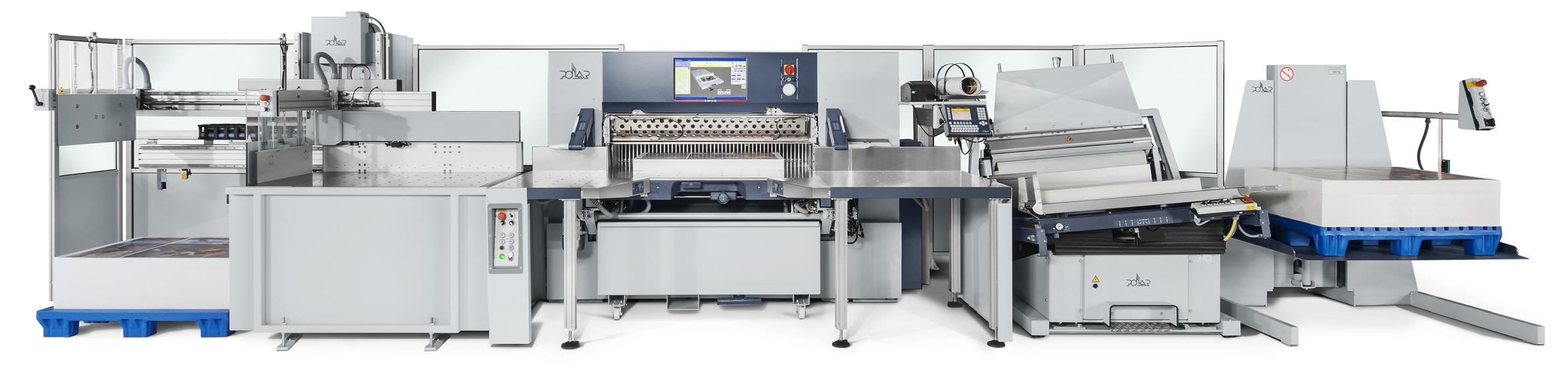
7 minute read
ALWAYS A STEP AHEADHeidelberg Postpress solutions.
ALWAYS A STEP AHEAD
Heidelberg Postpress solutions.
Advertisement
Heidelberg continues to lead the way in productivity throughout the entire production process. Whether it be prepress, printing, cutting, folding, or packaging requirements, Heidelberg is there to assist our partners with the latest technology, OEE, service & support.
As our partners have adapted to new technology in the pressroom over the last few years, bottlenecks then occur in different areas of production such as postpress. Polar, Stahl and our OEM partner MK Masterworks have several innovative solutions in this area, which we examine a little further below¬¬.
Polar - The postpress area of cutting offers a great deal of potential for improvement in production.
A solo high-speed cutter reaches its limits above a certain press output. The high-speed cutter is at a standstill during manual loading and unloading of cut material, hence valuable production time is lost. A typical cutting operation consists of the following processes: Loading, manual programming, cutting, unloading.
In the case of a Solo high-speed cutter, it can be assumed that approximately 35% of the time of the cutting process must be spent on loading material. 15% on programming with only about 25% of the time spent on the actual cutting. The last step in the process chain, unloading the cutting material, also takes about 25% of the time. The time taken by the supporting processes can be significantly reduced with a POLAR Cutting System 200, which includes a stack lift, an automatic jogger and a Transomat unloader. Existing high-speed cutters can easily be retrofitted with peripheral equipment.

The stack lift moves the cutting material to an ergonomic working height. This not only speeds up loading, but also reduces the strain on personnel. From there, the material can be fed to the automatic jogger, which precisely aligns the material. Parallel cutting is possible during the automatic jogging and spreading process. After cutting, the Transomat unloader unloads the cut products onto a pallet with edge accuracy. During the unloading process, the next cutting layer can be prepared or cut.
A POLAR Cutting System 200 increases productivity by up to 100% compared to a stand-alone high-speed cutter, improves quality and thanks to its ergonomic arrangement is easy on personnel, thus providing a solution that can prevent finishing from continuing to be a bottleneck.
