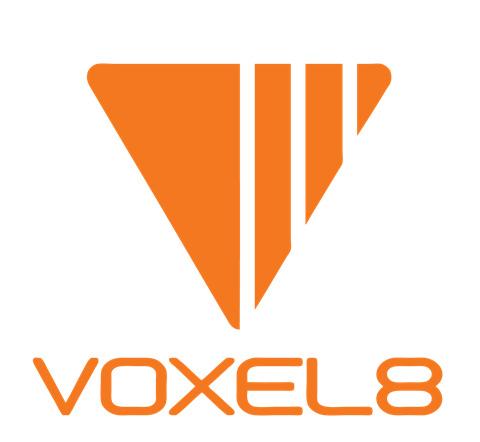
direct 3D print-on-part capabilities, advanced design software that can be easily integrated with any production floor software workflow, and versatile chemistry enabling on-the-fly formulation of high-performance elastomers to change the material properties of the resulting printed structures by multiple orders of magnitude.
This means reflective, high-density, silicone and metallics, as well as compression elements for sports and therapeutics, protection elements like cushioning and impact resistance, and functionality applications like anti-slip, waterproofing, and other qualities combining form and function that are key to Kornit’s vision of digitizing production in every conceivable manner.”
“Voxel8’s innovative and sustainable technology—tested by some of the world’s leading global fashion and footwear brands, such as Hush Puppies, which is part of Wolverine Worldwide, enables the digital creation of unique decorative and functional applications, while eliminating time and waste from the manufacturing process,” said Fred von Gottberg, Voxel8’s President and Chief Executive Officer. “Voxel8 shares Kornit’s vision of transforming the textile industry and couldn’t be more excited to be part of the journey to build the operating system of sustainable fashion on demand. We look forward to working together to embed Voxel8’s technology into Kornit’s customer offerings, which will collectively provide endless possibilities of enhanced applications and solutions.”
TriState Container Corporation steps into digital production with Xeikon IDERA
Xeikon and TriState Container Corporation today announced that TriState has become the first print provider to acquire IDERA, a brandnew digital printing solution for corrugated packaging converters.
TriState Container Corporation is an independently owned third generation manufacturer located in Bensalem Pennsylvania. TriState provides a wide variety of corrugated solutions from shipping containers to custom high graphic corrugated requirements through two divisions, TriState Container, and ProCorr Display and Packaging.
IDERA was created to bring easy, flexible, and sustainable packaging to the corrugated packaging industry. The IDERA architecture and specifications provide speed, flexibility, and agility to corrugated converters, delivering new opportunities with customers, and internal productivity gains to the converter.
To make this happen, IDERA prints on coated and uncoated corrugated sheets up to 63 inches wide x 110 inches long, enables variable printing speeds between 196ft/min and 393ft/ min flexibility in terms of in-line priming, varnishing and drying, and peripherals such as automatic prefeeding and stacking.
Allen Friedman, President, TriState Container Corporation commented, “I saw my first single pass digital press in a corrugated converting operation about five years ago. What struck me was the potential impact this technology could have on addressing limitations of current analog technologies, and the requirements converters place on packaging buyers to maintain internal efficiency and cost. As an independent, we are always looking for how we can create greater value for our customer, while building competitive advantage for ourselves. We believe the IDERA digital press positions TriState to achieve both. We envision internal and external benefits for TriState. Internally, we can move jobs to the digital press that are better suited to digital technology. Externally, we see this as a perfect fit for customers with emerging or proliferating brands. These types of jobs may be too small for flexo runs and too large for multi-pass. In the past, these brands were afraid of the associated time and costs when they wanted to improve print quality or make a design step change. Many have indicated a desire to change their order behaviour. We also see an opportunity to develop design capabilities for our customers.”
Friedman concludes, “We’re looking forward to promoting IDERA’s high print quality to our customers and being able to print short and long runs with all the benefits of a digital


CANON SINGAPORE PTE. LTD.
