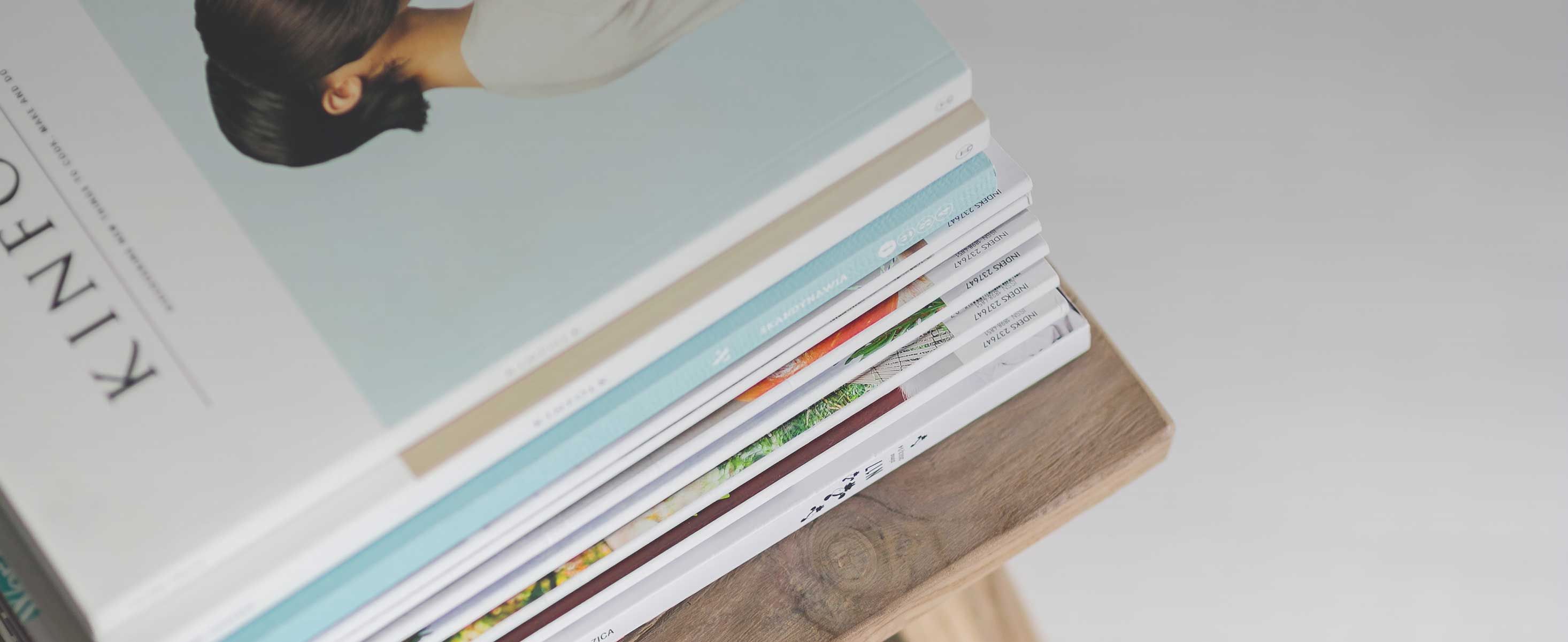
13 minute read
3.1.2 Thuyết minh qui trình
from BÁO CÁO KẾT QUẢ THỰC TẬP TÌM HIỂU QUÁ TRÌNH SẢN XUẤT TINH BỘT SẮN NHÀ MÁY TINH BỘT SẮN QUẢNG NAM
3.1.2 Thuyết minh qui trình: 3.1.2.1 Nguyên liệu: Nguyên liệu là củ sắn tươi được nhà máy thu mua từ các hộ thu mua sắn trên địa bàn tỉnh Quảng Nam và các tỉnh lân cận trong khu vực miền trung và Tây Nguyên. Sắn nguyên liệu được xe chở đến nhà máy, xếp theo thứ tự xe đến trước xếp trước xe đến sau xếp sau. Xe vận chuyển sắn đi qua cân điện tử để xác định khối lượng trước khi vào bãi nhập liệu. Sắn được tháo xuống bãi nguyên liệu nhờ công nhân và hệ thống cào bằng động cơ. Xe chở sắn đi theo hình chữ C để tránh chà cán lên sắn gây dập nát. Tại bãi nguyên liệu, nhân viên KCS tiến hành lấy mẫu sắn của mỗi xe đi kiểm tra hàm lượng tinh bột để định giá mua, đồng thời xác định lượng tạp chất trong nguyên liệu.
