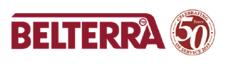
4 minute read
Delivering a successful project: Belterra
delivering a successful project
Belterra’s involvement in the K3-K1 overland conveyor project began back in summer 2019 with a preliminary meeting to discuss Belterra’s potential involvement.

2020 has been a year unlike any other.
In a year where CoVID-19 wreaked havoc on the overall economy, we were fortunate at belterra to be involved in some special projects in the potash industry. None more impressive than the k3-k1 overland conveyor project.
belterra’s involvement in the overland project began back in summer 2019 with a preliminary meeting to discuss belterra’s potential involvement. as belterra had the experience from the previous overland conveyor, we knew what to expect, and we were prepared for any obstacles that could present themselves.
once belterra was selected as the preferred vendor, the real work began. lead by steve Hornsby and our worldclass belterra steel cable division, we went to work planning the project over the next six months. the client’s expectation was that the successful bidder remains relatively self-sufficient and also facilitate subcontractors, rental equipment, and coordinate execution of their work around other contractors while adhering to all on-site safety and other project requirements.
Hornsby and his team created a plan that oversaw the planning, mobilization, execution, and closing of the proj-
Despite the challenges of this project in conjunction with the COVID-19 pandemic, the project was completed in five months; two weeks ahead of schedule and on budget.
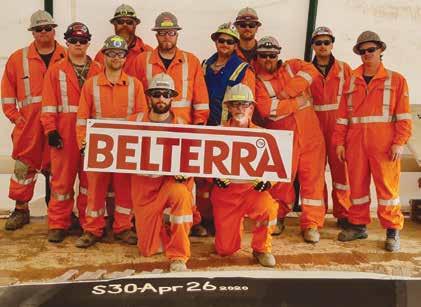
ect. Members of our service and support team were assigned to the project based on their areas of expertise and the project plan was broken into the key phases based over a 10-month schedule (including in-shop planning, on-site work, and project closing). the project team worked closely with the client to make sure no detail was overlooked. this allowed the customer to coordinate all work and make key decisions such as:
• Size of belt reels.
• Location and timing of work to be completed by all other contractors.
• Coordination of safety, quality, and construction documentation.
the scope of work was to install 74,200 feet of 54-inchwide st2500 steel cord conveyor belt, requiring 30 splices be executed in the field. suffice it to say, a project like this doesn’t come around often and would be a major undertaking since k3-k1 would be one of the longest continual conveyors in North america.
belterra mobilized to site, staged all the equipment, pulled on 30 rolls of st2500 x 2,500-foot belt, and com-
pleted 30 splices. Despite the challenges of this project in conjunction with the CoVID-19 pandemic, the project was completed in five months; two weeks ahead of schedule and on budget.
the reasons for a successful project:
• Belterra’s experience and leadership on previous largescale projects.
• Belterra’s familiarity with the site and the scope of this particular project.
• Belterra’s number of qualified and experienced belt technicians that we could dedicate to the project.
• Belterra’s planning and attention to detail on this project.
on completion of the project, all of the customer’s expectations had been met or exceeded, with the additional benefit of being able to move product on the conveyor ahead of schedule.
“thank you for the superb work you and your team have performed on our project. as you have stated, the work went very smoothly almost without issue and that was due in large part to the preparation, planning, and flawless execution provided by your team,” says Murray Daku, project manager for Wood. We are all very pleased that you have performed the work safely and still been able to complete earlier than the original schedule, even in light of all the CoVID-19 challenges that were thrown at us. thank you again to you and your team for the great work!”
belterra has proven itself to be a valuable partner, advisor, and product expert to the potash industry for decades. from large overland projects to everyday conveyor maintenance, at belterra, we keep you moving. s
We have partnered with premium suppliers to bring you the latest products, innovations, and expertise. Whether you need belting, components, advice, or immediate service solutions, we’re here to help you whenever you call. When it comes to Potash mining, the high-demand environment leaves no room for error. At Belterra, we have spent years researching and understanding your needs and we appreciate the tough conditions you operate under. Our responsive, 24/7 service is here to keep you operational at all times. With Belterra you can count on: • Lower costs per ton • Your single source for unsurpassed product selection and availability • More material through-put • Reduced downtime or unplanned outages • Measurable health and safety improvements • More efficient use of your facility staff time
Our core business:
• Conveyor belting • Conveyor components & accessories • Transfer point solutions • Industrial hose & fittings • 24/7 conveyor service
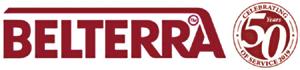
REGINA SASKATOON
157 Leonard Street N., Regina, SK S4N 5X5 302-50th Street E., Saskatoon, SK S7K 6X2 regina@belterra.ca saskatoon@belterra.ca
Tel: 306.546.2400 Tel: 306.244.2400 Fax: 306.546.2440 Fax: 306.244.2500 www.belterra.ca

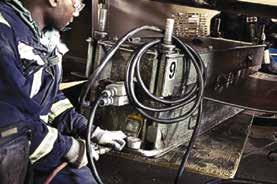
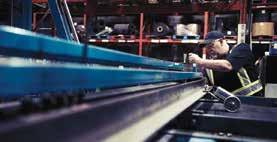