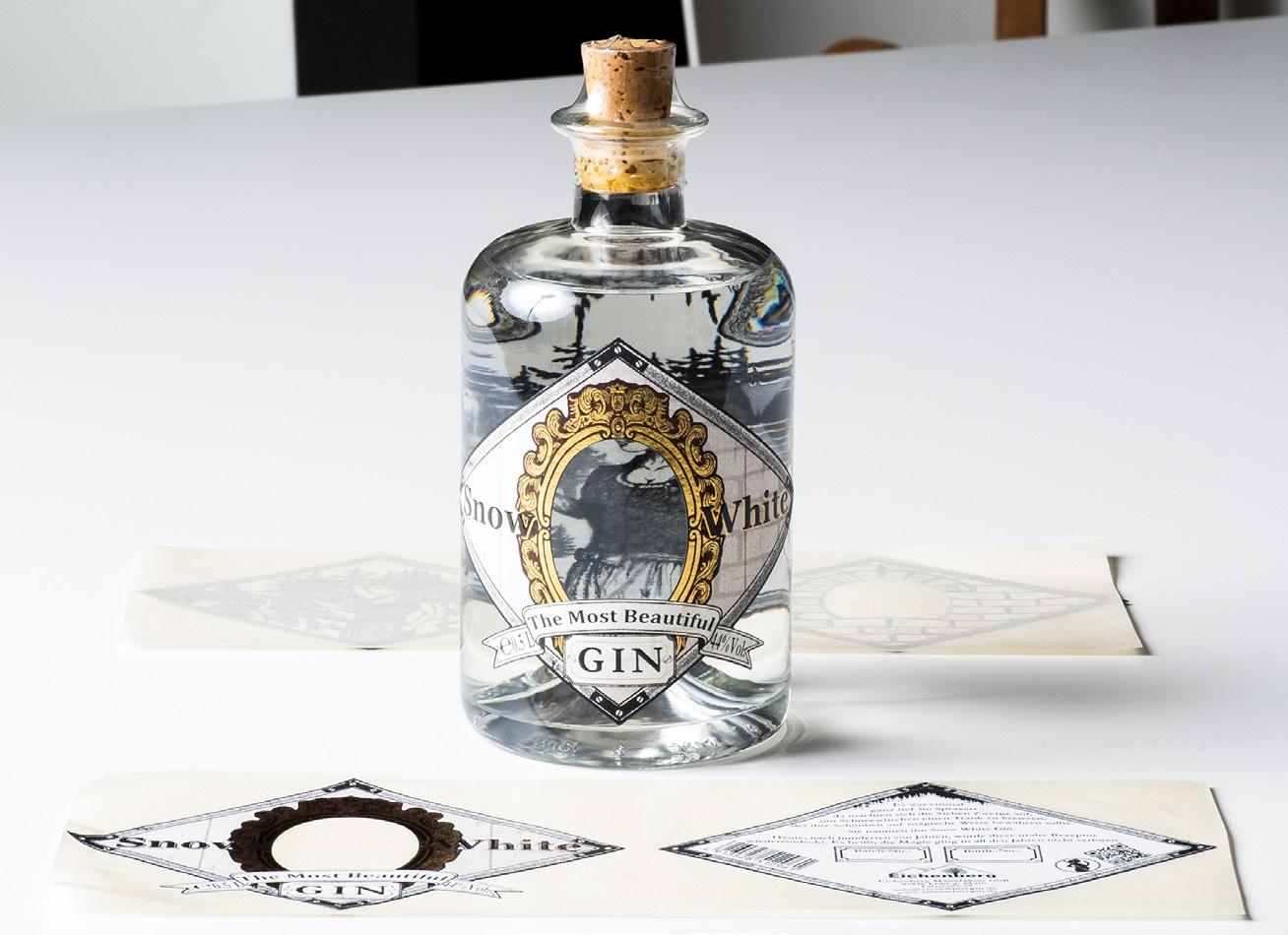
4 minute read
Next Generation Press Operators
What’s Needed & How to Train Them?
Printer or Operator
Advertisement
Ever since the introduction of the first servo-driven narrow web flexo press, MPS has held the printer in mind as being the key to delivering excellent quality product within the given timeframe. For a few years, we even had our logo reflect that vision: “Printers First”.
sustained in the future since in most countries, school and the educational systems skip traditional printing and focus more on the cleaner computer side of the industry.
