
7 minute read
Improving uptime when processing potash
BY CRAIG PEPPIN, CUSTOMER SERVICE MANAGER | FEECO INTERNATIONAL
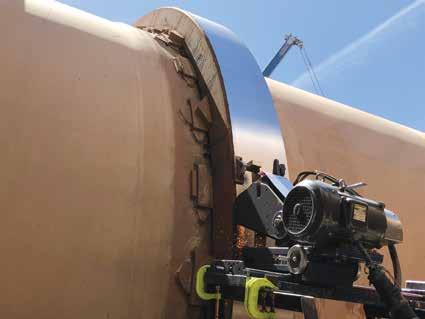
FEECO Rotary Dryer for processing potash. Tire grinding in progress.
With potash production booming, improving uptime and minimizing inefficiencies in production equipment has become more important to producers than ever before. And while welldesigned equipment is the first step in building a reliable and efficient process, equipment maintenance is just as important, particularly when it comes to potash, where challenging material characteristics and demanding operating conditions have the potential to quickly degrade equipment.
In addition to keeping up on OEM-recommended maintenance and lubrication schedules, the following maintenance procedures are often essential for potash producers. While some apply specifically to rotary drums, many of these principles apply to all types of potash production equipment, including dryers, mixers, disc pelletizers, bucket elevators, conveyors, and more.
Implement inspections & audits
The easiest and most costeffective way to ensure uptime is through maintenance and regular inspections. Operators and maintenance personnel must be thoroughly trained not only in operational and maintenance procedures, but also in inspecting the equipment. Personnel should be familiar with normal operating conditions and be able to quickly identify abnormalities and potential issues.
Inspections should be conducted daily, weekly, monthly, and biannually to catch problems at their onset, before they have a chance to escalate into a process upset or serious damage. Depending on the potash source, as well as site-specific operating conditions, each inspection interval should focus on different components, based on their potential for wear.
The plant manager or maintenance planner should also bring in the OEM or a third-party service provider to conduct a more thorough inspection of the equipment on an annual basis, particularly in the case of rotary drums, which are
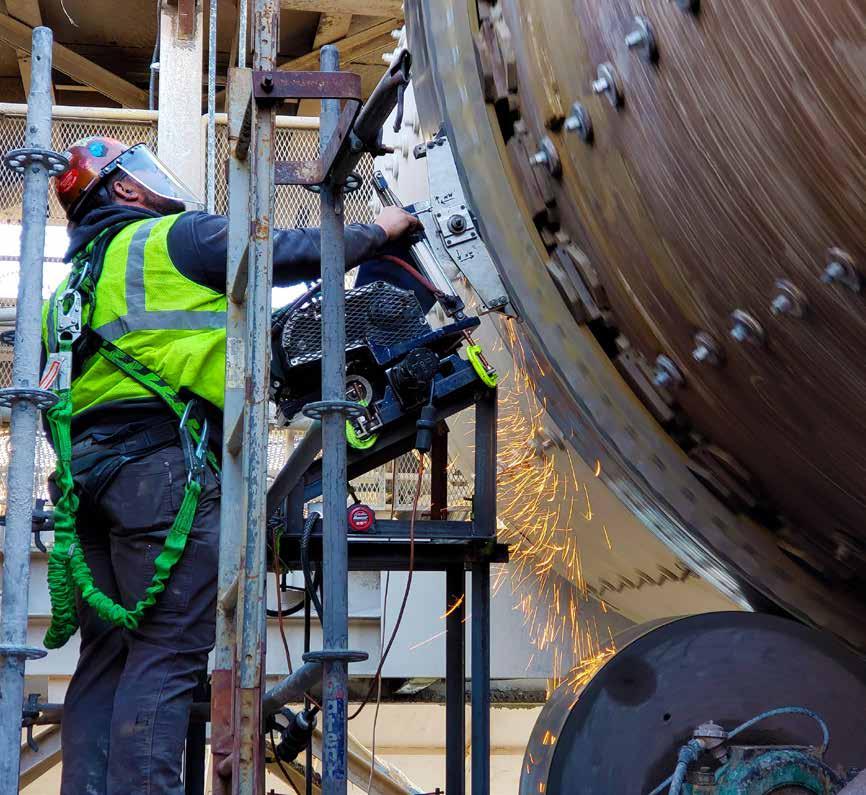
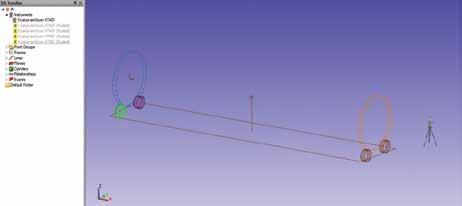
Software provides a visual representation of the rotary drum during laser alignment.
used to accomplish everything from scrubbing and drying, to granulation and coating when it comes to potash. In addition to early identification of issues, annual inspections provide valuable benchmark data.
Producers with multiple drums on site can take advantage of FEECO International’s Monthly Dynamic Inspections, in which only a single drum is shut down and given a static inspection, while the remaining drums receive a dynamic inspection as they continue to operate. Each month (or quarter, depending on the unique scenario), a different drum is shut down for a thorough inspection. This systematic approach to preventive rotary drum maintenance streamlines maintenance planning and procedures.
