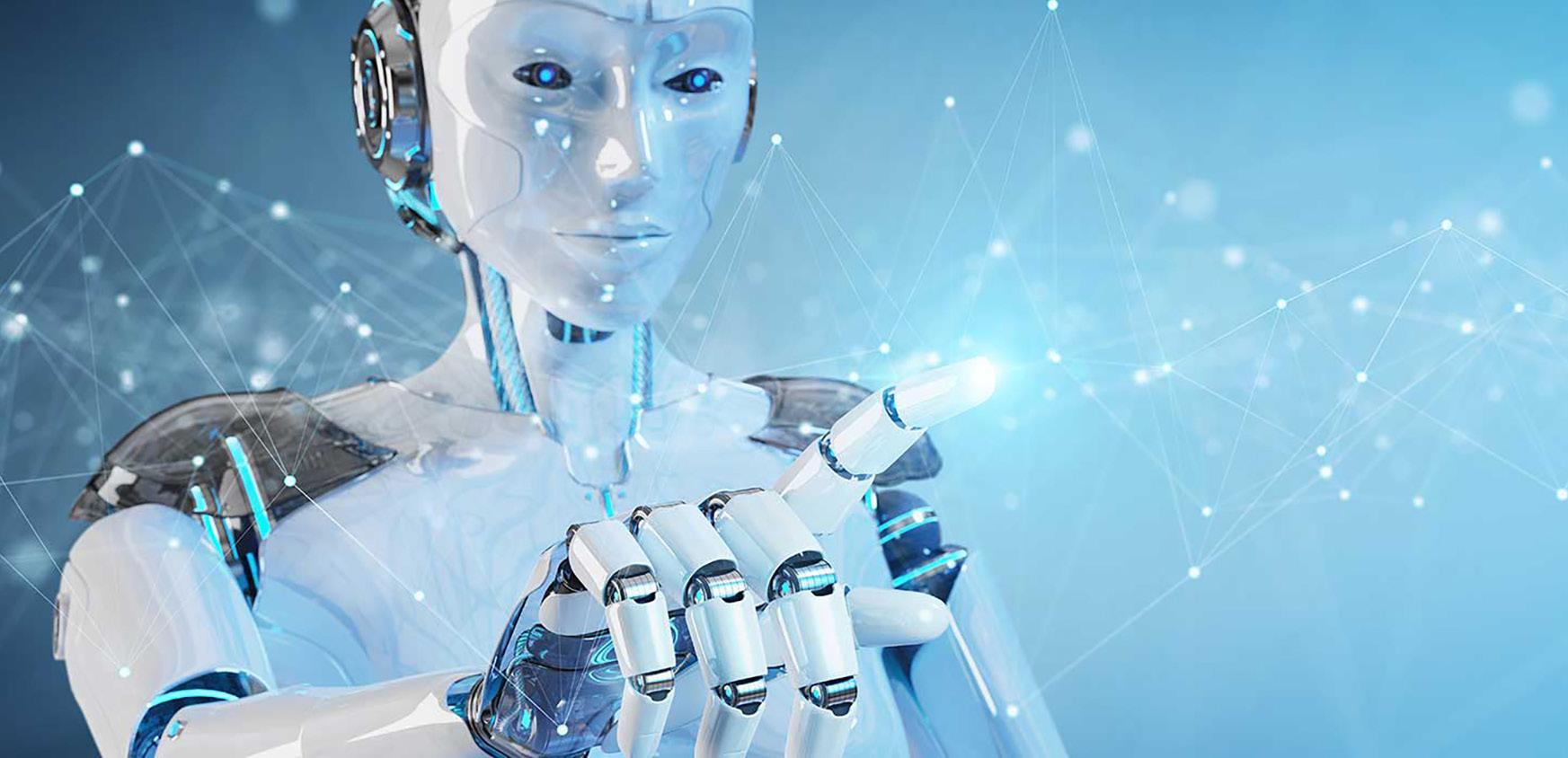
3 minute read
Are Robotic Technologies Ushering in a Job-pocalypse?
By James McKew, Regional President APAC, Universal Robots
In the past years, businesses were battered by the COVID-19 pandemic while the economy was significantly hit.