Stahlfolder TH / KH82-P range of folders carry forward peak performance
The Stahlfolder TH82 -P folding machines set the benchmark for productivity and quality. Since 2016 we have placed over 180 such units in the marketplace, whilst a further 70 units of the KH 82-P model can also be found worldwide.
The PFX feeder introduces the flat sheets into the folding system shingled, which helps achieve a folding output of up to 18,000 sheets per hour. This means that the Stahlfolder TH 82-P can keep pace with production on the Speedmaster XL 106, so that the peak performance in sheetfed offset printing
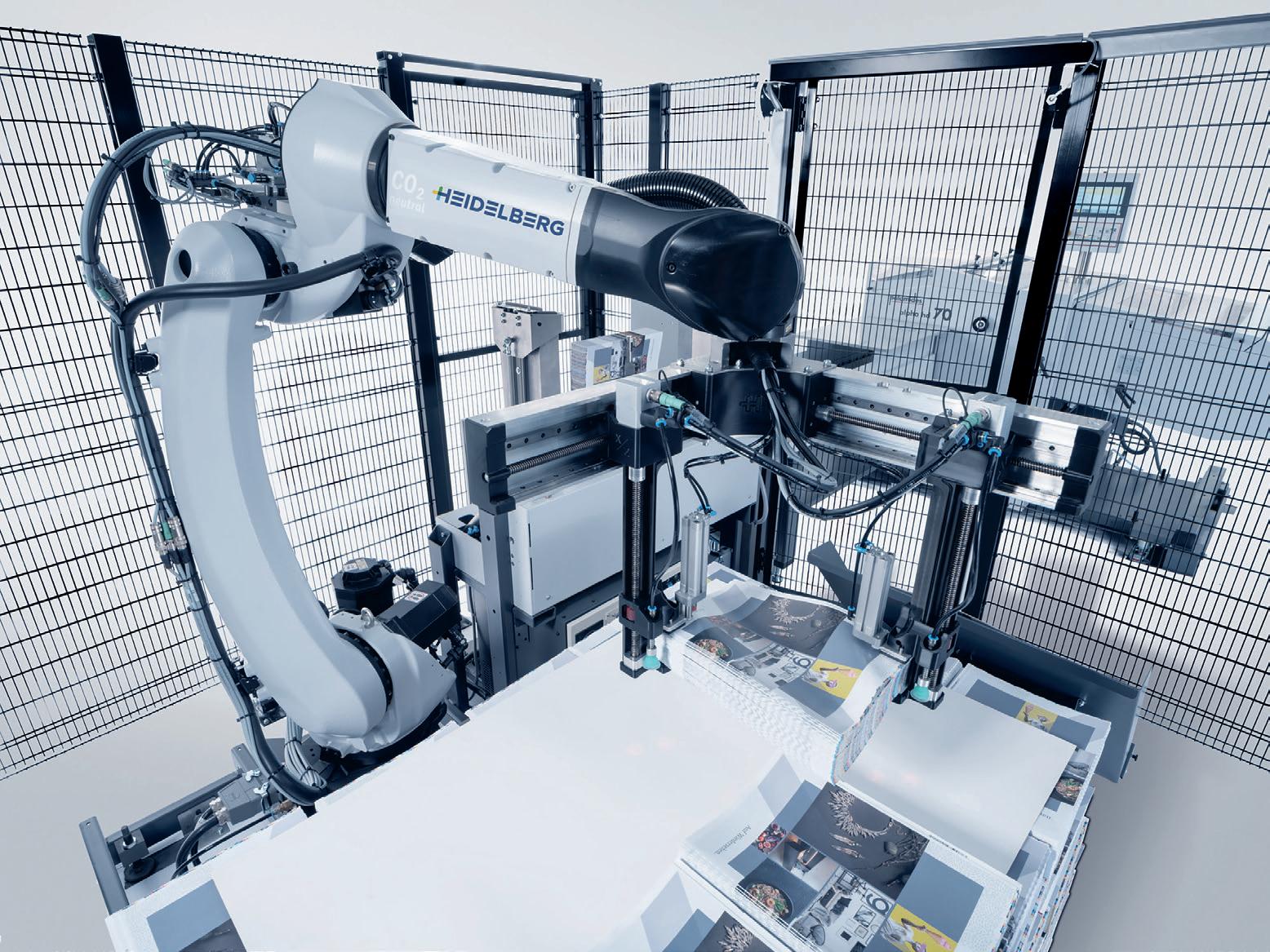
P Stacker – Signature unloading via Robotics
can be carried seamlessly through to postpress. A P-Stacker installed at the output of the folding machine will take the stacks of signatures and automatically set them down on pallets. Besides safeguarding excellent process stability at high speeds, the robot also takes care of heavy physical work that would otherwise be left to staff. This means employees can apply their skills to other production tasks instead.
