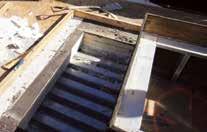
13 minute read
Condensation: Leak posers on a winter day
By meL hoFFarT
The new roof is cut down to the steel deck, then the curb is built with a new vapour barrier on the steel deck (right-hand side of photo). Finally, the roof reinstalled around the box.
The top of the curbs were not sloped and thus held water, which froze solid. When the snowblower was used to access the large units nearby, the resulting ice could get very thick.
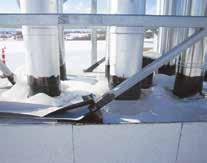
The following summer, a liquid membrane, complete with reinforcing mesh, was installed around the base of all the pipes and penetrations. In my years of working on many projects in the north, it has never ceased to amaze me at how few individuals in the building business have any real-world understanding of condensation. Many building managers with all types of buildings have an extremely difficult time understanding how condensation and roofing can be related, and how it can possibly be relevant to a roof inspector to know how condensation works. It is not uncommon at all for even professionals to believe that condensation collection only occurs in residential situations, such as a poorly ventilated attic. In this article, I will portray how even a large commercial facility, with a flat roof, can experience major problems with condensation and the resultant “posing” of the condensation as roof leaks. The design team had been requesting for several years after completion of this project to “find the leaks”, and reports were submitted, and although possible problems were located and fixed, the real problems were still occurring, and were significant in several ways.

1. They occurred almost exclusively in the winter after a long cold spell and the weather was warming up.
2. There was a notable amount of interior damage below these “leaks”, and they were always in the same spot.
The project was a design-build exercise – one of the first we were part of in the north. There were a couple of design elements on the roof that were new to us on this project, and yet, I must admit, these ideas have been used again and again. It is because of this “repetition of mistakes” that I write this article. In my experience, when one gets down to the basics, there are only two ways to learn; from your own mistakes, or from the mistakes of others.
The only aspect I will discuss here is the use of “super curbs” for dozens of smaller penetrations. In the sequencing of the construction, it was necessary to have the roof completed, with the vapour barrier and insulation and roof membrane all installed as quickly as possible on the building. Many months later, as the mechanical installation progressed, huge holes were cut in the roof system to construct these large-framed “boxes” to run the pipes and vents through. These boxes varied in size from four-foot square by fourfeet high to eight- or 10-feet square, but still four-feet high. They were framed with steel studs and fiberglass batts, not that unlike residential construction, and the outside had plywood and a two-ply SBS membrane. The vapour barrier was still on the original roof deck, albeit quite compromised by the time the various pipes, cables, and ducts were run through it. They were not considered part of the roof by the design team, and thus as roof inspectors, we were quickly and quietly told that our inspections or input were not required in regards to this aspect of the roof. After it started leaking, we were of course expected to find the leaks and have the roofing contractor fix them all as part of the warranty. To be fair, there were numerous vents and pipes run through the top of these curbs that were not well sealed. Many times this was due to the fact that the mechanical installation was too tight to allow flashings around the penetration. After
several years of chasing the problems down and solving only a few, and the refusal of the design team to accept the possibility of condensation being the culprit, I felt compelled to write a long letter to all parties involved. I have included an excerpt from that communication below.
To get condensation to reveal itself in the dramatic fashion as displayed in this report, there are two halves of the equation, the collection and the release, both of which have multiple factors affecting their efficiency and the outcome.
Collection of condensation can be as minor as the drops that collect around a glass of cold water on a warm, humid, summer day, or as major as having an entire attic in a modern home lined with over a foot of heavy hoar frost. I have seen both. The factors that affect this are several, including:
a) The relative humidity in the source air that is being cooled. If you have a very humid environment where the RH is 80 or 90 per cent, then it will only take a slight temperature drop to see large amounts of water condense out of the air, and find a place to collect. If the humid air is being slowly “re-humidified” by breaches in a vapour barrier for example, then the collection process will continue unabated.
Northern Roof-Life b) The surface temperature of the col-Specialists lection point. If the surface temperature of the collection point is well below freezing, even though the surrounding interior air temperature is above zero, then the water collection will quickly freeze to the surface and immediately begin seeking more moisture to capture and collect, with an even greater surface area to do so. E.g. steel studs have greater cold conduction than wood studs. They will thus collect frost on the inside surfaces readily when there is little or no R-factor on the outside surface, and the exterior temperature is cold enough to propel the conduction. MEMBERS OF c) The materials available for collection.
