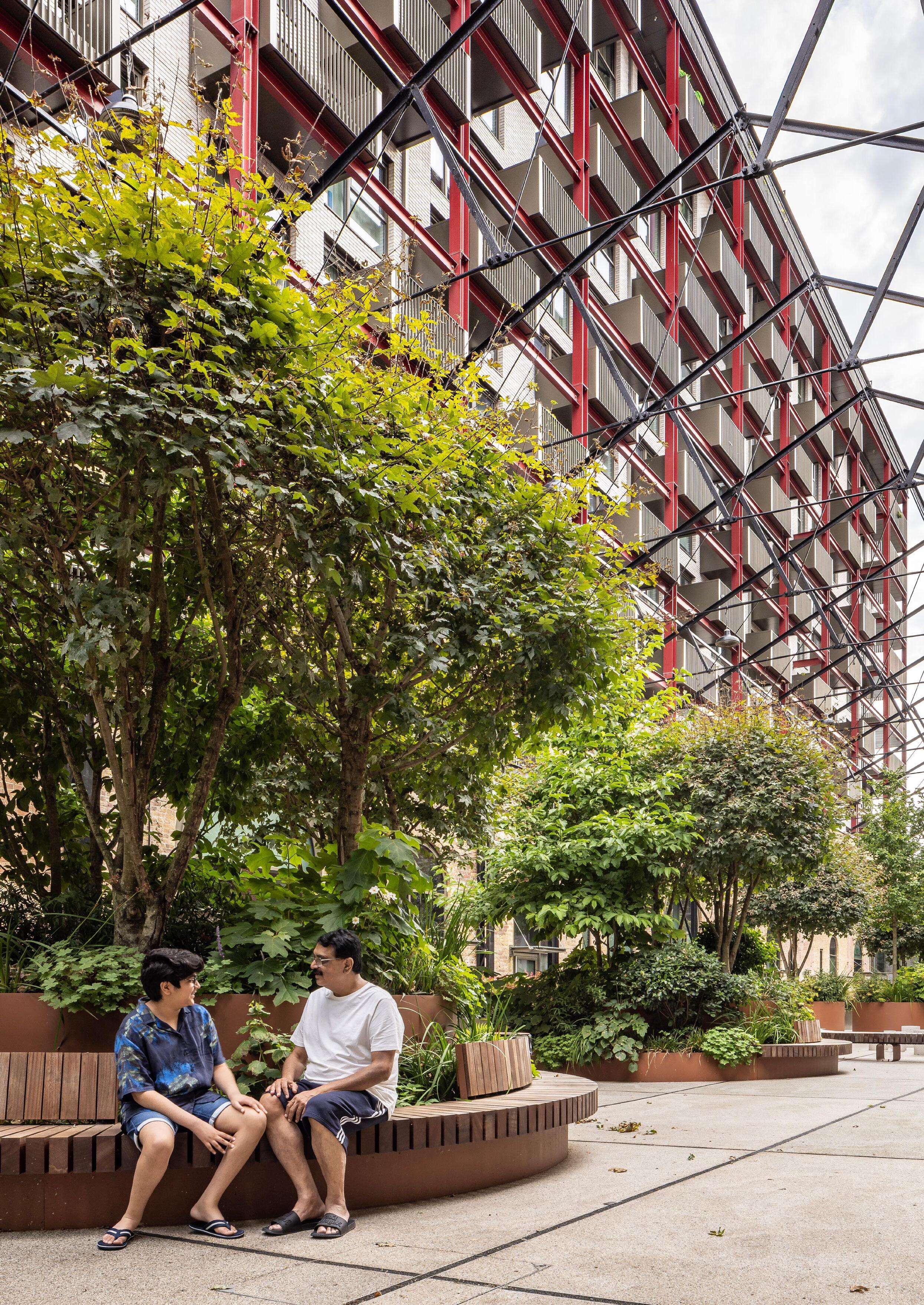
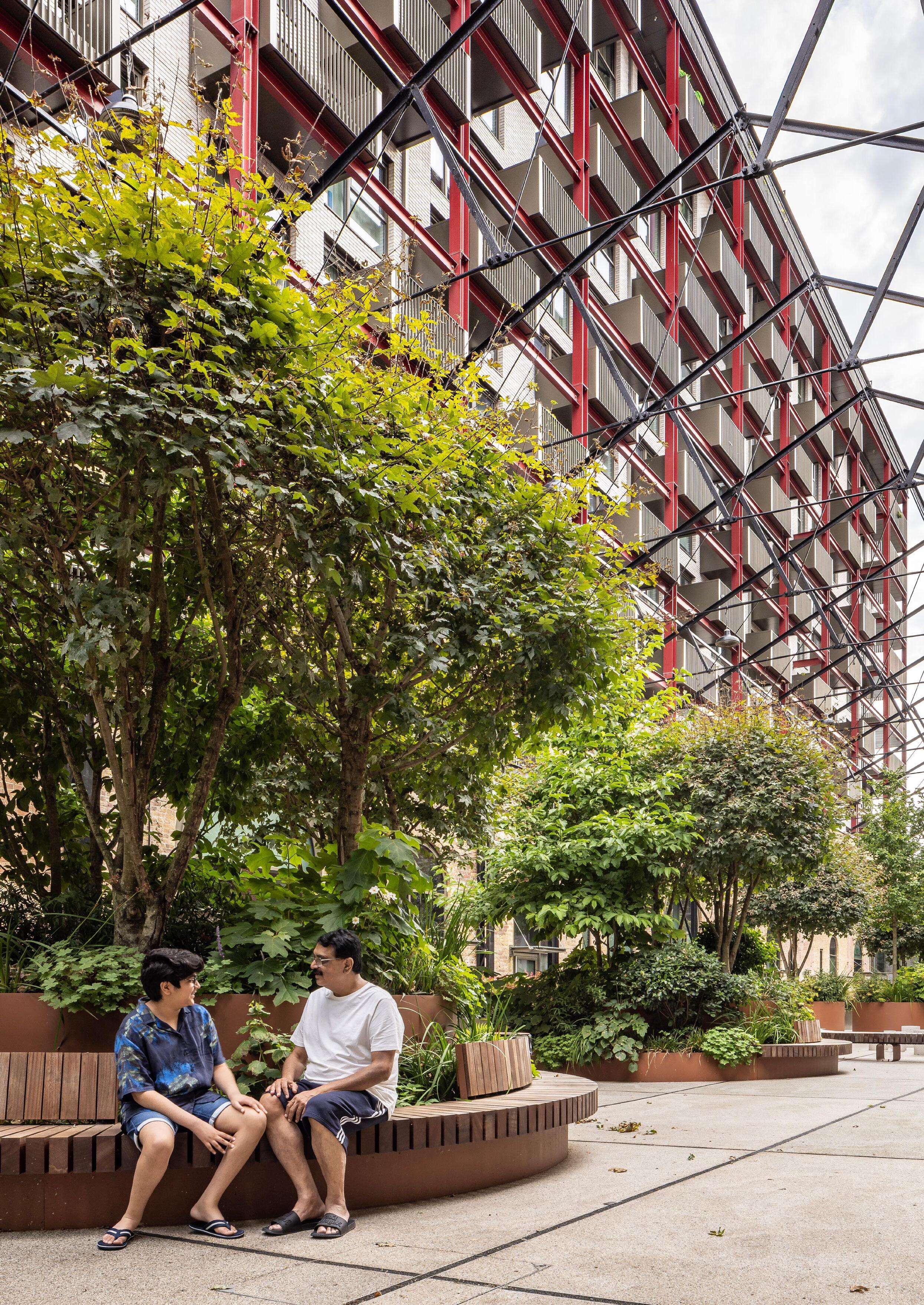
SUSTAINABLE DESIGN ETHOS
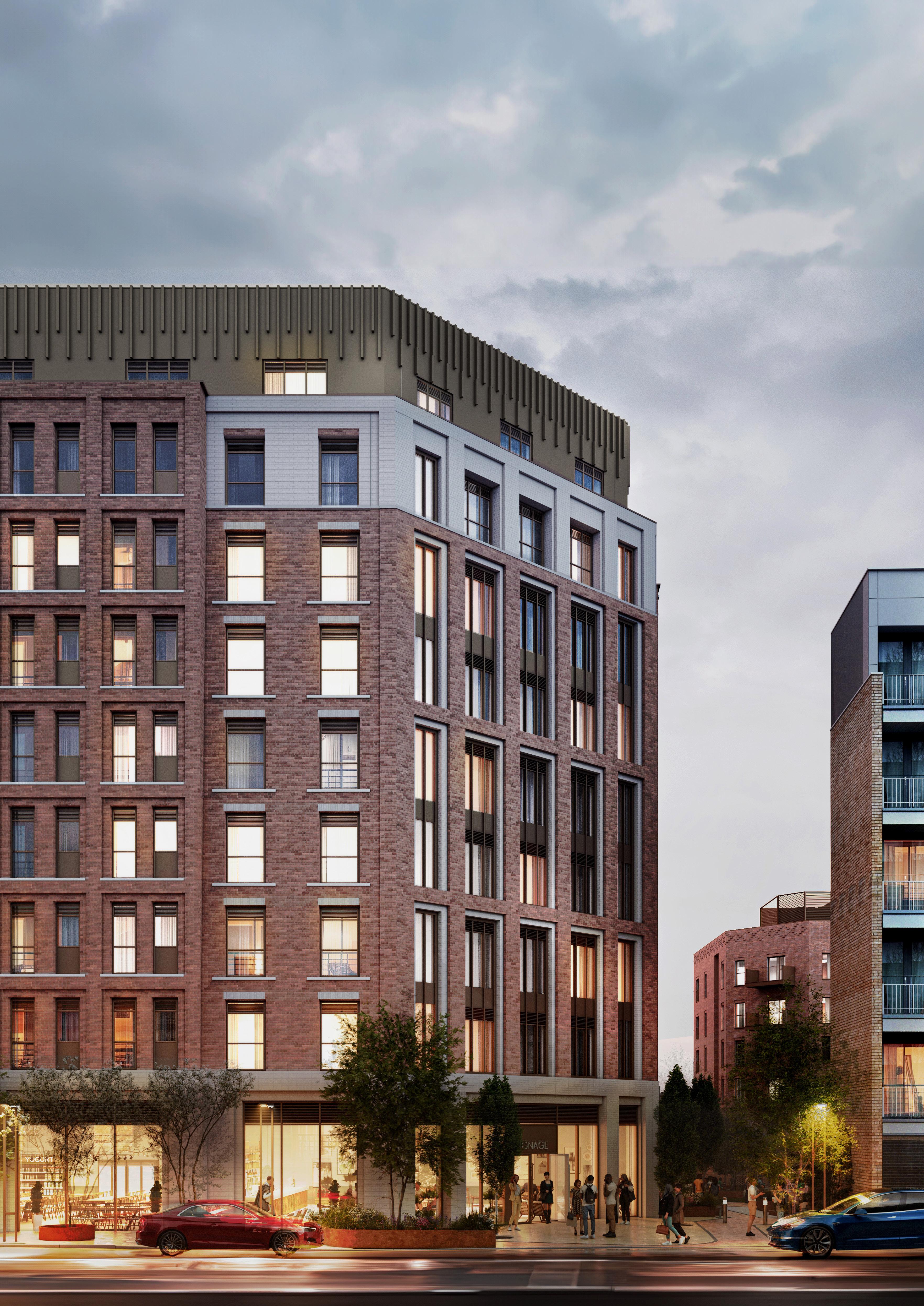
Image: Lordship Lane, Wood Green London - Targeted BREEAM Rating of Outstanding
Introduction
Corstorphine & Wright is committed to addressing climate change through a holistic, sustainable design approach Central to our design philosophy is the development of net-zero buildings that contribute to reducing global carbon emissions and improve people’s lives � We view it as our ethical responsibility to promote sustainability in all our projects, whether retrofitting existing structures or creating new ones, and encourage our clients to adopt high standards of sustainable design and procurement This ensures their buildings not only offer optimal environments but also minimise energy consumption and support the sustainable lifecycle of materials �
A key aspect of our work is maximising re-use within a Circular Economy framework, an essential strategy for achieving global carbon targets By retaining and reusing existing materials and assets at their highest value, we minimise embodied carbon, reduce the demand for new materials, and ensure our projects align with the urgent need for environmental stewardship This approach also contributes to improved health and wellbeing in the communities we serve
The Sustainable Design Ethos (SDE) reflects a holistic perspective, integrating ecological, social, and economic strategies that extend beyond carbon reduction We actively promote biodiversity, community resilience, and economic sustainability, striving for restoration and regeneration in our developments True sustainability, in our view, enhances biodiversity, improves ecological value, and mitigates the urban heat island effect by creating productive landscapes
To meet carbon reduction goals, our designs focus on sustainable site selection, emphasising proximity to public transport, green travel plans, and high-quality pedestrian and cycle access to local amenities We also prioritise water conservation, incorporating systems to reduce potable water use, recycle rainwater and wastewater, and creatively integrate natural watercourses into our projects, enhancing both habitats and community amenities
The Sustainable Design Ethos (SDE) reflects a holistic perspective, integrating ecological, social, and economic strategies that extend beyond mere carbon reduction �


Fig 1 Circular Economy Illustration by Circular Flanders
With our extensive experience in sustainable architecture, particularly through standards like BREEAM, we are positioned to exceed Net Zero Carbon requirements on future projects Utilising Whole Life Carbon (WLC) Assessments, guided by organisations such as LETI, UKGBC, and The Climate Framework we ensure that our designs are grounded in evidence-based best practice This expertise in Passive House, Retrofit, and BREEAM standards enables us to meet the stringent criteria necessary to combat climate change
The SDE plays a crucial role in advancing sustainability across all levels of our organisation and with our clients It serves as both a guide and an educational tool, ensuring that everyone involved in a project - from newly qualified staff to experienced professionalsunderstands and adheres to our sustainable design principles This consistent approach ensures uniformity in outcomes, enabling us to deliver projects that meet Net Zero Carbon targets and uphold the highest standards of environmental responsibility
In summary, our Practice is at the forefront of sustainable development, advocating for designs that address climate change holistically Through collaboration, evidence-based design, and a commitment to the Circular Economy, we create buildings that reduce carbon, enhance biodiversity, and foster resilient communities The Sustainable Design Ethos ensures that we continue to lead the way toward a Net Zero Carbon future, delivering lasting environmental, social, and economic benefits
The scale of the challenge confronting architects and the key milestones that must be reached to ensure the creation of zero-carbon built environments can be seen in the diagram overleaf
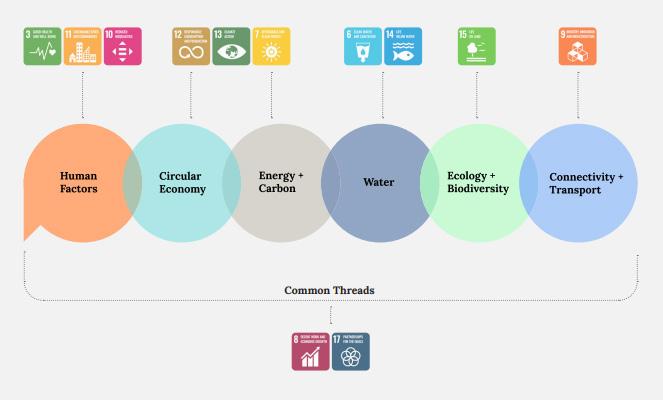
Zero Carbon Trajectory
0.5 Zero carbon trajectory
The following graphic sourced from the LETI Climate Emergency Design Guide illustrates the key milestones that must be achieved in order to ensure that the UK will have a zero carbon built environment by 2050
The following graphic illustrates the key milestones that must be achieved in order to ensure that the UK will have a zero carbon built environment by 2050.
2025-2030
Improved cost-effectiveness by industry upskilling.
Data disclosure
All buildings (new and existing) to disclose energy use data.
Operational energy
All new buildings designed to be net zero operational carbon.
Demand response Policy to mandate minimum requirements for metrics.
Operational energy
All new buildings to operate at net zero operational carbon.
Embodied carbon
All new buildings achieve a 65% reduction in embodied carbon emissions.
2020-2025
Five years to design and build pathfinders; working out what to do with existing stock.
Operational energy
UK building regulations must be updated to clearly signpost how and when it will transition to mandatory verification of in-use energy consumption. Building industry to adopt Energy Use Intensity (EUI) targets.
Operational energy
Introduction of regulatory performance framework with EUI requirements.
Embodied carbon
All buildings to conduct whole life carbon calculations and aim to achieve 40% carbon emission reductions.
Future of heat
All new buildings are fossil fuel free.
Data disclosure
All new buildings to disclose energy use data.
2022
Embodied carbon Benchmarks and methodology to be established and regulation introduced to ensure benchmarks are met.
Demand response Metrics around demand response to be established.
2050 2025-2050
Upgrade to zero carbon at a rate of 3,750 homes per day! Upgrade existing non-domestic buildings.
Figure
Objectives
The SDE is underpinned by the following objectives:
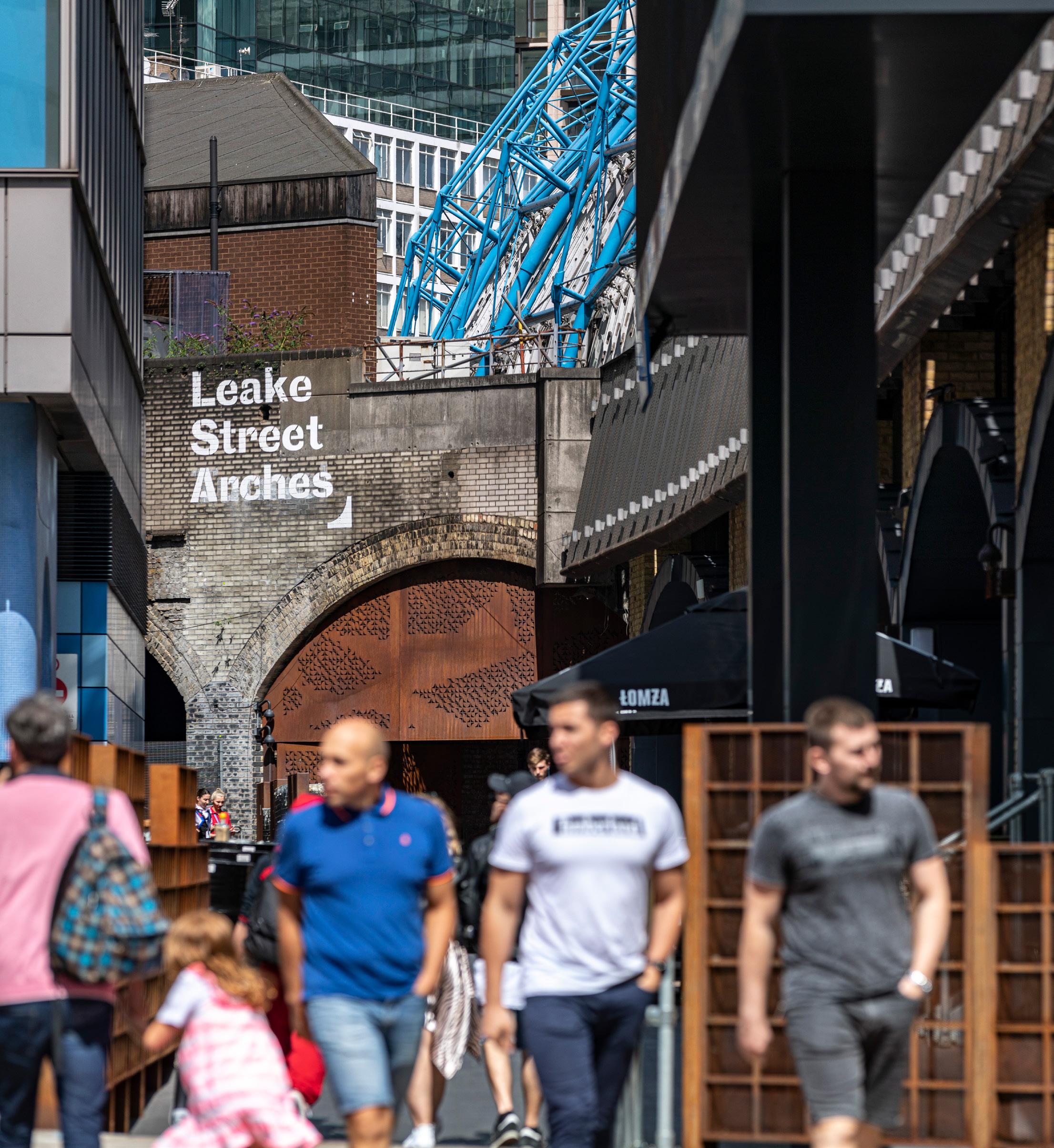
1. Standardise Practices
• Provide a clear framework for sustainable practices across the entire practice, ensuring uniformity and identify best practice in project designs
• Act as a reference when making decisions, helping prioritise sustainability at every phase of a project
2. Improve Client Communication
• Educate clients on the importance of sustainability, helping them understand the environmental, social, and economic benefits of sustainable design
• Align client’s expectations with C&W’s sustainable practices, fostering mutual understanding, collaboration, and support
3. Inspire and Empower Designers
• Encourage innovation and creative solutions to sustainable design problems
• Provide a framework for documenting and reflecting on sustainable strategies, fostering a culture of continuous improvement and knowledge sharing in sustainable design
4. Compliance & Advocacy
• Ensure design process aligns with local, national, and industry regulations and standards, as well as providing greater engagement and accountability in relation to QME requirements
• Empower colleagues to advocate for stronger sustainability policies and practices with clients, the Practice, and industry
5. Integrity & Responsibility
• Helps reinforce ethical responsibility to minimise environmental impact and promote sustainable development
• Demonstrating commitment to sustainability attracts clients and projects that promote environmental stewardship
6. Ensures Long Term Impact
• Future proof our designs, ensuring they are resilient, adaptable, and have a long term positive impact on the environment
• Enable designers and clients to leave legacy buildings for future generations
7. Collaboration & Integration
• Provide a shared language and set of objectives around sustainability that facilitates collaboration with consultants, contractors, and clients
• Encourage the importance of taking a holistic approach to sustainability, integrating environmental, social and economic aspects into design process
Outcomes
The SDE offers the Practice numerous benefits and outcomes. These include:
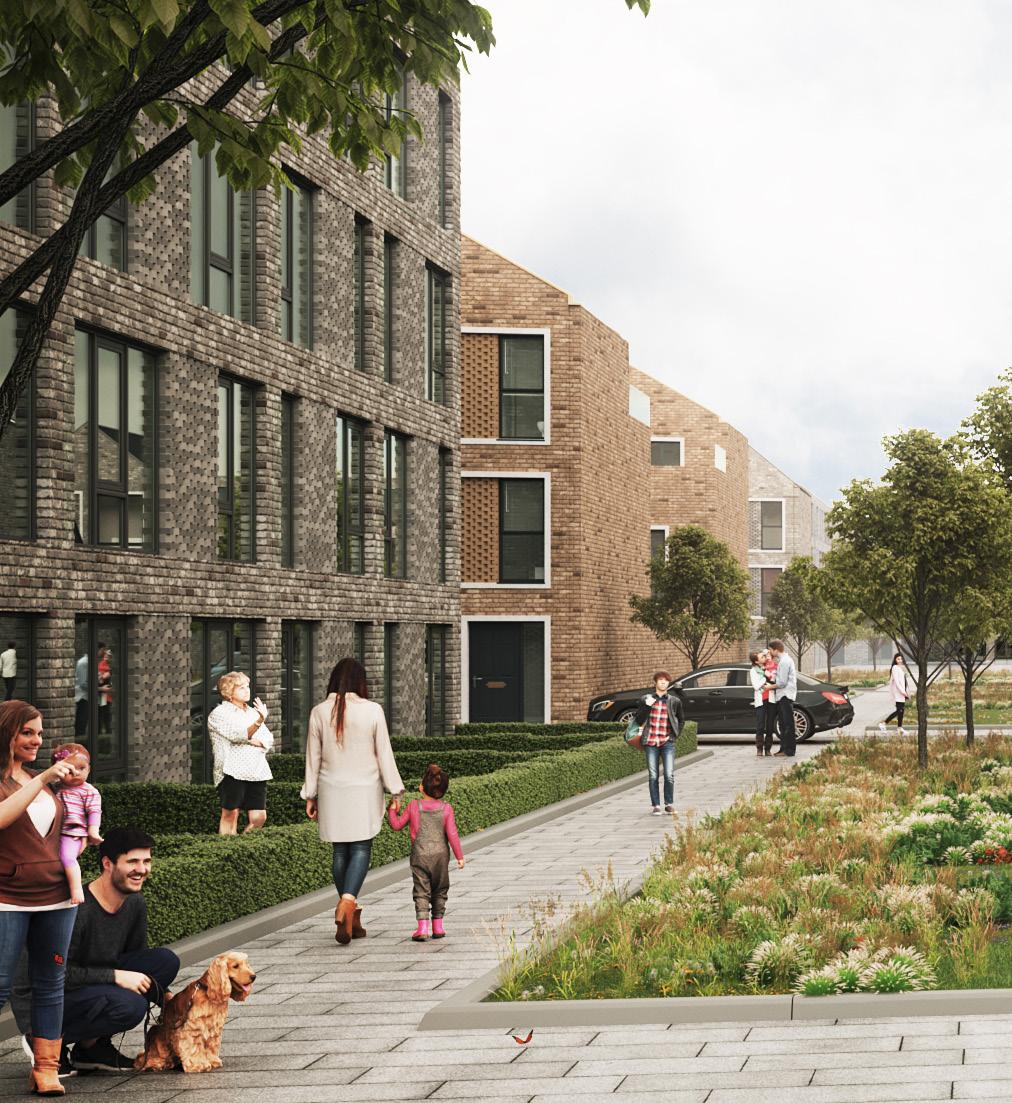
1. Reducing our Environmental Impact
More resilient buildings, greater support for local biodiversity and improved wellbeing for occupants, should result in a significant decrease in the carbon footprint of our buildings
2. Increased Demand & Client Satisfaction
Demonstrating we have the processes and expertise in place to deliver Net Zero buildings can lead to increased demand for our services and higher levels of client satisfaction
3. Contribution to Global Sustainability Goals
Designs that reduce resource consumption and promote sustainable development contribute to broader global efforts to combat climate change
4. Enhanced Design Quality
The SDE will drive continuous improvement in the sustainability of our designs, and greater client and end user satisfaction
5. Operational Efficiency
A standardised approach to sustainable design offers streamlined workflows, improved collaboration across teams, projects, and studios, as well as greater engagement in QME procedures
6. Market Differentiation
Demonstrating and advocating our commitment to sustainability can enhance reputation, attracting environmentally conscious clients willing to invest in this As a resource, the SDE can help position our practice as a leader in sustainable architecture
7. Continuous Professional Development
The SDE will serve as a valuable learning resource, helping our designers to stay updated with latest technologies, materials, and methods, helping to develop skills and foster a culture of continuous learning and innovation
MAKING THE USE OF THE
THE BEST THE SDE
Making the Best Use of the SDE
The Sustainable Design Ethos represents our commitment to designing better, more sustainable buildings It sets clear goals for sustainable design and encourages you to make sustainability a standard practice in our work To meet climate targets and elevate design quality, we must start integrating these practices nowmany of which are easy to implement
Our key message? Don’t wait for a perfect solution—there isn’t one Small, deliberate steps can lead to significant, positive change As designers, we need to think creatively and embrace circular economy principles: designing for longevity, reusing materials, reducing waste, and creating systems that regenerate resources rather than depLETIng them Though compromises are inevitable, what matters most is our progress toward a more sustainable, circular future
Some solutions may require an initial investment, but they provide long-term benefits, such as lower costs, improved efficiency, and greater durability They also contribute to environmental responsibility and economic resilience These are the crucial conversations we need to have with our clients
By minimising energy demand and supporting efficient infrastructure—such as local transit and the energy grid - we can design solutions that benefit people, communities, and the planet
To meet climate targets, whole life carbon must always be considered in our designs. This includes embodied carbon, which covers emissions from materials and construction (extraction, manufacturing, transport, installation, and disposal), and operational carbon, which comes from energy use during the building’s lifespan (heating, cooling, lighting, and appliances) Accounting for both types of carbon, helps create sustainable buildings, addressing environmental impacts at every stage of a building’s life
How to Make the Best Use of This Document
The SDE, aligned with the 2020 Plan of Work, provides standards and targets to achieve high levels of sustainability To support your efforts in meeting these goals, we have outlined key information regarding sustainable practices for each RIBA Stage, which includes:
• Overview – of each Stage, highlighting the required outcomes by its conclusion
• Key Actions - to consider at the beginning of each Stage, ensuring alignment with sustainability objectives
• Interactions - with key stakeholders, emphasising collaboration throughout each Stage
• Green Certifications/Building Standards - detailing what must be achieved for these at each Stage to meet the sustainability criteria
• Guidance – on design actions to maximise sustainability, encouraging Design Teams to work closely with clients to explore innovative solutions and integrate as many sustainable practices as possible
• Outcomes & Gateway Questions - to ensure that sustainability actions are reviewed and met before progressing to the next Stage
Finally, it’s crucial to connect with sustainability experts in your studio/region and collaborate with them and the Sustainability Champions to help meet our targets. Leveraging this expertise early will help achieve more informed, sustainable project outcomes.
