YOUR GUIDE TO EFFECTIVELY MANAGING INFECTION CONTROL IN HEALTHCARE
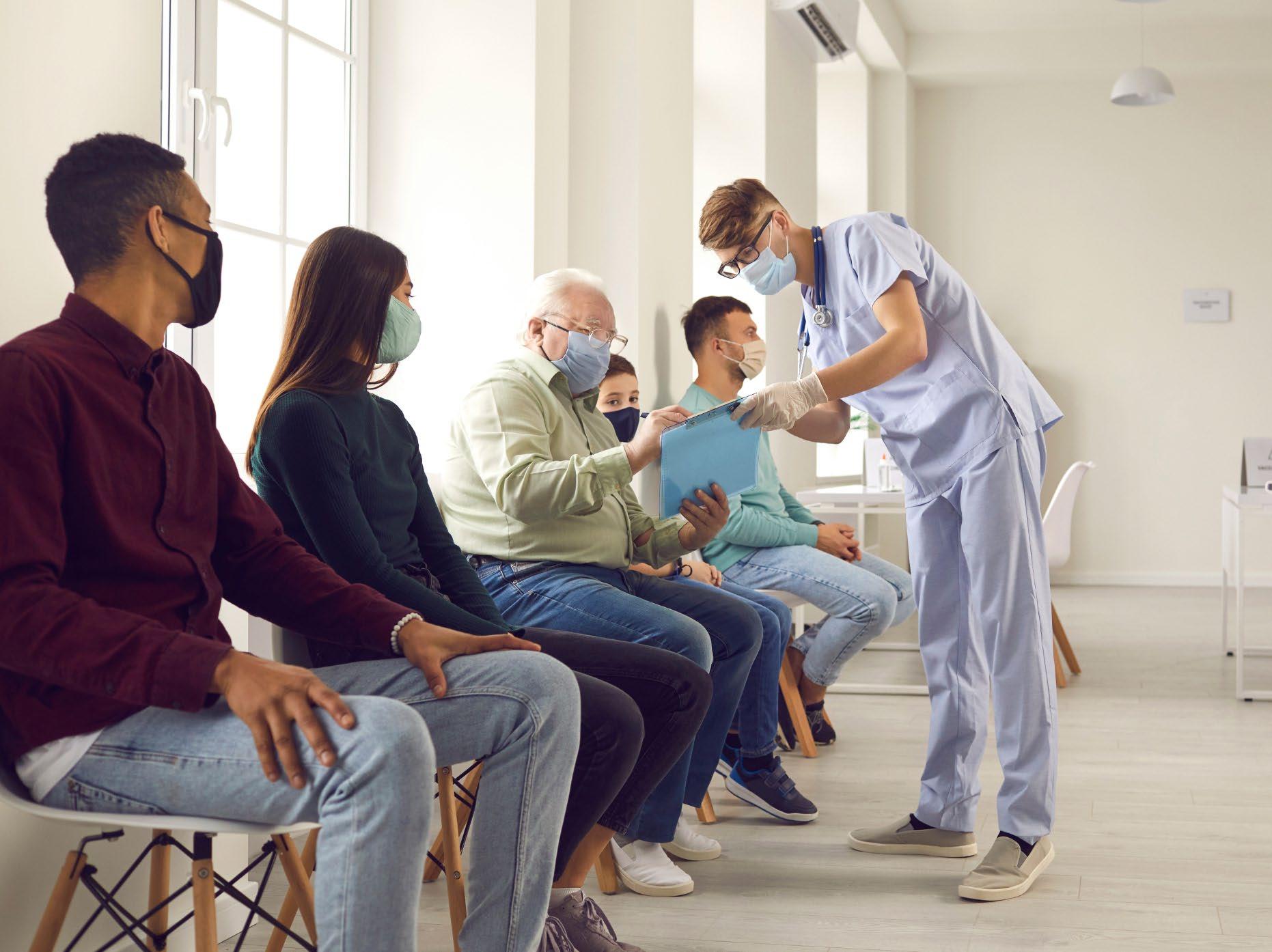

INFECTION
HAZARDS
INFECTION
HAZARDS
Healthcare facilities must comply with Infection Control Risk Assessment requirements despite labor shortages, tight capital budgets, and lack of appropriate equipment. Renting equipment from a knowledgeable provider offers an effective approach to overcome those challenges.