Advertisement
Countries around the world have witnessed huge implications caused by the pandemic, including sudden labour shortages, supply chain challenges and default work from home arrangements resulting in absenteeism of human resources. While the modern workflows were designed with productivity in mind, the lack of preparedness for an unforeseen pandemic and economic crisis has caught multiple sectors off guard.
Fast forward to today, despite signs of economic recovery, challenges involving labour shortages remain. Employees have begun to re-evaluate their working lives, resulting in many turning away from roles that are dull and dangerous. According to the 2021 APAC Workforce Insights Report, the top challenges reshaping the workforce include the lack of local talents, high attrition rate and retention of talents.
Businesses look for alternative solutions to solve manpower shortages. Many fast-tracked initiatives and fuelled the incorporation of automation to maintain business continuity. According to the PwC's Global Crisis Survey 2021, 95 per cent of businesses globally have prioritised transformation in the top three areas; mainly operation, IT infrastructure and technology. This creates another concern, employees are threatened by the rapid adoption of emerging technologies, fearing that they will be out of step with progress without the latest skills.
Cobots are friends not foes
With employees' fear of being replaced by technologies, and the constant labour shortage, manufacturers are caught between a rock and a hard place. They are navigating between the space of either investing in automation or hiring talents to increase production output. However, unlike the prejudices from
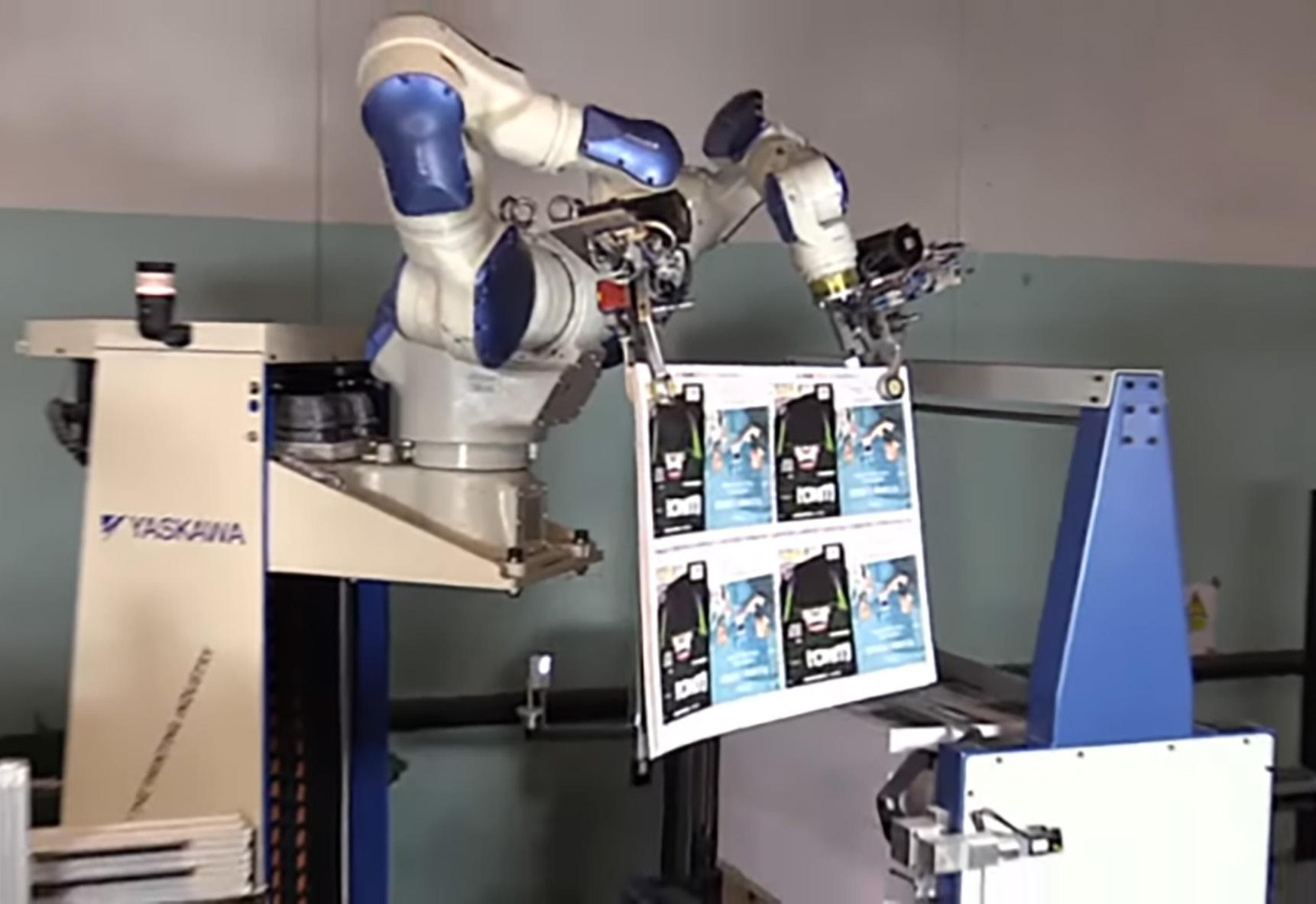
https://fujifilm-gcb.info/FBNZ_Revoria
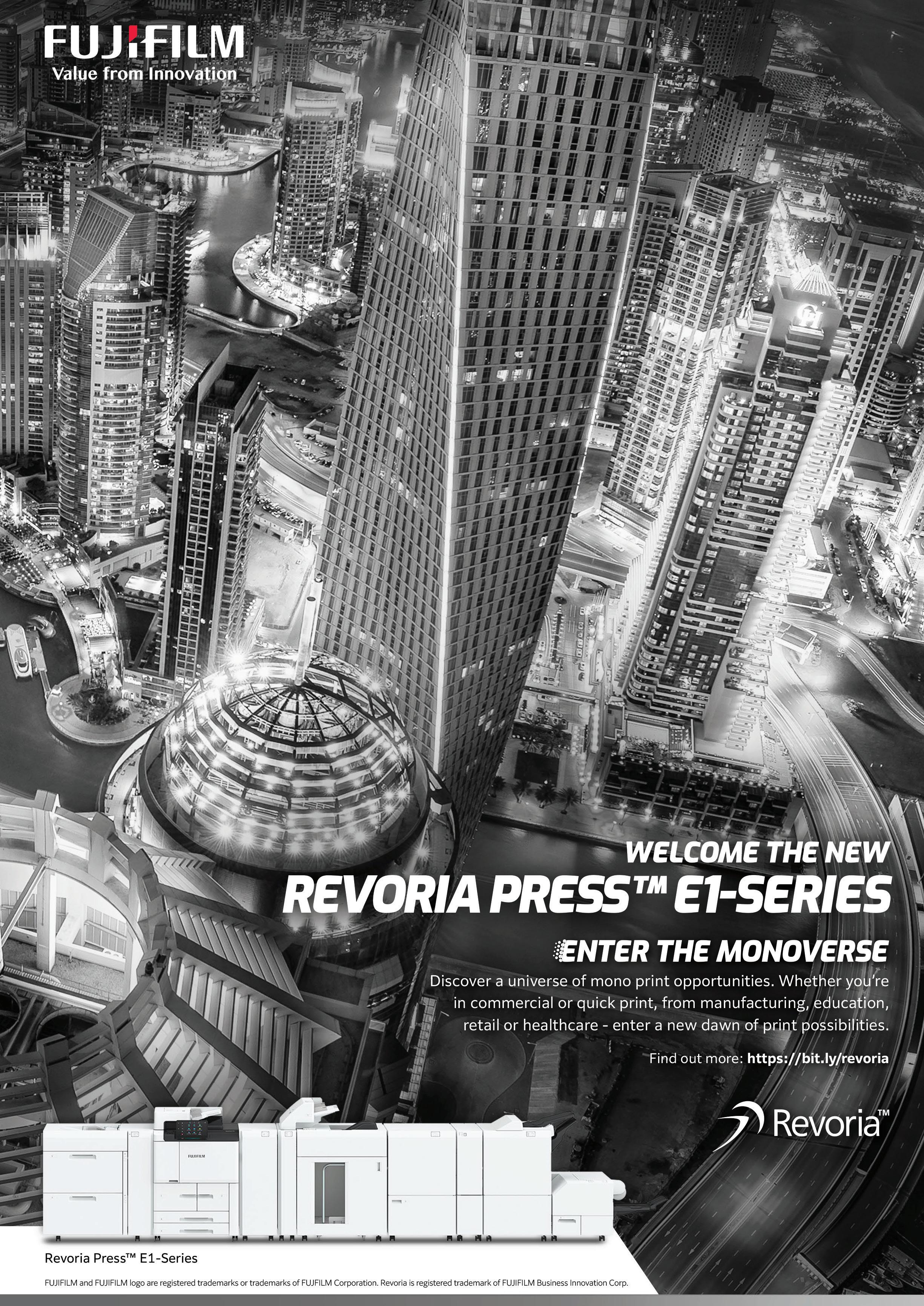
people, automation or specifically, robots may not be ushering a job-pocalyse after all. Cobots step in to tackle the repetitive, heavy and unpleasant tasks, much like a useful and highly productive tool for human workers. The increased output and revenue of the company may create more job opportunities, with better career advancement prospects for human workers.