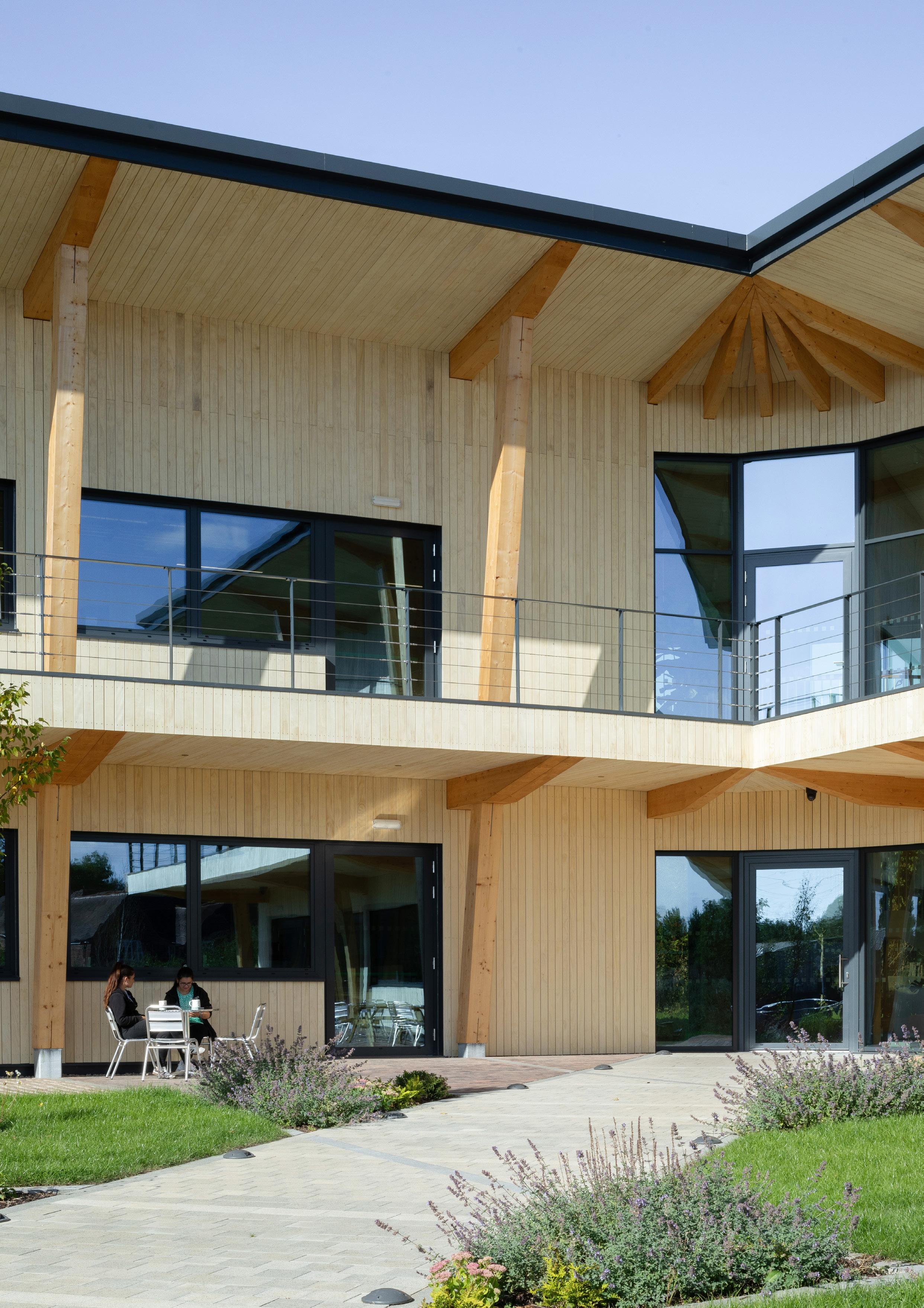
Image: Unusual Hq, Northampton, Uk
An Exemplar Test-Bed Project for Circular Economy Principles and Low-Carbon Design
Accreditations & Standards
Sustainability accreditations are increasingly valued by local planning authorities and clients alike BREEAM continues to be a preferred choice, with our established expertise in delivering buildings rated ‘Outstanding’ and ‘Excellent ’ The latest iteration, Version 7, is evolving to incorporate Whole Life Carbon Assessment and Post Occupancy Evaluation, ensuring the highest standards of sustainability At the same time, Passive House and WELL certifications are gaining momentum Enerphit should increase in popularity in line with prioritising retrofitting existing buildings over constructing new ones
As we strive to meet Net Zero Carbon goals, it’s essential to inform clients of the wide range of accreditations available to meet their sustainability requirements (see below)
BREEAM (Building Research Establishment Environmental Assessment Method)
BREEAM provides a holistic sustainability assessment framework for buildings and infrastructure, measuring sustainable value It evaluates projects across diverse categories, including energy efficiency, water use, health, and ecology
Scope: Applicable to new builds, refurbishments, and inuse buildings across commercial, residential, and public sectors
Third-Party Assessor: A licensed BREEAM assessor is required to determine the project’s certification level
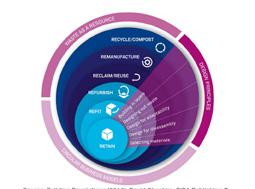
Circular Economy Design Principles
Circular economy design focuses on minimising waste, reusing materials, and creating regenerative systems to reduce environmental impact
Scope: Applicable to new construction and retrofit projects in any sector
Third-Party Assessor: Not typically required; principles can be integrated into design and construction processes by project teams Some local authorities require a Circular Economy Statement, this may be best carried out by a specialist consultant
WELL Building Standard
The WELL Building Standard focuses on enhancing health and wellbeing by assessing building performance in areas like air quality, water, nourishment, light, fitness, comfort, and mental health Projects must be recertified every three years to account for building ageing
Scope: Used in commercial offices, with pilot projects in healthcare facilities, educational institutions, and residential buildings
Third-Party Assessor: Required for certification, ensuring compliance with WELL’s performance criteria
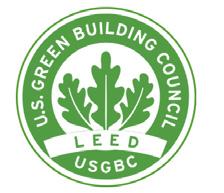
LEED (Leadership in Energy and Environmental Design)
LEED is a global sustainability certification system evaluating energy, water, materials, biodiversity, and indoor environmental quality to promote greener buildings
Scope: Applicable to all project types, including new builds, renovations, interiors, neighbourhood developments plus core and shell
Third-Party Assessor: LEED-accredited professionals review and verify projects to award the level of certification
Passive House Principles
Passive House (aka Passivhaus) principles aim to minimise energy demand while maximising occupant comfort This is achieved through excellent insulation and superior thermal performance, ensuring minimal heat loss Buildings are constructed with airtight envelopes to reduce unwanted airflow, combined with optimised ventilation systems that recover heat effectively Thoughtful design minimises thermal bridging, while high-performance triple glazed windows and strategic orientation take advantage of passive solar gains The design should be modelled and tested using PHPP modelling software
Scope: These principles can be implemented in any building type
Third-Party Assessor: Not required unless certification is pursued
Passive House Certification
Passive House (aka Passivhaus) certification verifies that a building meets the rigorous energy efficiency and comfort standards required by the Passive House Institute This includes features like airtight construction, high performance thermal envelope insulation, and efficient ventilation systems
Scope: Suitable for all building types
Third-Party Assessor: Required for certification, conducted by a certified Passivhaus Passive House assessor
EnerPHit Standard
EnerPHit is the Passive House standard for retrofitting existing buildings, optimising energy efficiency while accommodating the limitations of existing structures The required standards are less onerous than new-build Passive House
Scope: Specifically for retrofitting, but applicable to all building types
Third-Party Assessor: Required to verify compliance and issue certification
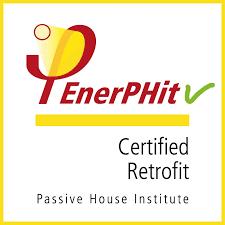
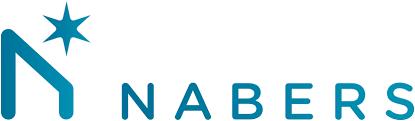
NABERS (National Australian Built Environment Rating System) Currently administered by CIBSE
NABERS measures the operational performance of buildings in areas like energy efficiency, water consumption, waste management, and indoor environmental quality
Scope: Primarily applied to offices, care, multiple occupancy, leisure and logistics
Third-Party Assessor: Required to conduct assessments and verify ratings

UK Net Zero Carbon Buildings Standard
This offers a framework for achieving and proving net-zero carbon buildings, providing targets across construction, operational emissions, embodied carbon and renewables
Scope: Covers all major building sectors
Third-Party Assessor: No external verification process in place UKGBC expect one to be operational within next 12 - 18months
STAGE 0-1: STRATEGIC DEFINITION PREPARATION & BRIEFING
Stage 0-1
Preparation & Briefing
Overview
The ‘Strategic Definition’ stage marks the beginning of the design process and establishes the sustainability agenda that influences the entire project lifecycle It focuses on laying a solid foundation for a project that is both environmentally responsive and architecturally innovative, while setting measurable targets to guide its progress
Throughout Stages 0 and 1, we prioritise open and detailed dialogue to ensure that sustainability ambitions are clearly understood, realistic, and achievable We explore opportunities for sustainable design and construction practices, including site selection, building orientation, resource use, energy efficiency, and the potential for renewable energy These insights are translated into measurable targets tailored to the specific project and building type
RIBA Stage 1 plays a crucial role in shaping the direction of the project This stage involves initial discussions to define project goals, aspirations, and the broader context in which the project will take place At this point, sustainability is integrated as a core objective, paving the way for an environmentally conscious, costeffective, and innovative solution
Outcome: Project Brief
Key Interactions
Clients
Our priority is to build strong working relationships through open and effective communication, to build trust and obtain a clear understanding of specific needs and goals As our goal is to significantly reduce environmental impact we advocate re-use or refurbishment of existing structures before considering new construction This also means we consider the ease of disassembly and future adaptability of materials at the earliest possible stage By working together to discover opportunities for sustainable solutions based on these principles, we develop tailored, practical strategies that align with long-term sustainability goals These remain a key priority throughout the project
Where applicable, feedback from Post Occupancy Evaluations of previous projects helps us assess past successes and highlight areas for improvement, enabling us to continuously refine our methods and enhance sustainability outcomes in future projects
Preliminary Actions
• Identify environmental, social, and regulatory sustainability constraints during site feasibility studies.
• Conduct in-depth feasibility assessments to evaluate the potential for reusing or refurbishing existing structures on the site, prioritising solutions that minimise environmental impact.
• Incorporate a biodiversity assessment in the feasibility study to ensure any net loss is adequately mitigated, such as through the strategic replacement of flora or enhancement of habitat areas.
• Ensure all Sustainability QME documentation is set up and is added to as the project progresses.
• Set project design parameters/targets, and establish regular review checkpoints to assess and refine sustainable design parameters, ensuring continuous alignment with sustainability goals.
• Ensure appointments are sustainability-driven.
• Check any relevant POE precedents that could help inform the Brief.
• Request a copy of Client’s Net Zero Carbon Policy or Sustainability Aspirations (if applicable).
Design Team
To ensure both effective collaboration and successful outcomes in Stage 0-1, the project must align with sustainability goals and focus on long-term operational efficiency To achieve this, it is essential to complete several key actions:
• Form a bespoke design team by selecting both internal staff and external consultants who have experience in relevant accreditations, sectors, design, and assessment services
• Review relevant Post Occupancy Evaluation (POE) or Facilities Management feedback to inform the Project Brief
• Obtain and review the client’s Net Zero Carbon Plan or sustainability aspirations Identify which RIBA Sustainability Outcomes apply to the project and engage the client early about the building’s future operation and maintenance
At this early Stage, designers should review the guidance below to identify actions that maximize the project’s sustainability These should be applied early in preparation, site review, cost planning, and stakeholder engagement Early integration supports better decisions, leading to eco-friendly, cost-effective solutions that meet community and user needs Design Teams are encouraged to include as many of the actions below as possible in their projects
Stage 0: Strategic Definition
1 Organise a workshop with the client and key stakeholders to discuss potential future use scenarios and assess how the building’s needs and those of its occupants may evolve over time
2 Collaborate with the client and design team to outline the ‘7 Principles of Circular Design’ - to be refined and expanded from Stage 2 onwards
3 Highlight opportunities for optimisation and areas requiring improvement and build a long-term financial case to assess potential savings Establish the target performance specification for the building fabric and services This ensures a high-performing building can feasibly be delivered, factoring the specification into initial designs and costs
4 Determine anticipated cost variations and budgets based on the minimum standard building design
Stage 1: Preparation and Brief
1 Carry out a comprehensive site appraisal to evaluate the site’s potential and optimise passive design The site analysis should include an assessment of the microclimate to identify challenges and opportunities, utilising environmental design strategies
2 Conduct a Pre-redevelopment Audit for buildings identified for demolition or renovation, creating a detailed inventory to facilitate the re-use of materials
3 Establish clear targets aimed at maximising the use of re-used, remanufactured, recycled, and natural/ biodegradable products In the early design visualisations, prioritise materials that allow for easy disassembly and future adaptability
4 Emphasise selecting materials that can be repurposed or recycled, avoiding permanent finishes like concrete flooring or rendered exteriors
5 Use the LETI Climate Emergency Design Guide (p26 – 33) to set the specification targets, referring to the suitable sector This information can also be found in the “Targets & Standards” section of the SDE under “LETI Design Measures”
6 The best time to establish an efficient form-factor is within the feasibility stage, as significant changes to mass can become more difficult later in the project
7 Reasonable construction thicknesses should be allowed for within feasibility studies in order not to limit achievable U-values and services opportunities As a rule of thumb until typical build-ups can be established, allow for: External walls: 500mm, Roof: 550mm, Ground floor: 600mm
Preparation & Briefing
Our Commitment
To effectively tackle the climate challenge in the built environment, our approach centres on a collaborative, multifaceted, and holistic strategy Our commitment to sustainability is embodied in the Climate Framework Initiative, a unified effort supported by the CrossIndustry Action Group, RIBA, UKGBC, LETI, and other esteemed professional bodies, membership organisations, and academic institutions This initiative represents a concerted effort to mitigate climate change and ecological degradation
Our commitment to creating genuinely sustainable environments involves addressing climate challenges within the specific social, economic, and environmental contexts of each project Our Sustainable Design Ethos (SDE) is anchored in six key themes: Human Factors, Circular Economy, Energy & Carbon, Water, Ecology & Diversity, and Connectivity & Transport By embedding these principles into our approach, we ensure that our designs not only address the impacts of climate change but also actively contribute to resilient, thriving communities
This holistic approach balances social equity, economic viability, and environmental stewardship
By adopting this strategy, we empower our Design Teams to foster a shared language, cultivate empathy and social awareness, and develop the essential knowledge and skills needed to create sustainable solutions This not only enhances collaboration within our teams and with clients but also ensures that sustainability is integral from the very beginning
We endeavour to equip our Design Teams with the best tools to protect both the planet and its people, fostering creativity in sustainable solutions We advocate for the use of proven methods grounded in Fabric First, Circular Economy, and LETI principles throughout every stage of a project
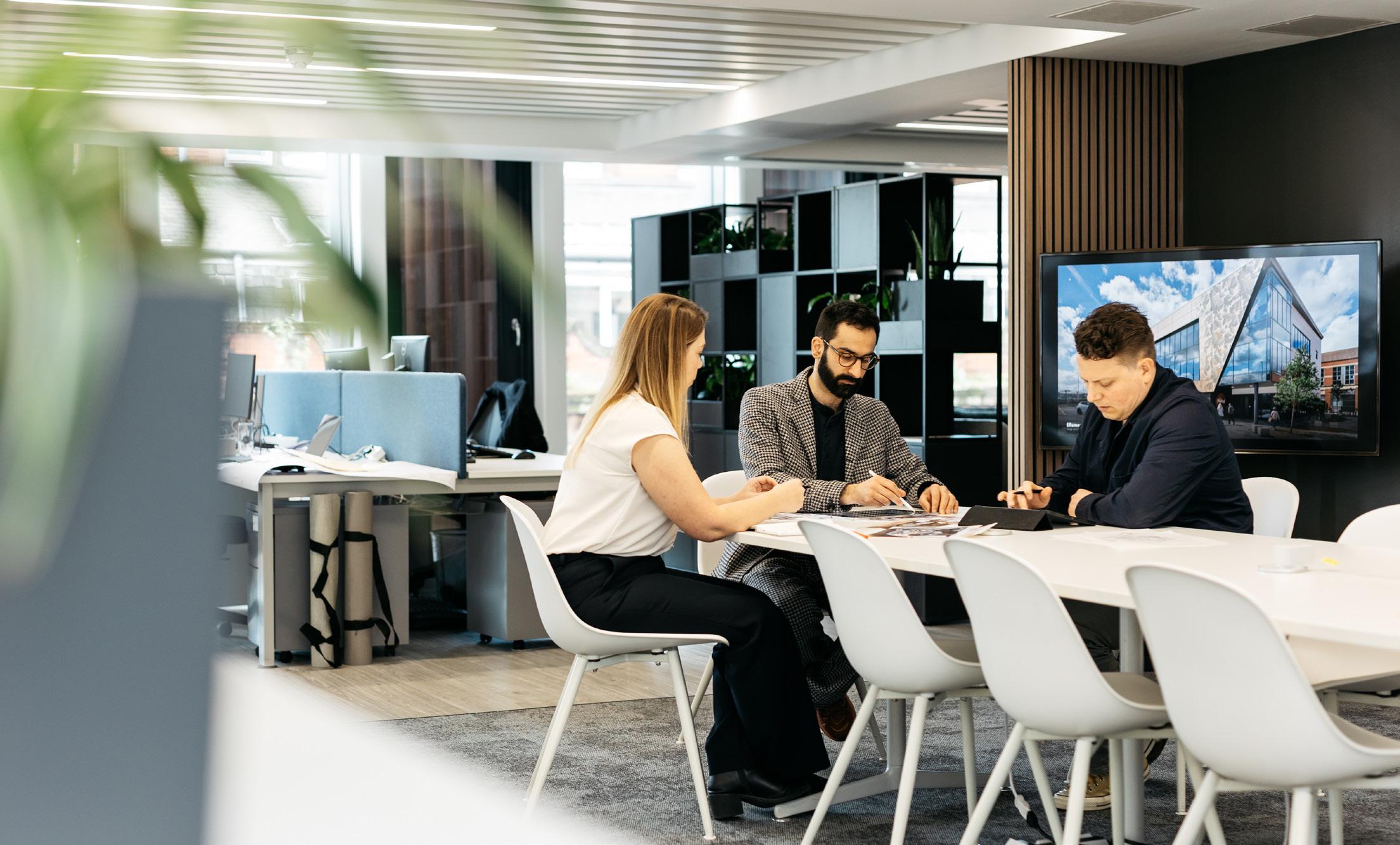
BREEAM
• Early engagement with a BREEAM Assessor is crucial as it sets the stage for a structured sustainability strategy The assessor will conduct an initial assessment of available credits, ensuring sustainability targets are integrated from the outset
• Establish a comprehensive stakeholder consultation plan adhering to BREEAM Man 01 A/B to ensure all key sustainability issues are addressed from the start
• Ensure all meetings and discussions are recorded
• At the conclusion of this stage, compile a Mat 06 Material Efficiency report setting forth targets and pinpointing opportunities to enhance material efficiency, thereby reducing environmental impact
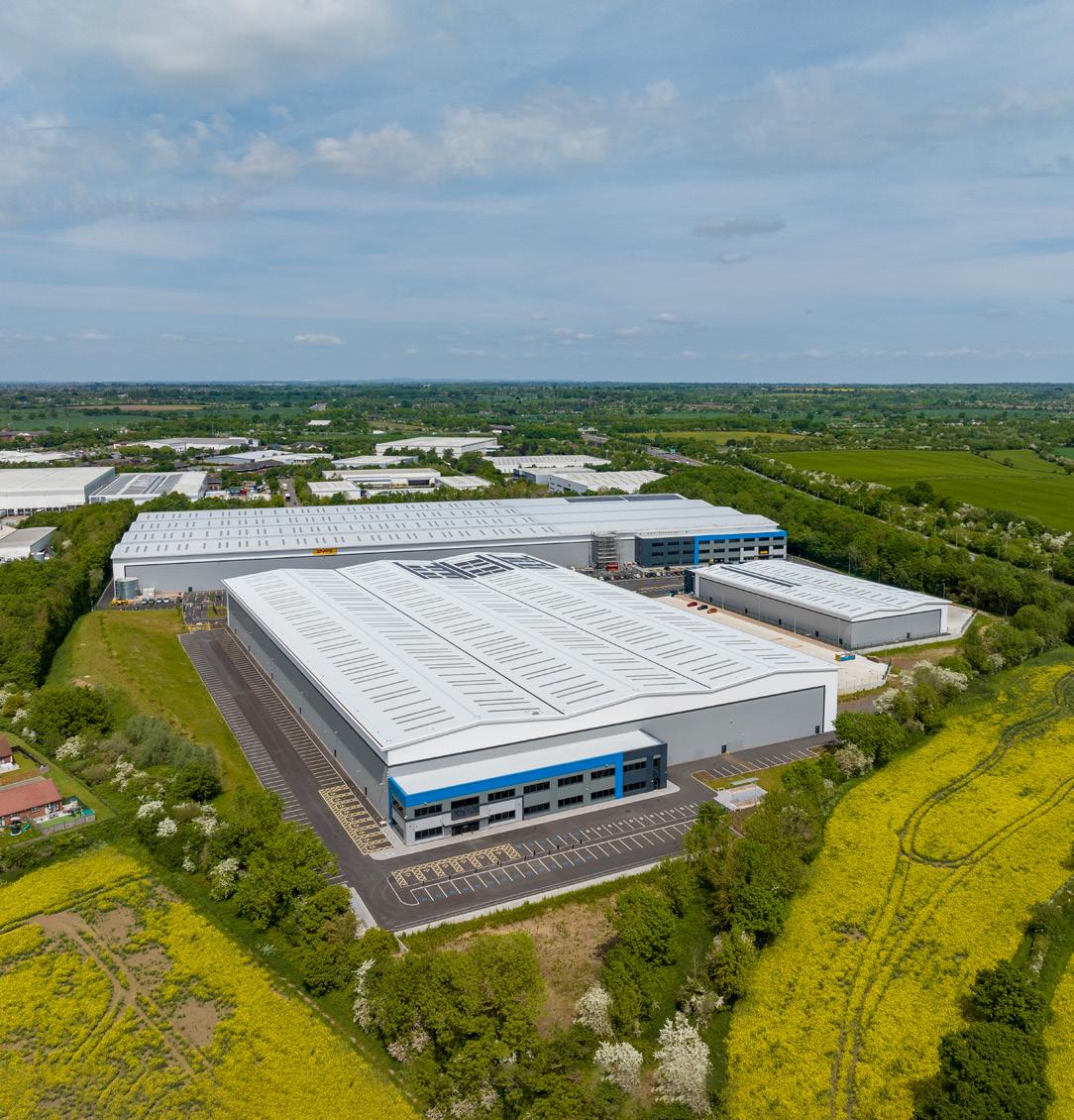
• Introduce Passive House Certification in early client discussions and determine if it is a suitable accreditation for the project
• Confirm with all necessary appointments early on to ensure a coordinated approach
• Ensure one of C&W’s Certified Passivhaus Designers is engaged on project to establish precise design metrics and sustainability targets
• If Certification required, engage a certified Passive House Assessor to assist with formulating a robust whole-life and embodied carbon strategy
• In the preliminary design phase, prioritise mechanical ventilation with heat recovery (MVHR), strategic room placement, effective solar shading, and optimal glazing percentages to maximise energy efficiency
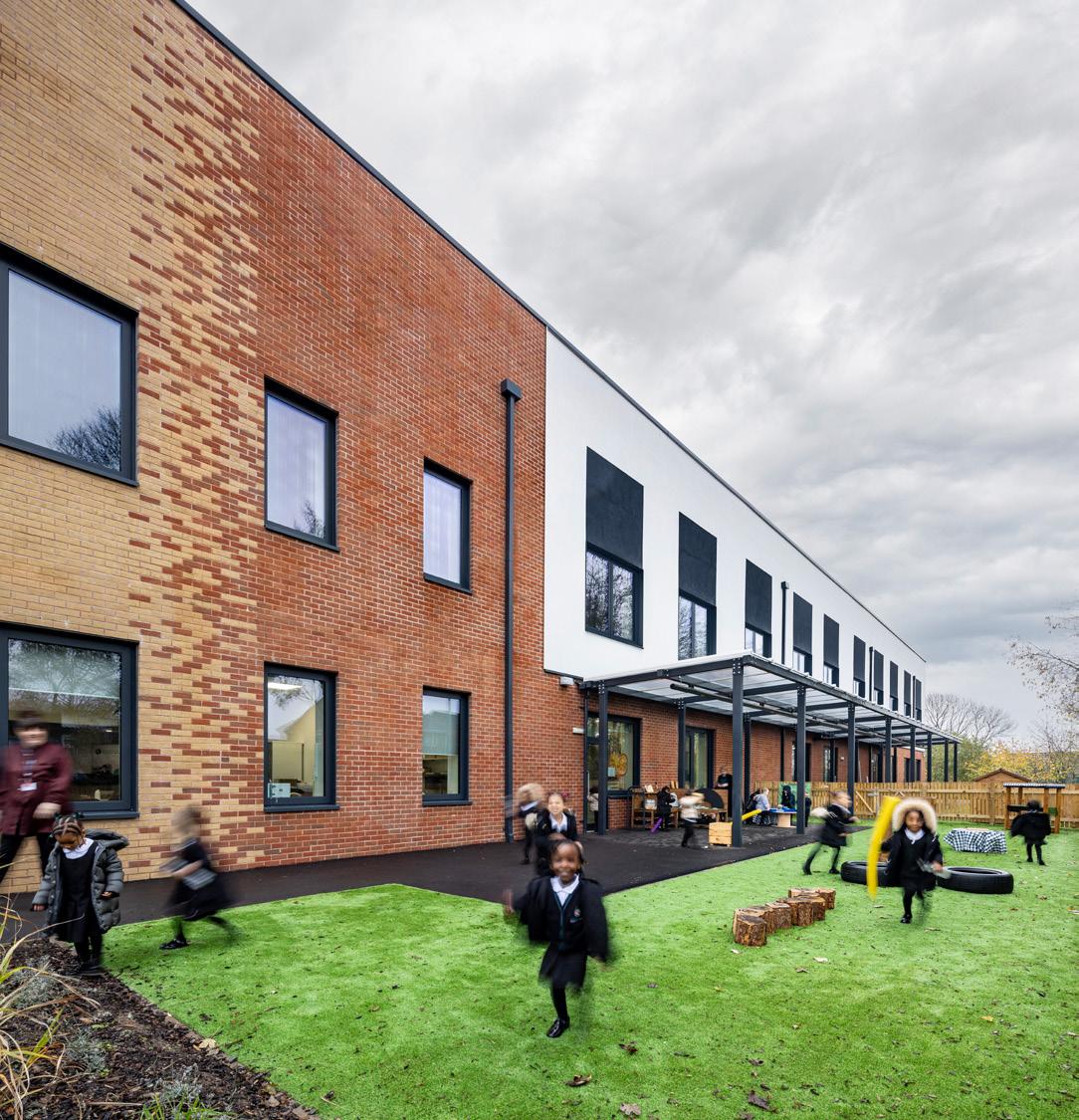
Coventry Logistics Park - BREEAM Outstanding Rated
Wednesfield Technology Primary School - New Passive House Primary School
Passive House
Certification Preparation & Briefing
WELL
• Determine the most suitable WELL standard (New and Existing Building, New and Existing Interiors, or Core and Shell compliance) based on the building type
• Confirm if building is to be owner-occupied or will follow WELL Core guidelines
• Define the project boundary to ensure consistent application across all WELL features
• Establish core principles of WELL Framework, including a programmeme that includes timelines and processes for the approval of each WELL core value
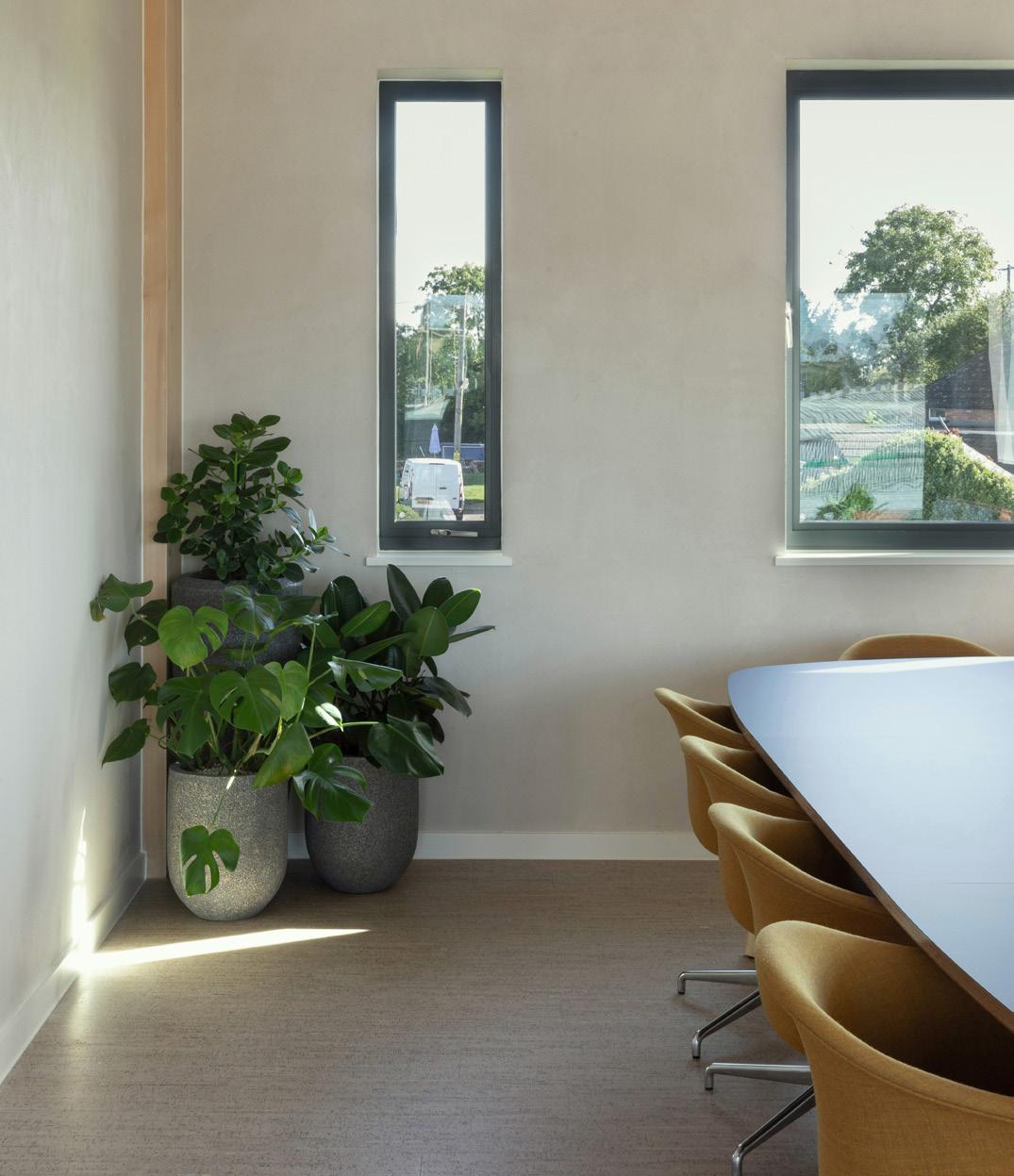
LETI recommends using four key principles for creating successful project briefs. (These are presented as the ‘Elements of a Net Zero Carbon Brief’
5 Elements of a Net Zero Carbon Brief - LETI Client Guide (2021) pg 29
Unusual Rigging HQ, Northampton
Outcomes & Gateways
We have introduced Gateway checks at the end of each RIBA stage to enhance sustainability, improve design quality, and support better decision-making We believe these checks help minimise errors, enable continuous improvement, support our audit processes, and promote data-driven practices for efficient project execution and carbon reduction
Request a copy of Client’s Net Zero Carbon Plan or Sustainability Aspirations, if available
Ensure advice letter QRD 3 30 has been issued to the Client and a recorded in accordance with QME requirements
Check whether any relevant precedents from POE or existing building’s Facilities Management team can be incorporated into the Project Brief
Check that an actionable plan addressing both immediate and future sustainability challenges has been completed
Ensure long-term impact and resilience are prioritised, ensuring that the project continues to meet sustainability goals even after completion
Identify relevant RIBA Sustainability Outcomes Targets for the project
Ensure clients asked how they intend to operate and maintain the facility
Confirm we have conducted an initial project workshop to establish clear, measurable performance objectives and identify internal design champions
Ensure sustainable aspirations have been agreed with the client, and targets identified in the Brief
Verify we have critically evaluated the potential of reusing existing structures or selecting brownfield sites before considering new construction
Ensure any internal/ external specialists relating to this specific building sector or accreditation have been identified, particularly if they are not already part of the team, and included in the Responsibility Matrix
Verify critical design aspects such as form factor, glazing percentage, and ventilation strategies have been thoroughly assessed for their sustainability impact
Use the LETI Sustainability Site Appraisal Checklist (see Appendix) to ensure all sustainability measures are considered and addressed
STAGE 2: CONCEPT DESIGN
Stage 2
Concept Design
Overview
This stage marks the first opportunity to transform the sustainability goals set during the Preparation and Brief phase into tangible, creative design concepts The objective is to develop innovative solutions that not only address the Client’s needs but also benefit the environment, the local community, and future generations
Designers should create a concept that incorporates key sustainable design principles, including energy efficiency, use of eco-friendly materials, water conservation, and waste reduction Additionally, renewable energy sources, natural ventilation, and daylighting strategies should be explored to minimise the building’s operational carbon footprint
Outcome: approved Concept Design aligned to the Project Brief
Key Interactions
Client
Maintain regular communication with the client during the design process, highlighting the importance of sustainable features for the project’s success Advocate for a sustainable approach and encourage discussions on Pre-Application consultations with the Local Authority to streamline approvals and ensure regulatory alignment
Local Planing Authority
Carry out a review of the Local Planning Authority’s sustainable design policy (if applicable) to establish their preferences in both sustainable design requirements and Biodiversity Net Gain If instructed by the Client, carry out Pre-Application discussions
Preliminary Actions
• Refer to Stage 1 outputs and ensure compliance with the SDE has been achieved.