In a healthcare facility, patient care is everything. And during construction, renovation, or general facility maintenance, keeping patients and employees safe becomes more critical than ever. Maintenance staff and contractors need to be aware of the hazards unique to working in the healthcare setting. To overcome those hazards, you must implement additional precautions and conform to best practices— because lives depend on taking meticulous care.
That’s why the Centers for Disease Control require healthcare facilities to perform an Infection Control Risk Assessment (ICRA) before any construction, renovation, or repair projects, including removal of building materials. The American Society of Health Care Engineering (ASHE) governs ICRA to ensure contractors establish and maintain appropriate containment for dust and moisture. Everyone on the job site, including the crew, needs to understand and conform to the requirements.
Also critical for contractors and maintenance staff is having access to the equipment, tools, and staff to get the job done safely and effectively. But healthcare facilities face several challenges that complicate ICRA compliance, including labor shortages, budget constraints, and unanticipated conditions on-site.
This Guide to Infection Control in Healthcare Construction covers:
• Hazards construction creates
• Precautions during planned or unplanned facility maintenance
• Steps required for a risk assessment
• Meeting ICRA protocol
• Equipment needed to implement precautions
• Ways rental providers can support hospital facilities staff and mechanical contractors.
Construction, renovation, repair, and demolition in healthcare facilities require careful planning and coordination to minimize the risk of airborne infection during and after activities.
It’s not just major projects that create issues. Even removing a few ceiling tiles during routine maintenance or minor renovation can let infectious particles become airborne.
During construction activities, dust and moisture are the greatest threats to patient health. Any time particulate matter becomes airborne, people in the vicinity can breathe it into their lungs—and if moisture is present, mold, bacteria, and microorganisms may become part of the mix. An individual already fighting infection, injury, or disease or who is immunocompromised is particularly at risk.
And the risk may continue even after the construction ends. Particles released into the air during healthcare construction projects can remain suspended for hours, days, and even weeks. Particles can also migrate from one area of a facility to another and pose a threat. Steps to contain particles during construction and thorough cleaning afterward mitigate the risk.
The infection control risk assessment is a systematic process that determines risk to patients in various areas of the hospital—from diagnosis and treatment, such as clinical laboratories, imaging, and emergency rooms, to inpatient care including oncology and burn units.
The location of activities is critical. Even if you’re working outside the facility, you need to keep dust and moisture from infiltrating. Inside, you’ll need barriers and controls to clean the air in and around the site. In addition, you must maintain positive or negative air pressure as required.
The goal is always to properly clean all areas during and after work to avoid the risk of spreading infection.
Here's a look at the four steps of the ICRA protocol. For further information, review the ICRA matrix.
ICRA divides construction activities into four types for the purpose of assessment.
TYPE A
Inspection and non-invasive activities. Example: removing ceiling tiles for inspection.
Small-scale, short-duration activities that create minimal dust. Example: running cable in the ceiling.
Major demolition and construction projects. Example: removing a complete cabling system. TYPE
Work that generates a moderate to high level of dust or requires demolition or removal of fixed building components or assemblies. Example: sanding a wall for painting or performing mechanical or electrical work above ceilings.
Healthcare facilities have unique populations with susceptibility to construction-related infections. Requirements for renovating the lobby will clearly be different from those for Central Sterile Supply. Here’s each risk level and an example of the relevant area.
ENDOSCOPY PHYSICAL THERAPY
EMERGENCY ROOM, LABOR & DELIVERY, SURGICAL UNITS
ONCOLOGY OR BURN UNIT
After you’ve identified the construction project type and risk group, you can use a matrix to determine which of the four infection control classifications is right for the activity. Cross-referencing will tell you what precautions are associated with activities both during and after completion of the project.
