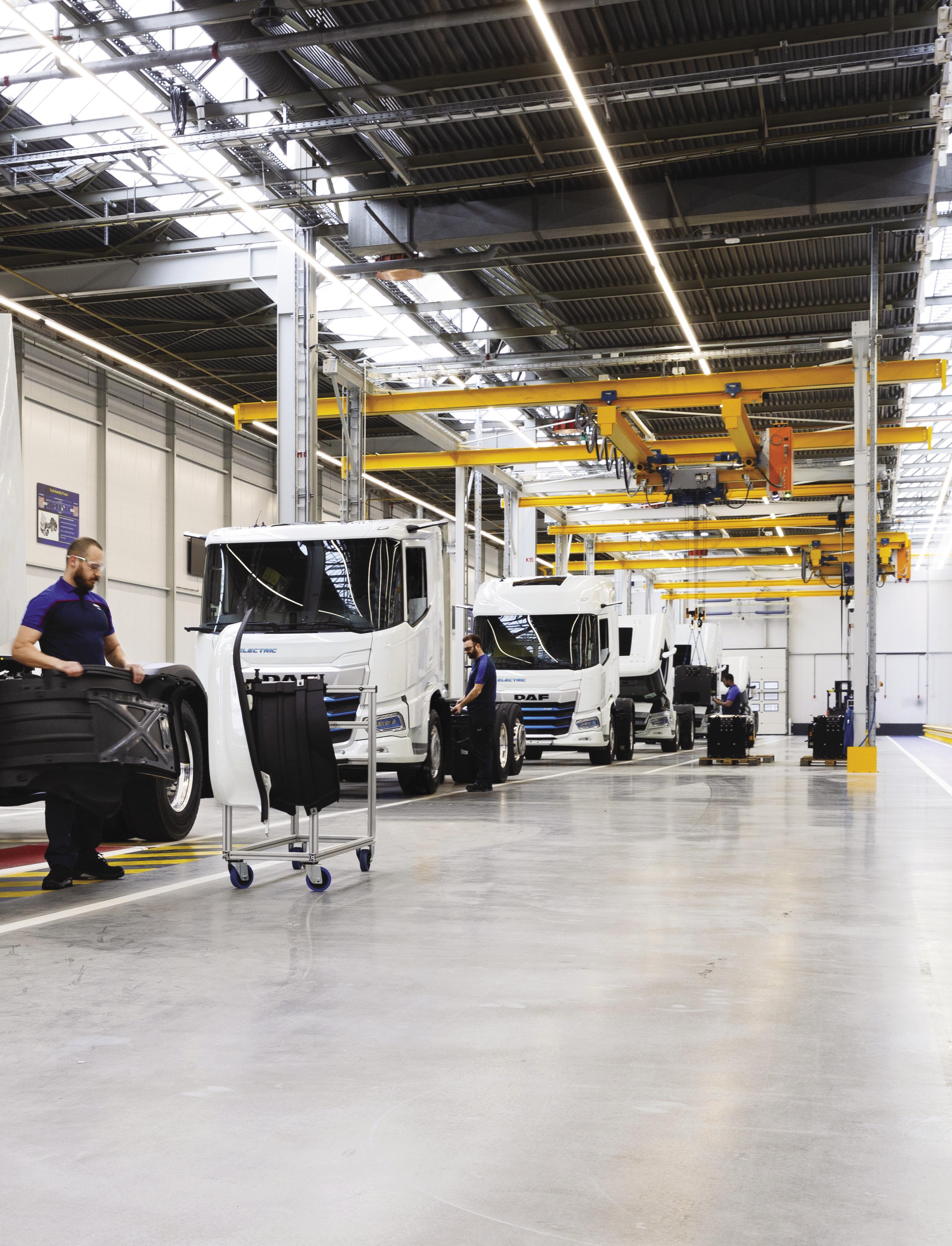
1 minute read
EXCLUSIVE
Ahead of the formal opening of the BEV facility, DDM gained exclusive access coupled to a personal guided tour by Jeroen van den Oetelaar, who is responsible for manufacturing strategy across all of DAF’s European assembly operations.
The all new Electric Truck Factory is in itself a fantastic example of environmental consideration and recycling as the building has been repurposed from what was originally a parts-distribution warehouse.
To say the operation is state of the art is an understatement, importantly safety is a paramount concern, PACCAR even created their own safety standards regarding the assembly of BEV vehicles, whilst conforming to ISO 26262 (ISO 26262 is an international functional safety standard for the development of electrical and electronic systems in road vehicles).
High-voltage assembly areas are protected by fences. To add an extra dimension of safety, the entire production area is protected by 24-hour surveillance including camera and smoke detection, all of which is connected to DAF’s own Fire Service.
The chosen battery technology is LFP (Lithium Iron Phosphate) with all batteries on site kept at a low rate of charge to minimise risk.
The batteries are configured in modules which are assembled in-house, with three modules forming one 105 KWh pack. Depending on range and use, vehicles can be specified with two to five battery packs giving 210KWh-525KWh.
Vehicles arrive from the main assembly line as rolling chassiscabs. Although they are specified as BEV at the point of order, they follow the same assembly process on the line as diesels to the point they become a rolling chassis-cab, when they are diverted to the new assembly facility.
A large proportion of the BEV-specific element of vehicle manufacture is completed as sub-assemblies. The EDM (Electric Drive Module), which is the main control element including an auxiliary battery, is assembled before being installed under the cab where the traditional engine would have once lived.
Motive power is supplied via an E-motor which drives a threespeed transmission and a standard drive axle.
Whilst in the vehicle assembly process within the BEV facility each vehicle is fitted with a removable and very heavy-duty pull bar, so in the unlikely event of an emergency, the truck can be removed from the production line immediately by the on-site emergency services and placed in a 14 x 3.3m steel box, that is locked and the vehicle completely submerged. This emergency vehicle-removal process was completely developed in-house.
The all new facility is set up to produce 2000 vehicles per annum, showing that DAF are already ahead of the market in relation to demand.