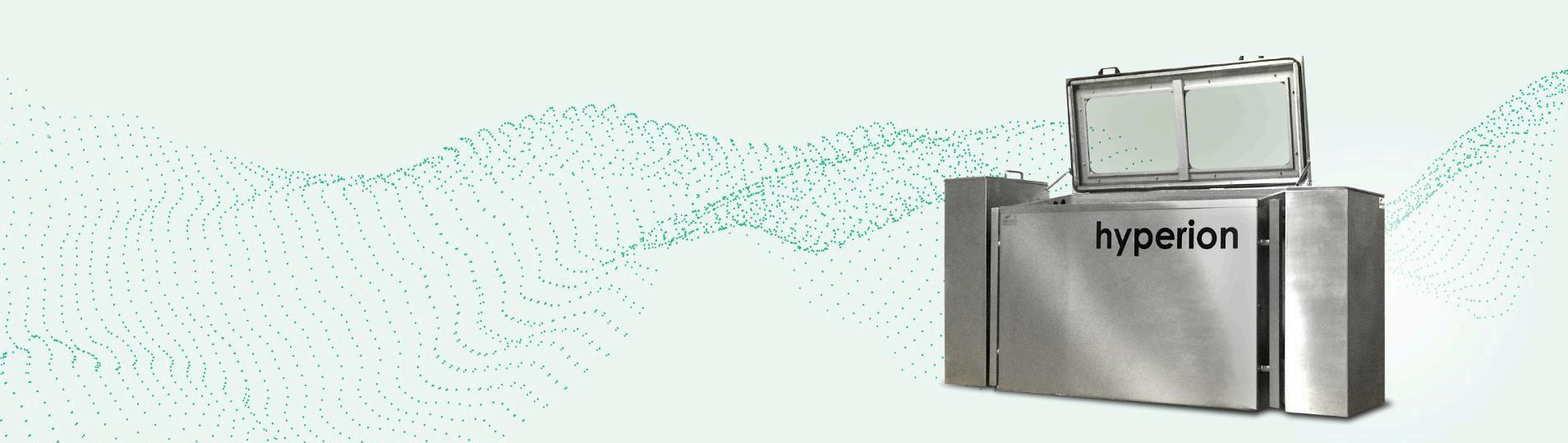
12 minute read
Hyperion à l’état de l’art de l’immersion dans le datacenter
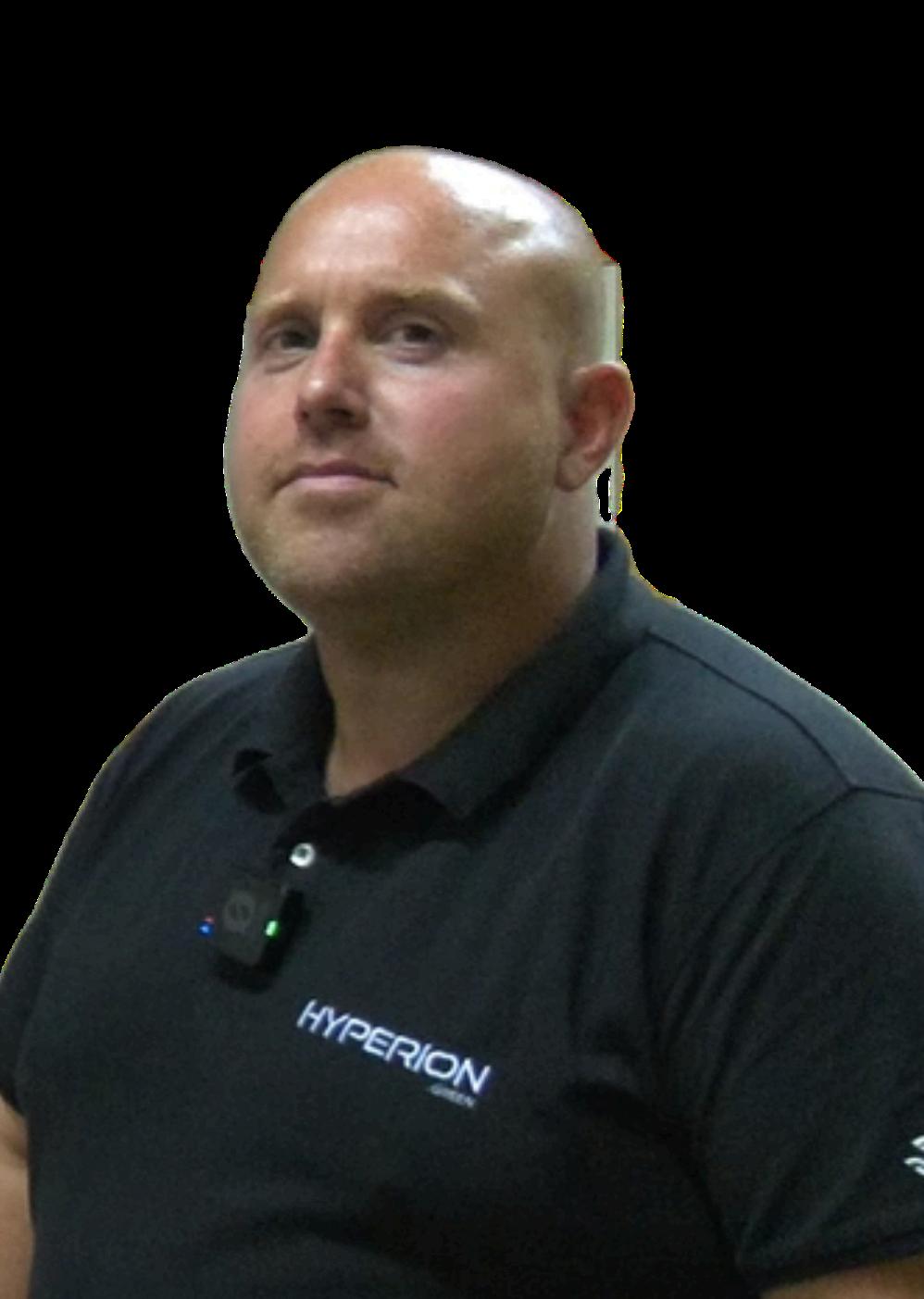
Nicolas Boulinguiez, fondateur et dirigeant du groupe Numains (MCT, Delta, Hyperion), crée et intègre des équipements pour lʼimmersion des datacenters, sous la marque Hyperion. Et il sʼapprête en 2025 à ouvrir son propre datacenter également en immersion. DataCenter Magazine lʼa rencontré pour évoquer son attrait pour lʼimmersion et ses projets.
Datacenter Magazine - Pourquoi un tel investissement dans lʼimmersion ?
Nicolas Boulinguiez - Nous avons créé une activité dédiée à l'industrie du datacenter, pour un data center et un numérique plus responsable, qui s'appelle Hyperion. Et qui est dédiée aux solutions de liquide cooling en immersion, avec une technologie de fluides diélectrique afin de minimiser l'impact des datacenters dans le monde qui nous entoure. C'est à notre avis dʼune importance majeure que de minimiser nos impacts pour accompagner un numérique plus durable et plus responsable pour les années qui viennent.
Pour nous, l'immersion, c'est un aboutissement de la maîtrise de l'impact énergétique des datacenter. On a toujours eu dans notre ADN de minimiser notre empreinte sur les consommations énergétiques, dans toutes les salles qu'on a construites, dans toutes celles qu'on a exploitées depuis toutes ces années. Et l'aboutissement de ce projet, qui va démarrer fin 2025, cʼest de dédier un data center à l'immersion, qui va se positionner pour aller accompagner un réseau de chaleur pour emmener la calorie qui va être utilisée pour faire fonctionner l'IT à destination d'un bâtiment. Pour pouvoir justement minimiser encore plus l'impact du numérique et également se servir de ce numérique pour aller réchauffer ce bâtiment.
