
5 minute read
LIFT OFF
A big crane on a relatively small chassis brings great adaptability for the operator and equally big challenges for the installer, and considering this is a UK first for DAF, it’s a pretty impressive effort.
Words: Courtesy of Commercial Motor magazine
Photographs: Karl Hopkinson a natural progression for the company and this DAF XG arrived in January 2023, fresh from its Fassi crane installation by Mac’s Trucks.
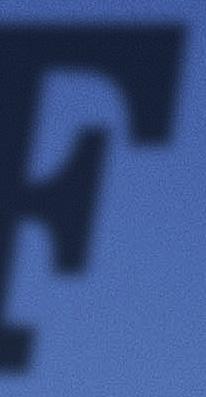
DAF XG 530 6x2 Tractor Unit
This New Generation DAF XG 530 6x2 tractor unit is in the FTS axle configuration with driven second axle and tag-axle rear. Although less common than the 6x2 mid-lift, it is ideal for this crane application. Firstly, the crane’s position bears the majority of its weight onto the drive axle, which is ideal for traction particularly as this XG operates predominantly as a solo mobile crane rather than an artic – its demountable body carrying a moderate payload in place of any imposed trailer load upon the fifth wheel. Secondly, the physical size of the 3-axle tractor makes it a lot more manoeuvrable than a rigid 8x4 chassis, for instance, which would generally be the more likely choice for this size of crane. Moreover, it features a 10,000kg capacity front axle, which is particularly useful in this application. Powered by DAF’s 13-litre MX-13 390 unit, it can call upon 530hp at 1,675rpm and 2,700 Nm of torque from 900rpm to 1,125rpm in the highest ratio of its TraXon automated transmission. It also boasts a torque plateau of 2,550Nm across 900rpm to 1,400rpm. All in all, that’s not a bad specification for your first ever truck!

The Operator
“Yes, this is our first truck,” says Jeremy Powell. “Admittedly it’s probably a bit unusual for it to be something like a DAF XG 530, but it really came about as a logical progression.”
PWL Contracts grew, like so many small companies, from a one-man operation. Jeremy Powell, found he was working more regularly with other one-man bands on bigger and bigger jobs, so setting up his own company was the next move. “We had none of our own transport or crane,” Powell explains. “Parts would be delivered to site, the hired-in crane would be in place, and we would then carry out all the installation, but with crane hire costs being so great, any delays would result in big costs, and for some of the rooftop jobs, a 60-tonne mobile crane sometimes needed road closures too.”
So the DAF artic means PWL is now self-sufficient in transport and crane work. “Pretty much,” Powell smiles. “We were originally going to look at a Volvo 8-wheeler, but some of the sites are so tight the 3-axle is much better. We essentially use it solo as a mobile crane, but it’s opened so many possibilities, being a tractor unit.
“We are looking to hire a trailer for de-commissioning work when the steel towers or rooftop installations have to be taken away, while the demountable body gives us just about all the carrying capability we need to site,” he confirms. It is that adaptability that marks out the DAF/ Fassi combination, but it’s a huge investment for a small company. “We have it on a six-year finance deal,” says Powell. “It doesn’t do huge mileages, probably 30,000 miles per year, so it’s a long-term investment.” “It will create more work for itself, I’m sure. We are also an abseiling company, so we are looking at potential window work, where we can lift window units to several floors up with the crane, and abseil down to fit them in. The remote control would be a boon here, as it is with rooftop work. The conventional crane’s operator cannot see onto the roof and is working purely from verbal instructions over the radio, but to be able to operate the crane from the rooftop is a big advantage in ease and safety.
