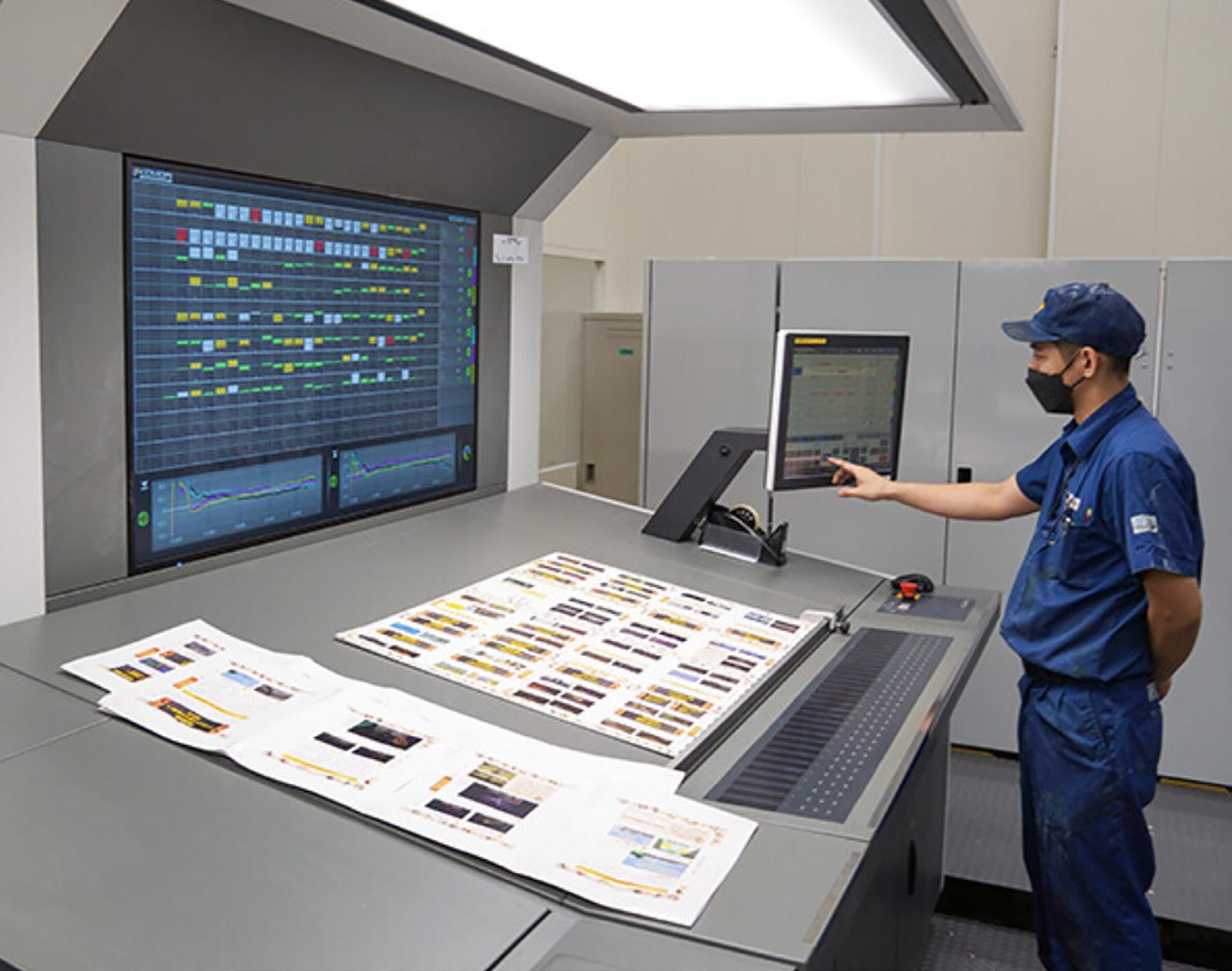
2 minute read
Full-fledged Integrated Small to Large Lots
Speedometer indicates 18,000 sheets per hour. Realization of high-speed printing. "For extremely small lots such as 1,000 or 2,000 sheets, we take advantage of quick changeover and finish printing right away. For large lots, productivity can be improved while maintaining quality by using high-speed printing and the color monitoring system."
Manufacturing Department speeds. The ability to preset not only paper size but also paper type is good," Nagai assesses.
Advertisement
Commitment to production with an emphasis on quality
The Goka Plant has positively implemented the use of quality inspection systems, and the RP press is equipped with PQA-S (Inline Print Quality Assessment System) and PDCSX (Spectral Print Density Control System).
"We have changed from visual inspection to quality checks using the electronic eye, which is ideal," says Nagai. For color control in particular, "Target densities are obtained very quickly.
Being able to check the current status on the large monitor from the start of printing is very desirable. Anyone can check the printing status of each color numerically, so that part of the operation is moving toward labor saving." Iwano said, "Color adjustments can now be made on the assumption that the operator does not touch the fountain keys."
Regarding the PDF Comparator System that can check the image information on the plate against that of the printed matter, Nagai gives his stamp of approval, saying, "This function allows the RP press to perform color measurement and quality confirmation at the same time." Amemiya said,
"While there are many jobs with strict quality requirements, such as skin colors, we are getting high assessments from clients for quality, including color and register."
Young people bring dramatic changes to operator work
Regarding changes in work, Iwano said, "Due to the functions of the automated systems, press operation is no longer dependent on the experience and ability of the operator. Up to now, register adjustment for a double-sided press was time consuming for both front and back sides, and individual differences occurred. With the RP press, the method has completely changed because PDC-SX can automatically adjust register on both sides and it's possible to confirm numerically."
"It's really amazing how the color matching can be done in the minimum number of times even for jobs with difficult quality requirements. My sense is that in many cases, it's at a level that's good enough to start production printing in the print start-up stage, and the number of test printings and sheets have decreased dramatically," he says. It also contributes significantly to the plant environment.
Nagai says that with the progress in automation, there has been a change in hiring. "It's actually easier for young people to learn how to use new functions. Since automation and numerical management compensate for the skills of experienced workers, we have selected a third-year employee to be the press chief."
The company is focusing on human resource development, and actively utilizes KGC's (Komori Graphic Technology Center) hierarchical operator training. The RP press operators are in training, and it seems that not only performance improvement on the system side but also these daily activities are the factors increasing the company's production efficiency.
Expecting further improvements in total strength
This new press is attracting attention even throughout the Kyodo Group and is positioned as a strategic machine that will lead to the securing of orders in cooperation with sales because of improved production efficiency.
"There are still many things I want Komori to do. I would like to ask for Komori's help in promoting further visualization, improving bottlenecks between processes, proposing preventive maintenance to reduce machine downtime, including for existing machines, providing more human resource training, and cultivating employees who can take on challenges such as the pursuit of what more can be done in printing," concludes Amemiya.
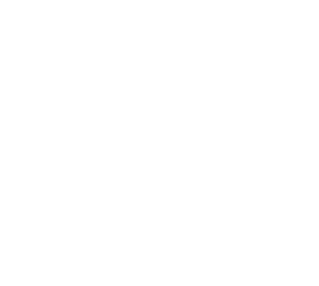
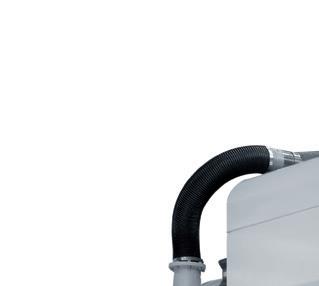

