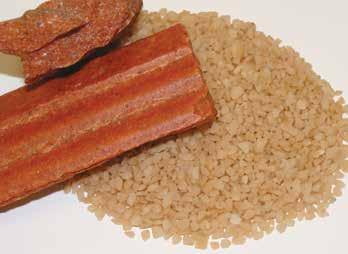
3 minute read
in compaction technology
processing fines prompts advances in compaction technology
fertilizer industry producers mine ore both underground and on the earth’s surface, and chemists and process engineers utilize numerous processes to yield product for distribution on farm land. one example involves the creation of k2so4 (soP) through the leblanc process, more specifically, the Mannheim process. this process creates premium potassium fertilizer required for healthy plant growth and plant metabolism. It promotes optimized crop yield and higher-quality produce. farmers typically use soP for high-value fruit farming with chloride-sensitive crops such as grapes, beans, berries, and legumes. soP, known for its abrasiveness, is typically extremely fine particle size distribution (PsD), following the completion
Ludman Industries Model 4440 Roll Compactor translates waste fines into salable granular product. of the Mannheim process. therefore, how do farmers transport and spread such a fine product onto their fields? farm fertilizer applications require product with high granular integrity, uniform size and shape, no dust, yet highly solubility in water. agglomeration processes, such as roll compaction, densifies highly fine powder into granular particles that can be stored, shipped to and distributed by farmers throughout the world, including billions of acres.

sulfates require high pressure per linear inch to compact product uniformly and with low friability. Compacting fine abrasive material presents challenges, solved by rugged reliable machines, like ludman Industries roll Compactors. ludman develops and invests in leading industry technology to provide the best roll compaction equipment for fertilizer producers.
examples of investments made to improve system yield and achieve quality product include:
• Hi-PAK Ludman Corrugated Rolls — fine PsD products call for larger nip zone in roll compaction equipment. slowing roll speed achieves larger nip zone, but conversely affects throughput. ludman’s corrugations capture more product and mitigate adverse roll speed factors. this approach maintains higher production volumes, while creating dense product.
• Synchronous roll technology to increase system yield and lower cost of ownership — Deep Groove technology employs consistent corrugation patterns that, likewise lead to consistent product. Maintaining geometric product shape in congruence with total roll control involves synchronizing roll operation. While simple in concept, in practice, rolls constantly work in opposition to the other, as torque forces vary on each roll. ludman roll
Positioning technology allows for complete control by forcing the rolls to work together. output with this method shows consistent shapes, consistent thickness, and uniformly dense product.
• Advanced alloy technology — as mentioned, soP abrasiveness requires rugged heavy duty metals, yet reliable performance to compact ideal product. balancing roll hardness and
brittleness is key to answering this problem. ludman’s highchrome, spun-cast shells with forgiving cores complement time-tested, industry-leading roll compactors. advanced roll technology provides reliable and longer-lasting roll faces that withstand high pressure and continuous operation.

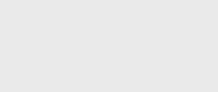
total process solutions for roll compaction paired with innovative machine technologies bolsters potash producers looking to achieve greater yield and consistently superior product. s
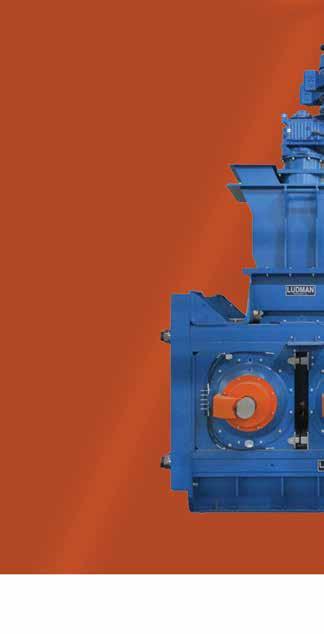
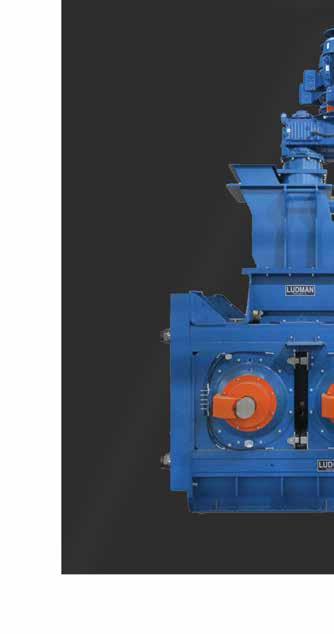
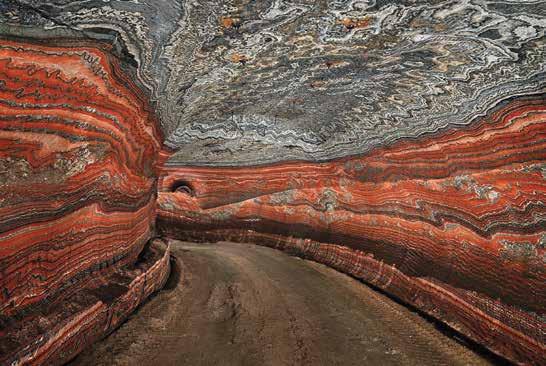