Class I: Minimize raising dust - If you remove a ceiling tile for visual inspection when the task is done, replace it immediately and clean the area.
Class II: Control dust, block off and seal air vents, and remove or isolate the HVAC system where work is being performed.
Class III: Remove or isolate HVAC system where work is being performed. Complete all critical barriers to seal from non-work areas or implement the control cube method (HEPA Cart), and maintain negative air pressure within the work site using HEPA filtration.
Class IV: Isolate HVAC system where work is being performed, Complete all critical barriers to seal from non-work area or implement control cube method (HEPA Cart), construct sealed anteroom, and require all personnel to pass through before entry/exit, maintain negative air pressure within the work site using HEPA filtration, do not remove barriers from work area until completed project is inspected by the owner's safety department and Infection Control department.
If Class III or Class IV control procedures are required, you’ll also need to get infection control approval first.
The remainder of the ICRA matrix helps you put a plan into place. You’ll identify the site of activity, issues related to it, containment measures, and specifics for the facility. Contractors generally work through these steps and discuss infection prevention with the project coordinator, construction superintendent, manager, and foreman for the job.
Proactive strategies make it easier to implement precautions to prevent airborne infections during construction, renovation, and demolition. But healthcare facilities today face a number of challenges when meeting ICRA requirements.
First is the labor shortage, which impacts teams in healthcare engineering and maintenance, according to ASHE Health Facilities. Retirements, resignations, and a lack of new candidates have shrunk the hospital workforce, and inadequate planning for moving forward has intensified the shortage. But hospitals must still operate safely. Contractors can help, but so can a rental company with well-maintained equipment and tools and trained personnel who can assist with set-up, tear-down, and operation.
Like most organizations, healthcare facilities are aiming to do more with less. Budgets are shifting from capital to operating expenditures, which makes it sensible to consider renting equipment. That way, facilities spend opex budget with no or low upfront cost and the option to spread the investment over time. A rental company that carries key equipment and tools to meet ICRA requirements in an organized and safe manner can make budgeting much easier.
Healthcare facilities and contractors also run into complications on projects, including equipment that’s not working properly. That often means a delay while you order parts and wait for delivery, which can upset your construction or maintenance schedule. Or you could rent from a provider that has a large selection of clean, bagged, and tagged IAQ and mobile containment equipment stored in dedicated facilities and ready to go.
In short, many of the challenges healthcare facilities face can be met by working directly with a reputable rental equipment provider or asking the mechanical contractor to do so. The right company will understand the importance of infection control and conformance with ICRA standards.
Working with a company like Sunbelt Rentals can make compliance with ICRA much easier. We have all the equipment necessary and can provide it to healthcare facilities or mechanical contractors on a temporary basis:
Scientific Air Management System-400 3-stage air scrubbers with UV-C light technology kill up to 99.9995% of airborne pathogens, including mold
3-stage filtration including pre-filter, HEPA filter, and post-filter removes both larger and microscopic particles
Maintain indoor design temperatures for the facility with temporary or supplemental heating and cooling solutions
Collect outside and room air, remove dust and other particles, and adjust temperature and humidity to supply healthy, comfortable air to rooms
HEPA vacuums in many sizes provide wet/dry operation and multi-stage filtration
Mobile HEPA soft containment cart can contain negative pressure airborne particles in many applications
DEHUMIDIFICATION OR HUMIDIFICATION EQUIPMENT
Maintain ideal humidity to make critical care environments safer for patients
Aesthetically pleasing STARK modular walls exceed ICRA Class IV requirements, keep dirt and debris inside the construction site, and provide optimal flexibility for different project phases
Accessories like hinged doors and preassembled windows solve containment issues
Effectively and efficiently keep floors clean and dry and avoid risk of slips and falls
Disinfect in a powerful, efficient, and cost-effective way
Ensure appropriate differentials across isolated spaces with a system to monitor air pressure
Full range of high-performance tools meets every construction and demolition need
PRO TIP: Establish a Sunbelt Rentals account before you ever need equipment or tools to save time and keep your project on schedule.