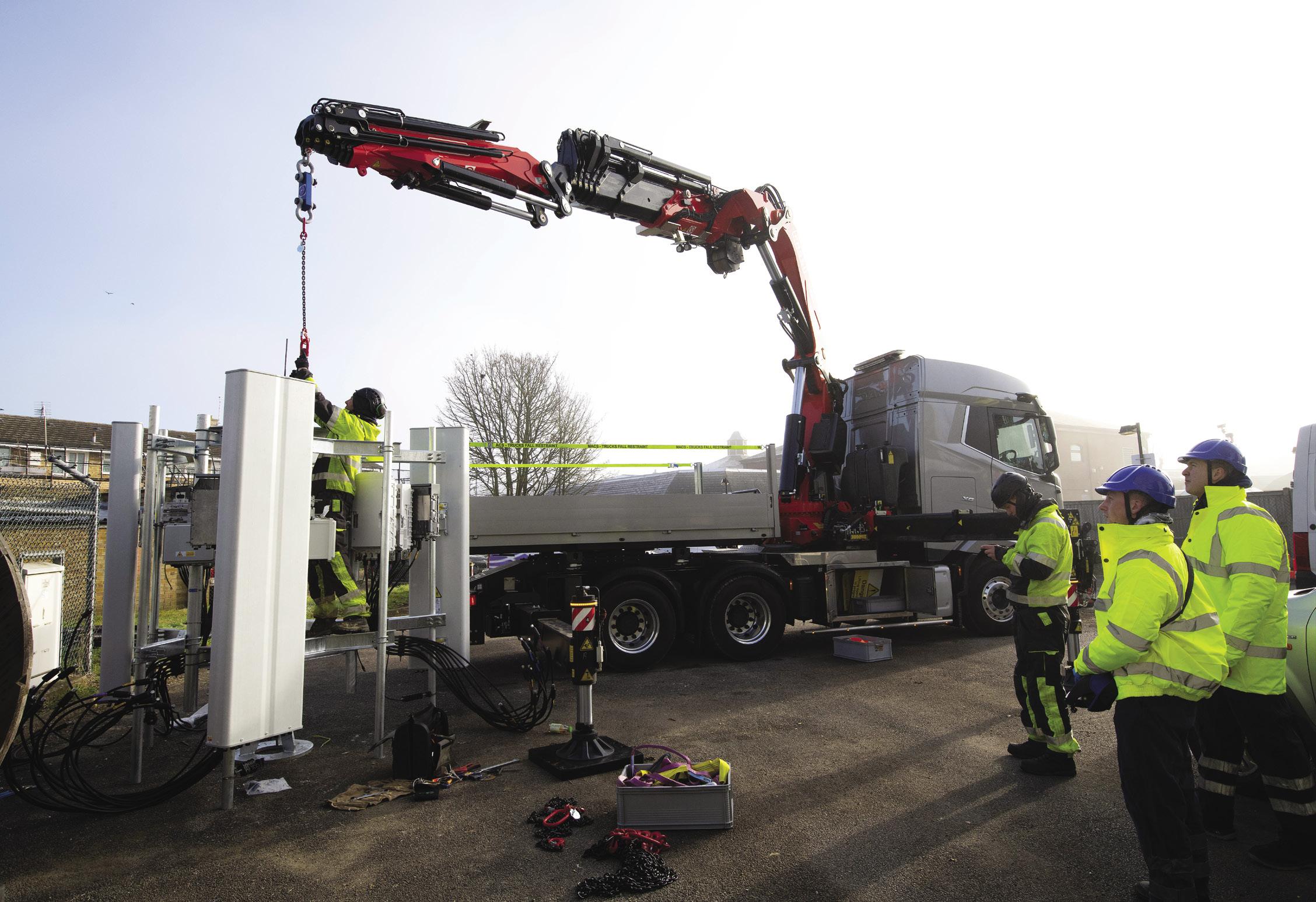
The Fassi F820 RA 2.26 xhe is an impressive piece of kit in anyone’s book. Rated at 82-tonne/m, it offers a total reach with its extendable L516 fly-jib of 33.5m. Moreover, where hard-bitten building and construction crane operators think of the limit of reach as being the point at which it can still handle a nominal 1-tonne load, the F820RA boasts 945kg at some 28.1m. The crane’s high angle means that 33m of reach equates to a vertical point more than 31m above the chassis, ideal for the rooftop installation and removal jobs with which it is generally tasked. This one is also equipped with the optional winch, widening its scope to full crane capabilities aside from the arm’s inherent dexterity, all of which makes the traditional lorryloader nomenclature akin to damming by faint praise for these sophisticated units. It’s all radio remote-controlled too, with myriad warnings and preventions for plain overload, reach and balance, with a continuous 360-degree capability taking account of the imposed loading limits to rear, side or forward stabiliser units. It also just happens to be the largest crane ever fitted to a 3-axle DAF tractor in the UK.
