
4 minute read
Do-it-yourself-Digitalisierung
für die Prozessindustrie
Warum warten, bis der Systemanbieter der Wahl endlich eine lang geforderte Funktionalität liefert? PTC befähigt seine Kunden durch die industrielle IoT-Plattform ThingWorx, die App-Entwicklung selbst in die Hand zu nehmen und damit nach eigenem Gusto die Digitalisierung voranzutreiben – Konzepte der Interessengruppe NAMUR lassen sich damit einfach verwirklichen. Und erste renommierte Firmen in der Prozessindustrie ließen sich bereits überzeugen.
Advertisement
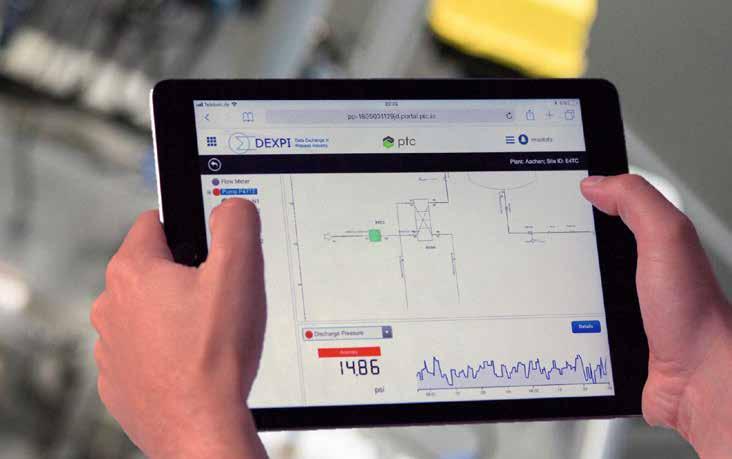
Die Prozessindustrie nimmt eine herausragende Stellung in unserer Wirtschaft ein. Im Jahr 2016 betrug die Bruttowertschöpfung der chemisch-pharmazeutischen Industrie in Deutschland rund 75 Milliarden Euro, was einem Anteil von 2,6 Prozent an der gesamtdeutschen Bruttowertschöpfung entspricht (1). Und die Digitalisierung beflügelt diesen Wirtschaftszweig in besonderem Maße.
Allein das Potenzial in der chemischen Industrie (etwa 42,5 Milliarden Euro 2016) durch Industrie4.0-Anwendungen liegt bei satten +30 Prozent bis zum Jahr 2025, was einer jährliche Steigerung der Bruttowertschöpfung von etwa 2,2 Prozent entspricht (2). Dazu sollte man wissen, dass die Kennzahl „Bruttowertschöpfung“ dem Gesamtwert der im Produktionsprozess erzeugten Waren und Dienstleistungen abzüglich des Werts an Vorleistungen entspricht. Das bedeutet: Je kostengünstiger die Produktion, desto höher die Wertschöpfung.
Die Prozessindustrie ist eine sehr kapitalintensive Branche, tut sich daher schwer mit neuen Geschäftsmodellen. Bei ihren Initiativen rund um die Digitalisierung konzentriert man sich aus diesem Grund vornehmlich auf Kosteneinsparungen. Aber wie kann die Digitalisierung dort gelingen? Denn die Ausgangssituation ist alles andere als vielversprechend. Schließlich ist in einem typischen Chemieunternehmen an dessen Standorten eine Vielzahl unterschiedlicher IT-Systeme installiert, die im Großen und Ganzen autark arbeiten. Viele der Arbeiten, die notwendig sind, um den Betrieb aufrecht zu erhalten und Regularien zu erfüllen, werden mit einem hohen Papieraufwand erledigt, und die erfassten Daten werden anschließend in die Back-End-Systeme manuell übertragen – Prozessdaten werden zwar digital gespeichert, aber ganz im Gegensatz zur gut digitalisierten Anlagenautomati-
Auf Fehlersuche: Per Fahrrad durch die Galaxis Ein möglicher Arbeitsgang (eigentlich eher eine Rundfahrt, weil häufig mit einem Fahrrad) im Chemiepark läuft in der Regel nach folgendem Schema ab: Während der Begutachtung wird ein auffälliges Geräusch oder Leck in einer Leitung entdeckt. Der Anlagentechniker nimmt Kontakt mit der Leitwarte auf und fragt nach, ob bereits Hinweise auf etwaige Unregelmäßigkeiten vorliegen. Das anschließende Telefonat führt zu einem weiteren Arbeitsschritt. Der Techniker fährt daher mit seinem Fahrrad zurück zur Leitwarte, um die Ursachenforschung zu vertiefen. Im weiteren Verlauf der Recherche beschließt man, Kontakt mit dem zuständigen Dienstleister aufzunehmen. Schlussendlich kommt in den nächsten Tagen tatsächlich ein Mitarbeiter der Wartungsfirma vorbei und versucht, den Fehler zu beheben. Vor Ort stellt dieser Techniker allerdings fest, dass ihm noch Informationen fehlen, und die Suche nach den passenden Dokumenten geht weiter.
