
11 minute read
Technical Challenges of Passive House Certification and Why the Standard is Here to Stay
By Peter Dushenski and Veronica Johnson
Above: Cambridge Lofts Penthouse. Right: Vancouver House Bjarke Ingels.
What is Passive House?
Passive House is a German-based standard that ensures high-performance building envelopes with the broad mandate of reducing energy loss through the building envelope by 90 per cent. Although the international Passive House Institute (PHI) is based in Germany, it actually has Canadian roots. Following the Oil Crisis of the early 1970s, The Saskatchewan Conservation House (SCH) laid the groundwork for the Passive House Standard as we know it today! Funded and built as a government research project, this early prototype didn’t have many windows and wasn’t what we might call “classically beautiful,” but it was incredibly effective at reducing operational energy demands. Of course, with 1970s glazing technology, it was easier to keep the building warm by reducing glazed area overall. However, given the productivity and mental health benefits of larger windows that have since then been well demonstrated, particularly with the recent global pandemic, with the benefit of hindsight we can now see that SCH made tradeoffs in the name of efficiency that didn’t translate into occupant well-being. So is there a way to have our cake and eat it too? Can we create a Passive House project that’s efficient, beautiful, and enjoyable to inhabit?
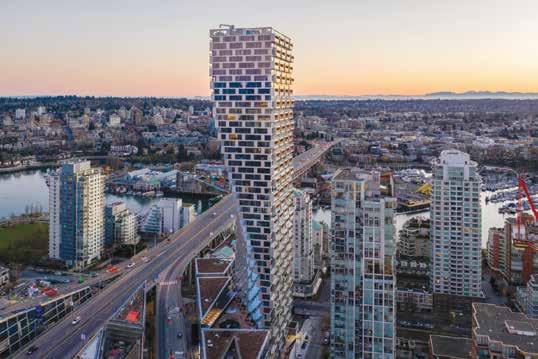
Cambridge Lofts Penthouse
In 2011, an Alberta-based curtain wall manufacturer rose to the challenge of building an entirely passively ventilated single-family residence with curtain wall on all four sides. Replacing a mechanical shed on the 19th floor of a former office building turned condominium in downtown Edmonton, this humble box was transformed by a team of talented architects at Reimagine (formerly Manasc Isaac) into a stunning two-bedroom penthouse in the sky. All of the corrugated steel from the mechanical shed was replaced with fibreglass-framed triple-glazed curtain wall, to incredible effect. Today, over a decade later, the penthouse is still occupied and very much enjoyed, remaining entirely comfortable down to -20 degrees Celcius with just the radiant heat from the floors below. Below such temperatures, as happens in Edmonton, there are a couple of fireplaces that have been installed.
Certifying to the Passive House standard
The curtain wall manufacturer officially
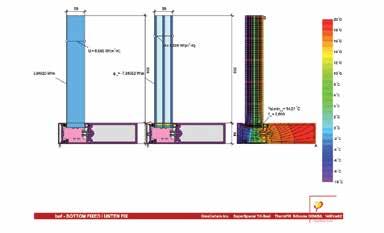

launched at Greenbuild in Philadelphia in 2013, and since then has become the North American leader in curtain wall thermal performance. As such, certifying to the up-and-coming Passive House Institute (PHI) Standard seemed like a logical move, perhaps even a straightforward one. So in 2017, the company submitted their designs and models to PHI for review, hoping to achieve at least Cool Temperate Climate certification (0.8 W/m2K overall system). Turns out, the German Passive House standard was much more difficult to achieve than anticipated!
The conventional manner of improving overall curtain wall performance is to increase the centre-of-glass performance, but Passive House closes this convenient loophole by limiting the centre-of-glass performance in Cool-Temperate Climates to 0.70 W/ m2K and to 0.52 W/m2K in Cold Climates, putting greater emphasis on framing and glass edge performance. Given the triple-glazed fibreglassframed curtain wall’s performance on the Edmonton penthouse, the curtain wall manufacturer expected its standard system to meet at least Cool-Temperate climate requirements right out of the box, ie. 0.80 W/m2K overall. Modelling
780-994-9084 info@glascurtain.ca PO Box 67198 Meadowlark Park, Edmonton, AB, T5R 5Y3


Passive House Tower Cornell. Saskatchewan Conservation House.