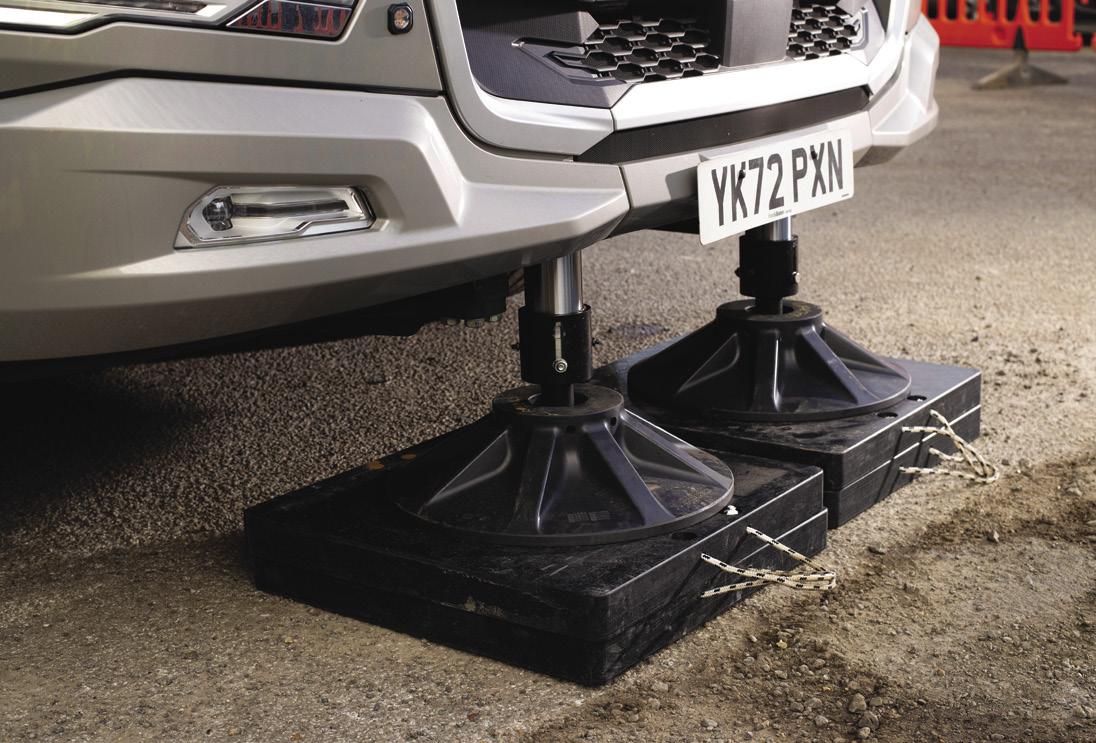

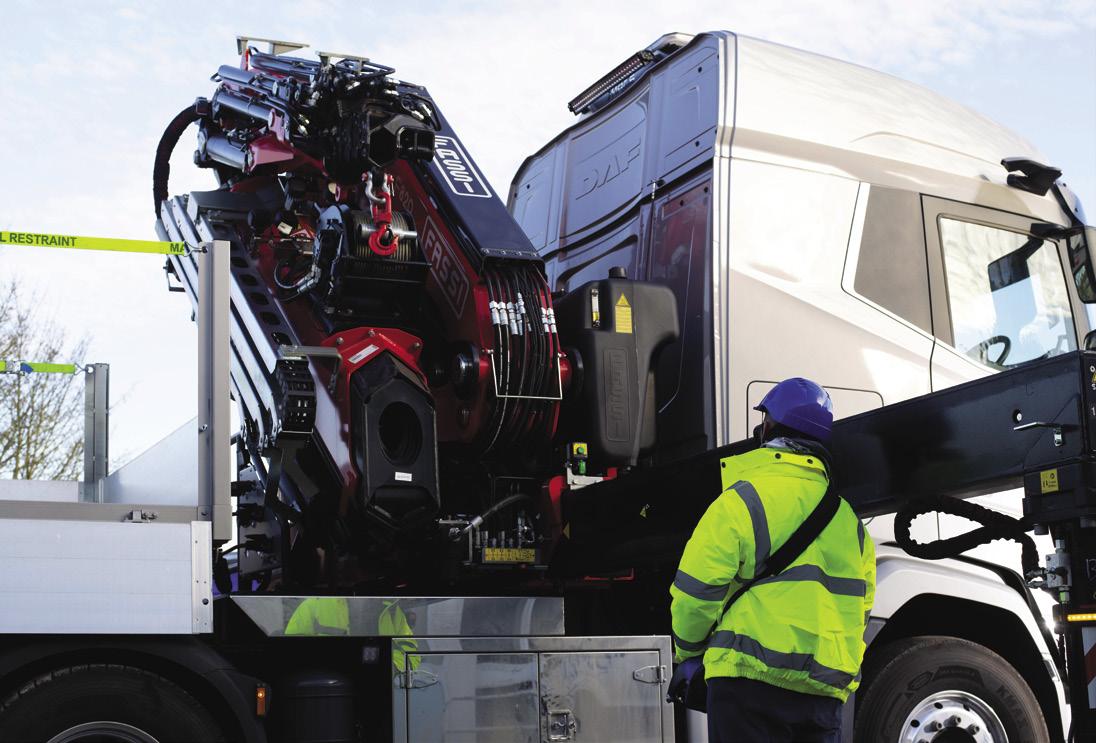
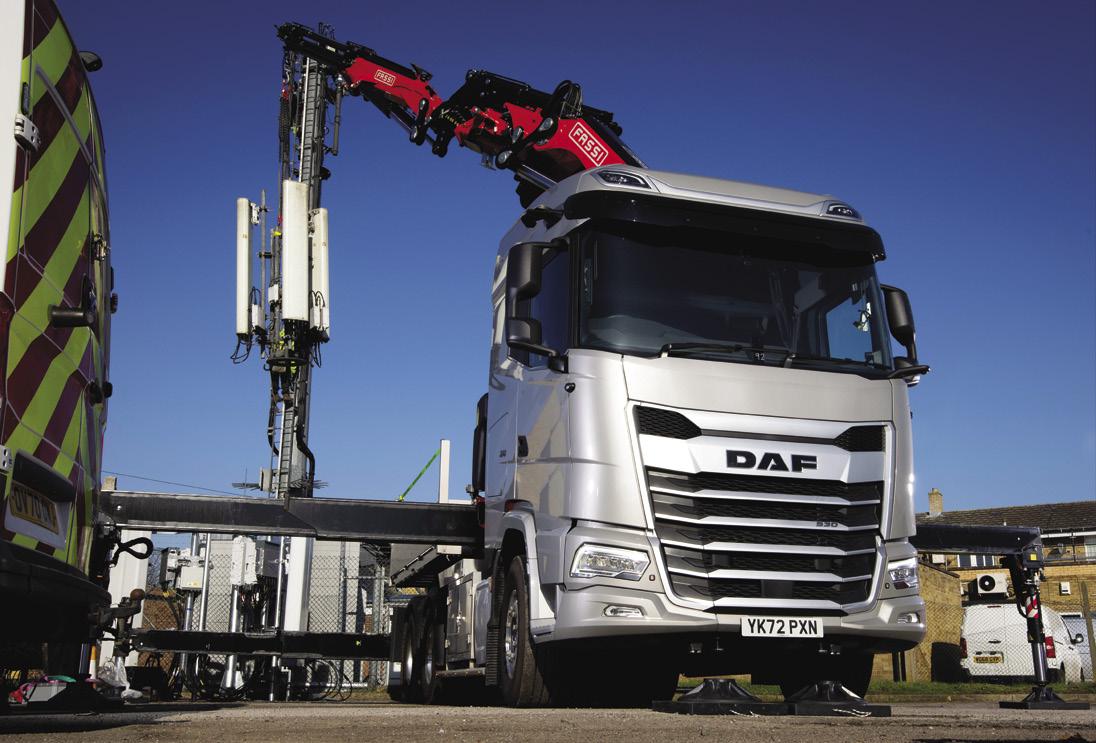
The Builder
Mac’s Trucks was first established as a truck dealership in 1973, but over the last 10 years or so it has become one of the UK’s leading lorry-crane installers. Its build and installation facility in Huddersfield has eight crane fitting bays in constant use, and the company installed around 240 cranes last year, and is looking at a likely 300 units during 2023, making it the most prolific installer of Fassi cranes in Europe.
