
7 minute read
Heidelberg leads in the packaging market in ANZ
COVID- 19 Created a lot of uncertainty in the commercial printing sector, but not in packaging. The last 24 months has seen a phenomenal increase in sales of new presses primarily add on equipment to companies across Australia and New Zealand.
Market Dynamics
A combination of factors has seen a massive increase in packaging printing throughout not only Australia and New Zealand but also throughout the World. With Covid and severe lockdowns an increase in food packaging has seen packaging print volumes increase dramatically, added to this has been the pressure to shift away from plastic packaging to cardboard which has also led to further increases in print volumes.
In addition to the success in the commercial market Heidelberg Australia and New Zealand has or will also install 6 hi tech packaging presses 3 of which are for the IML market and 3 for board packaging. The 3 packaging presses are raised and feature the latest technology.
• XL106-6LYYLX – 6 colour with double coaters and Logistics • XL106-7LYYLX – 7 colour with double coaters and Logistics • XL106-7LYYLX – 7 colour with double coaters and Logistics • XL106-7+L with CutStar at a highquality label printer • CX102-6+L with CutStar at a highquality label printer • XL106-D rotary die cutter
Plan ahead
Australia and New Zealand are not the only markets with increased demand, North America, Japan, Korea, and many countries in Europe have also stepped up their sales dramatically. It used to take up to 6 months to make and ship a press to most countries but with capacity in Germany at and queued processes. Intelliguide simulates the time-optimized sequence live and, if necessary, also includes the steps to be executed manually.
Plate loading systems
• Auto plate XL a complete plate change in less than one minute. • Auto plate pro plate changing in approximately two minutes. • Auto plate allows for plate changing in 40 seconds per printing unit.
Drying system Heidelberg DryStar©
Fully flexible drying solutions are available for individual application requirements. • DryStar • DryStar LED UV • DryStar UV • DryStar LE low energy
Logistics
For continuous high volume packaging printing, Heidelberg logistics systems are tailored for maximum output and material movement.
Prinect Inpress Control 3
The latest generation of colour measurement system enables fully automated colour and register control for make ready on the job change over. Prinect Inpress Control 3 has a new algorithm for waste sheet reduction during make ready.
recent record levels manufacturing times are out to 6-8 months and with international shipping now delayed you could wait for up to a year to become operational.
Switching to Heidelberg
One of the largest packaging printing companies globally who have for a number of years been using Heidelberg Speedmaster VLF presses in the USA and Europe have for the first time purchased a Heidelberg press in New Zealand. The press is a Speedmaster XL106-6+LYYLX with smart technology including Fully Automatic Logistics, Push to Stop autonomous features and with double coating capability.
Technology makes the difference
Heidelberg customers are enjoying record breaking performance thanks to the addition of the latest Speedmaster XL 106 technology 2020 generation. With the continuous development and improvement of the Heidelberg peak performance models, productivity and output KPIs are being exceeded globally.
Speedmaster XL 2020 generation
Key innovations and features:
Push to Stop fully automated production processes
For the first time, navigated printing with Push to Stop is possible on all Speedmaster machines. The patented Intellistart 3 defines all the steps required for the job change without any operator intervention and provides maximum transparency across all active
Operating system Prinect Press Center UX
Heidelberg UX is the holistic and intuitive operation of all Heidelberg touch points.
Heidelberg leads in the packaging
Speedmaster XL106 – Higher Performance
Intelligent assistants and a uniform user interface reduce complexity and simplify production processes.
Customized solutions for the packaging sector
A global trend also evident in Australia is the number of installed customized presses is growing. As many as 20 printing and coating units with interdeck and end-of-press dryers as well as multiple cold foil modules can be installed in one sheetfed offset printing press from Heidelberg. Here a Speedmaster XL 106-2+LYY-P8+LYY-1+L with 2 FoilStar cold transfer modules for efficient inline finishing of the inside and outside of folding cartons.
In a trend that has been emerging for a long time now, a growing number of print shop customers are demanding printed products with sophisticated coatings and special effects. This development is particularly striking in folding carton and label printing, with branded goods manufacturers aiming to generate a steady stream of new purchasing incentives through the use of particularly effective, stand-out packaging designs. However, print shop customers in the commercial segment also want to run their marketing campaigns with custom-designed print products that stand out from the crowd thanks to striking and sophisticated coatings and special effects.
At Heidelberg these market requirements are being met by presses with increasingly long custom configurations and a wide variety of equipment.
The general market recovery is also being clearly reflected in the demand for customized machines. The trend toward print products with increasingly sophisticated surface finishing is still growing and is boosting the profitability of branded goods manufacturers and print shops in equal measure.