Whether or not a healthcare facility is undergoing construction or renovation, you may need critical environmental products to maintain uninterrupted power, temperatures, humidity, indoor air quality, and facilities. Sunbelt Rentals provides the following equipment to help:
• Spot cooling
• Temporary generators
• Electric heaters
• Heat pumps
• Light towers
• Lifts
Healthcare facilities perform a critical service but are not immune from natural disasters, from hurricanes and wildfires to tornados and floods. To be ready, develop a contingency plan with a rental company that can provide the equipment you need as soon as you need it.
In terms of ICRA:
• You need a plan to handle dust and moisture intrusion if an HVAC system fails
• A rental partner can save you precious time by working through scenarios and ensuring you have the equipment you need
• Whether it's climate control, power generation, or anything in between, we have you covered
Sunbelt Rentals maintains a fleet of reliable, high-quality equipment to help you establish and maintain containment according to ICRA standards. Our experienced team understands the hazards created by dust and moisture in a healthcare facility and can help you engineer an effective and budget-conscious solution.
You can trust that we will deliver the equipment you need on time and support you throughout the rental. If anything goes wrong, we will fix it. We have equipment locations around the country and deliver the right solution immediately.
Our people and processes make the difference that gives your organization a superior outcome. For a free consultation or to discuss equipment to comply with ICRA requirements, reach out to our team at 844-247-9693 or visit us online at sunbeltrentals.com.
Every winter, the price of fuel to run temporary construction heaters rises - whether that's propane, natural gas, diesel, or electricity.
But in 2022, the prices are already starting from a higher point. For example:
Propane cost $3.29 per gallon on average in March 2022
Natural gas peaked at $0.89 per therm in August
As of July, diesel has been running anywhere from $5.50-$7.00 per gallon delivered
That leaves contractors wondering how to keep their projects on budget this winter. Temporary heating serves a critical purpose, from concrete pour to installing finishes.
But now, fuel prices play a more significant role than ever in your construction heating solution.
Understanding the cost of various fuels used to operate temporary construction heaters is essential when selecting the fuel type for your project.
*Note that the therm is defined as the amount of natural gas needed to produce 100,000 BTUs
*Source EIA.gov
With rising fuel costs, staying on budget is critical. Here are five strategies contractors can use.
1.
Attempt to have the structure sufficiently complete to install a temporary or permanent natural gas meter. Natural gas is the most cost-effective fuel with the lowest carbon impact
2.
Ensure the building envelope is as tight as possible to mitigate heat loss and control infiltration.
3.
Ensure that you right-size your heating system by working with a temporary construction heating expert who can calculate your heat loss and design the most fuel-efficient solution.
4.
Plan ahead of the heating season to lock in a low fixed cost with a seasonal lease.
5.
Maximize the fuel efficiency on temporary construction heaters by utilizing THP-Series heaters with self-modulating gas burner controls whenever possible.
Most temporary construction heaters utilize a thermostat to control temperature.
Since 1965, Temp Air Manufacturing (now a division of Sunbelt Rentals) has designed & manufactured industry-leading temporary construction heaters. We are always looking for innovative ways to produce a better heater. If you set it at 65°F, the heater cycles on and off to maintain the temperature.
The THP-Series heaters are equipped with self-modulating gas controls, which automatically adjust gas flow to outside temperature changes, thus only using the specific amount of fuel needed to heat the space to the desired temperature. This prevents overheating the space, which wastes fuel and poses safety risks.
The centrifugal blowers provide constant high CFM air delivery with high static pressure for better heat distribution and drying times.
THP-Series heaters can operate off liquid propane (LP) or natural gas (NG), an advantage once the gas meter is installed. The seamless switchover leaves the contractor with the option to start on LP and switch over to NG.
Fuel savings can significantly offset the rental/lease cost of temporary heaters.
The expense of fuel and energy will be far higher than the cost of renting the solution. A highly efficient system can save you money in the form of fuel savings.
Take a look at the chart below to compare the cost of running an indirect fired heater and a THP-Series heater with self-modulating controls under identical conditions.
