
10 minute read
Cleaning, flushing and treating hydronic systems
By Roy Collver
Although not an expert in this topic, I have been observing over the years what seems to work and what doesn’t. I have listened to many “experts” and I think I have a pretty good handle on it. Cleaning out and treating a hydronic system is an important, but often forgotten, step in protecting system components and maximizing efficiency. The two different reasons to perform these procedures each require a slightly different approach.
New systems:
When a new system is installed, it should be flushed to remove any debris, solder flux, pipe dope, oil, etc. This step should never be skipped, and the stories are many when it comes to the kind of stuff found in some brand-new systems. I personally have dug twigs and leaves out of a “Y” strainer, wood splinters out of pump impellers, and once – a glass marble out of an air separator. I have seen strange gel plugging a basket strainer, and dealt with noisy boilers due to oil and grease coating water-side heat exchanger surfaces – all in brand-new systems.
If an installer has taken reasonable precautions to be sure there are no big
Sammy Tong
Western Region Sales Manager
Mississauga Offi ce
Tel: 866-805-7089
Sparks, NV 800-987-9042 chunks in the new piping and to be sure that there is no solder flux or oil in there, they might lobby to get by with a clean water flush and dump of the system – don’t buy it. Get your mechanical engineer or facilities manager to specify that the installer engage with a firm that is an acknowledged local expert in hydronic fluid treatment and system cleaning. These people will assess the system and water quality, and prescribe a cleaning and treatment regime appropriate to the materials in your system and appropriate to the condition of the local water. They should be capable of ongoing testing of the system, and have a “suite” of chemicals that will be compatible with each other and not gum up the works. This all applies to new systems and retrofit situations when boilers and other major components are replaced.
Old systems:
You should also clean and flush when an older system gets fouled by sludge, rust/lime scale, algae, etc. There are all kinds of nasty things that can show up, including exhausted chemicals and glycol that has “gone bad” (usually faded down into an acidic state – very hazardous to your system). Part of a regular maintenance check should be to drain fluid samples and check pH and chemical inhibitors. Should there be any chemicals in the system, you will need to know what they are; if need be, farm the job out to your supplier who will be unlikely to cause any “mix’n’match” problems. Some chemical suppliers will provide you with a test kit to go along with the chemicals you buy from them so that you can do this yourself. This detail is important and should be a key decision point in deciding which chemical supplier to work with. Equally good are the suppliers that have a lab with quick turnaround, where you can send a sample for testing.
Other ways to determine if a system needs to be cleaned include draining some water from low spots in the system if any are accessible, and looking at what comes out. Depending on the materials of your system, the fluid may be coloured – and this is not always a bad sign – but there should never be any grit that comes out. I am a great believer in “Y” strainers and cartridge filters, and the newest dirt separators are brilliant. All of these devices will help capture
junk in your system, but just as crucial,
Belimo Americas
219-6279 Eagles Drive Vancouver, BC V6T 2K7 Tel: 604-221-6105 Cell: 778-772-6273 sammy.tong@ca.belimo.com www.belimo.ca

they can be the canary in the coal-mine; if the strainers or filters plug up, it’s a likely sign that you should be cleaning the system out. (Filtration is a topic worthy of an article all on its own – perhaps the upcoming spring issue of Ops Talk.)

Indicators that a system needs cleaning include:
• Noisy boilers. For fixed-fire boilers, the noise increases as the boiler heats up. With the new modulating boilers, noise will start at some mid-fire point and become louder as the burner modulates to higher firing rates.
Many high mass/high water volume boilers will not warn you however, and the first indication you might have is water on the boiler room floor from a cracked pressure vessel. • Seized or noisy pumps. Crud gets onto the bearing surfaces and in no time, it means “bye-bye” for your circulator. • Leaks. Relief valves, pump seals, piping joints, radiators, air vents – just some of the components that may spring a leak due to fouling or corrosion. • No heat or reduced heat in some loops, radiators or other heat transfer components. Junk builds up in piping or terminal units and either stops flow completely, or reduces it enough to restrict heat transfer and performance. The most common customer complaint that should trigger a
“gummed-up” system investigation is the cold radiator tale of woe. • Valves won’t close off. Zone valves, gate valves, compression valves, relief valves – any valve with a seat may suddenly fail to completely shut off when it should. There is a pretty good chance there is crud on the sea preventing positive shut-off.
The procedures for cleaning and flushing are pretty simple, and common sense should prevail: Step no. 1 – Get the supplier to assess the system. This means taking water samples, checking the system for leaks and blockages (cold loops and radiators), noting the different metals making up the system, and documenting any issues (more about metals shortly). Step no. 2 – Use the chemicals in a systematic procedure to: • Clean the crud out of the system. • Passivate the system after cleaning. • Install some kind of filtration device(s). • Refill the system and treat with appropriate chemicals. • Provide ongoing protection and monitoring/documentation after the system is refilled. Note: When replacing a boiler, it is a real “dandy” idea to clean, flush, and then put in the new boiler. Just for the record: I have never been a big fan of adding chemicals to hydronic systems – but I now consider it a necessary evil, given the nature of today’s mixed-metal systems. Multi-metals make life in the closed-loop hydronic system interesting, and can create lots of work for what I have always called “the chemical guys”. Have a look at the galvanic table of metals chart.