their system with the limited glazing, however, yielded an overall system U-value of only 0.93 Watts W/m2K, nearly 15 per cent shy of the CoolTemperate target. To call this result disappointing would be an understatement, particularly given that several European curtain wall manufacturers had managed the feat of Cool-Temperate PHI certification using highly conductive aluminiumframed systems to achieve their ends. Given the vastly superior thermal properties of fibreglass (200 times less conductive than aluminium), how could the up-start Canadian manufacturer be so far off the mark? Needless to say this early result was a wake-up call to the strict standard by the Passive House Institute with regards to thermal bridging and air-tightness. It is quite simply on another level from any other standard or certification programme in North America. Not that the Canadian company was about to shy away from the challenge, quite the opposite. Now was the time for its design engineers to roll up their sleeves and show the world that Canada can still build world-class products leveraging domestic manufacturing capabilities. But where to start? Clearly the fibreglass itself wasn’t the issue, so it became only too apparent that the other components of the curtain wall system were in need of improvement. So back to the drawing board for new nosing designs, gaskets, screws, and cavity insulation! With this comprehensive redesign underway, this also presented the Canadian manufacturer with an opportunity to review and rethink its standard framing system, then based on a design already 10 years old. Thus began the research and development of the company’s V2.0 systems that would not only have the rigorous Passive House Standard in mind, but also nearly a decade of project experience across some of the most demanding climates and environments in the world. The resulting systems would be able to achieve Cool-Temperate certification with a stretch goal of Cold Climate certification, becoming the first system in the world to achieve the demanding Cold Climate level.
Focusing on the new Passive House certified system, the Canadian design engineers, with technical assistance from building envelope consultants at RDH Vancouver, as well as financial support of Alberta Innovates, set about sourcing and modelling a variety of different components to selectively isolate and eliminate thermal bridging in this new curtain wall framing system. Leaving no stone unturned, this new system would use a recessed screw chase, stainless steel screws, advanced gaskets with additional air pockets, and custom extruded EPS insulation in the nosing cavity. Combined with the incredible thermal performance of fibreglass, this new framing system turned out to be so highly insulating that it was no longer in the curtain wall manufacturer’s direct scope to limit the most significant thermal bridging remaining, namely because now the glass edge spacers were the primary thermal bridge. Indeed, for the first time in curtain wall history, the framing system was not the primary thermal bridge in the overall system, it was the insulating glass unit (IGU). Not that selecting and sourcing the required glass was exactly straightforward either. Many ultrahigh-performance glass units, such as vacuum-insulated glass (VIG), have very conductive edge seals that preclude their use in this specific application. So after running a variety of different simulations and talking to some of the top IGU suppliers from around the world, it was determined that larger air spaces between the three lites would be required – 19 millimetre argon-filled spaces instead of the more conventional 13 millimetre spaces – and that a special secondary glass edge seal would also be necessary to meet the stringent PHI thermal performance targets. With supplier letters in-hand, the Canadian curtain wall manufacturer was able to demonstrate - to the Passive House Institute’s satisfaction - not only the technical possibility of this groundbreaking new curtain wall system but also its commercial availability. With IGUs secured and significantly upgraded fibreglass framing ready, the finalized system was certified to PHI Cold Climate criteria in 2019, becoming the first curtain wall system in the world to accomplish this and the first manufactured in North America to certify to any PHI level. With an overall system U-value of
0.6 W/m2K (including frame and glass), the newest Canadian fibreglass curtain wall system also achieved a best-in-class phA+ passive house efficiency class for airtightness and comfort.
Why certify?
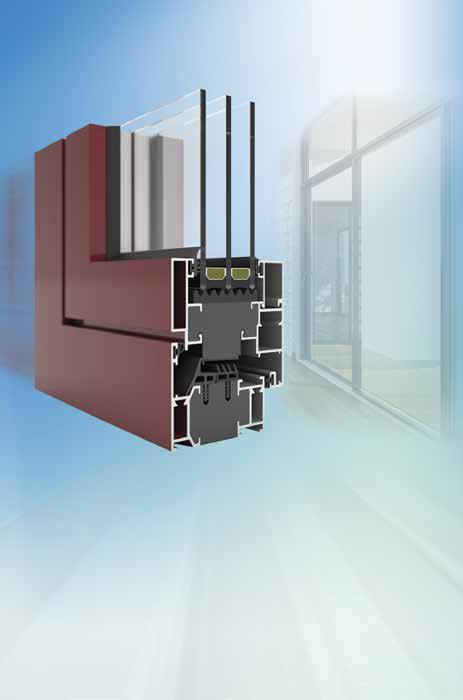
The Passive House Institute (PHI) in Darmstadt, Germany distinctly certifies two different categories: products and projects. Products are building envelope components that are certified by PHI to provide third-party verification that manufacturer performance claims are accurate and legitimate. For architects, engineers, and specifiers, this verification greatly simplifies product selection during the design process. Designing a PHI certified project can be a very difficult task to begin with. Reducing whole-building energy consumption up to 90 per cent while still making it beautiful, functional, and meeting all building code requirements is an enormous undertaking. Simplifying product selection for these ultra-highperformance projects is therefore facilitated by the Passive House Component Database, which contains many of the world’s highest thermally performing building envelope products as certified by PHI. With this tool in-hand, the availability of PHI certified products essentially fast tracks incorporation of compliant systems into project designs seeking certification. Completed projects are then certified by PHI to provide further quality assurance by verifying correct installation of the approved products, particularly as it pertains to air-tightness and energy use. Projects aren’t strictly required to have all products be certified, but it’s typically the case that the vast majority of products are. At the very least, product certification dramatically improves awareness and increases visibility for compliant manufacturers. The level of design and engineering required to obtain PHI product certification is the most demanding in the world, which very much sorts the wheat from the chaff in an industry where manufacturer claims unfortunately fail to hold up in the field more often than any of us would like.