Impression counts
Increased volumes = High output – It has now become common place for high volume packaging printers to produce 70 million impressions per year this volume is unbelievable when you consider most companies will run their machines for between 10 and 15 years. Total volumes when machines are being traded out can easily have between 700 and 1.2 billion impressions and that is before the machine is resold and starts it life again in a secondary market. Records Tumble Fort Dearborn, a custom label and packaging company with twenty locations nationwide, reached nearly 82 million impressions on its Heidelberg Speedmaster XL 106-8+L in 2020. This high level of productivity was especially critical to Fort Dearborn’s success as demand at grocery stores due to COVID-19 surged.
To produce so many impressions annually require a well-built machine that is reliable and is supported by the largest technical network in the World. Uptime is critical to continuous printing as is the ability to monitor the equipment remotely
Predictive monitoring
Heidelberg’s predictive monitoring and remote service diagnostics makes it possible to deliver high uptime availability of the press. This is achieved through continuous data collection. With predictive monitoring, the system records and monitors up to 500 million data records per year. The System algorithms detect irregularities and propose predictive measurements to prevent failures.
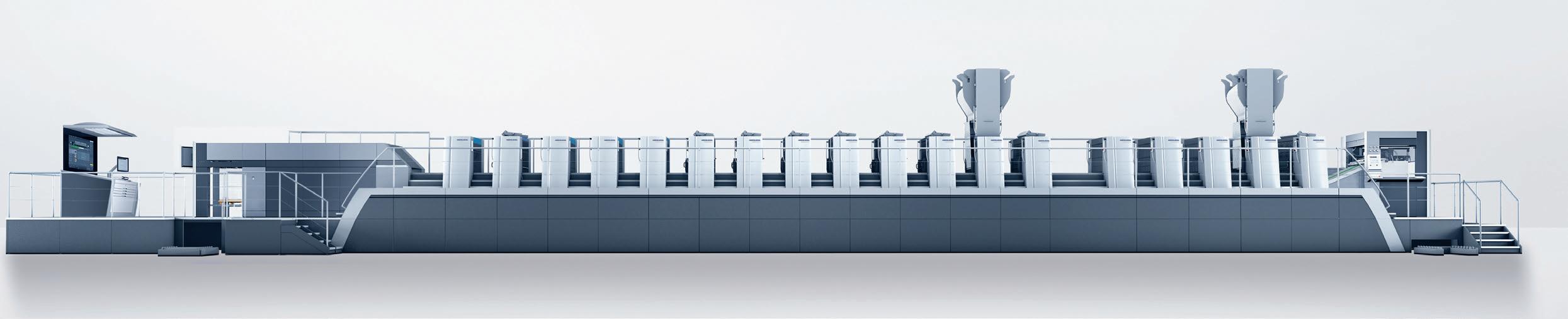
Heidelberg expert creates an intelligent task list and plans execution: • Remotely • Next planned visit • Immediate on-site call (exception)
Full reporting is possible via regular monthly data reviews, service reports or with regular phone conferences.
Masterworks Die Cutters continue their growth
8 Years after the partnership was formed Heidelberg and Masterworks in 2014 have enjoyed great success selling the Diecutters and folding box gluers with over 500 machines being sold. Since 2013 Masterworks has sold over 3,000 diecutters internationally. Both packaging and commercial printers have benefited from the competitively priced machines.
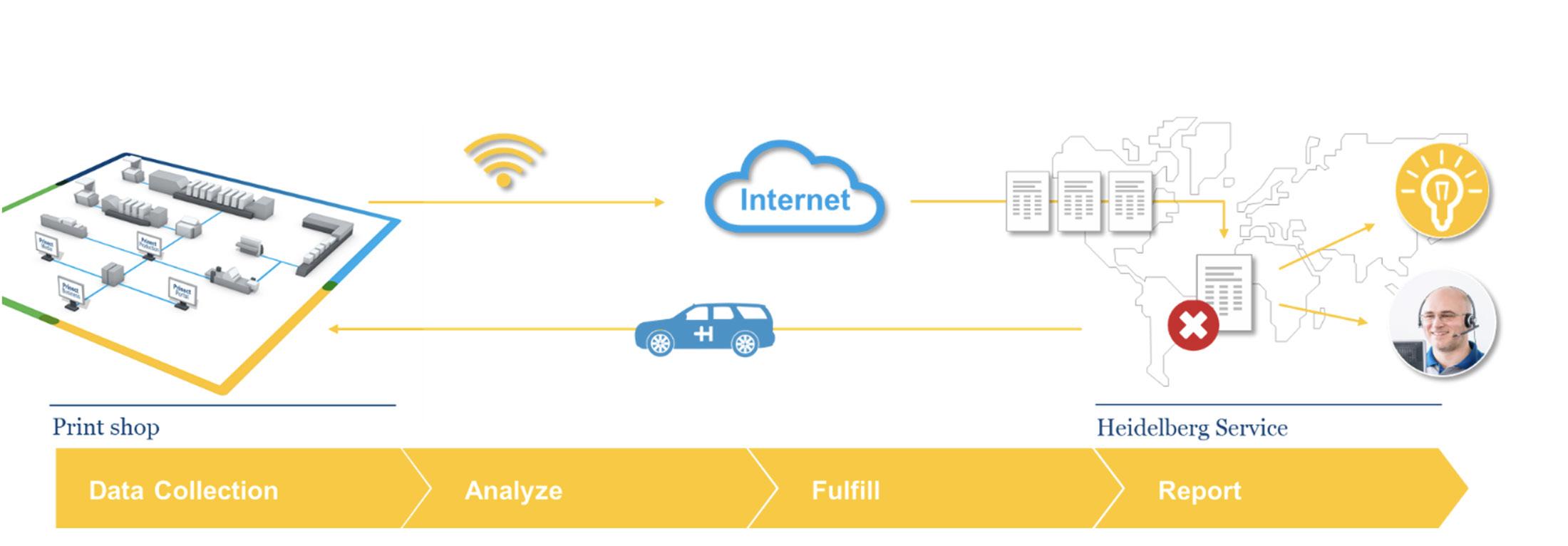
Safety and technology
The Geprüfte Sicherheit ("Tested Safety") or GS mark indicates that the equipment meets German and, if available, European safety requirements for such devices, including operating procedures. The GS mark confirms that the compliance with the European safety requirements has been tested and certified by a state-approved independent body. The GS mark is based on the German Product Safety Act ("Produktsicherheitsgesetz"). GS certification is voluntary.
Models to suit all applications