• If taking on the project at this stage from another colleague, studio or Practice, allow for relevant handover and clear conveyance of sustainability targets.
• Ensure all Sustainability QME documentation is up to date and amend through the workstage.
• Review adherence with established project targets.
• Utilise the LETI Sustainability Site Appraisal Checklist from workstage 1 ensuring the site’s potential and constraints are fully understood.
• Carry out an initial Whole Life Carbon Assessment covering both operational energy and embodied carbon.
• Progress the design of the building, landscape, and layout with a sustainability focused design review.
• Develop a detailed Responsibility Matrix that clearly outlines each team member’s role in maintaining the sustainability goals of the project.
Contractor
Assess and carefully consider the sustainability credentials of potential contractors, focusing on their previous projects and their openness to adopting innovative, eco-friendly construction methods
Design Team
Clearly communicate and collectively pursue common goals to maintain alignment and cohesion throughout the design process, minimising inconsistencies Incorporate regular sustainability updates in Design Team Meetings to promote ongoing improvement and success
At Stage 2, designers should review the guidance below to find the best sustainable actions to improve the project’s impact These actions should be included early in the process, such as during site reviews, cost planning, and discussions with stakeholders This will help make wellinformed decisions that lead to environmentally friendly, cost-effective solutions that meet the needs of both the community and future users
1 Consult with the Client to set clear operational energy use targets, documenting and devising strategies to achieve them Share these strategies with all stakeholders to ensure alignment and collaboration
2 Advocate to the Client to consider Whole Life Carbon assessment to be carried out on the project
3 Embrace strategies for reducing embodied carbon through careful selection of building materials and construction techniques
4 Implement the ‘7 Principles of Circular Design’ via an early design workshop with one of our Sustainability Champions and/or external Sustainability Consultant: 1 Building in layers 2 Designing out waste 3 Designing for longevity 4 Designing for adaptability/flexibility 5 Designing for disassembly 6 Using systems, elements or materials that can be re-used and recycled 7 Using re-used products and materials
5 Define the building design according to these principles, and record on the Circular Economy Tracker
6 Encourage all members of the design team to follow these design principles
7 Adhere closely to the LETI Climate Emergency Design Guide to inform design decisions that affect operational energy, such as: fabric U-values and efficiency measures Window-to-wall ratios tailored to the scale and function of the building
8 Early energy modelling should be carried out to review the energy consumption and space heating demand are achieving the LETI targets for kWh/m² yr
9 Ensure building fabric targets are being met as part of the design process, reviewing the targets and noting non-compliance within the stage report
10 Ensure the window area percentage is calculated and reviewed, as well as reconfirm that reasonable construction build-up allowances have been given to achieve the target U-values and airtightness
11 Consider MVHR routes as part of the design process, providing suitable space allowance
12 It is advisable that pre-planning advice is to be sought from the Local Planning Authority, with a focus to better understand their sustainable design guidance (if applicable)
13 Ensure the window area percentage is calculated and reviewed, and reconfirm that reasonable construction build-up allowances have been given to achieve the target U-values and airtightness
14 Consider MVHR routes as part of the design process, providing suitable space allowance Early energy modelling should be carried out to review the energy consumption and space heating demand are achieving the LETI targets for kWh/m2 yr
Concept Design
Carbon Reduction Potential as Project Progresses
Creating the Vision/Scoping
Finding the most carbonminimising, cost-effective and strategic business case and concept, where Net Zero Carbon is embedded into the brief
Reducing and Formalising
Assessing and adapting a design that meets measurable embodied carbon targets, and reducing demand by increasing fabric efficiency.
Constructing and Minimising Minimising performance gap through ensuring construction quality, and commissioning through Soft Landings procedures.
Optimising and Offsetting Testing the built asset’s operational carbon to optimise its performance and offsetting remaining carbon.
Figure 7 - Carbon Reduction Potential as Project Progresses
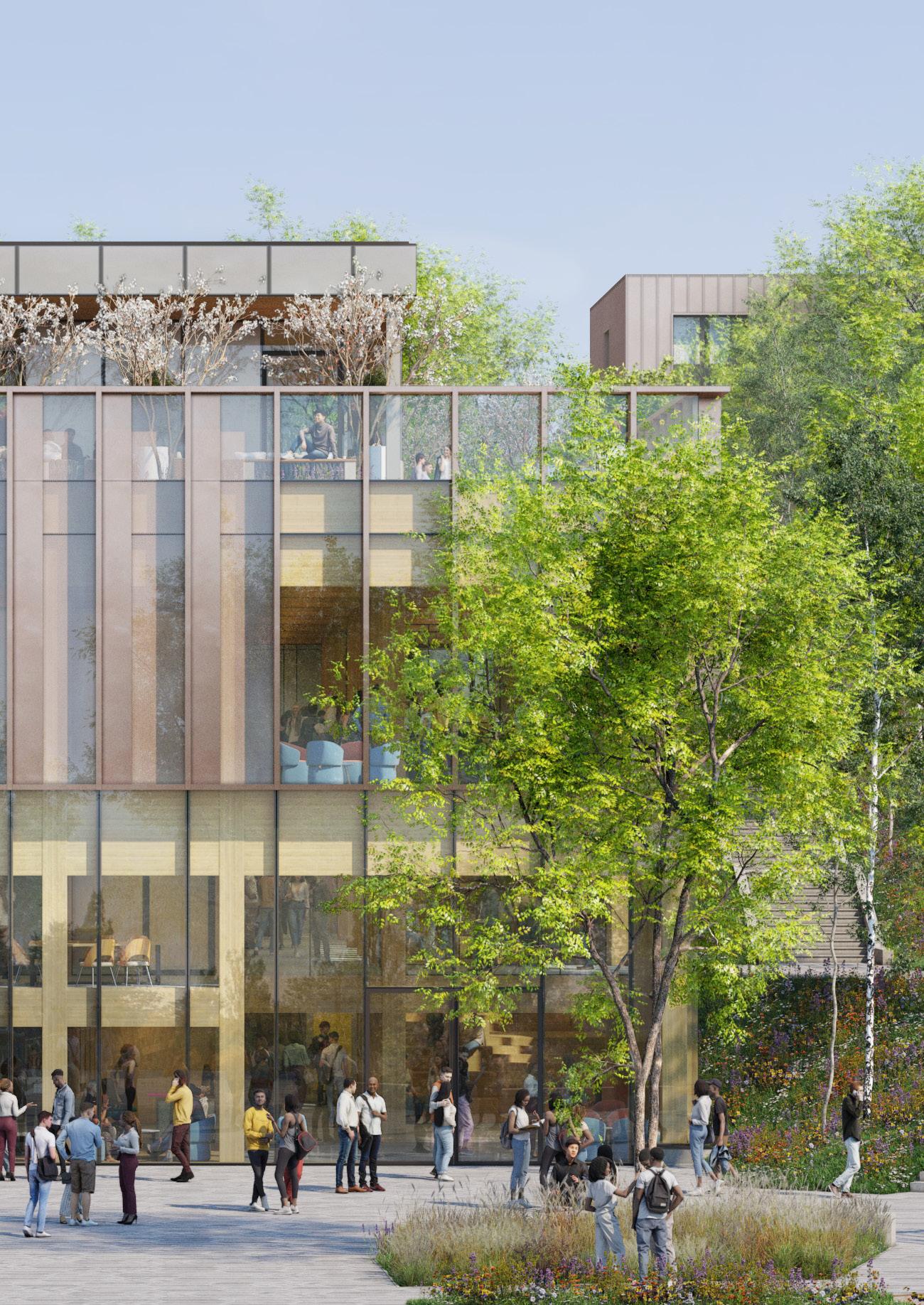
Image: Staffordshire University Village Hub, Stoke-on-Trent, UK Targeted Net Zero Carbon Development
Concept Design
Certification
BREEAM
• Integrate outcomes from Operational Energy Performance Workshops, Passive Design Analysys & LZC Feasibility Studies into the project from the outset
• Liaise with specialist consultants in preparation of Life Cycle Assessment Update the Materials Efficiency Report (Stage 2) outlining strategies for efficient material use
• Ensure designs maximise natural daylight and provide quality views to enhance the wellbeing of building occupants
• Collaborate with Architectural Liaison Officers or Security Consultants to review and enhance the security aspects of the design
• Integrate safe and accessible design for all users incorporating sustainable transport solutions
• Conduct a design for disassembly study, ensuring that future adaptability and end-of-life disassembly are considered, promoting sustainability beyond the initial use phase
• Ensure that landscaping and biodiversity net gain (BNG) objectives are not only met but integrated in a way that enhances the ecological value of the site
• Engage with one of our in-house Certified Passive House (PH) Designers early in the design process to ensure specialised knowledge integration
• Organise a coordination meeting with the client, MEP Engineers, and PH Designer to confirm the Passive House strategy based on the PH report
• Review the suitability of early contractor involvement, update the Procurement Strategy, and discuss with contractors and specialist subcontractors testing Passive house objectives outlined in the Concept Design and Passive House Plan
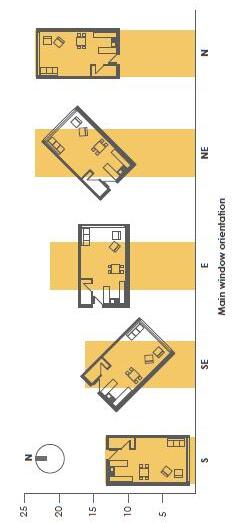

Fig 7 Why orientation is important LETI Climate Emergency Design Guide (2020) pg 48
Passive House
Certification
WELL
• Engage with one of our in-house Certified WELL Associated Professional early in design process to assist with integration and tracking of values and WELL criteria
• Consider access points to buildings to ensure they provide safe and healthy routes through the site and scheme
• Integrate biking, walking, and other forms of active transit by providing secure bike storage, showers, and changing facilities
• Develop spaces that encourage physical activity through the design of staircases, corridors, and common areas that invite movement and interaction
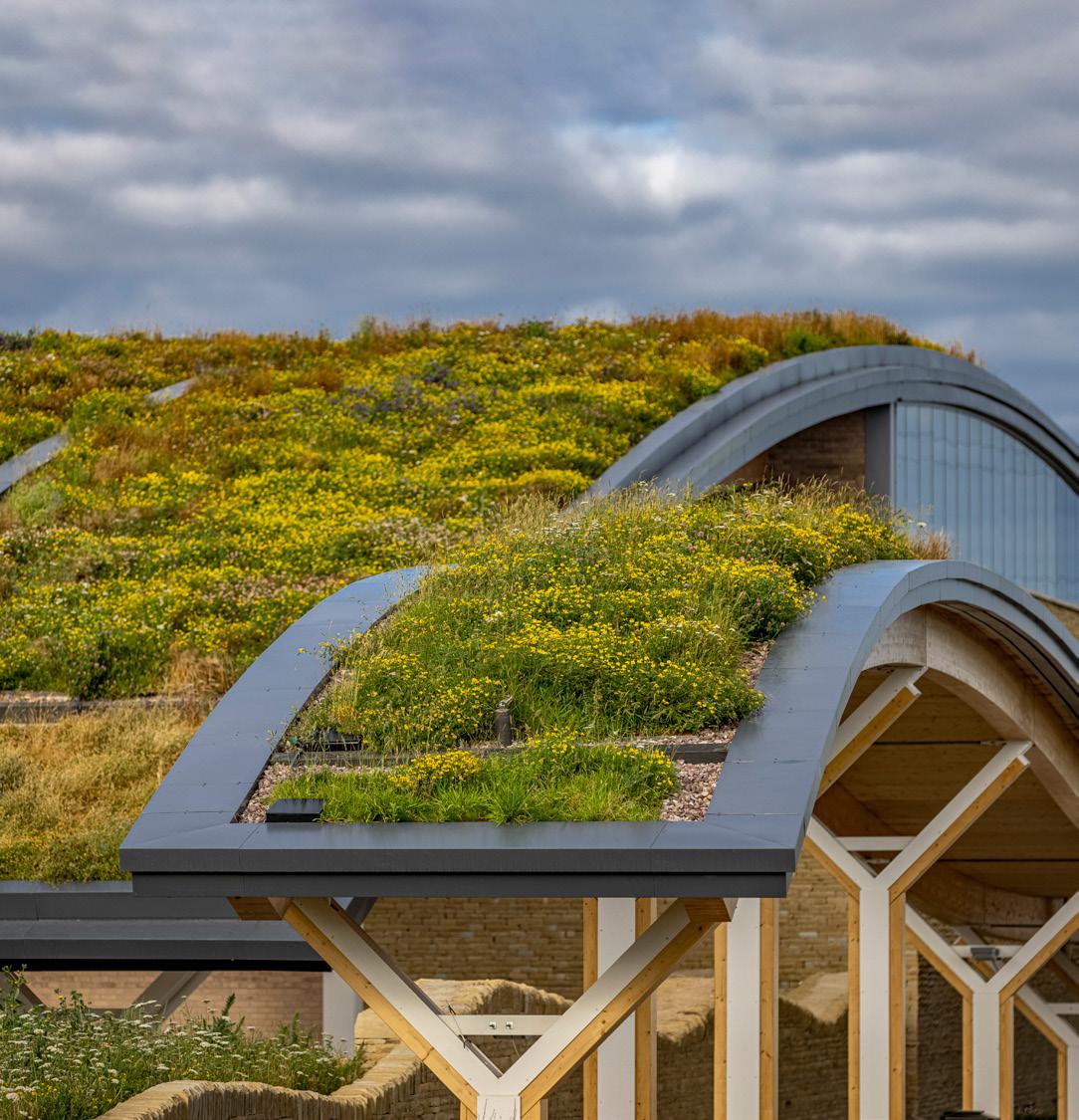
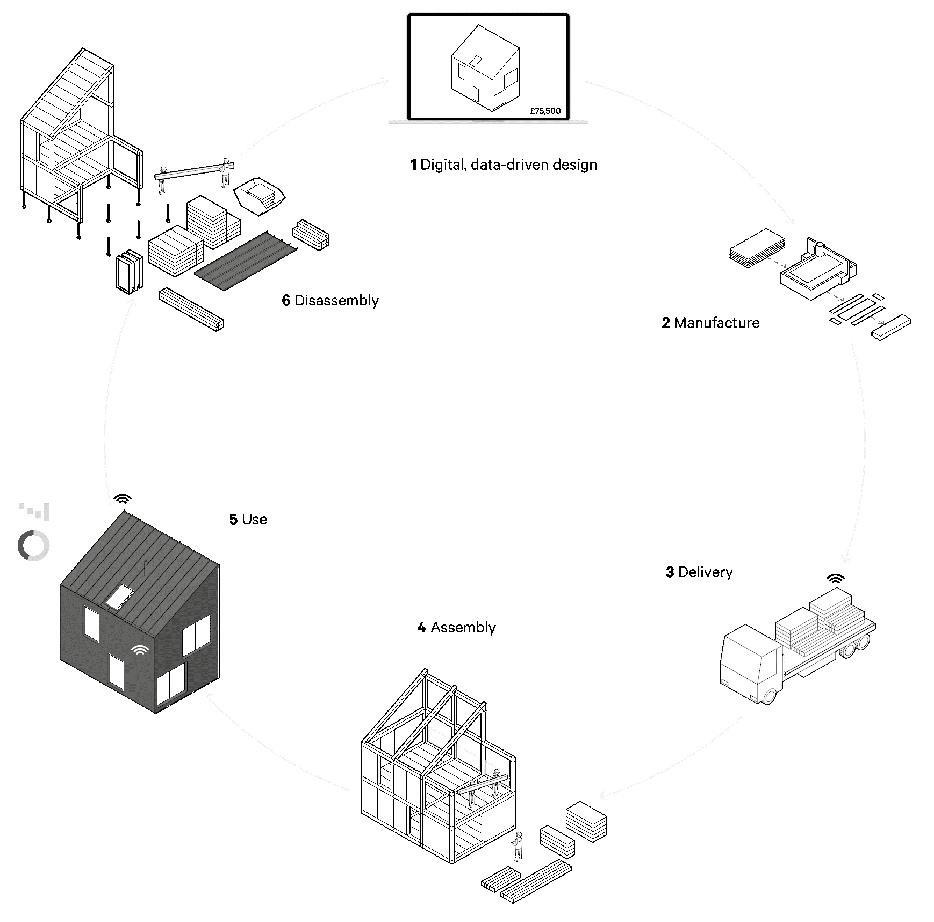
8 Life cycle assessment (LCA) LETI Climate Emergency Design Guide (2020) pg 57
Diagram adapted from Hawkins\Brown using illustrations from Open Systems Lab 2018 licensed under Creative Commons CC-BY-ND
Skelton Lake, Leeds, UK - Featuring 5,000m2 of Green Roof
Figure 2.1 - Life cycle assessment (LCA)
Concept Design
Key pe r fo rmance i nd ica to rs
Key Performance Indicators: LETI_Climate
M eet u pf ro nt
em bod i ed
ca r bo n
em i s si o n ta rg et s
fo r b u i l di n g
e l em ent s:
D o m es t i c
Design Guide
E q ui v. to 4 0 %
red uct i o n ove r
b a se l i n e
3 0 % m ate r i a l s f ro m re - u sed so u rces
5 0 % m ate r i a l s ca n b e re - u sed at e n d of l i fe
N on-
d o m es t i c
U pf ro nt em bod i ed ca r bo n em i s si o n s to be
Bu i l d i n g e l e m e nt ta rg et s i n c l u d e p ro d u ct s, t ra n s p o r t a n d co n s t r u ct i o n of
F i g u re s exc l u d e t i m b e r s e q u e s t rat i o n
Fig 9 Key Performance Indicators, Building element targets (include products, transport and construction of substructure, superstructure, MEP, façade and internal finishes (A1-A5). Figures exclude timber sequestration, LETI Climate Emergency Design Guide (2020), Pg 54
E q ui v to 4 0 % red uct i o n ove r b a se l i n e
3 0 % m ate r i a l s f ro m re - u sed so u rces
8 0 % m ate r
5 0 % m ate r i a l s ca n b e re - u sed at e n d of l i fe E q ui v. to 6 5 % red uct i o n ove r b a se l i n e 5 0 % m ate r i a l s f ro m re - u sed so u rces
b a se l i n e 5 0 % m ate r i a l s f ro m re - u sed so u rces
8 0 % m ate r i a l s ca n b e re - u sed at e n d of l i fe
Outcomes & Gateways
We have introduced Gateway checks at the end of each RIBA stage to enhance sustainability, improve design quality, and support better decision-making We believe these checks help minimise errors, enable continuous improvement, support our audit processes, and promote data-driven practices for efficient project execution and carbon reduction
Confirm preliminary advice has been actively sought from the local authority to ensure that the project exceeds the baseline sustainability requirements set by the Local Planning Authority, including BNG requirements
Verify that the project’s Form Factor has been accurately calculated and properly documented for future reference and accountability
Confirm all appointed Design Team members align with C&W’s sustainability goals and that their credentials in sustainable projects have been verified Depending on the complexity, this may include expertise in Passive House (PH) assessment, Whole Life Carbon assessment, and Life Cycle assessment
Ensure the plan has been continuously referenced throughout the project’s duration If a BREEAM project, confirm that BREEAM AP Stage 2 report has been completed to align with the programmeme’s guidelines
Continuously review the targets set during RIBA Stages 0/1 and evaluate whether the proposed construction meets the required building specifications in alignment with sustainability goals
Ensure the client has an indicative cost plan that demonstrates project targets can be met within the allocated budget Conduct additional feasibility studies if requested to verify this
If applicable, document key design decisions related to achieving sustainability targets within the formal stage report or, alternatively, provide a separate summary report
Embodied Carbon:
The carbon emissions emitted producing a building’s materials, their transport and installation on site as well as their disposal at end of life.
Fig 10 LETI Embodied Carbon, LETI Climate Emergency Design Guide (2020), pg 8
STAGE 3: SPATIAL COORDINATION
COORDINATION
Stage 3
Spatial Coordination
Overview
During this stage, the focus shifts from broad design to precise specifications, integrating sustainability more deeply The objective being to ensure compliance with statutory requirements while reducing environmental impacts, enhancing building longevity, and promoting user wellbeing The project’s aesthetics and functionality are finalised, with a focus on sustainable design and construction practices to enhance energy efficiency, minimise waste, and conserve resources Targets set in Stage 0/1 must be reviewed and reaffirmed, with any adjustments made, where necessary
Outcome: architectural and engineering information Spatially Coordinated
Preliminary Actions
• Refer to Stage 2 outputs and ensure compliance with the SDE has been achieved.
• If taking on the project at this stage from another colleague, studio or Practice, allow for relevant handover and clear understanding of sustainability targets.
• Ensure all Sustainability QME documentation is up to date and amend throughout the workstage.
• Carry out a comprehensive review of existing sustainability related reports and trackers and establish any immediate actions.
• Arrange a Design and Technical Review for the project with a sustainability focus.
• Where relevant, re-engage with Sustainability Consultant to ensure collaborative progression from Stage 2.
• Review and update project targets, and track any risks which may affect compliance.