Employees with little to no robotics or programming experiences can easily operate a cobot. The deployment of cobots relieves human workers to work on high-value tasks, provides upskilling opportunities as employees shift from working on dull and dirty tasks to programming cobots and monitoring their performance, carving out new skills and career advancement opportunities for them.
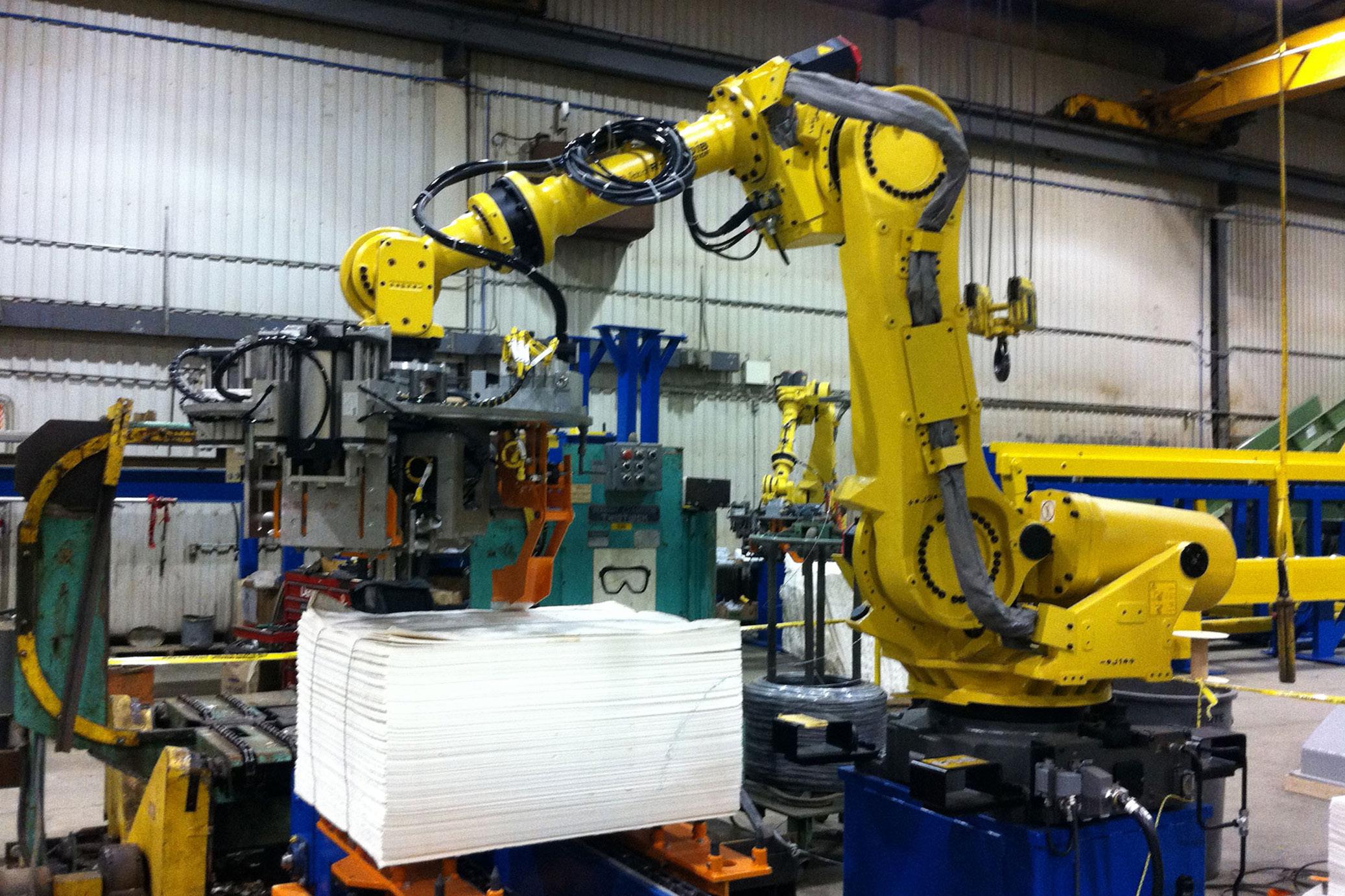
Cobots have become a solution for manufacturers that require a costeffective and space-saving solution to curb manpower shortages and retention challenges.