P Stacker – Signature unloading via Robotics
As of today, the operator of one of our Peak Performance folding machines in industrial signature folding, moves up to 7 tons of paper per shift from the delivery to the pallet. This is equivalent to the weight of a large, full-grown elephant. The P- stacker increases the productivity and profitability of the folding machine, as it can produce at full speed, without interruption. Personnel costs fall and the attractiveness of the workplace increases.
This makes it easier to recruit skilled personnel for the finishing department in the future.
With the Stahlfolder P-Stacker, postpress is taking another major step towards operator-independent productivity and its demand has exceeded our expectations with the factory being fully booked until mid2023 for delivery. Together with our Stahlfolder TH/KH 82-P and autonomous signature production, the result is a coherent overall concept in line with Heidelberg's Push to Stop philosophy.
Heidelberg's total solution including Postpress packaging solution
Heidelberg offers products along the complete value chain of packaging production: starting with Prinect software solutions for structural design, digital workflow with solutions for color management, nesting, layout, separation and rendering, thus offering a complete software suite for converters.
We excel with our CX & XL range of presses in complex applications for high-end folding cartons, as well as in efficient manufacturing. For finishing,

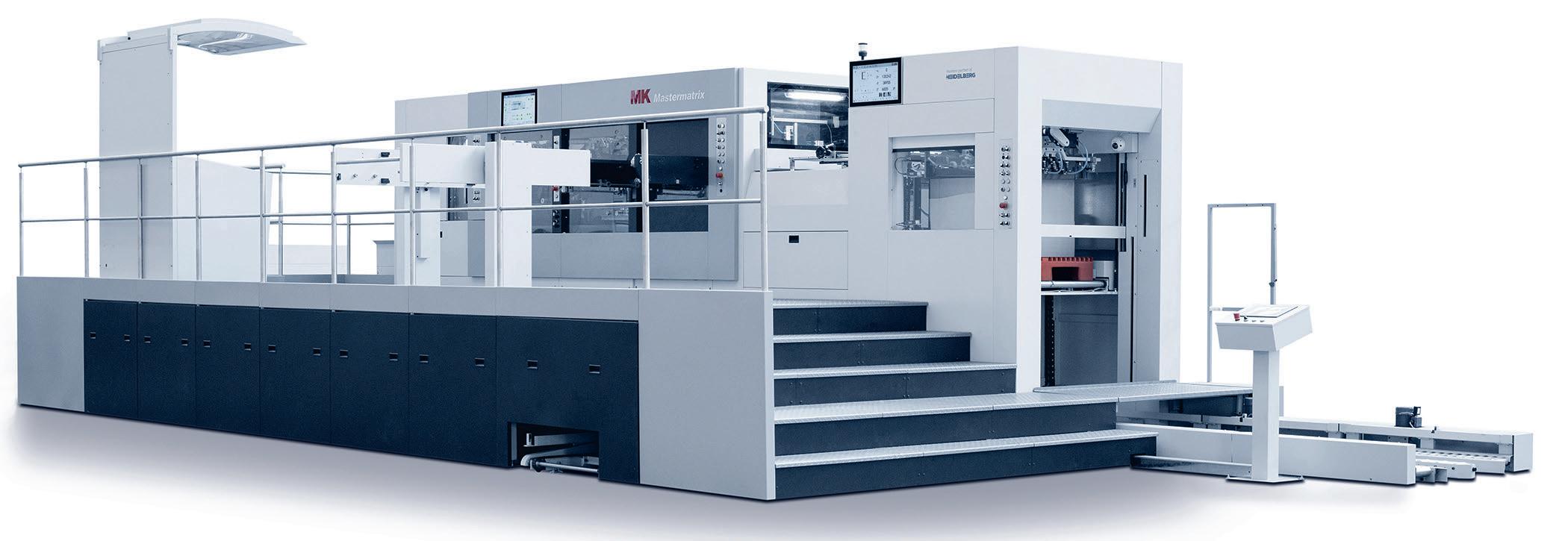
we have worked for 8 years exclusively with products from MK Masterwork. That gives us access to more than 20 products for a wide range of finishing applications like foil-stamping, diecutting, inspection and folding carton gluing.
Beyond the products, Heidelberg also maintains the largest service network of any supplier to the folding carton industry. But our system service offerings go far beyond the traditional support after an incident has happened: Video Call, one of our latest products, enables the service engineers to look directly into a machine for a live diagnosis.
We might even be able to advise a work around to keep your machine in production. Another highlight of our service products is “Predictive Monitoring”: this service detects anomalies in our printing presses before malfunctions and related downtime occur – with the help of big data analysis and our experts we can plan countermeasures before the worst case is happening.
Postpress package market conditions and situation