Key Interactions
Client
Initiate Stage 3 with a focused meeting with the Client to confirm and, if necessary, realign the project’s sustainability targets and strategies This ensures all parties maintain a unified vision as the project progresses Maintain a continuous and open dialogue with the Client about the evolution of the design Inform clients promptly about necessary adjustments or enhancements, such as changes in specifications to enhance energy performance
Manufacturers and Suppliers
Alignment with accreditation goals is vital Actively refer to sustainable accreditation benchmarks such as BREEAM, LEED, or WELL standards to guide procurement choices Ensure all specified products and materials meet or exceed these sustainability targets to foster eco-friendly construction practices Obtain Environmental Product Declarations (EPDs) where required
Contractor
Initiate preliminary discussions with potential contractors to communicate the importance of compliance with both legal requirements and specific client-led sustainability initiatives Assess contractors’ previous experience and capabilities in delivering sustainable projects to ensure alignment with project goals Include sustainability criteria as a core component of the contractor selection process
Design Team
As a collective, ensure common goals are understood and targeted, avoiding progression in isolation which may lead to disparity in the design Sustainability updates and actions should be a regular feature in Design Team Meetings
Designers should review the guidance below to find the most appropriate or creative sustainable actions that continue to improve the project’s sustainability Design Teams should aim to include as many of these actions as possible to ensure they cover design development, choose the right materials, assess carbon impact, and complete final checks This should also include compliance reviews before submitting plans, making sure they meet Stage 3 sustainability requirements
1 Review and update the design according to the “7 Principles of Circular Design” established at Stage 2
2 Ensure structural design is optimised as this is where a significant proportion of embodied carbon sits
3 Choose a regular approach to the building grid and design to modular sizes to minimise wastage during construction
4 Ensure each building ‘layer’ is independent and exchangeable so that they can be altered or transformed without affecting other layers
5 Identify potential for using re-used products and materials, and design to incorporate these This may involve ‘baggy design’ whereby flexibility is built in Specifications to be confirmed later once re-used products have been procured
6 Prioritise quality and longevity of materials to maximise the building’s lifespan
7 Develop a construction and deconstruction plan Document the building components through material passports and BIM Wherever possible, specify products from manufacturers with established take-back schemes
8 Ensure energy modelling is carried out (or developed from Stage 2) to review the energy consumption and space heating demand are achieving the LETI targets for kWh/m² yr
9 Ensure building fabric targets are being met as part of the design process, reviewing the targets and noting noncompliance within stage report
10 Ensure the window area percentage is calculated and reviewed, as well as reconfirm that reasonable construction build-up allowances have been given to achieve the target U-values and airtightness
11 Consider MVHR routes as part of the design process, providing suitable space allowance
12 When detailing and coordinating the design, keep services separate from the external thermal and airtightness envelope to avoid weak points
13 Implementation of OneClick LCA or a similar software will be used to facilitate a comprehensive carbon footprint analysis of the entire project lifecycle
14 An extensive and comprehensive Whole Life Carbon study should be performed to encompass all aspects of the construction process This will feature a detailed analysis of embodied carbon for each individual element of construction, aiming to highlight areas where substantial carbon reductions can be achieved The study will focus on identifying ‘big ticket items’ - elements where the greatest carbon reductions can be realised, thus maximising our sustainability efforts
15 Develop an Adaptability Plan
16 Early energy modelling should be carried out to review the energy consumption and space heating demand are achieving the LETI targets for kWh/m² yr
17 Prior to the planning submission, undertake a final review of construction allowances to ensure viability of achieving target U-values and MVHR routes, as well as a ‘final’ window area calculation
Spatial Coordination
BREEAM
• Organise a meeting with the BREEAM Assessor to review the information submitted during Stage 2 design This will help identify the credits required for Stage 3
• Capitalise on the opportunity to enhance the evidence provided at previous stages as more information becomes accessible This iterative process is crucial for maximising the project’s sustainability potential
• Confirm the Life Cycle Assessment (LCA) for Mat01 has been duly submitted and registered with the Building Research Establishment (BRE) before proceeding with planning submissions This ensures that the project aligns with established sustainability standards and benchmarks
• Ensure any sustainability measures identified in targeted credits are included in the planning information, e g cycle storage, landscaping, and ecology measures
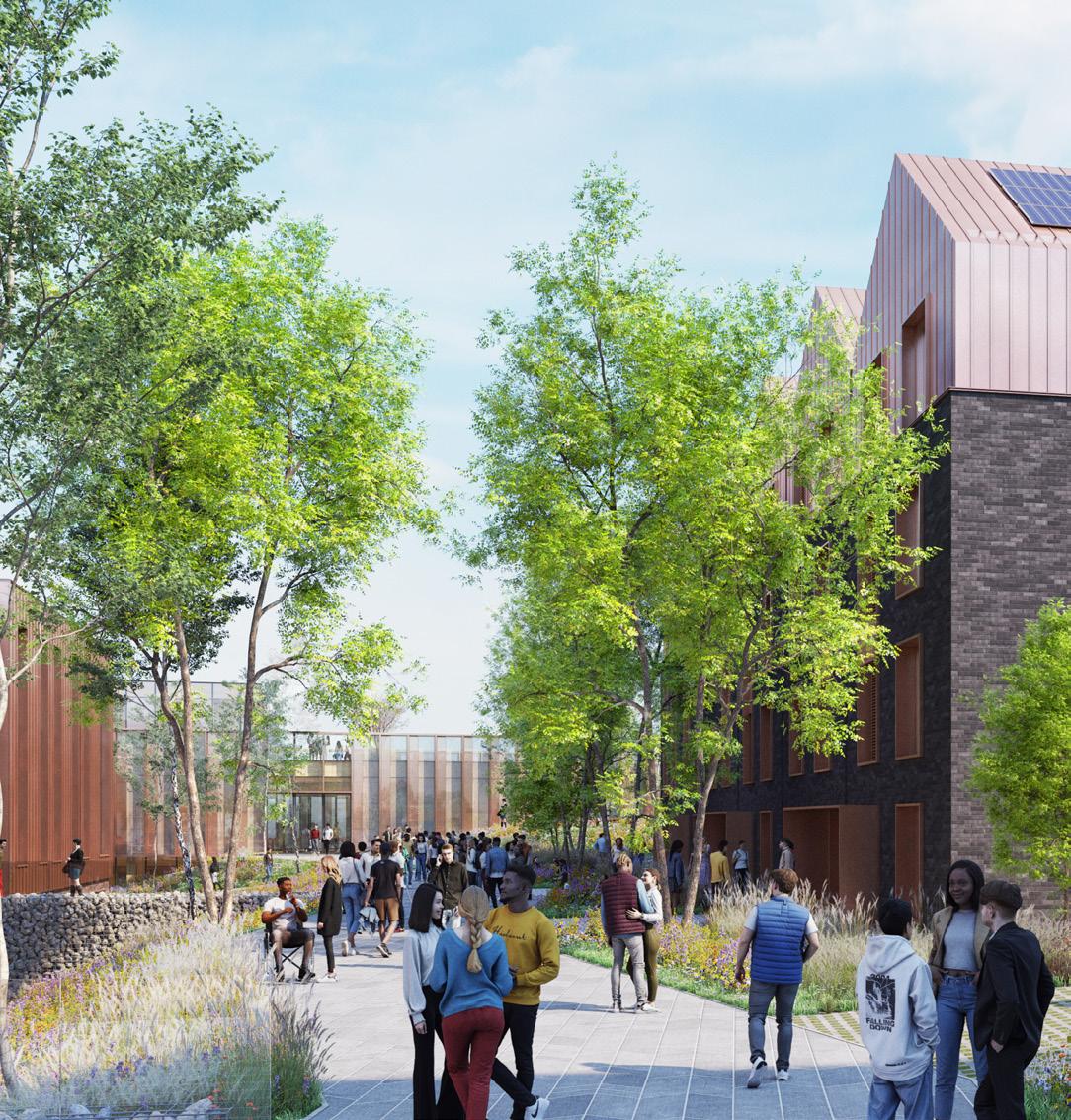
• Design solutions for Passive House requirements after Stage 3 becomes restricted to expensive solutions such as improved windows, solar shading etc This is the final stage to make any fundamental design changes such as improving form factor whilst being cost sensitive
• Update the Passive House Plan with the project team to reflect this stage of design development, review a cost optimised design against Passive House Certification criteria using PHPP, and review both the Certification Strategy and the Certification Status
• Liaise with in-house Passive House Designer/ Consultant and take onboard feedback from previous Information and progress design accordingly Synthesise design with feedback from preplanning application discussions
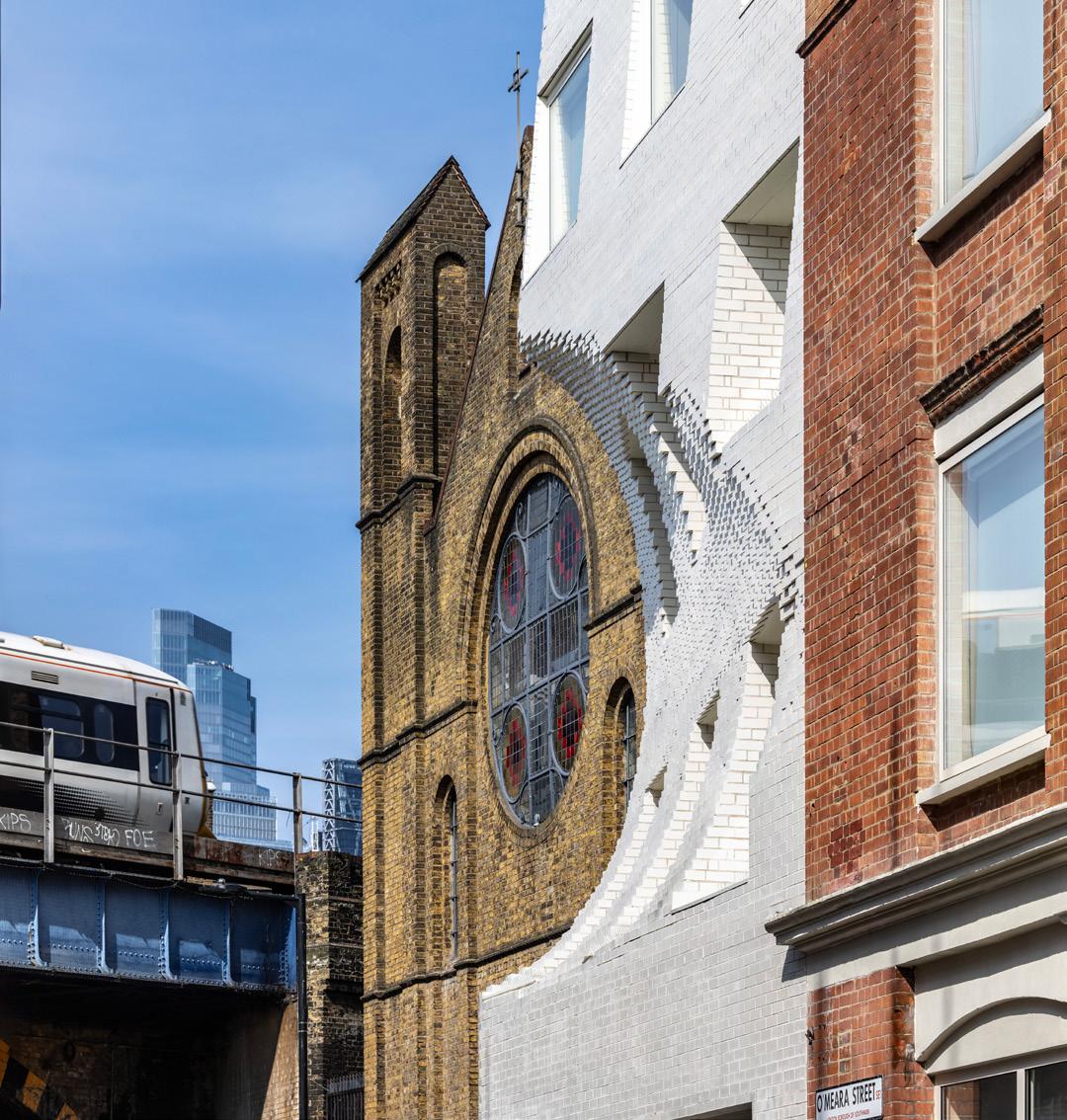
Staffordshire University Student Village, Stoke-on-Trent, UK
The Scoop, London, Uk Certification
Passive House
Certification
WELL
• Organise regular meetings to assess design progress again targeted WELL values and Pre-Conditions to ensure all evidence is captured This can be done in parallel with BREEAM to avoid duplication of relevant information
• Liaise with Design Team to implement WELL Framework, outlining which parties are to take responsibility for monitoring and submmitting evidence of compliance with relevant values
• Begin to develop strategies for how internal spaces will address mindfulness, comfort, and spatial quality of occupants, including;
- Light quality
- Temperature
- Safety and Security
- Materiality and aesthetics
- Social integration and activity
- Integrating natural elements into building
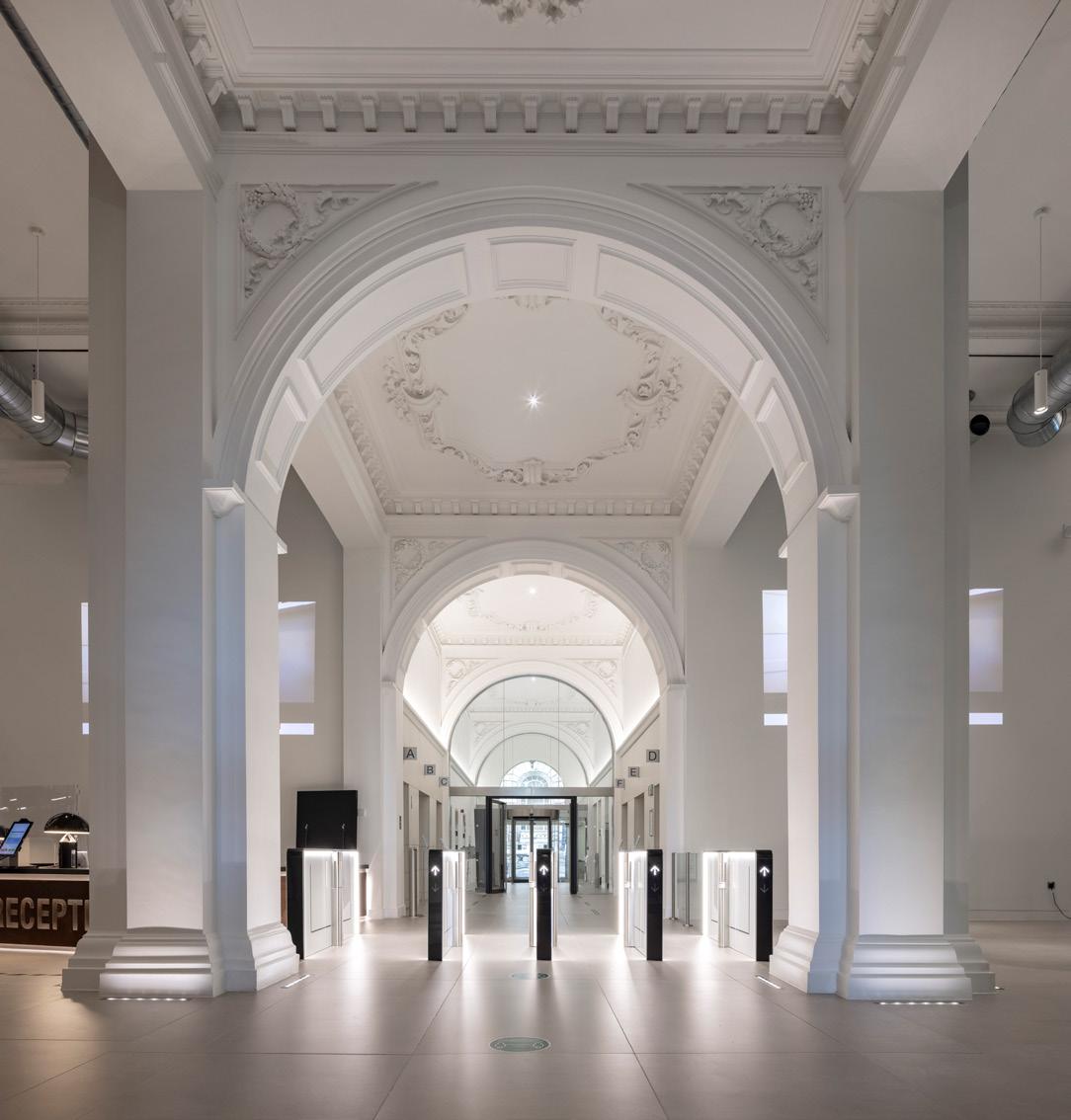
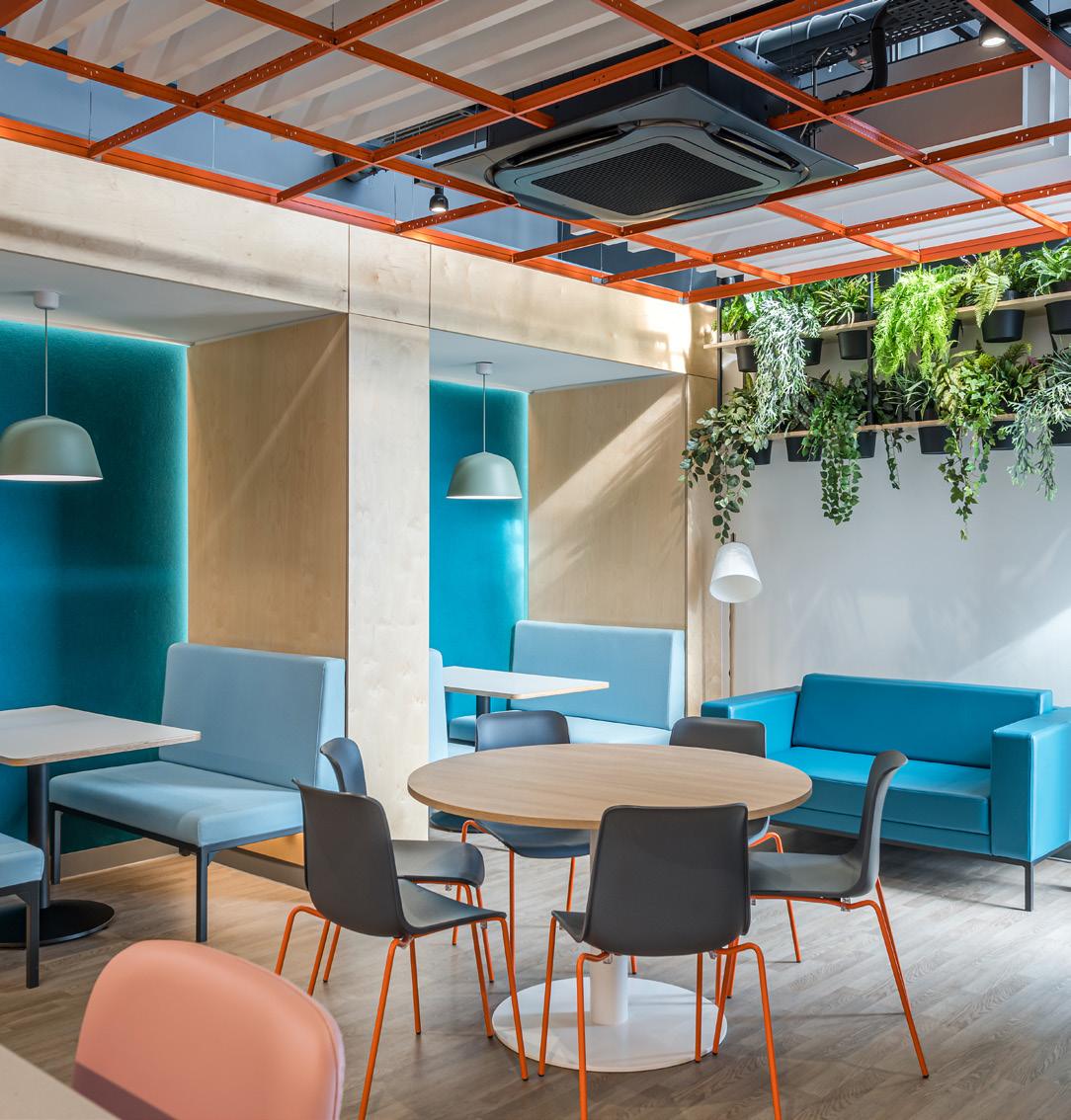
Royal Liver Building, Liverpool - Masterplan & Retrofit
Moray East Offshore Windfarm O&M Building, Fraserburgh
Spatial Coordination
Outcomes & Gateways
We have introduced Gateway checks at the end of each RIBA stage to enhance sustainability, improve design quality, and support better decision-making We believe these checks help minimise errors, enable continuous improvement, support our audit processes, and promote data-driven practices for efficient project execution and carbon reduction
Test sustainability targets eg by evaluating building performance following the Plan for Use
Integrate sustainability targets into coordinated spatial designs, aligning with stakeholder feedback
Identify and assess potential performance risks to guide the development of Stage 4 tasks and deliverables
Mitigate any deviation from sustainability targets, and record in QF206
If required, embed any requirements for POE into procurement strategy
Confirm that the design has been reviewed for compliance with local authority requirements and national environmental regulations as part of the planning package
Establish future milestones for accreditation approvals are clearly defined and communicated to all stakeholders
Ensure that deadlines for submissions relevant to sustainability accreditations have been met
Ensure all necessary reports (environmental impact assessments etc ) and drawings have been completed to support the planning application and sustainability objectives
Check the design allows for a realistic transition to Stage 4 without compromising on sustainability goals
Confirm that the selected products and materials are sustainable and easily accessible, and correctly specified to prevent significant changes during the Technical Design Stage
Establish all consultants, including environmental specialists, engineers, and architects, have fulfilled their roles as outlined in the Responsibility Matrix specific to this stage
Ensure there is clear documentation of each party’s contributions towards meeting the sustainability targets
Verify that the cost plan aligns with the sustainability strategy requirements for the project
Ensure any deviation from sustainability targets have been appropriately mitigated and recorded
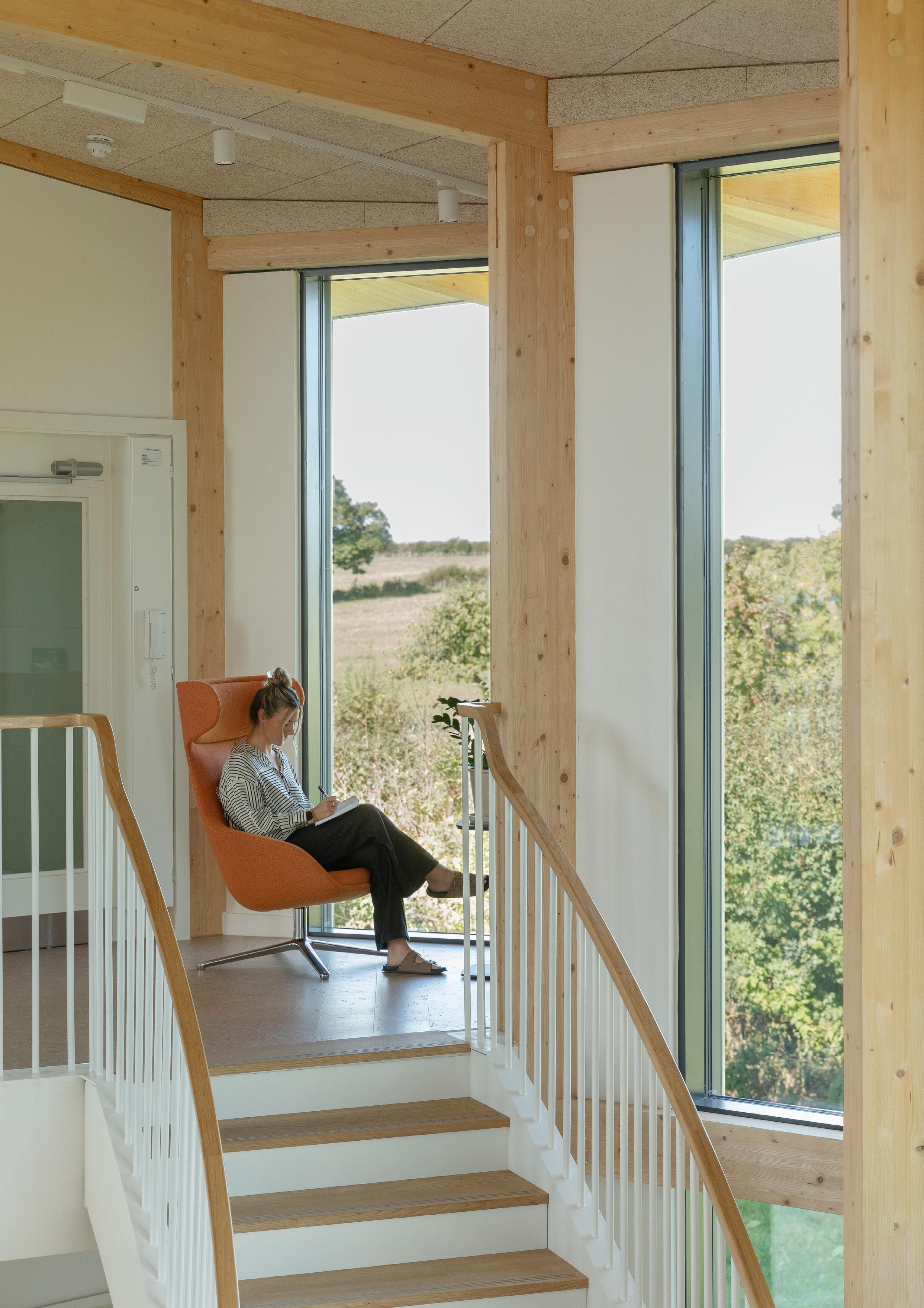
Image: Unusual Hq, Northampton, Uk
An Exemplar Test-Bed Project for Circular Economy Principles and Low-Carbon Design
STAGE 4: TECHNICAL DESIGN
Stage 4
Technical Design
Overview
Technical Design translates completed designs into actionable plans that adhere to our sustainable design ethos This phase focuses on specifying materials, systems, and techniques that meet high environmental standards It solidifies design decisions for construction, ensuring the projects sustainability goals are achievable
Effective collaboration with engineers, quantity surveyors, and specialists is central to refining sustainability strategies, ensuring technical viability and compliance with all regulatory and performance requirements
By meticulously detailing construction aspects, the aim is to minimise environmental impact, reduce operational costs, and enhance occupant wellbeing for long term viability
Outcome: Completion of all design info required for project manufacture and construction
Key Interactions
Client
Proactively communicate any design changes, such as the inclusion of plant screens on rooftops as mechanical, electrical, and plumbing (MEP) layouts are finalised, or adjustments in wall thickness to meet targeted U-values, to ensure alignment with sustainability goals Maintain transparency in the selection of suppliers and contractors, ensuring that sustainability credentials and performance metrics are key factors in the decision-making process
Manufacturers and Suppliers
Utilise a rigorously vetted list of suppliers and contractors specialising in sustainable materials and practices as recommended in the LETI Client Guide (p 56) during the Stage 4 design process Ensure transparency in supplier and contractor selection criteria based on sustainability credentials and performance metrics Oversee specialist contractors to ensure their designs align with sustainability targets through regular coordination meetings
Preliminary Actions
• Reassess Stage 3 outputs, including architectural plans and sustainability goals, to ensure alignment with established sustainability objectives, identifying areas for enhancement.
• Ensure all Sustainability QME documentation is up to date and amend throughout the workstage.
• Carry out a comprehensive review of existing sustainability related reports and trackers and establish any immediate actions.
• Establish and maintain clear communication channels among the design team, construction teams, and suppliers to ensure coherent implementation of sustainability objectives.
• Maintain a centralised technical library of sustainable materials and information to support consistent and high-quality design practices.
• Develop and implement a ‘Green Hierarchy’ to guide decision making and value engineering, prioritising sustainability in all design adjustments and cost considerations.
Contractor
Following the directives from stage 3, actively engage with the contractor to ensure their commitment towards achieving the sustainable targets Advocate for the appointment of local sub-contractors on the project where feasible, to support/promote local economies and reduce carbon footprint due to transportation
Design Team
Coordinate designs to ensure sustainable outcomes in the detailed design Regular design team meetings should focus on integrating sustainable materials, optimising energy efficiency, and aligning all systems with environmental goals The team should also refine construction methods to minimise waste and reduce the carbon footprint, ensuring the final design fully meets the project’s sustainability objectives
Designers should review the guidance below with aim of finding the most creative ways to maximise the project’s sustainability to meet Stage 4’s goals—technical design, energy efficiency, sustainability, material selection, and lifecycle considerations
1 Refer back to efficiency measures at start of technical design, embedding air tightness and thermal bridging within the design and tender requirements to ensure allowance within costing
2 Establish clear and prescriptive Whole Life Carbon requirements and targets at the start of the procurement process, incorporating them into project specifications and tender documentation to guide all stakeholders
3 Include specific queries regarding embodied carbon reduction and operational energy efficiency in the tender return forms, prompting contractors to propose innovative solutions and improvements
4 Rigorously align technical design elements with the operational carbon reduction targets through comprehensive modelling approaches, such as PHPP or Chartered Institution of Building Services Engineers TM54 (CIBSE TM54)
5 Ensure energy modelling is updated and developed to review that the energy consumption and space heating demand are achieving the LETI targets for kWh/m² yr
6 Coordinate with the Life Cycle Assessment (LCA) analyst to regularly update the Whole Life Costing (WLC) budget, ensuring it reflects all design changes and their impacts, and simultaneously maintain the Net Zero Carbon Risk Register to monitor and manage potential sustainability risks
7 Review details with the relevant specialist suppliers with regards to thermal bridging and airtightness
8 Ensure building fabric targets are being met as part of the design process, reviewing the targets and noting non-compliance within stage report
9 When detailing and coordinating the design, keep services separate from the external thermal and airtightness envelope to avoid weak points
10 Document all design modifications that impact the project’s energy consumption, detailing changes in occupancy patterns and building components to trace and manage the implications of energy performance
11 Explore and propose additional strategies to decrease operational energy demands, ensuring these are viable within the project constraints and client objectives
12 Encourage continuous engagement from all design team members in applying rigorous numerical analysis and utilising materials guides to enhance material specification decisions, focusing on sustainability without compromising on quality or functionality
13 Review and update the design according to the ‘7 Principles of Circular Design’ established at Stage 2
14 Design building components and junctions to maximise dismountability and reusability, ensuring a flexible building lifecycle that supports deconstruction and adaptation Mechanical fixings should be used rather than adhesives, welding, etc
15 Prioritise the use of natural and locally sourced materials in construction to reduce environmental impact and support regional economies
16 Specify products and materials that have take-back schemes and/or have obtained circular certifications, such as Cradle to Cradle, to promote environmental stewardship and ensure materials can be responsibly recycled or repurposed at the end of their life cycle
17 Consider products as a service approach, for example furniture and lighting This ensures they are re-used or recycled at the end of their useful life within the building
18 Ensure robust materials and detailing to maximise the lifespan of the building
Technical Design
Certification Certification
BREEAM
• Review, and ensure that previously targeted credits are being actively pursued and address any credits with imminent deadlines to maintain momentum
• Confirm that all specified construction products have an Environmental Product Declaration (EPD) to support the BREEAM ‘golden thread’ of project information
• Ensure Tender Information Pack includes all products required for the BREEAM credits targeted, and that these specifications align with the BREEAM credit requirements
• Update the Life Cycle Assessment (LCA) with the latest product and material information
• Review and update the Material Efficiency Report to reflect decisions and revisions made during Stage 4
• Update the Adaptation to Climate Change report to reflect the current design stage
• Revise the Design for Disassembly report to include recent design changes and strategies for Stage 4
• If dealing with contaminated land, ensure all remediation reports comply with BREEAM requirements
• Confirm that the landscaping and ecological measures are integrated into the tender package without conflicts
• If involved in contractor selection, ensure that contractor has the relevant accreditations and standards in place to satisfy the targeted credit
Passive House
• Ensure the PHPP model incorporates finalised inputs from all relevant consultants
• Conduct a comprehensive simulation using the final pre-construction model to verify alignment with sustainability targets
• Perform an in depth review of all construction junction details to confirm that they meet the specified targets for thermal bridging and airtightness
• Prioritise the use of certified junction details to ensure reliable Psi (linear thermal bridge coefficient) and Chi (point thermal bridge coefficient) values
• Require thermal bridging analysis for any junction details that deviate from standard certified solutions to maintain integrity in building envelope performance
• All critical building elements, including external fabric (insulation, facades) and service components (e g , doors, windows, mechanical ventilation with heat recovery (MVHR) units), must be specified to Passive House standards
• Ensure that all specified products are vetted for compliance with Passive House criteria to uphold energy efficiency and indoor environmental quality
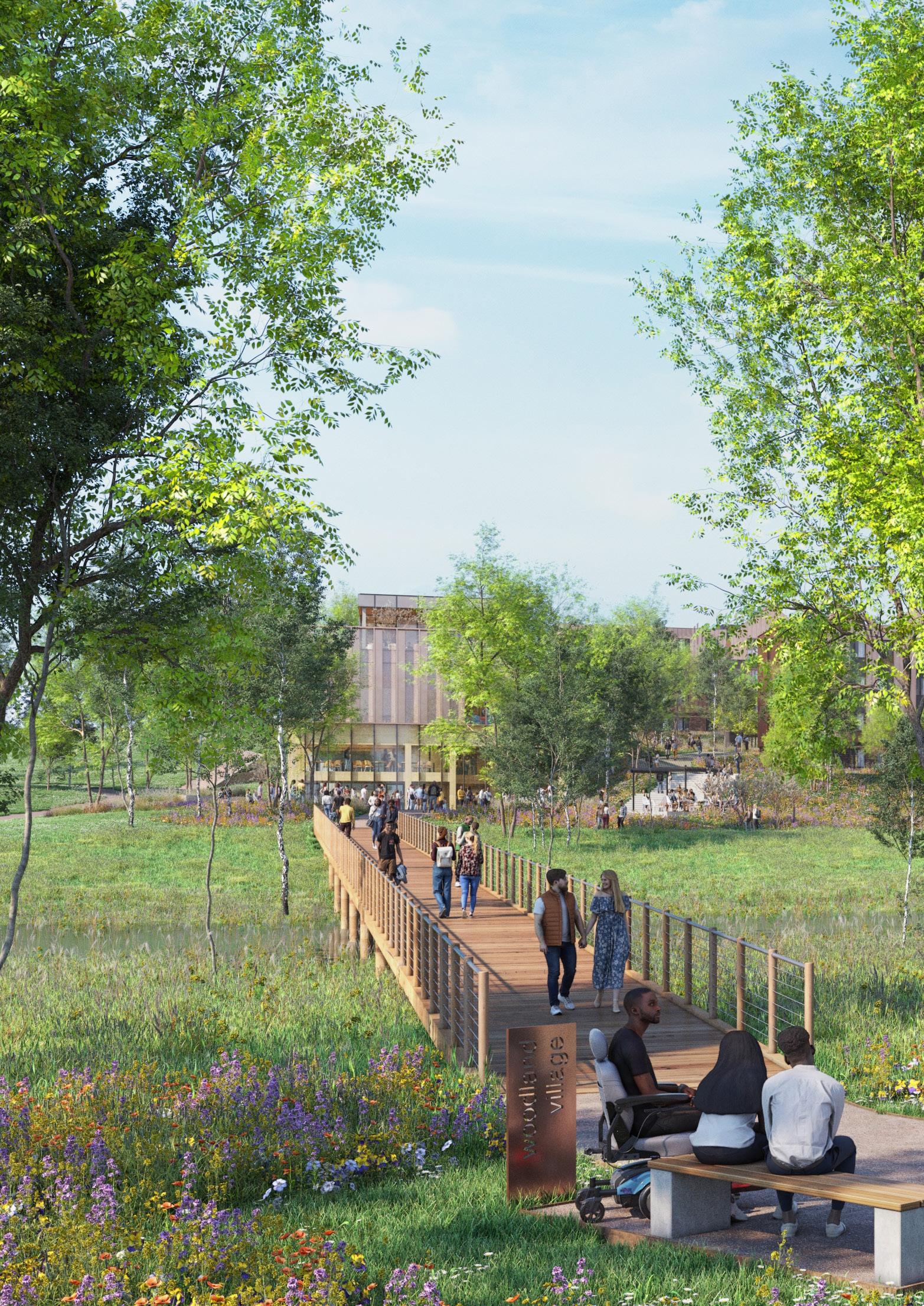
Image: Staffordshire University Village Hub, Stoke-on-Trent, UK Targeted Net Zero Carbon Development
Technical Design
Certification
WELL
• Work with our in-house WELL AP to update and track progress again target values
• Perform regular project reviews to ensure Design Team are aligned in path to certification
• Select materials that ensure indoor environments are safe and healthy
• Work with M&E Consultants to develop detailed strategy for occupant comfort, including controlling Solar Glare, regulating thermal comfort, air quality and employing lighting solutions that enhance mood and productivity
• Provide a clear strategy for how the design will provide aesthetically pleasing spaces and contribute to a sense of place and purpose, including selections of colour, materiality, spatial flow, social considerations and mindfulness
• Consider how the building specification can help improve occupant experience, reducing stress, enhance creativity, and improve overall wellbeing
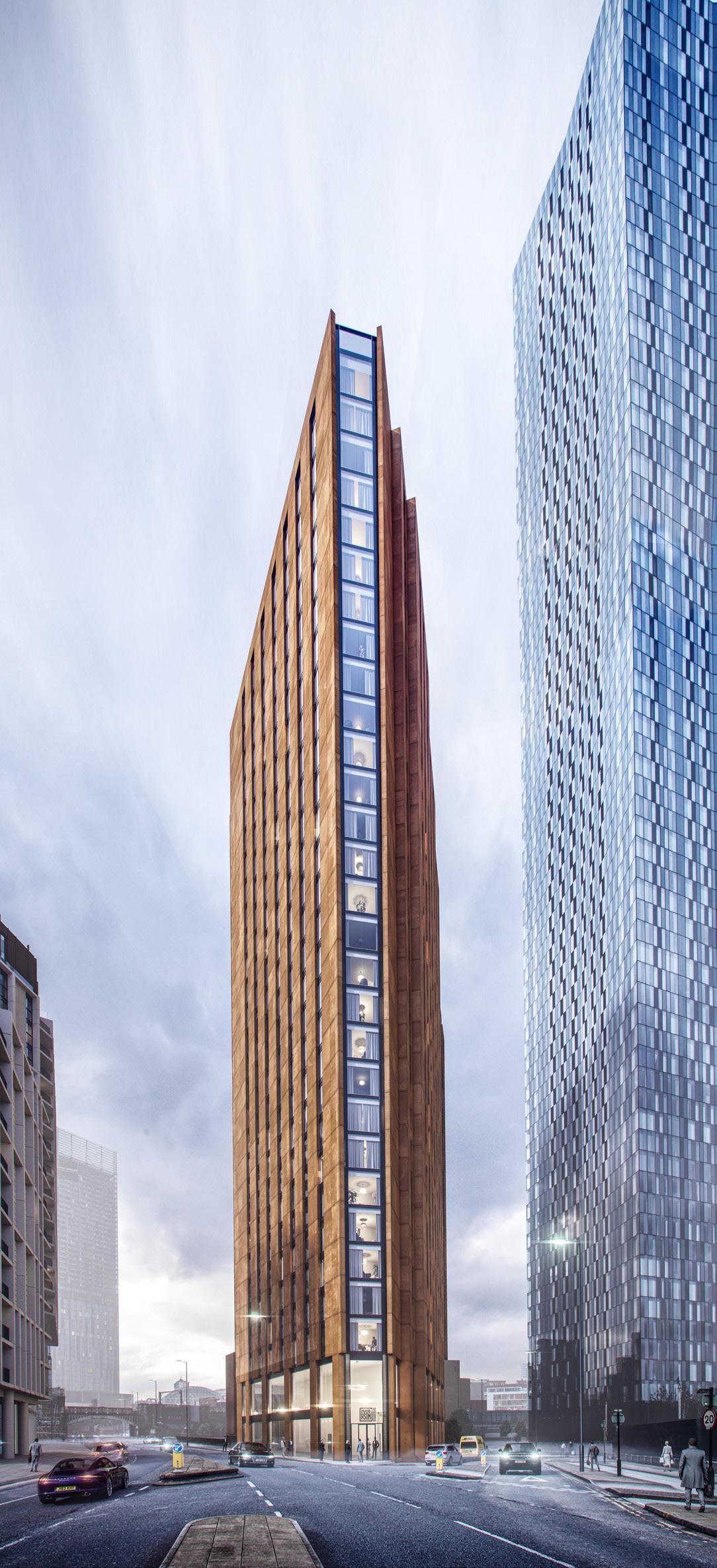
Deansgate, Manchester - Targeted BREEAM Rating of Excellent
Outcomes & Gateways
We have introduced Gateway checks at the end of each RIBA stage to enhance sustainability, improve design quality, and support better decision-making We believe these checks help minimise errors, enable continuous improvement, support our audit processes, and promote data-driven practices for efficient project execution and carbon reduction
Review Tender Returns against Sustainability Targets
Address sustainable targets and Parts F, G & L Regs and submit Building Regs Application
Minimise building performance and climate impact risks, and develop strategies to manage any remaining ones
Coordinate integration of manufacturing and construction information with the final specification, ensuring the incorporation of sustainability targets into the Plan for Use Strategy
Update any target commitments eg reduce carbon/energy/water use
Confirm that all technical documents, specifications, and drawings are complete, accurate, and readily accessible to smoothly transition into RIBA Stage 5 (Construction)
Conduct a thorough review of all sustainability targets to confirm that they are being met or exceeded Any variations due to value engineering (VE) must be critically assessed, justified, and documented in the appropriate location, to ensure continued compliance with sustainability accreditations
Ensure all contractors considered during the Tender Stage have been rigorously vetted to confirm their capability and commitment to meet the sustainability objectives outlined in the employer’s requirements
Confirm the selected contractor has committed to appointing a dedicated Net Zero Champion/Manager or Sustainability Champion This role is crucial to oversee and advocate for the sustainability targets throughout the construction process
Check design against established client targets, Any non-compliance is to be addressed through updating the design or revising the target by the end of the Stage
If applicable, document key design decisions related to achieving sustainability targets within the formal Stage Report or, alternatively, provide a separate summary report
STAGE 5: MANUFACTURING CONSTRUCTION
MANUFACTURING & CONSTRUCTION
Stage 5
Manufacturing & Construction
Overview
In Stage 5, designs transform from plans into functional buildings and the focus is on implementing sustainable practices such as using eco-friendly materials, energyefficient techniques, and waste reduction strategies
The goal is to ensure that the construction process is as environmentally responsible as possible, with lasting positive impacts on both the environment and building occupants
Outcome:
Manufacturing, construction and commissioning completed
Preliminary Actions
• Refer to Stage 4 outputs and ensure compliance with the SDE has been achieved.