As you can see, despite the THP-Series heater costing $2,500 more to rent over the course of a winter, you would ultimately save 3,000 gallons of propane and $7,300.
To adapt this to your own situation, Sunbelt Rentals can calculate the best temporary heating solution for your application.
In addition to THP-Series, Sunbelt Rentals offers every type of temporary heating solution. Ultimately, we want to meet all your requirements for budget, timing, conditions, safety, and other critical factors.
Factors such as fuel and energy available and local restrictions will determine what types of heaters you can choose.
Direct fired heaters provide dependable heat for contractors and workers due to their rugged design and dependable operation on construction sites.
DIRECT FIRED
Indirect fired heaters provide clean, dry, odorless heat. They also include air outlets that accommodate flexible ducting, which allows placing the heaters a safe distance from special event tents and other structures.
Hydronic / ground heaters provide high-efficiency solutions for thawing frozen ground and curing concrete. Trailer mounted for easy towing.
These heaters will provide dry, even heat when combined with steam or hot water. Ideal for use in renovation or construction projects with access to steam or hot water such as universities, hospitals, and other municipal locations.
Radiant heaters are ideal for heating people and objects in wide open spaces.
Electric heaters can provide clean, dry heat for various small to mid-size construction projects with the available power requirements.
Contractors, investors, employees, and building owners are all paying increased attention to sustainability initiatives to meet Environmental, Social, and Governance (ESG) goals.
In addition to saving on fuel costs for construction heating, greater fuel efficiency can lower greenhouse gas (GHG) emissions which will help your company meet ESG goals.
Sunbelt Rentals also has ESG goals—to reduce GHG emissions by 15% by 2025, 35% by 2030, and 50% by 2035. We're already working with many manufacturers and organizations pursuing innovative clean energy technologies.
For example, we recently purchased 700 Ford F-150 EV trucks for employee use. That commitment makes us ideal partners for other companies aiming to reduce environmental impact. That commitment extends to construction heating solutions.
If you have questions on achieving your organization’s ESG goals, we’re happy to help. We’re doing the research so we can see what’s on the horizon and beyond, and share our learnings, equipment, and resources with you.
As the leading provider of temporary, portable, supplemental, large scale, and emergency cooling, heating, and dehumidification equipment, Sunbelt Rentals can help you with your temperature control and HVAC rental needs for commercial, construction, and industrial requirements.
Our portable and larger packaged cooling and heating systems, coupled with the expertise of our climate control team, can ensure the right permanent or temporary temperature control solutions.
For help selecting the best temporary heating solution, contact us today at 866-964-0819 or visit us online at sunbeltrentals.com
GUIDANCE AND CALCULATIONS FOR COOLING JOB
The costs of heat outweigh costs of cooling.
1. PRODUCTS AND SERVICES: Mistakes resulting in more defects and lower quality
OF EXCESSIVE HEAT 4 $ $ $
2.
EMPLOYEES Increased turnover and absenteeism
3. PRODUCTIVITY: Decreased worker and economic output
4. SAFETY: Heat-related illness due to environmental conditions and heat stress
EXCESSIVE HEAT OFTEN COSTS MORE than the investment in temporary cooling. The key is determining the right cooling solution for your situation.
How to control temperature and humidity in critical situations.
COMFORT:
Keep occupants comfortable
CONSTRUCTION:
Maintain optimal conditions for application and curing of interior finishes and coatings
HEAT REMEDIATION:
Cool personnel in extreme conditions
PROCESS:
Meet demands for a process, equipment, or product
SPOT:
Manage conditions in a defined area or zone
TYPE
Air-cooled
COOLING MECHANISM
Pumps cool air into a space and exhausts hot air and enables fast installation.
APPLICATION
Facility maintenance, education, retail
TYPE
Water-cooled
COOLING MECHANISM
Cooling with an external water source, like a central cooling tower or chiller.
APPLICATION
Hospitals or retail
TYPE
Evaporative or swamp cooler
COOLING MECHANISM
Internal or external water source and a fan that pushes air across a space.