For sure, the scope of an operator’s work changes as they become part of a continuous performance process. When using analogue print technology, like flexo or offset, process issues will occur for e.g., density change during printing, dirty print, ghosting, etc. These are typical print issues that can be measured and detected however not (yet) automatically resolved.
As the global economy develops and new technology enters our world, as well as social and demographic challenges, it is fair to say that a printer working on a label or packaging press has, and will, move more into an operator role. Where the printer by trade or education has knowledge of the basic printing process and all parameters involved in striving to deliver the best printed product, the operator will tend more towards operating the press and delivering the product.
Making sure the operator delivers that quality (and the volumes) as expected in the 21st century, a different approach is required, especially considering the development of highly decorated labels throughout the years and the sustainability challenges we face by using modern, highly automated printing presses.
Not only traditional flexo becomes more digital, the move and decision to using digital printing technology in either a stand-alone or hybrid configuration requires a different approach on hiring and educating operators. All press manufacturers develop technical solutions to help the operator achieve this.
Using most of these technical solutions still requires basic printing knowledge and one can argue whether this can be
Next to the technical and datadriven flexo press, print shops should embrace a continuous improvement approach where press data is combined with improving print shop processes to achieve the highest possible Overall Equipment Efficiency (OEE) and the capital investment that is made does pay off.
In addition to the press HMI, relevant information, suggestions, and advice is provided to the press operator not only helps but also motivates the operators in their day-to-day work. This virtual coach, as well as benchmark data, is featured in a second screen as part of the press HMI.


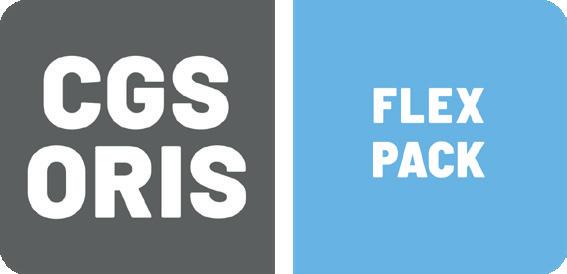
We are now in a transitional phase where press information is combined with production and customer workflow data. This requires human interpretation and often human intervention of specialists who have the knowledge and can combine press data with production data and requirements.
In this situation, refreshment training of an operator can be partially triggered by the press itself. Specialist analysis is necessary to improve other components of a job change. Specialists of the print shop and the press manufacturer ideally team up in a continuous performance improvement program.

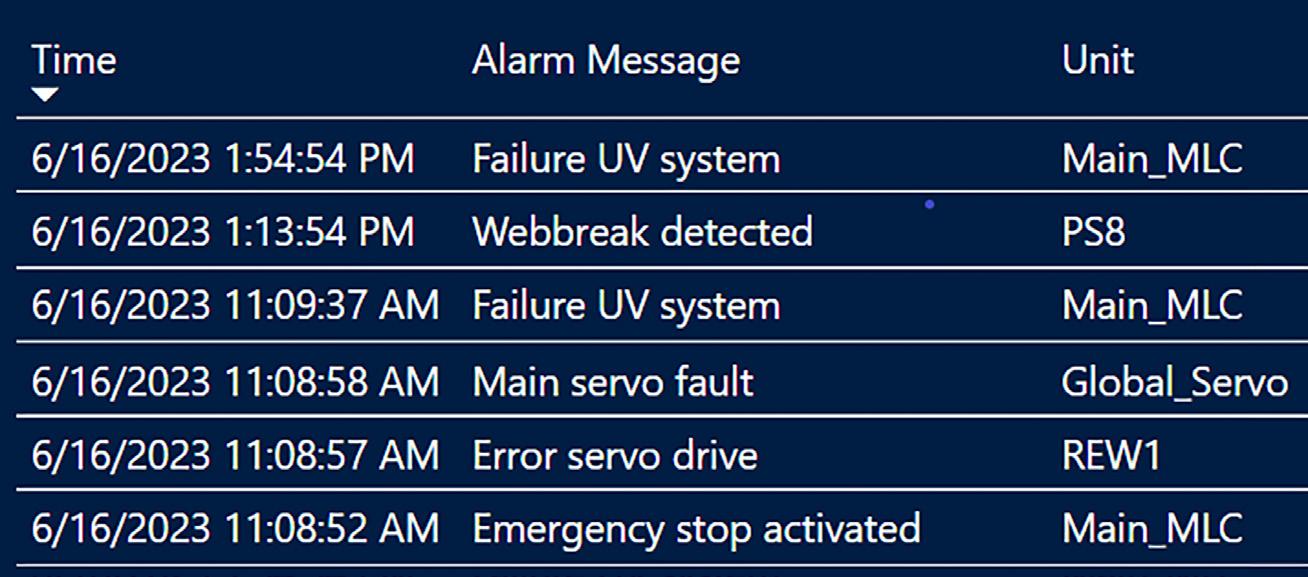
Latest developments show steps towards a more autonomous form of training or coaching. In addition to the virtual coach that helps the operator, online training and e-learning sessions are available on the press HMI and can be automatically triggered by the press performance data or can be separately attended. The next development is to include algorithms that create a form of AI to replace logic and programmed actions by autonomous analysis, corrective actions, and proactive coaching.