“This one was particularly interesting,” says Mac’s Technical
Director Andy Hall. “Normally, we’d expect to see a crane of this size on a 6x4 or 8x4 rigid chassis, rather than a tractor unit,” he admits, with the New Generation DAF XG cab giving Hall and his team a few more interesting aspects to deal with. “These new DAF cabs are very deep, which on an 8-wheel rigid would not be such a problem, but on a tractor we were very tight on space, especially with such a big crane, for the chassis,” he explains. The DAF XG’s much-vaunted aerodynamic efficiency of cab design also needed to be considered. The front support unit which mounts into the front chassis cross-member is usually positioned ahead of the front bodywork, protruding slightly ahead of the vehicle’s bumper line, but on the XG this was not acceptable.
Supporting act
“We were determined we were not going to affect the aerodynamics of the
XG cab,” explains Hall. “This meant that the front support unit had to be mounted behind the front grille, yet obviously without impeding the airflow itself.” The DAF’s axle layout was more favourable to this build, however, since a steering or lifting second or third axle layout would bring increased complexity to the chassis equipment, while the second-drive, third-tag axle configuration is (slightly) simpler. Essentially this was Mac’s prototype build for this size of crane on a 3-axle DAF tractor, so everything had to be bespoke built.
“The two main issues were the short chassis and the aerodynamics of the cab,” confirms Hall, and although tight for space, stabilisers, hydraulic reservoir and the piping, all had to be accommodated on the sub-frames once installed without encroaching on the truck’s original chassis fittings. Likewise the demountable load/tackle body, sitting over the fifth-wheel coupling. However, more than the engineering challenges overcome, Hall is most proud of the two members of staff who were most involved with the build. Both came through Mac’s Truck’s apprenticeship scheme. Gabe Hall, who at 24-years- old is a qualified crane examiner, carried out all the programming of the control system, setting up the crane and demonstrating it to the customer, whilst 21-year-old Thomas Graham, a plater/ welder, was responsible for the subframe mountings and the front support system, which had to be concealed behind the XG’s grille.
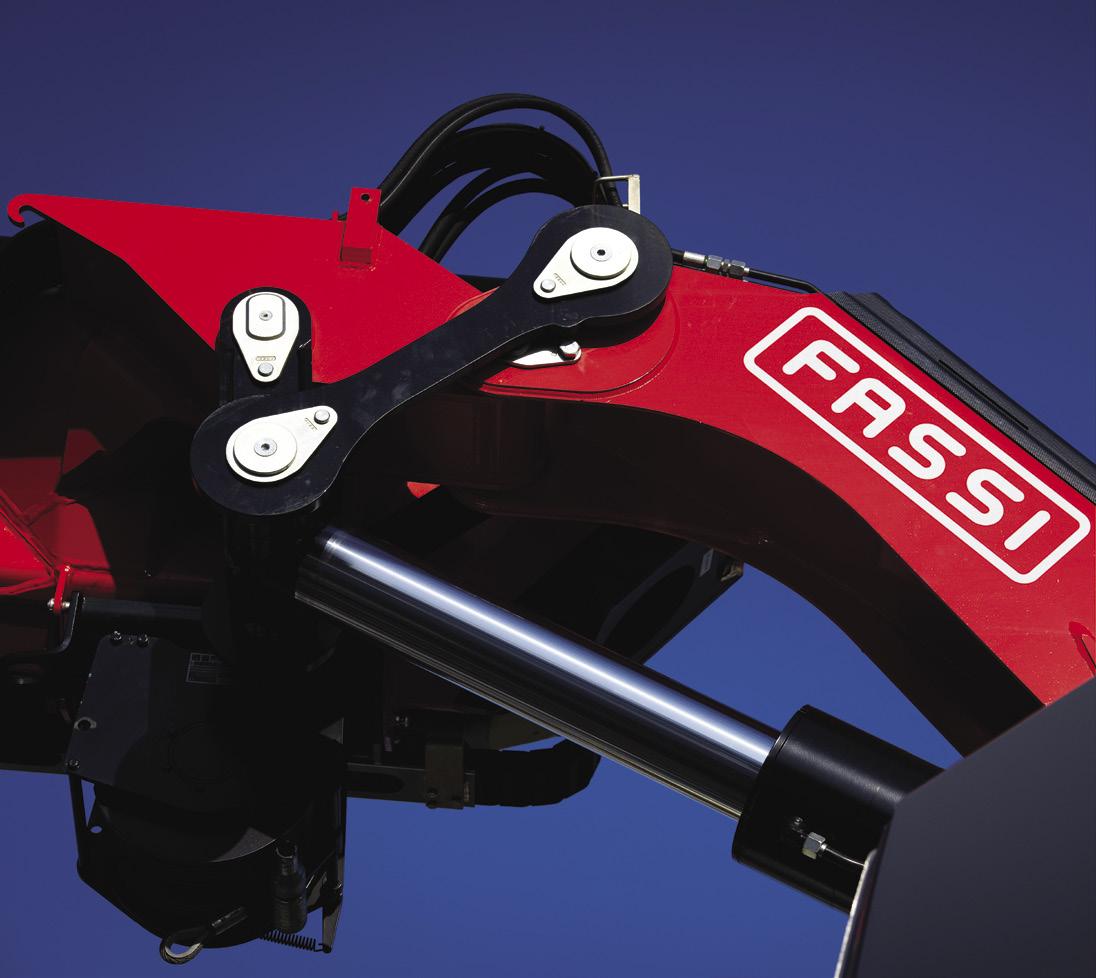

“It’s great to see these lads coming through as apprentices and taking on the big projects, problem-solving and building their confidence. Learning on the job is the only way to achieve that,” Hall states.