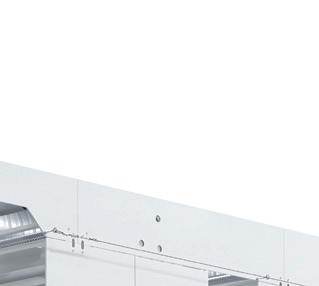

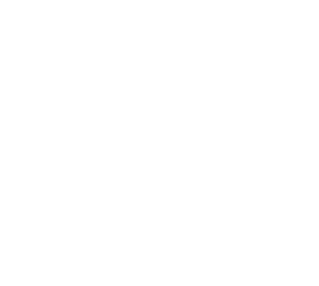
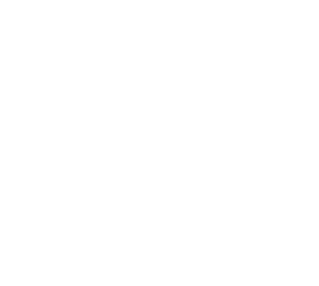
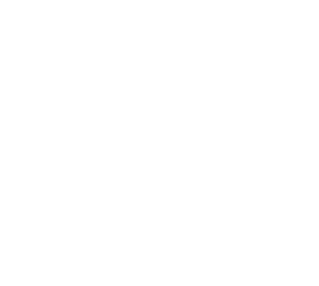
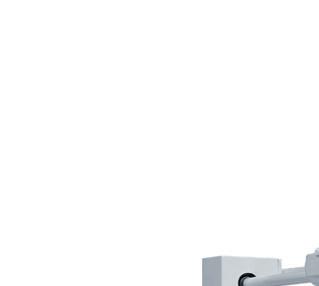
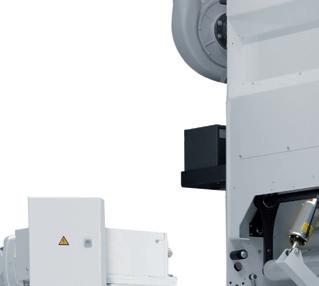
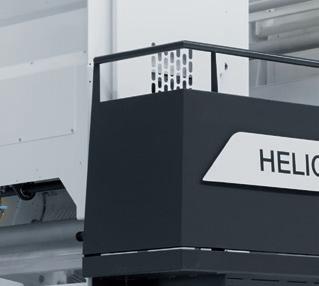
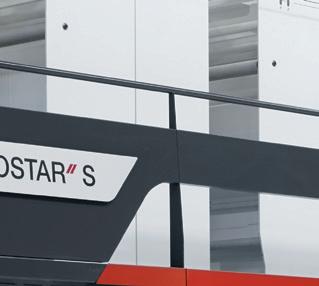