In this situation, proactive service support can be generated either by the press itself, the press manufacturer, or by any OEM in the press to make sure the operator can continue to produce.
Press training where the operator is taught how to use the press will still be required; however, typical print and application training might take a different approach. Early of 2023, MPS introduced the virtual coach that
Technology will help the operator produce high quality product and the press itself; the pressroom infrastructure will also support the operator in maintaining and improving quality and productivity. The Operator Screen shows relevant data for improving the press performance and productivity, and is derived from objective, unbiased information provided by MPSConnect to a print shop’s leadership and management team.
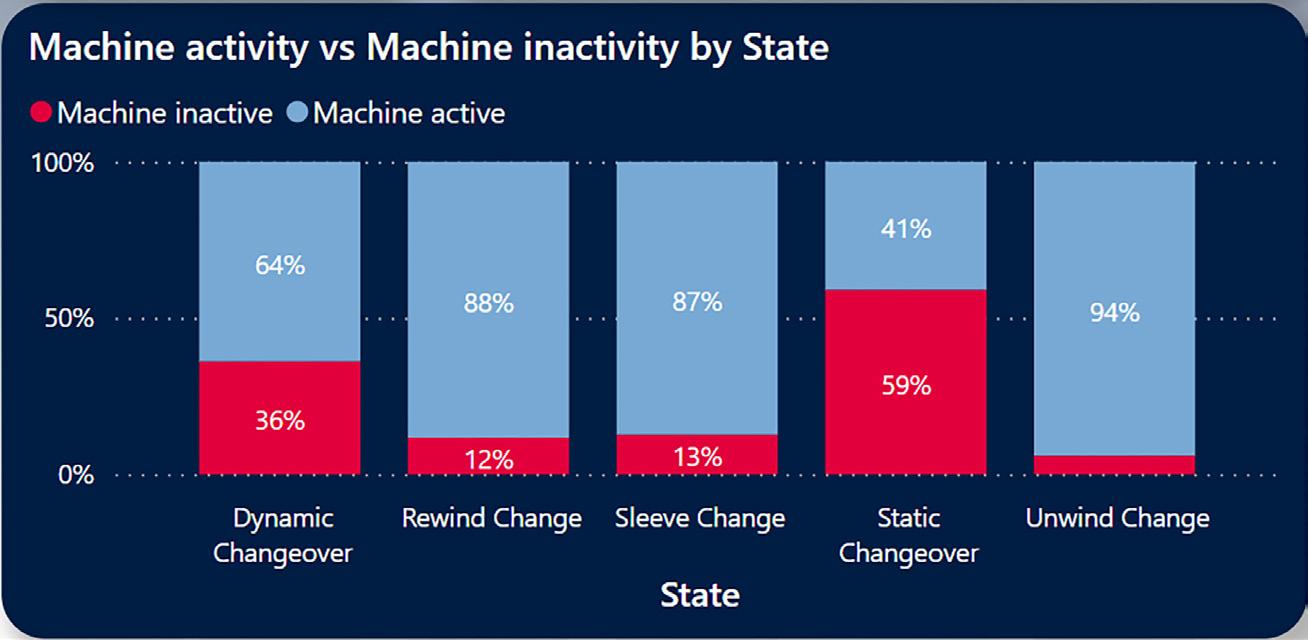
For print shops, it is key that they continue fostering their operators and develop alternatives for the gap that local schools leave behind. As we are experiencing large mergers and acquisitions in our industry, the larger groups can set up in-house training and certification programs where the focus should be on retaining qualified staff. In parallel, the industry trade organizations could play a role in facilitating training for smaller print shops and coordinate industry-wide programs and standardization where possible.