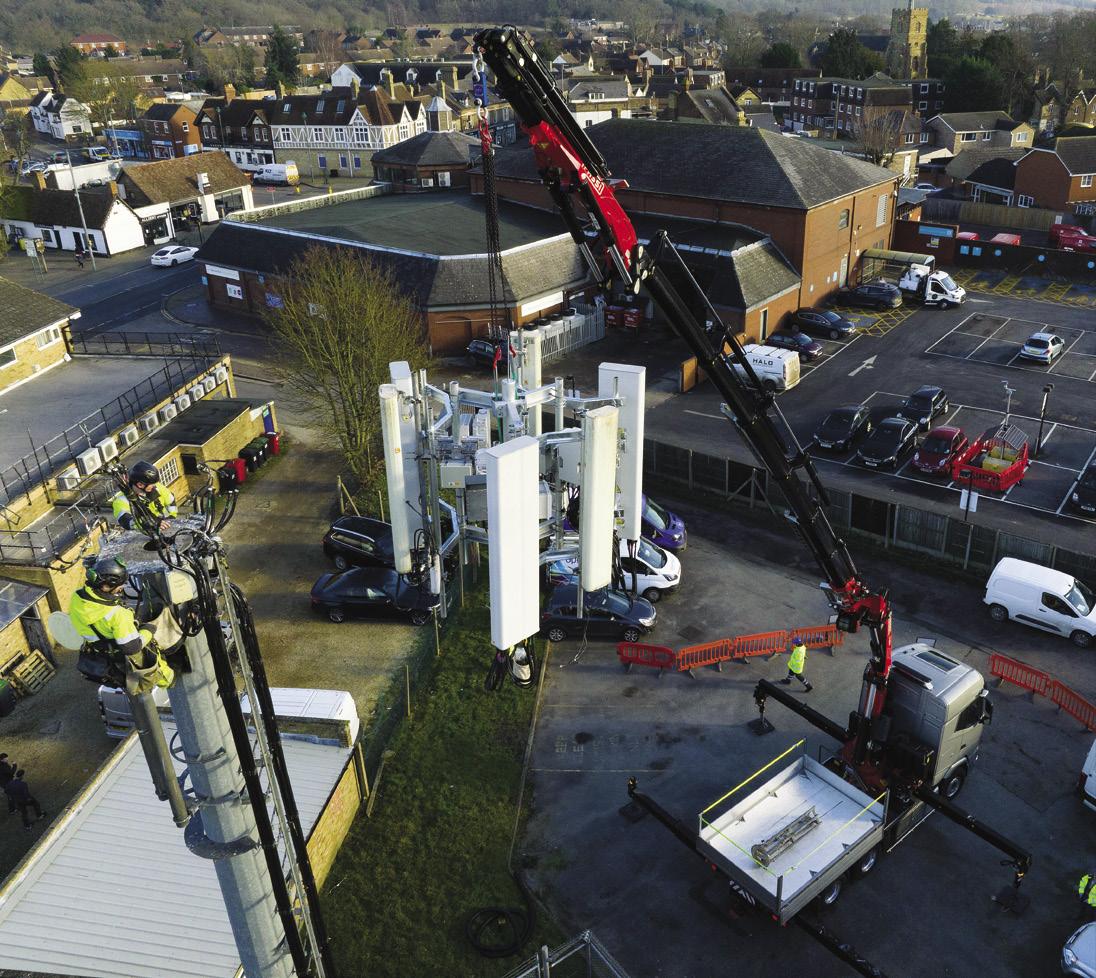