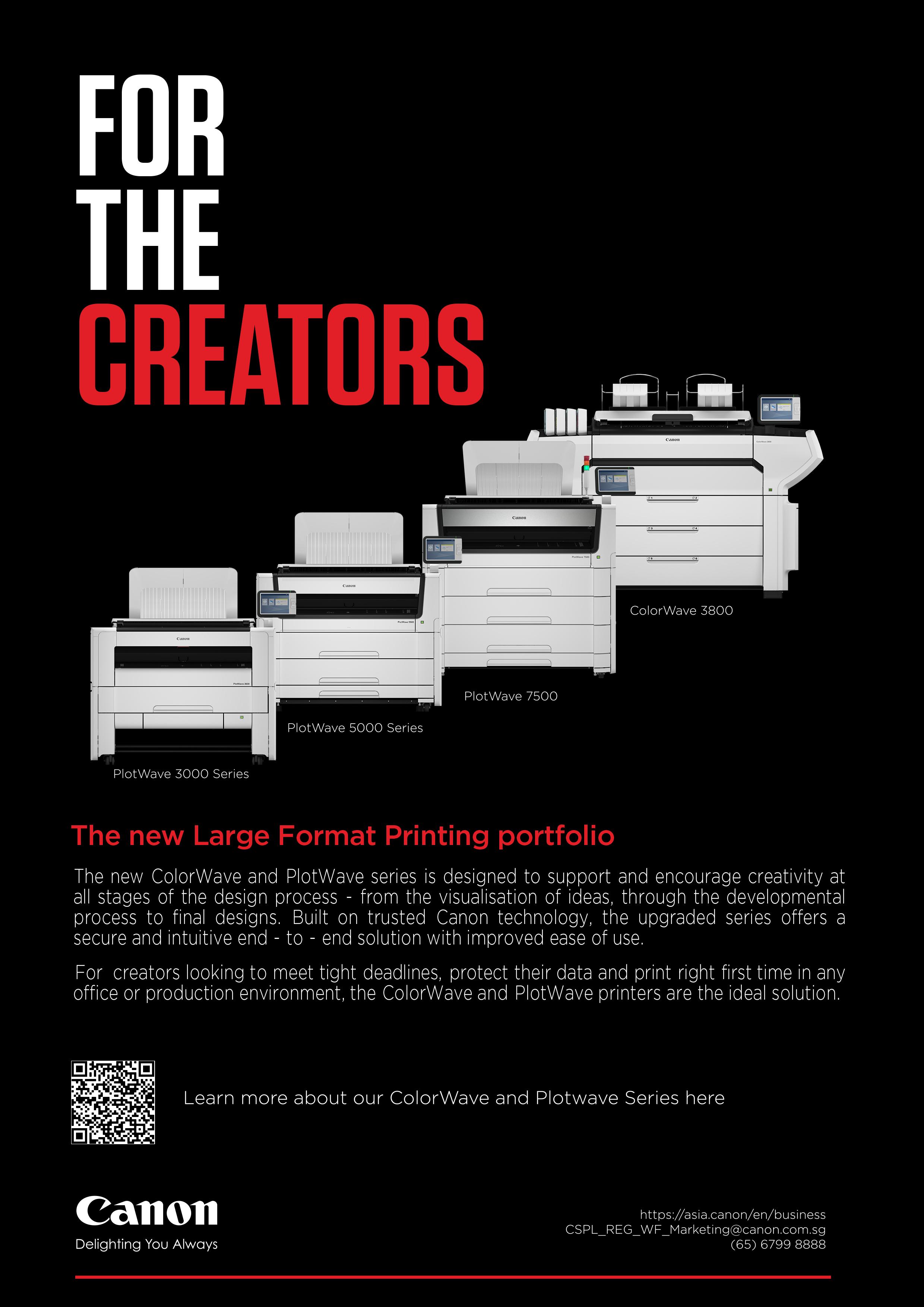
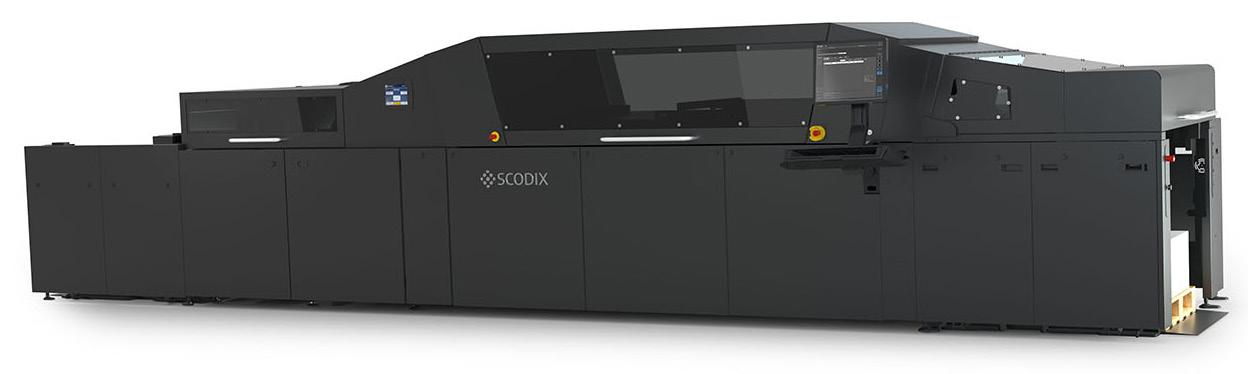
print-on-demand solution, including reduced waste. Even more importantly, we have kicked off a long-term partnership with Xeikon as I believe they are one of the few providers with the competences, resources and approach to succeed in the digital corrugated box market.”
To develop IDERA, Xeikon combined its long established in-house digital expertise with the experience and manufacturing footprint of its parent company, Flint Group. As the number one supplier of inks for corrugated packaging, Flint has a deep understanding of the corrugated market.
Sebastien Stabel, Market Segment Manager, Carton Packaging for Xeikon notes that “Xeikon is, of course, excited about digital potential in the corrugated market, but it’s critical to successfully implement this reference installation. Together with TriState we have developed a business model as well as a technical solution to kick-off digital production.”
Stabel concludes, “IDERA is backed up by Xeikon’s own food-compliant IDERA AT inks, industrial inkjet and workflow know-how. We have worked closely with Flint Group, our partners, and most importantly our customers, to customize hardware and ink sets to address the changing needs of the corrugated market.”
Large format digital enhancement press brings new market growth opportunities
Carlson Print Group is well-known for its eye-popping customized print pieces, produced for many of the most recognizable brands in the world. With the Scodix Ultra 6000 press addition, CPG broadens its offering of high-end, tailored enhancement for new and existing clients in this market. The new 41” large-format digital enhancement press will also see the company actively promoting the growth of its market share in the packaging sector.