Des opérateurs de data centers, des DSI, des techniciens sont attirés par cette technologie, mais ont encore peur de faire la bascule, dʼutiliser des outils qui sont dans de l'huile. Que leur répondez-vous ?
Ils appréhendent surtout. Le mieux, c'est de venir nous voir pour pouvoir mettre les mains dedans, pour voir que ça ne sent pas les hydrocarbures, que c'est une machine qui va parfaitement s'intégrer dans un environnement de data center qui est pensé pour être exploité. C'est d'abord notre métier que d'exploiter des salles et de l'IT en salle. On l'a vraiment pensé de cette manière là, pour que ça puisse se faire en grand nombre avec notre vision qui est celle de l'immersion en mode filière, avec nos partenaires industriels. Donc venez nous visiter, nous rencontrer en Mayenne pour qu'on vienne vous présenter et vous expliquer tout ça.
Ajoutons quʼil y a aussi le service, qui est indispensable aujourd'hui.
Oui, c'est très juste. Nous sommes d'abord une entreprise de service et la partie immersion est une brique par rapport aux autres services qui sont les nôtres et une des forces qui sont les nôtres. En plus de la maîtrise industrielle, de la technologie et de la fabrication des cuves et de toute l'intégration bâtimentaire avec nos partenaires, c'est également la capacité à accompagner les DSI, de les migrer d'environnement air cooling en immersion cooling, soit dans du rétrofit de datacenter, soit de l'intégration sur des collectivités comme on a pu le faire récemment pour une collectivité qui a souhaité se rééquiper on-premise chez elle avec des cuves en immersion, parce qu'elle voulait minimiser son empreinte énergétique dans ses locaux.
Nous sommes sur une filière française, avec des fabricants français, et des personnes qui participent à la conception française de ce produit.
Nous sommes sur une chaîne de valeur intégrée, effectivement, avec des partenaires français de premier choix. La SERAP est un spécialiste des cuves en inox depuis des générations. Motul est un fabricant de fluides français avec lequel on a travaillé des recettes spécifiques pour être au top en termes de récupération énergétique, d'effet sur les mains et sur les équipements pour pouvoir traiter convenablement cette appréhension pour les techniciens. Et enfin Wilo qui nous a également accompagné et qui est à nos côtés sur la partie circulation des fluides. Pour maximiser la récupération de chaleur et la dissipation calorifique.
Notre reportage se déplace dans le Lab d’Hyperion, où Nicolas Boulinguez nous présente les premiers bacs à immersion développés par la société, et un bac en cours d'intégration et de test pour un client.
Parlons de votre premier projet en immersion, la maquette en quelque sorte.
Le tout premier prototype est un usage détourné d'une cuve à fromage à l'origine, sur laquelle nous avons réalisé les premiers tests en labo qui nous ont permis de concevoir effectivement la technologie qui est maintenant sur le marché. La cuve était déjà en inox, pour une vision de durabilité et de machine industrielle à intégrer dans des environnements industriels.
Qu'est ce que cette maquette vous a appris?
Elle nous a appris que cela nous permettait en l'état de récupérer de la calorie, mais qu'on pouvait optimiser notre méthodologie de récupération de chaleur en mettant en place un système de convection en plus du système de circulation en paroi. Également que le mode de récupération de calories est réellement nécessaire et qu'il fallait plus réfléchir en mettant un groupe froid pour intégrer du froid, mais qu'il fallait d'abord extraire les calories et la chaleur pour en faire un usage tierce et être dans une vision de l'économie circulaire. Le bac à double paroi offre une isolation double peau qui permet de traiter le syndrome de la porte du four qui nʼest pas chaude. L'intégralité de la calorie doit rester dans la cuve et ne pas se diffuser dans le datacenter. La chaleur reste dedans avant dʼêtre extraite avec le système de circulation.
