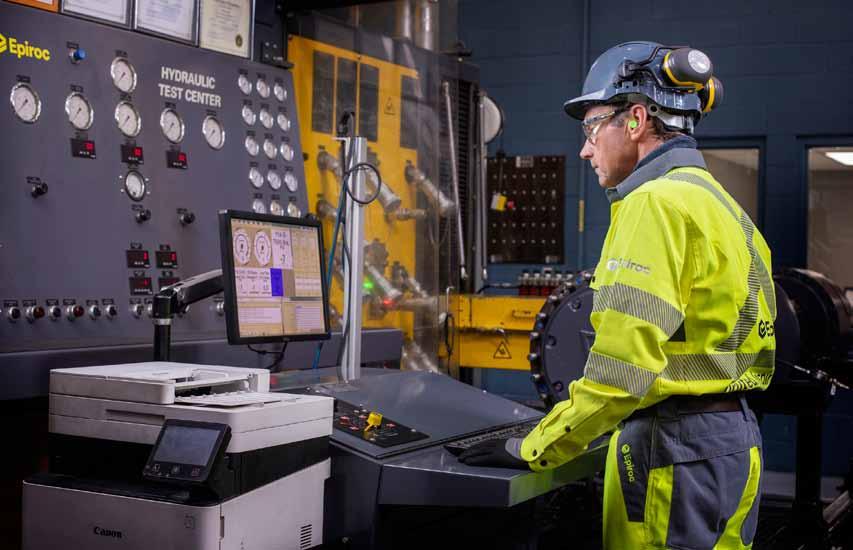
2 minute read
Reman Center focuses on major powertrain components and comprehensive testing methods
Epiroc’s newest Reman Center has found its home in Sudbury, Ontario. Founded in 1873 as part of the Atlas Copco Group until June 18, 2018, Epiroc develops and provides innovative and safe equipment, including drill rigs, rock excavation and construction equipment and tools for surface and underground applications. Epiroc also offers world-class service and aftermarket support and solutions for automation, digitalization and electrification. Based in Stockholm, Sweden, Epiroc boasts about 14,000 employees worldwide in more than 150 countries.
Epiroc has two Reman Centers in North America: one in Tucson, Arizona, and one in Sudbury, Ontario, which just opened up. This state-of-the-art Reman Center is the newest facility to open, which supports Epiroc’s Reman Program, according to Andre Bertrand, Epiroc’s Business Line Manager for Parts and Services Canada-wide and Reman Program Project Manager. While the Tucson location focuses on surface components, Sudbury’s Reman Center focuses on underground components.
“Central Canada has a very strong underground market,” Bertrand says. “If you look at the gold belts, you reach into Val-d’Or, Timmins and Red Lake, and it’s the strongest in the market.” Sudbury’s Reman Center manages the process of recycling components to the newest and latest specifications, guaranteeing availability of components, which include a product range of: • Hydraulic components; • Axels; • Cylinders; • Radiators; • Transmissions; • Torques; • Boom components; • Complete booms; • Boom extensions; • Rotary devices; • Pumps; and • Motors.
“We’ve developed everything this program offers because we’ve seen a missing link in the industry,” Bertrand says. “And it’s really around the biggest benefit, which is guaranteed availability.”
In today’s market, having secure components for one’s fleet, making sure they’re operational, is key. Epiroc is keen on not waiting until destruction to have components in place.
Stock.
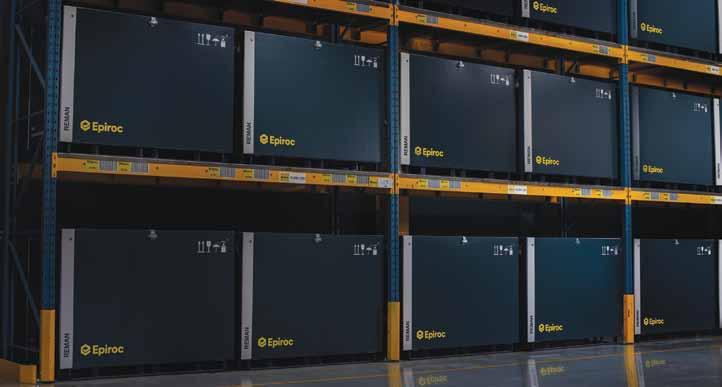
“This is a specialized center that works on continuous improvement. We take components, upgrade them to the latest standards and then go beyond that,” Bertrand says. “If we see a transmission lasting a lifecycle of 6,000 hours, then our goal is to get a life improvement of 8,000 or 10,000 hours. Life expectancy improvements are a big part of our program. That brings a lot of reliability, and in turn for the mining operators, gives them a lower cost of operation.”
Their components also help companies save money, providing 30 to 40 per cent savings over new ones. “We are a certified lean manufacturing facility, but there is lot of detail that goes into every component. Every component is built the exact same way every time, and tested repeatedly,” Bertrand says.
Epiroc developed its own test bench, load centers and flows. Every single component that leaves Epiroc’s doors has been tested through its automated program.
“We designed our own test bench with a testing program that runs components to their desired state, temperature and optimal load times.”
For more information, visit epiroc.com.
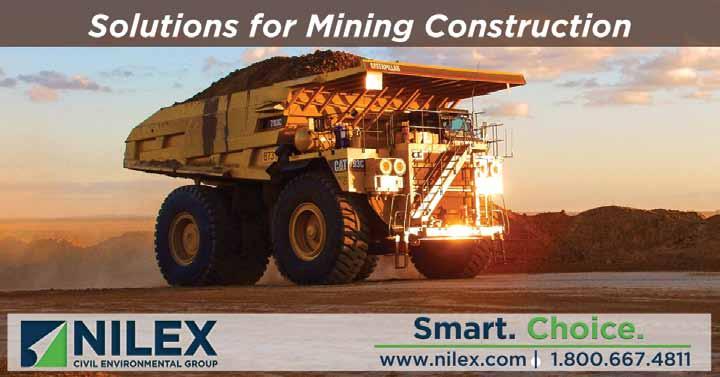