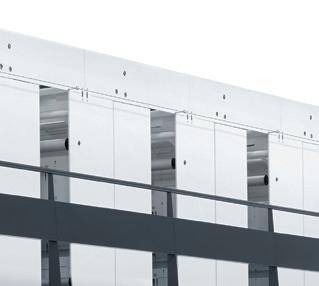
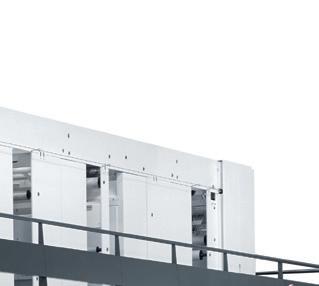
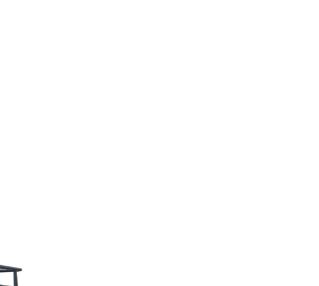
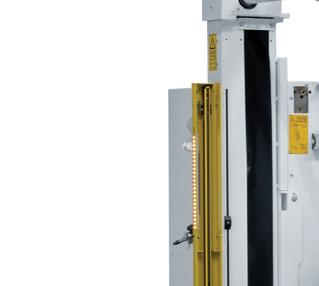
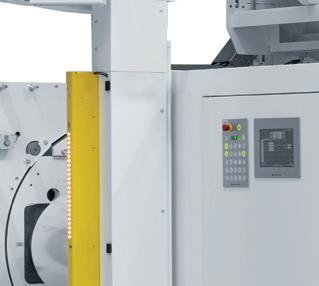

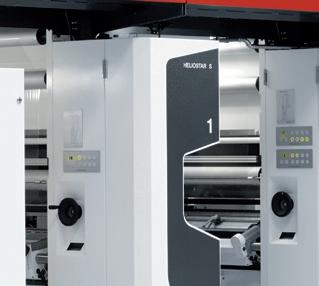

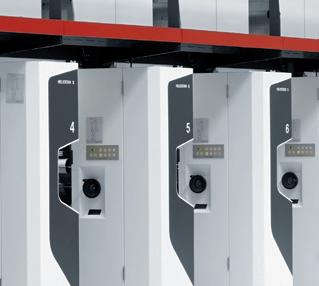


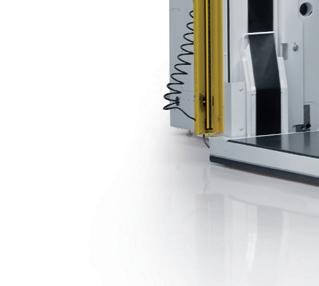

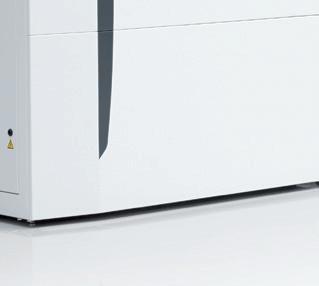
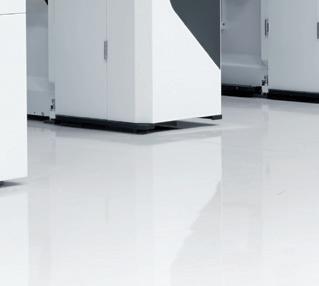
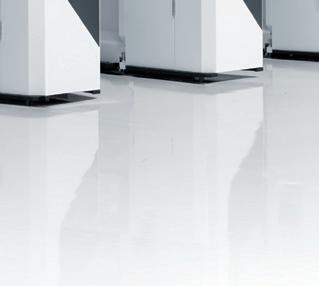
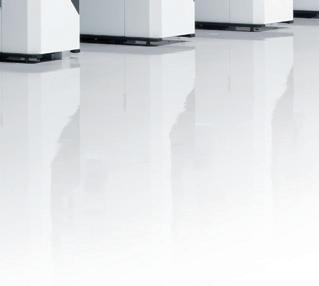
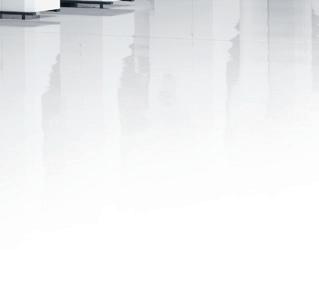

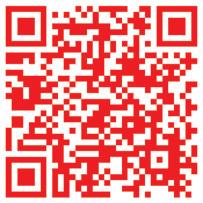
