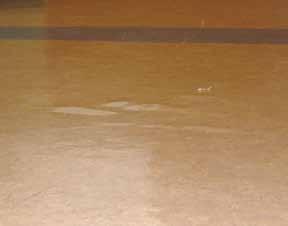
7 minute read
Case Study: Blistering in Linoleum Flooring Installed Over a Concrete Slab-On-Grade
CASE STUDY:
By Stephen Hunter, P.Tech. (Eng.), FSFE
Introduction
This case study is about a failure involving blistering in linoleum sheet flooring installed over a concrete slabon-grade in a school constructed on the Canadian prairies. (Photograph 1). It includes a summary of the investigation methodology and observations. There is also a discussion on why the failure occurred and what could have been done to prevent it.
Methodology
This investigation started with a conversation to understand the issues. We then reviewed the design and construction documents. This was followed by a visit to the school to review the issues first-hand.
During our site visit, the moisture content of the floor assembly was recorded in several locations – both
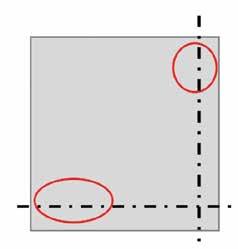
Photograph 1: Typical blistering in the linoleum sheet flooring. Figure 1: Approximate building footprint with the service ducts indicated by dashed lines. The locations of blistering are indicated by red circles.
where the blistering was occurring and where it was not.
At some blister locations, the linoleum flooring was cut and removed to examine it and the underlying assembly. To better understand the composition of the concrete slab-on-grade floor assembly as a whole, core samples were taken at several locations.
Observations
The floor assembly was illustrated in the drawings as follows (from top to bottom): • Linoleum sheet flooring • 100 millimetre concrete slab
• 6 mil polyethylene sheet layer • 150 millimetre granular fill The floor was slightly above grade and was bordered on the building perimeter by concrete foundation walls with strip footings. The foundation walls extended approximately 1.5 metres below grade. The foundation wall assembly was illustrated in the drawings as follows (from exterior to interior): • 13 millimetre concrete facing above grade • 50 millimetre extruded polystyrene insulation panels • 200 millimetre concrete
No membrane was shown in the drawings between the foundation walls and either the above grade walls or slabon-grade. No drainage tile was shown in the drawings. During our document review we also learned that two concrete service ducts were present on the site prior to construction.
Both service ducts extended through the building footprint. One duct ran north/south and the other ran east/west (Figure 1). The service ducts measured approximately two metres wide by one metre high. During construction, the concrete service ducts were abandoned and filled with soil. They were not blocked or sealedoff where they entered the building footprint. At each duct location, the full height foundation wall was interrupted and a 0.6 metre high grade beam was

Left: Photograph 2: Large blister with a saturated moisture content.
Right: Figure 2: Exterior view of the as-built condition of the building enclosure at grade.
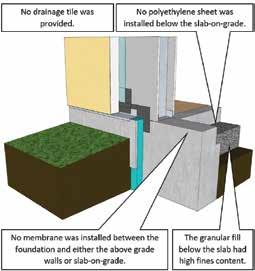
provided. This created oversized openings for the service ducts to extend through the foundation walls.
During our site visit, we observed that the blistering was occurring mainly above the service ducts and near the building perimeter (Figure 1).
The moisture content near the surface of the floor assembly was consistently higher where the blistering was occurring (Photograph 2).
Where the linoleum flooring was cut and removed at blisters, it was apparent that it had failed adhesively and cohesively (Photograph 3). Mould was starting to develop within the flooring.
While taking the core samples, it was determined that a polyethylene sheet layer was not present below the concrete slab-on-grade (Photograph 4). The material taken from below the slab-on-grade in the core locations was a granular fill. It had a high fines content. That is, it had a lot of small particles that filled the voids between the larger gravel particles. It was assumed that no membrane was installed between the foundation walls and either the above grade walls or slab-on-grade, as one was not shown in the drawings and no polyethylene sheet layer was provided below the slab-ongrade. It was also assumed that no drainage tile was provided, as none was shown in the drawings and there was no record of it being installed during construction. Figures 2 and 3 illustrate the as-built condition of the building enclosure at grade, and the key observations made during our investigation. Discussion
In this type of assembly, the polyethylene sheet layer under the concrete slab-on-grade acts as a vapour barrier and capillary break. The granular material under the polyethylene sheet layer also acts as a capillary break and drainage layer; however, it only performs these functions effectively if it’s composed of coarse gravel with minimal fines. Granular fill with high fines content has small pores. As a consequence, liquid water migrates through the granular fill layer via capillary suction. It is also retained.