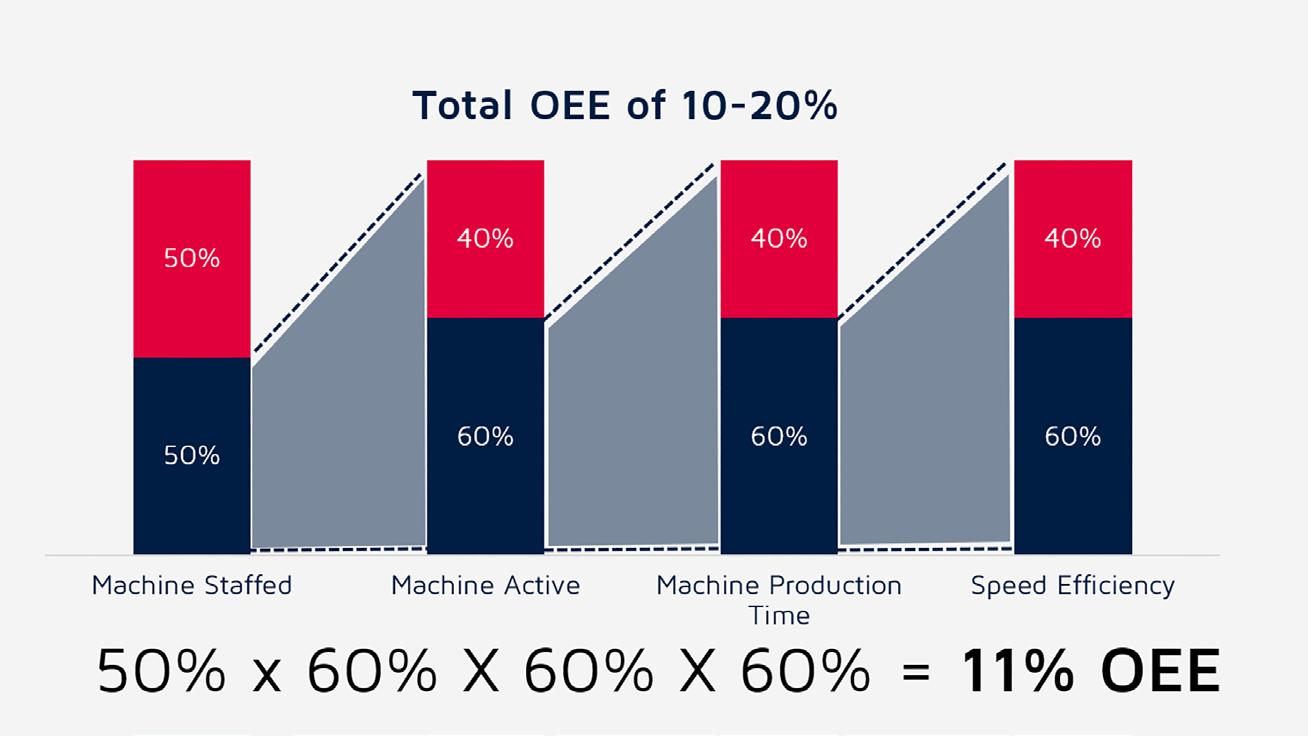
However, consumer markets continue to change and some markets require complex products where several different print techniques are combined with multi-step converting to create a highly appealing label. Even with the range of (digital) technology available— human knowledge, skills, and above all creativity—will always be required.
Certainly, many operators, factory managers, and owners have been working in this industry for many years. They know their business and applications well. Nevertheless, these new technologies provide insights to perform even better and remain competitive. Though it often requires a new approach.

The use of factual data and intelligence around the printing press is rapidly developing. The use of this data and (artificial) intelligence requires working methods different from the traditional one of craftmanship that are still prevalent in our business to some extent.
