
5 minute read
The improved efficiency of modulating condensing boilers
By Brad Poulsen
Condensing boiler heat-exchanger.
In the final year of my apprenticeship, I was in a classroom of fourth-year plumbers who were also preparing for their gas certification. Al Gore’s An Inconvenient Truth had just come out and the instructor expressed that the film left him feeling a sense of helplessness about global warming. I remember this because (although many of us have felt that way) it still was fairly ironic, for in that class we were learning about how to properly size, commission and troubleshoot gas-fired equipment. We had the privilege of saying that every day we would be improving the efficiency of the equipment we work on, and reducing its carbon footprint. The heating profession can make a very real contribution to turning the tide against energy waste.
Since the energy crisis of the late 1970s, the public has been aware that there are environmental limitations to our energy consumption: this awareness has been continuous in Europe, while in North America it has come in waves (closely linked to the cost of fuels). Probably the largest single response from the heating industry has been the widespread adoption of modulating-condensing (mod-con) boilers and furnaces.
The two innovations of modulating-condensing boilers are, not surprisingly, modulation and condensation. Modulation refers to a mod-con boiler’s ability to adjust its firing rate according to the changing needs of the system. Ideally, this flexible firing rate matches the system input to the building’s heat loss. When multiple modulating boilers are networked together, the range of operation becomes even more impressive: taking six boilers, each with a modulating range of 80,000 to 399,000 Btu/hour (23.4 to 117 kW), we have a “virtual boiler” capable of inputs from 80,000 to 2.4 million Btu/hr. This gives the network great flexibility in matching a load that changes over the course of a day or a year. Furthermore, “resizing” the boiler to match the heat loss of the building results in less room temperature over- and under-shoot, which will be more comfortable to the occupants. Finally, lower heating outputs with longer cycles are easier on the equipment and promise longer appliance life.
The main reason mod-con boilers are more efficient is that they condense the water vapour in the flue gases. The water is created during ignition as hydrogen atoms from the natural gas combine with oxygen atoms, and of course this water is in the steam phase until the heat exchanger can drop its temperature to the point where the vapour condenses into liquid water. Sustained flue gas condensation is a phase change releasing significant amounts of energy. (Note that this is also exactly what conventional boiler design must prevent from happening.) Condensing boilers will operate at higher efficiencies than conventional boilers, but the most significant improvements occur when the return water temperature is low enough to promote full condensation. This means that efficiencies are best with radiant floor and cast-iron radiator loads. As we will see, even higher-temperature loads such as finned-tube baseboard and some air handlers can benefit from condensing technology.
It’s very easy to get a sense of the improved efficiencies with condensing boilers if you’ve ever had the misfortune to touch the exhaust venting of a conventional boiler or water heater – it is hot. Those flue gases have to be around 400°F to be buoyant enough to draft properly, and that’s a lot of heat into the sky. By contrast, the flue-gas temperature from a condensing boiler may be as low as 100°F (it will be between 10° to 40° of the return water temperature). Heating applications for relatively low water temperatures, such as serving a radiant floor, will produce the lowest flue temperatures. Even for the highest temperature load, the flue gases can still be expected to be
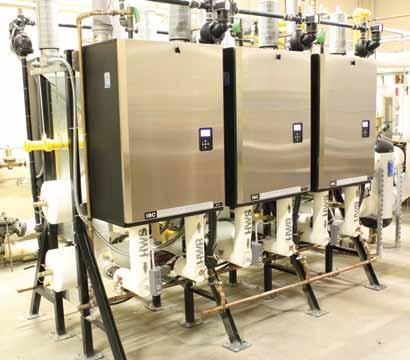
Combustion cycle.
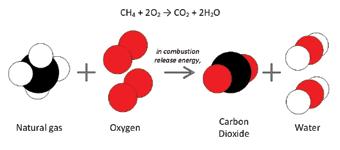
below 220°. This is a tangible measure of how much more heat is being transferred from the ignited fuel than is possible with conventional draft equipment.
Fortunately, modern condensing boiler controls are capable of exploiting opportunities for efficiency that were previously possible only in sophisticated industrial controls. With the availability of outdoor reset, mod-con boilers can use software to regulate the supply water temperature in reference to the actual outdoor temperature. The idea behind outdoor reset is that building-heat loss is proportional to the temperature difference between indoors and outdoors. In practical terms, it allows a heating system that demands high-temperature water during the coldest weather to move into the lower-temperature, condensing range during milder weather. This can result in a major improvement in gas consumption.
The electrical consumption of key components has also dropped significantly. This factor is often ignored, but it is rewarding to do the math on the lifetime operating costs of various circulators. For example, if a small 90-watt wet rotor circulator with a PSC motor runs 4,000 hours a year at the B.C. rate of 9.28¢ per kWh, it has an annual operating cost just over $33 a year. Equivalent ECM motor-pumps operate with approximately half that power consumption. When we factor operation over an expected 20-year life, with a five per cent annual increase in energy costs, we see that one ECM pump saves over $550 in electricity. Remember that the savings of either kind of wet rotor circulator over a conventional ¼-hp pump will be significantly greater. (As a side-note, I acknowledge that some of the old-time gravity-circulating hydronic systems operated without any electrical draw of circulators and combustion blowers. However, their generously sized distribution piping required a very labour-intensive craftsmanship that has long ceased to be economical.)
Modulating-condensing boilers are significantly, often dramatically reducing consumption rates of conventional fuel boilers whenever they replace natural draft boilers. No doubt further innovations in efficiency are in store for us, but for the time being we can be glad when we walk into a boiler room
An efficient, modern modulating-condensing boiler system.
and see part of the solution right there in front of us.
About the Author: Brad Poulsen is a certified hydronics systems designer based in Vancouver. Poulsen draws upon 10 years of experience in the field in his capacity as a technical support professional. He hopes that his degree in philosophy from the University of Toronto is somehow being put to use, as well. b
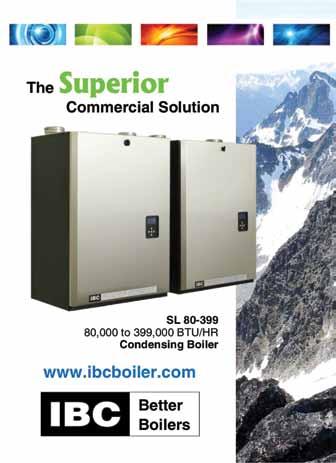