Darren Carlson, Carlson Print Group President and CEO, says, “We’ve developed a well-earned reputation in the industry for designing and producing some of the coolest and most inventive work for our nationwide clientele, many of whom appear in the Fortune 100 to 500 lists. They represent a variety of businesses, who want to stand out and are willing to invest in award-winning attentiongrabbing projects. The new Scodix Ultra 6000 press with its 41” sheet size and diverse enhancement capabilities provides our clients with bold, unique products as we continue to expand our specialty print and packaging business. In addition, this press provides us the ability to transition to a complete Scodix finishing workflow solution immediately impacting our business productivity.”
Carlson Print Group has partnered with Scodix on the purchase of the Scodix Ultra 6000 Digital Enhancement Press, which is set to be installed at CPG’s Eden Prairie, Minnesota location immediately. The capability of the new press allows for more highly-detailed, shortrun and data-variable personalized projects with tactile applications such as embossing, foil, metallic effects, glitter, and specialty finishes. A clear advantage with the Scodix Ultra 6000 is the size of the press which accommodates 29 x 41 inch sheets. Earl Guinter, Carlson Print Group Sales Manager, comments, “Having the Scodix Ultra 6000 press is revolutionary because it allows us to use a common, large-format sheet size across all our presses. This saves our customers time and money, while increasing the enhancement design possibilities dramatically.”