Well-insulated cavity wall construction will rarely have condensation collection on fibreglass insulation, even when it is exposed to the humid air without a vapour barrier. This material does not have the mass to effectively conduct cold through it, and even if there is a bit of frost collected on it, it will usually be absorbed into the fibres and released as vapour before it becomes liquid. The effective
R-factor may well suffer as a result of repeated occurrence of this, but that is not highly relevant here.
d) The air circulation over the collecting surfaces. To have little or no air circulation over the collection-prone surface is to invite more condensation. This is the reason heat ducts come through the floor below the windows. If this design aspect is short changed by closing heavy drapes over the window and thus preventing the air from getting behind the curtains, the result is heavy water collection on the glass surface, which, when left long enough, will begin to form ice at the bottom edge of the window frame. Further consequences will follow.
e) Length of collection time. If humid air is constantly provided to a cold collection-prone surface, then the amount of frost collected will be greater as more time passes. The rate of collection per square inch of surface will slow down significantly when the frost reaches a certain depth, because, like snow, frost has an insulating factor of its own; but, there are now more square inches of collection surface due to the outside area of the frost collection.
Release of the collected frost/water has also several factors that can alter the drama factor and how much damage results.
a) Delta T over time. How fast the exterior temperature changes will have a major impact on the release of the
Northern Roof-Life Specialists

Consulting • Condition Reports • Thermography Specifications and Tendering Quality Control Inspections
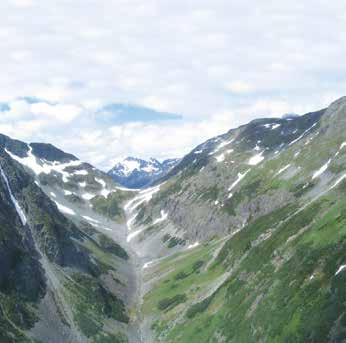
Dawson Creek, BC 250-782-6878 Dick Van Genne RRO
Terrace, BC 250-641-4204 Mike Van Genne Grande Prairie, AB 780-538-4190 Mel Hoffart RRO
ACCEPTED INSPECTION FIRM
Email: mel@topsideconsulting.ca
RCABC and ARCA Accepted Inspectors
After another couple of years, and the liquid ingress continued, the pipes had custom-built stack flashings installed with soldered joints. These custom flashings were then sealed in with another application of liquid membrane, again with reinforcing mesh, and storm collars caulked on every pipe. To be fair, the first application of liquid membrane was cracking at the base line from the thermal movement of the pipes. This repair has held, but the liquid ingress from several of the supercurbs continued until vent louvres were cut in the walls near the top.

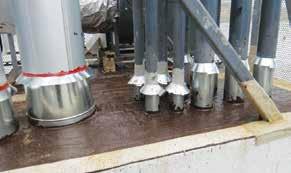
frost. This is one factor that our climatic zone can become almost violent in the way it plays out. This is why I mentioned this in the report. To have six inches of hoar frost melt in less than a day, from a large surface, will have a devastating effect on any susceptible building materials downstream from it.
b) Air circulation over the surface. Here again the air circulation plays a huge role. If there is dry air moving quickly over the surface as the frost melts, then large amounts of the water will evaporate and be carried away without notice by any downstream materials. If, however, the air surrounding the surface is stagnant, or already at a high RH, then the vaporization rate will be slow, and the downstream materials will see water incursion.
c) Absorption rate of downstream materials. If the surface where the frost collects will absorb moisture, like wood studs or fibreglass insulation, then at least part of the potential water incursion is delayed or prevented. If there is a collection mat where the water drips, that can readily release the moisture again as vapour, then many times the interior of the building will not notice a problem. In many cases the older homes with poor ventilation in the attic would function this way.