• If taking on the project at this stage from another colleague, studio or Practice, allow for relevant handover and clear communication of sustainability targets.
• Ensure all Sustainability QME documentation is up to date and amend throughout the workstage.
• Confirm robust change control procedures are in place to safeguard the sustainability criteria, performance capabilities, and client targets of the building.
• Ensure the appointment of a dedicated Net Zero Champion or Sustainability Manager by the contractor to oversee and promote sustainability practices throughout the project.
• Monitor and discuss on-site waste reduction strategies with the site manager during site visits, ensuring continuation of practices initiated in the previous stages.
• Set up site visits to monitor construction processes and encourage the client to employ a Clerk of Works to assess the quality of work.
Key Interactions
Client
Advocate for the appointment of a Clerk of Works to oversee construction quality and adherence to sustainable practices Maintain ongoing communication with both the client and contractor throughout the project to stress the importance of meeting or surpassing the established sustainability objectives
Manufacturers and Suppliers
Employ rigorous quality control measures to assess materials, workmanship, and compliance with sustainable design specifications during the construction phase
Contractor
Collaborate with the contractor to ensure the implementation of effective quality assurance processes that uphold the integrity of the sustainable design
Use rigorous change control procedures to protect the sustainability criteria and performance capabilities of the building Engage actively with subcontractors and contractors in ongoing professional development, particularly for complex projects, and review sample construction details on-site before granting final approval
Design Team
Check regularly that the Design Team is meeting its sustainability responsibilities and commitments during this phase Confirm that they have the necessary authority, responsibilities, fees, and time to handle onsite queries effectively They should also frequently visit the site to help monitor construction, ensuring it aligns with the sustainable vision and design specifications
Guidance
For RIBA Stage 5, Design Teams should review the guidance below to identify ways to keep enhancing the project’s sustainability, adopting as many of the following steps as possible to ensure the building design stays sustainable This includes focusing on design quality, reusing materials, managing airtightness, and improving energy performance
1 Maintain a clear and effective Net Zero leadership presence on site during the construction phase and ensure that all site labour personnel are equipped with the necessary skills and motivation to successfully deliver a Net Zero Carbon Building
2 Ensure that precise and comprehensive installation details are readily available for all construction personnel to ensure seamless workflow
3 Encourage the contractor to start collating the O&M manual early, and provide a comprehensive document that captures specific information on building elements, including deconstruction or any existing end-of-life interest from suppliers or customers
4 Maintain strict adherence to the ‘7 Principles of Circular Design’ established during Stages 2-4 in any design development and detailing that transpires during the construction phase
5 Ensure both a waste management plan and re-use mandate are part of the contractor’s tender documentation The waste management plan should aspire towards 0% waste, with stringent targets set
6 Actively support and motivate contractors to source re-used materials wherever possible, with a special emphasis on materials such as steel and raised access flooring
7 Establish relationships with relevant re-use platforms in advance to ensure deconstructed materials/products have a route to market
8 Ensure the contractor appoints an Airtightness Champion to oversee all detailing on site, this is crucial to achieving low airtightness figures A preliminary air test is to be carried out as early as possible in the construction process to allow any potential remedial works to be easily carried out
9 Allocate a sufficient budget for the appointment of a highly trained Airtightness Manager and incorporate regular airtightness testing sessions throughout the construction phase into your schedule
10 Interrogate detailing on site with special attention on thermal bridging and airtightness
11 Consistently verify insulation continuity throughout the entirety of the construction phase to ensure maximum energy efficiency
12 Ensure building fabric targets are being met as part of the design process, reviewing the targets and noting non-compliance within stage report Ensure any design variations align with project targets
13 Implement regular monitoring systems to accurately verify auditable environmental credentials and construction carbon data at predetermined intervals throughout the construction process
14 Ensure the inspector responsible for the defects list has a thorough understanding and awareness of Net Zero Carbon principles and practices
15 Ensure energy modelling is updated and developed (if there are design changes during Stage 5) to review the energy consumption and space heating demand are achieving the LETI targets for kWh/m² yr
16 Ensure that Operations & Maintenance (O&M) manuals incorporate a detailed end-of-life deconstruction plan EPDs should be included for all materials The level of detail in these declarations may vary based on the specific requirements of the project
17 Prior to starting any deconstruction, prepare and agree on a method statement for disassembly with the contractor
18 Carry out trials of deconstructing key elements to understand and overcome barriers to re-use
Manufacturing & Construction
Certification
BREEAM
• Conduct a thorough review of the BREEAM credits achieved in the previous stages to ensure continuity and focus on achieving targeted credits
• Provide information for outstanding credits to the BREEAM assessor to ensure timely completion
• Confirm the contractor is fully informed about their responsibilities regarding BREEAM credits, particularly those related to sustainable practices such as waste management and responsible sourcing of materials
• Scrutinise any substitutions of materials or products to ensure they comply with the established BREEAM criteria, such as certifications for low VOCs and EPDs
• Check and compile necessary documentation and evidence needed to support BREEAM credit claims, including meeting minutes, correspondences, and other relevant records
Passive House
• Conduct regular site inspections to verify adherence to critical construction specifications, ensuring Passive House standards are met consistently
• Mandate the appointment of a certified airtightness specialist, to verify airtight construction details
• Schedule a preliminary airtightness test post-building envelope completion and prior to the commencement of interior finishes to allow for rectification of any issues
• Facilitate ongoing communication and coordination between the Passive House Certifier and the construction team to guarantee that construction details are documented and certified at each project stage
• Use the PHPP model to assess the impact of any proposed design modifications, ensuring that any changes are validated and agreed upon before implementation
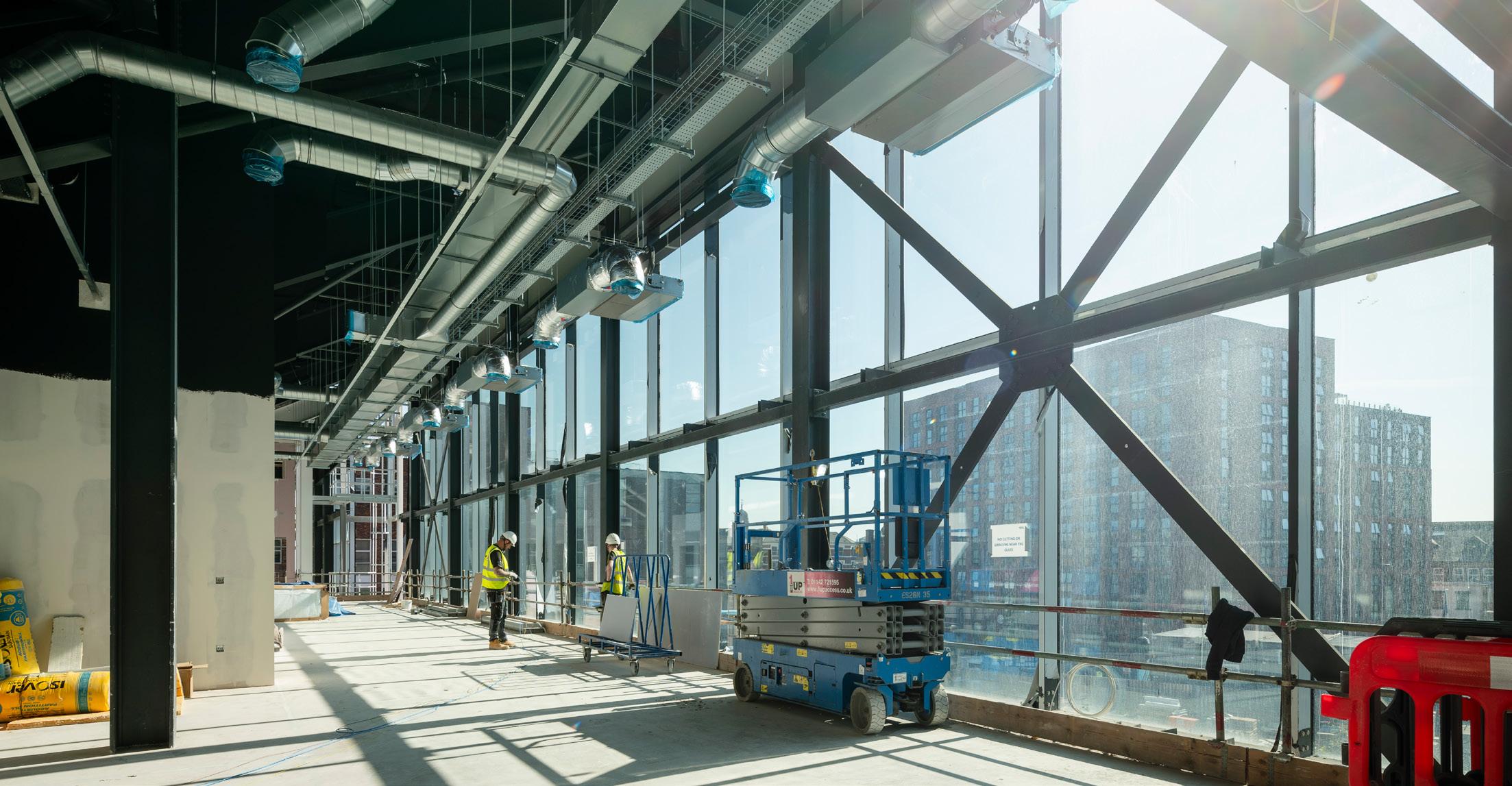
Becketwell Live, Performance Venue, Derby, Uk
Manufacturing & Construction
Outcomes & Gateways
We have introduced Gateway checks at the end of each RIBA stage to enhance sustainability, improve design quality, and support better decision-making We believe these checks help minimise errors, enable continuous improvement, support our audit processes, and promote data-driven practices for efficient project execution and carbon reduction
Ensure that all sustainability criteria such as U-values, air tightness, and other energy performance indicators have been achieved according to the project’s sustainability targets
Implement periodic reviews and testing during construction to confirm compliance Confirm that the building manual is complete and up to date prior to handover This manual should include detailed documentation of all building systems and materials, emphasising demountable and reusable components
Ensure that the manual highlights any sustainable features and their maintenance requirements to facilitate future adaptability and re-use
Issue of the Practical Completion Certificate, verifying that all construction works have been completed in accordance with contract specifications, including adherence to sustainable design principles outlined in earlier stages
Establish continuous monitoring mechanisms during construction to track sustainability targets Set up a clear and accessible record of sustainability targets that includes both achievements and areas for improvement This should be a living document that evolves with the project and provides a basis for post-construction reviews
Organise a formal review session post-construction to evaluate the sustainability outcomes against the initial targets This session should involve key project stakeholders, including design and construction teams, and should aim to document lessons learned as well as best practices for future projects
Initiate early feedback mechanisms concerning the sustainable features with the building’s end-users This feedback can be invaluable in assessing the practical aspects of sustainability measures and user interaction with the built environment
STAGE 6: HANDOVER
Stage 6
Handover
Overview
The aim of RIBA Stage 6 is to ensure a seamless handover by delivering all planned sustainable systems and features Clear documentation and guidance should be provided to help occupants maximise the benefits of the sustainable design
This stage also involves reflecting on the project’s performance to assess the effectiveness of our sustainable practices and to apply these insights to future projects
Outcome:
Successful Handover
Preliminary Actions
• Refer to Stage 4 & 5 outputs and ensure compliance with the SDE has been achieved.
• Ensure all Sustainability QME documentation is up to date and amended throughout the workstage.
• Carry out a comprehensive review of post practical completion asset information.
• Arrange a final review with the Design Team, end users and Sustainability Consultant to assess the sucesses of the project, gathering lessons learnt.
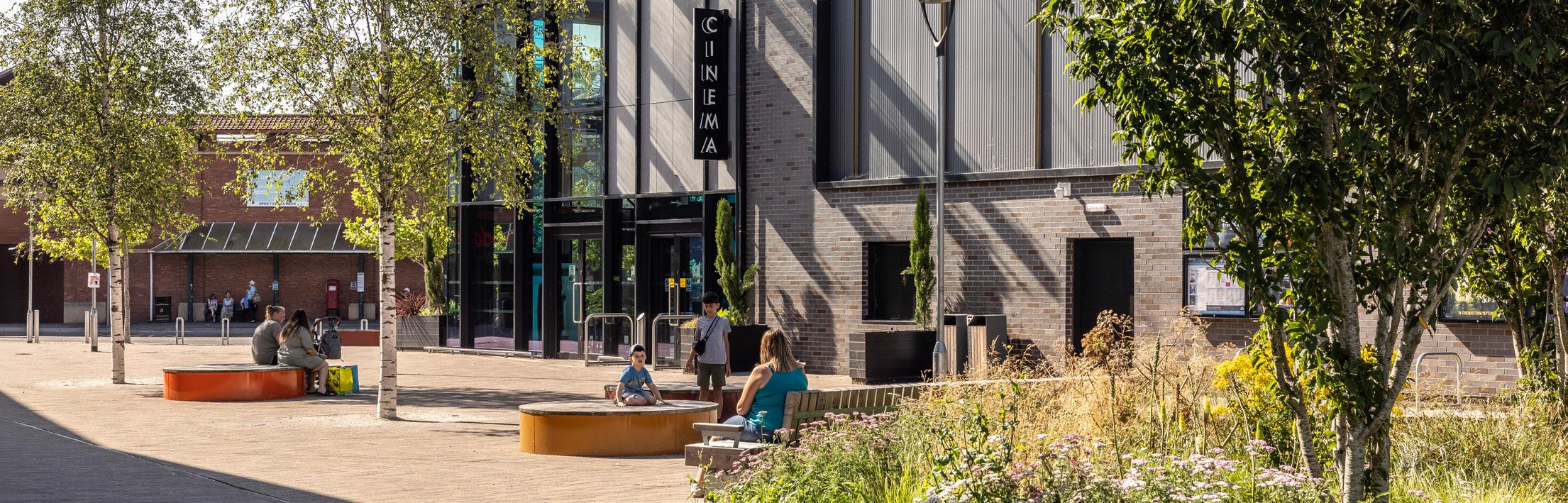
Key Interactions
Ensure the client is aligned and well informed on the maintenance and operation of the building in use, in line with the sustainability principles set throughout the project
Manufacturers and Suppliers
Provide certification and user manuals for relevant systems and building components, ensuring their longevity through proper maintenance and operation These documents should offer clear guidance for the client and maintenance teams Facilitate on-site training with suppliers and manufacturers to educate the client and maintenance teams on the correct operation and maintenance of sustainable systems This helps maximise efficiency and prolong the lifespan of key components
Secure Post construction feedback on processes that have impacted on buildability This is valuable for improving detailing, and building systems based on real world construction processes
Design Team
Deliver Record Drawings as part of a handover pack Operational carbon predictions, and Whole Life Carbon analysis will provide a final measure against meter readings to assess whether the project has been successful in achieving the sustainable targets
Client
Contractor
Northgate Yard, Bridgwater, UK
Guidance
Designers should regularly review the guidance below to identify and implement the most relevant actions that continue to enhance the project’s sustainability This involves ensuring the facilities team is prepared from the outset, integrating O&M manuals and circular economy principles, keeping the client informed and equipped with the necessary tools, and establishing a clear plan to evaluate the building’s performance after it is occupied
1 Engage the facilities/management team as early as possible into the built process, to enable them to contribute and have a good understanding of the new building
2 Ensure the O&M manuals include a detailed deconstruction and re-use plan for the building, including details of any buy-back programmemes associated with any building elements
3 Include the circular economy tracker ‘7 Principles of Circular Design’ as part of the handover information
4 At handover, hold workshops with the client explaining the format and information included in the material passports and other documentation produced
5 Ensure the client/building management can monitor and modify the information contained in the passports so that the documentation can be updated in case of maintenance works during the asset’s life
6 Ensure the handover documents brief the building users on the building fabric design and how this might affect their use of the building For example, additional penetrations through the external envelope should be avoided as this weakens the airtightness and thermal envelope
7 Arrange a date for a Post Occupancy Valuation, normally 1 year post Practical Completion
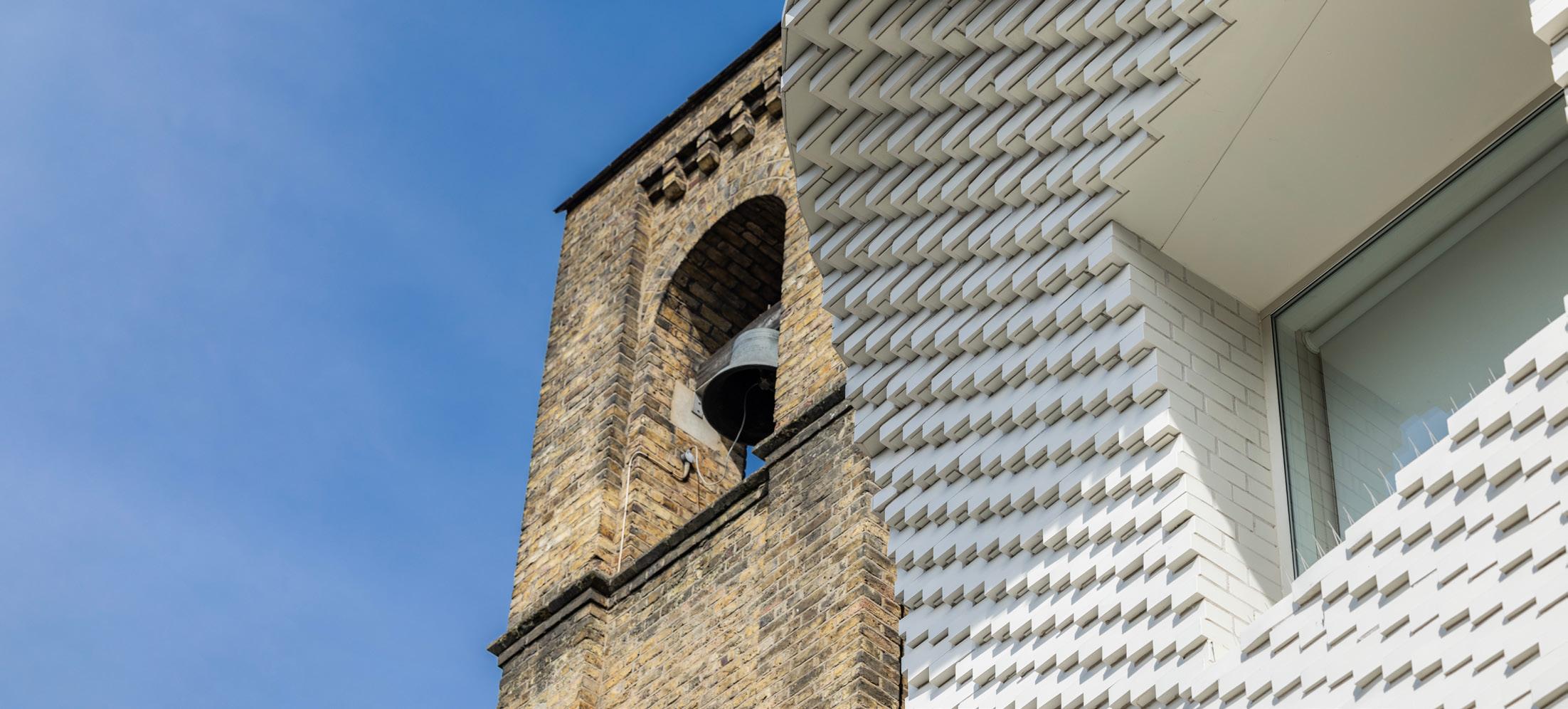
The Scoop, London, Uk - Award-winning building with retained facades
Handover
Outcomes & Gateways
We have introduced Gateway checks at the end of each RIBA stage to enhance sustainability, improve design quality, and support better decision-making We believe these checks help minimise errors, enable continuous improvement, support our audit processes, and promote data-driven practices for efficient project execution and carbon reduction
Review post practical completion, record drawings in line with the sustainable targets set at project outset
Ensure all relevant QME requirements have been completed
Carry out a final review with the design team to record lessons learned and record feedback
Review final position and certification of accreditations sought in line with the sustainability targets
Schedule a date for the post occupancy evaluation with end users and building owner to assess operational energy use
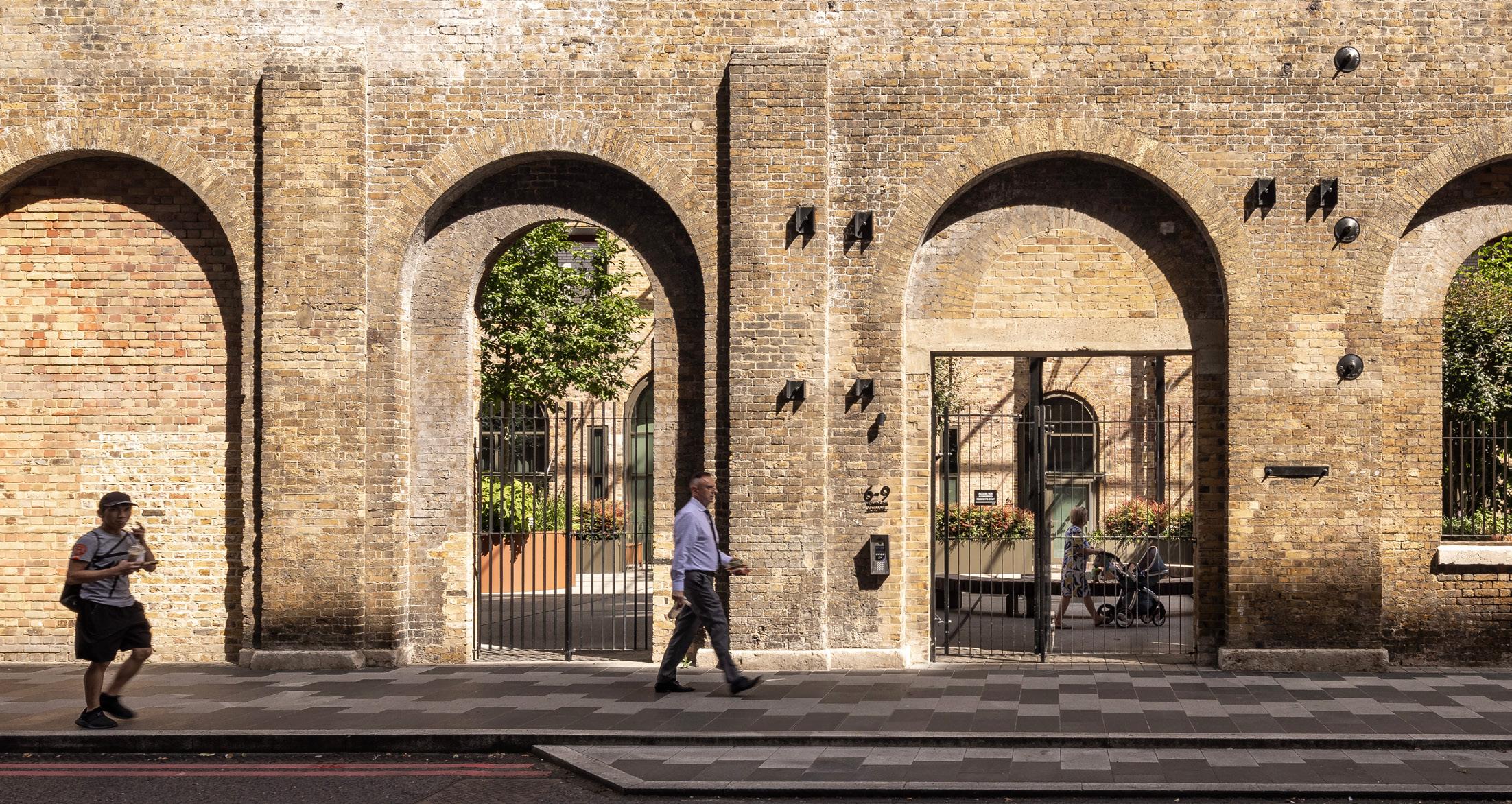
Windsor Square, London, UK
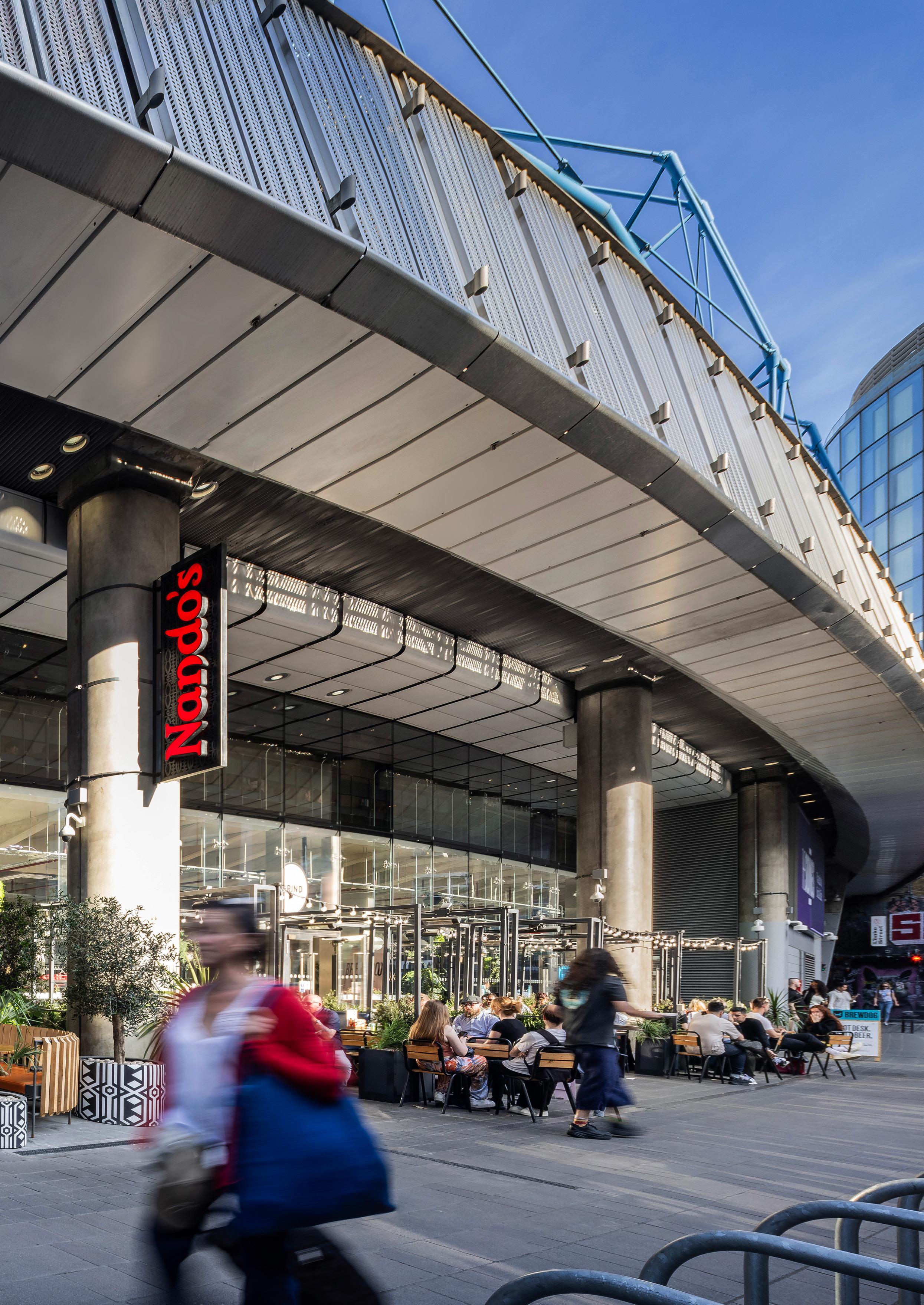
Image: The Sidings, Waterloo, London BREEAM Excellent Rated & Re-purposing of Existing
STAGE 7: USE
Stage 7
Use
Overview
RIBA Stage 7 focuses on testing and assessing our sustainable design measures in the built environment Although the Design Team’s direct involvement is limited, they remain dedicated to ensuring that the embedded sustainability principles function as intended Feedback and performance data is gathered during this stage
This is vital for refining our approach and improving future projects This ongoing analysis helps enhance our methods and achieve higher standards of environmental responsibility in each new project
Key Interactions Outcome: Building used, operated and maintained efficiently
Client
Provide ongoing guidance to the client on best practices for the building’s operation, ensuring that sustainable systems are used effectively, and the building’s environmental impact is minimised
Manufacturers and Suppliers
An assessment of the sustainability credentials including performance and longevity will help to inform on future material choices Staying informed with regards to new innovative materials and existing materials that perform well will help to guide sustainable specifications
Preliminary Actions
• Organise the post occupancy evaluation with end users and building owner to assess operational energy use.
• Assess fabric performance of sustainable materials used. Record findings to inform future decisions regarding durability, maintenance, and fitness for purpose.
• Ensure all findings are recorded as part of the project information and that all QME procedures are complete.