FEECO also offers process and equipment audits for helping potash producers troubleshoot issues, optimize production, and train operators on their unique production environment. Such efforts can often mitigate inefficiencies, eliminate unnecessary downtime, and quickly contribute to the bottom line. This is particularly useful in plants employing a pin mixer-disc pelletizer setup, where operators must have a solid understanding of the principles behind tumblegrowth agglomeration (wet granulation).
Keep up on rotary drum tire & trunnion grinding (reconditioning)
As load-bearing surfaces of the rotary drum, trunnions and tires are often the first to exhibit wear when an underlying issue is present. This may be the result of misalignment, excessive wheel skewing, poor housekeeping, or any number of other potential problems.
Grinding is carried out on tires and trunnions in order to recondition the surfaces of the components for smooth and proper operation. Combined with a trunnion wheel laser alignment, this minimizes mechanical stress and circumvents more severe damage down the road.
Monitor tire creep
Tire creep is a function of the gap between the tire inside diameter (ID) and mounting block outside diameter (OD). A good rule of thumb for a dryer is to have less than half an inch of tire creep per drum revolution. When creep is greater than half an inch, the drum should be monitored quarterly (or more frequently). It’s also a good idea to have a shim kit on hand; when tire creep reaches or exceeds three quarters of an inch, plan to re-shim during the next scheduled outage.
When creep becomes excessive, it can cause wear on filler bars and tire keepers (tire keepers hold the tire in its axial position and if allowed to wear, can cause the tire to exhibit excessive axial movement).
Evaluating or measuring tire creep is an important indicator of the tire mounting system and should be measured annually at a minimum. Tire re-shim projects vary in scope from simply adding or replacing the thin shims under floating blocks, to replacing all the floating blocks. If there is significant wear on the shell under or on the floating blocks, the whole tire mounting system may need to be replaced. When planning a re-shimming job, the drum shell temperature needs to be taken into account to determine the proper gap and creep.
Keep up on rotary drum alignment
Proper alignment of mechanical components, and most notably the trunnion bases, is also essential to rotary drum longevity, as a misaligned drum puts undue stress on all components.
Wear on tires or trunnions, or chattering noises, may indicate that a drum has fallen out of alignment. Further, rotary drums must be realigned after any major repairs or changes to the base conditions, as this will cause the drum to become misaligned.
FEECO recommends plant managers take advantage of laser alignment techniques, which offer faster, more precise alignment compared to manual methods. The laser tracking system can also be used in other production settings, such as alignment of offset-mounted machines, power transmission alignment, conveyor pulley and frame alignments, and more.
Encourage regular cleanout
Potash’s corrosive nature means that if allowed to build up and sit in equipment, the material is likely to cause corrosive damage.
While this requires a preventive approach during the initial design stages, it’s also critical to regularly clean out production equipment in order to circumvent any corrosive action.
This is made even more important because of the fact that potash is a hygroscopic material, which makes it prone to clumping and buildup.
Regular cleanout also gives operators and maintenance personnel the opportunity to more closely inspect the equipment’s internals.
Additional retrofits such as liners, knockers, or alternate materials of construction are helpful to slow degradation with existing equipment. Equipment should also be fully seal-welded to prevent potential places where material could collect and begin corroding the unit.
Monitor drum wear
Measurement and evaluation of the wear on rotary drum internals and shell thickness should be logged annually. Having a trend of wear is critical in evaluating the lifespan of a rotary dryer or cooler, especially in a potash application.
Critical rotary drum areas to evaluate are at the infeed end, where the material moisture tends to accelerate the material’s corrosiveness, as well as where material velocity is greater. These locations are typically high-abrasion areas. Areas that combine abrasion and corrosion risks are the highest-risk areas requiring the most attention.
Keep wear-critical parts on hand
While not a direct maintenance requirement, it’s a good idea to work with the OEM to keep an inventory of wear-critical parts on-hand. This might include mixer shafts, trunnion wheel assemblies with bearings, tire-mounting kits, thrust rollers, sprockets/pinion gears, or otherwise.
Keeping these parts on-hand helps to prevent excessive costs on critical components and extended shutdowns due to long lead times.
Conclusion
Reliable production equipment is the foundation of a successful potash production facility. By keeping equipment properly maintained, be it a dryer, mixer, elevator, or otherwise, producers can maximize process uptime and mitigate inefficiencies and excessive maintenance costs.
In addition to keeping up on OEM maintenance and lubrication recommendations, a preventive maintenance program should implement a rigorous inspection program, ensure equipment is regularly cleaned out, and pay particular attention to the specific maintenance needs of rotary drums, such as monitoring key measurements and wear, as well as conducting regular grinding and alignment as needed. Additionally, keeping wear-critical parts on hand can save significant time and cost by allowing for a fast change out in a bind.
With over 70 years of experience, FEECO is the potash industry’s preferred provider for custom potash processing equipment and extensive parts and service support, including all of the services mentioned here. For information on how we can keep your potash operation running its best, visit us at FEECO.com. s