Nach den nunmehr acht Jahre währenden intensiven Diskussionen rund um Industrie 4.0, Predictive Monitoring/Maintenance und intelligentes Dashboarding müsste eigentlich jedem klar sein, wie beim geschilderten fiktiven Fall eine durchgängige Digitalisierung die Fehlerbehebung von Tagen auf wenige Stunden reduzieren könnte – und darüber hinaus, wie viel Klarheit sie darüber schaffen würde, welchen Einfluss der Fehler auf den Gesamtzustand des Anlagensegments hat. Die Realität sieht freilich anders aus. Denn nach wie vor herrscht die Mentalität: Hände weg! – „never touch a running system“. Verständlich ist dies insofern, als Sicherheit oberstes Gebot ist, aber auch beim Ausfall einer Komponente die Wahrscheinlichkeit hoch ist, dass es zu einem Totalausfall des gesamten Produktionssystems kommen könnte,
Quelle: PTC 2019 was Umsatzeinbußen und erhöhte Kosten nach sich zieht. Daher werden eher die Instandhaltungsbudgets erhöht, als in vorbeugende Maßnahmen in Zuge einer Digitalisierungsstrategie investiert wird. Es bedarf viel Überzeugungsarbeit, um hier ein „Crossing the Chasm“1 zu erreichen.
Schritte heraus aus dem Dilemma
Viele Daten in der Prozessindustrie liegen außerhalb der Prozessleitsysteme kaum maschinenlesbar vor –zum Beispiel als historische Datenreihen („Historians“) – beziehungsweise können nur selten systemübergreifend konsolidiert werden, weil es eben an Vernetzung und Integration fehlt. Auf der anderen Seite könnten gerade diese Daten in Verbindung mit Informationen aus dem ERP-System, mit Umgebungsmesswerten und anderen für die Produktion wichtigen Informationen aus der Automatisierungspyramide (ISA-95) in Beziehung gesetzt, wertvolle Einblicke in die Abläufe der Anlage gewähren. Ein derartig konsolidierter Datenbestand könnte dazu genutzt werden, ihn auf Anomalien zu untersuchen, zum Beispiel mithilfe von rollenspezifisch aufbereite ten Dashboards, unabhängig von der Datenherkunft. Viele aufwendige manuelle Schritte bei der Ursachen forschung würden obsolet.
Wie kann dies gelingen? Zum Beispiel über eine Plattform, die Daten aggregiert, zu Informationen ver dichtet und im betrieblichen Kontext darstellt. Hier bei kommen analytische Methoden zur Anwendung, die die Abhängigkeiten des Prozessverhaltens in der Anlage aufzeigen. Mit den Mitteln der Digitalisierung ist es möglich, dem Anwender schnell und flexibel die Informationen bereitzustellen, die er für die jeweili ter Ausfallzeiten und einer Verbesserung der OEE
• das Auswerten qualitätsrelevanter Daten, um Einflüsse auf die Ergebnisqualität zu verstehen und am Ende so die Kundenzufriedenheit zu erhöhen
• die Nutzung der Konstruktionsdaten zur Erstellung von Augmented-Reality-(AR-)Anwendungen durch Überlagerung digitaler 3D-Modelle und Handlungsanweisungen mit real existierenden Komponenten. Instandhaltungsmitarbeiter könnten so auf einfache Weise eine animierte Darstellung der Montage und Demontage auszutauschender Komponenten erhalten.
Diese hier vorgestellten Maßnahmen können als Teil einer Digitalisierungs-Roadmap verstanden werden. Entlang dieser Roadmap und mit besserem Verständnis des Nutzens von IT-Technologien sind auch tiefere Integrationen in die eigenen Geschäftsprozesse sowie Interaktionen in der Automatisierungspyramide denkbar.
Plant Asset Navigator visualisiert werden. PAN liefert zum Beispiel Inhalte, die die Instandhaltungsmitarbeiter benötigen: Hervorheben des aktuellen Status einer Komponente innerhalb des P&ID (deshalb interaktives P&ID)
Identifizierung der voneinander abhängigen Komponenten durch Klicken in das P&ID Darstellung der Anlagenstruktur als zusätzliche Orientierungshilfe aufgabenspezifische Aufbereitung der Informationen, auch für mobile Endgeräte Verlinkung und Darstellung von Unternehmensdaten, zum Beispiel aus dem ERP Verlinkung zu Arbeitserlaubnis-Freigaben Schritt-für-Schritt-Anleitungen von Instandhaltungsaufgaben unter Einhaltung von Sicherheitsvorschriften.
Zu den Hauptvorteilen gehören nicht nur ein verbesserter Informationsfluss bezüglich Qualität und Zuverlässigkeit sowie die Reduzierung administrativer Tätigkeiten, es wird auch das Zusammenspiel von Engineering und Produktion optimiert sowie die Integration der Instandhaltung verbessert.