• Where possible, arrange a ‘lessons learned’ session to enhance learning across other projects.
Contractor
Continued communication during the defects period is valuable to understand the systems that were specified and learn where improvements can be made on future projects
Design Team
Provide feedback to the design team to address any operational challenges that have arisen, ensuring sustainable systems are optimised for long term success
Guidance
1 Carry out Post Occupancy Evaluation, and compare the building in-use against the design targets for energy consumption and space heating demand in kWh/m2 yr
2 Record the findings of the POE in the relevant location to inform future projects
Outcomes & Gateways
We have introduced Gateway checks at the end of each RIBA stage to enhance sustainability, improve design quality, and support better decision-making We believe these checks help minimise errors, enable continuous improvement, support our audit processes, and promote data-driven practices for efficient project execution and carbon reduction
Carry out the post occupancy evaluation with end users and building owner to assess operational energy use
Assess fabric performance of sustainable materials used Record findings to inform future decisions regarding durability, maintenance, and fitness for purpose
Review and record Post Occupancy Evaluation findings against the project’s sustainable targets Ensure all relevant QME requirements have been completed
Present ‘lessons learned’ within your studio as part of knowledge sharing
TARGETS & STANDARDS
STANDARDS
Targets and Standards
Our inclusion of Targets & Standards in the SDE reflects our commitment to delivering net-zero buildings—both new and refurbished—and ensures that everyone has access to the best advice on how to achieve this goal
Practices that follow the targets and standards set by organisations like LETI (London Energy Transformation Initiative) and RIBA can greatly improve the sustainability of their designs These guidelines provide clear, science-based benchmarks for reducing energy use, cutting carbon emissions, and improving resource efficiency By adopting these standards, our designers can create buildings that use less energy, rely more on renewable sources, and have a lower impact on the environment This not only helps combat climate change but also leads to healthier, more comfortable spaces for people to live and work in, while often saving money on energy costs in the long term
Further information regarding these targets and standards can be found on the Intranet




Fig 11 RIBA Sustainable Outcomes RIBA, Sustainable Outcomes Guide (2019), pg 8
The following pages provide examples of key design metrics from RIBA, LETI, and Passive House. These metrics support the Guidance section for each RIBA Stage within the SDE.
RIBA Sustainable Outcomes Metrics
1 Net Zero Operational Carbon Dioxide emissions, (kWh/m2/y and kgCO2e/m2/year)
The carbon dioxide produced as a result of the production and use of the energy from fossil fuels consumed for the day-to-day operation of the building or structure, including Low/zero carbon renewable energy technologies both on and off-site, plus recognised offset schemes where essential
As principally defined by CIBSE TM 54 Evaluating Operational Energy Use of Buildings at Design Stage, 2013, or Passive House PPHP
Target – Net Zero for new buildings and retrofit buildings
2 Net Zero Embodied Carbon Dioxide (kWh/m2/y and kgCO2e/floor area m2)
The carbon dioxide produced from the energy used in the extraction, fabrication and transportation from place of origin of the materials used in the construction, including recognised carbon offset schemes
As principally defined by RICS Whole Life Carbon Assessment for Built Environment, 2017
Target – Net Zero for new buildings and retrofit buildings including offsetting
3 Sustainable Water Cycle (m3/person/year)
Analogous to operational carbon dioxide, the amount of mains water used in the operation of the building including the offset by use of greywater or recycled water to reduce mains water consumption
As principally modelled by England and Wales building regulations water calculator
Target – To achieve 40% reduction in potable water use per person per day
4 Sustainable Connectivity and Transport (kgCO2e per km per person per annum)
The purpose of this outcome is to measure the resultant carbon impact of the travel of occupants and visitors to and from site or building to a local transport hub or local retail and community facilities
As principally defined by BREEAM 2018 Transport Credits
Target – To achieve Net Zero Carbon emissions per person per day
5 Sustainable Land Use and Bio-diversity (increase in new flora or fauna species on site)
The intention is that this outcome should be used as a measure of actions taken to maintain, protect and improving the flora and fauna on site
As principally defined by BREEAM 2018 bio-diversity credits, Urban Green Factor, London Plan
Target – To achieve net positive species impact and 0.3-0.4 urban green factor on all new sites
RIBA Sustainable Outcomes taken from “RIBA Sustainable Outcomes Guide”, 2019
6 Good Health and Wellbeing (various metrics)
This outcome includes key variables of internal occupant health and wellbeing, including Indoor Air Quality, Daylight, overheating, acoustic comfort, responsive controls, and physical contact to outside
As principally defined by CIBSE TM 40, 52, and 59, Good Homes Alliance overheating guidance and/or WELL Building Standard v2 Preconditions, 2019
Target – To achieve good indoor health metrics as per 2030 challenge, including CIBSE TM 40, TM 59 Overheating Avoidance RIBA Sustainable Outcomes Guide 11
7 Sustainable Communities and Social Value (various metrics)
The intention of this outcome is to measure the positive impacts of good placemaking on a local community
As principally defined by RIBA Social Value Toolkit, 2019
8 Sustainable Life Cycle Cost (£/m2)
The ensure a holistic outcome with regards to economic sustainability, the intention is to use Government Soft Landings requirement for measuring operational costs of buildings As principally defined by ICMS Global Consistency in Presenting Construction and Other Life Cycle Costs, 2019
RIBA Sustainable Outcomes taken from “RIBA Sustainable Outcomes Guide”, 2019 RIBA
The following section outlines practical recommendations and design measures approved by LETI and Passive House, which set clear benchmarks for ‘good’ design across the industry. These guidelines should be integrated into our design processes at all applicable stages to ensure we reduce both operational energy consumption and embodied carbon.
LETI Design Measures
The Sustainable Design Ethos (SDE) is founded on the application of established standards and strategies for both new and existing buildings The LETI Guidance, created by over 1,000 industry professionals, is widely accepted and supported by UK professional bodies

The Council House, Derby - BCO National Award Winner & BREEAM Excellent and EPC A+ Ratings
Small scale housing
Operational energy
Implement the following indicative design measures:
Fabric U-values (W/m2.K)
Walls
0.13 - 0.15
Floor 0.08 - 0.10
Roof 0.10 - 0.12
Exposed ceilings/floors 0.13 - 0.18
Windows 0.80 (triple glazing)
Doors 1.00
Efficiency measures
Air tightness <1 (m3/h. m2@50Pa)
Thermal bridging 0.04 (y-value)
G-value of glass 0.6 - 0.5
MVHR 90% (efficiency) ≤2m (duct length from unit to external wall)
Maximise renewables so that 100% of annual energy requirement is generated on-site
Form factor of 1.7 - 2.5
Embodied carbon
Focus on reducing embodied carbon for the largest uses:
Products/materials (A1-A3)
Transport (A4)
Construction (A5)
Maintenance and replacements (B1-B5)
End of life disposal (C1-C4)
Window areas guide (% of wall area) North 10-15% East 10-15% South 20-25% West 10-15%
Balance daylight and overheating
Include external shading
Include openable windows and cross ventilation
Reduce energy consumption to:
kWh/m2.yr Energy Use Intensity (EUI) in GIA, excluding renewable energy contribution
Reduce space heating demand to:
kWh/m2.yr
kgCO2/m2 Reduce embodied carbon by 40% or to:
Heating and hot water
Implement the following measures:
Fuel
Ensure heating and hot water generation is fossil fuel free
Heating
Demand response
Implement the following measures to smooth energy demand and consumption:
Peak reduction
Reduce heating and hot water peak energy demand
Maximum 10 W/m ventilation)
Maximum 10 W/m2 peak heat loss (including ventilation)
Hot water
Maximum dead leg of 1 litre for hot water pipework
'Green' Euro Water Label should be used for hot water outlets (e.g.: certified 6 L/min shower head – not using flow restrictors).
Active demand response measures
Install heating set point control and thermal storage
Electricity generation and storage Consider battery storage
Electric vehicle (EV) charging Electric vehicle turn down
Behaviour change
Incentives to reduce power consumption and peak grid constraints.
Data disclosure
Meter and disclose energy consumption as follows:
Metering
1. Submeter renewables for energy generation
2. Submeter electric vehicle charging
3. Submeter heating fuel (e.g. heat pump consumption)
4. Continuously monitor with a smart meter
5. Consider monitoring internal temperatures
6. For multiple properties include a data logger alongside the smart meter to make data sharing possible.
Disclosure 123
1. Collect annual building energy consumption and generation
2. Aggregate average operational reporting e.g. by post code for anonymity or upstream meters
3. Collect water consumption meter readings
4. Upload five years of data to GLA and/or CarbonBuzz online platform
5. Consider uploading to Low Energy Building Database.
Medium and large scale housing
Operational energy
Implement the following indicative design measures:
Fabric U-values (W/m2.K)
Walls 0.13 - 0.15
Floor 0.08 - 0.10
Roof 0.10 - 0.12
Exposed ceilings/floors 0.13 - 0.18
Windows 1.0 (triple glazing)
Doors 1.00
Efficiency measures
Air tightness
<1 (m3/h.m2@50Pa)
Thermal bridging 0.04 (y-value)
G-value of glass 0.6 - 0.5
MVHR 90% (efficiency) ≤2m (duct length from unit to external wall)
Maximise renewables so that 70% of the roof is covered
Form factor of <0.8 - 1.5
Embodied carbon
Focus on reducing embodied carbon for the largest uses:
Products/materials (A1-A3)
Transport (A4)
Construction (A5)
Maintenance and replacements (B1-B5)
End of life disposal (C1-C4)
Window areas guide (% of wall area)
North 10-20%
East 10-15%
South 20-25%
West 10-15%
Include external shading
Include openable windows and cross ventilation Balance daylight and overheating
Energy Use
Intensity (EUI) in GIA, excluding renewable energy contribution
Reduce energy consumption to: 35 kWh/m2.yr
Reduce space heating demand to:
15 kWh/m2.yr
Reduce embodied carbon by 40% or to:
<500 kgCO2/m2
Area in GIA
Small resi Med/high resi
Heating and hot water
Implement the following measures:
Fuel
Ensure heating and hot water generation is fossil fuel free
Heat
The average carbon content of heat supplied (gCO2/kWh.yr) should be reported in-use
Heating
Maximum 10 W/m2 peak heat loss (including ventilation)
Hot water
Maximum dead leg of 1 litre for hot water pipework
'Green' Euro Water Label should be used for hot water outlets (e.g.: certified 6 L/min shower head – not using flow restrictors).
Demand response
Implement the following measures to smooth energy demand and consumption:
Peak reduction
Reduce heating and hot water peak energy demand
Active demand response measures
Install heating set point control and thermal storage
Electricity generation and storage
Consider battery storage
Electric vehicle (EV) charging Electric vehicle turn down
Behaviour change
Incentives to reduce power consumption and peak grid constraints.
Data disclosure
Meter and disclose energy consumption as follows:
1. Submeter renewables for energy generation
2. Submeter electric vehicle charging
3. Submeter heating fuel (e.g. heat pump consumption)
4. Continuously monitor with a smart meter
5. Consider monitoring internal temperatures
6. For multiple properties include a data logger alongside the smart meter to make data sharing possible. Metering
Disclosure 123
1. Collect annual building energy consumption and generation
2. Aggregate average operational reporting e.g. by post code for anonymity or upstream meters from part or whole of apartment block
3. Collect water consumption meter readings
4. Upload five years of data to GLA and/or CarbonBuzz online platform
5. Consider uploading to Low Energy Building Database.
Commercial offices
Operational energy
Implement the following indicative design measures:
Fabric U-values (W/m2.K)
Walls 0.12 - 0.15
Floor 0.10 - 0.12
Roof 0.10 - 0.12
Windows 1.0 (triple glazing)1.2 (double glazing)
Doors 1.2
Fabric efficiency measures
Air tightness <1 (m3/h. m2@50Pa)
Thermal bridging 0.04 (y-value)
G-value of glass 0.4 - 0.3
Power efficiency measures
Lighting power density 4.5 (W/m2 peak NIA)
Lighting out of hours 0.5 (W/m2 peak NIA)
Tenant power density 8 (W/m2 peak NIA)
ICT loads 0.5 (W/m2 peak NIA)
Small power out of hours 2 (W/m2 peak NIA)
System efficiency measures
MVHR 90% (efficiency)
Heat pump SCoP ≥ 2.8
Chiller SEER ≥ 5.5
Central AHU SFP 1.5 - 1.2 W/l.s
A/C set points 20-26oC
Embodied carbon
Focus on reducing embodied carbon for the largest uses:
Products/materials (A1-A3)
Transport (A4)
Construction (A5)
Maintenance and replacements (B1-B5)
End of life disposal (C1-C4)
Window areas guide (% of wall area)
North 25-40%
East 25-40%
South 25-40%
West 25-40%
Balance daylight and overheating
Include external shading
Include openable windows and cross ventilation
Reduce energy consumption to:
Energy Use
55 kWh/m2.yr
Intensity (EUI) in GIA, excluding renewable energy contribution
Maximise renewables to generate the annual energy requirement for at least two floors of the development on-site
Form factor of 1 - 2
Heating and hot water
Implement the following measures:
Fuel
Ensure heating and hot water generation is fossil fuel free
Heat
The average carbon content of heat supplied (gCO2/kWh.yr) should be reported in-use
Heating
Maximum 10 W/m2 peak heat loss (including ventilation)
Connect to community wide ambient loop heat-sharing network to allow excess heat from cooling to be made available to other buildings
Hot water
Maximum dead leg of 1 litre for hot water pipework
'Green' Euro Water Label should be used for hot water outlets (e.g.: certified 6 L/min shower head – not using flow restrictors).
Demand response
Implement the following measures to smooth energy demand and consumption:
Peak reduction
Reduce heating and hot water peak energy demand
Active demand response measures
Install heating and cooling set point control
Reduce lighting, ventilation and small power energy consumption
Electricity generation and storage
Consider battery storage
Electric vehicle (EV) charging Electric vehicle turn down Reverse charging EV technology
Behaviour change
Incentives to reduce power consumption and peak grid constraints
Encourage responsible occupancy.
Data disclosure
Meter and disclose energy consumption as follows:
Metering
(Metering strategy following BBP Better Metering Toolkit guidance)
1. Record meter data at half hourly intervals
2. Separate landlord and tenant energy use meters and clearly label meters with serial number and end use
3. Submeter renewable energy generation
4. Use a central repository for data that has a minimum of 18 months data storage
5. Provide thorough set of meter schematics and information on maintenance and use of meters
6. Ensure metering commissioning includes validation of manual compared to half hourly readings.
Disclosure 123
1. Carry out an annual Display Energy Certificate (DEC) and include as part of annual reporting
2. Report energy consumption by fuel type and respective benchmarks from the DEC technical table
3. For multi-let commercial offices produce annual landlord energy (base building) rating and tenant ratings as well as or instead of a whole building DEC
4. Upload five years of data to a publicly accessible database such as GLA and/or CarbonBuzz.
Schools
Operational energy
Implement the following indicative design measures:
Fabric U-values (W/m2.K)
Walls 0.13 - 0.15
Floor 0.09 - 0.12
Roof 0.10 - 0.12
Windows 1.0 (triple glazing)
Doors 1.2
Fabric efficiency measures
Air tightness
<1 (m3/h. m2@50Pa)
Thermal bridging 0.04 (y-value)
G-value of glass 0.5 - 0.4
Power efficiency measures
Lighting power density 4.5 (W/m2 peak NIA)
Lighting out of hours 0.5 (W/m2 peak NIA)
Small power out of hours 2 (W/m2 peak NIA)
System efficiency measures
MVHR 90% (efficiency)
Heat pump SCoP ≥ 2.8
Central AHU SFP 1.5 - 1.2 W/l.s
Maximise renewables so that 70% of the roof is covered
Embodied carbon
Focus on reducing embodied carbon for the largest uses:
Products/materials (A1-A3)
Transport (A4)
Construction (A5)
Maintenance and replacements (B1-B5)
End of life disposal (C1-C4)
Window areas guide (% of wall area)
North 15-25%
East 15-25%
South 15-25% West 15-25%
Include openable windows and cross ventilation Balance daylight and overheating Include external shading
Form factor of 1 - 3
Reduce energy consumption to:
Energy Use
kWh/m2.yr
Reduce space heating demand to:
Intensity (EUI) in GIA, excluding renewable energy contribution
kWh/m2.yr
Average split of embodied carbon per building element:
- Façade 13% - MEP
Heating and hot water
Implement the following measures:
Fuel
Ensure heating and hot water generation is fossil fuel free
Heat
The average carbon content of heat supplied (gCO2/kWh.yr) should be reported in-use
Heating
Maximum 10 W/m2 peak heat loss (including ventilation)
Hot water
Maximum dead leg of 1 litre for hot water pipework
'Green' Euro Water Label should be used for hot water outlets (e.g.: certified 6 L/min shower head – not using flow restrictors).
Demand response
Implement the following measures to smooth energy demand and consumption:
Peak reduction
Reduce heating and hot water peak energy demand
Active demand response measures
Install heating and cooling set point control
Reduce lighting, ventilation and small power energy consumption
Electricity generation and storage Consider battery storage
Electric vehicle (EV) charging Electric vehicle turn down Reverse charging EV technology
Behaviour change
Incentives to reduce power consumption and peak grid constraints Encourage responsible occupancy.
Data disclosure
Meter and disclose energy consumption as follows:
Metering
(Metering strategy following BBP Better Metering Toolkit guidance)
1. Record meter data at half hourly intervals
2. Clearly label meters with serial number and end use
3. Submeter renewable energy generation
4. Use a central repository for data that has a minimum of 18 months data storage
5. Provide thorough set of meter schematics and information on maintenance and use of meters
6. Ensure metering commissioning includes validation of manual compared to half hourly readings.
Disclosure 123
1. Carry out an annual Display Energy Certificate (DEC) and include as part of annual reporting
2. Report energy consumption by fuel type and respective benchmarks from the DEC technical table
3. Upload five years of data to a publicly accessible database such as GLA and/or CarbonBuzz. Include information about the building (do not anonymise).
and Standards
For a building to be considered a Passive House, it must meet the following criteria (for detailed criteria, please see the building certification section):
1 The Space Heating Energy Demand is not to exceed 15 kWh per square meter of net living space (treated floor area) per year or 10 W per square meter peak demand
In climates where active cooling is needed, the Space Cooling Energy Demand requirement roughly matches the heat demand requirements above, with an additional allowance for dehumidification
2 The Renewable Primary Energy Demand (PER, according to PHI method), the total energy to be used for all domestic applications (heating, hot water and domestic electricity) must not exceed 60 kWh per square meter of treated floor area per year for Passive House Classic
3 In terms of Airtightness, a maximum of 0 6 air changes per hour at 50 Pascals pressure (ACH50), as verified with an onsite pressure test (in both pressurised and depressurised states)
4. Thermal Comfort must be met for all living areas during winter as well as in summer, with not more than 10 % of the hours in a given year over 25 °C For a complete overview of general quality requirements (soft criteria) see Passipedia
Passive House buildings are planned, optimised, and verified with the Passive House Planning Package (PHPP)
All of the above criteria are achieved through intelligent design and implementation of the 5 Passive House principles: thermal bridge free design, superior windows, ventilation with heat recovery, quality insulation and airtight construction Passive House Standards
The following five basic principles apply for the construction of Passive Houses:
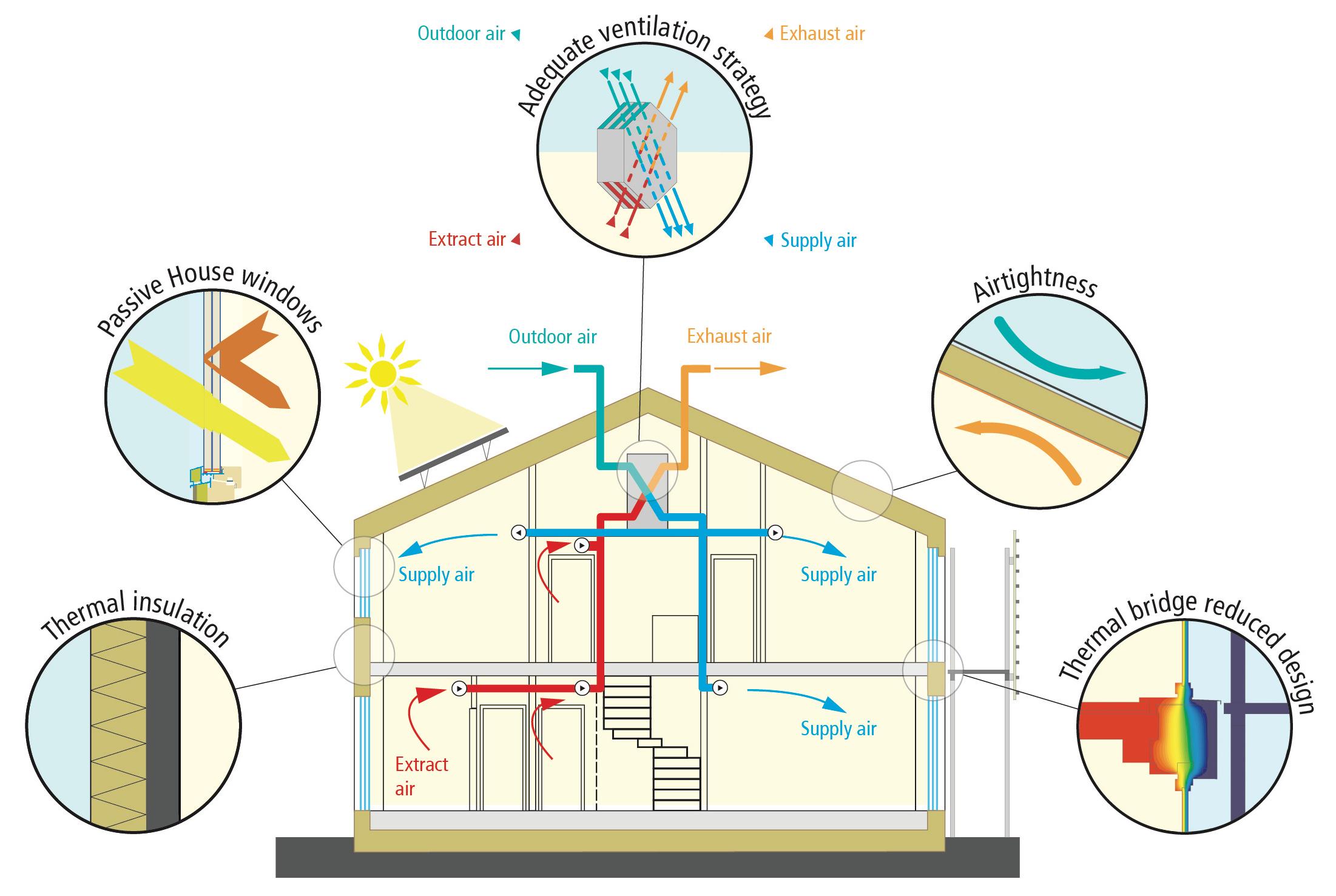
with U-value ≤ 0.8 W/(m²K).
Ventilation heat recovery (MVHR) - ≥ 75% of exhaust air heat recovered.
4. Airtight construction - Max. 0.6 air changes per hour (n50 ≤ 0.6/h).
5. Thermal bridges - Avoided or minimised through carefully planned detailing.
Note: Passive House standards are applicable to all building types, not only housing.
Fig 13 Basic principles to apply for the construction of Passive Houses https://passivehouse.com/02_informations/02_passive-house-requirements/02_passive-house-requirements.htm
1. Excellent thermal insulation - U-values ≤ 0.15 W/(m²K).
2. High performance windows - Triple glazing
3.