Corrosion of metals results from galvanic action (a reaction between two dissimilar metals). The severity and type of corrosion will vary, depending primarily on pH imbalance, oxygen in the solution, fluid conductivity and bacterial attack. Minerals in the water add confusion to the mix, and chemical additives can also become problematic.
You can see from the chart that if all of the system components are ferrous, they are not going to aggressively attack each other unless conditions are really bad, at which point they literally cannibalize themselves. We have hundreds of years of history and experience in dealing with corrosion in ferrous piping systems, and have developed a toolbox of chemicals and techniques for
reducing corrosion. In contrast, modern hydronic systems have a real “mixed bag” of materials in them. It is normal now to see copper and steel pipe, castiron, plastic pipe, rubber components, brass and bronze, stainless steel and aluminum all within a single system. The further apart the different metals are on the chart determines the likely-hood that the less “noble” metal will give up its ions to the more noble metal. The reason magnesium and aluminum are used as anodes in water heaters is that they sacrifice themselves to save the steel tank from rusting away; the same thing can happen to your aluminum boiler. Also, the various metals in the system may best respond to different conditions, especially pH, so at times we could have a conflict in how best to treat a system.
Consult with the boiler manufacturer to get their recommendation as to water quality and chemical treatment. Keep in mind that the boiler manufacturer is primarily interested in making sure their boiler is not damaged – the chemical suppliers are primarily interested in getting you to buy their chemicals. A responsible boiler manufacturer will have precise instructions as to the pH levels required and what other fluid conditions will keep their boiler happy. They should also detail the maintenance intervals for checking and adjusting additive levels so that water chemistry doesn’t wander off into the sunset. You should find that aluminum boiler manufacturers will provide the most detail, because aluminum boilers are the most sensitive to damage; the castiron/steel guys should be next, with less concern from the copper boiler people, and the stainless and stainless/titanium manufacturers are the least worried – the same order you see in the galvanic table.
Remember that cleaning chemicals are NOT designed to be left in the system. That’s where the “flush” part of “clean and flush” comes from. Again – make sure you follow the manufacturer’s instructions as to how long to circulate the chemicals, at what temperature, and how to dispose of them. Most manufacturers will have a testing procedure so that you can check to make sure all of the cleaning chemicals have been flushed out and/or neutralized.
A cautionary note – if you are dealing with an old system, or one that has been subject to serious corrosion, the clean and flush procedure may reveal and/or cause the system to spring one or more leaks. It is important to have someone monitor the system for leaks during the procedure so as to limit damage should a leak occur.
To justify my insistence that you get a true expert involved, consider the following example of aluminum boilers in a traditional system. (I am not trying to demonize aluminum boilers here, by the way; if you look at the Galvanic Table, you can see that in the right conditions, even stainless steel, in its active state, can be affected by corrosion.) Aluminum just happens to be more sensitive to galvanic corrosion due to its sensitivity to high pH and its position on the chart in relation to other common metals used in systems today. However galvanic action often occurs on the same piece of metal (even stainless steel and copper) where a corrosion cell takes up residence on a small area of the metal and creates a cathode and anode adjacent to each other – in essence, making the same piece of metal dissimilar to itself – weird. A corrosion pit will develop at these locations.
When pH wanders away from where it is supposed to be, the system “robs Peter” (the aluminum heat exchanger) to “pay Paul” (the copper pipe and steel panel radiators).
So what is this sensitivity to pH then, and where is the confusion? Here is a quick example. One of the most popular inhibited propylene glycol-based heat transfer fluids on the market, when mixed to a recommended concentration of 50/50, has a pH of 9.5 to 10.5. The aluminum boiler manufacturers I have checked with all state a maximum pH level of eight to 8.5; so just doing what we have been doing for years is obviously not going to work in the case of aluminum boilers. My understanding is that ferrous metals respond well in alkaline environments, but aluminum will go downhill fast. Aluminum is more forgiving of a slight acid environment, but ferrous components will suffer. “The chemical guys” have special inhibitors, and the knowledge necessary to safely use them. These compounds are meant to protect the various metals, and although I have always been skeptical of some of this stuff (over-enthusiastic sales people make much of it seem like hocus-pocus and mega-vitamin supplements), it is clear that many of these products can help prevent corrosion and prolong the life of your equipment. Just make sure you employ someone who knows what they are doing.
Happy hydronics! b
B.G.E. Service & Supply Ltd.
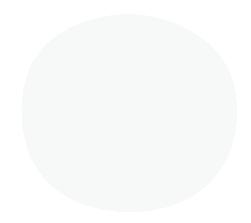
Leaders in Filtration Quality and Service
Commercial, Industrial & Residential HVAC Filtration Air Filtration Service Programs Paint Booth Service Programs AIRCUITY Building Performance Monitoring Odor & Corrosion Control Systems HEPA Filters & Clean Rooms Fully Stocked Service Centres Custom Filter Manufacturing Dust Collection Equipment and Cartridges (604) 526-3154 Vancouver
(250) 564-6178 Prince George
www.thefiltershop.com Calgary Edmonton Fort McMurray Prince George Regina Saskatoon Vancouver Winnipeg