3.1.2.2 Phễu nạp liệu: Mục đích: Chứa nguyên liệu, điều tiết lượng sắn cấp lên băng tải một cách vừa phải và cấp liệu một cách dễ dàng, tạo điều kiện dây chuyền hoạt động liên tục, chủ động. Thực hiện: Xe xúc đưa sắn từ bãi nguyên liệu vào phễu nạp liệu. Phễu được thiết kế dạng đáy hình côn dưới đáy có cửa thoát, có bộ phận sàng rung đặt ngay dưới cửa thoát, sàng rung chuyển động tịnh tiến nhờ động cơ, 5 giây dao động một lần giúp phân phối nguyên liệu lên băng tải nghiêng một cách đều đặn với khối lượng thích hợp.
Advertisement
3.1.2.3 Băng tải nghiêng 1: Mục đích: vận chuyển sắn từ phễu nạp liệu đến lồng bóc vỏ. Thực hiện: Băng tải được đặt nghiêng so với mặt đất, nối giữa phễu nạp liệu và lồng bóc vỏ, chuyển động nhờ động cơ truyền động cho tang dẫn động và tang căng giúp đưa nguyên liệu lên lồng bóc vỏ. 3.1.2.4 Lồng bóc vỏ Mục đích: Loại bỏ phần vỏ gỗ chứa chủ yếu cellulose, hemicellulose không có giá trị trong sản xuất tinh bột và phần lớn đất đá, tạp chất dính trên củ sắn, nhằm tăng hiệu quả cho công đoạn rửa và tăng chất lượng tinh bột thành phẩm. Thực hiện: Sắn được băng tải chuyển từ phễu nạp liệu đến lồng bóc vỏ, lồng bóc vỏ có thiết kế một khe hở nhỏ hơn củ sắn để loại một phần tạp chất nhỏ. Lồng bóc vỏ có dạng hình trống bên trong có cánh xoắn, trống quay được nhờ động cơ. Tại đây, một phần vỏ lụa sẽ được tách ra khỏi củ sắn nhờ lực ma sát giữa củ sắn với nhau, giữa củ với thành của lồng bóc vỏ và với các cánh xoắn bên trong lồng. Vỏ lụa và tạp chất sẽ lọt qua thành của lồng bóc vỏ và rơi xuống máng chứa tạp chất. Sau khi qua lồng bóc vỏ sắn được làm sạch 50 – 55% vỏ lụa.
3.1.2.5 Rửa củ: Mục đích: Tách phần vỏ lụa còn sót lại, làm sạch củ sắn, loại những tạp chất còn sót lại trên nguyên liệu Thực hiện: Sau khi qua lồng bóc vỏ, sắn được đưa đến bể rửa. Tại đây, sắn được làm sạch nhờ tác dụng khuấy đảo của cánh khuấy và nước. Sắn được khuấy đảo tạo lực ma sát giữa sắn với cánh khuấy, giữa sắn với thành bể và giữa sắn với nhau giúp loại bỏ vỏ lụa còn lại và tạp chất. Nước được cung cấp liên tục vào bể và các vòi nước được bố trí phía trên phun xuống bể rửa giúp tăng hiệu quả làm sạch. Sau khi qua máy rửa, sắn được loại bỏ 90% vỏ gỗ và phần lớn tạp chất. 3.1.2.6 Chặt cùi Mục đích: Loại bỏ những phần cùi cứng của củ sắn, cùng một số thành phần tạp chất lớn sót lại, tạo điều kiện cho máy băm hoạt động hiệu quả hơn. Thực hiện: Sau khi được rửa sạch sắn được đưa lên băng tải nghiêng 2, trên đường đi của băng tải nghiêng 2 có bố trí hai công nhân ngồi bên cạnh để chặt bỏ cùi sắn, loại các tạp chất còn sót lại.