C'est dans ce Lab Hyperion que vous avez expérimenté vos technologies en immersion jusquʼau produit fini devant nous.
Exactement. Le Lab a été notre première intégration dans un bâtiment dédié à cela, avec la partie pilotage et automatismes qui se trouve derrière la gestion hydraulique, et l'intégration bâtimentaire avec la tuyauterie blanche qui est le modèle dédié pour nous à l'extraction de chaleur sans revalorisation. La tuyauterie noire avec le ballon tampon permet d'utiliser la calorie extraite de la chaleur numérique de manière à pouvoir la revaloriser à son maximum. La partie noire vient alimenter tout le bâtiment. Cette installation nous permet de revaloriser le déchet qu'est l'énergie électrique qui est consommée pour faire fonctionner l'IT. Vous avez le système de portique qui était pour nous une égoutter les machines et gérer le trop plein quand on fait des mouvements. En termes d'entrées et sorties de matériel, il est une évidence que le trop plein de fluide doit être géré. Cela fait partie des choses que l'on a rajouté à la cuve proto.
Vous avez également développé tout ce qui permet de piloter l'installation.
Nous avons deux circuits : un circuit primaire pour la circulation des fluides, sur lequel on a travaillé avec un partenaire industriel ; et le circuit secondaire qui est juste la partie système hydraulique d'eau pour lequel on doit pouvoir piloter les variations des circulateurs pour aller optimiser la récupération, ouvrir, fermer des vannes pour pouvoir extraire plus ou moins en fonction de la puissance IT qui est intégré dans les cuves. Nous avons fait le choix de l'esthétique rudimentaire et industrielle. Ce nʼest pas quelque chose où lʼon met du clinquant avec
Pour concevoir ce bac à immersion, vous avez activé la filière locale.
Sur la partie marché de l'immersion, on travaille en mode filière avec plusieurs partenaires industriels. Concernant les fluides diélectriques pour faire fonctionner les équipements, nous avons un partenaire industriel français de premier choix, Motul. Notre second partenaire est Wilo pour des circulateurs que l'on a intégrés et qui nous a permis de doubler le système de circulation. La partie cuve en inox est produite par une entreprise mondialement connue, la Serap, qui est dédiée au marché de l'inox et à l'étanchéité des cuves, qui est une appréhension forte que l'on peut avoir avec nos interlocuteurs à qui lʼon explique que nous ne ne sommes pas un chaudronnier. Notre vision de la filière est de travailler avec des partenaires industriels de premier plan, qui nous permettent de sécuriser et de justifier la qualité et le fait que les installations ne fuiront pas.
Nous poursuivons notre échange avec Nicolas Boulinguez sur le lieu d’implantation du futur data center d’Hyperion, où un système en immersion est déjà en production.
Ce site est celui de notre projet de data center full en immersion au sein de l'agglomération de Laval, pour lequel on a démarré la mise en production du bac.
On constate que c'est finalement assez facile à installer...
C'est l'idée, en fait. A la différence des racks que vous pouvez connaître, des racks en air qui peuvent être montés sur site, là on amène des cuves sur le site de destination intégralement déjà étanches et sur roulettes.
Nous avons travaillé sur des cuves qui sont en largeur 80, facilement transportables, qui permettent de s'installer à peu près n'importe où à partir du moment où on a simplement la partie récupération de chaleur sur le circuit secondaire au niveau de l'hydraulique.
Justement, parlons des fluides. Vous travaillez en particulier avec Motul. Est ce que la sélection du fluide a posé un problème et comment vous en êtes arrivés à travailler avec eux ?