Once printed, a carton needs to be diecut and processed on a folder gluer. In many converting operations, the finishing side has not enjoyed the same level of investment activity than the printing side. It seems that both diecutting and folding gluing haven’t moved in several years – yet nothing could be further from the truth: options that were once considered high-end only are today available in more affordable segments (for instance auto non-stop feeding with a pallet logistics system, optical sheet alignment, and even the blanking station itself). Standardized tools and quick-locks functions in all stations are speeding up make-readies. Another option is to combine two processes in one machine – for instance hot-foiling and die-cutting.
Heidelberg and MK Masterwork offer the unique Duopress with two cutting stations for this requirement. The first platen station allows for instance for hot-foiling or embossing across the complete blank, the second station is used for die-cutting and creasing, stripping and blanking stations follow. This machine reduces inventory and speeds up significantly the manufacturing of high-end folding cartons.
For folder gluers, the machine development has been one of specialization on the one hand and efficient high-speed manufacturing on the other hand. For pharma cartons, an inline braille system plus inspection helps to comply with all compliance regulations, including 100% braille and print inspection. Luxury cartons can now be finished in one pass on a folding carton gluer, thanks to a turning station.
And for high-speed straight line carton manufacturing, we offer even the complete logistics system around the folder gluer, including robotic depalletizing and feeding to automatic blank packing in several rows and layers. The packers can even be equipped with a carton erector, tiesheet inserter, a labeling system and a palletizing robot – completing the fully automatic features.
Cooperation with Heidelberg and Masterwork
The collaboration between Heidelberg and MK Masterwork started in 2014 – and has grown stronger in many dimensions over the years. To date, more than 850 machines have been sold through Heidelberg – and with MK Masterwork as the exclusive OEM partner more growth is in the forecast. Since 2019 MK is also the largest single shareholder of Heidelberg, underlining that the partnership between the two companies runs deeper than the standard OEM relationship.
With the successful launch of the Mastermatrix in 2021, Heidelberg has now a complete product lineup available – for shorter runs with lower volumes all the way to our peak performance machines. The last 12 months have been the strongest 12 months ever in order intake for Heidelberg’s postpress packaging products – the post COVID recovery of our customers drove our success to new heights.

