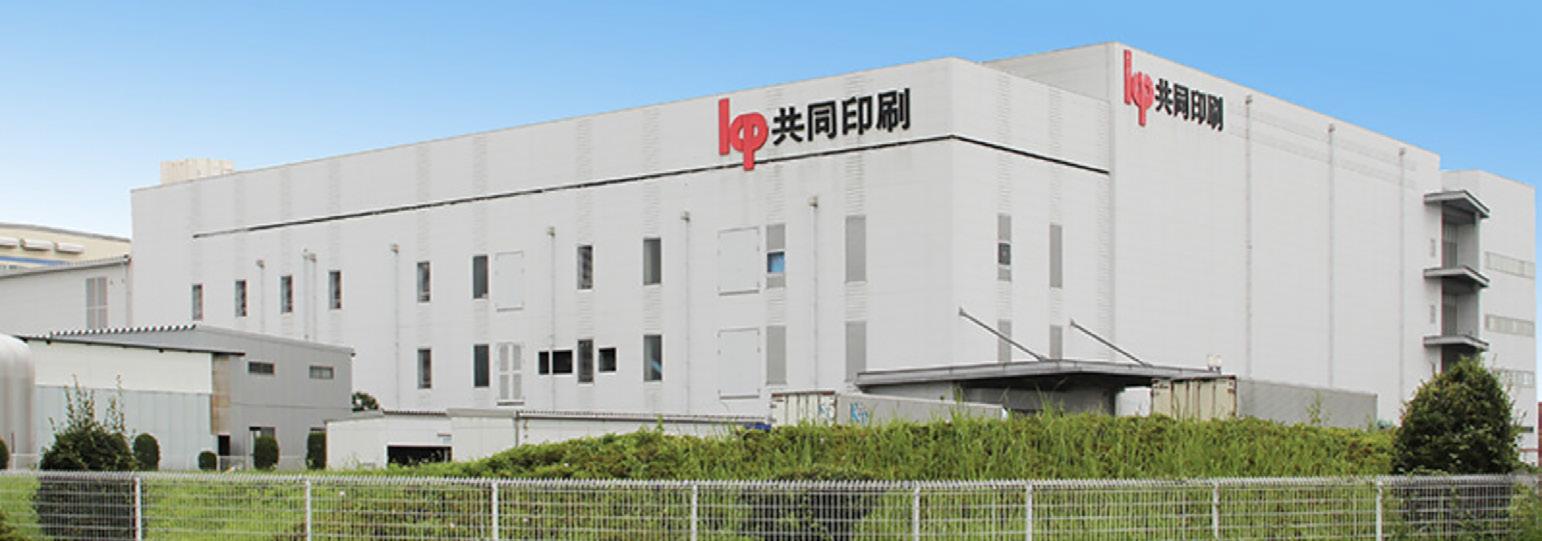
2 minute read
Strengthens Full-fledged Production from Small
Japan, Kyodo Printing Media Product Co., Ltd. | Lithrone GX40RP advance [GLX-1040RP-A]
The Goka Plant, the core of the Kyodo Printing Group's publishing and commercial printing business, was built in 1993, during the heyday of weekly comics magazines. The strength of this factory lies in its production system, which allows platemaking, printing, processing, and delivery to be completed in one location. In May 2022, the plant installed the Lithrone GX40RP advance (40-inch doublesided offset printing press) to further strengthen integrated production.
Advertisement
We asked Hiroaki Amemiya, Director and Plant Manager of the Goka Plant; Takao Nagai, General Manager, First Manufacturing Department; and Hideki Iwano, Section Manager of the First Section, First Manufacturing Department, about the installation process, the assessment after operation, and the outlook for the future.
RP press is the essential choice due to work flexibility
About 400 people, including those from partner companies, work at the Goka
Plant on a site of about 80,000 square meters. The plant manufactures a wide variety of publications and commercial printed materials, providing one-stop services ranging from printing to bookbinding, wrapping for individual shipments, sorting, and shipping.
Regarding the concept of equipment supporting the plant's integrated production system, Plant Manager Amemiya said, "From a profit, cost, and productivity standpoint, a one-pass double-sided press is essential. Since the customer's paper is used for nearly all our publication printing, a press with paper-size flexibility is required. A perfecting press was not an option due to the margin at sheet tail, so we chose the RP press, which offers a single-sided gripper configuration with no limitations on paper size."
This time, the decisive factors for choosing the Komori press were the applicability to current production and the possibility of handling high-mix, low-volume printing. "The RP press is superior in terms of maximum printing speed and paper loading capacity, and we judged that it would be sufficient for production for current business. For small lot production, which is increasingly accelerating, a press and equipment offering quick changeovers were necessary.
It is just shortly after the press's introduction, even though the average lot size is one half and job changeovers are about twice as many compared to our existing double-sided UV press. High operating results have been obtained and output is more than equal although it is an oil-based press. As to the number of colors, we adopted a press with six colors on the front side and four colors on the back side because we can print the front cover, which often uses special colors, and text in one pass," he explained.
Challenging automatic printing with parallel control
"Since most of the work we do on the new press is small lots, we installed the latest printing system in order to print efficiently, quickly, and at low cost," says Nagai. "In particular, parallel control enables almost fully automatic operation from plate changing to startup printing.
"Reductions in paper, energy, and transportation naturally lead to reductions in CO2 emissions. This press not only greatly reduces waste paper but also contributes to integrated production. When printing can be completed this quickly, postpress processing must also be more efficient, and the challenges in ensuring even more efficient production become apparent."
-- Hiroaki Amemiya, Director and Plant Manager
In addition, jobs that require high quality are run on the RP press even for high-volume work due to its sharp reproduction of halftone dots." To handle high-speed oil-based doublesided printing, this press uses Komori's newly developed belt-type suction wheel in the delivery.
"The new suction wheel has excellent paper braking and is quite effective in stabilizing paper alignment even at high