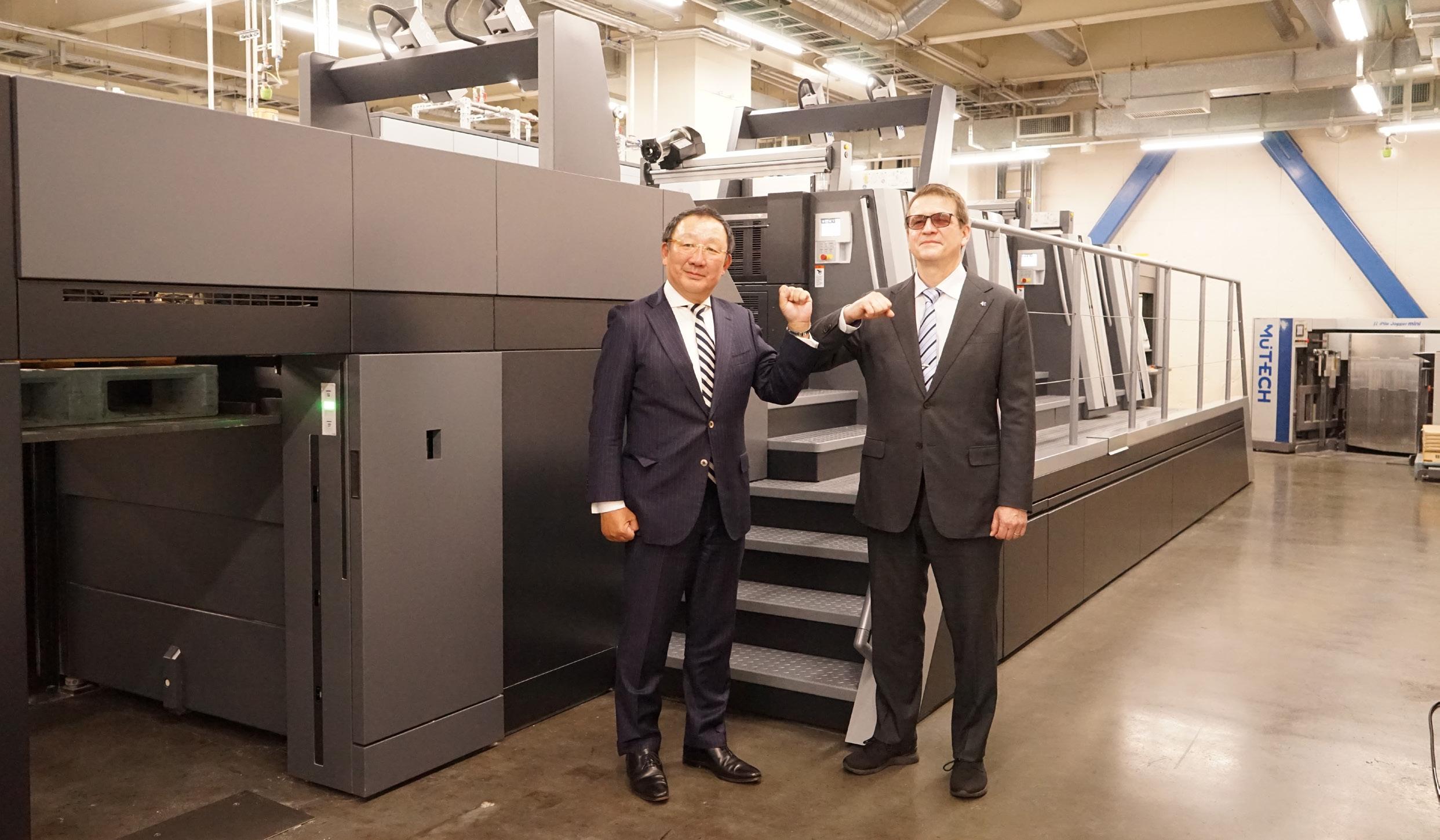
5 minute read
Speedmaster XL106-4-P, the sixth four-colour press in five years.
Uematsu Corporation President Hiroshi Fukuda and Heidelberg Japan President Jorg Bauer exchange elbow touches in front of the sixth Speed-master XL 106-4-P.
• Uematsu Installed the sixth Speedmaster XL106-4-P within five years. • Push to Stop and Internal project “IJIGEN” to address the growing shorter job run segment. • Continuous Improvement in internal workflow and process to increase output and profitability.
Advertisement
Since its foundation in 1958, Uematsu Corporation has specialised in the fields of plate-making, printing and finishing. Uematsu is one of the most productive prin-ting companies in Japan as a contract manufacturer specialising in sheet-fed offset printing. In the previous years Heidelberg Polar cutting and Stahl folding machi-nes had previously been installed by Heidelberg Japan, however 2017 was the first time a Heidelberg Speedmas-ter was installed.