These are the main factors explained as objectively as possible. In the case of this facility, we do not have photos of many of the elevated curbs, as they were never part of the warranty, and our inspection services were not required. The few photos we have reveal that the construction of these curbs was fairly basic. Twoby-six steel studs frame the walls and flat top of the curb, and the outside is sheathed with half-inch plywood. There are two or three plies of SBS membrane on the outside of the plywood and the vapour barrier from the roof system appears to be running straight through under the curb and airspace within. The walls and roof of the curb we saw were filled with batt insulation.
This box will not collect condensation at the first minor dip in temperature as in the scenario portrayed in your letter. Instead, it will take a significant drop below freezing to see the dew point move to the interior surfaces of the box. Our experience tells us that in the range of -20 to -25 C outside, the inside surfaces of the studs would start to collect condensation, and at some point, a few degrees colder would begin to collect hoar frost. This dew point exterior temperature range could vary significantly if there were a heat source inside the box, such as radiant heat from a B-vent. The time that the cold lasted would also play a role, since the conduction through the studs would take a while. Two months at -25 could have more effect than two nights at -40. There is also the related role that the summer season plays in drying out the materials within the box. The first incidents of condensation collection are usually minor, and if the materials are very dry, their absorption will prevent the release of water from showing inside, at least until the saturation point is reached. The photos we have do not show the pipes, cables, and other assorted penetrations that come through the box as to what sort of cut was made in the vapour barrier to accommodate them. We hope that these breaches in the membrane were properly sealed at the time of installation. But, even if they were, we also know from experience that thermal movement of metal pipes, and to some degree, even plastic pipes, not to mention the vibration that sometimes occurs during use of the pipes, can, and has, opened the seal that was originally installed. In order for there to be no possibility of condensation inside of these boxes, this seal requires perfection.
As to the release of a possible collection; if all of the studs had just half an inch of frost on the inside surface area, and it all melts within a day, to land on the vapour barrier just above the steel deck, it is likely to have a fair bit of depth to it. If there is condensation to release, then there is a hole in the vapour barrier to let it in there to start with, and this same hole will let the water into the building. To our knowledge, there is no appreciable air flow inside of these boxes to allow evaporation, so this is not really part of the equation. The water will remain as a liquid until it either flows inside to drip on a ceiling tile, or the temperature warms enough to vaporize it inside the box and drive it out through whatever egress it can find. Water vapour is 14 times larger than liquid.
This letter received a reply from a couple of the building management team, thankful that I had explained what was going on better than they had ever understood the problems before. The design team never replied one way or the other.
The “supercurbs” eventually had large ventilation louvres cut in their walls to allow the moist air to flow through. The “leakage” has not been a problem since. These supercurbs are used, I have been told, to facilitate some leeway in the location of the pipes, vents, chimneys, and ductwork that are required by the mechanical installation. Indeed, we have seen up to 20 penetrations through just one large supercurb. In the fact that these dozens of small penetrations are raised above the roof line, it is far superior to the alternative. The consequences for possible condensation collection however, cannot be ignored, and are better addressed right at the design phase then as a remedial repair with limitations as to what was still feasible.
It is up to all of us in the construction business to learn from our mistakes, but even more importantly, to pass the lessons learned in finding the solution onto others, especially the next generation. n
CONSULTANTS | SUPPLIERS INSTALLERS | MANUFACTURERS
For over 50 years we have been Canada’s oldest and most-trusted sports contractor. When your equipment is built by Royal Stewart Ltd., IT IS BUILT TO LAST! • Gymnasium Equipment • Scoreboards • Indoor & Outdoor Spectator Seating
T: 204.757.4534 www.royalstewart.com
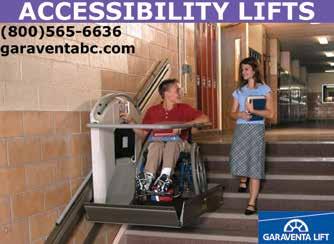
F: 204.757.4618 240 IXL Crescent (St. Clements Industrial Park), Lockport, MB Mailing address: Box 2, Grp. 329, RR #3, Selkirk, MB R1A 2A8
Performance Floors and Walls for Schools and Sports
ERV PARENT
Tarkett iQ Vinyl Flooring Tarkett xf2 Linoleum Altro Safety Flooring Mondo Sport Rubber Wall Protection Systems
Erv Parent Co. Ltd. 791 Caldew Street, Delta, BC Tel: 604-525-4142 www.ervparent.com