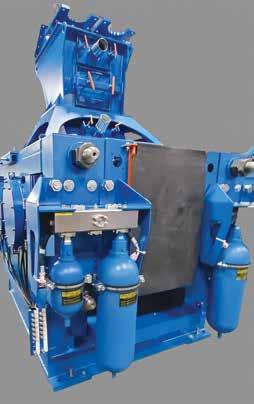
3 minute read
Allis-Chalmers’ legacy in potash roll compaction continues today

Ludman Industries Model No. 2826 Roll Compactor(s).
In 1956, heaping salt fine piles filled potash mines. Producers understood it was uneconomical to ship salt long distances by land, so Allis-Chalmers engineers, working in these mines, saw an opportunity to turn it into salable granular product. All they needed was a machine to accomplish that feat. They surmised a 2020 Flaking Mill would compress and shear the fines, like it had for over 75 years, being a household name in the cereal flaking business. However, the force of the machine could not compact the salt enough. Therefore, engineers determined a larger 2424 machine with greater horsepower would be necessary to satisfy customers’ demand. The first roll compactor (also known as a roll press) received its name after producing stellar results in both salt and potash trials.
After inventing the first roll compactor, Allis-Chalmers received tremendous amounts of business, selling over 60 machines in the first five years of the product’s life. The original Allis-Chalmers compactors had 24-inch diametre rolls with a 24-inch face (roll length). These machines consisted of smooth rolls, powered by 200 horsepower (150 kilowatt) motors, with one floating roll applying required hydraulic pressing force. A gravity-feed chute fed potash into the compactor. This setup pioneered drastic improvements in industry profitability. Sustained compaction business led to greater gains in process improvement and quality.
Ludman Industries acquired Allis-Chalmers’ Mining and Food Divisions, including various product lines, such as compactors, granulators, briquetters, and flaking mills in 1986. Prior to the acquisition, Ludman Industries manufactured Allis-Chalmers machines for close to a decade. Since that time, Ludman Industries has engineered, manufactured, and serviced well over 100 roll compactors for potash customers globally.
The latest roll compactor includes elements from the original 1950s design; however, technology
and continuous product improvement significantly improve performance. Roll patterns, such as corrugated roll faces, have replaced smooth rolls. Roll corrugation increases the nip angle, allowing production of a thicker cake and provides capacity increases. In addition, corrugation prevents slippage between roll surfaces and minerals, lessening wear and lowering energy consumption. Slippage can cause “glazing” on rolls, in which potash fuses to the roll surface. Timing corrugated rolls produces uniform flake thickness and quality. Uniformity results in less fines generation in the downstream crushing process, increasing production and reducing material recycled to the compactors. Corrugation patterns vary based on size distribution of material feed. Despite immense product improvement over 66 years of potash compaction, a number of roll compactors supplied by Allis-Chalmers as long ago as 1959 continue to operate in potash mines. However, most of these machines have been retrofitted or rebuilt to improve performance. Many of the improvements include managing temperature of the roll face and bearings through utilizing coolants and lubricants, improving roll wear resistance and structural integrity, operating machines with single- or twin-force feeders, multiple bearing designs, variable speed motors, and planetary reducers. The future of roll compaction appears bright with a number of new projects underway in the potash industry, showcasing the most advanced compaction technology. s




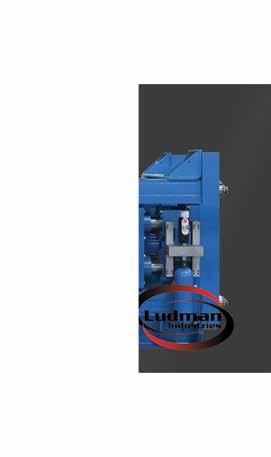
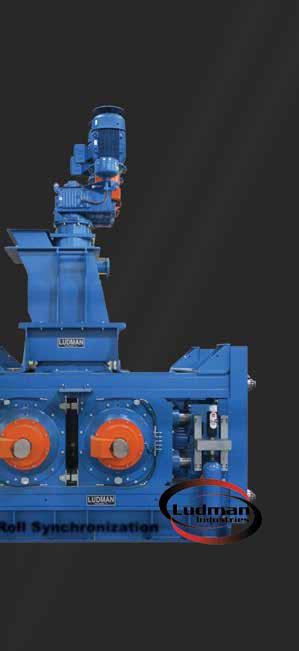
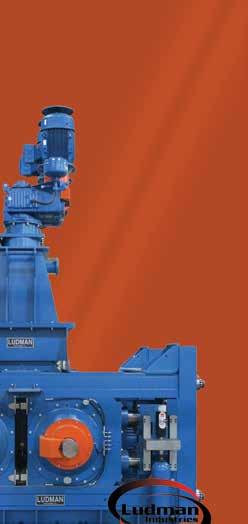
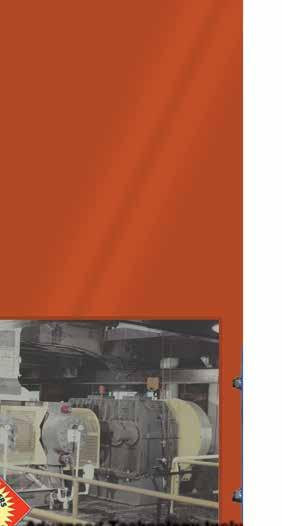
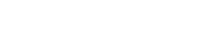
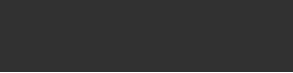