GLOSSARY OF TERMS
Glossary of Terms
Definitions
Biogenic Building Materials: Materials which come from living organisms and are formed through natural biological processes, for example timber frame, hempcrete, wood fibre insulation
Biogenic Carbon: Carbon that is absorbed and sequestered in biological materials, such as plants, trees and soil This can also refer to any emissions associated with this sequestered carbon
Carbon Factor: This refers to the measure used to calculate the carbon emissions from the electricity used in buildings The amount of carbon varies depending on how the electricity is produced In the UK, the carbon factor changes throughout the day and seasons because the amount of renewable energy being generated changes
Carbon Sequestration: A natural or artificial process by which carbon dioxide is removed from the atmosphere and held in solid or liquid form, e g reforestation or, in the built environment through using timber
Carbon Sink: Something that takes up more carbon from the atmosphere than it releases
Circular Economy: A Circular Economy is an industrial system that is restorative or regenerative by intention and design It replaces the linear economy and its ‘Endof-Life’ concept with restoration, shifts towards the use of renewable energy, eliminates the use of toxic chemicals and aims for the elimination of waste through the design of materials, products, systems
Cradle-to-Cradle: This concept improves on the “cradle to grave” approach and aligns with the idea of a Circular Economy It means designing products so that when they are no longer useful, they can easily be reused or recycled instead of being thrown away in a landfill 1
Cradle-to-Gate: Refers to the process of measuring the environmental impact of a product from the moment raw materials are taken from the earth (the “cradle”) up to when the finished product is ready to leave the factory (“the gate”) This includes steps like transporting, refining, processing, and manufacturing the materials or product 1
Cradle-to-Grave: Refers to a way of measuring the total environmental impact of a material or product throughout its entire life It starts from the beginning (when raw materials are taken from nature) to the end (when the product is disposed of, reused, or recycled)
This includes not just its production and transportation but also its use (like maintenance) and what happens to it after it’s no longer useful 1
Energy Budget: A specific target for Energy Use Intensity (EUI) that LETI believe developments must not exceed in order to achieve Net Zero Carbon, as demonstrated through archetypes See also top-down modelling
Embodied Carbon (EC): The ‘Embodied Carbon’ emissions of an asset a material/product are the total GHG greenhouse gas emissions and removals associated with materials and construction processes throughout the whole life cycle of an asset; from the extraction of raw materials, through manufacturing and transportation, to the construction and disposal stages (Modules A1-A5, B1B5, C1-C4)
Embodied Energy (EE): Embodied Energy (EE) is the total amount of energy used to make a product or system This includes all the energy from direct and indirect processes, starting from raw materials to the point where the product is ready to leave the factory (Cradle-to-Gate) The energy is usually measured in megajoules (MJ)
Energy Performance Certificate (EPC): A document that rates how energy efficient a building is
Environmental Product Declaration (EPD): An independently verified and registered document that communicates transparent and comparable information about the life cycle environmental impact of a product EPDs are commonly used to calculate the embodied carbon of a product
Energy Use Intensity (EUI): Energy Use Intensity (EUI) is a way to measure how much energy a building uses in a year It helps us understand how well a building performs by focusing on its actual energy use, not the carbon emissions tied to the electricity grid
LETI sees EUI as essential for designing new buildings that help combat climate change It’s a reliable way to track building performance because it is based on the energy recorded on bills (measured in kWh) and can be checked during both design and everyday use
EUI includes all the energy used in a building, such as:
• Regulated energy: Heating, hot water, cooling, ventilation, and lighting
• Unregulated energy: Energy for appliances like kitchen equipment, computers, and other electronics It does not include energy used for charging electric vehicles EUI also allows comparisons between similar types of buildings to see how efficient they are in realworld use
Fossil Fuel: A natural fuel such as petroleum, coal or gas, formed in the geological past from the remains of living organisms The burning of fossil fuels by humans is the largest source of emissions of carbon dioxide
Life Cycle Assessment: Is a process used to measure the environmental impact of a building, including carbon emissions (both from materials and energy use) and other effects like pollution and ecosystem damage It examines the building’s impact throughout its entire life, divided into stages:
• A1-3: From material production to the factory gate (“Cradle-to-Gate”)
• A1-3 + A4-5: Adds transport and construction (“Cradleto-Practical Completion”)
• B1-5: During the building’s use (“Use”)
• C1-4: Demolition and disposal (“End-of-Life”)
• D: Additional benefits, like recycling (“Supplemental”)
For Whole Life Carbon, an LCA looks specifically at greenhouse gas emissions, converted into “carbon dioxide equivalent” to measure the building’s Global Warming Potential (GWP) By using estimated carbon data for each stage of the building’s life, developers can compare different designs and prove they’ve achieved planned carbon reduction goals during the design phase
Material Passport: Documentation that gathers and organises data about materials contained within a building For the design team, it captures information from surveys and other formation sources For operations teams, it provides a single location to record or link maintenance information Material passports are a key element of the Circular Economy as they provide the full data information of every part of a building, allowing it to be repaired/maintained/re-used/recycled during and at the end of a building’s life
Net Zero Embodied Carbon: A ‘Net Zero Embodied Carbon’ asset is one where the sum total of GHG emissions and removals over an asset’s life cycle (Modules A1-A5, B1-B5 and C1-C4) are minimized, meets local carbon targets* (e g kgCO2e/m2 ), and with additional ‘offsets’, equals zero 2
Net Zero Carbon - Operational Energy: A ‘Net Zero Carbon – Operational Energy’ asset is one where no fossil fuels are used, all energy use (Module B6) has been minimized, meets the local energy use target (e g kWh/m2/yr) and all energy use is generated on- or off site using renewables that demonstrate additionality Any residual direct or indirect emissions from energy generation and distribution are ‘offset’ 2
Net Zero Upfront Carbon: A ‘Net Zero Upfront Carbon’ asset is one where the sum total of GHG emissions, excluding ‘carbon sequestration’, from Modules A1-A5 is minimized, meets local carbon targets* (e g kgCO2e/ m2), and with additional ‘offsets’, equals zero 2
Net Zero Whole Life Carbon: A ‘Net Zero (Whole Life) Carbon’ Asset is one where the sum total of all asset related GHG emissions, both operational and embodied, over an asset’s life cycle (Modules A1-A5, B1-B7, C1-C4) are minimized, meet local carbon*, energy and water targets, and with residual ‘offsets’, equals zero 2
*Use the Embodied Carbon Target Alignment document to target a rating For the time being current bestpractice performance for projects in the early design phase is considered to be a C rating, while a B and above is considered a robust stretch target
Offsetting: Offsetting is the process of compensating for the remaining carbon emissions balance by contributing, usually financially, towards solutions to reduce emissions elsewhere Typically, this is put in practice by establishing carbon offset funds which then invest in renewable energy and other carbon reduction measures See Appendix 10 of the LETI Embodied Carbon Primer for more information
Operational Carbon (kgCO2e): ‘Operational Carbon –Energy’ (Module B6) is the GHG emissions arising from all energy consumed by an asset in-use, over its life cycle 2
Performance Gap: This term refers to the discrepancy between energy predictions at design stage, compared to in-use energy consumption of buildings
Definitions
Post-Occupancy Evaluation (POE): Post-occupancy evaluation is the process of obtaining feedback on a building’s performance in use after it has been built and occupied By accurately measuring factors such as building use, energy consumption, maintenance costs and user satisfaction, POE allows for a process of continuous improvement in the construction industry 4
Renewable Energy: Renewable energy technologies use natural energy sources to generate electricity and/ or heating/cooling Sources include solar, wind, wave, marine, hydro, etc
Soft Landings Framework: The term Soft Landings refers to a strategy designed to make an easy transition from the construction to occupation phases of a project with the overriding aim of realising optimal operational performance It’s all about narrowing the performance gap between design intent and operational outcomes that can emerge at any stage in a construction project 5
Upfront Embodied Carbon: ‘Upfront Carbon’ emissions are the GHG emissions associated with materials and construction processes up to practical completion (Modules A1-A5) Upfront carbon excludes the biogenic carbon sequestered in the installed products at practical completion 2
U-Value: the rate of transfer of heat through a structure (which can be a single material or a composite), divided by the difference in temperature across that structure The units of measurement are W/m² K
Whole Life Carbon (WLC): ‘Whole Life Carbon’ emissions are the sum total of all asset related GHG emissions and removals, both operational and embodied over the life cycle of an asset including its disposal (Modules: A1-A5; B1-B7 (plus B8 and B9 for Infrastructure only); C1-C4) Overall Whole Life Carbon asset performance includes separately reporting the potential benefit from future energy recovery, re-use, and recycling (Module D) 2
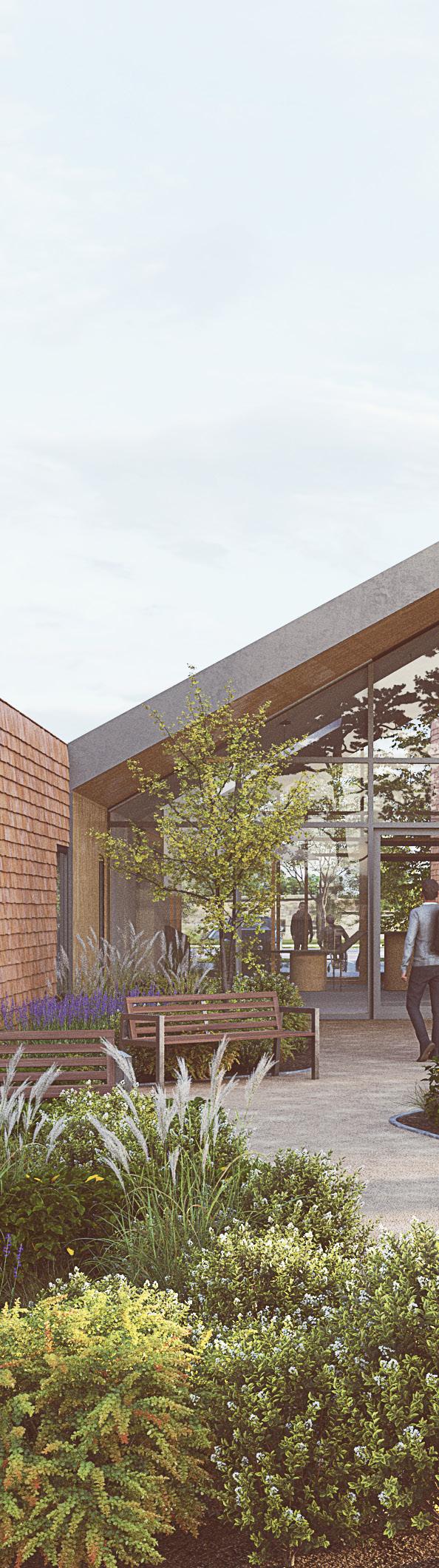
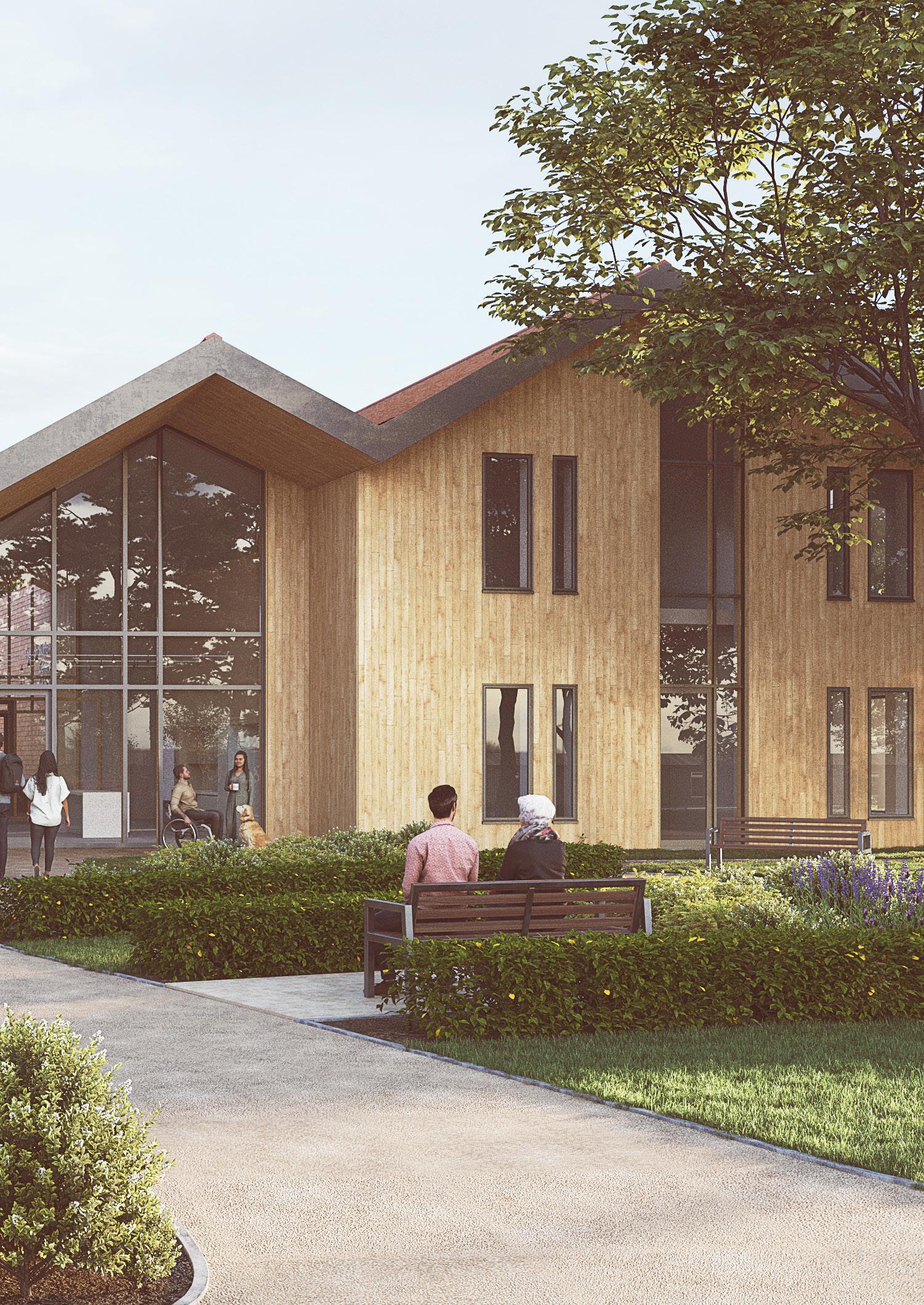
Image: The Rob Burrow Centre for MND - Targeted BREEAM
www circularecology com
2 Improving Consistency in Whole Life Carbon Assessment and Reporting; Carbon Definitions for the Built Environment, Buildings and Infrastructure (https://www LETI london/carbonalignment)
3 Athena, Sustainable Material Institute Definition
4 RIBA POE Primer (https://www architecture com/-/ media/gathercontent/post-occupancy-evaluation/ additional-documents/ribapoebpeprimerpdf pdf)
5 NBS (www thenbs com)



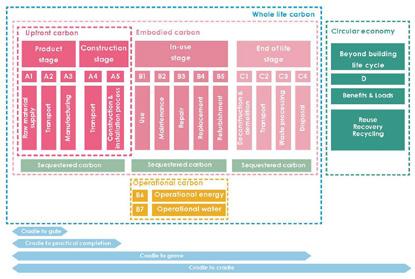
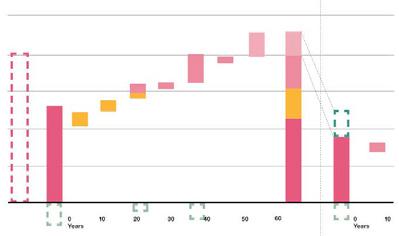








Abbreviations
BBP Better Buildings Partnership
BIM Building Information Modelling
BMS Building Management System
BRE Building Research Establishment
BREEAM Building Research Establishment Environmental Assessment Method
BUS Building Use Studies
CABE Chartered Association of Building Engineers
CIBSE Chartered Institution of Building Services Engineers
CLT Cross Laminated Timber
CO2 Carbon Dioxide
COP Coefficient of performance
DEC Display Energy Certificate
EC Embodied Carbon
EPC Energy Performance Certificate
ESG Environmental, Social, and Governance
EUI Energy Use Intensity
EoL End-of-Life
FF&E Furniture, Fixtures, and Equipment
FSC Forest Stewardship Council
GHG Greenhouse Gases
GIA Gross Internal Area
GLA Greater London Authority
GWP Global Warming Potential
HQ Headquarters
IPI Integrated Project Insurance
LCA Life Cycle Assessment
LETI London Energy Transformation Initiative
MEP Mechanical, Electrical and Public Health
MVHR Mechanical Ventilation with Heat Recovery
NABERS National Australian Built Environment Rating System
NBS National Building Specification
O&M Operation and Maintenance
PHPP Passive House Planning Package
PI Professional Indemnity
POE Post Occupancy Evaluation
PV Photovoltaic Panels
QS Quantity Surveyor
RFI Request for Information
RIBA Royal Institute of British Architects
RICS Royal Institute of Chartered Surveyors
SuDS Sustainable Urban Drainage
UKGBC United Kingdom Green Building Council
UN United Nations
WorldGBC World Green Building Council
WLC Whole Life Carbon
WLCN Whole Life Carbon Network
NZC /ZC Net Zero Carbon
BIBLIOGRAPHY
BIBLIOGRAPHY
Bibliography
ACAN Climate Framework Design Guide (2024)
Ellen MacArthur Foundation https://www.ellenmacarthurfoundation.org/
RIBA Sustainable Outcomes Guide (2019)
LETI Client Guide for Net Zero Carbon Buildings (2021)
LETI Climate Emergency Design Guide (2020)
UKGBC https://ukgbc.org/
Huw Heywood, 101 Rules of Thumb for Low Energy Architecture (2021), RIBA Publishing
The Passivhaus Trust https://www.passivhaustrust.org.uk/
five basic principles apply for the construction of Passive Houses:
References:
Fig 1 Circular Economy Illustration by Circular Flanders- Available at https://vlaanderen-circulair.be/en
Fig 2 Climate Framework Overview Available at https://www.climateframework.com
Fig 3 Zero Carbon Trajectory - LETI Climate Emergency Design Guide (2020)
Fig 4 Huw Heywood, 101 Rules of Thumb for Low Energy Architecture (2022)
Fig 5 Elements of a Net Zero Carbon Brief - LETI Client Guide (2021)
Fig 6 Carbon Reduction Potential as Project Progresses - LETI Client Guide (2021)
Fig 7 Why orientation is important LETI Climate Emergency Design Guide (2020
Fig 8 Life cycle assessment (LCA) LETI Climate Emergency Design Guide (2020) Diagram adapted from Hawkins\ Brown using illustrations from Open Systems Lab 2018 licensed under Creative Commons CC-BY-NDDiagram adapted from Hawkins\Brown usingillustrations from Open Systems Lab 2018 licensed under Creative Commons CC-BY-ND
Fig 9 Key Performance Indicators, Building element targets (include products, transport and construction of substructure, superstructure, MEP, façade and internal finishes (A1-A5) Figures exclude timber sequestration, LETI Climate Emergency Design Guide (2020)
Fig 10 LETI Embodied Carbon, LETI Climate Emergency Design Guide (2020
Fig 11 RIBA Sustainable Outcomes RIBA, Sustainable Outcomes Guide (2019
Fig 12 Design Measures - LETI Climate Emergency Design Guide (2020)
Fig 13 Basic principles to apply for the construction of Passive Houses https://passivehouse.com/02_informations/02_passive-house-requirements/02_passive-houserequirements.htm
Fig 14 RIBA Sustainable Outcomes - RIBA Sustainable Outcomes Guide (2019)
Fig 15 Net Zero Carbon & Sustainability Site Appraisal Checklist - LETI Client Guide (2021) Appendix 3
Fig 16 Sustainability Assessment & Certification Methods - LETI Client Guide Appendix 5
Fig 17 Net Zero Operational Carbon Summary - LETI Climate Emergency Design Guide (2020) Appendix A,
Fig 18 CE hierarchy for building approaches (from London Plan Policy D3 Figure 3 2), GLA Guidance Document, (2022)
Fig 19 Building layers and their indicative lifespans, GLA Guidance Document, (2022
Fig 20 Circular Economy RIBA Plan of Work Overlay - https://www.architectscan.org/circular-economydesign-guide
Fig 21 ACAN Climate Framework Design Guide (2024) - https://www.architectscan.org/
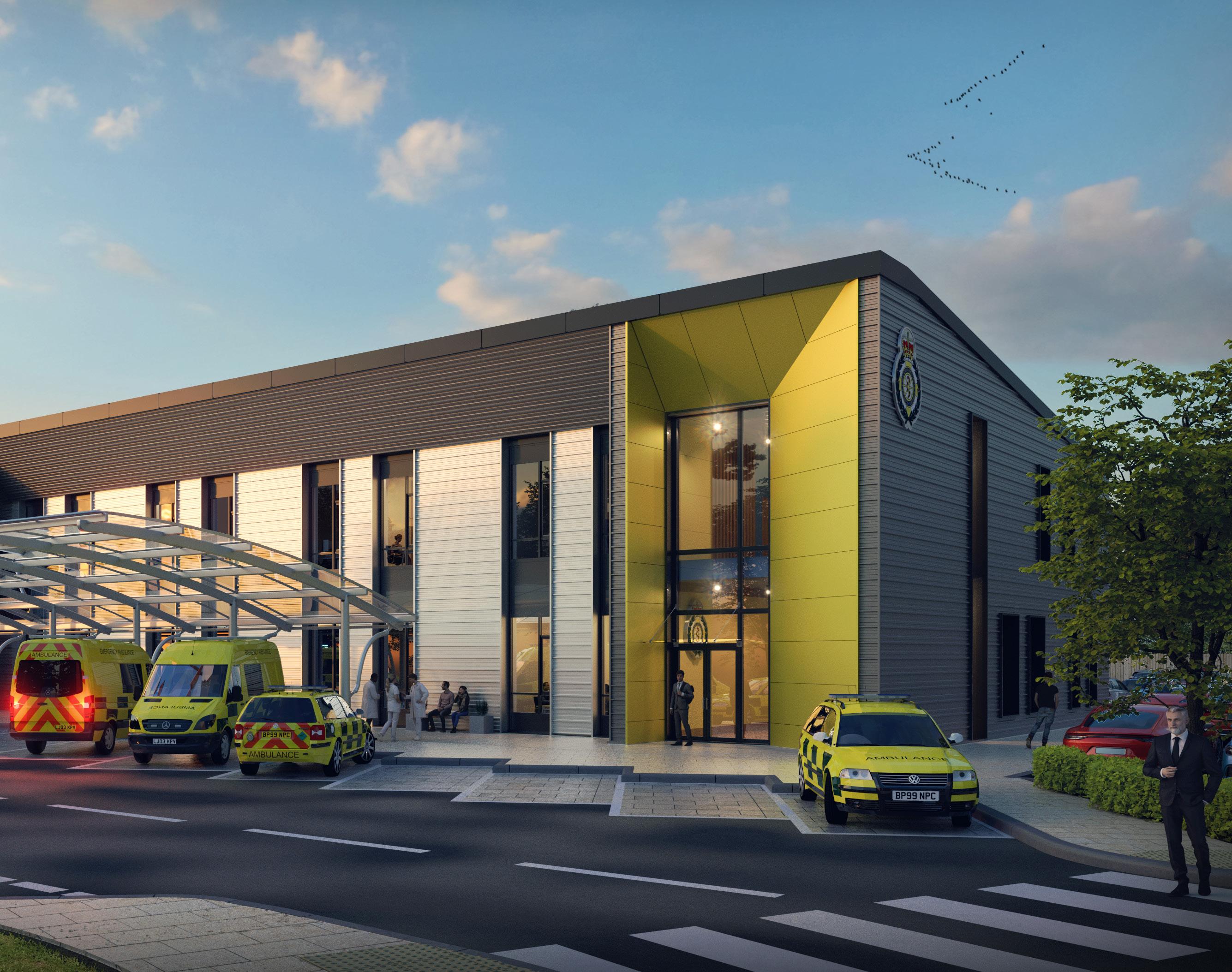
Bury St Edmunds Ambulance Hub - BREEAM Excellent Rated
Net Zero Carbon & Sustainability Site Appraisal Checklist
A3: Net Zero Carbon & Sustainability Site Appraisal Checklist
Operational Carbon
Assess micro-climate
→ Rainfall
→ Sunlight
→ Wind
→ Temperature
Assess opportunities for passive design
→ Orientation
→ Optimise glazing for passive heating and overheating
→ Local green and blue infrastructure to neutralise urban heat island effect
Understand the existing context and infrastructure
Assess opportunities for renewable technologies
→ Opportunity for heat recovery for heat pumps (water, ground, sewerage, etc.)
→ Opportunity for renewable energy generation including wind, solar, hydro
→ Opportunities for sharing heat with local buildings
→ Opportunities for micro-grids with battery storage, electric vehicle connection
Embodied Carbon & Circular Economy
Possibility of re-rue of whole of part of the existing building and infrastructure
→ Survey of existing buildings, material and infrastructure on site
Avoid sites requiring soil stabilisation and deep foundation
→ Site survey of ground conditions
Connectivity & Transport
Access proximity to public/low carbon transport and pedestrian/cycle routes
→ Proximity
→ Extent of network
Planning restrictions on density of development
→ Proposed development to be dense enough to promote walking and cycling
→ Density not to be harmful to existing biodiversity
Ecology & Biodiversity
Identify opportunities to increase biodiversity on- and off-site
Audit of existing ecology and ecosystems
Always prioritise brownfield sites in site selection
Water
Examine risk of site to flooding
Assess opportunities for Sustainable Urban Drainage solutions (SuDS)
Examine potential for grey water recycling, rainwater harvesting, on-site black water cleansing
Social Value
Connection to external spaces
Site air quality
Daylighting
Proximity to nature / green spaces
Site noise levels
Identify opportunities for placemaking and enhancing existing successful social structures, as well as neighbourhood / communities patterns of the area
Access opportunities for meanwhile use
Appendix B
Sustainability Assessment & Certification Methods
A5: Sustainability Assessment & Certification Methods
Operational Energy & Carbon
Circular Economy & Embodied Carbon
LETI Targets
LETI Residential Targets
→ Residential Total EUI = 35 kWh/m 2 /yr (GIA)
→ 2020 design target (for buildings designed in 2020) a C rating should be achieved.
→ Schools Total EUI = 65 kWh/m 2 /yr (GIA)
(<500 kgCO2 /m 2 upfront embodied carbon and <800 kgCO2 /m 2 total embodied carbon)
→ Commercial Offices Total EUI = 55 kWh/m 2 /yr (GIA)
→ 2030 design target (for buildings designed in 2030) an A rating should be achieved.
→ Space Heating EUI = 15 kWh/m 2 /yr
(<300 kgCO2 /m 2 upfront embodied carbon and <450 kgCO2 /m 2 total embodied carbon)
Assessment Certification & Process Tools
→ For more typologies see https://www.leti.london/carbon alignment
→ BREEAM
Assessment Certification & Process Tools
→ CIBSE TM22
→ CIBSE TM54
→ BREEAM
→ Green Star (AUS)
→ Green Star (AUS)
→ Home Quality Mark (BRE)
→ LEED
→ Home Quality Mark (BRE)
→ LEED
→ Living Building Challenge
→ Living Building Challenge
→ Guidance & Reference
→ RIBA Plan for Use
→ Passivhaus
→ Soft Landings
→ RIBA Plan for Use
Guidance & Reference
→ Soft Landings
→ LETI Embodied Carbon Primer
Guidance & Reference
→ LETI Embodied Carbon Target Alignment
→ LETI Climate Emergency Design Guide
→ LETI Embodied Carbon One Pager
→ LETI Whole Life Carbon One Pager
→ LETI Whole Life Carbon One Pager
→ Unlocking the Delivery of Net Zero Carbon Buildings - UKGBC
→ Low Carbon Refurbishment: 10 Ways to reduce Embodied Carbon Emissions - OneClick LCA
→ Net Zero Carbon Buildings: A Framework Definition - UKGBC
→ Circular Economy Actor and Resource Map - UKGBC
→ TCPA Practical Guides - Guide 4: Master Planning for Net-zero Energy
→ Circular Economy in the Built Environment - ARUP
→ The Building System Carbon Framework - WBCSD
→ Design for a Circular Economy Primer - Mayor of London
→ Responsible Retrofit Guidance Wheel - STBA
→ Net Zero Carbon Pathway Framework - BBP
→ Building the Case for Net Zero:
→ A Feasibility Study into the Design, Delivery and Cost of New Net Zero Carbon Buildings - UKGBC
→ Whole Life Carbon Assessment for the Built Environment - RICS
Client Guide
L E T I
Circular Economy & Embodied Carbon
Circular Economy & Embodied Carbon
LETI Residential Targets
LETI Residential Targets
→ 2020 design target (for buildings designed in 2020) a C rating should be achieved.
(<500 kgCO2 /m 2 upfront embodied carbon and <800 kgCO2 /m 2 total embodied carbon)
→ 2020 design target (for buildings designed in 2020) a C rating should be achieved. (<500 kgCO2 /m 2 upfront embodied carbon and <800 kgCO2 /m 2 total embodied carbon)
→ 2030 design target (for buildings designed in 2030) an A rating should be achieved. (<300 kgCO2 /m 2 upfront embodied carbon and <450 kgCO2 /m 2 total embodied carbon)
→ 2030 design target (for buildings designed in 2030) an A rating should be achieved. (<300 kgCO2 /m 2 upfront embodied carbon and <450 kgCO2 /m 2 total embodied carbon)
→ For more typologies see https://www.leti.london/carbon alignment
→ For more typologies see https://www.leti.london/carbon alignment
Assessment Certification & Process Tools
Assessment Certification & Process Tools
→ BREEAM
→ BREEAM
→ Green Star (AUS)
→ Green Star (AUS)
→ Home Quality Mark (BRE)
→ LEED
→ Home Quality Mark (BRE)
→ LEED
→ Living Building Challenge
→ Living Building Challenge
→ RIBA Plan for Use
→ RIBA Plan for Use
→ Soft Landings
→ Soft Landings
Guidance & Reference
Guidance & Reference
→ LETI Embodied Carbon Primer
→ LETI Embodied Carbon Primer
→ LETI Embodied Carbon Target Alignment
→ LETI Embodied Carbon Target Alignment
→ LETI Embodied Carbon One Pager
→ LETI Embodied Carbon One Pager
→ LETI Whole Life Carbon One Pager
→ LETI Whole Life Carbon One Pager
→ Low Carbon Refurbishment: 10 Ways to reduce Embodied Carbon Emissions - OneClick LCA
→ Low Carbon Refurbishment: 10 Ways to reduce Embodied Carbon Emissions - OneClick LCA
→ Circular Economy Actor and Resource Map - UKGBC
→ Circular Economy Actor and Resource Map - UKGBC
→ Circular Economy in the Built Environment - ARUP
→ Circular Economy in the Built Environment - ARUP
→ Design for a Circular Economy Primer - Mayor of London
→ Design for a Circular Economy Primer - Mayor of London
Appendix B
Appendix 5
Sustainability Assessment & Certification Methods
Connectivity & Transport
Targets
→ 0 kgCO2e/km per person/yr for the travel of occupants and visitors within the site, or from site to a local transport, retail and/or community hub (as applicable)
→ All developments design to be connected to smart technology to manage peak loads and close the performance gap.
Assessment Certification & Process Tools
→ BREEAM
→ Green Star (AUS)
→ LEED
→ Living Building Challenge
→ RIBA Plan for Use
→ Soft Landings
Water
Targets
40% reduction in potable water use/person/day Domestic Potable Water Use:
→ 2020 - < 110 l/p/day
→ 2025 - < 95 l/p/day
→ 2030 - < 75 l/p/day
Non-Domestic Potable Water Use:
→ 2020 - < 16 l/p/day
→ 2025 - < 13 l/p/day
→ 2030 - < 10 l/p/day
Assessment Certification & Process Tools
→ BREEAM
→ Green Star (AUS)
→ LEED
→ Living Building Challenge
→ RIBA Plan for Use
→ Soft Landings
Ecology & Biodiversity
LETI Targets
→ Net Positive Species
→ Urban Greening Factor on all New Sites: 0.3 for Non-domestic and 0.4 for Residential
Assessment Certification & Process Tools
→ BREEAM
→ Green Star (AUS)
→ Home Quality Mark (BRE)
→ LEED
→ Building with Nature
→ Living Building Challenge
→ RIBA Plan for Use
→ Soft Landings
Guidance & Reference
→ Nature-based Solutions to the Climate Emergency: The Benefits to Business and Society - UKGBC
→ Spatial Planning INstruments and the Environment (SPINE) - OECD
→ BREEAM Biodiversity Credits - BRE
→ Urban Green Factor - Mayor of London
→ Urban Greening for Biodiversity Net Gain: A Design Guide - Mayor of London
→ Practical How-to Guide: Understanding Green Infrastructure at Different Scales - Barker, A., Clay, G., Morrison, R. et al, University of Manchester
→ Making the Case for Green Infrastructure: Lessons from Best Practice - UKGBC
→ Developing and Implementing a Green Infrastructure Strategy - UKGBC
Appendix B
Sustainability Assessment & Certification Methods
Human Factors
Good Health & Wellbeing
Targets
→ Overheating: 25-28 °C maximum for 1% of Occupied Hours
→ Daylighting: > 2% average Daylight Factor, 0.4 Uniformity
→ CO2 levels: < 900 ppm
→ Total VOCs: < 0.3 mg/m 3
→ Formaldehyde: < 0.1 mg/m 3
→ Open windows within 7m
Assessment Certification & Process Tools
→ BREEAM
→ BUS Methodology
→ CIC Design Quality Indicators
→ Green Star (AUS)
→ Home Quality Mark (BRE)
→ LEED
→ CIBSE TM59 and CIBSE TM52
→ Living Building Challenge
→ Leesman Index
→ NABERS
→ Passivhaus
→ WELL Building Standard
→ RIBA Plan for Use
→ Soft Landings
Human Factors
Human Factors
Sustainable Cities & Communities
Sustainable Cities & Communities
Assessment Certification & Process Tools
→ BREEAM
Assessment Certification & Process Tools
→ BREEAM
→ Green Star (AUS)
→ Green Star (AUS)
→ Home Quality Mark (BRE)
→ LEED
→ Home Quality Mark (BRE)
→ LEED
→ Living Building Challenge
→ Living Building Challenge
→ RIBA Social Value Toolkit
→ RIBA Social Value Toolkit
→ RIBA Plan for Use
→ RIBA Plan for Use
→ Soft Landings
→ Soft Landings
Guidance & Reference
→ LEED ND
Guidance & Reference
→ LEED ND
→ Well Community
→ Well Community
→ BREEAM Communities
→ BREEAM Communities
→ RIBA Social Value Toolkit
→ RIBA Social Value Toolkit
Human Factors
Human Factors
Sustainable Life Cycle
Sustainable Life Cycle
Targets
Targets
→ Operation costs per area (£/m 2) compared with the return on investment value created by the project, (including rental value, building value and social value)
→ Operation costs per area (£/m 2) compared with the return on investment value created by the project, (including rental value, building value and social value)
Assessment Certification & Process Tools
→ LEED
Assessment Certification & Process Tools
→ LEED
→ Living Building Challenge
→ Living Building Challenge
→ RIBA Social Value Toolkit
→ RIBA Social Value Toolkit
→ RIBA Plan for Use
→ RIBA Plan for Use
→ Soft Landings
→ Soft Landings
Net Zero Operational Carbon
LETI - Net Zero Operational Carbon Summary
Ten key requirements for new buildings
By 2030 all new buildings must operate at net zero to meet our climate change targets. This means that by 2025 all buildings will need to be designed to meet these targets. This page sets out the approach to operational carbon that will be necessary to deliver zero carbon buildings. For more information about any of these requirements and how meet them, please refer to the: UKGBC - Net Zero Carbon Buildings Framework; BBP - Design for Performance initiative; RIBA - 2030 Climate Challenge; GHA - Net Zero Housing Project Map; CIBSE - Climate Action Plan; and, LETI - Climate Emergency Design Guide.
Low energy use
1 2
Total Energy Use Intensity (EUI) - Energy use measured at the meter should be equal to or less than:
• 35 kWh/m2/yr (GIA) for residential1
For non-domestic buildings a minimum DEC B (40) rating should be achieved and/or an EUI equal or less than:
• 65 kWh/m2/yr (GIA) for schools1
• 70 kWh/m2/yr (NLA) or 55 kWh/m2/yr (GIA) for commercial offices1,2
Building fabric is very important therefore space heating demand should be less than 15 kWh/m2/yr for all building types.
Measurement and verifcation
3
Annual energy use and renewable energy generation on-site must be reported and independently verified in-use each year for the first 5 years. This can be done on an aggregated and anonymised basis for residential buildings.
Reducing construction impacts
4
Embodied carbon should be assessed, reduced and verified post-construction.3
Developed in collaboration with:

Developed with the support of:
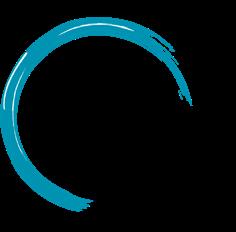
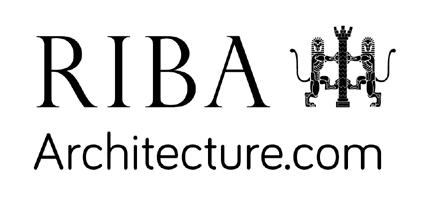
Notes:
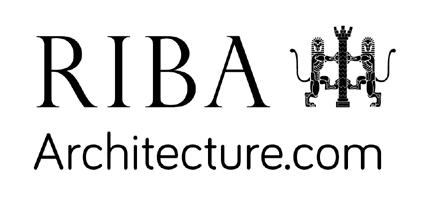
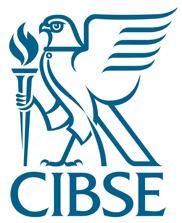
Heating and hot water should not be generated using fossil fuels.
The average annual carbon content of the heat supplied (gCO2/kWh) should be reported.
On-site renewable electricity should be maximised.
Energy demand response and storage measures should be incorporated and the building annual peak energy demand should be reported.
Zero carbon balance
A carbon balance calculation (on an annual basis) should be undertaken and it should be demonstrated that the building achieves a net zero carbon balance.
Any energy use not met by on-site renewables should be met by an investment into additional renewable energy capacity off-site OR a minimum 15 year renewable energy power purchase agreement (PPA). A green tariff is not robust enough and does not provide ‘additional’ renewables.
Note 1 – Energy use intensity (EUI) targets The above targets include all energy uses in the building (regulated and unregulated) as measured at the meter and exclude on-site generation. They have been derived from: predicted energy use modelling for best practice; a review of the best performing buildings in the UK; and a preliminary assessment of the renewable energy supply for UK buildings. They are likely to be revised as more knowledge is available in these three fields. As heating and hot water is not generated by fossil fuels, this assumes an all electric building until other zero carbon fuels exist, (kWh targets are the same as kWhelec-eq). Once other zero carbon heating fuels are available this metric will be adapted.