Jason Rollo, Scodix President of North America, continues, “We are delighted that CPG has joined Scodix and will lead the adoption of digital print enhancement in the specialty and packaging markets. Carlson Print Group’s leadership in trading cards is a perfect product for digital enhancement application just as a starting point. We’ve seen so many innovative projects come from this company, we can’t wait to see how they will put digital enhancement into effect – especially in large format. Their vision to increase brand awareness capabilities sets the bar at a new height and pushes creativity even further. Together, we are excited to be at the forefront of the large format digital enhancement movement.”
10-15 production orders produced daily within weeks of installation
Boxes Inc was the first company in the USA to install the flagship Highcon® Beam 2C digital finishing system for corrugated earlier this year.

The company added the Beam 2C to their digital workflow primarily to support their online, customized packaging web-to-pack site, Xceed but is now also expanding usage to support other more traditional parts of their organization. Describing the install as its easiest ramp-up ever, Boxes Inc. benefitted most from the increased speed-to-market afforded by Highcon’s digital finishing technology.
With a clear commitment to excellence, this industry leader, together with subsidiary Mid America Display, has been producing industrial shipping and packaging products, POP displays and signage for over 40 years.
According to Jason Mueller, Sr. Vice President, General Manager, “We have installed a number of new machines over the last few years, and this was by far the easiest ramp-up I have had the privilege of being part of. … within weeks we were routing and running 10 to 15 production orders a day on the Highcon.”
Boxes Inc. is currently running 2 shifts, substantially improving their overall efficiency, Jason Mueller adds: “If I had to pick one benefit as the “key benefit” I would have to say that we have benefited most from the speed to market improvements the Highcon system has provided. We no longer have the delay from ordering tooling. We have reduced our delivery time by more than 40%”
The Highcon Beam 2C digital finishing system is available in 2 configurations: pallet-based and a nonstop version with nonstop feeder, nonstop stacker and waste removal. It has been engineered to meet the stringent market requirements for corrugated packaging; non-crush process, customizable to enable rightsizing and light-weighting of packaging; strong enough to allow product to be shipped in its own box; and at the same time providing a positive unboxing experience that supports brand owners. For more details: https://www.highcon.net/ product/highcon-beam-2c/
UV silver coatings offer a range of sustainability and premium quality benefits
ACTEGA, manufacturer of specialty coatings, inks, adhesives and sealing compounds for the print and packaging industry, today reveals the latest coatings to be incorporated into the extensive ACTEGA portfolio. Five WESSCO® POLAR UV silver coatings, comprising four WESSCO® POLAR UV flexo silver coatings and one UV offset silver coating for use from the ink duct, deliver, in combination with highly transparent overprint varnishes, highly reflective properties and brilliantly glossy effects. Additional benefits include outstanding flexibility, efficiency, overprint ability with UV offset inks, and a strong sustainability offering.
Addressing the growing importance of sustainable printing, the solventfree WESSCO® POLAR coatings provide businesses with a highquality alternative to traditional hot or cold foil stamping and metallized board. In addition, the use of these new coatings eliminates plastic waste and streamlines the recycling process, providing a performance and efficiency boost to users as they remove the additional foil application step from the printing process.
Andreas Käfferlein, Product Manager Metallics, comments, “With demand for premium, high-value print products still on the rise, our UV silver coatings capture the attention of the consumer due to their luxurious quality. This makes them highly attractive to our customers in paper-based packaging, commercial applications, and book and magazine printing. Add to this the incredible environmental advantages of the WESSCO® POLAR range and the economical savings to be made, and the appeal of these UV coatings speaks for itself.”