ThingWorx und Standards in der Prozessindustrie
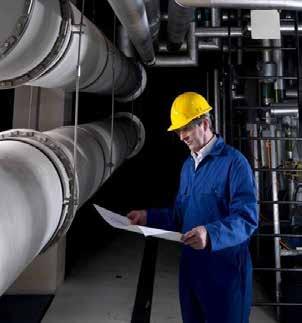
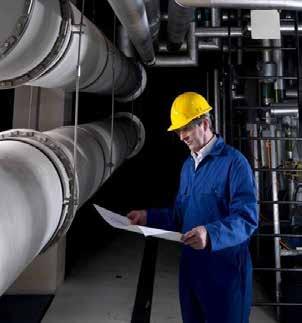
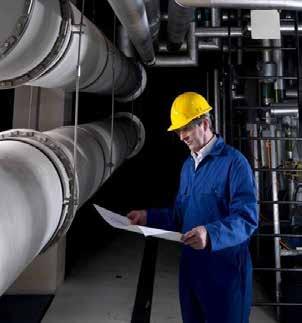
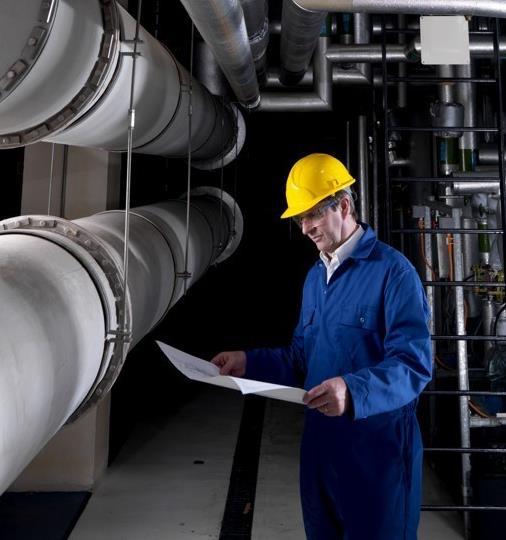
Der zuvor beschriebene Anwendungsfall „Instandhaltung“ und der Navigator „PAN“ als zugrunde liegende Technologie sind nur ein möglicher Use Case zur Umsetzung einer Digitalisierungsstrategie. Wesentlich mehr derartiger Use Cases sind denkbar, die natürlich alle in Hinsicht auf das Potenzial für Business Cases (Nutzen übertrifft Aufwand) analysiert werden müssen. Die Basis für die Umsetzung der Anwendungsfälle ist die IIoT-Plattform ThingWorx von PTC, die folgende Eigenschaften auszeichnet:
• Konnektivität: Das Modellieren von Schnittstellen geht sehr leicht von der Hand. Ein wesentlicher Punkt für die Prozessindustrie ist, diese Schnittstellen zu erstellen, um die unterschiedlichen Steuerungs- und Backbone-Systeme anbinden zu können. PTC hat diese Funktionalität in der ThingWorx Foundation zusammengefasst. Neben Standards wie OPC-UA, Modbus oder ODBC werden mehr als 150 Protokolle der unterschiedlichen Steuerungsanbieter interpretiert. Die ThingWorx-Plattform nutzt beispielsweise die Rest-APIs, sodass die OT- und IT-Ebenen sehr gut miteinander verknüpft werden können.
• Rapid Application Builder: Apps lassen sich schnell und intuitiv durch Drag & Drop erstellen. Mit anderen Worten: Die Kontextualisierung von Daten kann das Unternehmen selbst herstellen.
• Skalierbare Datenmodellierung: Es lassen sich automatisiert Datenmodelle herstellen, die für sehr unterschiedliche Anwendungsfälle nutzbar sind und die als Basis für immer neue Applikationen dienen können.
Mit der Übernahme von ThingWorx 2013 hat PTC einmal mehr ein Gespür für Zukunftstechnologien bewiesen. ThingWorx ist die Erfolgsstory für den Systemanbieter in vielen Branchen schlechthin – und damit auch für die Prozessindustrie. (bv)



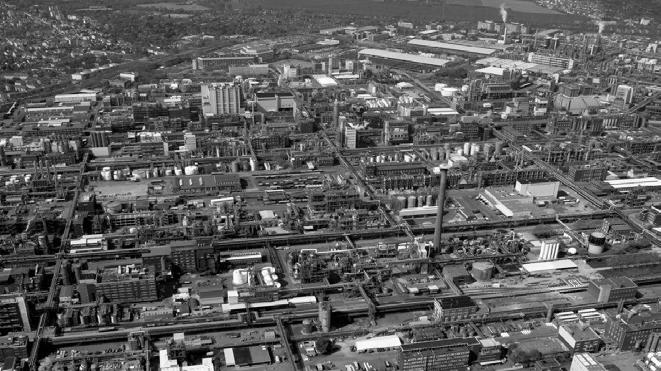