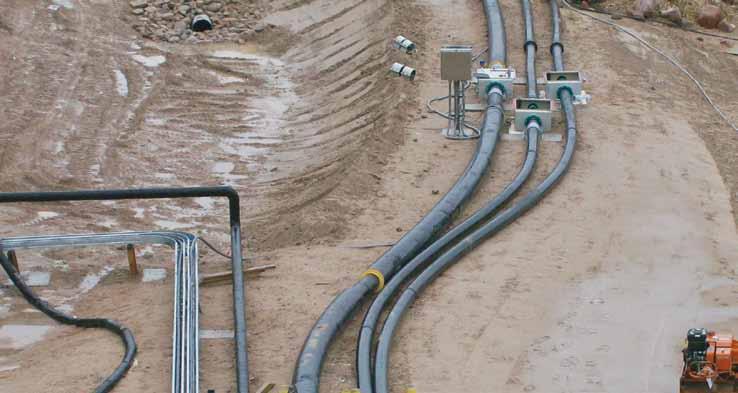
4 minute read
HDPE pipe use in potash mining
By Eric lamontagne, p.Eng., gE Environmental solutions inc.
high-density polyethylene pipe (HDPE) has been used in potash mining for well over 30 years. HDPE pipe can come in many forms, with the most popular by far being the solid wall HDPE pipe. Solid wall HDPE pipe is a continuous and homogenous wall that varies in thickness depending on pressure ratings. This pipe is primarily used for slurry or water conveyance, however, can be utilized with any process piping infrastructure.
The resin that is used to manufacture HDPE pipe is continuously advancing, allowing for more design flexibility. These advancements allow for the potash mining processes to become more operationally efficient.
The HDPE pipe is already well known in the industry and widely accepted, however, the designing, fusing, and installing is still an area to focus on as a producer. Designing with HDPE pipe requires material engineers to combine knowledge with chemical and civil engineers. This process is crucial to ensure the design with HDPE pipe is suited for each individual site.
During the design phase, one characteristic to review is the head loss in fittings. The head loss in fittings can be affected by various fusion characteristics. This includes moulded elbows versus mitered elbows. Mitered elbows are created using the butt fusion process and may have multiple miters which creates additional head loss. Mitered elbows are customizable, however molded elbows provide less head loss but require more space for installation.
During process applications such as slurries in potash mining, a considerable amount of time should be dedicated to understanding what pressure surges may occur in the selected HDPE lines. HDPE in comparison to other pipe materials is fatigue resistant primarily due to two factors. The first factor being that HDPE has a lower stiffness than other pipe materials. The second factor is that the higher-pressure rating required of other pipe materials is generally not required with HDPE to cope with the effects of pressure surges.
The area of thermal fusing requires fully trained staff to ensure quality welds. Training is typically provided by distributors and/or fusion machine manufactures. There are currently no third-party training providers for HDPE pipe fusion. The fusion equipment manufacturers require that you are trained with their equipment, however being trained on equipment does not ensure your knowledge of HDPE fusion is sufficient. It is recommended to ensure your training curriculum includes equipment training along with organizations that have extensive knowledge of HDPE pipe fusion techniques and manufacturing processes.
Each potash site has challenges with new and existing HDPE pipe. This includes fusing existing pipe onsite to new HDPE pipe. The probability that the resins of old and new pipe are not the same is high. The melting point for each resin may be different, therefore this will change the procedure of the thermal fusion process. HDPE, along with all polymers, are subject to UV degradation over time. Most manufacturers include a percentage of carbon black additive as a stabilizer, which causes the pipe to be black in colour. Studies have shown that the oxidization of the HDPE exposed to UV can still retain original performance for greater than 50 years of service life.
During installation, it is imperative to understand the behaviours of the HDPE pipe during operation and whether the pipe will be confined, restrained, or unrestrained. Unrestrained pipe has a great deal of expansion/contraction that can occur. If confined, or buried, there are various calculations used to determine burial depth of a specified pipe. Factors such as material conditions, saturation, water level, burial depth, and load capacities, among others, should be taken into consideration.
Insulation on exposed HDPE pipe in Canadian winters is another huge consideration for designers and installers. Selecting the right insulation is dependant on the expected temperature of the material being conveyed, along with external temperatures.
The other common pipe is corrugated HDPE pipe. These materials do not have their walls made of solid HDPE. The primary use for this material is for culvert crossings in acidic environments. These pipes, dependent on the manufacture, has enough strength for deep burial applications. More specialized HDPE pipe comes in the form of a smooth inner/outer surface with an air annulus inside the wall. This pipe is also used in burial applications as culvert crossings. When designing with these materials, there are specific formulas to use based on the manufacturing technique. Beyond the live loads, it is important to consider the material used for cover of these products. The corrosion resistance and ability to withstand large burial pressures make the ideal choice for producers when considering water conveyance for site runoff applications.
The use of HDPE pipe products, particularly in the potash producing sector, has had a positive sustainable impact on operations. Capital expenditures are reduced with HDPE pipe, while significantly extending infrastructure life expectancies. l
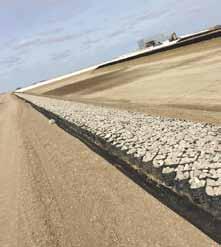
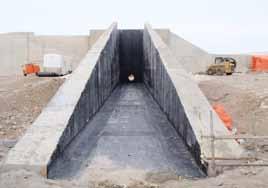
CONCRETE PROTECTIVE LINER HDPE PIPE
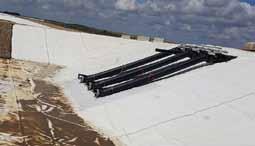
CELLULAR CONFINEMENT
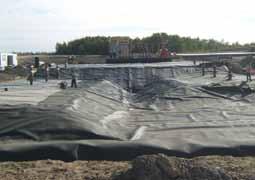
COOLING POND CONTAINMENT DRILLING PADS
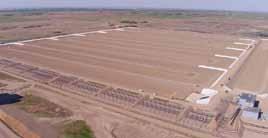