APPLICATION
Warehouses and outdoors
CALCULATING THE HEAT LOAD based on contributing factors helps you choose the right portable cooling equipment for your application.
Start with requirements in an empty room.
ASSUMPTIONS
• Building well sealed and envelope insulated
• No minimum air changes per hour required
• No internal heat sources
• Conditioned space ≤ 12 feet high
COMFORT COOLING AT 75-85ºF
ENVIRONMENT
COOLING GUIDANCE starts with square footage, but factors that impact requirements include openings and internal heat.
Adjust your calculations based on situation specifics.
AREAL EXTENT:
Square footage that needs cooling
SOLAR LOADING:
20-40ºF temperature increase due to sun on glass creating surface temperatures as high as 130ºF
OPENINGS:
Heat gain due to hot air outside entering and replacing cool air inside
INSULATION:
Resistance to heat transfer depend on “R” value
TEMPERATURE AND HUMIDITY
REQUIREMENTS:
Differs for an office, hospital, school, retail store, warehouse, or server room
CEILING HEIGHT:
Greater than 12 feet increases demands
INTERNAL HEAT LOADS:
Heat generated by electronics, machinery, and people
that contribute to heat, simple calculations will help you approximate heat load in various situations.
Calculate heat gain based on insulation values.
R VALUES
R = Insulation value = 13 SF·°F/BTU
U= Thermal transmittance = 1/R = 0.077 BTU/SF ·°F
ΔT = Temperature difference = 100ºF (outside) - 80ºF (inside) = 20ºF
A = Area = 14,400 SF
Q = Heat load
Q = U x A x ΔT
Q = 0.077 BTU/SF·°F x 14,400SF x 20ºF
Q = 22,176 BTUs
To determine the R value when several types of insulation are used, you perform the heat loss or heat gain calculation for each material and area covered, then sum these to get the total heat loss or gain for the space.
Determine internal heat load for adequate server cooling.
EXAMPLE CALCULATION:
Use the kW rating for the uninterruptible power supply (UPS) to determine electronic heat loads.
Assume UPS rated for 24 kW.
24 kW x 3,413 BTUs/kW = 81,912 BTUs
81,912 BTUs/12,000 BTUs/ton = 6.8 tons
Add BTUs for size of space.
Assume space is 400 SF.
6.8 tons + 1 ton = 7.8 tons or almost 8 tons of cooling capacity.
OTHER FACTORS TO CONSIDER include the required ΔT, location of AC equipment, and ways to exhaust condenser air from the space.
Outside cooling creates unique demands.
• Tents with sides require ~1 ton of cooling/125 SF
• 24 people require ~1 ton of cooling—and more if they’re dancing or there are service tables for dining.
• Tents require more cooling if they’re clear or situated on asphalt rather than grass
• For an open tent in 100ºF, choose an evaporative cooler or power breezer instead of an air conditioner
CALCULATION:
Assume a 600 SF tent with 60 people.
Q = 600 SF x 1 ton of cooling/125 SF + 60 people x 1 ton of cooling/24 people
Q = 4 tons + 2.5 tons = 6.5 tons or ~7 tons
TO COOL A MEDICAL TENT, consider indoor air quality required and rental duration, which may change cooling to heating requirements.
Protect product and people from excessive heat.
GUIDANCE:
• Start with comfort cooling requirements.
• Check specifications to determine the optimal temperature inside space.
• Determine BTUs from process equipment, ovens and furnaces.
• Sum up to reach total heat load.
• May require outside air to meet minimum air changes
• May require cascading air conditioners to cool outside air
IN LARGE FACILITIES, you can also identify the specific areas or zones that most need cooling and treat these as spot cooling applications.
Experience and expertise ensure adequate cooling. Heat load calculations are straightforward—but figuring out the variables and intangibles to use is not. That’s where expert guidance and years of experience pay off.
Sunbelt Rentals partners with you to create an optimal, cost-effective cooling solution. We’d be happy to provide a free estimate for your project to ensure you’ve right-sized the job.
For more information, contact us today at 866.213.6840 or visit us online at sunbeltrentals.com.