3.1.2.7 Máy băm: Mục đích: Làm nhỏ củ sắn, tạo điều kiện thuận lợi cho công đoạn chế biến tiếp theo, tránh tắc nghẽn khi mài, giảm chi phí năng lượng đáng kể và nâng cao hiệu suất của máy mài. Thực hiện: Nguyên liệu được chuyển đến máy băm nhờ băng tải nghiêng 2. Tại đây, nguyên liệu được băm thành những đoạn ngắn khoảng 5cm nhờ hệ thống dao tĩnh và dao động của máy băm.
3.1.2.8 Máy mài Mục đích: Phá vỡ cấu trúc củ sắn, giải phóng tinh bột vào nước để tạo hỗn hợp sau mài gồm tinh bột, nước và bã. Hiệu suất mài càng cao thì lượng tinh bột thu hồi càng lớn. Tại công đoạn này còn bổ sung dung dịch acid H2SO3 nhằm ngăn chặn sự xâm nhập của vi sinh vật gây biến màu tinh bột.
Thực hiện: Sau khi qua máy băm, sắn được mài trong hệ thống 4 máy mài nhờ ma sát với trục mài. Để tránh sự cố và giảm trở lực nên bổ sung nước (nước bổ sung ở đây lấy chủ yếu là dịch của trích li tận dụng và trích li thu hồi). Lượng nước được bổ sung phải phù hợp để dịch sữa không quá đặc hay quá loãng. Nếu lượng nước bổ sung ít thì dịch sữa đặc sẽ gây nghẽn bơm và tổn thất tinh bột theo bã, nhưng nếu nước bổ sung nhiều thì thùng chứa của máy mài sẽ bị quá tải và tốn năng lượng để loại nước ở công đoạn sau.
3.1.2.9 Trích ly thô Mục đích: Tách riêng phần bã ra khỏi dịch sữa. Quá trình này có bổ sung acid H2SO3 để chống sự xâm nhập của vi sinh vật nhằm giữ độ trắng cho dịch tinh bột
Thực hiện: Dịch sữa hỗn hợp từ thùng chứa của máy mài được bơm đến hệ thống trích ly thô gồm 10 máy. Tại đây xảy ra sự tách pha lỏng - rắn dựa vào lực ly tâm và lưới lọc tạo thành 2 phần: phần dịch sữa sau trích ly và phần bã đi ra khỏi máy trích ly theo 2 đường khác nhau. Dịch sữa về thùng chứa sau đó được bơm đến sàng cong 1, phần bã ra máng chứa bã được cánh vít vận chuyển đến thiết bị trích ly tận dụng.
3.1.2.10 Trích ly tận dụng: Mục đích: Tiếp tục trích ly lượng tinh bột còn sót trong bã sau trích ly thô, nhằm nâng cao hiệu suất thu hồi bột.
Thực hiện: Bã sau trích ly thô ở máng chứa được đưa vào hệ thống trích ly tận dụng gồm 10 máy. Tương tự như trích ly thô, tại đây cũng bổ sung H2SO3 vào, dưới tác dụng lực ly tâm và lưới lọc xảy ra sự tách pha rắn chia làm 2 phần: phần dịch lỏng được dùng để cấp cho máy mài, phần bã đưa qua trích ly thu hồi. 3.1.2.11 Trích ly thu hồi: Mục đích: Lấy tối đa lượng bột sót trong bã. Thực hiện: Bã sau trích ly tận dụng sẽ qua hệ thống trích ly thu hồi gồm 3 máy, dạng trích ly ngang. Tại đây, cũng dưới tác dụng của lực ly tâm và lỗ lưới xảy ra sự tách pha rắn – lỏng. Phần dịch lỏng trích ly được sẽ được bổ sung vào máy mài, phần bã rắn đươc đưa đi xử lý bã.
3.1.2.12 Sàng cong: Mục đích: Tách tạp chất có kích thước lớn hơn hạt tinh bột. Thực hiện: Gồm có 2 hệ thống sàng cong: sàng cong cấp 1 có kích thước 50μm và sàng cong cấp 2 có kích thước 75μm. Dịch sữa sau trích ly thô được bơm đến sàng cong cấp 1 (gồm 7 máy) và sàng cong cấp 2 (gồm 6 máy), tại đây dưới tác dụng của áp lực vòi phun và lỗ lưới, xảy ra sự tách pha rắn - lỏng: phần qua lưới sàng cong cấp 1 sẽ về thùng chứa để đến sàng cong cấp 2, phần qua lưới sàng cấp 2 sẽ đi đến công đoạn phân ly; phần không qua ở sàng cong cấp 1 sẽ quay lại trích ly thô và phần không qua lưới ở sàng cong cấp 2 thì sẽ quay trở lại sàng cong cấp 1.