From the simple diecutter right through to the fully equipped machine with stripping and blanking Masterworks offers a comprehensive range of machines to suit the market demands. Masterworks even offers a machine (Duo Press) that can foil as well as Diecut, strip and blank all in the one pass.
Folding Box Gluers
To complete the box manufacturing process the Internationally renowned folding box gluers formally known as Jagenberg. The product series “Diana” is existing since 1958 and high-speed Diana folder gluers (with 600m/min. belt speed) were already introduced in the late 1980s by Jagenberg.
The new generation Diana X 115 model, Heidelberg integration of first folder gluer with single servo drives was launched on Drupa 2008.
Heidelberg through its partnership with Masterworks has sold and installed over 142 folding box gluers worldwide and continues to build on its reputation as a total solution provider.
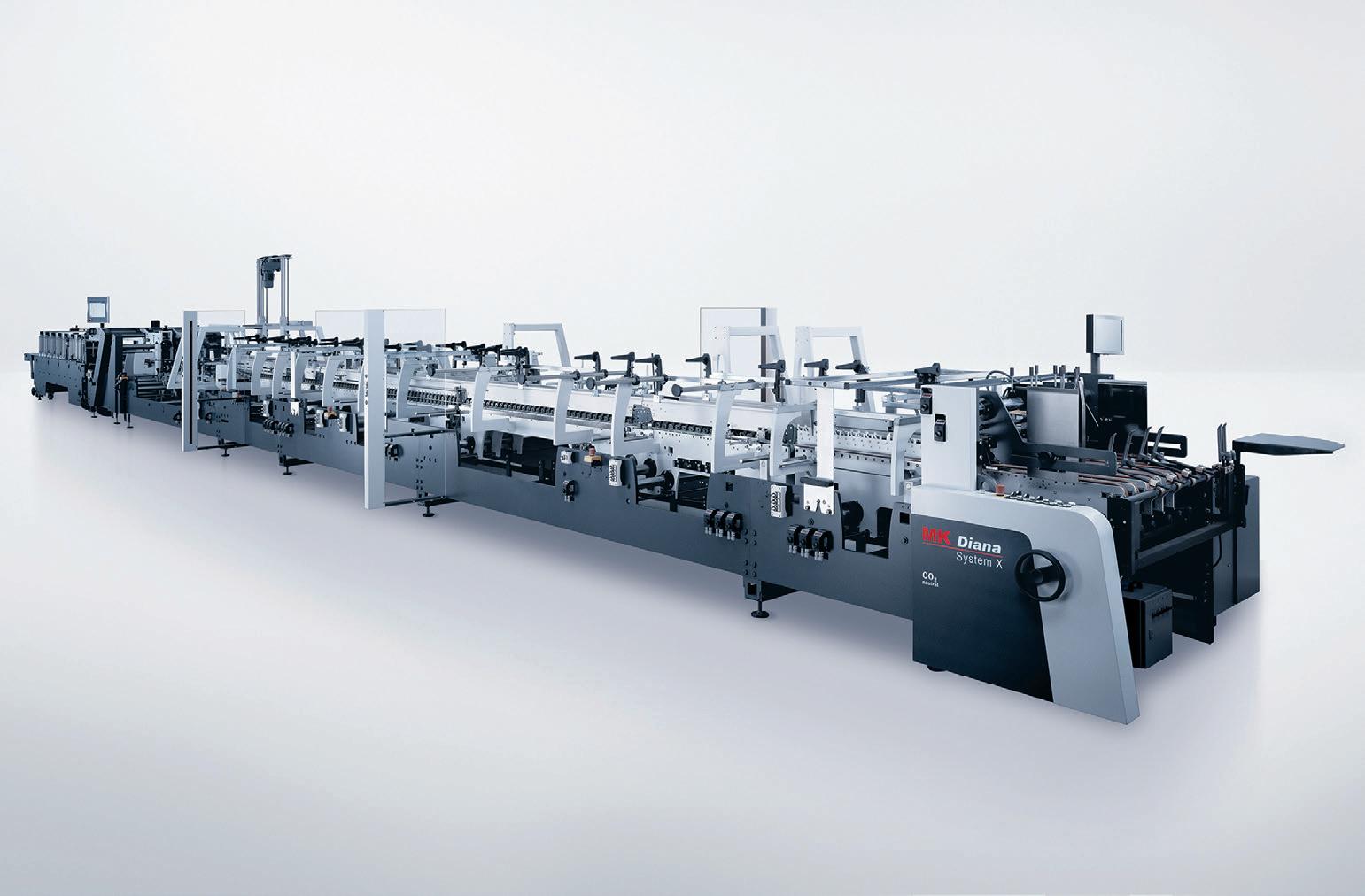
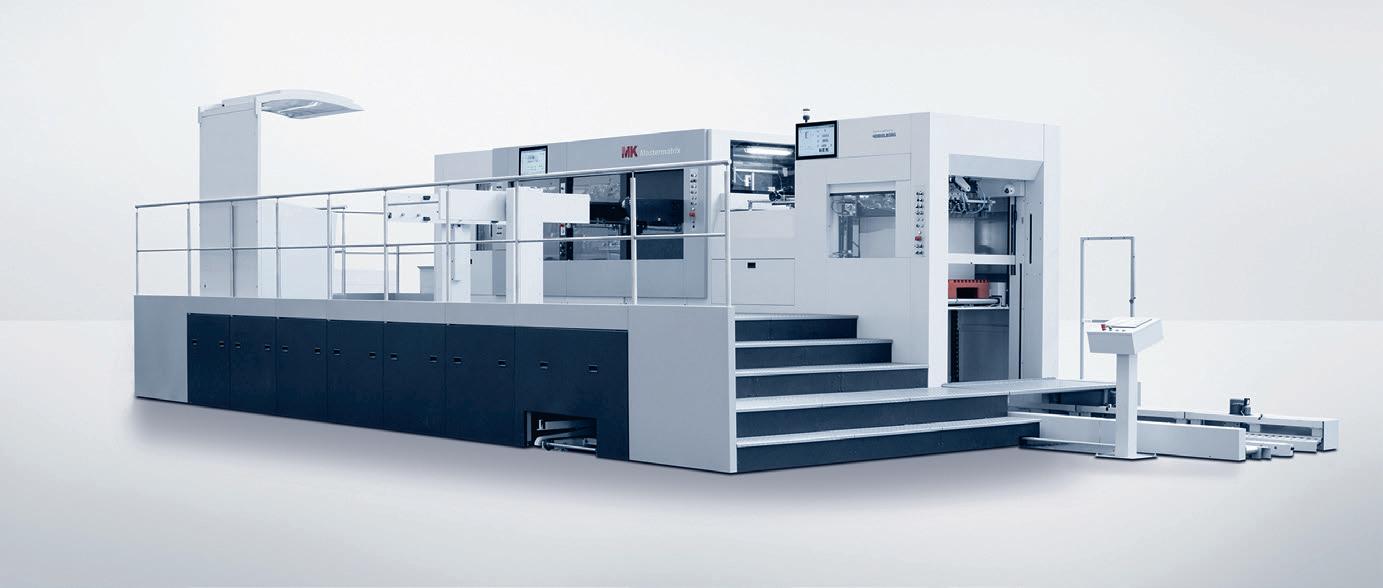
Heidelberg is well positioned to supply and support turn key solutions to the packaging and label sectors. From sales consultancy to software solutions, machinery, after sales service support as well as a full consumables product range. This strong portfolio places Heidelberg firmly in the leading position as the partner of choice in Australia and New Zealand.