Note 2 – Commercial offces With a typical net to gross ratio, 70 kWh/m2 NLA/yr is equivalent to 55 kWh/m2 GIA/yr. Building owners and developers are recommended to target a base building rating of 6 stars using the BBP’s Design for Performance process based on NABERS.
Note 3 – Whole life carbon It is recognised that operational emissions represent only one aspect of net zero carbon in new buildings. Reducing whole life carbon is crucial and will be covered in separate guidance.
Note 4 – Adaptation to climate change Net zero carbon buildings should also be adapted to climate change. It is essential that the risk of overheating is managed and that cooling is minimised.
7 Principles of Circular Design
Designing buildings for the circular economy requires a multi-faceted and holistic approach The following 7 principles offer a way to define and focus an architectural design for the circular economy
Each project, and each aspect of a project, will have its strengths and weaknesses across different ‘principles’ to others The 7 Principles are there to ensure there is always an awareness of circularity at every moment and stage of the design process
The SDE requires all projects to be defined by these 7 principles, and for this definition to be reviewed and updated at every stage
*Points 1-6 are as defined by the GLA’s guidance document for Circular Economy Statements Building In Layers
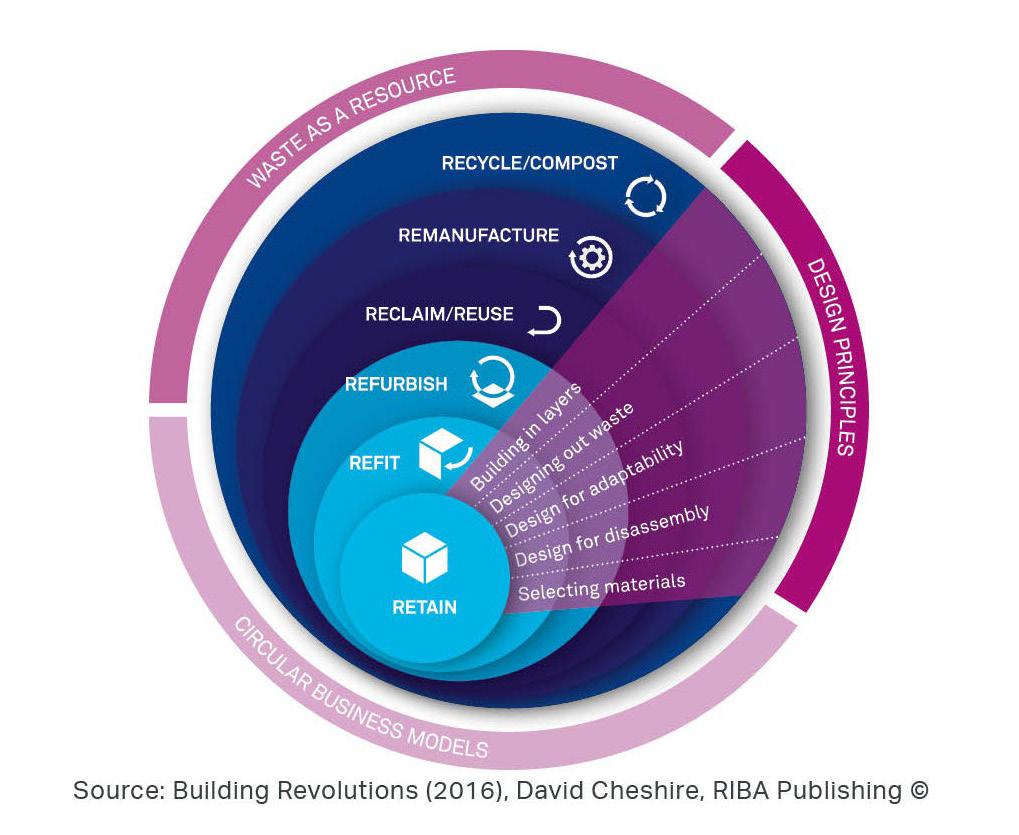
Fig 19 Building layers and their indicative lifespans, GLA Guidance Document, (2022)
Figure 2: Building layers and their indicative lifespans 10
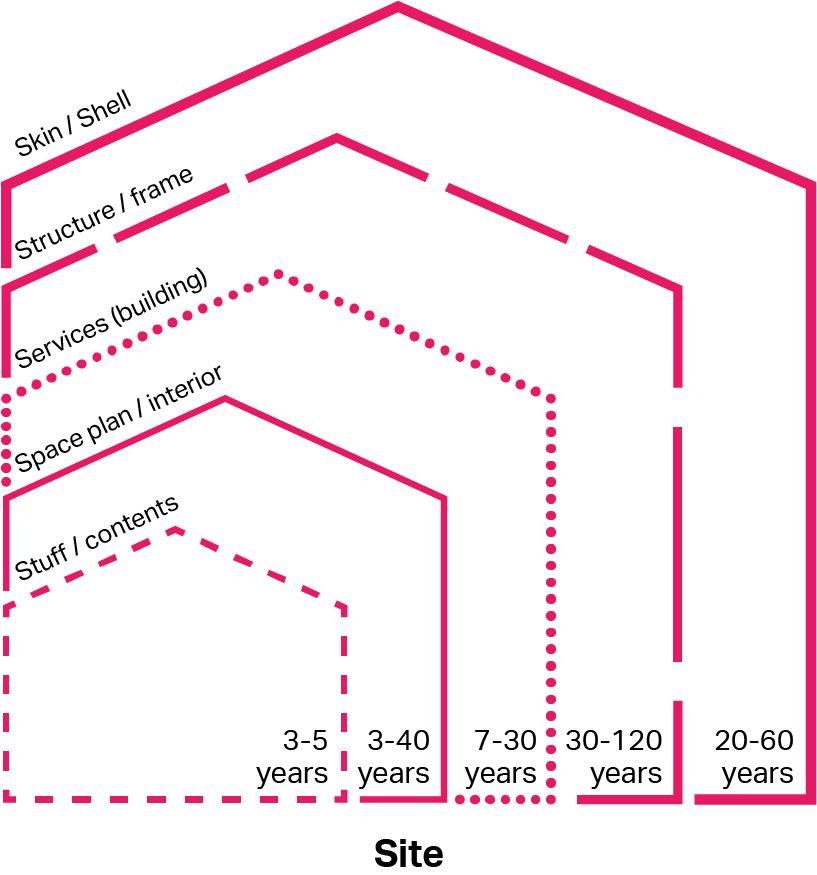
Fig 18 CE hierarchy for building approaches (from London Plan Policy D3 Figure 3.2), GLA Guidance Document, (2022)
Fig 19 Building layers and their indicative lifespans, GLA Guidance Document, (2022)
2.2.4. A standard list of layers is defined in Table 1 below, with reference to the Royal Institute of Chartered Surveyors (RICS) New Rules of Measurement (NRM) (2012) 11 building elements where relevant. The NRM building elements form the basis of CE statement reporting, particularly from outline application stage in the Bill of Materials.
Table 1: Building layer summary and equivalent building element/RICS reference
location, context,
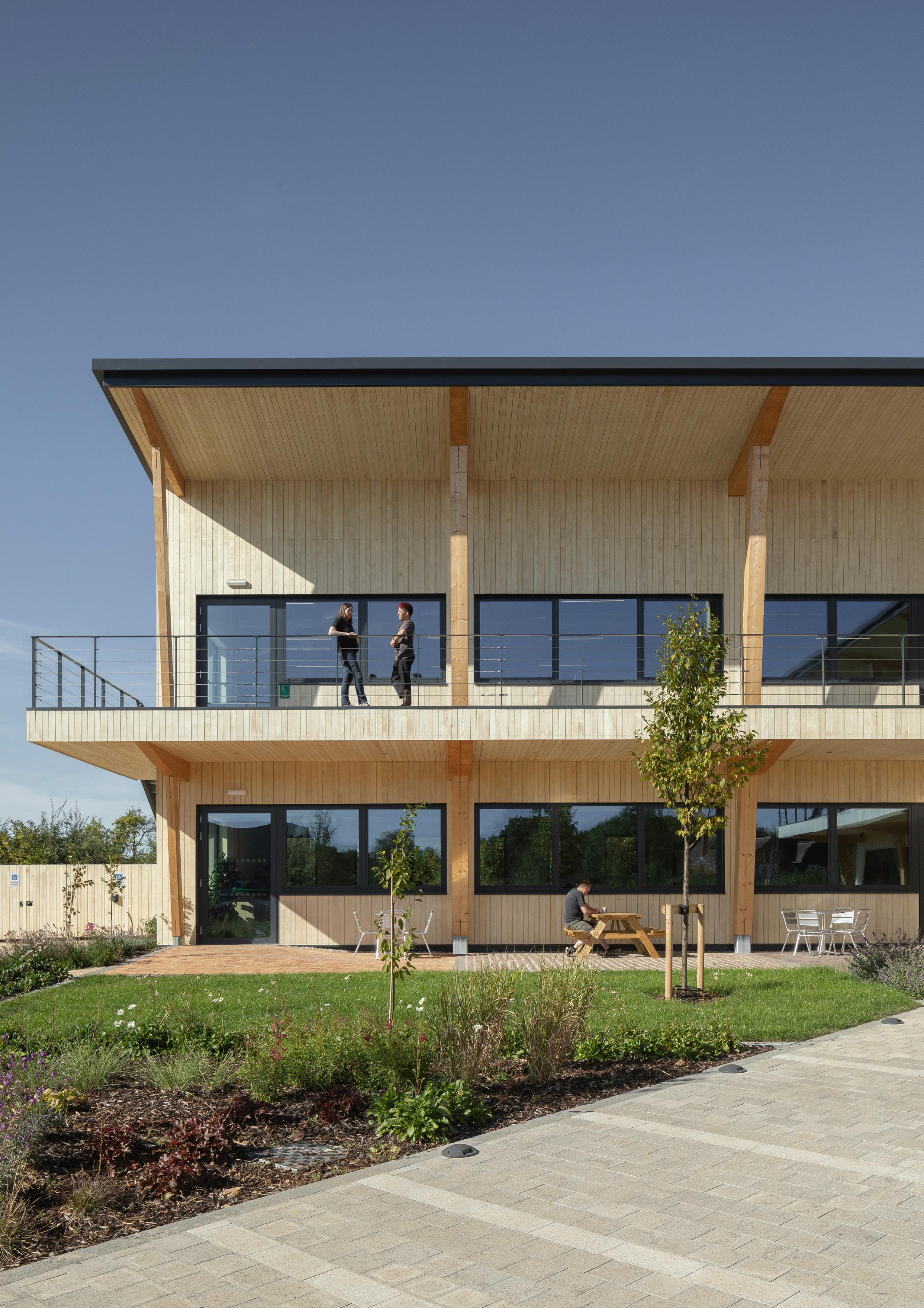
Image: Unusual Hq, Northampton, Uk
An Exemplar Test-Bed Project for Circular Economy Principles and Low-Carbon Design
Circular Economy RIBA Plan of Work Overlay
A0.2: Actions by RIBA Stage
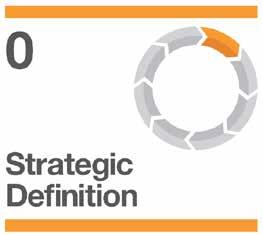
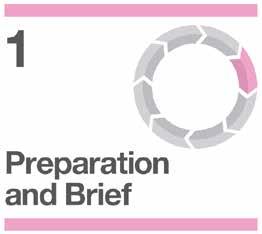


Operational carbon, future of heat, demand response and data disclosure
1. Identify a net zero carbon champion.
2. Identify project team responsibilities to achieve operational energy use targets including the calculation of operational targets, documenting assumptions behind these, managing risks and validating in-use performance.
3. Consider contractual incentives for achievement of performance targets.
4.Identify a project team member who can advise on demand response.
1. Set clear intent for zero carbon targets and defi ne what this includes, document boundaries and targets.
2. Set an energy use intensity target and embed within the brief
3. Discuss localised energy constraint issues with DNO.
4. Identify likely eligible demand response programmes at a national and regional scale.
5. Incorporation of data disclosure into BIM requirements.
1. Establish clear energy use targets, document targets and strategies to achieve this and share with all stakeholders.
2. Develop the concept design in accordance with critical design parameter recommendations in this guide. Specifi c aspects to consider at this stage include:
→ Building orientation
→ Building form factor
→ Facade glazing ratio
→ Likely occupancy patterns and operating scenarios
→ Facade glazing ratio
→ Technical systems integration.
3. Develop a preliminary operational energy model aligned to the Energy Use Intensity targets. Use this model to guide design throughout RIBA 2
4. Use the LETI Future of Heat Decision Tree when making decisions on heating and hot water systems.
5. Implement the most signifi cant carbon/energy reduction measures in design including demand response and energy storage opportunities.
6. Highlight the roles and opportunities for overcoming performance gap, for example by following the BSRIA Soft Landings Framework.
1. Refi ne a full operational energy model for evaluation of predicted energy demand. Ensure this simulation goes beyond regulated energy and considers energy use from all items in the building.
2. Test proposed design changes using the energy model.
3. Update and document detailed targets and strategies to achieve these. Include design measures and assumptions of likely occupancy patterns and operating scenarios as well as strategies for long term adaptability.
4. Ensure proposed construction details are robust to support low energy and airtightness performance characteristics.
5. Ensure that the risk of overheating has been assessed and mitigated.
6. Develop demand response strategy and simulate potential impact.
7. Develop sub-metering strategy using LETI energy disclosure guidance. Heating and cooling energy consumption (kWh) should be metered separately to enable fabric performance to be assessed.
8. Establish a secure remote source for metered data to be transmitted over a communications network for aggregation and storage.
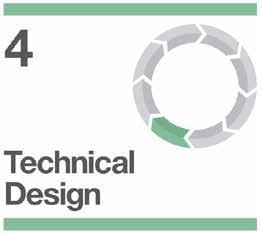
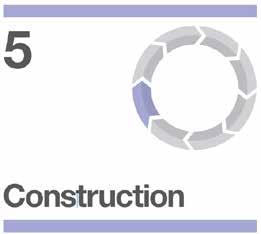
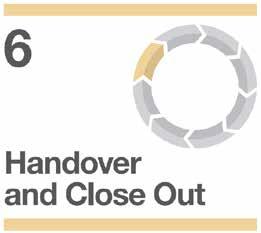
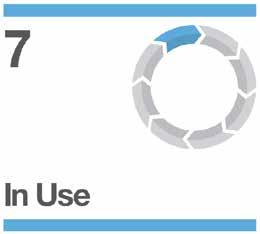
1. Update building energy model with latest design amendments, and ensure that operational energy targets are still being achieved. Document detailed targets and strategies to achieve these targets e.g. by creating a Building Performance Register.
2. Confi rm envelope specifi cation and complete detail design, ensuring good continuity of insulation and airtightness.
3. Check the suitability of the heating and hot water system using the LETI Future of Heat Decision Tree. Confi rm HVAC systems type and performance specifi cation.
4. Iterate demand response model with exact design data to gain a more accurate prediction of carbon savings and monetary gains. Ensure that specifi ed equipment can integrate fully to carry out demand response processes and events easily.
5. Ensure specifi ed metering is incorporated.
6. Include operational energy targets in the construction tender package, e.g. using a Design for Performance type of target and feedback loop.
7. Incorporate in contractors’ prelims with guarantees to recalculate energy model if items in the register are changed or value engineered, to demonstrate that ‘as built’ project meets agreed operational targets. Create risk register and confi rm responsibility for managing this during construction and commissioning.
1. Where possible, ensure the appointment of a clerk of works is responsible for quality checks.
2. Update energy model to account for any changes in the design or assumptions behind it and reject substitutions and omissions if achieving performance targets may be compromised by the changes.
3. Engage with the supply chain regarding the design targets of the project and where possible provide toolbox talks to help upskill contractors and to communicate the importance of quality construction.
4. Ensure the contractors understand commissioning requirements, including metering commissioning and validation of manual vs half hourly readings.
5. Ensure the contractor has quality monitoring processes in place to ensure proper installation of insulation, airtightness layer and mechanical equipment for the whole of the construction period.
6. Carry out benchmark inspections to clarify quality expectations and continue to monitor construction quality, including in-situ thermal performance tests, thermographic and air tightness testing.
7. Ensure the contractor understands the commissioning requirements.
1. Review fi nal construction including rectifi cation work, for quality, including in-situ thermal performance tests, thermographic and air tightness testing.
2. Finalise as-built energy model to account for any changes in the design or assumptions behind it.
3. Ensure commissioning and testing is fully completed and witnessed and that the ‘as installed’ controls strategies, setpoints, commissioned fl ow rates, metering etc. are in line with the energy model.
4. Ensure the building user is trained and understands use of the building systems.
5. Ensure that planned demand response activities occur correctly as part of the commissioning process and that the initial setup parameters are recorded.
6. Ensure a suitably qualifi ed individual understands the energy management and measurement systems. For further information regarding role and duties, refer to BBP better metering toolkit.
7. Ensure that performance data from sensors and meters are reconciled with main meter, spot meter and BMS readings and that logs are set up in BMS to facilitate long term monitoring of building performance.
1. For the fi rst year of occupation both the building and the targets should be tuned to actual building usage patterns. Ensure a dual focus of improving accuracy of targets as well as improving building operation.
2. Ensure hourly energy consumption trends match operating hours.
3. Ensure the metering system is operating correctly and is regularly validated against utility meters.
4. Identify and track key effi ciency metrics. Aim to track the fewest but most useful metrics.
5. Assign an annual budget for monitoring energy use and tuning controls in response. Aim for monthly review and quarterly ‘deep dive’ analysis.
6. Line up energy effi ciency assessments with post occupancy evaluation assessments to ensure occupant satisfaction with conditions in the building.
7. Upload total energy and heating energy consumption data to a public data platform for fi rst 5 years post-completion.
Circular Economy RIBA Plan of Work Overlay
The RIBA Stages 1-5 ‘For LCA Specialists’ contents were extracted from the call out box ‘Embodied and whole life carbon considerations through RIBA Plan of Works’ with some amendments made by FARNETANI, Mirko. CIRIA Briefing - Whole-life carbon reduction strategy: good practice methodology. January 2017. Available from: https://www.ciria.org/ [Accessed 25 April 2019] .
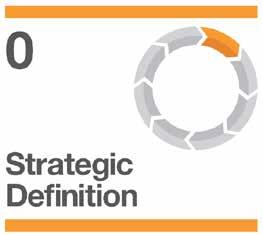
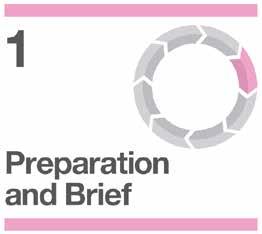
Embodied carbon - for the designer
1. Discuss whole life carbon ambitions with client.
2. Review opportunity for retention of existing structure and building fabric and how the quantum of materials of the new build can be reduced.
1. Client brief to be developed: it should incorporate embodied carbon reduction targets.
2. Appoint a LCA specialist or design team member to be responsible for whole life carbon assessment.


1. Use rules of thumb guidance during concept to maximise opportunities for low carbon design.
2. Analyse carbon reduction options for building elements using numerical analysis.
1. Include requirements and targets for whole life carbon in specifi cations and tender documentation at start of procurement.
2. Have discussions with the potential contractors and subcontractors around whole life carbon targets, asking for options for improvement and including carbon questions on tender return forms.
3. Continue numerical analysis and use material guides to optimise material specifi cation.
Embodied carbon - for the Life Cycle Assessment (LCA) specialist
1. Set initial embodied carbon targets using rule of thumb guidance and benchmarks.
OUTCOMES: Early recommendations on low carbon options ahead of RIBA Stage 2.
1. As the design develops, provide more detailed analysis of the options around the key building systems: frame, fl oors, envelope. This is discussed with the design team through workshops.
OUTCOMES: More detailed analysis and recommendations of the agreed design options. Improved understanding of embodied and whole life carbon within design team.
1. In depth analysis of the elemental and component parts of the entire building, identifying specifi c materials, products and lifespans, to generate a whole life carbon budget baseline.
2. Assess low carbon alternatives to the baseline. Agree a carbon reduction target - either percentage or absolute.
OUTCOMES: A whole life carbon budget, representing the total carbon emitted over the lifetime of the building, and an associated carbon reduction target. Initial carbon reduction option list, which will be further developed during technical design stage.
SIGNPOST Embodied Carbon Primer
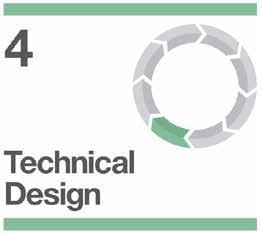
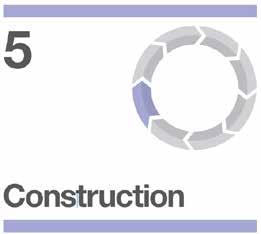
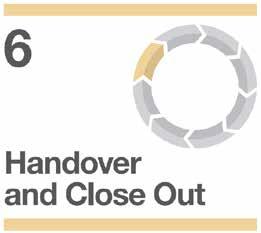
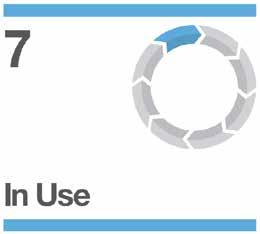
1. Finalise requirements and targets for whole life carbon in specifi cations and tender documentation at start of procurement.
2. Finalise requirements with the potential contractors and subcontractors around whole life carbon targets, asking for options for improvement and including carbon questions on tender return forms.
3. Continue numerical analysis and use material guides to optimise material specifi cation.
1. Update whole life carbon budget to include design development and fi nalise the carbon reduction options list.
2. Send pre-procurement Request for Information (RFI) to suppliers to collect carbon data in order to provide supplementary information for supplier selection. Review returned RFIs and analyse the environmental credentials of procurement options.
OUTCOMES: Agree carbon reduction targets and carbon reduction options list in order to infl uence specifi cations. A list of recommended low-carbon supplier. Assess design against embodied carbon targets. Ensure specifi cations include embodied carbon of materials. Recommend a list of suitable low carbon suppliers.
Material and product declaration
1. Engage with contractors to reduce waste.
2. Review alternative products and materials selections proposed by the contractor against technical and performance standards and against the whole life carbon requirements.
3. Prepare for postcompletion analysis by collecting numerical data through the construction phase.
1. Send RFIs to suppliers in order to receive construction carbon data and verify the environmental credentials.
2. Undertake building site monitoring through monthly site logs and construction progress reporting.
OUTCOMES: Facilitate gathering of data for the construction stage analysis and achieve the agreed carbon reduction targets.
1. Undertake post completion analysis using as-built information to assess upfront embodied carbon.
1. At the end of site works, the contractor should confi rm the fi nal carbon related data to the LCA specialist. Develop the practical completion carbon report. Align the design stage carbon targets with what was achieved at the end of construction.
OUTCOMES: Practical completion carbon report to be issued to the client.
1. Recommendations regarding embodied carbon reduction strategy over the in-use stage should be followed throughout the building life cycle including at the end of life stage.
Material and product verifi cation
As build carbon report to client
1. Embodied carbon reduction strategy to include in-use and end of life stages.
OUTCOMES: Client to have relevant information to continue embodied carbon reduction strategy throughout in-use and end of life stages.
In-use carbon report to client
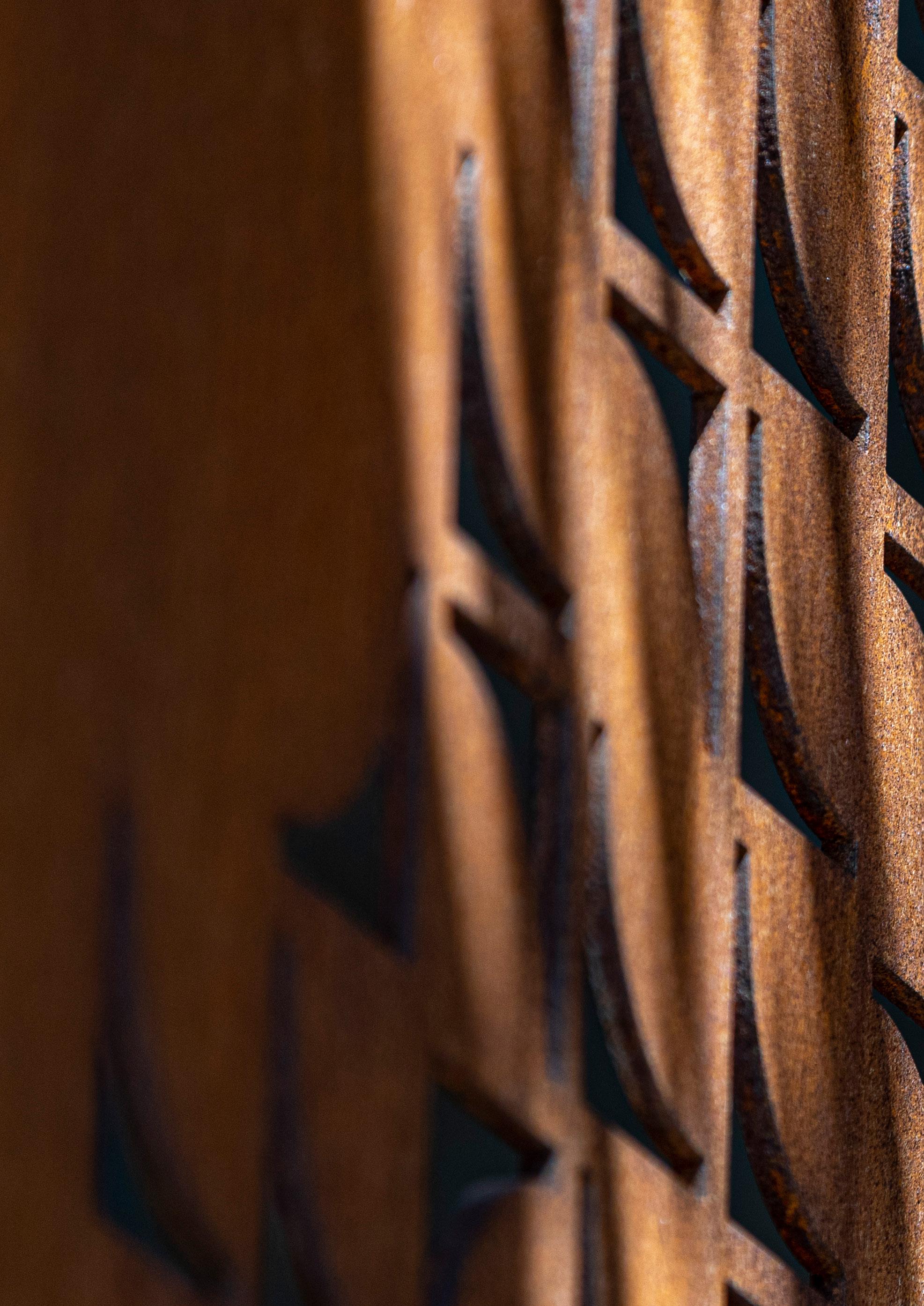
00 TBC First Issue Revision Log
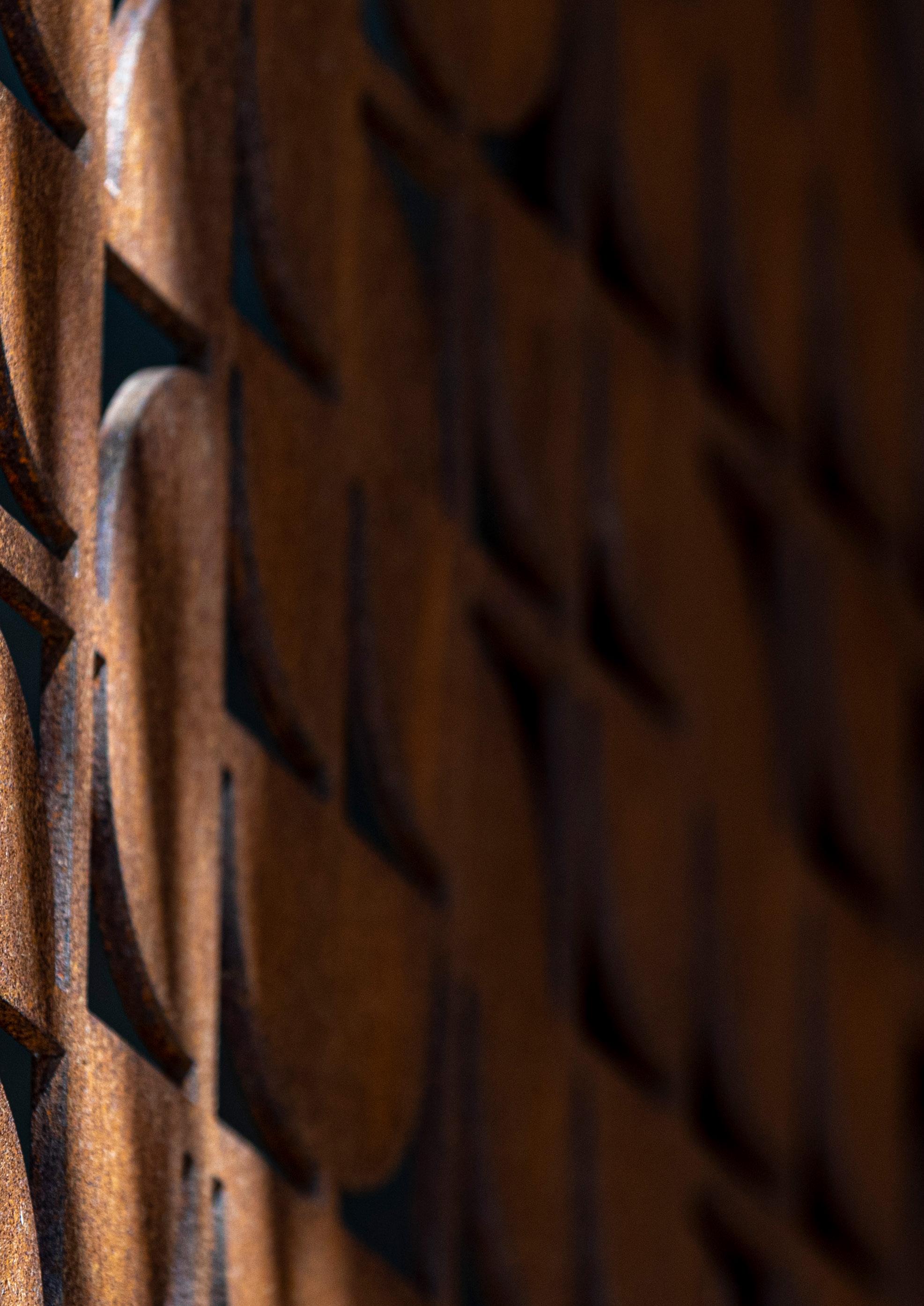
© Corstorphine & Wright Ltd
All designs and original information produced by Corstorphine & Wright within this document remain the Intellectual Property of Corstorphine & Wright This document may contain confidential or privileged information and is intended solely for the use of the intended recipient only No part of this publication may be reproduced or transmitted, in any form or by any means, without the express written permission of Corstorphine & Wright No warranty is provided for the accuracy or completeness of information contained in this document and we will not be liable to any person or entity who has relied on this document without our consent
www corstorphine-wright com
contact@cw-architects co uk
corstorphine-wright
@cwrightarch
corstorphinewright