3.1.2.13 Phân ly: Mục đích: Tách mủ chứa các hợp chất hữu cơ không mong muốn như protein, lipid, các hợp chất kết tụ ra khỏi dịch sữa tinh bột giúp nâng cao chất lượng bột thành phẩm. Thực hiện: Quá trình phân ly được thực hiện nhờ lực ly tâm và chênh llệch khối lượng, qua 2 giai đoạn bằng máy phân ly cao tốc: + Phân ly giai đoạn 1: Gồm 3 máy, số vòng quay 4500 vòng/phút. Dịch tinh bột được bơm từ thùng chứa sau sàng cong cấp 2, qua cyclon tách đất đá, vào máy phân ly cấp 1. Tại đây, dưới tác dụng của lực ly tâm và sự khác nhau về khối lượng xảy ra sự tách pha lỏng - lỏng. Các thành phần tạp chất hữu cơ nhẹ và nước chuyển động lên trên và nhờ bơm hút ra ngoài. Phần nặng chứa tinh bột
sẽ đi xuống dưới về thùng chứa theo kênh riêng. Dịch sữa tinh bột sau phân ly 1 đạt nồng độ 7-14ºBe thì được bơm qua phân ly cấp 2. Nếu không đạt nồng độ trên thì phải phân ly lại đến khi đạt yêu cầu. + Phân ly giai đoạn 2: Gồm 3 máy, vận tốc quay 5700 vòng/phút. Hoạt động với nguyên lý tương tự như phân ly giai đoạn 1. Sau phân ly 2, dịch sữa đạt nồng độ 17- 20º Be sẽ đưa về thùng chứa đến ly tâm, nếu không đạt yêu cầu thì hồi lưu về thùng chứa sau phân ly 1 để tiếp tục quá trình phân ly 2 nhằm nâng cao độ Be. Quá trình phân ly có bổ sung một lượng lớn nước nhằm tách triệt để mủ và các thành phần hữu cơ không mong muốn. Nước thải của giai đoạn phân ly được đưa ra ngoài theo mương dẫn nước thải đến hồ kị khí.
3.1.2.14 Ly tâm: Mục đích: Tách phần lớn nước ra khỏi dịch tinh bột để thu hồi bột ẩm ( có độ ẩm từ 30-40%), tạo điều kiện thuận lợi và giảm chi phí cho giai đoạn sấy. Thực hiện: Dịch sữa tinh bột sau phân ly giai đoạn 2 được bơm đến hệ thống ly tâm tách nước gồm 4 máy. Tại đây, dưới tác dụng của lực ly tâm và lỗ lưới, xảy ra sự tách pha lỏng - rắn: phần bột rắn sẽ đươc trục vít và băng tải đưa qua sấy, phần nước ly tâm hồi lưu về thùng chứa sau phân ly 1, hoặc thùng chứa sau sàng cong 1 nếu thùng chứa phân ly 1quá tải. 3.1.2.15 Sấy và làm nguội: Mục đích: Làm khô tinh bột sắn đến độ ẩm yêu cầu (11-13%). Thực hiện: Sấy khí động: bột ẩm sau ly tâm được vít tải đưa xuống băng tải đến thùng chứa, tại đây bột được đánh tơi nhờ các vít đánh tơi. Sau đó, bột vào hệ thống sấy nhờ vít tải, và quạt hút chân không, vít tải vừa có nhiệm vụ cấp bột vừa định lượng, đưa bột vào hệ thống sấy một cách vừa phải ổn định. Bột được sấy khô nhờ hệ thống sấy khí động. Trên đường đi, bột tiếp xúc trực tiếp với không khí nóng trao đổi nhiệt với không khí nóng làm bay hơi ẩm và được làm khô đến độ ẩm yêu cầu.