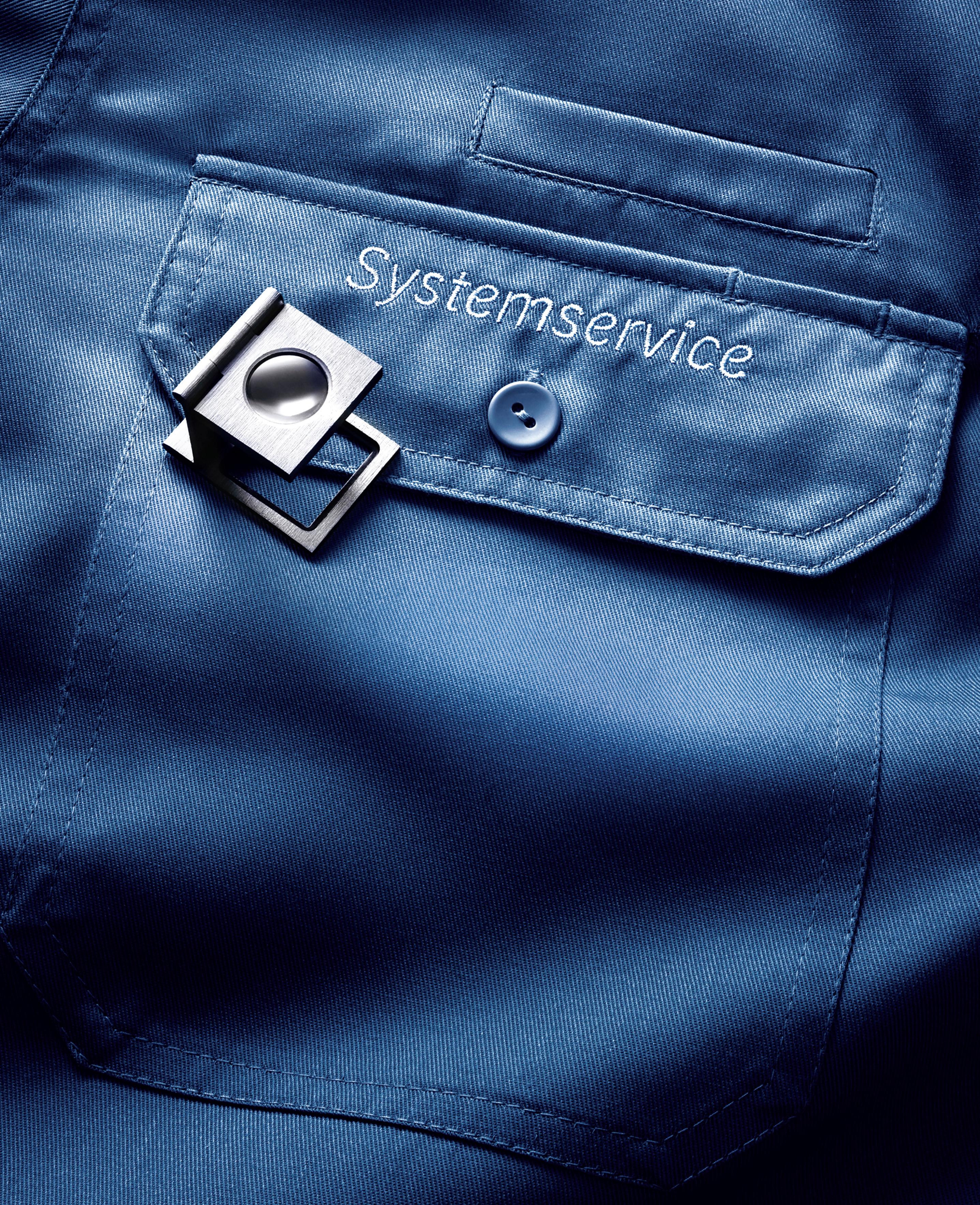