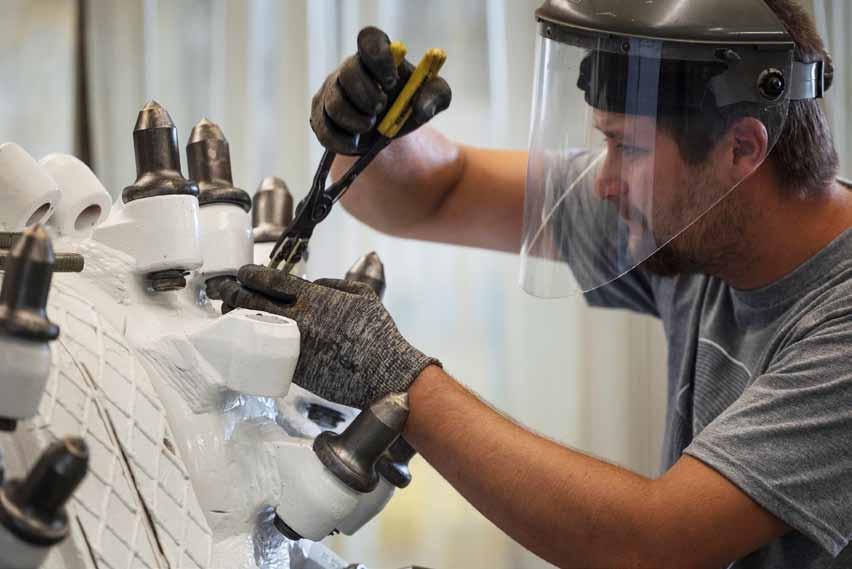
2 minute read
Steps to improved cutting performance
By Scott Bahr
In the world of underground mining, the various methods of mechanical cutting have one general feature in common — the requirement for a properly designed and fabricated cutting assembly. Considering variables like the effects of bit spacing, ease of bit change, and the need for robust design, will increase the performance and service life. This is over and above the initial considerations presented by the mining conditions such as machine configuration, horsepower levels, penetration rate, and the ore being cut. At Bit Service, we ensure we select the method and design aspects for the best possible cutting assembly to suit the site’s particular needs.
Optimizing machine OpeRatiOns
When we begin the process of fabricating a cutting assembly at Bit service, we first meet with our clients and assess their needs. With our time in the industry comes experience and knowledge about the various machines and what they’re best suited for. Three main machines are typically considered — a boring machine, a continuous miner, and a roadheader. each has unique features that would be useful to various mining operations. For example, a boring machine, with its rotors rotating about an axis perpendicular to the cutting face, compared to a continuous miner which has a cutting drum rotating about an axis parallel to the face. The layouts are very different and would lend to different mining operations and types of ore. Each however are considered using the operations requirements of rate of penetration, extraction rate and utilization.
pReventative maintenance
When working with mechanical cutting equipment, it is critical to keep up with preventative maintenance to
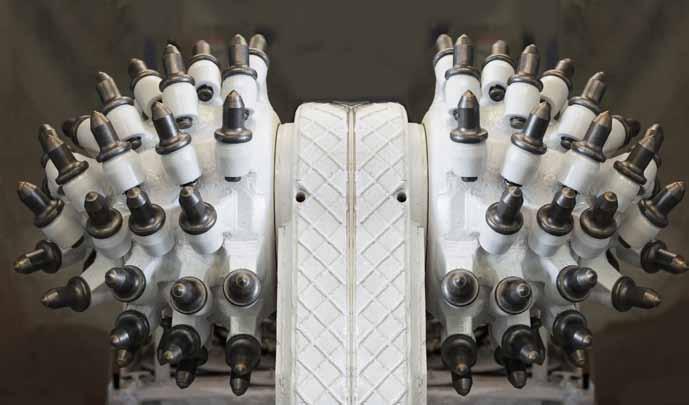
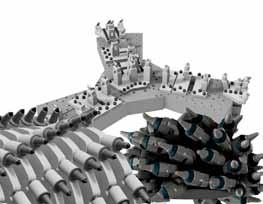
ensure it can operate at its highest function. The cutting assemblies we at Bit Service design and manufacture for our clients are crafted with thoughtful design considerations in mind and are unique from others on the market. To keep up with prime functionality, we have a specialized team to conduct preventative maintenance. We offer inspection, refurbishing, and repair of cutting assemblies for development roadheaders and continuous miners.
cOnditiOn Of cutting bits and bit hOldeRs
The carbide bits are often the front line of mining operations in soft rock and industrial mineral mining. It is essential to make sure the bits themselves are in prime working condition so the machine can be as efficient as possible. Regular maintenance of bits helps ensure the most efficient return on resources.
Optimization of the cutting assembly itself is done at the fabrication or rebuild stage, through revised bit positioning, bit spacing, and the cutting assembly’s generalized layout. We do so to optimize the rate of penetration and the size of the cut ore to be able to maximize the efficiency of the machine. After optimizing different elements, our final step is further assessment of the entire assembly’s working order and efficiency. Once maintenance is required, it’s important to optimize how easily the bits could be changed. We aim to maintain serviceability in the design of the cutting assembly to accommodate ongoing maintenance, bit changes and future repairs. At Bit Service, we are excited to solve problems like these for the Canadian mining industry, and are eager to discuss how we can help apply this process at your site.
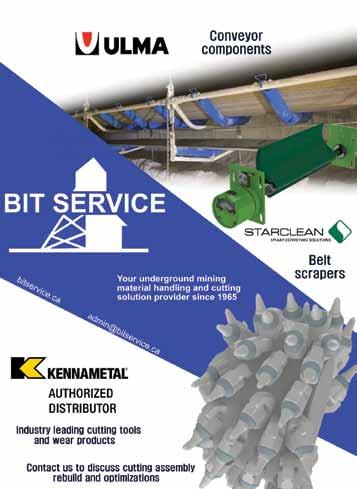