Sau sấy, bột được thu hồi nhờ hệ thống cyclone, bột theo không khí nóng đi vào tiếp tuyến với thành cyclone, va đập vào thành cyclone mất động năng và rơi xuống đáy của cyclone sau đó được vít gom bột gom lại dưới đáy hệ thống cyclone và được đưa qua hệ thống rây – bao gói. Trên đường đi bột sẽ được làm nguội nhờ trao đổi nhiệt gián tiếp với không khí bên ngoài thông qua thành ống. Không khí nóng sau khi qua cyclone đã được tách hết lượng bột và được thải ra ngoài nhờ quạt hút.
3.1.2.16 Rây và bao gói:
Mục đích: Rây bột để thu bột đạt kích thước đồng nhất, loại các tạp chất còn sót, tăng chất lượng thành phẩm. Đóng gói để bảo quản bột tránh các tác nhân gây hư hỏng từ bên ngoài và thuận tiện cho vận chuyển phân phối. Thực hiện: Tinh bột sau khi được làm nguội sẽ được đưa vào các cyclon thu hồi đặt trên máy rây - đóng gói. Tương tự như các cyclone ở hệ thống sấy hạt tinh bột được gom lại dưới hệ thống cyclone và được rơi vào hệ thống rây. Tại đây, các hạt tinh bột lọt lưới rây sẽ xuống máng phía dưới và được phân phối vào các đường ống đến hệ thống đóng gói. Cân và đóng gói bằng hệ thống bán tự động, khối lượng tịnh mỗi bao là 50kg hoặc 20kg tùy theo yêu cầu.
3.1.2.17 Xử lý bã: Bã sắn công nghệ sau quá trình trích ly có độ ẩm W= 90% được chia làm 2 phần: Một phần nhỏ (khoảng 5% khối lượng) được đưa qua bộ phận thu gom bên ngoài để đóng bao và bán cho công ty sản xuất thức ăn gia súc Tân Lợi. Một phần (95% khối lượng) được băng chuyền đưa vào máy ép cấp 1 và máy ép cấp 2 có kích thước lỗ nhỏ hơn để loại bớt nước và giảm độ ẩm xuống còn khoảng 65%-70%. Sau khi đạt đến độ ẩm 65%-70%, bã được băng tải đưa vào thiết bị sấy thùng quay. Quá trình sấy bã thì bã sẽ tiếp xúc trực tiếp với không khí nóng. Ở đây, bã sắn được cấp nhiệt vừa đủ để giảm độ ẩm của bã một cách chậm rãi nhằm tránh hiện tượng hồ hoá bã (bã sắn bị vón cục) nhiệt độ lò đốt ở đây là trên 400ºC tùy vào lượng bã cấp vào, nhờ hệ thống cánh xoắn trong trống quay mà bã vừa được đánh tơi vừa giúp bã di chuyển. Bã từ trống quay ra theo 2 đường, nếu bã có kích thước nhỏ, nhẹ được hút vào bộ phận cyclone làm mất động năng và xuống máy đánh tơi, nếu bã có kích thước to hơn và nặng hơn thì rơi xuống máy gom đi qua sàng để loại bỏ sạn to, bã dính cục và xuống máy đánh tơi, tiếp theo bã được vít tải đưa vào máy vung và qua hệ thống sấy khí động lần 1 có nhiệt độ của lò đốt là 220-240OC, bã cùng không khí nóng di chuyển theo ống nhờ quạt hút và được cyclone thu gom lại còn không khí nóng thì quạt hút ra ngoài. Bã xuống máy gom và đưa sang hệ thống sấy khí động 2 có nhiệt độ lò đốt là 200-220ºC, máy vung bã lên và bã cùng với không khí nóng di chuyển theo đường ống, bã nặng hơn nên gặp hệ thống cyclone sẽ rơi xuống còn không khí được quạt hút ra ngoài. Bã tiếp tục di chuyển theo đường ống để làm nguội và được cyclone thu lại còn không khí nóng nhờ có quạt hút không khí ra ngoài. Sau đó bã được đưa đi đóng bao để bán cho đơn vị có nhu cầu thu mua. Khi hết bã trong trống sấy thì hạ nhiệt độ lò đơn điều chỉnh để bã đi ra hết trống, không dính vào thành trống và chạy quạt trống làm nguội dưới 50ºC và dừng trống. Đồng thời điều chỉnh nhiệt độ trong 2 hệ thống sấy khí động bằng hệ thống van quạt cấp gas và cửa chính gió để hết lượng bã trong đường ống sấy và độ ẩm bã thành phẩm đạt yêu cầu.