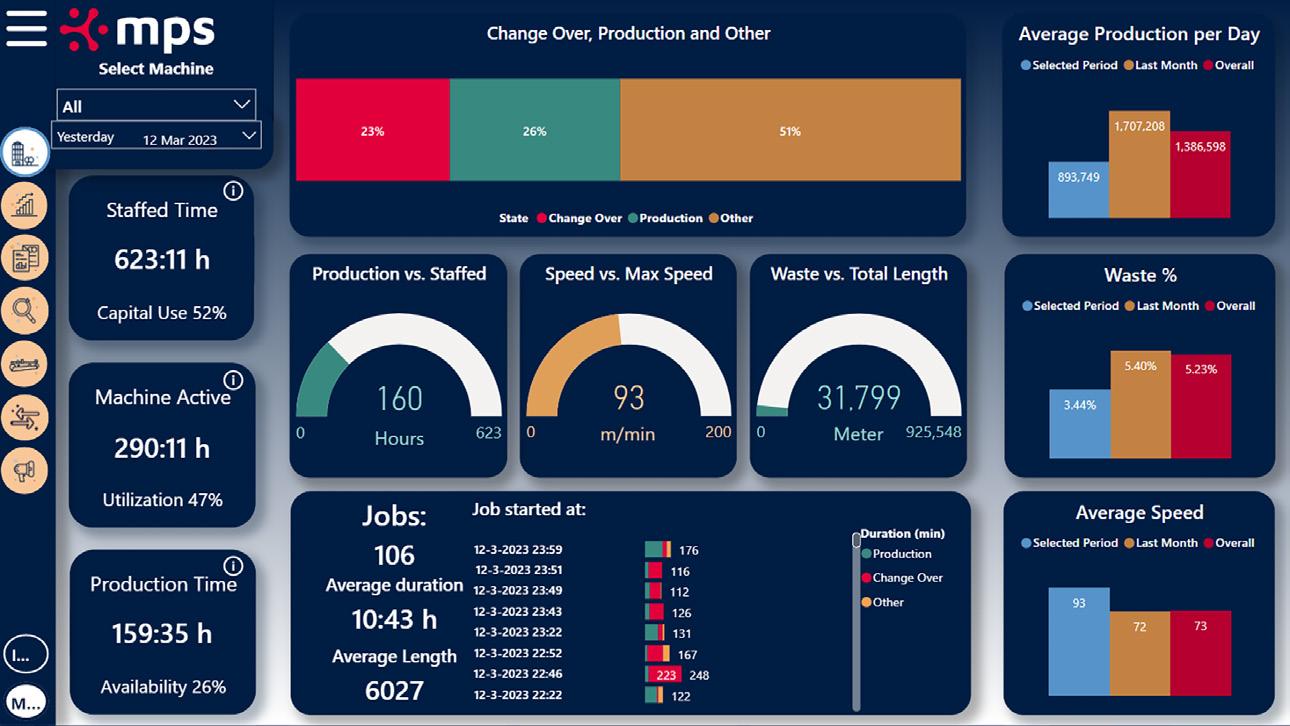
The printer by trade might become scarce, but their knowledge and experience will still be required in a different role. So next to all technology, education and taking the operator seriously as well as an open mindset to embrace new technologies is important to keep our industry vibrant.
About MPS
As a reputable manufacturer of high quality and highly automated flexo, offset and hybrid printing presses in the label and packaging industry, MPS looks beyond the machine through intensive cooperation with its customers. Founded in 1996 and celebrating our 27th anniversary year, innovation and continuous improvement are in our DNA.
By connecting with MPS as your performance partner, you ensure the best in reliability and productivity from your printing press. Connect with our machines to create insights in productivity.