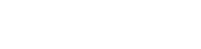

Ludman develops and invests in leading industry technology to provide the best roll compaction equipment for fertilizer producers.
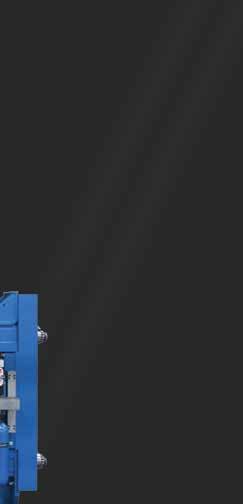
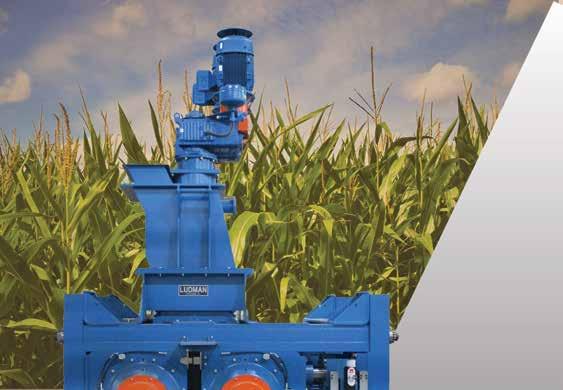
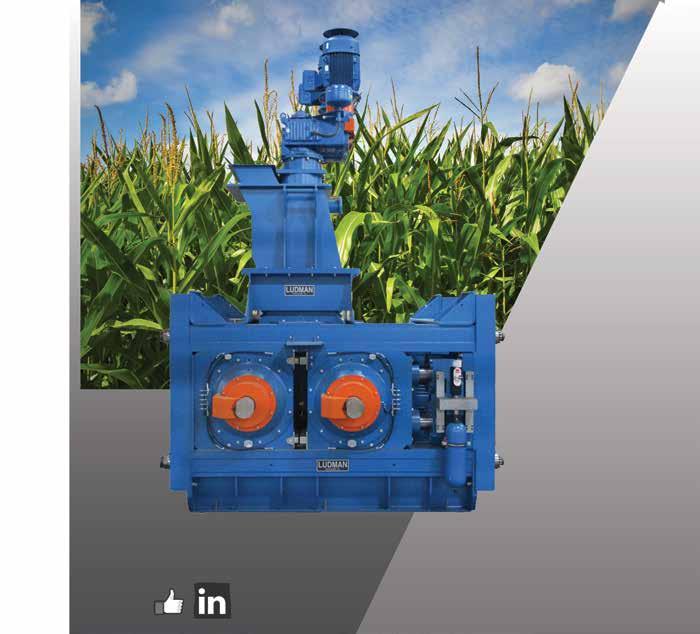
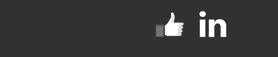

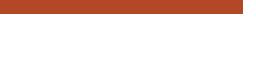
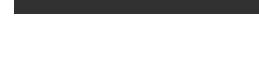