Masao Tsuchiyama, the Head of Sales at Heidelberg Japan, said: ‚President Fukuda, who came from the financial industry, has very high expectations on cost-effectiveness, and this has been instilled into the management team of Uematsu. This is the reason why it is a great pleasure for us that he decided to install the first printing machine five years ago and has added several machines since then, and now five years later, Heidelberg Japan recently installed a sixth machine, including a further two machines for one of the groups company Smart Graphics Co. “It gives all of us a great pleasure and confidence that Uematsu see’s Heidelberg Japan as a first choice partner” adds Tsuchiyama.
Before the first installation of the XL106, Uematsu had been proactively adopting the concept of “Digital transformation” through the adoption of digitalisation and automation of all processes.
This Is also aligned with Heidelberg’s strategy of the autonomous Smart print shop, an area which has been seeing a huge adoption and success globally within the commercial printing segment, and The new Speedmas-ter XL 106 is also equipped with all of the high automa-tion devices to eliminate unnecessary manual interven-tion during the production process.
Our production is now conducted with a clear separati-on between what should be done by machines and what should be done by people.
Push to Stop and Internal project “IJIGEN” to cover the growing market demand for short production run lengths
Mr Fukuda, President of the Uematsu Corporation, states “In the course of our efforts to improve producti-vity, we were able to visit the most productive printing company in the world in 2014 by arrangement with Hei-delberg. It was a company called ESP in the UK, and the president, Anthony Thirlby, who today is a visionary within the Printing industry with a production philoso-phy thoroughly committed to high productivity.

They were producing as much volume and more printed sheets as our whole company was with just two prin-ting presses. While we had 18 various offset machines at the time. Although there were differences in their printing business compared to ours, such as our use of proofs and manual press checks, I thought there was something extraordinary to be learnt from ESP and Anthony.
So I launched our internal “IJIGEN project (Different Dimension)” as soon as I returned to Japan. The idea was to dramatically improve productivity by reducing the press set up and make ready time to the ultimate levels Heidelberg, on the other hand, also the XL 106 with the highest levels of automation and speed.
These are machines have features such as full job data set up and color control, fully automatic plate chan-ging and job preparation this eliminates the need for manual operation and therefore reduce the make ready times significantly. That‘s exactly what the times demanded, the IJIGEN project we are working on together with Heidelberg‘s ability to realise Push to Stop Autonomous print production is a gutsy match.“ He stated.
“We believe that the Heidelberg Speedmaster machines being more productive in turn generate vastly more be productive and profitab-le, such as 1/1 and 2/2 and special spot colour printing.” He also expressed.
Continued strong support, end to end for the best per-formance and success
Jorg Bauer, the managing director of Heidelberg Japan said: “We are very grateful to President Fukuda, who has held many important positions in the industry, including Chairman of HDF21, and who understands the value of Heidelberg’s solutions and is committed to DX, productivity improvement and execution. I am very grateful to him for understanding the value of the Heidelberg solution and for investing with Heidelberg for six machines over five years.

had the ‘Push to Stop concept”, which aimed for automation by elimi-nating as many of the manual processes that we were all too familiar with in our way of work.
In this sense, we thought that we could take on the challenge of our internal process Improvement “IJIGEN project” together with Heidelberg, so we decided to form a partnership with the aim of improving nume-rous predefined KPI’s .“ Explains Mr Fukada. As for why the Speedmaster XL 106 was chosen, he ad-ded: ”The decrease in production run lengths has been extraordinary since 2017. No matter how much the number of individual job orders increases, the decrease in run lengths outweighs it. sa-les are better for the company’s profits Even the initial investment was significantly higher than our previ-ous acquisitions, the Heidelberg Presses are far more profitable in the long-term. In reality, the data we are recording proves how far more productive Heidelberg machines are.” Mr Fukada added.
Two specific and unique Heidelberg technology’s equip-ment that were decisive in our decision to choose Heidelberg as our project partner were the Prinect Produc-tion Manager Prinect Inpress Control, which reduces manual touch points to an absolute minimum, and the Hi-Color Multi Drive, which allows the preparation of units during production, among other things, this has a tremendous effect on reducing make ready time. He added: “With these new features, we are able to expand into new business areas and I was shown the Uematsu production site today and all of the machines were running at maximum production speed with various paper substrates, bringing out the best performance of our machines. We are very pleased and Heidelberg Japan will continue to provide the best in class end to end sales and service support for the success of Uematsu Co.“We are com-mitted to working together in a strong partnership to achieve success,” he said.
1. Speedmaster XL 106-6, in May 2017 2. Speedmaster XL 106-5, in Jan 2018 3. Speedmaster XL 106-6, in Jan 2019 4. Speedmaster XL 106-8-P*, in October 2019 5. Speedmaster XL 106-8-P*, in October 2019 6. Speedmaster XL 106-4-P, in December 2021 *Machines supplied to Group company Smart Graphics Inc.