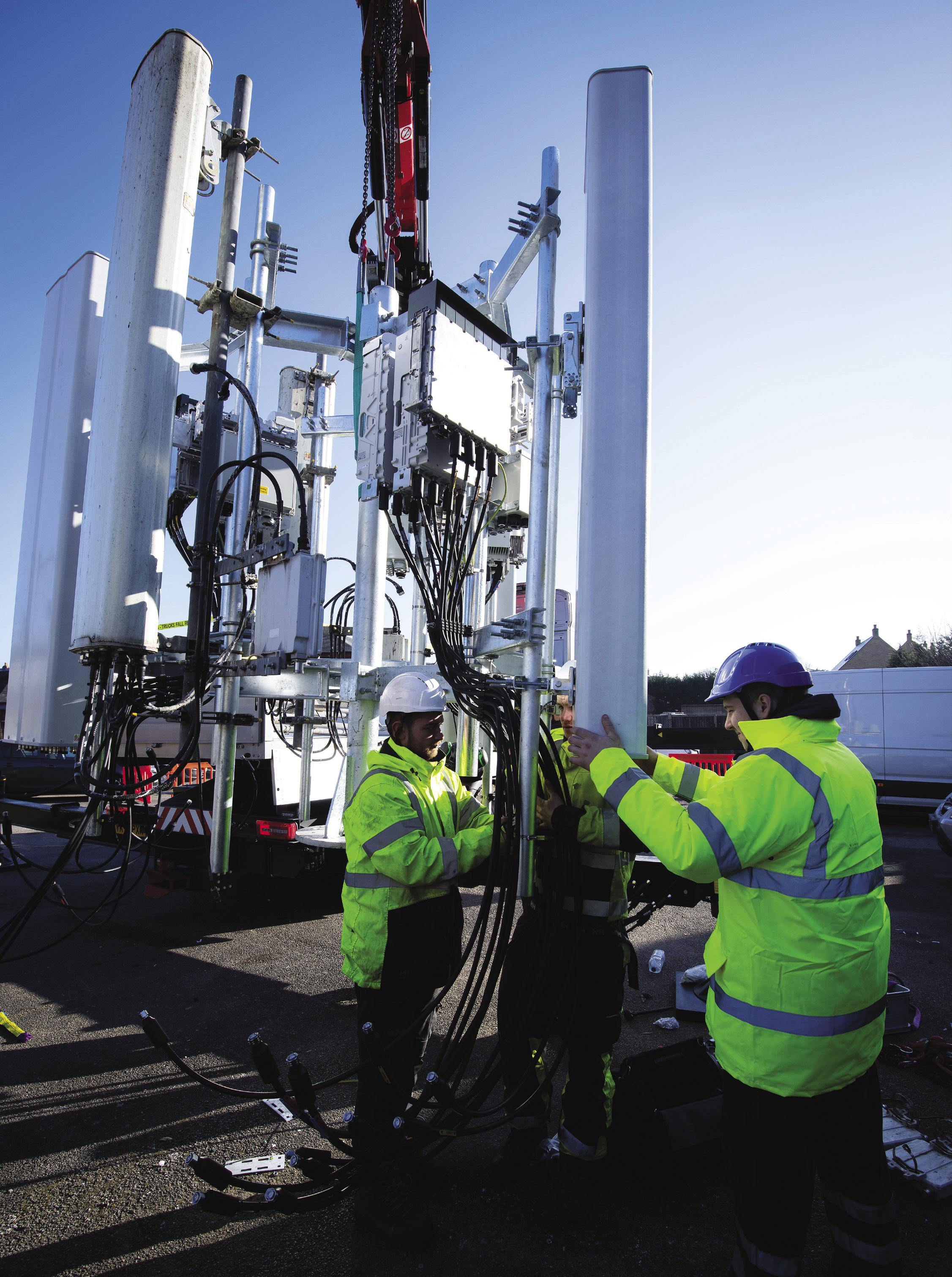