The WESSCO® POLAR UV Silver coatings are well-suited to a range of paper-based print and packaging applications including food and other sensitive packaging types, thanks to properties such as low migration and compliance with Swiss Ordinance and Nestlé requirements. Customers also benefit from reduced lead times and improved cost efficiency due to the avoidance of time-consuming material ordering and extended delivery periods. The high costs associated with metallized or TransMet boards are also eliminated.
Andreas Käfferlein concludes, “The efficiencies and environmental benefits of the WESSCO® POLAR range strongly support ACTEGA’s companywide goal to support advances towards more sustainable print production. With this new range, we can offer yet more coatings that will support our customers’, and their customers’, sustainability objectives, while det

to get the optimal ink transfer – ink starvation to the anilox can occur. This will be evident once the doctor blade is applied. If this was not noticed when the anilox was applied to the plate and impression set, you will see the starvation results.
Swiss direct mail and brochure printer installed Contiweb equipment to achieve maximum productivity and minimize production costss
Contiweb, a specialist in state-of-theart technologies for advanced drying, web-handling and web-processing, announces today that Swiss print service provider, Druckerei Kyburz AG, has invested in a Contiweb Digital Fluid Applicator (DFA) and CDN non-stop unwinder for its Dielsdorf facility. The company had previously invested in 5 other splicers from Contiweb.
A family-run business, Druckerei Kyburz AG has been operating for 49 years to provide Switzerland and its neighbouring countries high-quality print products including self-mailers and brochures. Druckerei Kyburz AG started as a sheet fed and web offset printer and added later multiple web-finishing lines and digital print technologies. As part of the company’s ongoing aim to expand and stay ahead of the competition, the team is now installing a digital print production line in conjunction with Contiweb and Canon, including inline i-Web US finishing equipment.
This line is created with a length of 2 x 40 meters over 2 floors, setting new standards in digital printing. The new production line enables Druckerei Kyburz AG to start with a blank roll of paper and finish with a ready product, without having to stop, with the aim of meeting the growing demand for heavily personalized, low to mid volume, high quality mailings.
Patrick Kyburz, CEO, Druckerei Kyburz AG states, “Our long-standing partnership with Contiweb, as we own five splicers, and our positive previous experience with Contiweb splicers that we use in our web offset printing lines and with the CDN, meant we were sure the machines would be a worthwhile investment. So much so that we didn’t even look at other options! We like how it has been built, and it looked sturdier to have the DFA and non-stop unwinder from Contiweb alongside our Canon ProStream 1800. As we started to prepare our unique line, the aim was to develop a tailor-made system to be able to efficiently implement our customers’ extraordinary ideas.”
Mr. Kyburz continues, “The looming pandemic last year accelerated our designs on improving the business in any way we could. We essentially wanted to stay in front of the competition by making bold decisions, early. From the beginning of this process, we believed that we were not going to have a manual unwinder, we knew we needed a non-stop splicer. It is very common for digital printers to perform manual reel changing. For us – being a web offset printer – this looked very traditional.
“If you finish online, it is very important that the line doesn’t stop. At every stop you have the risk of a web break. Many printers coming from sheet fed are anxious and ask us if we are not afraid for web breaks using automatic splicers, but the risk of them occurring is much higher if you do this manually. Contiweb systems are extremely modern and reliable.”
Druckerei Kyburz AG uses Contiweb winding solutions in combination with the Contiweb Digital Fluid Applicator with the silicone application option included, to prevent the printed matter from damages in their own finishing line as well as in the sorting centres of postal providers. The DFA is a Plug’N’Play standalone remoistening applicator for digital web presses that works with a sleeve system, applying a very precise amount of water and (optionally) silicone to the web. The system has been developed to significantly improve and repair basic paper properties, and to increase the smoothness of the run through the press and finishing equipment.
Mr. Kyburz continues, “If you finish inline, the paper gets stressed. We believe remoistening will help especially with the Canon ProStream 1800 press. It has a huge dryer (up to 180 degrees) so there is a lot of heating energy. The paper becomes wet one side due to the ink, then it is dried, following that the process continues on the other side of the paper. Remoistening will help us to apply more folds and prevent it from breaking and let the press line run faster.