Passive House isn’t perfect…
Although the Passive House Standard has been incredible for sparking innovation and encouraging much better building envelope construction, like all things, it isn’t perfect. To take just one example, the Standard does not currently consider the embodied environmental impact of certified products, which is something that Canada Green Building Council (CaGBC) has been doing since the introduction of LEED v4 in 2017.
This is of particular concern because Passive House buildings are so well-
Azon Saves Energy
Azo-Core™ thermal barrier
The Azo-Core™ ultra-low conductance high-density polyurethane foam is engineered to allow aluminum fenestration manufacturers worldwide to achieve the highest standards in energy efficiency, strength and durability. Contact us to learn about the newest Azon thermal barriers used in energy conservation.
* Product featured: Eurotermic Plus Series Grupo Ayuso | Madrid
1-800-788-5942 • azonintl.com
insulated and all those additional building materials have to come from somewhere. As such, Passive House buildings typically have higher embodied carbon and higher overall embodied environmental impacts relative to conventional buildings. As with electric cars, this delta may or may not be made up for by operational gains over the lifecycle of the building, depending on carbon and environmental impacts of the grid where the building is located, as well as how long the building is left standing before it’s knocked down or otherwise rendered unfit for service.
It’s important to remember just because we’re designing buildings that consume less energy in operation, it doesn’t necessarily mean these buildings will require less energy to manufacture, or even that they’ll have a net-reduction in environmental impact over the building’s lifecycle. Also, front-loading the environmental impact of a building during the manufacturing process does little to meet aggressive global emissions targets. We only have one planet, after all, and the emissions have to go somewhere, particularly in buildings where so many components are imported from overseas, whether from Europe or Asia.
Speaking of imported products, global supply chain challenges will not be news to many of us in 2022, but do you know how many imported products are used in a typical Passive House project? A lot! For example, at the time of this writing there’s currently not a single PHI certified commercial door manufacturer in North America, so all Passive House doors come from overseas. We can only hope that improved product availability is around the corner for the North American market because reliance on imported products might have some cachet (if from Europe) or some costeffectiveness (if from Asia), but it doesn’t take a huge external shock to derail our best intentions. The world seems to be getting more crazy and unpredictable with every passing year, so it can put us in a fragile position to hinge the success of our projects on these niche imported products. Of course, at the moment there isn’t always an alternative, but it shows just how much more buy-in is needed from North American manufacturers if the Passive House Standard is going to succeed here long-term. Another less invisible trade-off from focusing so narrowly on operational energy performance is building aesthetics. Of course energy matters, but so does beauty. After all, the most sustainable building in the world isn’t the most efficient one, it’s the most beautiful one… because the beautiful building is the most likely to be preserved and maintained for generations to come. Typical Passive House buildings are many things but they’re not always that beautiful. Too often they’re more like bunkers and less like the creative buildings designed by Bjarke.
Bringing it all together
All of that being said, Passive House is still the gold standard in the industry. It’s incredibly demanding for manufacturers and designers, and if nothing else is a world-class benchmark for thermal performance and air-tightness of building envelopes. It’s probably not a silver bullet to solve our environmental concerns, but it does an outstanding job of independently validating the best building products in the industry and separating them from the merely adequate. In an age of increasing uncertainty where resilience has more and more appeal for clients, we can expect to see growing demand for Passive House certified projects across North America and beyond. It’s time for all of us, especially manufacturers, to plan accordingly. n
With over 15 Years’ Experience in Supply and Install of: • Vinyl Siding • Hardie Board Cement Siding • CanExel Siding • Lux Metal Cladding • Sagiper Siding • Soffit & Fascia
www.absoundexteriors.com No job is too small!
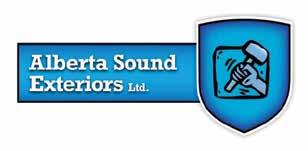