Addressing labour shortages with cobots
Craft And Technik Industries (CATI), an automotive component manufacturer in India deployed a UR (Universal Robots) cobot to solve manpower challenges and decrease the number of product rejects at its plant. Considering that tasks were completed manually, customer rejections due to faulty components were common before the implementation of UR cobot. Additionally, CATI was facing challenges searching for manual labour.
After installing a UR cobot, which loaded and unloaded a vertical CNC machine and performed automatic inspections, CATI had witnessed an increased efficiency and increased production volume of 15 to 20 per cent with no defects or customer rejections.
Another company that addressed labour shortages by installing UR cobots in its production line was PLC Industries. The Singapore-based service provider in precision engineering was faced with a shortage of skilled labour, coupled with rising material costs. With the deployment of two UR10 cobots, the company have boosted production output by 40 per cent and further increased product variety.
In response to global disruption, the manufacturing industry has changed. Manufacturers are planning ahead, finding ways to take their perceived disadvantages and turn them into advantages. They are working smarter and making modest automation investments with cobots to address labour shortages and retain employees at the same time. Future manufacturers will be embracing cobots as the perfect companion for both employees and employers, shifting into a new work environment.
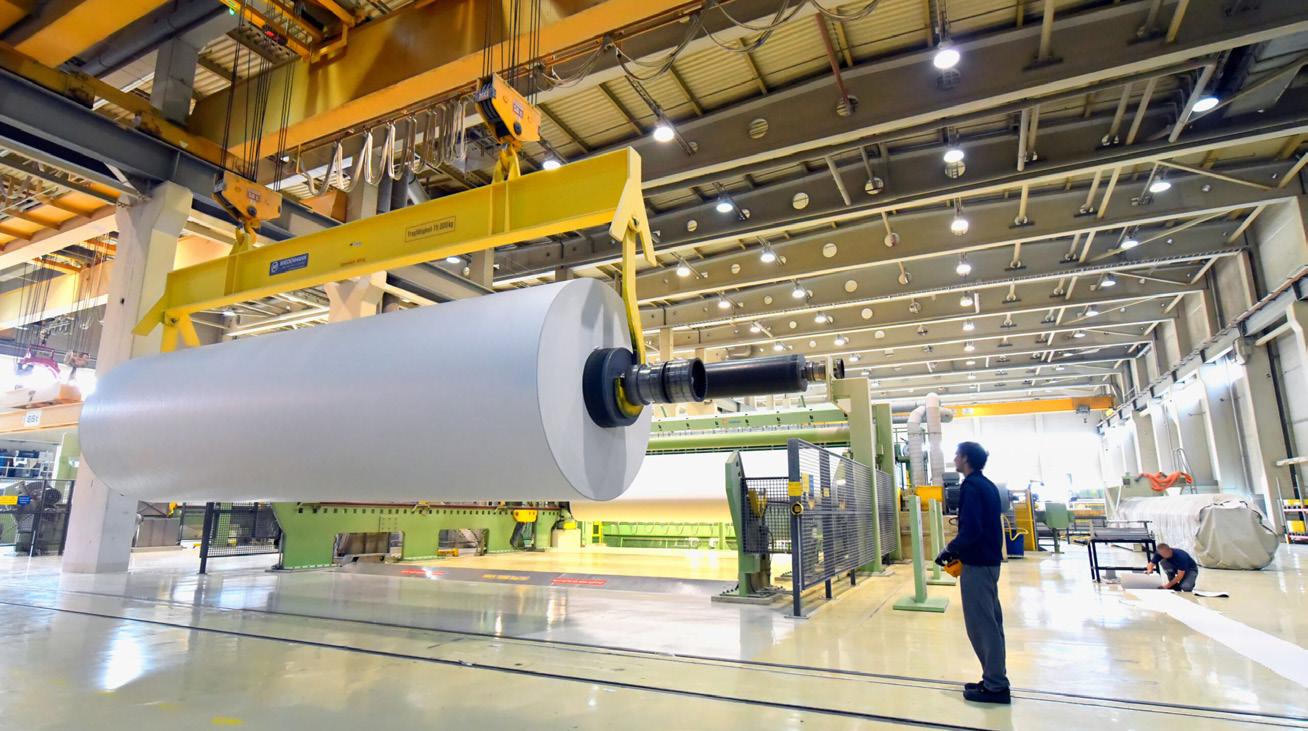
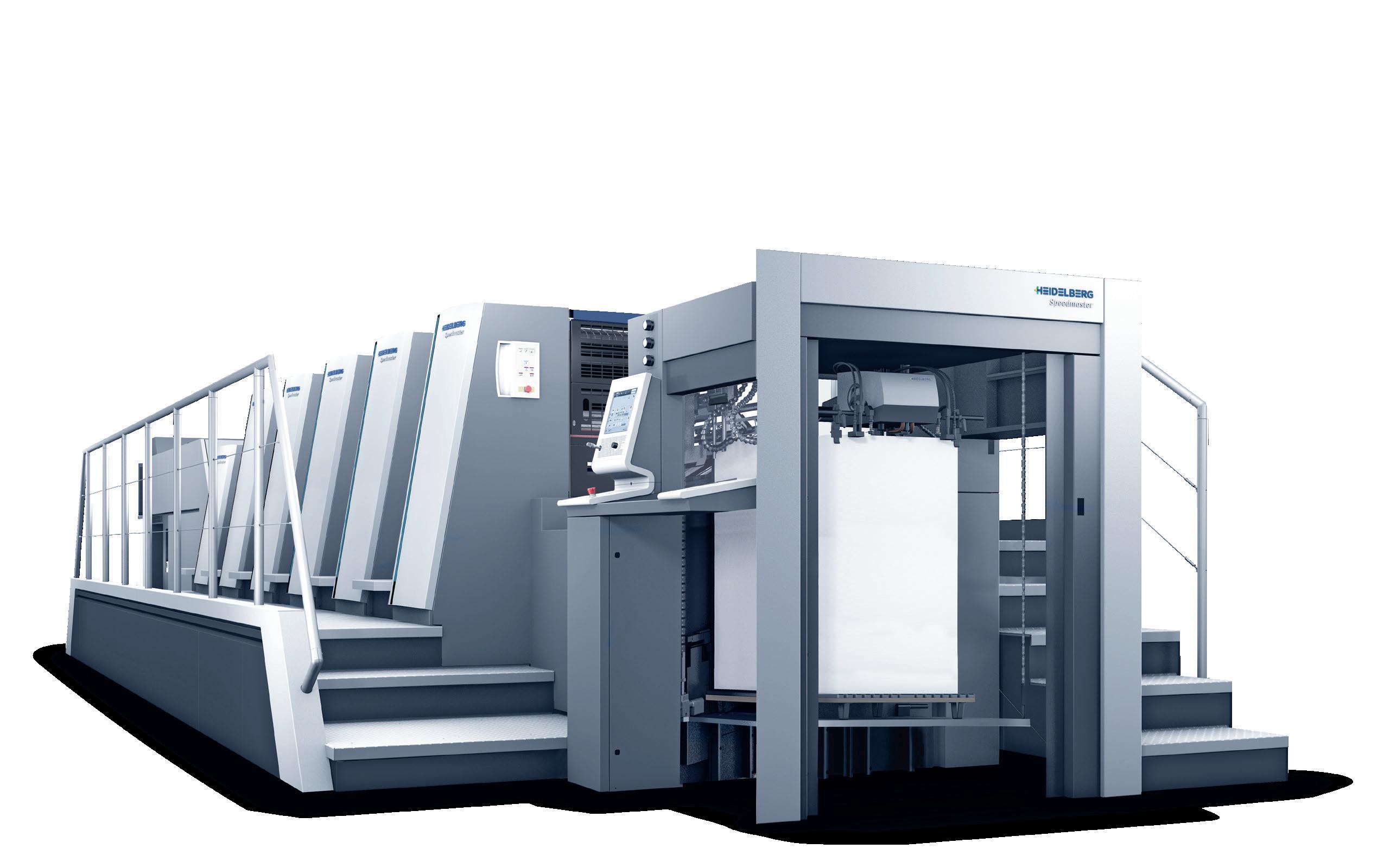
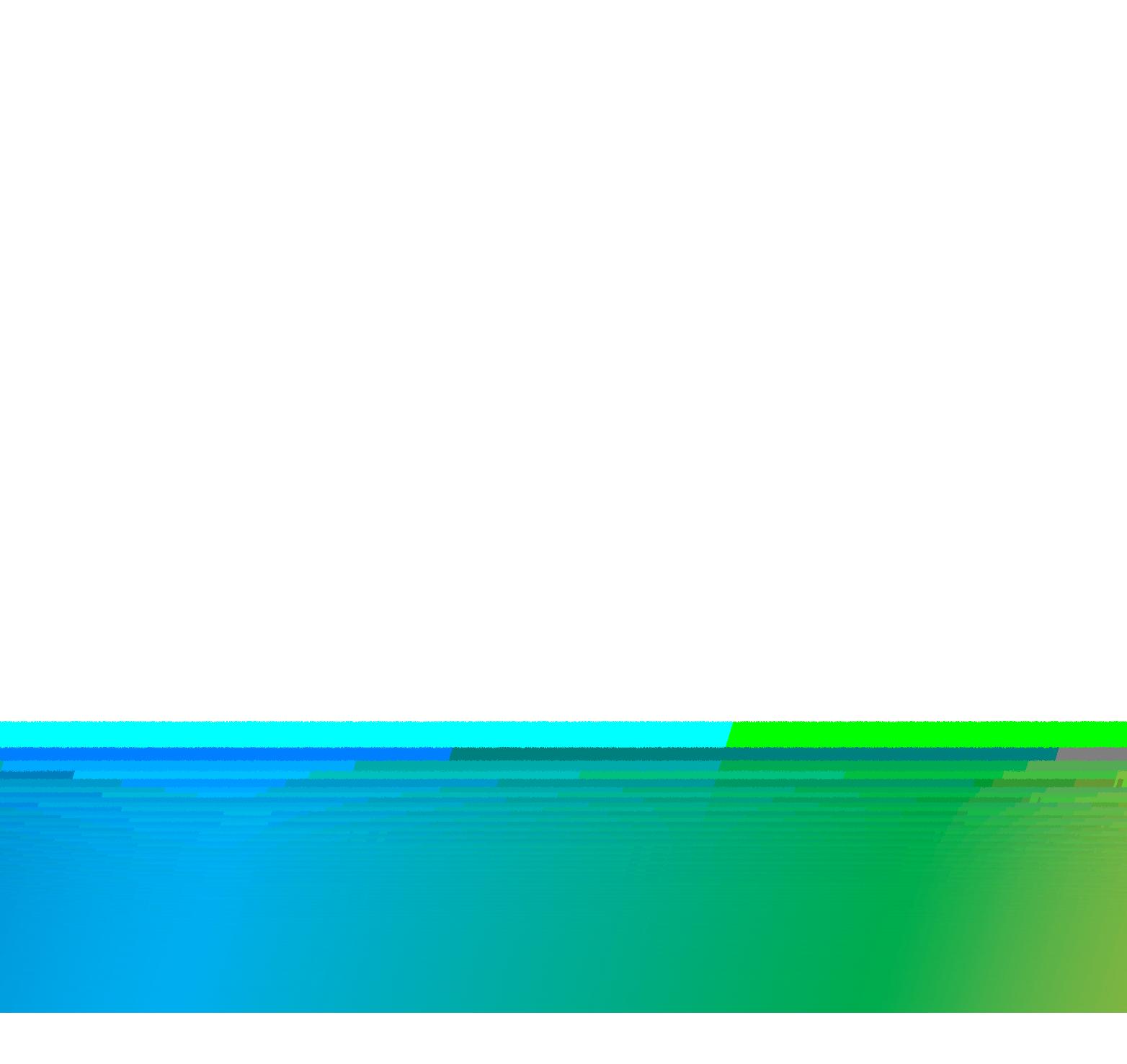
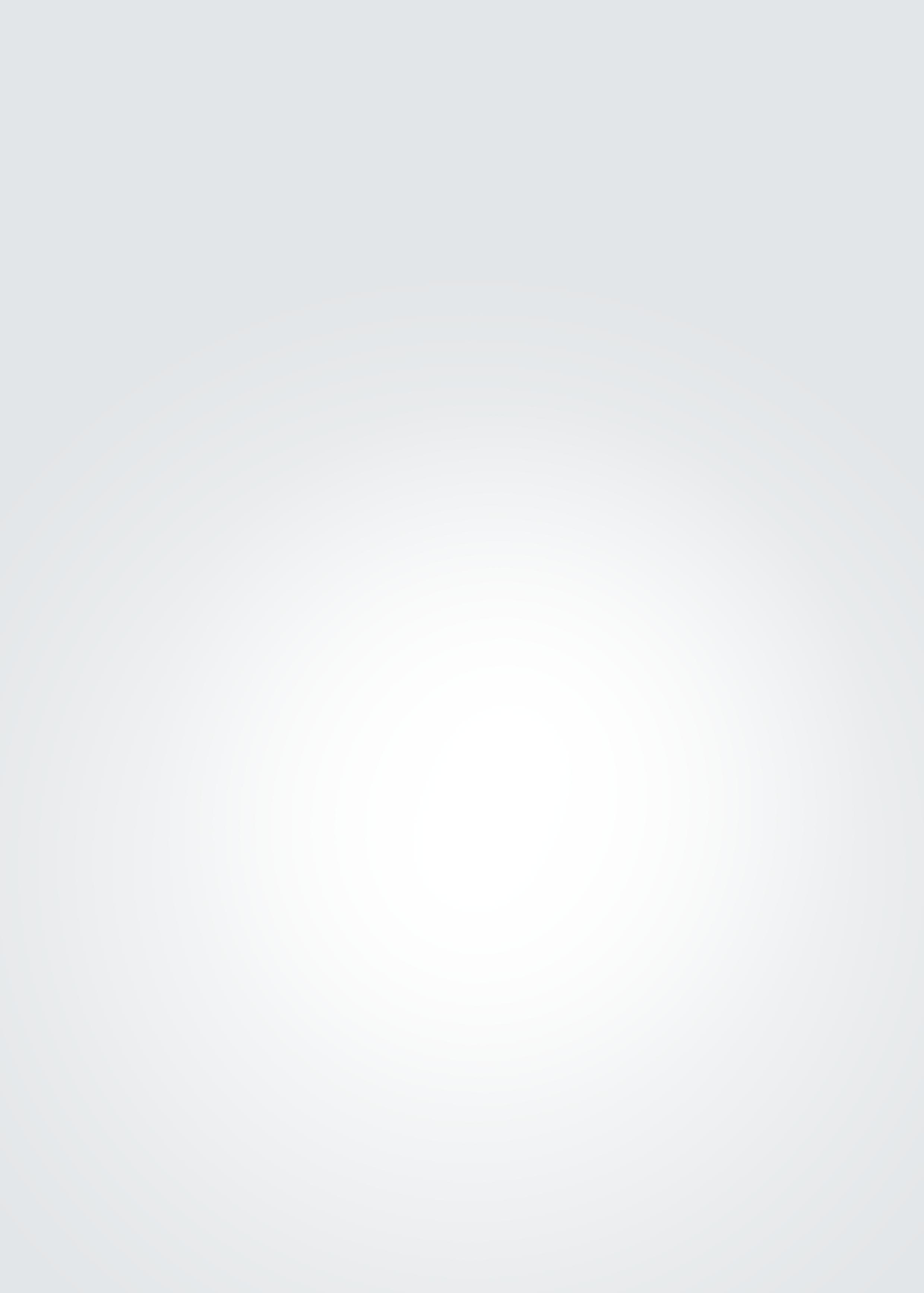