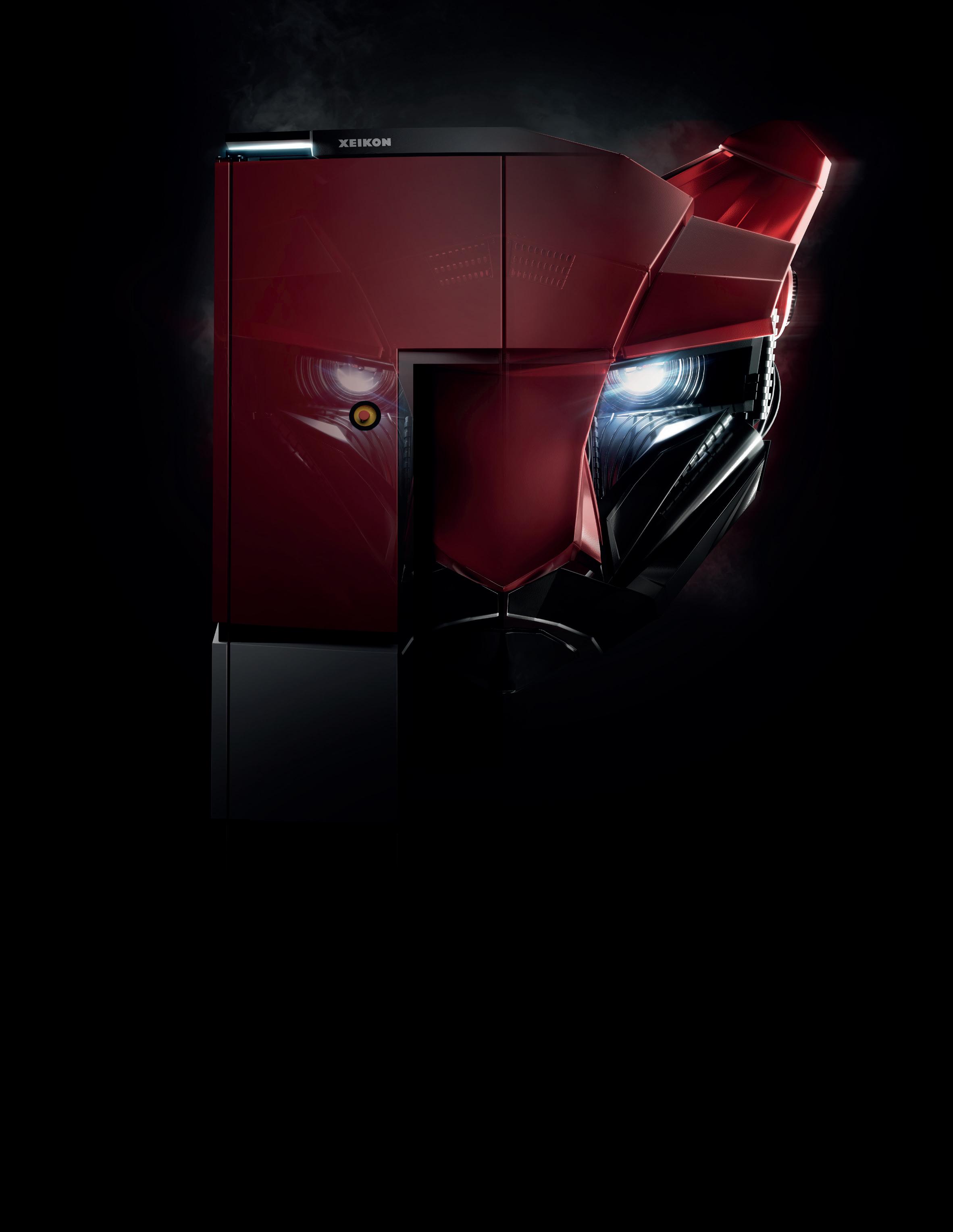