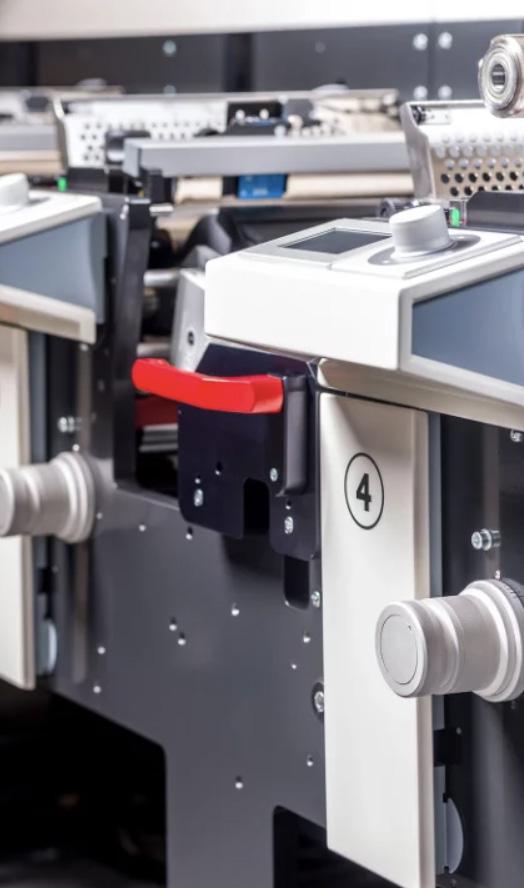
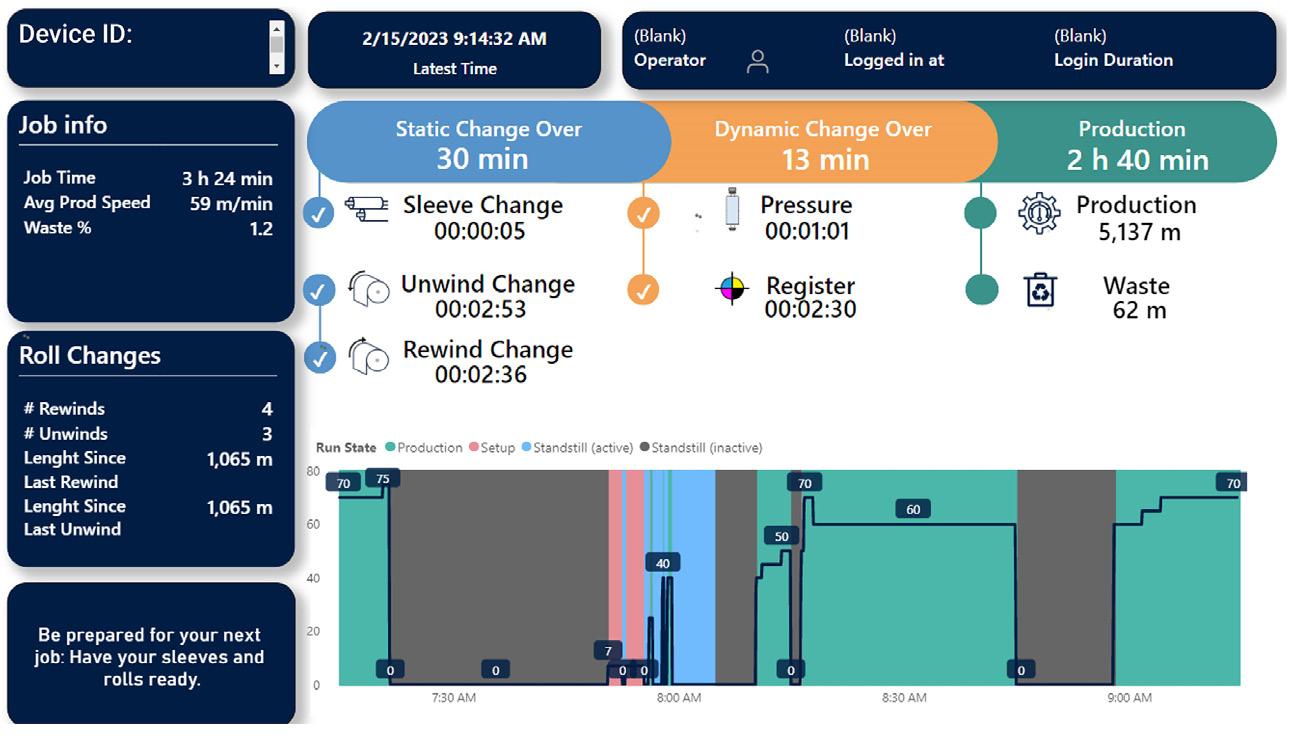
Connect with our service for maximum uptime. Connect with our specialists to create access to knowledge and expertise.
This is how we evolve: connect to grow, together.