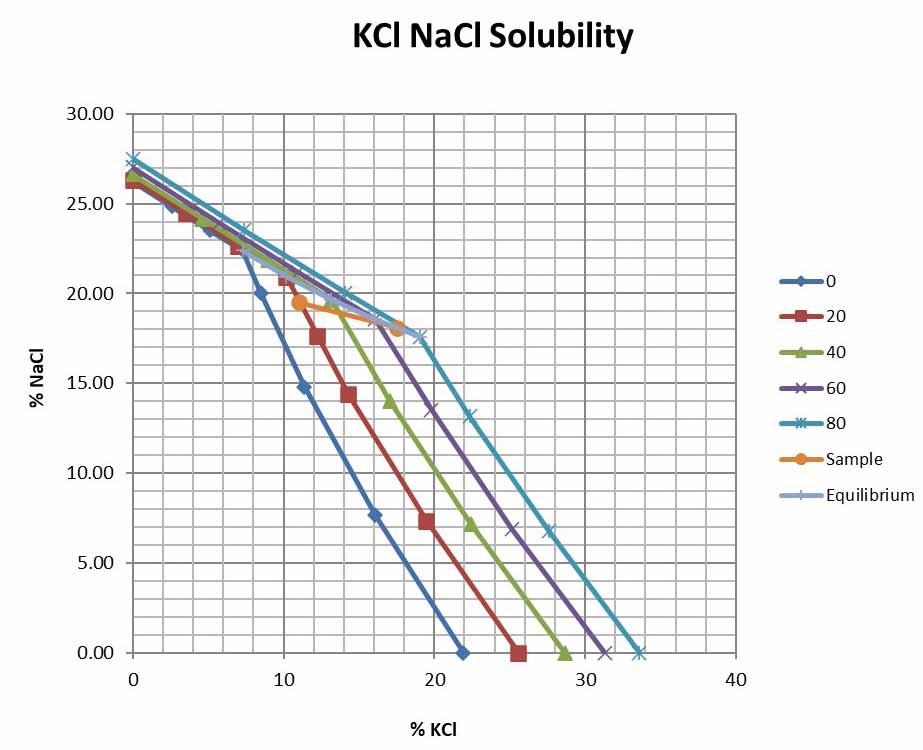
3 minute read
THe neeD foR GooD SCienCe in THe DeSiGn of SeLeCTive SoLuTion MininG of PoTaSH
By harvey haugen, ceo, BPPc
istarted working in potash in 1969, my son in 2000, and my granddaughter in 2020. A lot has been learned over the years since the early days. Unfortunately, sometimes as an industry matures, it starts to rely on established principles that need to be reconsidered. “That equipment has always been used”, “We tested that 20 years ago and it didn’t work”, “We need saturated NaCl brine”, and so on. Young process people come on site and are overwhelmed by the established body of knowledge. Even the highpriced consultants know how it is done.
This is particularly true of solution mining. Many of the designs for new selective solution mines are not working and will not work since they are designed from ideas out of old patents, and traditional ideas that cannot be supported by good science and engineering.
Carnallite was solution mined in Germany as far back as 1861. The first attempt at solution mining of potash in Saskatchewan was in 1951 by Western Potash at Unity. A number of companies tried solution mining through the ‘50s into the early ‘70s. Only one of these attempts produced an operating mine. The PP&G mine resorted to 400-year-old total dissolution mining techniques, but limiting vertical development with oil (German patent 182,042, 1907).
To go forward, we need to understand the phase chemistry. The simple phase diagram details solubility of mixes of KCl and NaCl at various temperatures. This is essential for design and modelling of a solution mining method. The mystery of the effect of carnallite is also readily explained by looking at the more complex phase diagram, including KCl, MgCl 2, and NaCl.
We need dissolution rate data. Starting in 1960, the Saskatchewan Research Council “undertook to investigate ways of eliminating the need for shafts” due to the difficulties being experienced in shaft sinking, and the lack of positive results in solution mining. The study was summarized by Selim Ozsahin and W.H.W. Husband in “An Investigation of the Potential of Solution Mining in Saskatchewan”. The report recognized the lack of any detailed study available in the public domain on dissolution rate versus temperature, flow velocity, degree of saturation, and ore grade, and provided valuable studies to correct that deficiency. This is a valuable resource.
The SRC studies were done on pressed salt-potash mixes. Over the past 20 years we have done hundreds of dissolution tests on real potash ore samples and have confirmed that these dissolution rate results apply to Saskatchewan ore. These dissolution studies are required to model the mining process.
The report does contemplate the possi- bility of “selective dissolution” using a saturated NaCl solution and “replacement of NaCl with dissolved KCl”. The concern raised is the possibility of salt precipitation in the cavern coating the surface. This has been one of the real problems in current attempts.
The use of saturated NaCl solution and the plating of salt in the cavern are a couple of the problems limiting selective mine development. Use of saturated NaCl is simply an error. Plating is real but can easily be understood and managed by understanding phase chemistry. This is not complicated, but almost never appears in current design work.
The third aspect is understanding what happens in the cavern with only the potash being dissolved (the definition of selective mining). We need to come up with plans for cavern development and do detailed modelling of flow patterns of brine and solids to get a workable selective mine. The development of directional drilling has been an easy claim to a mine design. So far that does not seem to be working. The idea that potash can somehow be extracted from the in-place salt matrix like oil from sandstone has not been explained and will not work beyond a few centimetres in high-grade ore. Crazy claims are made about cavern temperature and injected fluid temperature requirements that simply cannot be supported by calculation.
Get the mine right and the plant involves simple contact cooled crystallizers. A well-designed selective solution mine could cut capital cost (per tonne) by 80 per cent, operating cost by 40 to 50 per cent, with no tailings, minimal water consumption, and low carbon. Good science.
As the old guy in the trade, maybe we need to do some seminars and demonstrations in process design. Process design certainly involves awareness of current practice and established knowledge, but we need to make sure that it is supported scientifically if we are going to succeed and go forward.
Let’s make potash. l
We understand that protecting infrastructure drives profit. Feeding your process refinery safely and without interruption is paramount.
We have the solution...
Pre-Krete G-8
Pocono Fabricators’ Pre-Krete G-8 has been safeguarding site piping of Potash slurry from abrasive and corrosive conditions at elevated temperatures since 1982.