Without the polyethylene sheet layer above the granular fill, water can
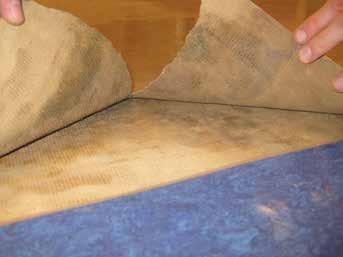
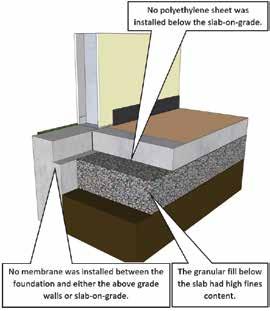
Left: Photograph 3: Wet linoleum flooring that failed cohesively.
Right: Figure 3: Interior view of the as-built condition of the building enclosure at grade.
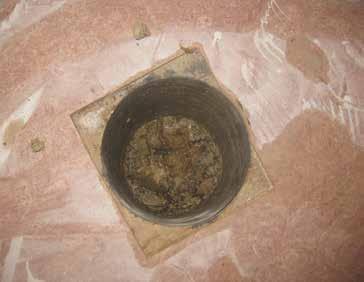
Left: Photograph 4: Typical core sample.
Right: Figure 4: Exterior view of the improved condition of the building enclosure at grade.

migrate into and through the concrete slab above, mainly by capillary suction.
Similarly, without a membrane to provide a capillary break between the foundation walls and slab-on-grade, water can also migrate from the soil, through the foundation walls, and into the slab-on-grade.
The linoleum sheet flooring has relatively low permeability to vapour and liquid water. As such, water migrating to the interior of the building from below the slab-on-grade accumulates between the flooring and concrete.
When concrete is wetted, an alkaline solution is created with a pH up to 12 to 13 (Photograph 5).
Water-based flooring adhesives are often sensitive to highly alkaline solutions. The alkaline solution created under and within the linoleum sheet flooring appeared to be causing the adhesive to fail. This adhesive breakdown, combined with the pressure associated with evaporating water at the underside of the flooring, ultimately caused the blistering.
The presence of water and a nutrient source led to conditions suitable for mould growth.
Of course, all of this requires a source of water below the slab.
It’s telling that the blistering was concentrated at the building perimeter
Left: Photograph 5: An alkaline solution is created at the wet concrete surface. Right: Figure 5: Interior view of the improved condition of the building enclosure at grade.
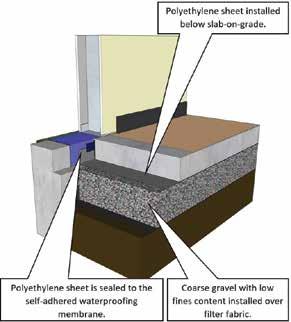
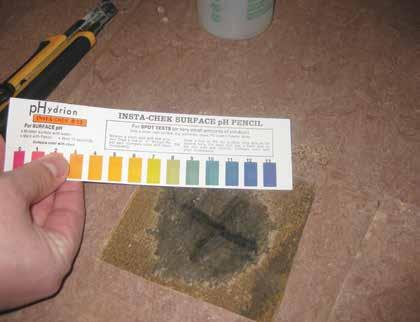
and above the concrete service ducts.
As noted, shallow grade beams were provided at these locations, resulting in openings in the foundation walls near grade.
It’s likely that water from precipitation was entering the building footprint at the openings provided for the service ducts. The ducts themselves may have also been conveying water below the building.
Perimeter drainage tile at grade beam depth would have reduced the amount of water retained in the soil, and thus would have reduced the amount of water entering the building footprint at these locations.
It’s worth noting that moisture from casting the concrete didn't seem to be causing the issues. One would expect the issues to be more uniform if the flooring were installed over concrete with a high moisture content.
It’s also interesting that there were no issues reported in the southeast corner of the building where two service ducts penetrated the foundation. This area had permeable carpet flooring, and consequently, the water was not entrapped.
Prevention
A few simple measures implemented during design and construction could have prevented this failure from occurring, as illustrated in Figures 4 and 5.
There should have been a continuous capillary break to separate the abovegrade assemblies from the soil. A polyethylene sheet layer and coarse gravel with minimal fines would have served this function below the slab-ongrade. This would have prevented water from migrating to and through the floor assembly. Depending on structural requirements, the coarse gravel may be placed over a layer of compacted granular fill with higher fines content. Filter fabric can be placed below the coarse drainage gravel to separate it from the soil or granular fill below, and minimize the risk of it becoming clogged with fines.
In the assembly illustrated in Figures 4 and 5, a self-adhered waterproofing membrane is applied over the top of the foundation wall to provide a capillary break between it and the adjacent slabon-grade and above-grade wall. If these (or similar) measures were implemented at this building, the blistering likely would not have occurred.
Ideally, the out-of-service ducts would have also been removed, at least at the foundation walls. This would have permitted the foundation walls to be continuous, and would have reduced the amount of water entering the building footprint. At this site, the improved building enclosure would perform well without perimeter drainage tile. The need for drainage tile should be determined based on project specific conditions. n
Calgary 403.571.4080 | Edmonton 780.453.6682 | www.cascadeaqua.com