La sélection du fluide n'est pas un problème, c'est la solution. À la différence de l'air, qui est un isolant, le fluide est un conducteur. Donc pour nous, c'était un élément majeur que l'on devait être capable de maîtriser en termes de risque. Notamment pour les techniciens qui interviennent, par les parties du toucher et olfactives, et par l'appréhension car c'est vraiment un changement de métier que d'avoir des équipements IT qui sont en immersion. Donc, nous avons travaillé un certain nombre de fluides différents, plusieurs recettes de fluides qui ont été faites et validées avec Motul, qui est l'entreprise de choix pour accompagner notre stratégie de filière française de technologie, de fluides et d'immersion. Ici, nous sommes sur un fluide qui en plus a une empreinte spécifique, notamment sur le fait que le fluide qui reste sur les doigts y reste très peu longtemps. Aujourd'hui, vous avez d'autres fluides du marché, qui sont également des fluides diélectriques, mais qui restent très longtemps sur les mains. Le nôtre y reste très peu, dès qu'on s'essuie les mains, ça s'en va immédiatement.
C'est étonnant, je m'attendais à ce que vous nous parliez des capacités conductrices, de la chaleur, etc. Mais en fait, le vrai problème c'est l'acceptation par les équipes.
Tous les fluides diélectriques ont une capacité de récupération calorifique qui est à peu près la même, à plus ou moins quelques pour cent. Nous avons fait des tests avec le pôle Cristal, qui est le laboratoire avec lequel on travaille à Dinan. Sur différents types de fluides, ça se joue à un ou 2 %, ce n'est pas représentatif. Le vrai enjeu, effectivement, c'est l'acceptation de ce que ça fait pour les équipes techniques de mettre les mains dans un fluide. C'est en fait le choix qui a été le nôtre, de nʼimmerger aucune des connectiques. Il nʼy a uniquement que la partie compute calcul et chipset qui est en immersion. Toute la partie connecteur est vraiment au-dessus du fluide de manière à ce que ça permette l'acceptation pour les équipes techniques, de ne pas mettre les mains dans un fluide en fait.
Pour la partie connectique, qui a été placée à l'arrière, nous avons redondé l'intégralité de la chaîne, que ce soit la partie LAN, la partie électrique, la partie hydraulique, justement pour être capable de pouvoir changer des équipements en mode production. L'enjeu majeur de la dernière version de notre bac, ce sont les travaux qu'on a fait au niveau des circulateurs par rapport à la pompe initiale. Nous avons désormais deux circulateurs qui nous permettent de gérer avec une variation la nécessité d'évacuation de la calorie ou de récupération selon comment on se positionne dans la chaîne primaire ou secondaire. Et avec un système de pilotage en mode bus qui nous permet de remonter dans l'intégralité des tableaux de contrôle et de pilotage de la cuve elle-même. Il faut savoir que dans le choix que l'on a fait dans nos installations, chaque cuve est indépendante. On ne mélange pas les fluides d'une cuve à une autre pour des raisons diverses, notamment dans nos choix de maintenance. Nous faisons de manière annuelle un prélèvement sur le fluide pour être sûr qu'il garde toutes ses facultés et qu'il n'y a pas une hygrométrie trop forte au niveau du fluide.
Le circuit secondaire est du même acabit d'un point de vue pilotage, on a mis également des circulateurs. Wilo est capable de gérer au plus fin la partie gestion de la calorie et récupération de la chaleur fatale en termes de variation, de données et de métriques. Tout est intégré sur la cuve, avec la partie pompe. Dans une installation sur laquelle on enchaîne les cuves, on supprime le placard technique, et on traite toute la partie pompage et échangeur dans un local qui est dédié. En termes de gains, c'est une vraie question parce que c'est un des enjeux majeurs. Aujourd'hui, on baisse de 40 % la consommation énergétique parce qu'on n'a pas du tout besoin de climatisation. Et surtout on récupère aujourd'hui plus de 90 % de la chaleur fatale que lʼon convertit à plus de 90 % en l'électricité pour des usages X ou Y, soit en eau chaude sanitaire, soit en chauffage de bâtiment ou en apport calorifique sur une piscine.
Retrouvez l’intégralité des interviews de Nicolas Boulinguiez d’Hyperion sur notre chaine YouTube.